Проблемы машиностроения и надежности машин, 2023, № 2, стр. 34-43
Определение влияния скорости скольжения на контактное трение при осадке с кручением
П. А. Петров 1, *, И. А. Бурлаков 1, 2, Ю. А. Гладков 3, А. А. Гартвиг 3, Т. Х. Нгуен 1
1 Московский политехнический университет
Москва, Россия
2 Производственный комплекс “Салют” АО “ОДК”
Москва, Россия
3 ООО “КванторФорм”
Москва, Россия
* E-mail: petrov_p@mail.ru
Поступила в редакцию 04.01.2022
После доработки 29.10.2022
Принята к публикации 20.12.2022
- EDN: COTVDB
- DOI: 10.31857/S0235711923020062
Аннотация
Метод конечных элементов является прогрессивным инструментом для разработки и оптимизации технологических режимов обработки металлов давлением. Однако для получения корректных результатов моделирования необходимо максимально точно задать граничные условия. В настоящее время в расчетных программах, как правило, используются законы трения, не учитывающие скорость скольжения. Как показывают многочисленные исследования значительное влияние на процесс формообразования при обработке давлением, при определенных условиях течения деформируемого материала на границе “инструмент–заготовка”, оказывает скорость скольжения деформируемого металла по поверхности инструмента. В настоящей статье приведены результаты экспериментов и расчетов связанные с изучением влияния контактного трения на параметры процесса осадки с кручением.
В работах исследователей [1–10] отмечается, что многие процессы обработки давлением требуют знания трибологических характеристик (износ и стойкость инструмента) на поверхности контакта инструмента с пластически деформируемой заготовкой. Наиболее существенное влияние на трибологические характеристики оказывают такие параметры, как контактное давление [9, 10], скорость скольжения по поверхности контакта [6, 9, 10], шероховатость контактной поверхности [2, 7, 11], наличие технологической смазки и ее фактор трения [2–5], температура контактной поверхности [8, 12] и др. Авторами работы [7, 8] отмечается, что при относительно низкой скорости деформируемого материала вдоль границы “инструмент–заготовка”, контактное давление на формообразующей поверхности увеличивается; как следствие, увеличивается контактное трение, что вызывает появление абразивного износа штампового инструмента [7]. С другой стороны, снижение контактного трения на границе “инструмент–заготовка” возможно за счет уменьшения шероховатости формообразующей поверхности либо увеличения толщины слоя технологической смазки/покрытия [8]. Влияние температуры контактной поверхности [8, 12] определяет текущее значение напряжения текучести деформируемого материала, а, следовательно, значение касательного напряжения на его контактной поверхности с деформирующим инструментом. В работе [13] проведен детальный анализ факторов, влияющих на эффекты, происходящие на границе “инструмент–заготовка” и показано, что необходимо как можно более точно описать контактное трение при выполнении численных расчетов.
Наиболее существенное влияние рассмотренных параметров проявляется в тех процессах обработки давлением, в которых площадь контакта между инструментом и заготовкой увеличивается по мере формообразования при пластической деформации. К таким процессам, в частности, относится малоизученный процесс осадки с кручением с точки зрения влияния на течение материала и технологические параметры контактного трения, теплопереноса на контактной поверхности и ее шероховатости.
Осадка с кручением является одним из перспективных процессов изготовления тонкостенных заготовок с изотропными свойствами, изучению которых посвящен ряд работ [14, 15]. Его особенностью является значительное различие в скорости скольжения металла по поверхности вращающегося инструмента, которая увеличивается от нуля в центре вращения заготовки до максимума на периферии, при заданных геометрических размерах. Существенную роль в процессе осадки с кручением играет контактное трение на границе “инструмент–заготовка”.
Метод конечных элементов дает возможность оптимизировать процессы формообразования, в том числе осадку с кручением. Учитывая, что граничные условия в зоне контакта заготовки и инструмента (модель контактного трения) оказывают значительное влияние на характер течения металла, важно задать корректный закон трения для точного математического моделирования процесса. Без правильного задания граничных условий и, соответственно, определения напряжений на инструменте невозможно осуществить достоверное моделирование формообразующего процесса, что возможно при правильном вычислении касательных напряжений в каждой точке контакта заготовки с инструментом. Обычно, в расчетных программах применяют расчет касательных напряжений трения, основанный на законах Кулона–Амонтона, Зибеля или Леванова. Однако скорость скольжения металла по поверхности инструмента существенно влияет на касательные напряжения в зоне контакта заготовки с инструментом [1], что учитывается в расчетах (моделировании) за счет модели контактного трения. Как показали наши исследования, имеет место существенное различие экспериментальных данных и результатов моделирования, как по силе процесса формообразования, так и по температуре при назначении при моделировании процесса осадки с кручением фактора трения постоянной величины. Ряд исследователей [16–21] считают, что для точного моделирования процесса формообразования заготовок необходимо максимально точно учитывать напряжение на границе контакта “инструмент–заготовка”. В частности, было установлено, чем выше скорость скольжения металла, тем меньше влияние контактного трения [5]. Для определения величины контактного касательного напряжения τR, основываясь на работах Аласти и Ноймайер [16, 17, 19], Б.А. Беренс [5] предложил следующее уравнение (IFUM friction model):
(1)
${{\tau }_{R}}\, = \,\left[ {0.3\left( {1 - \frac{{{{\sigma }_{{{\text{eq}}}}}}}{{{{\sigma }_{s}}}}} \right){{\sigma }_{n}}\, + \,mk\frac{{{{\sigma }_{{{\text{eq}}}}}}}{{{{\sigma }_{s}}}}\left( {1\, - \,\exp \frac{{ - \left| {{{\sigma }_{n}}} \right|}}{{{{\sigma }_{s}}}}} \right)} \right]f({{\nu }_{{{\text{rel}}}}}),$Формула (1) представляет собой модель контактного трения. В этой формуле влияние скорости скольжения металла определяется уравнением, оценивающим величину потерь за счет проскальзывания на контактной поверхности
(2)
$f({{\nu }_{{{\text{rel}}}}}) = \exp \frac{{ - 1}}{2}{{\left( {\frac{{f({{\nu }_{{{\text{rel}}}}})}}{C}} \right)}^{2}},$В уравнении (2) эмпирический коэффициент С отражает зависимость контактного трения на границе “инструмент–заготовка” и скоростью проскальзывания (рис. 1). С увеличением значения эмпирического коэффициента С уменьшается влияние скорости скольжения на касательное напряжение скольжения.
Рис. 1.
Влияние коэффициента С на снижение контактного трения: 1 – C = 1; 2 – C = 15; 3 – C = 30; 4 – C = 50; 5 – C = 150.

Учитывая, что при переходе в пластическое состояние σeq/σs = 1, уравнение (1) примет вид
(3)
${{\tau }_{k}} = mk\left( {1 - {{e}^{{\frac{{ - \left| {{{\sigma }_{n}}} \right|}}{{{{\sigma }_{S}}}}}}}} \right){{e}^{{ - 0.5{{{\left( {\frac{{{{{v}}_{{{\text{rel}}}}}}}{C}} \right)}}^{2}}}}},$Методика выполнения работы. Напряжения σn и σs рассчитывались в процессе моделирования осадки с кручением медного сплава БрХ08 с использованием определенной нами реологический модели по формуле, предложенной А. Хензелем и Т. Шпиттелем [23]
(4)
$\begin{gathered} {{\sigma }_{i}} = A\exp ({{m}_{1}}T){{T}^{{{{m}_{9}}}}}\varepsilon _{i}^{{{{m}_{2}}}}\exp ({{{{m}_{4}}} \mathord{\left/ {\vphantom {{{{m}_{4}}} {{{\varepsilon }_{i}}}}} \right. \kern-0em} {{{\varepsilon }_{i}}}}){{\left( {1 + {{\varepsilon }_{i}}} \right)}^{{{{m}_{5}}T}}} \times \\ \times \;\exp ({{m}_{7}}{{\varepsilon }_{i}})\dot {\varepsilon }_{i}^{{{{m}_{3}}}}\dot {\varepsilon }_{i}^{{{{m}_{8}}T}}, \\ \end{gathered} $Таблица 1.
Коэффициенты уравнения (4) медного сплава БрХ08
Тип деформации | A | m1 | m2 | m3 | m4 | m5 | m7 | m8 | m9 |
---|---|---|---|---|---|---|---|---|---|
20 и 400°С | 10.0491 | –0.012 | 0.436 | 0.009 | –0.029 | 0.0004 | –0.924 | 0 | 1.3935 |
600 и 800°С | 10.0134 | –0.004 | 0.087 | –0.008 | –0.045 | –0.001 | 0.303 | 0 | 0.7614 |
В случае изменения %-содержания химических элементов, входящих в состав сплава БрХ08 либо изменения марки медного сплава, структура уравнения (4) не изменяется; изменяются численные значения коэффициентов реологической модели. Полученная в соответствии с уравнением (4) модель сплава БрХ08 справедлива при следующих условиях: Т ∈ [20; 800]°С, ε ∈ [0.002; 1.5], $\dot {\varepsilon }$ ∈ [0.001; 0.4] с–1.
Величина контактного касательного напряжения с учетом скорости скольжения ${{{v}}_{{{\text{rel}}}}}$ в процессе моделирования определялась разработанной фирмой “КванторФорм” подпрограммой “friction.sliding_velocity” (рис. 2).
Фактор трения m определяли экспериментально методом осадки кольцевого образца, подробно изложенным во многих работах, связанных с исследованием контактного трения при обработке металлов давлением, например авторами работы [23]. Далее, в разделе “Обсуждение результатов” приводится краткое описание данного метода и его применения для оценки значения фактора трения. Коэффициент С находили путем сопоставления экспериментальных и расчетных данных, наиболее точно отражающих реальный процесс формообразования.
Экспериментальная осадка с кручением (рис. 3) была осуществлена на модернизированном гидравлическом прессе с применением заготовок из медного сплава БрХ08 диаметром 40 мм и высотой 7 мм, полученных методом электроэрозионной вырезки. На модернизированном прессе имеется система сбора и анализа данных, позволяющая записывать в режиме реального времени текущее значение силы деформирования и температуры деформируемого образца. Моделирование процесса осадки с кручением осуществили с применением программы QForm [24] и приведенной выше подпрограммой “friction.sliding_velocity” для определения величины контактного касательного напряжения.
Рис. 3.
Схема исследуемого процесса осадки с кручением (а) на модернизированном гидравлическом прессе; (б) – образец медного сплава БрХ08 до осадки с кручением; (в) – образец медного сплава БрХ08 после осадки с кручением.
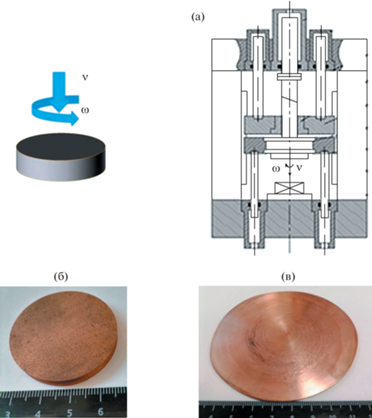
Обсуждение результатов. Результаты моделирования приведены на рис. 4–6. Как видно из приведенных графиков на силу процесса и, следовательно, характер процесса одновременно оказывают существенное влияние два параметра – фактор трения m и коэффициент С. Для минимизации ошибок моделирования процесса фактор трения был определен экспериментально путем осадки кольцевых образцов с размерами наружного и внутреннего диаметров и высоты 30 × 15 × 5 мм на 50%.
Рис. 4.
Результаты моделирования зависимости силы (Fдеф, МН) осадки с кручением от хода инструмента (h, мм) при разных факторах трения m, коэффициент С = 50 (1, 2, 3: m = 0.2; 0.45; 0.7 соответственно).
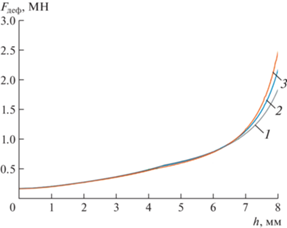
Рис. 5.
Результаты моделирования зависимости силы (Fдеф, МН) осадки с кручением от хода инструмента (h, мм) при разных факторах трения; коэффициент С = 50 (1, 2, 3: m = 0.2, 0.45, 0.7 соответственно) и при коэффициенте С = 1 (4 – m = 0.7).
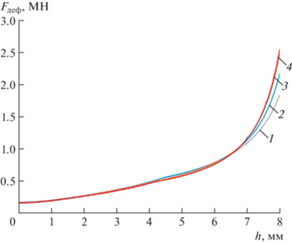
Рис. 6.
Результаты моделирования зависимости силы (Fдеф, МН) осадки с кручением от хода инструмента (h, мм) при разных значениях коэффициента С; фактор трения m = 0.7 (1 – C = 1; 2 – C = 50; 3 – C = 25; 4 – C = 10).
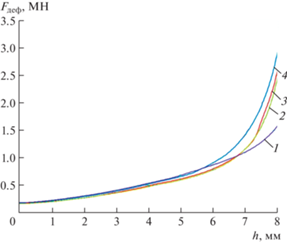
Образцы до и после осадки показаны на рис. 7.
После осадки образцы имели размеры 38.2 × 8.39 × 2.5 мм. Уменьшение внутреннего диаметра составило 44.1% и уменьшение высоты 50%. В соответствии с графиком (рис. 8), фактор трения равен 0.56.
Рис. 8.
График для определения фактора трения методом осадки образцов с соотношением геометрических размеров 6:3:1 [25].
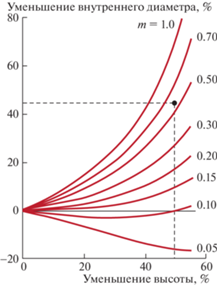
Моделирование осадки кольцевого образца с аналогичными размерами и из медного сплава БрХ08 с применением найденной реологической модели с различными факторами трения до получения заготовки с экспериментально найденными размерами позволило установить, что наилучшее совпадение расчетных и экспериментальных данных имеет место при факторе трения равным 0.61.
Для оценки влияния подпрограммы “friction.sliding_velocity” на контактное трение при осадке с кручением было проведено моделирование осадки заготовки из сплава БрХ08 с ее применением и без нее (рис. 9). Как видно из графиков моделирование с фиксированным фактором трения m показывает на 15–20% более высокие значения момента.
Рис. 9.
Результаты моделирования зависимости момента кручения (Мкр, Нм) на инструменте от его хода (h, мм) при осадке при факторе трения m = 0.61 и С = 40, кривая 1 без применения подпрограммы LUA, 2 – с применением подпрограммы LUA.
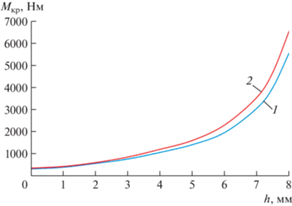
С учетом полученных данных по фактору трения при осадке кольцевых заготовок и с применением подпрограммы по учету влияния скорости скольжения металла (рис. 2) были осуществлены осадка с кручением пакета из двух заготовок из медного сплава БрХ08 и моделирование процесса. Диаметр и высота каждой заготовки составляли 40 и 7 мм соответственно. Результаты моделирования и осадки приведены на рис. 10.
Рис. 10.
Сравнение результатов моделирования и осадки пакета из двух заготовок из сплава БрХ08: (а) – моделирование (92%); (б) – эксперимент.
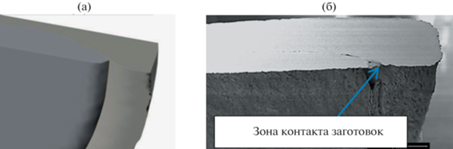
Анализ полученных данных позволил получить зависимость, отражающую влияние скорости скольжения на контактное трение. Сравнительный анализ результатов моделирования осадки с кручением с назначением постоянного фактора трения равным 0.61 и с дополнительным использованием подпрограммы “friction.sliding_velocity” с фактором трения m = 0.61, коэффициентом влияния контактного давления а = 1.25 и параметром влияния скорости проскальзывания С = 40 показал, что учет зависимости влияния скорости проскальзывания на контактное трение дает более точные результаты моделирования как по зависимости “сила–ход инструмента”, так и по геометрическому подобию заготовок, получаемых моделированием (рис. 11) и экспериментами (рис. 10), что подтверждается микрошлифом, приведенным на рис. 10.
Рис. 11.
Сравнительный анализ результатов моделирования осадки с кручением с назначением постоянного фактора трения равным 0.6 и с дополнительным использованием подпрограммы “friction.sliding_velocity”: (а) – моделирование с постоянным фактором трения; (б) – моделирование с теми же параметрами, как и “а”, но с применением подпрограммы “friction.sliding_velocity”.
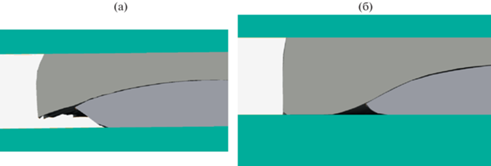
С учетом найденных нами данных зависимость, отражающая влияние скорости скольжения на контактное трение, имеет вид
(5)
${{\tau }_{k}} = 0.61k\frac{{{{\sigma }_{{{\text{eq}}}}}}}{{{{\sigma }_{s}}}}\left( {1 - {{e}^{{\frac{{ - \left| {{{\sigma }_{n}}} \right|}}{{{{\sigma }_{S}}}}}}}} \right){{e}^{{ - 0.5{{{\left( {\frac{{{{{v}}_{{{\text{rel}}}}}}}{{40}}} \right)}}^{2}}}}}.$Однако для более полного изучения процесса необходимо углубленное изучение энергосиловых параметров процесса.
Заключение. 1. Экспериментами по осадке кольцевых образцов с размерами наружного и внутреннего диаметров и высоты 30 × 15 × 5 мм на 50% их начальной высоты и последующим моделированием натурного эксперимента программой QForm установлено, что при холодной осадке заготовок из медного сплава БрХ08 фактор трения m равен 0.61 (среднеарифметическое значение по результатам серии опытов). 2. Сравнительный анализ силовых параметров процесса и геометрической формы получаемых заготовок позволил определить коэффициенты m и C (формула (3)), которые составили 0.61 и 40, соответственно. Определение значений выполнено на основе расчетов в программе QForm, в которой был поставлен виртуальный эксперимент об осадке с кручением. 3. Выполненные теоретические и экспериментальные работы позволили определить зависимость, отражающую влияние скорости скольжения на контактное трение, в явном виде (5) и позволяющую существенно повысить точность результатов компьютерного имитационного моделирования процесса осадки с кручением.
Список литературы
Зибель Э. Обработка металлов в пластическом состоянии. Теоретическое обоснование процессов ОМД. Пер. с нем. М.: ОНТИ, 1934. 199 с.
Леванов А.Н., Колмогоров В.Л. и др. Контактное трение в процессах обработки металлов давлением. Изд. “Металлургия”, 1976. 416 с.
Behrens B.-A., Schafstall H. 2D and 3D simulation of complex multistage forging processes by use of adaptive friction coefficient // J. of Materials Processing Technology. 1998. V. 80 (1). P. 298. https://doi.org/10.1016/S0924-0136(98)00187-3
Becker P., Jeon H.J., Chang C.C. et al. Modelling the Friction interface in bulk forming processes // In: Neugebauer R (ed) 10. Sä Fachtagung Umformtechnik in Chemnitz October 14–15, 2003, Wissenschaftliche Skripten, Zwickau, S. 179.
Behrens B.A., Bouguecha ., Hadifi T., Mielke J. Advanced friction modeling for bulk metal forming processes // Prod. Eng. Res. Devel. 2011. V. 5. P. 621. https://doi.org/10.1007/s11740-011-0344-8
Jain S.C., Bramley A.N. Speed and Frictional Effects in Hot Forging // Proc.Inst.Mech.Eng. 1968. V. 182. № 39. P. 783.
Davoudi M., Ali Farokhi Nejad, Koloor S.S.R., Petrů M. Investigation of Effective Geometrical Parameters on Wear of Hot Forging Die // J. of Materials Research and Technology. 2021. V. 15. P. 5221.
Widomski P., Gronostajski Z. Comprehensive Review of Methods for Increasing the Durability of Hot Forging Tools // Procedia Manufacturing. 2020. V. 47. P. 349.
Lee K.J., Lee M.G. Pressure and sliding velocity dependent surface asperity based friction model: Application to springback simulation // IOP Conf. Ser. Mater. Sci. Eng. 2019. V. 651. https://doi.org/10.1088/1757-899X/651/1/012079
Cillaurren J., Galdos L., Sanchez M., Zabala A., Sáenz de Argandoña E., Mendiguren J. Contact pressure and sliding velocity ranges in sheet metal forming simulations // ESAFORM. 2021. https://doi.org/10.25518/esaform21.426
Sigvant M. et al. Friction in sheet metal forming: influence of surface roughness and strain rate on sheet metal forming simulation results // Procedia Manufacturing. 2019. V. 29. P. 512. https://doi.org/10.1016/j.promfg.2019.02.169
Waanders D., Marangalou J.H., Kott M., Gastebois S., Hol J. Temperature Dependent Friction Modelling: The Influence of Temperature on Product Quality // Procedia Manufacturing. 2020. V. 47. P. 535. https://doi.org/10.1016/j.promfg.2020.04.159
Behrens B.A., Bouguecha A., Lüken I., Mielke J., Bistron M. Tribology in Hot Forging. In: Comprehensive Materials Processing // Comprehensive Materials Processing. 2014. V. 5. P. 211.
Петров П.А., Бурлаков И.А., Нгуен Хань Тоан. Перспективы применения гибридных заготовок в машиностроении // Технология металлов. 2021. № 8. С. 10.
Бурлаков И.А., Петров П.А., Бач Ву Чонг. Изготовление осесимметричных заготовок из титана ВТ1-0 с изотропными свойствами // Технология металлов. 2020. № 10. С. 52.
Behrens B.-A., Bouguecha A., Hadifi T., Mielke J. Advanced friction modeling for bulk metal forming processes // German Academic Society for Production Engineering (WGP). 2011. № 5. P. 621.
Neumaier T. Zur Optimierung der Verfahrensauswahl von Kalt-, Halbwarm- und Warmmassivumformverfahren. Dissertation, Universität. Hannover, VDI Verlag Düsseldorf, 2003.
Alasti M. Modellierung von Reibung und Wärmeübergang in der FEM-Simulation von Warmmassivumformprozessen. Ph.D. Thesis, Leibniz Universität Hannover, 2008.
Nägele H. Simulation des Herstellungsprozesses präzisionsgeschmiedeter Zahnräder mit der Finite-Elemente Methode. Dissertation, Universität Hannover, VDI Verlag Düsseldorf, 1995.
Behrens B.-A., Alasti M., Bouguecha A., Hadifi T., Mielke J., Schäfer F. Numerical and experimental investigations on the extension of friction and heat transfer models for an improved simulation of hot forging processes // Int. J. Mater. Form. 2009. V. 2 (Suppl. 1). P. 121.
Doege E., Bederna C. Analysis of boundary stresses and temperatures in hot massive forming // Production Engineering, Bd. 1996. V. 3 (2). P. 89.
Bernhardt R. Ein Beitrag zur experimentellen und numerischen Analyse lokaler Kontaktspannungen und Kontakttemperaturen in der Wirkfuge von Gesenkgravuren unter besonderer Beachtung des Randreibungsproblems. Dissertation, TU Freiberg, 1998.
Хензель А., Шпиттель Т. Расчет энергосиловых параметров в процессах обработки давлением. Справочник. М.: Металлургия, 1982. 360 с.
Грудев А.И., Зильберг Ю.В., Тилик В.Т. Трение и смазки при обработке металлов давлением. М.: Машиностроение, 1982. 312 с.
http://qform3d.ru/files_ru/2008_0001_0.pdf (дата обращения 12.09.2021).
Дополнительные материалы отсутствуют.
Инструменты
Проблемы машиностроения и надежности машин