Прикладная биохимия и микробиология, 2022, T. 58, № 4, стр. 382-387
СРАВНИТЕЛЬНОЕ ВЫЩЕЛАЧИВАНИЕ МЕДНО-НИКЕЛЕВЫХ КОНЦЕНТРАТОВ И МЕТАЛЛУРГИЧЕСКОГО ШЛАКА БИОГЕННЫМ РАСТВОРОМ ТРЕХВАЛЕНТНОГО ЖЕЛЕЗА
Н. В. Фомченко 1, А. Е. Панюшкина 1, В. С. Меламуд 1, М. И. Муравьёв 1, *
1 Институт микробиологии им. С.Н. Виноградского, Федеральный исследовательский центр
“Фундаментальные основы биотехнологии” Российской академии наук
119071 Москва, Россия
* E-mail: maxmuravyov@inmi.ru
Поступила в редакцию 02.02.2022
После доработки 26.02.2022
Принята к публикации 28.02.2022
- EDN: SMATVM
- DOI: 10.31857/S0555109922040043
Аннотация
Исследовано выщелачивание цветных металлов из медно-никелевых сульфидных концентратов и медно-никелевого шлака раствором сульфата трехвалентного железа, полученного микробным окислением сульфата двухвалентного железа. Процесс проводили при 80°С, рН 1.15 и концентрации Fe3+ 9.8 г/л. Показано, что основная часть никеля из шлаков выщелачивалась в течение 1.5 ч. При выщелачивании медно-никелевых концентратов в течение 7 ч не была достигнута максимально возможная концентрация цветных металлов. Скорости выщелачивания меди и никеля из шлаков были близкими и достигали 177 и 141 мг/(л ∙ ч) соответственно. Скорости выщелачивания цветных металлов из медно-никелевых концентратов были значительно ниже и составляли от 25 до 39 мг/(л ∙ ч) для никеля и от 14 до 23 мг/(л ∙ ч) для меди. Эффективность выщелачивания медно-никелевых концентратов не зависела от их химического состава, однако извлечение никеля в жидкую фазу было примерно в 4 раза выше извлечения меди. При этом во всех осадках выщелачивания содержание меди повысилось по сравнению с исходными концентратами. Выщелачивание шлаков характеризовалось относительно небольшой продолжительностью, высоким извлечением цветных металлов в жидкую фазу (99%) и низким их содержанием в осадке выщелачивания (0.11–0.14%).
Переработка многих сульфидных полиметаллических руд связана с технологическими трудностями их обогащения флотационными способами, которые не позволяют экономически эффективно получать селективные концентраты цветных металлов [1, 2]. Однако получение коллективных сульфидных концентратов, например, таких как медно-цинковые и медно-никелевые, осуществляется относительно просто и дешево. Непригодные для пирометаллургической переработки, они могут представлять интерес для биогидрометаллургии, основанной на выщелачивании металлов с использованием микроорганизмов [3, 4].
Перспективным направлением является интенсивная биогидрометаллургическая технология переработки коллективных сульфидных концентратов цветных металлов с использованием биораствора трехвалентного железа, полученного с помощью хемолитотрофных микроорганизмов [5, 6]. При этом представляет интерес направление по селективному растворению минералов с низким электродным потенциалом (например, сфалерита) и концентрирование минералов с высоким электродным потенциалом (например, халькопирита) в твердой фазе с получением медного концентрата [7]. Ранее было показано, что из различных медно-цинковых концентратов наиболее эффективно выщелачивался цинк, а медь преимущественно оставалась в осадке, причем, чем выше было содержание халькопирита в концентрате и ниже содержание сфалерита, тем эффективнее цинк переходил в жидкую фазу из сфалерита, а халькопирит концентрировался в осадке выщелачивания [8].
Для развития направления по селективному выщелачиванию и концентрированию цветных металлов представляет интерес сравнение эффективности выщелачивания никеля из пентландита ((Ni,Fe)9S8) и виоларита (FeNi2S4) по сравнению с медью из халькопирита (CuFeS2) в зависимости от соотношения содержания меди и никеля в концентратах.
Кроме того, сырьем для получения цветных металлов, в том числе меди и никеля, с помощью химического выщелачивания биораствором сульфата трехвалентного железа могут являться металлургические шлаки, полученные при переработке сульфидного сырья [9]. В шлаках цветные металлы могут содержаться в свободном виде, а также в виде сульфидов, оксидов и силикатов. Химизм выщелачивания металлургических шлаков с использованием раствора сульфата трехвалентного железа в сернокислой среде может быть описан упрощенными реакциями:
(1)
${\text{C}}{{{\text{u}}}^{0}} + {\text{F}}{{{\text{e}}}_{{\text{2}}}}{{\left( {{\text{S}}{{{\text{O}}}_{{\text{4}}}}} \right)}_{3}} \to {\text{CuS}}{{{\text{O}}}_{4}} + 2{\text{FeS}}{{{\text{O}}}_{4}},$(2)
${\text{MeS}} + {\text{F}}{{{\text{e}}}_{{\text{2}}}}{{\left( {{\text{S}}{{{\text{O}}}_{{\text{4}}}}} \right)}_{3}} \to {\text{MeS}}{{{\text{O}}}_{4}} + 2{\text{FeS}}{{{\text{O}}}_{4}} + {{{\text{S}}}^{0}},$(3)
${\text{M}}{{{\text{e}}}_{{\text{2}}}}{\text{Si}}{{{\text{O}}}_{4}} + 2{{{\text{H}}}_{{\text{2}}}}{\text{S}}{{{\text{O}}}_{4}} \to 2{\text{MeS}}{{{\text{O}}}_{4}} + {{{\text{H}}}_{{\text{4}}}}{\text{Si}}{{{\text{O}}}_{4}}~,$В растворе серной кислоты могут растворяться оксиды меди и никеля:
(4)
$\begin{gathered} {\text{CuO}} \cdot {\text{F}}{{{\text{e}}}_{{\text{2}}}}{{{\text{O}}}_{3}} + 4{{{\text{H}}}_{{\text{2}}}}{\text{S}}{{{\text{O}}}_{4}} \to \\ \to \,\,{\text{CuS}}{{{\text{O}}}_{4}} + {\text{F}}{{{\text{e}}}_{{\text{2}}}}{{\left( {{\text{S}}{{{\text{O}}}_{{\text{4}}}}} \right)}_{3}} + 4{{{\text{H}}}_{{\text{2}}}}{\text{O}}, \\ \end{gathered} $(5)
$\begin{gathered} {\text{NiO}} \cdot {\text{F}}{{{\text{e}}}_{{\text{2}}}}{{{\text{O}}}_{3}} + {\text{4}}{{{\text{H}}}_{{\text{2}}}}{\text{S}}{{{\text{O}}}_{4}} \to \\ \to \,\,{\text{NiS}}{{{\text{O}}}_{4}} + {\text{F}}{{{\text{e}}}_{{\text{2}}}}{{\left( {{\text{S}}{{{\text{O}}}_{{\text{4}}}}} \right)}_{3}} + 4{{{\text{H}}}_{{\text{2}}}}{\text{O}}. \\ \end{gathered} $С целью возможной комбинированной переработки сульфидных концентратов и металлургических шлаков важно провести сравнение скорости выщелачивания цветных металлов из них.
Цель работы – исследование химического выщелачивания медно-никелевых сульфидных концентратов с различным содержанием меди и никеля, а также медно-никелевого шлака и сравнение скорости выщелачивания цветных металлов из них.
МЕТОДИКА
Выщелачиваемый материал. В работе были использованы три пробы медно-никелевых концентратов, полученных при флотационном обогащении сульфидной руды Шанучского рудного поля (Камчатский край, Россия). Медно-никелевый шлак, полученный при металлургической переработке сульфидных руд, также был объектом исследований.
Выщелачивающий раствор. Для приготовления выщелачивающих растворов для высокотемпературного выщелачивания было использовано сообщество ацидофильных хемолитотрофных железоокислителей, включающее бактерии Acidithiobacillus ferrooxidans и Leptospirillum sp. Сообщество было выделено при 30°С из лежалых пиритных отходов обогащения сульфидных руд Гайского горно-обогатительного комбината (Россия). Выщелачивающий раствор был приготовлен путем биоокисления коммерческого реагента соли FeSO4·7H2O при 30°С в среде Сильвермана и Лундгрена 9 К [10]. Исходное число клеток составляло 2 × 107/мл. Культивирование проводили в бутылях на 5 л в течение 48 ч в условиях интенсивной аэрации со скоростью подачи воздуха 4 л/ч. Величину рН на уровне 1.4 в процессе биоокисления поддерживали добавлением 98.5%-ной серной кислоты. Полученный раствор содержал 9.8 г/л Fe3+. Численность микроорганизмов сообщества достигала 5 × 108 кл./мл. Этот раствор разбавляли дистиллированной водой до необходимой концентрации Fe3+ и после добавления 98.5%-ной серной кислоты до pH 1.15 использовали для окислительного высокотемпературного выщелачивания исследуемых продуктов.
Выщелачивание. Опыты проводили в реакторе объемом 500 мл, содержавшем 200 мл суспензии, при перемешивании верхнеприводной четырехлопастной мешалкой (с наклоненными под углом 45° лопастями) с скоростью 500 об./мин. Реактор был погружен в водяную баню для термостатирования при 80°С. Выщелачиваемый материал загружали в таком количестве, чтобы содержание твердой фазы в суспензии составляло 1%. Продолжительность выщелачивания составляла 7 ч для медно-никелевых концентратов и 3 ч для медно-никелевого шлака.
Аналитические методы. Значения рН измеряли с помощью рН-метра рН-150МИ (“Измерительная техника”, Россия). Концентрации Fe3+ и Fe2+ в жидкой фазе определяли титриметрическим методом с трилоном Б [11]. Концентрацию ионов меди и никеля определяли на атомно-абсорбционном спектрометре с пламенной атомизацией 3100 (“Perkin Elmer”, США).
Выход твердой фазы (%) определяли по формуле:
где mос – масса осадка (г) после биовыщелачивания, mисх – масса исходного концентрата (г) в суспензии.Извлечение цветных металлов (%) в раствор определяли по формуле:
где С – концентрация металла в растворе (мг/л), V – объем реакционной смеси (л), βисх – содержание металла в исходном сырье (%).Среднюю скорость выщелачивания меди и никеля (мг/(л · ч)) определяли по формуле:
где τ – время (ч).Удельную скорость выщелачивания цветных металлов (мг/(г · ч)) определяли по формуле:
Статистический анализ. Все эксперименты и измерения проводили в двух повторностях. Статистическую обработку выполняли с помощью программы Microsoft Excel 2013. Достоверность результатов оценивали с помощью t-критерия Стьюдента при уровне значимости p ≤ 0.1.
РЕЗУЛЬТАТЫ И ИХ ОБСУЖДЕНИЕ
Исследование химического и минерального состава сульфидных концентратов показало, что они содержали халькопирит (CuFeS2), пентландит ((Ni,Fe)9S8), виоларит (FeNi2S4), пирротин (Fe1 – xS), пирит (FeS2), а также нерудные минералы – ярозит, плагиоклаз, хлорит, кварц. Основная кристаллическая часть металлургического шлака была представлена фаялитом (Fe2SiO4). Медь присутствовала как в свободном виде (Cu0), так и в составе дигенита (Сu9S5), борнита (Сu5FeS4) и халькопирита (СuFeS2). Никель в шлаке находился в составе серпентина ((Mg,Fe,Ni)3Si2O5(OH)4). Содержание основных элементов в концентратах и шлаке дано в табл. 1.
Таблица 1.
Содержание основных элементов в концентратах и шлаке
Продукт | Содержание, % | k* | ||||
---|---|---|---|---|---|---|
Cu | Ni | Fe | S | Si | ||
Шлак | 2.1 | 2.7 | 16.7 | 1.9 | 17.1 | 0.8 |
Концентрат Sh0 | 10.8 | 7.2 | 21.8 | 26.5 | 7.95 | 1.5 |
Концентрат Sh1 | 15.7 | 7.5 | 21.3 | 29.0 | 5.97 | 2.2 |
Концентрат Sh2 | 19.1 | 4.6 | 21.6 | 30.3 | 5.74 | 4.1 |
В процессе выщелачивания проводили контроль концентрации ионов железа и цветных металлов. Показано, что трехвалентное железо восстанавливалось до двухвалентного, при этом цветные металлы переходили из твердой фазы в жидкую. На рис. 1 представлена динамика изменения концентрации Fe2+ в процессе выщелачивания концентратов и шлака. Из данных следует, что химическое выщелачивание шлака протекало значительно быстрее, чем медно-никелевых концентратов. Так, за 2 ч была достигнута максимальная концентрация ионов Fe2+ и процесс выщелачивания практически завершился. При выщелачивании медно-никелевых концентратов накопление ионов двухвалентного железа продолжалось на протяжении всего процесса (7 ч).
Рис. 1.
Концентрация Fe2+ при выщелачивании медно-никелевых концентратов Sh0 (1), Sh1 (2), Sh2 (3) и медно-никелевого шлака (4).
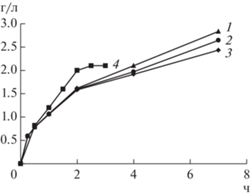
Изменение концентрации цветных металлов в зависимости от времени выщелачивания представлено на рис. 2. Данные свидетельствуют о значительно более высокой скорости изменения концентраций меди и никеля при выщелачивании шлаков. При этом процесс выщелачивания шлаков почти прекращался по прошествии 1.5 ч от начала, так как при этом была зафиксирована максимальная концентрация цветных металлов в жидкой фазе. В случае медно-никелевых концентратов даже за 7 ч не была достигнута максимально возможная концентрация цветных металлов, а концентрация никеля превышала концентрацию меди для всех трех концентратов.
Рис. 2.
Концентрация никеля (1–4) и меди (1'–4') при выщелачивании концентратов Sh0 (1, 1'), Sh1 (2, 2'), Sh2 (3, 3') и шлака (4, 4').

Результаты расчетов скорости выщелачивания цветных металлов представлены на рис. 3. Для шлаков скорости выщелачивания металлов были близкими, достигая 177 и 141 мг/(л ∙ ч) для никеля и меди соответственно. Скорости выщелачивания цветных металлов из медно-никелевых концентратов были значительно ниже. Так, скорость выщелачивания никеля из концентратов Sh0 и Sh1 были близкими – 39 и 37 мг/(л ∙ ч), так как содержание никеля в них было близким. При этом увеличение содержания меди в концентрате Sh1 почти на 5% по сравнению с концентратом Sh0 на скорость выщелачивания никеля влияния не оказывало. Самая низкая скорость выщелачивания никеля наблюдалась для концентрата Sh2 (25 мг/(л ∙ ч)) и была связана с наименьшим содержанием этого металла в концентрате. Скорость выщелачивания меди была значительно ниже, чем скорость выщелачивания никеля – от 14 до 23 мг/(л ∙ ч).
Рис. 3.
Средняя скорость выщелачивания меди и никеля из концентратов Sh0 (1), Sh1 (2), Sh2 (3) и шлака (4).
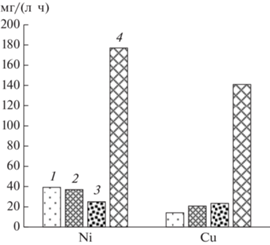
Для сравнения эффективности выщелачивания всех исследованных продуктов были рассчитаны удельные скорости выщелачивания из них цветных металлов (рис. 4). Данные свидетельствуют о том, что удельная скорость выщелачивания никеля из трех концентратов была схожей – 49.3–54.7 мг/(г ∙ ч). При этом скорость выщелачивания меди также различалась незначительно, но была существенно ниже – 14.1–23.5 мг/(г ∙ ч).
Рис. 4.
Средняя удельная скорость выщелачивания меди и никеля из концентратов Sh0 (1), Sh1 (2), Sh2 (3) и шлака (4).
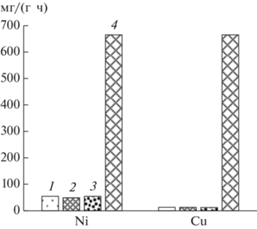
Сравнение процессов выщелачивания меди и никеля из медно-никелевых концентратов и медно-никелевого шлака выявило значительную разницу в удельной скорости выщелачивания цветных металлов. Скорость выщелачивания как никеля, так и меди из шлака достигала 665 мг/(г ∙ ч). Такое высокое значение, очевидно, связано с тем, что основное количество металлов в шлаке присутствовало в свободном виде, а также в составе оксидов, которые относительно быстро растворялись в кислом растворе сульфата трехвалентного железа. Таким образом, удельная скорость выщелачивания никеля из шлака превышала таковую для сульфидных концентратов приблизительно в 13 раз.
На основании рис. 1 расчет средней скорости накопления двухвалентного железа в жидкой фазе в течение 2 ч, которое образовывалось при восстановлении железа в окислительно-восстановительных реакциях, показал, что максимальное ее значение наблюдалось при выщелачивании шлаков и составило 1000 мг/(л ∙ ч). При выщелачивании концентратов Sh0, Sh1 и Sh2 эта скорость была ниже и составила около 790 мг/(л ∙ ч).
Расчет расхода Fe3+, приходящегося на 1 мг выщелоченных суммарно меди и никеля из исследуемых продуктов, показал, что наименьшее значение было получено для шлака – 2.5 мг/мг. Расход Fe3+ при выщелачивании трех проб концентратов был близким по отношению друг к другу и составил около 7.2 мг/мг. Полученные результаты свидетельствуют о том, что в концентратах преобладали сульфидные минералы с высокой энергией кристаллической решетки, окисление которых требовало большего времени окисления и большего расхода окислителя. В шлаках, очевидно, преобладали легкоокислямые компоненты, например, свободные металлы и оксиды. Такие соединения легко окисляются или растворяются в растворах сернокислого трехвалентного железа [12].
По результатам проведенных исследований были рассчитаны основные технологические показатели высокотемпературного химического выщелачивания всех исследованных медно-никелевых продуктов. Результаты исследований представлены в табл. 2. Данные свидетельствуют о том, что выщелачивание шлаков характеризовалось высоким извлечением цветных металлов в жидкую фазу (99%) и получением осадка с очень низким их содержанием (0.11–0.14%). Эффективность выщелачивания медно-никелевых концентратов не зависела от их химического состава, однако извлечение никеля в жидкую фазу было примерно в 4 раза выше извлечения меди. При этом во всех осадках выщелачивания содержание меди повышалось по сравнению с исходными концентратами.
Таблица 2.
Основные результаты исследований высокотемпературного выщелачивания медно-никелевых концентратов и шлака при 80°С, рН 1.15
Продукт | Выход осадка, % | Извлечение, % | Содержание, % | ||
---|---|---|---|---|---|
Ni | Cu | Ni | Cu | ||
Концентрат Sh0 | 76.5 | 39.3 | 10.5 | 5.7 | 11.5 |
Концентрат Sh1 | 75.5 | 39.7 | 9.7 | 6.0 | 18.8 |
Концентрат Sh2 | 76.5 | 38.6 | 9.3 | 3.7 | 22.7 |
Шлак | 77.1 | 99.6 | 99.4 | 0.11 | 0.14 |
Таким образом, показано, что основные закономерности, полученные при выщелачивании медно-цинковых коллективных концентратов, сохранялись и при выщелачивании медно-никелевых концентратов. Медь, находившаяся в них в виде упорного (трудноокисляемого) халькопирита, концентрировалась в твердой фазе. Никель, как и цинк, переходил в жидкую фазу, но из-за более высоких электродных потенциалов никелевых минералов эффективность их выщелачивания была ниже, чем эффективность выщелачивания цинка из сфалерита.
Высокотемпературное выщелачивание медно-никелевого шлака позволило перевести в жидкую фазу медь наравне с никелем, так как оба эти металла находились в этом сырье в более легкоокисляемой и легкорастворимой форме по сравнению с медно-никелевыми концентратами.
Осадок выщелачивания характеризовался низким содержанием цветных металлов и мог считаться отходом. Хранение полученных после выщелачивания отходов, очевидно, не будет оказывать отрицательного влияния на окружающую среду, в то время, как хранение самих шлаков загрязняет почву и воду тяжелыми металлами в местах их складирования.
Список литературы
Черноусенко Е.В., Алексеева С.А., Рухленко Е.Д., Мит-рофанова Г.В. // Горный журн. 2020. № 3. С. 45–50.
Лесникова Л.С, Дациев М.С., Сисина А.Н., Чикильдин Д.Е. // Цветные металлы. 2020. № 6. С. 28–32.
Ahmadi M., Hosseini M.R., Ahmadi A., Foroutan A. // Miner. Eng. 2020. V. 156. № 106529. https://doi.org/10.1016/j.mineng.2020.106529
Abdollahi H., Shafaei S.Z., Noaparast M., Manafi Z., Niemelä S.I., Tuovinen O.H. // Int. J. Miner. Proc. 2014. V. 128. P. 25–32.
Муравьев М.И., Панюшкина А.Е., Меламуд В.С., Булаев А.Г., Фомченко Н.В. // Прикл. биохимия и микробиология. 2021. Т. 57. № 4. С. 380–387.
Carranza F., Palencia I., Romero R. // Hydrometallurgy. 1997. V. 44. № 1–2. P. 29–42.
Фомченко Н.В., Муравьев М.И. // Прикл. биохимия и микробиология. 2017. Т. 53. № 1. С. 82–87.
Fomchenko N.V., Muravyov M.I. // Hydrometallurgy. 2019. V. 185. P. 82–87.
Fomchenko N., Muravyov M. // Minerals. 2020. V. 10. № 12. P. 1097. https://doi.org/10.3390/min10121097
Silverman M.P., Lundgren D.C. // J. Bacteriol. 1959. V. 77. № 5. P. 642–647.
Davis D.G., Jacobsen W.R. // Anal. Chem. 1960. V. 32. № 2. P. 215–217.
Sun J., Zhou W., Zhang L., Cheng H., Wang Y., Tang R., Zhou H. // J. Environ. Manag. 2021. V. 284. № 112133. https://doi.org/10.1016/j.jenvman.2021.112133
Дополнительные материалы отсутствуют.
Инструменты
Прикладная биохимия и микробиология