Прикладная биохимия и микробиология, 2021, T. 57, № 4, стр. 380-387
Химическое выщелачивание коллективных сульфидных концентратов раствором сульфата трехвалентного железа
М. И. Муравьёв 1, *, А. Е. Панюшкина 1, В. С. Меламуд 1, А. Г. Булаев 1, Н. В. Фомченко 1
1 Институт микробиологии им. С.Н. Виноградского, Федеральный исследовательский центр
“Фундаментальные основы биотехнологии” Российской академии наук
119071 Москва, Россия
* E-mail: maxmuravyov@gmail.com
Поступила в редакцию 27.11.2020
После доработки 15.01.2021
Принята к публикации 22.02.2021
Аннотация
Исследовано выщелачивание цветных металлов из медно-цинкового и медно-никелевого сульфидных концентратов раствором сульфата трехвалентного железа, полученным микробным окислением сульфата двухвалентного железа, при разных условиях (температура, плотность пульпы, концентрация окислителя). Установлено, что максимальная концентрация цветных металлов в жидкой фазе была достигнута при 80°С. Показано, что плотность пульпы не оказывала существенного влияния на выщелачивание меди, однако ее повышение от 1 до 3% снижало извлечение цинка и никеля в жидкую фазу. Исследование влияния концентрации окислителя (ионов Fe3+) показало, что при концентрации Fe3+ 10 г/л извлечение цинка и никеля было максимальным. При всех исследованных режимах цинк переходил в жидкую фазу более эффективно, чем никель, однако медь преимущественно концентрировалась в осадке обоих концентратов. Показано, что в осадках выщелачивания содержание цинка снижалось c 7.36 до 0.05%, никеля – c 9.45 до 6.86% при повышении содержания меди в обоих случаях. Предложенный способ селективного выщелачивания минералов из коллективных концентратов может рассматриваться как одна из стадий повышения качества сульфидных концентратов.
Переработка многих сульфидных полиметаллических руд связана с технологическими трудностями их разделения на кондиционные индивидуальные концентраты в процессе обогащения, что обусловлено как флотационными свойствами самих минералов руды, так и морфологическими особенностями их строения (срастанием друг с другом, вкрапленностью и др.). Наиболее распространенные флотационные методы обогащения руд позволяют эффективно и с высокой скоростью получать коллективные сульфидные концентраты, такие как медно-цинковые и медно-никелевые [1, 2]. Непригодные для пирометаллургической переработки, они могут представлять интерес для биогидрометаллургии, основанной на выщелачивании металлов с использованием микроорганизмов [3–5]. Наибольшее применение в промышленности нашло использование сообществ ацидофильных хемолитотрофных микроорганизмов, способных окислять двухвалентное железо и восстановленные соединения серы, для извлечения меди из руд вторичных сульфидов, а также золота из пиритно-арсенопиритных руд [6]. Это обусловлено относительно быстрым и полным растворением минералов группы халькозина в кислых растворах трехвалентного железа в первом случае и высокой стоимостью золота – во втором.
Наиболее распространенный сульфидный минерал меди – халькопирит (CuFeS2) – характеризуется устойчивостью в растворах сернокислого трехвалентного железа в том числе в процессах биовыщелачивания, вызванной как образованием продуктов реакции (элементарная сера, ярозит) на поверхности частиц, препятствующих доступу окислителя в зону реакции, так и электрохимическими характеристиками самого минерала [7, 8]. Попытки коммерческого использования биогидрометаллургии для переработки сырья, содержащего халькопирит, в биореакторах не увенчались успехом в связи с высокими эксплуатационными расходами, необходимыми для обеспечения активности термофильного микробного сообщества [9].
Известно, что окисление смеси сульфидных минералов обуславливается в том числе их гальваническим взаимодействием. При этом в большей степени растворяется минерал, обладающий меньшим значением электродного потенциала (рис. 1) [10].
На основании этого для получения кондиционного для пирометаллургии монометаллического концентрата представляет интерес селективное выщелачивание минералов из коллективных сульфидных концентратов. Одними из перспективных для такой переработки могут быть халькопирит-сфалеритовые и халькопирит-пентландит-виоларитовые концентраты для удаления из них цинка и никеля соответственно и получения качественного медного концентрата.
Выщелачивание металлов при окислении сфалерита (ZnS), халькопирита (CuFeS2), пентландита (Ni,Fe)9S8 и виоларита (FeNi2S4) можно выразить в виде следующих упрощенных уравнений:
(1)
${\text{ZnS}} + 2{\text{F}}{{{\text{e}}}^{{3 + }}} = {\text{Z}}{{{\text{n}}}^{{2 + }}} + {{{\text{S}}}^{0}} + 2{\text{F}}{{{\text{e}}}^{{2 + }}},$(2)
${\text{CuFe}}{{{\text{S}}}_{2}} + 4{\text{F}}{{{\text{e}}}^{{3 + }}} = {\text{C}}{{{\text{u}}}^{{2 + }}} + 2{{{\text{S}}}^{0}} + 5{\text{F}}{{{\text{e}}}^{{2 + }}},$(3)
$2{{\left( {{\text{Ni,Fe}}} \right)}_{9}}{{{\text{S}}}_{8}} + 36{\text{F}}{{{\text{e}}}^{{3 + }}} = 9{\text{N}}{{{\text{i}}}^{{2 + }}} + 16{{{\text{S}}}^{0}} + 45{\text{F}}{{{\text{e}}}^{{2 + }}},$(4)
$\begin{gathered} {\text{FeN}}{{{\text{i}}}_{{\text{2}}}}{{{\text{S}}}_{4}} + 18{\text{F}}{{{\text{e}}}^{{3 + }}} + 8{{{\text{H}}}_{{\text{2}}}}{\text{O}} = \\ = \,\,2{\text{N}}{{{\text{i}}}^{{2 + }}} + 2{\text{SO}}_{4}^{{2 - }} + 2{{{\text{S}}}^{0}} + 19{\text{F}}{{{\text{e}}}^{{2 + }}} + 16{{{\text{H}}}^{ + }}. \\ \end{gathered} $Разрушение кристаллической решетки сульфидных минералов протекает за счет их химического взаимодействия с ионами трехвалентного железа в сернокислой среде. Известно, что скорость химических реакций повышается с увеличением температуры. Кроме того, на нее могут влиять основные технологические параметры процесса – плотность пульпы, концентрация окислителя (Fe3+) и др. [11], поэтому представляет интерес сравнение скорости и эффективности селективного выщелачивания цинка и никеля из медно-цинкового и медно-никелевого некондиционных сульфидных концентратов растворами сульфата трехвалентного железа в различных условиях. В предыдущих работах было показано, что процесс выщелачивания может эффективно осуществляться с помощью растворов сульфата трехвалентного железа, полученного микробным окислением [12, 13].
Цель работы − определение эффективности выщелачивания цветных металлов из медно-цинкового и медно-никелевого некондиционных сульфидных концентратов с помощью раствора сульфата трехвалентного железа, полученного с помощью биоокисления, в зависимости от параметров процесса.
МЕТОДИКА
Концентраты. Объектами исследований являлись медно-цинковый сульфидный концентрат руды Тарньерского месторождения (Свердловская область, Россия), а также медно-никелевый сульфидный концентрат руды месторождения Шануч (Камчатский край, Россия). Медно-цинковый концентрат содержал следующие сульфидные минералы: халькопирит, сфалерит, пирротин (Fe1 –xS), пирит (FeS2) и молибденит (MoS2). Нерудные минералы были представлены ярозитом, а также глинистыми разновидностями – иллитом, хлоритом и каолинитом. Медно-никелевый концентрат содержал халькопирит, пентландит, виоларит, пирротин, пирит, а также нерудные минералы – ярозит, плагиоклаз, хлорит, кварц. Содержание основных элементов и сульфидных минералов в концентратах представлено в табл. 1 и 2 соответственно.
Таблица 1.
Содержание основных элементов в концентратах
Концентрат | Содержание, % | |||||||
---|---|---|---|---|---|---|---|---|
Cu | Zn | Ni | Fe | Со | S | Ca | Si | |
Медно-цинковый | 10.1 | 7.36 | – | 36.1 | – | 34.5 | 0.1 | 1.77 |
Медно-никелевый | 10.9 | – | 9.45 | 21.3 | 0.25 | 26.8 | 0.91 | 7.28 |
Таблица 2.
Содержание основных сульфидных минералов в концентратах
Концентрат | Содержание, % | |||||
---|---|---|---|---|---|---|
CuFeS2 | ZnS | Fe1 – xS | FeS2 | (Ni,Fe)9S8 | FeNi2S4 | |
Медно-цинковый | 29 | 11 | 34 | 13 | 0 | 0 |
Медно-никелевый | 31 | <0.5 | 4 | 4 | 15 | 11 |
Выщелачивающий раствор. Для приготовления выщелачивающих растворов для высокотемпературного выщелачивания была использована смешанная культура ацидофильных хемолитотрофных железоокислителей, включающая бактерии Acidithiobacillus ferrooxidans и Leptospirillum sp. Культура была выделена при 30°С из лежалых пиритных отходов обогащения сульфидных руд Гайского горно-обогатительного комбината (Оренбургская область, Россия). Выщелачивающий раствор был приготовлен путем биоокисления коммерческого реагента соли FeSO4 × 7H2O при 30°С в среде Сильвермана и Лундгрена 9К [14]. Величину рН на уровне 1.4 в процессе биоокисления поддерживали добавлением 98.5%-ной серной кислоты. Полученный раствор содержал 20 г/л Fe3+. Этот раствор, либо растворы, полученные его разбавлением дистиллированной водой до необходимой концентрации Fe3+, после добавления 98.5%-ной серной кислоты до pH 1.15 были использованы для окислительного высокотемпературного выщелачивания исследуемых концентратов.
Выщелачивание. Опыты проводили в реакторе объемом 500 мл, содержащем 200 мл суспензии, при перемешивании верхнеприводной четырехлопастной мешалкой (с наклоненными под углом 45° лопастями) с частотой 500 об./мин. Реактор был погружен в водяную баню для термостатирования на заданном уровне. Продолжительность выщелачивания составляла 5 ч.
Аналитические методы. Значения рН измеряли с помощью рН-метра рН-150МИ (“Измерительная техника”, Россия). Концентрации Fe3+ и Fe2+ в жидкой фазе определяли титриметрическим методом с трилоном Б [15]. Концентрацию ионов меди, цинка и никеля определяли на атомно-абсорбционном спектрометре с пламенной атомизацией 3100 (“Perkin Elmer”, США).
Выход твердой фазы (%) определяли по формуле:
где mос – масса осадка (г) после биовыщелачивания, mисх – масса исходного концентрата (г) в выщелачиваемой суспензии.Извлечение цветных металлов (%) в раствор определяли по формуле:
где βос и βисх – содержание металла в осадке биовыщелачивания и исходном концентрате соответственно (%).Скорость выщелачивания цветных металлов (г/(г·ч)) определяли по формуле:
где τ – продолжительность выщелачивания (ч).РЕЗУЛЬТАТЫ И ИХ ОБСУЖДЕНИЕ
Влияние температуры. Исследования по влиянию температуры на выщелачивание металлов из концентратов проводили при плотности пульпы 1%, рН 1.15 и начальной концентрации ионов Fe3+ 10.0 г/л. Результаты выщелачивания медно-цинкового и медно-никелевого концентратов при 50, 65 и 80°С представлены на рис. 2 и 3 соответственно.
Рис. 2.
Концентрация цинка (1–3) и меди (4–6) в жидкой фазе при выщелачивании медно-цинкового концентрата при 50 (1, 4), 65 (2, 5) и 80°C (3, 6), содержании твердой фазы в суспензии 1%, начальной концентрации Fe3+ 10 г/л и pH 1.15.

Из данных рис. 2 следует, что скорость повышения концентрации цветных металлов в жидкой фазе значительно зависела от температуры, причем максимальная концентрация цинка была достигнута при 80°С и составила 731 мг/л, а меди – 261 мг/л. При этих же условиях (рис. 3) максимальная концентрация никеля составила 400 мг/л, а меди – 107 мг/л.
Анализ снижения концентрации ионов Fe3+ в результате взаимодействия с минералами показал, что при выщелачивании медно-цинкового концентрата при 50°C концентрация ионов Fe3+ в жидкой фазе снижалась с 10.0 до 7.25 г/л, при 65°С – до 6.23 г/л, а при 80°С – до 4.76 г/л. При выщелачивании медно-никелевого концентрата остаточная концентрация Fe3+ составила 8.46, 8.36 и 7.56 г/л соответственно. Эти данные свидетельствовали о том, что более активное выщелачивание цветного металла (цинка) связано с более активным восстановлением ионов Fe3+, то есть снижением его концентрации в процессе выщелачивания.
Следует отметить, что медь находилась в составе минерала халькопирита в обоих концентратах и содержание ее было сходным. Однако из медно-цинкового концентрата она выщелачивалась лучше, чем из медно-никелевого, что может быть объяснено как различием свойств халькопирита в разных концентратах, так и гальваническим взаимодействием между минералами, образующих в том числе пару халькопирит-пирит для медно-цинкового концентрата и халькопирит-пирротин/пентландит для медно-никелевого концентрата. Так как с повышением температуры эффективность выщелачивания увеличивалась, все последующие опыты были проведены при 80°C.
Влияние содержания твердой фазы в суспензии. Исследования по влиянию плотности пульпы на выщелачивание металлов из концентратов проводили при 80°С, рН 1.15, концентрации ионов Fe3+ 10.0 г/л и плотности пульпы 1 и 3%. Результаты выщелачивания представлены на рис. 4 и 5.
Рис. 3.
Концентрация никеля (1–3) и меди (4–6) в жидкой фазе при выщелачивании медно-никелевого концентрата при 50 (1, 4), 65 (2, 5) и 80°C (3, 6), содержании твердой фазы в суспензии 1%, начальной концентрации Fe3+ 10 г/л и pH 1.15.
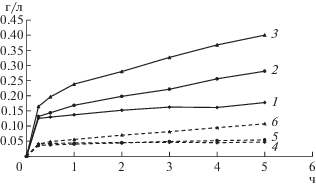
Рис. 4.
Извлечение цинка (1, 1'), меди (2, 2') (а) и концентрация Fe3+ (3, 3') в жидкой фазе (б) при выщелачивании медно-цинкового концентрата и содержании твердой фазы в суспензии 1% (1, 2, 3) и 3% (1', 2', 3') при 80°С и начальной концентрации Fe3+ 10 г/л, pH 1.15.
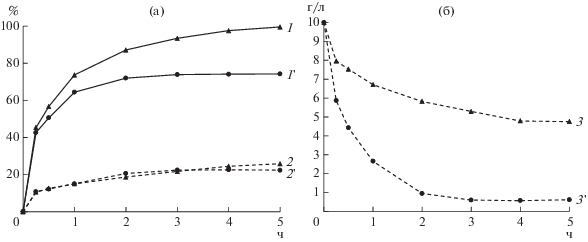
Из рис. 4 следует, что при плотности 1% концентрация ионов трехвалентного железа снижалась ~ на 50%, а извлечение цинка при этом достигало 99.5%. При плотности 3% основное количество железа потреблялось за 2 ч, поэтому за оставшиеся 3 ч извлечение цинка не возрастало и оставалось на уровне 74.2%. Следует отметить, что на извлечение меди плотность пульпы не оказывала существенного влияния и оно составило 22.4–25.8%.
Из рис. 5 следует, что при плотности 1% концентрация ионов трехвалентного железа снижалась почти на 25%, а извлечение никеля при этом составило 42.4%. Повышение плотности твердой фазы до 3% увеличивало потребление ионов Fe3+ более чем в 2 раза, но извлечение никеля снижалось на 12.6% и составило 29.8%. На извлечение меди плотность суспензии не оказывала влияния, и оно оставалось низким (7.5–9.8%). Выход осадка выщелачивания не зависел от плотности пульпы и составил для медно-цинкового концентрата 73.5% при плотности пульпы 1% и 75.0% – при 3%, а для медно-никелевого 79.5 и 82.5% соответственно.
Влияние концентрации окислителя в выщелачивающем растворе. Для проведения исследований были выбраны следующие концентрации ионов трехвалентного железа в выщелачивающем растворе: 5, 10 и 20 г/л при плотности пульпы 1% и выщелачивании при 80°С и рН 1.15. На рис. 6 приведена динамика изменения концентрации цинка и меди при выщелачивании медно-цинкового концентрата, а на рис. 7 – никеля и меди при выщелачивании медно-никелевого концентрата при различных концентрациях ионов Fe3+.
Рис. 5.
Извлечение никеля (1, 1') и меди (2, 2') (а) и концентрация Fe3+ (3, 3') в жидкой фазе (б) при выщелачивании медно-цинкового концентрата при содержании твердой фазы в суспензии 1% (1, 2, 3) и 3% (1', 2', 3') 80°С, начальной концентрации Fe3+ 10 г/л, pH 1.15.
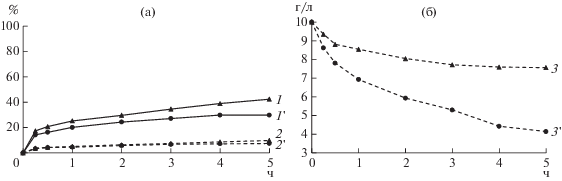
Рис. 6.
Концентрация цинка (1–3) и меди (4–6) в жидкой фазе при выщелачивании медно-цинкового концентрата при начальной концентрации Fe3+ 5 (1, 4), 10 (2, 5) и 20 г/л (3, 6) 80°С, содержании твердой фазы в суспензии 1%, pH 1.15.
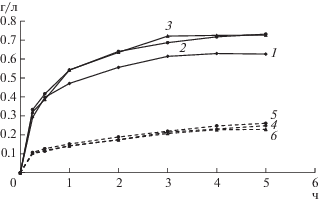
Из рис. 6 и 7 следует, что концентрация трехвалентного железа не оказывала влияния на выщелачивание меди как из медно-цинкового, так и из медно-никелевого концентратов. Выщелачивание цинка было сходным при концентрации трехвалентного железа 10 и 20 г/л и снижалось при снижении концентрации железа до 5 г/л. Выщелачивание никеля из медно-никелевого концентрата было максимальным при использовании выщелачивающего раствора, содержащего 10 г/л трехвалентного железа.
Извлечение металлов и выход осадка при выщелачивании концентратов при различной концентрации окислителя представлены в табл. 3. Из данных следует, что повышение концентрации окислителя Fe3+ от 10 до 20 г/л приводило к значительному повышению выхода осадка выщелачивания – на четверть для обоих концентратов, что свидетельствовало о выпадении осадка трехвалентного железа (очевидно, в виде труднорастворимого ярозита) и приводило к потере его качества.
Таблица 3.
Основные результаты исследований высокотемпературного выщелачивания медно-никелевого и медно-цинкового концентратов при 80°С, рН 1.15
Концентрация Fe3+, г/л | Медно-цинковый концентрат | Медно-никелевый концентрат | ||||
---|---|---|---|---|---|---|
выход осадка, % | извлечение, % | выход осадка, % | извлечение, % | |||
Zn | Cu | Ni | Cu | |||
5 | 64.5 | 85.2 | 24.5 | 76.0 | 35.4 | 8.1 |
10 | 73.5 | 99.5 | 25.8 | 79.5 | 42.4 | 9.8 |
20 | 102 | 98.9 | 22.6 | 105.0 | 38.2 | 7.5 |
Таким образом, оптимальной концентрацией окислителя была концентрация Fe3+ в выщелачивающем растворе, равная 10 г/л.
Анализ результатов показал, что выщелачивание цинка из медно-цинкового концентрата было значительно эффективнее выщелачивания никеля из медно-никелевого за то же время. Однако стоит отметить, что эффект селективного выщелачивания никеля из никелевых минералов по сравнению с медью из медных минералов подтвердился и для медно-никелевого концентрата.
Рис. 7.
Концентрация никеля (1–3) и меди (4–6) в жидкой фазе при выщелачивании медно-никелевого концентрата при начальной концентрации Fe3+ 5 (1, 4), 10 (2, 5) и 20 г/л (3, 6), 80°С, содержании твердой фазы в суспензии 1%, pH 1.15.
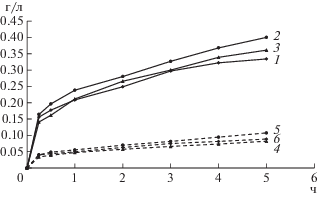
Максимальное извлечение как цинка из медно-цинкового концентрата (99.5%), так и никеля из медно-никелевого концентрата (42.4%) наблюдалось при следующих условиях: 10 г/л Fe3+ в выщелачивающем растворе, 80°С и плотность пульпы 1%. При этом извлечение меди оставалось относительно низким и составляло 25.8 и 9.8% соответственно. Большее извлечение меди при выщелачивании медно-цинкового концентрата могло быть связано как с различными физико-химическими характеристиками халькопирита из разных месторождений, так и наличием кратно большего количества пирита. Например, ранее были показаны различия в эффективности окисления пирита разных месторождений культурами ацидофильных микроорганизмов, различавшегося, по мнению авторов, физическими, химическими и электрофизическими характеристиками [16, 17]. Во многих исследованиях было показано увеличение интенсивности окисления халькопирита при добавлении пирита, что в результате привело к разработке промышленного процесса Galvanox® [18]. Ранее также было показано увеличение скорости (био)выщелачивания сфалерита при увеличении доли халькопирита в сульфидном концентрате [19–21].
В табл. 4 представлена средняя скорость выщелачивания меди, цинка и никеля из сульфидного сырья, содержащего сфалерит, халькопирит и/или виоларит/пентландит, полученная в исследованиях различных авторов. Из табл. 4 видно, что средняя скорость выщелачивания цинка находилась преимущественно в диапазоне 0.19–0.36 г/(г ∙ ч) в зависимости от условий опыта. Низкая средняя скорость выщелачивания цинка, полученная в работе [24], связана с большой длительностью процесса (10 ч) с целью выщелачивания халькопирита и достижения почти полного выщелачивания сфалерита задолго до его окончания. Выщелачивание никеля из пентландит/виоларитового сырья протекало со значительно меньшей скоростью – 0.052–0.085 г/(г ∙ ч), что, вероятно, объяснялось образованием слоя элементарной серы на поверхности минералов, препятствующего доступу окислителя [26]. Низкая скорость выщелачивания никеля в исследовании [27] связана с проведением опыта в колбах на роторной качалке, массообменные характеристики которых существенно хуже по сравнению с таковыми в реакторах с механическим перемешиванием. Средняя скорость выщелачивания меди из халькопирита составляла 0.023–0.067 г/(г ⋅ ч), при этом во всех исследованиях наблюдалось сильное замедление выщелачивания меди со временем за счет пассивации поверхности минерала. Анализ скорости выщелачивания цветных металлов из сульфидного сырья показал перспективность селективного удаления сфалерита из халькопирит-сфалеритовых концентратов при выщелачивании в растворе сульфата трехвалентного железа. Использование предложенного способа удаления никеля из медно-никелевого сульфидного сырья сдерживается низкой скоростью выщелачивания никеля и может быть перспективным для медного сульфидного сырья с низким содержанием никеля.
Таблица 4.
Средняя скорость выщелачивания цветных металлов из сульфидного сырья в растворах сульфата трехвалентного железа в реакторе в периодическом режиме
Выщелачиваемый материал (содержание, %) | Средняя скорость выщелачивания, г/(г ∙ ч) | Условия опыта | Источник | ||
---|---|---|---|---|---|
Zn | Ni | Cu | |||
Сфалерит-халькопиритовый концентрат (Zn 7.36, Cu 10.1, Fe 36.1) | 0.20 | – | 0.051 | 80°С, 10 г/л Fe3+, 1% твердой фазы, pH 1.3, 500 об/мин, 5 ч |
Настоящее исследование |
Халькопирит-сфалеритовый концентрат (Zn 17.0, Cu 14.8, Fe 26.9) | 0.19 | – | 0.040 | 80°С, 12 г/л Fe3+, 1% твердой фазы, pH 1.25, 800 об/мин, 5 ч |
[22] |
Халькопирит-содержащий сфалеритовый концентрат (Zn 42.8, Cu 2.1, Fe 9.9) | 0.36 | – | 0.067 | 80°С, 28 г/л Fe3+, 5% твердой фазы, 0.5M H2SO4, 350 об/мин, 2.7 ч |
[23] |
Сфалерит-содержащий халькопиритовый концентрат (Zn 2.8, Cu 22.2, Fe 30.9) | 0.10 | – | 0.030 | 80°С, 12 г/л Fe3+, 1% твердой фазы, pH 1.25, 800 об/мин, 10 ч |
[24] |
Сфалерит-халькопиритовый концентрат (Zn 8.47, Cu 4.92, Fe 34.6) | 0.25 | – | – | 80°С, 10 г/л Fe3+, 2% твердой фазы, pH 1.25, 600 об/мин, 3.3 ч |
[25] |
Пентландит-виоларит-халькопиритовый концентрат (Ni 9.45, Cu 10.9, Fe 21.3) | – | 0.085 | 0.023 | 80°С, 10 г/л Fe3+, 1% твердой фазы, pH 1.3, 500 об/мин, 5 ч |
Настоящее исследование |
Пирротиновые хвосты флотации (Ni 1.0, Cu 0.2, Fe 42.5) | – | 0.052 | – | 80°С, 10 г/л Fe3+, 0.5% твердой фазы, pH 0.65, 600 об/мин, 10 ч |
[26] |
Пентландитовый концентрат (Ni 30.6, Cu 0.5, Fe 32.3) | – | 0.025 | – | 80°С, 14 г/л Fe3+, 10% твердой фазы, 2M H+, в колбах при 400 об/мин, 4 ч |
[27] |
По уравнениям химических реакций (1–4) был рассчитан стехиометрический расход трехвалентного железа на окисление всех сульфидных минералов цветных металлов (учитывая степень их окисления), находящихся в концентратах. Расчеты показали, что для медно-цинкового концентрата этот расход составил 6.5 г/л, а для медно-никелевого – 2.75 г/л, тогда как фактический расход составил 5.25 и 2.44 г/л соответственно. Небольшая разница между теоретическим и фактическим значениями в обоих случаях свидетельствовала о частичном кислотном растворении сульфидных минералов (видимо, преимущественно пирротина [28, 29]) и об отсутствии интенсивного образования ярозита, приводящего к связыванию ионов трехвалентного железа.
Расчеты показали, что осадок выщелачивания медно-цинкового концентрата содержал 0.05% цинка и 10.2% меди. Осадок, полученный после выщелачивания медно-никелевого концентрата содержал 12.4% меди и 6.86% никеля. Таким образом, количество меди в нем повышалось на 1.47%, а никеля снижалось на 2.59% по сравнению с исходным концентратом.
Таким образом, показано, что основные закономерности, полученные при выщелачивании медно-цинкового концентрата, сохранялись и при выщелачивании медно-никелевого концентрата. Никель, как и цинк, преимущественно переходил в раствор, а медь концентрировалась в твердой фазе. Однако из-за большей стойкости пентландита в сернокислых растворах трехвалентного железа по сравнению со сфалеритом эффективность выщелачивания никеля была ниже, чем цинка.
Список литературы
Алгебраистова Н.К., Маркова А.С., Прокопьев И.В., Развязная А.В. // Горный информационно-аналитический бюллетень (научно-технический журн.). 2016. № 1. С. 187–195.
Абрамов А.А. Флотационные методы обогащения: учебник для вузов. М.: Издательство “Горная книга”, 2016. 595 с.
Brierley C., Brierley J. // Appl. Microbiol. Biotechnol. 2013. V. 97. № 17. P. 7543–7552.
Olson G., Brierley J., Brierley C. // Appl. Microbiol. Biotechnol. 2003. V. 63. № 3. P. 249–257.
Fomchenko N., Muravyov M. // Hydrometallurgy. 2017. V. 174. P. 116–122.
Mahmoud A., Cezac P., Hoadley A.F.A., Contamine F., D’Hugues P. // Int. Biodeter. Biodegr. 2017. V. 119. P. 118–146.
O'Connor G., Eksteen J. // Minerals Engineering. 2020. 154. № 106401.
Zhao H., Zhang Y., Zhang X., Qian L., Sun M., Yang Y., Wang J., Kim H., Qiu G. // Minerals Engineering. 2019. V. 136. P. 140–154.
Batty J., Rorke G. // Hydrometallurgy. 2006. V. 83. № 1–4. P. 83–89.
Riekkola-Vanhanen M., Heimala, S. // International Biohydrometallurgy Symposium. Proceed. V. 1. Jackson Hole: TMS, 1993. P. 561–570.
Levenspiel O. Chemical Reaction Engineering. 2nd Ed. N.Y.: Wiley, 1972. 578 p.
Муравьёв М.И., Фомченко Н.В. // Прикл. биохимия и микробиология. 2019. Т. 55. № 4. С. 396–402.
Фомченко Н.В., Муравьёв М.И. // Прикл. биохимия и микробиология. 2017. Т. 53. № 1. С. 82–87.
Silverman M.P., Lundgren D.G. // J. Bacteriol. 1959. V. 77. № 5. P. 642–647.
Davis D.G., Jacobsen W.R. // Anal. Chem. 1960. V. 32. № 2. P. 215–217.
Tupikina O., Kondrat’eva T., Samorukova V., Rassulov V., Karavaiko G. // Hydrometallurgy. 2006. V. 83. № 1–4. P. 255–262.
Тупикина О.В., Саморукова В.Д., Кондратьева Т.Ф. // Микробиология. 2009. Т. 78. № 2. С. 202–212.
Dixon D., Mayne D., Baxter K. // Can. Met. Q. 2008. V. 47. № 3. P. 327–336.
Fomchenko N., Uvarova T., Muravyov M. // Minerals Engineering. 2019. V. 138. P. 1–6.
Fomchenko N., Muravyov M. // Hydrometallurgy. 2019. V. 185. P. 82–87.
Фомченко Н.В., Муравьёв М.И. // Прикл. биохимия и микробиология. 2020. Т. 56. № 4. С. 366–372.
Carranza F., Palencia I., Romero R. // Hydrometallurgy. 1997. V. 44. № 1–2. P. 29–42.
Santos S.M.C., Machado R.M., Correia M.J.N., Reis M.T.A., Ismael M.R.C., Carvalho J.M.R. // Miner. Eng. 2010. V. 23. № 8. P. 606–615.
Carranza F., Iglesias N., Mazuelos A., Palencia I., Romero R. // Hydrometallurgy. 2004. V. 71. № 3–4. P. 413–420.
Lorenzo–Tallafigo J., Iglesias–Gonzalez N., Romero R., Mazuelos A., Carranza F. // Minerals Engineering. 2018. V. 125. P. 50–59.
Garg S., Judd K., Mahadevan R., Edwards E., Papangelakis V. // Can. Met. Q. 2017. V. 56. № 4. P. 372–381.
Corrans I.J., Scholtz M.T. // J. South African Inst. Min. Met. 1976. № 10. P. 403–411.
Wang H. // Miner. Proc. Extr. Met. Rev. 2007. V. 29. № 1. P. 1–41.
Zhang Y., Zhao H., Qian L., Sun M., Lv X., Zhang L., Petersen J., Qiu G. // Minerals Engineering. 2020. V. 158. № 106586.https://doi.org/10.1016/j.mineng.2020.106586
Дополнительные материалы отсутствуют.
Инструменты
Прикладная биохимия и микробиология