Журнал неорганической химии, 2023, T. 68, № 1, стр. 115-132
Получение функционально-градиентных материалов на основе карбида кремния и высоколегированной стали по технологии искрового плазменного спекания
С. В. Чуклинов a, В. И. Сергиенко b, Е. К. Папынов c, *, О. О. Шичалин c, А. А. Белов c, Е. Ю. Марчуков a, А. Н. Мухин a
a Московский авиационный институт (национальный исследовательский университет)
125993 Москва, Волоколамское ш., 4, Россия
b Президиум ДВО РАН
690000 Владивосток, ул. Светланская, 50, Россия
c Дальневосточный федеральный университет
690922 Владивосток, о. Русский, п. Аякс, 10, Россия
* E-mail: papynov@mail.ru
Поступила в редакцию 01.08.2022
После доработки 24.08.2022
Принята к публикации 31.08.2022
- EDN: GVWBOH
- DOI: 10.31857/S0044457X22601237
Аннотация
Важной научной задачей практического материаловедения является получение металлокерамических композитов в виде функционально-градиентных материалов (ФГМ) для изделий специального назначения. В этой связи в работе проведено исследование по применению технологии искрового плазменного спекания (ИПС) для эффективного диффузионного соединения SiC-керамики и высоколегированной стали (марка Х18Р15) с получением соединенного ФГМ-композита. В комплексном экспериментальном исследовании изучена динамика консолидации и изменение фазового состава дисперсного SiC в условиях различных температур и скорости разогрева, давления прессования, времени выдержки. В результате оптимизированы условия ИПС для получения SiC-керамики высокой относительной плотности (>82%) и микротвердости (>500 HV) стабильного фазового состава. Исследованы физико-химические основы формирования прочного соединения двухкомпонетной системы SiC-керамики и стали в условиях ИПС без добавок и с использованием смеси добавок в виде связующего, реакционного связующего и демпфера (системы добавок Ti–Ag, Ti–TiH2, Ti–Ag–TiH2 и Ti–Ag/Mo). Методами РФА, РЭМ и ЭДС изучена структура, состав керамики и промежуточных (связующих и демпферных) слоев, а также диффузия элементов на границе сформированных соединений в ФГМ-композитах. Установлено, что добавка Ti–Ag/Mo в соотношении 30 мас. % Ti–70 мас. % Ag и плотная прослойка Mo (толщина ~2 мм), выполняющего роль демпфера для компенсации температурного коэффициента линейного расширения, обеспечивают формирование соединенного ФГМ-композита целостной формы. Представленные исследования реализованы впервые, являются перспективными и требуют дальнейшего развития с целью наработки научных знаний изготовления композитных изделий специального назначения.
ВВЕДЕНИЕ
Функционально-градиентные материалы (ФГМ) в виде соединенных композитов слоистой (ступенчатой [1]) структуры представляют основу различных специальных изделий и ответственных конструкций в автомобиле-, судо-, машино-, ракето- и авиастроении и др. [2]. За счет ФГМ достигают более высоких физико-химических и механических характеристик, повышают эксплуатационные свойства, улучшают эргономику и, соответственно, снижают себестоимость производства изделий и конструкций [3, 4]. Высокий практический интерес представляют металлокерамические ФГМ [5]. Это композитные системы, которые сочетают в себе симбиоз таких привлекательных свойств керамики и металла, как износостойкость, термическая, химическая, коррозионная устойчивость, жаропрочность, радиационная стойкость и др., которые распределяются в объеме ФГМ градиентно. Они демонстрируют значительный потенциал для экстремальных применений, где альтернатива подобным материалам минимальна или отсутствует полностью.
Получение металлокерамических ФГМ соединенного типа осуществляют с применением традиционных способов сварки, спаивания, спекания и сплавления, в том числе с учетом использования различных связующих добавок и при их отсутствии [6]. Однако данный процесс является сложной технологической задачей, которая заключается в формировании прочного соединения в области контакта двух разнородных материалов. Ключевыми проблемами, препятствующими успешному получению ФГМ целостной формы, являются различия в физико-химической природе керамики и металлов [7]. Это приводит к возникновению негативных эффектов на границе их контакта [8]: 1) различие в типе химических связей материалов затрудняет атомную диффузию; 2) образование промежуточных оксидных, карбидных, нитридных слоев приводит к повышенной хрупкости; 3) низкая смачиваемость керамики металлом не позволяет использовать припои; 4) различие в температурных коэффициентах линейного расширения (ТКЛР), теплопроводности и устойчивости к тепловому стрессу приводит к возникновению внутренних деструктивных напряжений и др. Последнее является наиболее распространенной проблемой, требующей научного решения.
Минимизацию внутренних напряжений, вызванных различием ТКЛР, проводят путем диффузионного соединения вышеуказанными методами, в том числе с использованием добавок (наполнителей) [8–10]. В частности, применяют добавки металлов с повышенной пластичностью, способные частично переходить в расплав на границе контакта, и металлы с высокой упругостью, имеющие близкие ТКЛР для керамики. Данные добавки выполняют роль демпферов и компенсируют напряжения на границе контакта и в объеме композита, а также в ряде случаев являются связующими слоями между соединяемыми материалами. При этом для нивелирования градиента температур в объеме соединяемых образцов и, соответственно, снижения возможного теплового стресса при их разогреве ученые предлагают использовать современные термические способы диффузионного соединения. Это электрофизические способы, основанные на разогреве образца однонаправленным импульсным электрическим током, реализуемые, например, по технологии искрового плазменного спекания (ИПС) [11], которая применяется для получения различных керамик [12–18] и сплавов [19–21]. В известных работах [22] исследователи отмечают высокую перспективу ИПС для получения соединенных ФГМ-композитов, которую связывают с уникальностью механизма разогрева: а) обеспечивается высокий локальный разогрев образца, возникающий за счет электрического сопротивления на границе контакта соединяемых материалов, в тот момент когда температура всего образца остается ниже; б) достигается высокая скорость диффузии на границе контакта соединяемых материалов за счет мгновенного локального разогрева и генерации Джоулева тепла в условиях ИПС. Технология была успешно применена для соединения SiC/C при температуре 2000°C с результирующей прочностью на растяжение 18 МПа в отсутствие дефектов [23, 24]. Также в работе [25] было продемонстрировано успешное соединение композита SiC/С с дополнительным CVD-покрытием SiC как прямым диффузионным спеканием в условиях ИПС, так и со связующими добавками стеклокерамики, смеси SiC + + 5 мас. % B4C и с фольгой из чистого Ti. Кроме того, по технологии ИПС соединяли Ti со сталью без хрупких интерметаллических соединений Fe–Ti и искажения формы исходных материалов [26]. Были соединены сложные сплавы Ti–6Al–4V с низколегированной сталью при температуре 950°C с достижением максимальной прочности на растяжение 250 МПа [27], а также получены композиты TiAl/Ti2AlNb с использованием Ti как промежуточного слоя при температурах от 650°C [28]. Оригинальное решение по использованию оксалата серебра Ag2C2O4 в качестве реакционного связующего, которое подвергается деструкции в условиях ИПС с образованием металлического Ag и обеспечивает формирование связующего слоя для соединения объемных образцов Cu/Cu, было успешно продемонстрировано в [29, 30]. При этом количество подобных работ ограничено, а по широкому ряду систем отсутствует полностью. В частности, в литературе не представлены исследования по применению технологии ИПС для получения металлокерамических ФГМ, соединенных на основе SiC со сталью или сплавами различного типа, включая жаропрочные, изделия из которых имеют неограниченный практический спрос. Научный интерес в данном случае обусловлен высокой сложностью соединения данных разнородных по физико-химическим и механическим характеристикам материалов, имеющих различающиеся более чем в 3 раза величины ТКЛР (SiC 4.4 × 10–6°C–1, сталь, например марки 304, 17.3 × 10–6°C–1) и температуры плавления, с возможностью получения целостного ФГМ-композита.
В связи с этим цель настоящей работы – изучение применения технологии ИПС для эффективного диффузионного соединения SiC-керамики и высоколегированной стали марки Х18Р15 с получением ФГМ-композита соединенного типа, включая оптимизацию режимов консолидации SiC-керамики, а также выбор и использование перспективных связующих и демпферных компонентов.
ЭКСПЕРИМЕНТАЛЬНАЯ ЧАСТЬ
Реактивы. Получение керамических образцов проводили с использованием порошка SiC (КНР). Образцы стали изготавливали из коммерческого порошка марки ПХ18Н15 (ГОСТ 13084-88, АО “Полема”, Тула, Россия). В качестве связующих добавок и демпферов использовали порошки производства ООО “Передовые порошковые технологии” (Новосибирск, Россия): Ti (чистота 99.98%, средний размер частиц 80–110 нм, насыпная плотность 2.85 г/см3, удельная поверхность по БЭТ 13.8 м2/г), Ag (чистота 99.99%, средний размер частиц 100 нм, насыпная плотность 5.8 г/см3, удельная поверхность по БЭТ 6.5 м2/г, точка плавления 960°С), TiH2 (чистота 99.6%, средний размер частиц 200 нм).
Оборудование. Эксперименты по консолидации образцов керамики и стали, а также их соединение с получением образцов ФГМ проводили на установке искрового плазменного спекания SPS-515S фирмы Dr.Sinter-LABTM (Япония). Контроль температуры разогрева осуществляли с использованием оптического пирометра IR-AHS Hitachi (Япония). Гранулометрический анализ порошка SiC проводили на лазерном анализаторе частиц Analysette-22 NanoTec/MicroTec/XT Fritsch (Германия), выполняя по три измерения для каждого образца, далее результаты усреднялись. Рентгенофазовый анализ (РФА) образцов SiC-керамики проводили на многоцелевом рентгеновском дифрактометре D8 Advance Bruker AXS (Германия), CuKα-излучение, Ni-фильтр, средняя длина волны (λ) 1.5418 Å, диапазон углов съемки 10°–80°, шаг сканирования 0.02°, скорость регистрации спектров 5 град./мин. Изображения структуры исследуемых образцов были получены методом растровой электронной микроскопии (РЭМ) на приборе CrossBeam 1540 XB Carl Zeiss (Германия) при ускоряющем напряжении 5–15 кВ и токе пучка 100 пА с приставкой для энергодисперсионного спектрального анализа (ЭДСА). Измерение удельной плотности (ρуд) проводили методом гидростатического взвешивания на весах AdventurerTM “OHAUS Corporation” (США).
Методика эксперимента
Получение образцов SiC-керамики. Консолидацию образцов керамики по технологии ИПС проводили по следующей схеме (рис. 1): 2 г порошка карбида кремния помещали в графитовую пресс-форму (параметры: внешний диаметр 30 мм, внутренний диаметр 15.5 мм, высота 30 мм), подпрессовывали (давление 20.7 МПа), далее заготовку помещали в камеру спекания, вакуумировали (остаточное давление 6 Па), затем проводили разогрев импульсным током. Температуру процесса контролировали с помощью оптического пирометра, сфокусированного на отверстие, расположенное на середине плоскости внешней стенки пресс-формы глубиной 5.5 мм. Для предотвращения припекания консолидируемого порошка к пресс-форме и плунжерам, а также для легкого извлечения полученного компаунда использовали графитовую фольгу толщиной 200 мкм. Пресс-форму оборачивали в теплоизолирующую ткань для снижения теплопотерь при разогреве. Характеристика импульсного тока в режиме периодичной подачи On/Off пакетами 12/2 (длительность пакета импульса 39.6 мс/пауза 6.6 мс). Максимальная сила тока при спекании составила 1000–1200 A, напряжение 4 В. В ходе ИПС-процесса получали четыре серии образцов керамики за счет варьирования следующими параметрами:
Рис. 1.
Общий вид установки SPS-515S “Dr.Sinter·LABTM” (а), пресс-оснастка в разобранном виде (б) и в сборе с установкой между электродами (в), разогрев в камере спекания (г), готовый консолидированный образец (д).
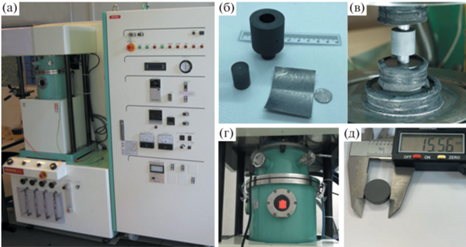
– температура процесса в диапазоне 1600, 1700, 1800, 1900 и 2000°С, скорость разогрева 100 град./мин, время выдержки при максимальной температуре 5 мин и постоянном давлении прессования 50 МПа;
– давление прессования в диапазоне 20, 30, 50, 70 и 100 МПа, температура консолидации 1900°С, скорость разогрева 100 град./мин, время выдержки при максимальной температуре 5 мин оставались постоянными;
– скорость разогрева составляла 25, 50, 100 и 200 град/мин, температура консолидации 1900°С, время выдержки при максимальной температуре 5 мин и давление прессования 50 МПа оставались постоянными;
– время выдержки при максимальной температуре составляло 1, 5, 8, 15 и 30 мин, температура консолидации 1900°С, скорость разогрева 100 град/мин и давление прессования 50 МПа оставались постоянными.
Геометрические размеры полученных образцов керамики цилиндрического типа: диаметр 15.3 мм, высота 3–5 мм (в зависимости от режимов спекания). Общий вид образцов представлен на рис. 2.
Рис. 2.
Общий вид образцов SiC-керамики, полученных при различных условиях ИПС, варьировались: температура (а); скорость разогрева (б); давление прессования (в); время выдержки при максимальной температуре (г).
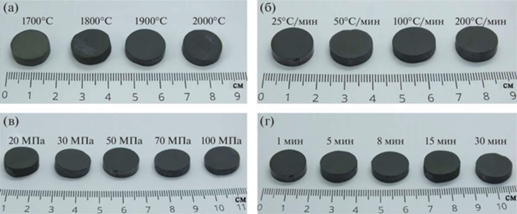
Получение образцов стали проводили аналогично вышеописанной методике: температура 1000°С, скорость нагрева 100 град/мин, давление прессования 25 МПа.
Геометрические размеры полученных образцов стали цилиндрического типа: диаметр 15.3 мм, высота в пределах 4 мм.
Получение образцов ФГМ соединенного типа по технологии ИПС. Получение образцов ФГМ проводили с использованием образцов SiC-керамики и стали за счет формирования прочного соединения на границе контакта керамики и стали в условиях ИПС согласно следующей схеме: образцы керамики и стали (рис. 3а) помещали в графитовую пресс-форму цилиндрического типа (внешний диаметр 30 мм, внутренний диаметр 15.5 мм, высота 30 мм), которая отличается от стандартного типа пресс-форм наличием дополнительного сквозного окна для контроля температуры (рис. 3б), где съемку температуры проводили оптическим пирометром с области контакта соединяемых образцов. Расчетное значение возможного перегрева стали и керамики от значения температуры в области съемки может достигать не более 50°С. Разогрев проводили в камере спекания в среде вакуума (давление 6 Па) (рис. 3в). Контроль температуры образца осуществляли оптическим пирометром с поверхности образцов в области их контакта (рис. 3г). Охлаждение образцов осуществляли в течение 1 ч в среде вакуума.
Рис. 3.
Общий вид образцов SiC-керамики и стали для соединения (а), их расположение в пресс-форме (б), разогрев пресс-формы в камере спекания (в), область контроля температуры в месте контакта (соединения) образцов (г).
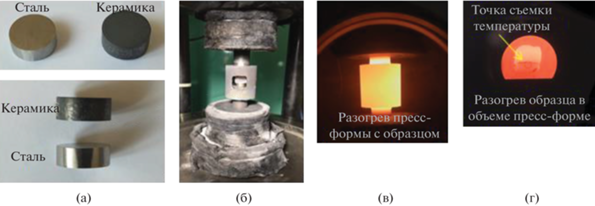
Отличие реализуемых экспериментов друг от друга заключалось в подходах для формирования прочного соединения образцов керамики и стали, включающих диффузионное спекание, спекание с использованием металлических добавок на основе связующих компонентов для получения промежуточного упрочняющего слоя, а также для компенсации внутренних напряжений, вызванных различной величиной ТКЛР. Описание данных способов реализации экспериментов представлено далее.
Подготовку поверхности соединяемых образцов керамики и стали проводили тонкой механической полировкой на полировальной станции Mecapol P320 (Франция) с использованием алмазных абразивных суспензий.
Формирование соединения без использования связующих добавок. Разогрев образцов керамики и стали для достижения формирования соединения проводили при температуре 1000°С, скорость разогрева 100 град/мин, время выдержки при максимальной температуре 5 мин, давление прессования 35 МПа.
Формирование соединения с использованием смеси металлических добавок, выполняющих функции связующего. В качестве добавки для получения ФГМ использовали смесь металлов на основе металлических порошков титана (Ti) и серебра (Ag) (соотношение 70 : 30 мас. %). Смесь системы Ti–Ag готовили механической гомогенизацией в планетарной мельнице при 870 об./мин в один цикл в течение 15 мин. Готовую смесь наносили ровным слоем (толщиной ~2 мм) в межконтактную область поверхностей керамики и стали. Далее заготовку помещали в пресс-форму и разогревали согласно указанной выше методике (рис. 3). Температура нагрева 1000°С, скорость разогрева 100 град/мин, время выдержки при максимальной температуре 5 мин, давление прессования 35 МПа.
Формирование соединения с использованием добавки на основе смеси металлического и реакционного связующих. В качестве добавки для получения ФГМ использовали смесь металлов на основе титана (Ti) и гидрида титана (TiH2) (соотношение 70 : 30 мас. %). Смесь системы Ti–TiH2 готовили механической гомогенизацией в планетарной мельнице при 870 об./мин в один цикл в течение 15 мин. Готовую смесь наносили ровным слоем (толщиной ~2 мм) в межконтактную область поверхностей керамики и стали. Далее заготовку помещали в пресс-форму и разогревали согласно указанной выше методике (рис. 3). Температура нагрева 1000°С, скорость разогрева 100 град/мин, время выдержки при максимальной температуре 5 мин, давление прессования 35 МПа.
Формирование соединения с использованием добавки на основе многокомпонентной смеси металлических и реакционного связующих. В качестве добавки для получения ФГМ использовали смесь металлов на основе трехкомпонентной порошковой системы Ti–Ag–TiH2 (соотношение 60 : 30 : 10). Смесь готовили механической гомогенизацией в планетарной мельнице при 870 об/мин в один цикл в течение 15 мин. Готовую композитную добавку наносили ровным слоем (толщиной ~2 мм) в межконтактную область поверхностей керамики и стали. Далее заготовку помещали в пресс-форму и разогревали согласно указанной выше методике (рис. 3). Температура нагрева 1000°С, скорость разогрева 100 град/мин, время выдержки при максимальной температуре 5 мин, давление прессования 35 МПа.
Формирование соединения с использованием металлических добавок в виде связующего и промежуточного плотного слоя молибдена в роли демпфера. Эксперимент по получению соединенного композита на основе SiC-керамики и стали, имеющих различие в ТКЛР более чем в 3 раза (SiC 4.4 × 10–6°C–1, сталь марки 304, 17.3 × 10–6°C–1), реализовывали путем формирования промежуточного плотного слоя на основе молибдена, имеющего промежуточное значение ТКЛР между соединяемыми материалами Mo 5.6 × 10–6°C–1, где в качестве связующей добавки использовали систему Ti–Ag (соотношение 70 : 30 мас. %).
Связующую добавку наносили ровным слоем (толщиной ~2 мм) в межконтактную область поверхностей соединяемых материалов между керамикой и молибденом (толщина ~2 мм), а также между молибденом и сталью. Далее заготовку помещали в пресс-форму и разогревали согласно указанной выше методике (рис. 3). Температура нагрева 1000°С, скорость разогрева 100 град/мин, время выдержки при максимальной температуре 5 мин, давление прессования 35 МПа.
Общий вид полученных образцов представлен на рис. 4.
РЕЗУЛЬТАТЫ И ОБСУЖДЕНИЕ
Исследование характеристик исходного порошка карбида кремния и керамики на его основе
Порошок карбида кремния. Согласно данным гранулометрического анализа, фракционный состав исходного порошка SiC, используемого для изготовления керамики, представлен частицами двух фракций (рис. 5а). Средний размер частиц основной фракции составляет ~3 мкм, меньшей по количеству фракции – ~0.3 мкм.
Данные гранулометрического состава подтверждаются результатами микроскопических исследований. На РЭМ-снимках (рис. 5б) видно, что размер частиц соответствует данным, полученным выше на гистограмме. Частицы не превышают размера 5 мкм в диапазоне, наблюдается также наноразмерная фракция <1 мкм. Крупные зерна представляют собой монолитные агломераты (рис. 5б, врезка).
Согласно РФА (рис. 6а, кривая 1), фазовый состав исследуемого исходного порошка представлен основной фазой карбида кремния (SiC) в кубической сингонии с незначительной (следовой) примесью карбида кремния с ромбоэдрической кристаллической решеткой, что, вероятно, обусловлено методом синтеза данного порошка. Из литературы известно, что частичное изменение кристаллической структуры SiC кубической формы на ромбоэдрическую возможно при постепенном нагреве SiC при 1700°С [6].
Рис. 6.
Дифрактограммы (а) исходного коммерческого порошка SiC и образцов керамик на его основе, полученных при различных температурах ИПС, и дилатометрические зависимости (б) скорости усадки данного порошка от температур нагрева.
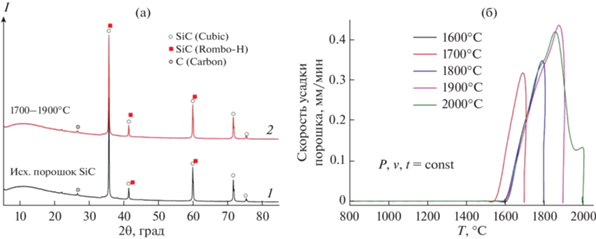
С целью установления оптимальных технологических режимов искрового плазменного спекания исследуемого в работе порошка SiC изучено влияние температуры, давления прессования, скорости разогрева и времени выдержки при максимальной температуре нагрева на конечные физико-химические и механические характеристики получаемых образцов SiC-керамики. Описание результатов исследования представлено ниже.
Влияние температуры искрового плазменного спекания. В ходе исследования динамики консолидации на основании дилатометрических зависимостей (рис. 6б) установлено, что спекание керамики протекает в одну основную стадию в температурном диапазоне от 1600°С и выше. Скорость уплотнения максимальна при наибольших температурах ИПС нагрева (1900 и 2000°С). Кроме того, наблюдается дополнительный перегиб на кривой скорости уплотнения для образца, спекаемого при 2000°С, полную величину которого отследить невозможно ввиду технического ограничения возможностей оборудования (предельно достигаемая температура на установке). При этом следует отметить, что данный эффект, отраженный на дилатометрической зависимости в области выше 2000°С, может быть обусловлен не только дополнительным уплотнением спекаемого порошка, но и изменением характеристик графитовой оснастки вплоть до ее разрушения в области высоких температур, как показано в работе [7].
По данным РФА (рис. 6а, кривая 2), состав полученной керамики не изменяется в ходе консолидации исходного порошка и соответствует основной фазе SiC в кубической сингонии. Также присутствуют незначительные по интенсивности рефлексы, соответствующие SiC c кристаллической решеткой ромбоэдрического типа, примесь которого была выявлена в исходном порошке SiC (рис. 6а, кривая 1), а его образование связано с трансформацией кубической кристаллической решетки в ромбоэдрическую при нагреве до 1700°С [31]. Наблюдается рефлекс при угле 2θ 26°–27°, который может соответствовать примеси диоксида кремния (SiO2) или углероду (С), чьи значения межплоскостного расстояния при данном угле отражения плохо различимы. Присутствие углерода более вероятно, так как он способен диффундировать в незначительном количестве с поверхности графитовой пресс-оснастки, что характерно для процесса ИПС и доказано в ряде исследований [32–35].
При помощи микроскопического анализа установлено, что ИПС-консолидация при температуре <1800°С не обеспечивает спекание частиц порошка SiC, так как образец, полученный при 1700°С, представляет собой спрессованный исходный порошок, частицы которого не имеют контактов спекания (рис. 7а). Повышение температуры до 1800°С и выше сопровождается спеканием частиц по границам их контактов с образованием крупных агломератов в виде монолитных областей, площадь которых по объему образца возрастает с достижением температуры 2000°С (рис. 7б–7г). При этом на снимке РЭМ (рис. 7г) видно, что образец, полученный при 2000°С, характеризуется наличием пористых областей в межграничных контактах некоторых зерен, что может свидетельствовать о недостаточно полном спекании порошка. Кроме того, наблюдается рост зерна SiC с повышением температуры до 2000°С (рис. 7а–7г).
Рис. 7.
РЭМ-изображения поверхности поперечного среза образцов SiC-керамики, полученных на основе коммерческого SiC-порошка при различных температурах ИПС (скорость разогрева 100 град/мин, давление прессования 50 МПа, время выдержки 5 мин).
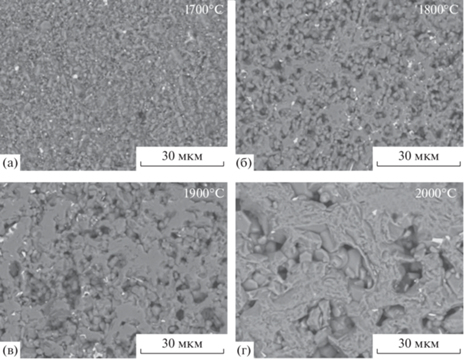
Установлено, что относительная плотность образцов SiC-керамики возрастает с увеличением температуры ИПС (рис. 8а). Максимальное значение (82.12%) для исследуемого диапазона температур достигается при 2000°С и незначительно отличается от величины, соответствующей 1900°С (81.94%). Данные значения плотности относительно высоки, однако ниже теоретического значения для SiC, что обусловлено наличием пористого объема в керамике, как было выявлено на РЭМ-снимках (рис. 7).
Рис. 8.
Зависимости относительной плотности (а) и дисперсия значений микротвердости по Виккерсу (б) для образцов SiC-керамики, полученных при различных температурах ИПС (скорость разогрева 100 град/мин, давление прессования 50 МПа, время выдержки 5 мин).
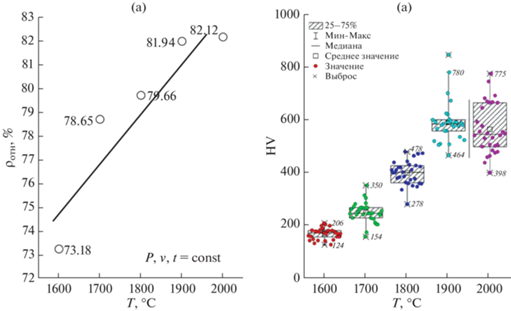
Увеличение температуры консолидации порошка SiC приводит к повышению твердости образцов получаемой керамики (рис. 8б), как и плотности (рис. 8а), за счет интенсификации спекания частиц, что подтверждается РЭМ-изображениями (рис. 7). Однако наблюдается некоторое снижение однородности в микроструктурной организации зерна в объеме керамики, о чем свидетельствует увеличение дисперсии в значениях микротвердости, полученных в 30 точках поверхности в отдельных локальных участках образца (рис. 8а). Показано, что с увеличением температуры спекания увеличивается число значений микротвердости, которые лежат на диаграмме размаха за пределами интерквартильного диапазона.
Согласно полученным и представленным результатам оптимальной температурой консолидации используемого коммерческого порошка SiC (дисперсностью до 5 мкм) в плотную керамику, обладающей наиболее высокими характеристиками, достигнутыми по технологии ИПС, из рассматриваемого диапазона 1600–2000°С, следует считать температуру 1900°С. При данной температуре достигается максимальная усадка порошка в выбранном диапазоне температур, с образованием керамики относительной плотности около 82% и микротвердости в пределах 600 HV, что соизмеримо образцу, полученному при 2000°С.
Влияние скорости разогрева, давления прессования и времени выдержки при максимальной температуре искрового плазменного спекания. Характер кривых скорости усадки порошка SiC, полученных при различной скорости разогрева (рис. 9а) указывает на то, что скорость основной стадии усадки в диапазоне свыше 1600–1900°С увеличивается при повышении скорости разогрева от 25 до 200 град/мин. При скоростях 25 и 50 град/мин скорость усадки порошка SiC незначительна, это указывает на то, что данные режимы недостаточны для достижения оптимального спекания за такой промежуток времени разогрева и выдержки.
Рис. 9.
Дилатометрические зависимости скорости усадки порошка SiC при различных условиях ИПС, варьировались: а – скорость разогрева; б – давление прессования; в – время выдержки при максимальной температуре нагрева (температура спекания 1900°С).
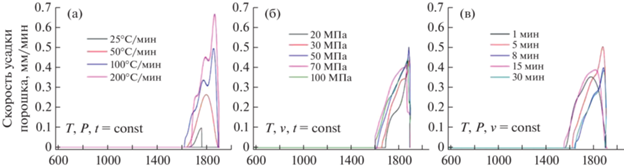
Установлено, что увеличение скорости разогрева приводит к повышению относительной плотности керамики до 84.82% (рис. 10а). Для дальнейших экспериментов с целью получения образцов SiC-керамики при 1900°С оптимальной скоростью разогрева целесообразно считать 100 град/мин как среднюю в исследуемом интервале температур.
Рис. 10.
Зависимость относительной плотности образцов SiC-керамики от различных режимов ИПС: а – скорость разогрева; б – давление прессования; в – время выдержки при максимальной температуре.
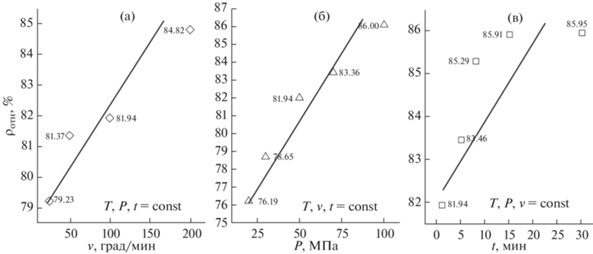
С учетом выбранных оптимальных условий температуры спекания и скорости разогрева исследование влияния давления прессования на спекание SiC-порошка проводили в интервале 20–100 МПа, где нижнее значение ограничено минимальными требованиями оборудования, а верхнее – прочностью графитовой пресс-оснастки. Дилатометрические зависимости скорости усадки от температуры ИПС для образцов SiC-керамики, полученных при различном давлении прессования (рис. 9б), также указывают на одностадийный механизм усадки порошка, где основная стадия спекания соответствует интервалу температур от 1600–1900°С. Показано, что скорости усадки порошка одинаковые и не изменяются при повышении давления прессования в интервале 20–100 МПа, при этом относительная плотность керамики повышается до 86% (рис. 10б). В этой связи оптимальной величиной давления прессования для получения исследуемой SiC-керамики выбрано значение 50 МПа, которое является средним в изученном диапазоне. Средняя величина нагрузки на пресс-оснастку позволит продлить срок ее эксплуатации, а также сократит время съема нагрузки при охлаждении образца.
По дилатометрическим зависимостям (рис. 10в) установлено, что варьирование времени выдержки образца при максимальной температуре ИПС не оказывает существенного влияния на величину усадки порошка и, соответственно, на его спекание. Наблюдается небольшое различие в кривых скоростей усадки, связанное с величиной исходной навески, что незначительно влияет на скорость разогрева образцов. Относительная плотность образцов керамики также изменяется незначительно и достигает 85.95% (рис. 11в). Фазовый состав образцов остается неизменным при изменении времени выдержки при спекании (рис. 6а).
Рис. 11.
Общий вид (а) и РЭМ-изображения (б–г) поперечного среза образца ФГМ-композита, полученного по технологии ИПС с использованием смеси металлических добавок (система Ti–Ag).
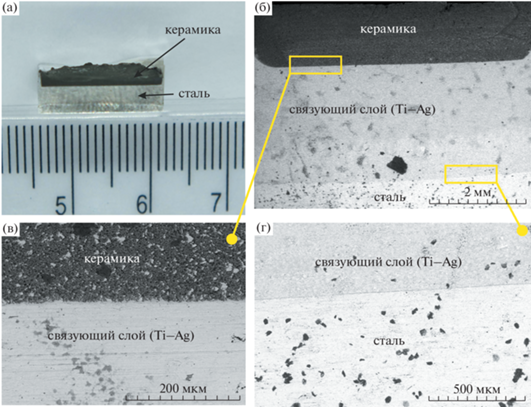
Экспериментально установлено, что минимально требуемыми условиями консолидации используемого коммерческого порошка SiC (дисперсность до 5 мкм) в плотную керамику по технологии ИПС следует считать температуру нагрева не менее 1900°С, скорость разогрева от 100 град/мин, давление прессования не менее 50 МПа, время выдержки при максимальной температуре 5–10 мин. При таких условиях достигается относительно высокая усадка порошка с получением SiC-керамики с относительной плотностью не менее 82% и микротвердостью в пределах 600 HV. Однако очевидно, что качество керамики может быть улучшено при достижении температуры нагрева до 2100°С, что в данном исследовании невозможно из-за технических возможностей используемого оборудования.
Исследование физико-химических характеристик образцов соединенных ФГМ-композитов
ФГМ-композит, соединенный без использования связующих добавок за счет диффузионного спекания. По результатам проведенного эксперимента показано, что отсутствие связующей добавки не позволяет сформировать прочное соединение в месте контакта керамики и стали, образец разрушается по границе соединения (рис. 4а). При этом выявлено, что на поверхности образца стали имеется тонкий слой керамики. Это указывает на протекание прямого диффузионного спекания данных разнородных материалов с образованием промежуточных слоев в приповерхностной области контактируемых материалов, связывающих их между собой. Наряду с этим имеются области, где керамика отсутствует полностью, что свидетельствует о низкой скорости диффузии в локальных областях в процессе разогрева.
ФГМ-композит, соединенный с использованием смеси металлических добавок, выполняющих функции связующего. Использование смеси металлических добавок системы Ti–Ag обусловлено функцией титана, выступающего в роли связующего компонента между керамикой и сталью, за счет образования прочных химических соединений TiC, TiSi2 и Ti3SiC2. При этом серебро является более легкоплавким и пластичным металлом и способствует смачиванию поверхности керамики, а также частично позволяет внутренние механические напряжения, вызванные различной величиной ТКЛР. В результате эксперимента получен образец низкой механической прочности, который раскололся на две части (рис. 4б). Установлено, что причиной разрушения явился дефект керамики, возникший в межграничной области контакта керамики и стали. При этом оставшаяся часть отколотой керамики равномерно припеклась к стали сплошным слоем толщиной около 2 мм (рис. 11а).
На РЭМ-изображениях (рис. 11) поперечного среза образца видно, что соединение керамики со сталью происходит через промежуточный (связующий) слой Ti–Ag. Показано, что на границе контакта керамики, связующего слоя и стали отсутствуют какие-либо дефекты. При этом выявлено, что связующий слой незначительно диффундирует в приповерхностный пористый слой керамики (рис. 11в).
Диффузия связующего слоя подтверждена также с помощью ЭДСА. Для титана она отчетливо проявляется на границе контакта с керамикой (рис. 12а). Установлено, что диффузия элементов на границе контакта связующий слой–сталь незначительна. Наблюдается некоторый перенос серебра (рис. 12б), который может быть вызван частичным расплавом серебра при данной температуре либо механической шлифовкой поверхности среза образца при его подготовке к анализу.
Рис. 12.
Карта распределения элементов (ЭДСА) по поверхности поперечного среза образца ФГМ-композита, полученного по технологии ИПС с использованием смеси металлических добавок (система Ti–Ag), область съемки на границе контакта: а – керамика и связующий слой; б – связующий слой и сталь.
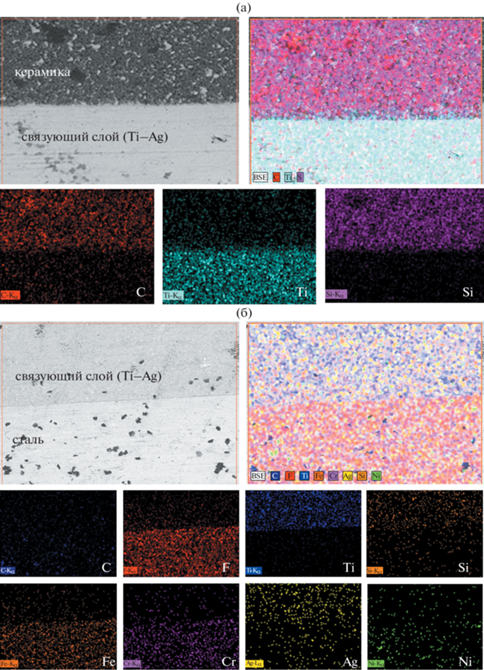
ФГМ-композит, соединенный с использованием добавки на основе смеси металлического и реакционного связующих. Использование добавки металлического и реакционного связующих в виде системы Ti–TiH2 связано с тем, что металлический титан, а также титан, образующийся при разложении гидрида титана, будут играть роль связующего компонента между керамикой и сталью при образовании прочных химических соединений TiC, TiSi2 и Ti3SiC2. Разложение гидрида титана при искровом плазменном разогреве способно приводить к резкому локальному повышению температуры на границе контакта керамики и стали, в связи с этим образование вышеуказанных соединений будет происходить мгновенно при более низких температурах без перегрева общего объема заготовки. Подобное снижение температуры разогрева заготовки позволит снизить градиент температуры по всей заготовке, что обеспечит ослабление механических напряжений на границе контакта материалов. Результатом эксперимента явился дефектный образец (рис. 4в).
Согласно данным микроскопии, причиной разрушения образца явился дефект (трещина) в объеме керамики, расположенный параллельно границе контакта керамики и стали (рис. 13а, 13б), как и в вышеописанном образце. При этом выявлено характерное отличие, связанное с тем, что дефект в керамике образован на более далеком расстоянии от границы контакта (от 1 до 3 мм). Показано, что соединение образовано через промежуточный слой титана в контакте с керамикой и сталью. Соединение на границе контакта сформировано равномерно при отсутствии каких-либо дефектов. Имеется незначительная диффузия титана в приповерхностный слой керамики и стали, о чем также свидетельствуют данные ЭДСА (рис. 14), это, по-видимому, является связующим слоем данных композитов.
Рис. 13.
РЭМ-изображения поперечного среза образца ФГМ-композита, полученного по технологии ИПС с использованием смеси металлического и реакционного связующих (система Ti–TiH2).
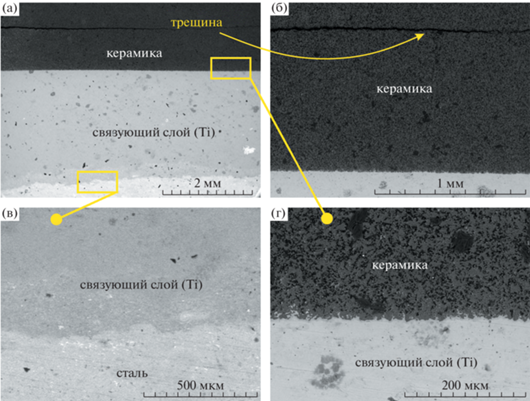
Рис. 14.
Карта распределения элементов (ЭДСА) по поверхности поперечного среза образца ФГМ-композита, полученного по технологии ИПС с использованием смеси металлического и реакционного связующих (система Ti–TiH2), область съемки на границе контакта: а – керамика и связующий слой; б – связующий слой и сталь.
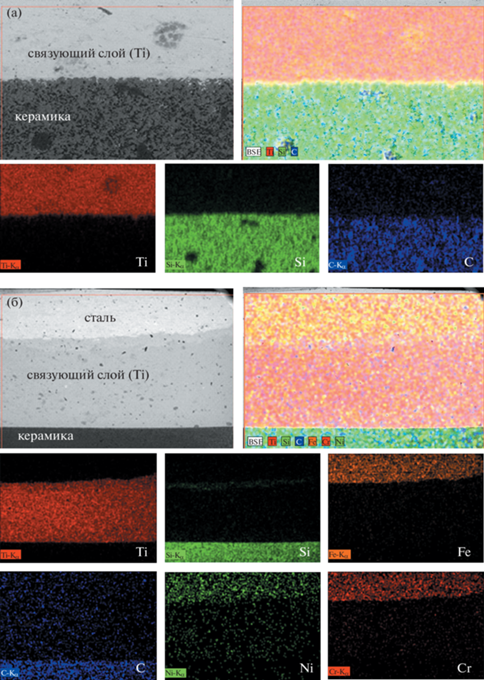
ФГМ-композит, соединенный с использованием добавки на основе многокомпонентной смеси металлических и реакционного связующих. В трехкомпонентном порошке системы Ti–Ag–TiH2 наряду со связующим титаном серебро использовалось в качестве более легкоплавкого и пластичного компонента для снижения нагрузки механических напряжений, вызванных различной величиной ТКЛР между керамикой и сталью. Результатом эксперимента явился образец целостной формы (рис. 4г), что ранее для исследуемых образцов не достигалось.
При микроскопическом исследовании поверхности поперечного среза образца (рис. 15а) выявлен дефект (трещина) в объеме керамики, как и в случае вышеописанных образцов. Однако этот дефект не проникает глубоко в объем образца, что обеспечило сохранность его целостности. На РЭМ-снимках (рис. 15б–15г) видно, что соединение керамики и стали обеспечено благодаря сформированному промежуточному слою системы Ti–Ag. Связующий слой образует равномерные границы контактов с керамикой и сталью в отсутствие каких-либо дефектов. Кроме того, следует отметить, что серебро, выполняющее функцию демпфера, сконцентрировано в нижней части образца на границе контакта со сталью (рис. 15б), что также подтверждено методом ЭДСА (рис. 16). Миграция серебра в нижнюю часть связующего слоя к границе со сталью, вероятно, связана с его частичным расплавлением. Такое расположение слоя может оказывать благоприятный эффект для компенсации механических напряжений, вызванных высоким значением ТКЛР стали по сравнению с SiC-керамикой.
Рис. 15.
Общий вид (а) и РЭМ-изображения (б–г) поперечного среза образца ФГМ-композита, полученного по технологии ИПС с использованием многокомпонентной системы Ti–Ag–TiH2.
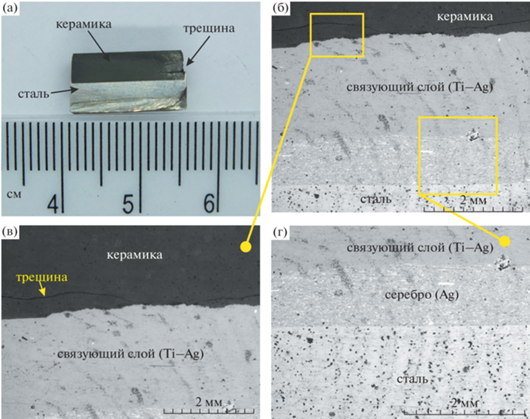
Рис. 16.
Карта распределения элементов (ЭДСА) по поверхности поперечного среза образца ФГМ-композита, полученного по технологии ИПС с использованием многокомпонентной системы Ti–Ag–TiH2.
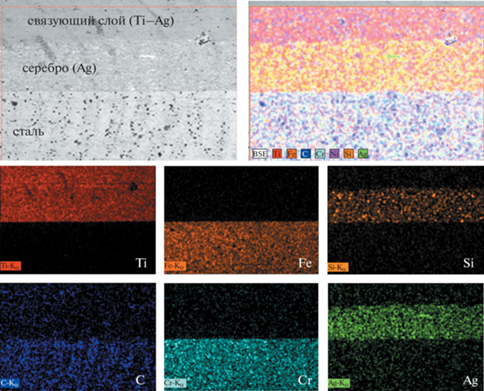
ФГМ-композит, соединенный с использованием металлических добавок в виде связующего и промежуточного плотного слоя молибдена. Эксперимент по получению соединенного композита реализовывали путем формирования промежуточного слоя металла в виде молибдена, расположенного между SiC-керамикой и сталью, имеющего более низкое значение ТКЛР, чем сталь, и близкое к керамике, а в качестве связующей добавки использовали систему Ti–Ag. По результатам эксперимента был получен образец соединенного ФГМ-композита (рис. 17а).
Рис. 17.
Общий вид (а) и РЭМ-изображение (б) поверхности поперечного среза образца ФГМ-композита, полученного по технологии ИПС с использованием металлических добавок в виде связующего (система Ti–Ag) и промежуточного слоя в виде демпфера (Mo).
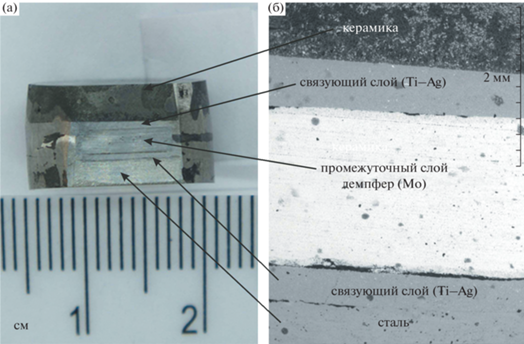
В ходе визуального контроля поверхности образца и его поперечного среза видимые дефекты (трещины) не выявлены (рис. 17а). На фотографии среза (рис. 17а), а также методами РЭМ (рис. 17б) и ЭДСА (рис. 18) показано, что структура образца представляет собой композит, состоящий из последовательно соединенных слоев: SiC-керамика/связующий слой Ti–Ag/Mo/связующий слой Ti–Ag/сталь. Слои характеризуются равномерными и бездефектными соединенными границами контактов. На РЭМ-снимке (рис. 17б) в некоторых локальных областях на границе контактов слоев обнаружены темные вкрапления, которые, по данным ЭДСА, соответствуют углероду (рис. 18). Его наличие может быть связано с пробоподготовкой образца для анализа (распиливание режущим инструментом и полировка абразивными материалами), в ходе которой он агломерировался на рельефной поверхности в виде примеси.
Рис. 18.
Карта распределения элементов (ЭДСА) по поверхности поперечного среза образца ФГМ-композита, полученного по технологии ИПС с использованием металлических добавок в виде связующего в составе с демпфером (система Ti–Ag) и промежуточного слоя в виде демпфера (Mo).
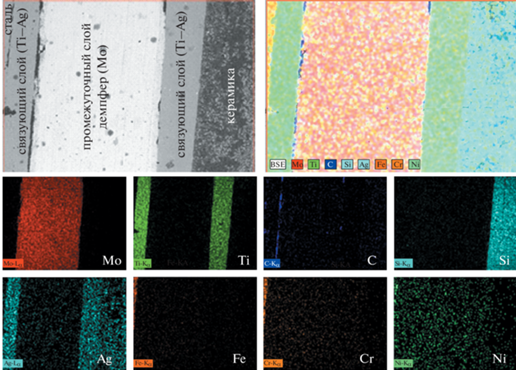
Эксперимент был продублирован, и результат формирования соединенного композита в отсутствие видимых дефектов был подтвержден. Следует отметить, что изготовление поперечного среза проводили с использованием алмазного режущего диска с трех разных сторон образца: со стороны керамики, со стороны стали, со стороны соединения керамики и стали. В результате на полученном срезе не было выявлено вновь образованных после механического воздействия дефектов (трещин) в каждом отдельном слое, что является важным показателем механической устойчивости образца, полученного предложенным способом.
Установлено, что в представленных выше экспериментах объемная деформация соединяемых образцов керамики и стали отсутствует, так как их геометрия формы остается неизменной.
ЗАКЛЮЧЕНИЕ
Проведен эксперимент по получению ФГМ-композита соединенного типа на основе SiC-керамики и стали Х18Н15 по технологии ИПС. Изучен фазовый состав и динамика консолидации дисперсного SiC при различном температурном нагреве, давлении прессования и времени выдержки в условиях ИПС. Установлено, что оптимальными условиями консолидации SiC-порошка в керамику с достижением относительной плотности >82% и микротвердости >500 HV без изменения фазового состава следует считать температуру нагрева не менее 1900°С, скорость разогрева от 100 град/мин, давление прессования не менее 50 МПа, время выдержки при максимальной температуре 5–10 мин. При этом показано, что физико-механические характеристики SiC-керамики могут быть улучшены при условии достижения температуры разогрева до 2100°С на оборудовании соответствующей мощности. Исследованы физико-химические основы формирования прочного соединения двухкомпонентной системы на основе образцов SiC-керамики и стали Х18Н15 способами диффузионного спекания без добавок и с использованием смеси добавок в виде металлического связующего, реакционного связующего и демпфера (системы добавок Ti–Ag, Ti–TiH2, Ti–Ag–TiH2 и Ti–Ag/Mo). Установлено, что формирование прочного соединенного ФГМ-композита целостной формы достигается по технологии ИПС за счет использования добавки Ti–Ag/Mo (соотношение смеси связующего и демпферного компонентов Ti–Ag составляло 70 : 30 мас. %) и плотного слоя молибдена, выполняющего роль демпфера для компенсации внутреннего напряжения за счет разницы величин ТКЛР. По данным РЭМ, полученный ФГМ-композит не имеет дефектов в объеме и на границе соединенных материалов керамики и стали. Ярко выраженной диффузии элементов между связующими слоями в композите, по данным ЭДСА, не выявлено. Отмечено незначительное проникновение серебра в приповерхностном слое керамики в области соединительного контакта, что связано с его частичным переходом в расплав и миграцией в поры керамического фрагмента. Согласно результатам исследования, предлагаемый способ формирования ФГМ-композитов соединенного типа указанного состава является перспективным и целесообразным для дальнейших исследований с получением образцов-демонстраторов конкретных изделий.
Список литературы
Kieback B., Neubrand A., Riedel H. // Mater. Sci. Eng. A. 2003. V. 362. № 1–2. P. 81. https://doi.org/10.1016/S0921-5093(03)00578-1
Saleh B., Jiang J., Fathi R. et al. // Compos. Part B. 2020. V. 201. P. 108376. https://doi.org/10.1016/j.compositesb.2020.108376
Sam M., Jojith R., Radhika N. // J. Manuf. Process. 2021. V. 68. P. 1339. https://doi.org/10.1016/S0921-5093(03)00578-1
Pasha A., B.M.R. // Mater. Today Proc. 2022. V. 52. P. 413. https://doi.org/10.1016/j.matpr.2021.09.077
Ruys A.J., Sutton B.A. // Met. Ceram., Elsevier. 2021. P. 327. https://doi.org/10.1016/B978-0-08-102869-8.00009-4
Martinsen K., Hu S.J., Carlson B.E. // CIRP Ann. 2015. V. 64. P. 679. https://doi.org/10.1016/j.cirp.2015.05.006
Uday M.B., Ahmad-Fauzi M.N., Noor A.M. et al. // Current Issues and Problems in the Joining of Ceramic to Metal. Join. Technol., InTech, 2016. P. 159–193. https://doi.org/10.5772/64524
Zhang Y., Chen Y.K., Yu D.S. et al. // J. Mater. Res. Technol. 2020. V. 9. № 6. P. 16214. https://doi.org/10.1016/j.jmrt.2020.11.088
Hausner S., Wielage B. // Adv. Brazing Sci. Technol. Appl., Woodhead Publishing Limited, 2013. P. 361–393. https://doi.org/10.1533/9780857096500.2.361
Nascimento R.M. do, Martinelli A.E., Buschinelli A.J.A. // Cerâmica. 2003. V. 49. № 312. P. 178. https://doi.org/10.1590/s0366-69132003000400002
Hu Z.Y., Zhang Z.H., Cheng X.W. et al. // Mater. Des. 2020. V. 191. P. 108662. https://doi.org/10.1016/j.matdes.2020.108662
Simonenko E.P., Simonenko N.P., Sevastyanov V.G. et al. // Russ. J. Inorg. Chem. 2019. V. 64. № 14. P. 1697. https://doi.org/10.1134/S0036023619140079
Papynov E.K., Portnyagin A.S., Modin E.B. et al. // Mater. Charact. 2018. V. 145. P. 294. https://doi.org/10.1016/j.matchar.2018.08.044
Simonenko E.P., Simonenko N.P., Nagornov I.A. et al. // Russ. J. Inorg. Chem. 2021. V. 66. № 12. P. 1887. https://doi.org/10.1134/S0036023621120172
Shapkin N.P., Papynov E.K., Shichalin O.O. et al. // Russ. J. Inorg. Chem. 2021. V. 66. № 5. P. 629. https://doi.org/10.1134/S0036023621050168
Papynov E.K., Shichalin O.O., Buravlev I.Y. et al. // Russ. J. Inorg. Chem. 2020. V. 65. № 2. P. 263. https://doi.org/10.1134/S0036023620020138
Shichalin O.O., Frolov K.R., Buravlev I.Y. et al. // Russ. J. Inorg. Chem. 2020. V. 65. № 8. P. 1245. https://doi.org/10.1134/S0036023620080148
Simonenko E.P., Simonenko N.P., Gordeev A.N. et al. // Russ. J. Inorg. Chem. 2018. V. 63. № 4. P. 421. https://doi.org/10.1134/S0036023618040186
Shichalin O.O., Buravlev I.Y., Portnyagin A.S. et al. // J. Alloys Compd. 2020. V. 816. P. 152547. https://doi.org/10.1016/j.jallcom.2019.152547
Shichalin O.O., Buravlev I.Y., Papynov E.K. et al. // Int. J. Refract. Met. Hard Mater. 2022. V. 102. P. 105725. https://doi.org/10.1016/j.ijrmhm.2021.105725
Buravlev I.Y., Shichalin O.O., Papynov E.K. et al. // Int. J. Refract. Met. Hard Mater. 2021. V. 94. P. 105385. https://doi.org/10.1016/j.ijrmhm.2020.105385
Naveen Kumar N., Janaki Ram G.D., Bhattacharya S.S. // Trans. Indian Inst. Met. 2019. V. 72. № 7. P. 1837. https://doi.org/10.1007/s12666-019-01662-8
Tsakiris V., Kappel W., Talpeanu D. et al. // Adv. Mater. Res. 2014. V. 1029. P. 200. https://doi.org/10.4028/www.scientific.net/AMR.1029.200
Okuni T., Miyamoto Y., Abe H. et al. // Ceram. Int. 2014. V. 40. P. 1359. https://doi.org/10.1016/j.ceramint.2013.07.017
Rizzo S., Grasso S., Salvo M. et al. // J. Eur. Ceram. Soc. 2014. V. 34. № 4. P. 903. https://doi.org/10.1016/j.jeurceramsoc.2013.10.028
Miriyev A., Barlam D., Shneck R. et al. // J. Mater. Process. Technol. 2014. V. 214. № 12. P. 2884. https://doi.org/10.1016/j.jmatprotec.2014.06.026
Miriyev A., Stern A., Tuval E. et al. // J. Mater. Process. Technol. 2013. V. 213. № 2. P. 161. https://doi.org/10.1016/j.jmatprotec.2012.09.017
Zhang B., Chen C., He J. et al. // Materials (Basel). 2020. V. 13. № 15. P. 1. https://doi.org/10.3390/ma13153300
Dudina D.V., Matvienko A.A., Sidelnikov A.A. et al. // Mater. Today Proc. 2019. V. 16. P. 187. https://doi.org/10.1016/j.matpr.2019.05.242
Dudina D.V., Matvienko A.A., Sidelnikov A.A. et al. // Metals (Basel). 2018. V. 8. № 7. https://doi.org/10.3390/met8070538
Хениш Г., Рой Р. // Карбид кремния. М., 1972.
Bokhonov B.B., Ukhina A.V., Dudina D.V. et al. // RSC Adv. 2015. V. 5. № 98. P. 80228. https://doi.org/10.1039/C5RA15439A
Bernard–Granger G., Benameur N., Guizard C. et al. // Scr. Mater. 2009. V. 60. № 3. P. 164. https://doi.org/10.1016/j.scriptamat.2008.09.027
Bertrand A., Carreaud J., Delaizir G. et al. // J. Am. Ceram. Soc. 2014. V. 97. № 1. P. 163. https://doi.org/10.1111/jace.12657
Papynov E.K., Shichalin O.O., Mironenko A.Y. et al. // Radiochemistry. 2018. V. 60. № 4. P. 362. https://doi.org/10.1134/S1066362218040045
Дополнительные материалы отсутствуют.
Инструменты
Журнал неорганической химии