Журнал неорганической химии, 2023, T. 68, № 1, стр. 17-25
Получение NASICON состава Na3Zr2Si2PO12 пиролизом органических растворов: особенности фазообразования
Д. Н. Грищенко a, *, В. Г. Курявый a, А. Б. Подгорбунский a, М. А. Медков a
a Институт химии ДВО РАН
690022 Владивосток, пр-т 100-летия Владивостока, 159, Россия
* E-mail: grishchenko@ich.dvo.ru
Поступила в редакцию 01.07.2022
После доработки 08.08.2022
Принята к публикации 27.08.2022
- EDN: GVETOJ
- DOI: 10.31857/S0044457X22601043
Аннотация
Разработан новый перспективный способ синтеза NASICON (Na3Zr2Si2PO12) пиролизом органических растворов. В качестве прекурсоров использованы олеат натрия, олеат цирконила, трибутилфосфат, тетраэтоксисилан. Установлены мольные отношения компонентов смеси для образования NASICON. Доказано влияние натрия на образование фазы диоксида циркония. Получен мелкодисперсный материал со средним размером зерна 0.2 мкм. Исследованы изменения морфологии и состава в зависимости от времени и температуры обжига образца. Результаты подтверждены методами рентгенофазового анализа и растровой электронной микроскопии. Для уточнения параметров кристаллической решетки выполнен полнопрофильный анализ методом Ритвельда. Процесс получения NASICON занимает ~9 ч, т.е. он наименее длительный из всех альтернативных способов его синтеза. Преимущества данного метода заключаются в возможности снижения температуры спекания, отсутствии необходимости контролировать множество параметров во время синтеза, минимизации длительности и многостадийности процесса. Метод способствует разработке и получению более перспективных ион-замещенных структур.
ВВЕДЕНИЕ
Соединения со структурой NASICON и химической формулой Na1 +xZr2SixР3 –xO12, где 0 < x < 3, известны уже более пятидесяти лет. Основные исследования сосредоточены на составах 1.8 < x < 2.2, так как именно в этом диапазоне NASICON обладает более высокой ионной проводимостью [1, 2]. В настоящее время разработаны перспективные материалы на основе данного структурного типа, где Na, Zr и/или Si заменены изовалентными элементами [2, 3]. Соединения NASICON могут быть получены в виде поликристаллических керамических компактов, монокристаллов или тонких пленок в зависимости от назначения материала. Основное применение этого типа соединений – твердый электролит в натрий-ионной аккумуляторной батарее. Тонкие или толстые пленки твердого электролита NASICON используются для ионоселективных электродов или газовых сенсорных устройств [4–6].
В настоящее время существует множество методов синтеза NASICON: твердофазный [7–9], золь-гель [10–12], негидролитический [13], соосаждение [14], механохимический синтез [15] и др. Основными считаются твердофазный и золь-гель методы. Первый основан на несколько раз повторяющихся стадиях длительного механического измельчения, прессования и спекания материала при высоких температурах (обычно ~1200°C). Главные недостатки метода – многостадийность и длительность процесса, который занимает 30–50 ч. Золь-гель метод основан на процессах контролируемого гидролиза соединений в водной, органической или спиртовой среде. Известно, что золь-гель метод позволяет получить NASICON с большей однородностью и меньшим размером зерна при более низких температурах. Однако необходимость контролировать множество параметров во время синтеза (pH, скорость добавления компонентов, температуру растворов) вносит существенные трудности в процесс, который занимает обычно 20–30 ч.
Получить чистый продукт предлагаемыми методами достаточно сложно. Синтез NASICON обычно сопровождается образованием дополнительных фаз: SiO2, ZrSiO4, Na3PO4, Na2SiO3. Чаще всего это ZrO2 моноклинной или тетрагональной сингонии. Присутствие примесных фаз может значительно ухудшить характеристики созданных керамических материалов. Считается, что диоксид циркония и различные силикатные фазы снижают ионную проводимость электролитов [16]. Фосфаты и аморфные стеклообразные фазы признаны химически нестабильными [17], и их наличие в NASICON приводит к ограниченной практической применимости материалов. Идентификация вторичных фаз имеет решающее значение для определения их потенциального влияния на характеристики NASICON.
Цель настоящей работы – разработка метода синтеза NASICON пиролизом органических растворов. Изучение фазообразования, зависящего от состава прекурсора, и условий обработки материала.
ЭКСПЕРИМЕНТАЛЬНАЯ ЧАСТЬ
Исходными компонентами прекурсора служили олеат цирконила (C36H66O5Zr, 98%, Реахим, Россия), олеат натрия (C18H33O2Na, 98%, Sigma Aldrich, Germany), трибутилфосфат (C12H27O4P, 99%, Acros Organics, USA), тетраэтоксисилан (C8H20O4Si, 99.5%, Реахим, Россия). В качестве органического растворителя использовали толуол (C7H8, 99.5%, Компонент-Реактив, Россия).
Рассчитанные количества олеатов натрия и цирконила растворяли в толуоле при температуре 60–70°С. В полученный прозрачный органический раствор добавляли трибутилфосфат и тетраэтоксисилан, перемешивали и выполняли отгонку растворителя при температуре 110°С. Смесь компонентов подвергали термической обработке в муфельной печи Nabertherm L5/13/B180 при 60°С в течение 30 мин для формирования аморфного порошка. Нагрев осуществляли со скоростью 5 град/мин, остывание происходило в открытом муфеле без извлечения образца. Остывший образец измельчали ручным сухим способом в течение 1 мин и подвергали обжигу при температуре 700–1300°С в течение 30 мин. Нагрев осуществляли со средней скоростью 9 град/мин, остывание происходило в открытом муфеле без извлечения образца. Получены порошки NASICON состава Na3Zr2Si2PO12.
Состав изготовленного материала исследовали методом рентгенофазового анализа (РФА) на дифрактометре Stoe Stadi P c использованием программы поиска EVA и базы порошковых данных ICDD PDF-2. Для определения качественного и количественного элементного состава, а также морфологии образцов использовали метод растровой электронной микроскопии. Изображение поверхности объекта с высоким пространственным разрешением снимали на электронном сканирующем микроскопе Hitachi S5500. Параметры кристаллической решетки полученного материала уточняли методом Ритвельда с помощью программы FULLPROF. Расчет производили для моноклинной фазы Na3Zr2Si2PO12 с пр. гр. С2/с и параметрами решетки: a = 15.6513, b = 9.055, c = = 9.2198 Å, β = 123.742° (PDF 01-084-1200).
Электропроводность измеряли при комнатной температуре методом электрохимической импедансной спектроскопии по двухэлектродной схеме с использованием анализатора частотного отклика SI 1260 и Dielectric Interface 1296 (Solartron). Частотный диапазон измерений составил 1 Гц–1 МГц с разверткой 10 точек на декаду, амплитуда возбуждающего сигнала – 0.5 В. Удельную электропроводность (σ) рассчитывали путем моделирования полученных импедансных спектров методом эквивалентной электрической цепи с помощью программы ZView (Scribner Association) с учетом геометрии образца по формуле σ = l/RbS, где l – толщина таблетки, S – площадь электрода, Rb – объемное сопротивление, рассчитанное при моделировании экспериментальных данных. Пробоподготовку осуществляли посредством холодного прессования (давление 140 и 300 МПа) порошка керамики в таблетки диаметром 15 мм, толщиной 1.8–3 мм с последующим нанесением серебряной токопроводящей краски. Использовали порошок керамики, отожженный при 1100°С в течение 30 мин.
РЕЗУЛЬТАТЫ И ОБСУЖДЕНИЕ
Исследования показали, что смешивание исходных компонентов в стехиометрическом соотношении (Na : Zr : Si : P = 3 : 2 : 2 : 1) позволяет получить продукт, состоящий из трех фаз: моноклинного Na3Zr2Si2PO12 (PDF 01-084-1200), триклинного Na2ZrSi2O7 (PDF 00-039-0209) и тетрагонального ZrO2 (PDF 01-079-1769). Опытным путем установлено, что образование максимально чистого целевого продукта (Na3Zr2Si2PO12) происходит при мольном соотношении компонентов 3.2 : 2.1 : 2 : 1.4, т.е. при сверхстехиометрических количествах Na, Zr, P.
Недостаток фосфора при стехиометрическом смешивании может быть связан с его частичным удалением в газовую фазу в виде фосфорного ангидрида. Вследствие этого исходная смесь компонентов становится дефицитной по содержанию элемента, что провоцирует образование Na2ZrSi2O7. О потерях фосфора сообщалось в ряде исследований, где использовались иные методы синтеза [10, 18]. Недостаток циркония вызывает кристаллизация ZrO2, которая происходит перед образованием NASICON. Известно [14], что это приводит к отклонению от стехиометрии смеси и препятствует формированию Na3Zr2Si2PO12. Недостаток натрия связан, скорее всего, с его участием в образовании незначительных по количеству фаз, которые не обнаруживает РФА. Они могут быть выявлены методом электронной микроскопии при тщательном изучении образцов. Например, установлено присутствие нетипичных для NASICON кристаллов в форме уплощенных призм со средними размерами 0.3 × 0.6 × 3 мкм (рис. 1а). Выявлены также кристаллы в форме шестиугольной призмы с размерами 0.2 × 0.2 × × 0.3 мкм (рис. 1б). Энергодисперсионные спектры показывают наличие большого количества Na в их составе (рис. 2а, 2б). Для сравнения на рис. 2в представлен энергодисперсионный спектр NASICON. Принадлежность кристаллов к тому или иному соединению определить не удалось ввиду спектрального рассеяния от прилегающих зон. Предположительно, это кристаллы карбоната натрия. В работах [5, 9] сообщали о необходимости добавлять Na выше стехиометрических количеств, ссылаясь на его улетучивание из прекурсора при получении NASICON. Но соединения натрия, используемые в синтезе, не являются летучими. Например, в твердофазном методе недостаток натрия чаще всего вызван непрореагировавшими исходными Na-содержащими соединениями [6].
Рис. 2.
Энергодисперсионные спектры образца в областях сканирования, отмеченных на рис. 1: 1 (а); 2 (б); 3 (в).
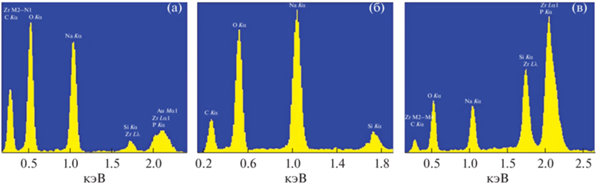
В то же время нами установлено, что увеличение концентрации только натрия в исходной смеси приводит к повышению содержания паракелдышита (Na2ZrSi2O7) в образце. Это обусловлено тем, что соотношение Na : Zr в Na2ZrSi2O7 составляет 2 : 1, а в NASICON – 1.5 : 1. Полученные данные согласуются с результатами работы [1], где добавление натрия и кремния в прекурсор (использовано соединение Na2SiO3 в количестве 7 мас. %) сопровождается появлением в образце NASICON примесей Na2ZrSi2O7 и Na3PO4. Нами также выявлено, что повышение концентрации только циркония в исходной смеси увеличивает содержание фазы ZrO2 в конечном продукте. Причем кроме тетрагонального появляется и моноклинный диоксид циркония. В процессе экспериментов установлено, что одновременное увеличение количеств Na и Zr в исходной смеси является необходимым условием для минимизации примесных фаз.
Обжиг состава с мольным соотношением компонентов 3.2 : 2.1 : 2 : 1.4 после отгонки растворителя сопровождается следующими фазовыми превращениями: при 600°С образуется рентгеноаморфный продукт; при 700°С появляется фаза тетрагонального ZrO2; в интервале температур 800–900°С образуется Na3Zr2Si2PO12 (рис. 3). При дальнейшем увеличении температуры обнаружена тенденция к уменьшению относительного количества ZrO2. Снижение содержания указанной фазы с увеличением температуры отмечено в работе [14]. Авторы предполагают, что тетрагональный ZrO2 является промежуточным продуктом образования Na3Zr2Si2PO12.
Рис. 3.
Дифрактограммы синтезированного образца при различных температурах обжига прекурсора: 1 – 600; 2 – 700; 3 – 800; 4 – 900°С.

Результаты наших исследований свидетельствуют о возможности образования Na3Zr2Si2PO12 при смешивании исходных компонентов в диапазоне мольных соотношений 3.2 : 2.1 : 2 : 1.4–3.6 : : 2.4 : 2 : 1.4, т.е. 20%-ное увеличение Zr в системе при одновременном увеличении Na с сохранением отношения Na : Zr = 1.5 не влечет образования дополнительных фаз или увеличения фазы ZrO2. Таким образом, дополнительные количества Na препятствуют образованию фазы ZrO2 в NASICON. Это согласуется с результатами работы [1], в которой установлено, что избыток Na сдерживает появление ZrO2. Именно образование ZrO2 негативно сказывается на значениях ионной проводимости керамики [19] вследствие фазового перехода, сопровождающегося изменением объема и приводящего к образованию трещин в электролите. Известно [1, 18, 20], что введение в прекурсор дополнительных количеств Na-содержащих компонентов (в пределах 5–10 мас. %) приводит к увеличению проводимости NASICON. Причины изменения исследователи связывают с увеличением постоянных решетки и, как следствие, увеличением в каркасной структуре керамики размера канала, необходимого для миграции Na. По-видимому, снижение содержания примесной фазы ZrO2 за счет дополнительных количеств Na можно рассматривать в качестве одной из причин увеличения ионной проводимости материала. Следует отметить, что для сохранения чистоты конечного продукта в нашей системе возможно лишь незначительное превышение Na в стехиометрическом для NASICON отношении Na : Zr = = 1.5, иначе в качестве примеси в образцах появляется паракелдышит. Допустимое значение отношения находится в пределах 1.5 < Na : Zr < 1.6.
Для дальнейших исследований и сравнения выбраны образцы с мольными соотношениями компонентов 3.2 : 2.1 : 2 : 1.4 (NAS1) и 3.6 : 2.4 : 2 : 1.4 (NAS2). Известно, что с увеличением температуры и длительности обжига материала в его составе появляются дополнительные фазы, влияющие на свойства конечного продукта. В связи с этим исследована устойчивость обоих образцов к изменению температурного и временного режима обработки. На рис. 4 представлены результаты обжига образцов NAS1 и NAS2 в течение 30 мин в интервале температур 1000–1300°С.
Фаза ZrO2 тетрагональной сингонии присутствует в NAS1 в качестве дополнительной фазы в следовых количествах при всех температурах обжига прекурсора (рис. 4а), что связано, как указано ранее, с более ранней кристаллизацией ZrO2 перед образованием NASICON. Содержание этой фазы в образце NAS2 гораздо выше (рис. 4б). Фаза ZrO2 моноклинной сингонии появляется в NAS1 при температуре 1300°С (рис. 4а). Рентгенофазовый анализ образца NAS2 выявляет эту фазу уже при 1200°С, и с увеличением температуры ее содержание растет (рис. 4б). Примечательно, что возрастание не происходит за счет изменения концентрации тетрагонального ZrO2, а, следовательно, за счет содержания циркония в целевой фазе. Установлено влияние времени спекания на фазовый состав материала. Образец NAS2 более устойчив к длительной температурной обработке, чем NAS1. Фаза моноклинного ZrO2 появляется у него при девятичасовом обжиге (рис. 5б), тогда как у NAS1 эта фаза наблюдается уже при шестичасовой обработке (рис. 5а). Для чистоты эксперимента обжиг проводили при температуре 1100°С, при которой в дифракционных картинах обоих образцов моноклинный ZrO2 не наблюдается.
Рис. 5.
Дифрактограммы образцов NAS1 (а) и NAS2 (б) с длительностью обжига при 1100°С: 1 – 3; 2 – 6; 3 – 9 ч.
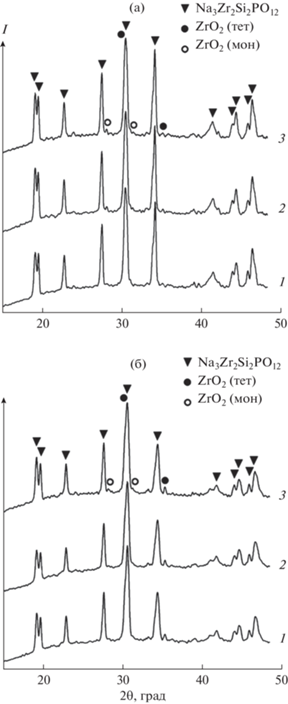
Условия обжига образцов отражаются на изменении параметров элементарной ячейки NASICON (табл. 1). Установлено, что с повышением температуры обжига параметры ячейки в основном существенно снижаются, тогда как с увеличением длительности обжига незначительно возрастают. Поскольку не все значения меняются пропорционально, объем элементарной ячейки является более показательной величиной. Результаты указывают на то, что изменение объема элементарных ячеек образцов NAS1 и NAS2 происходит с сохранением общей тенденции, характерной для определенного режима обработки материала. Наблюдаются различия в величинах. Объем элементарной ячейки для образца NAS1 находится в пределах 1085.057–1086.686 Å3, а для NAS2 – в пределах 1086.179–1088.256 Å3.
Таблица 1.
Изменение параметров элементарной ячейки кристаллической решетки NASICON в зависимости от температуры и времени обжига образцов
Образец | Температура обжига, °С | Длительность обжига, ч | Параметры элементарной ячейки, Å, град | Объем элементарной ячейки, Å3 | |||
---|---|---|---|---|---|---|---|
a | b | c | β | ||||
NAS1 | 1000 | 0.5 | 15.6953 | 9.0644 | 9.2349 | 124.197 | 1086.686 |
NAS1 | 1100 | 0.5 | 15.6834 | 9.0712 | 9.2199 | 124.068 | 1086.569 |
NAS1 | 1200 | 0.5 | 15.6874 | 9.0713 | 9.2102 | 124.058 | 1085.843 |
NAS1 | 1300 | 0.5 | 15.6745 | 9.0720 | 9.2053 | 124.011 | 1085.057 |
NAS1 | 1100 | 3 | 15.6846 | 9.0665 | 9.2119 | 124.031 | 1085.620 |
NAS1 | 1100 | 6 | 15.6896 | 9.0728 | 9.2099 | 124.073 | 1085.947 |
NAS1 | 1100 | 9 | 15.6916 | 9.0723 | 9.2117 | 124.094 | 1085.968 |
NAS2 | 1000 | 0.5 | 15.6575 | 9.0929 | 9.2568 | 124.336 | 1088.256 |
NAS2 | 1100 | 0.5 | 15.6280 | 9.0869 | 9.2283 | 123.928 | 1087.383 |
NAS2 | 1200 | 0.5 | 15.6288 | 9.0732 | 9.2278 | 123.875 | 1086.416 |
NAS2 | 1300 | 0.5 | 15.6354 | 9.0636 | 9.2281 | 123.842 | 1086.179 |
NAS2 | 1100 | 3 | 15.6150 | 9.0922 | 9.2380 | 124.030 | 1086.950 |
NAS2 | 1100 | 6 | 15.6136 | 9.0937 | 9.2415 | 124.029 | 1087.456 |
NAS2 | 1100 | 9 | 15.6111 | 9.1002 | 9.2453 | 124.075 | 1087.917 |
С изменением температуры обжига меняется морфология образцов. На рис. 6 представлены микрофотографии NAS1, отожженного при температурах 1000–1300°С. Образец NAS2 в указанном температурном интервале выглядит аналогично. Обжиг прекурсора при 1000°С позволяет формироваться материалу, границы зерен которого четко не определены (рис. 6а). Это указывает на наличие аморфной фазы вокруг зерна. Фаза агломерирует частицы, поэтому размер зерна можно назвать лишь условно 0.1–0.2 мкм. Образцы, полученные при 1100°С, характеризуются сравнительно однородным размером зерен 0.1–0.3 мкм с достаточно четкими контурами (рис. 6б). Форма кристаллов – неправильные многогранники. В образцах, отожженных при 1200°С, наблюдаются неоднородные по форме частицы. Средний размер зерен, имеющих форму многогранников, составляет 0.4 мкм. Отдельные частицы имеют кубическую форму, они крупнее многогранников и достигают размера 0.7 мкм (рис. 6в). Обжиг материала при 1300°С формирует кристаллы размером 0.4–0.8 мкм (рис. 6г). Присутствуют кристаллы кубической формы. Энергодисперсионные спектры, снятые для различных видов кристаллов, свидетельствуют об их идентичном составе. Результаты исследований указывают на тенденцию к увеличению размера зерна с повышением температуры спекания материала.
Рис. 6.
Микрофотографии образца NAS1, полученного при разных температурах обжига: а – 1000, б – 1100, в – 1200, г – 1300°С.
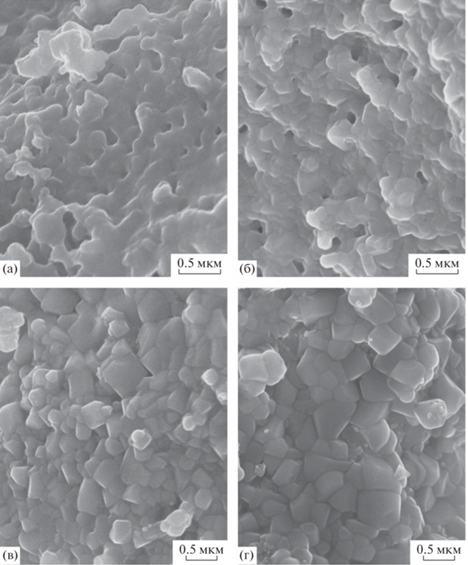
Изучено изменение морфологии образцов с увеличением длительности обжига, который осуществляли при температуре 1100°С. Микрофотографии NAS1 (рис. 7) свидетельствуют об уплотнении материала за счет увеличения размера зерна. Размер зерен после трехчасового обжига менее однородный, чем у образцов с получасовой выдержкой, и составляет 0.2–0.4 мкм, после шестичасового обжига – 0.2–0.5 мкм, после девятичасового – 0.2–0.8 мкм. Форма кристаллов – неправильные многогранники. Для образца NAS2 получены аналогичные результаты. Отдельно хочется отметить, что электронная микроскопия не выявила каких-либо признаков фазы ZrO2 в синтезированном материале. В работе [21] высказано предположение, что соединение присутствует в образцах не в виде дискретных частиц, а в виде непрерывной фазы, локализованной на границах зерен.
Рис. 7.
Микрофотографии образца NAS1, полученного при 1100°С, с длительностью обжига: а – 3, б – 6, в – 9 ч.
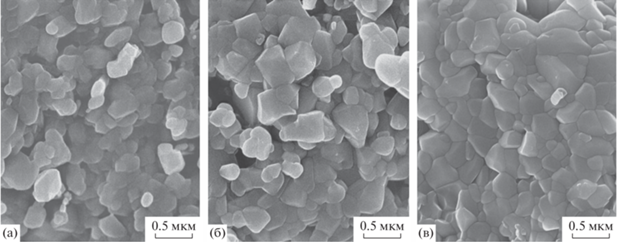
Лучшие значения электрической проводимости (1.2 × 10–3–1.8 × 10–3 См/см) показывают образцы NASICON, полученные методом искрового плазменного спекания [22]. Для материалов, изготовленных традиционными методами, характерны следующие значения: 8.57 × 10–5–1.28 × × 10–3 См/см. Большой разброс данных в основном объясняется разной плотностью и микроструктурой образцов, что напрямую связано с условиями их обработки и прессования. Так, например, в работах [16, 21] материал прессовали при 98 МПа, в работах [1, 19] – при 150 МПа, в [14] – при 300 МПа, а в [12] – при 500 МПа. Длительность спекания полученных твердотельных образцов также существенно различалась и составляла от 6 до 40 ч. Как известно [11, 12, 14], указанные условия подготовки материала являются ключевым фактором, определяющим показатели проводимости для исследуемых материалов.
Нами была изучена электропроводность образцов NAS1 и NAS2 в зависимости от условий обработки материала. Прессованию подвергали порошок NASICON, отожженный при 1100°С в течение 30 мин. Результаты представлены в табл. 2. Удельная проводимость твердотельного образца NAS2, изготовленного при 140 МПа без последующего спекания, составляет 1.23 × 10–5 См/см. Четырехчасовой обжиг спрессованного материала приводит к двукратному увеличению показателя. Прессование при 300 МПа и последующий обжиг увеличивают проводимость еще в ~2 раза. Спрессованный при 300 МПа без обжига образец NAS1 имеет практически такое же значение проводимости, как подвергнутый четырехчасовому обжигу NAS2. Таким образом, несмотря на сходство морфологии и фазового состава обоих образцов, NAS1 имеет лучшие показатели проводимости, чем NAS2. Скорее всего, это связано с наличием в составе NAS2 более высокого содержания ZrO2 тетрагональной сингонии. Хотя принято считать, что общую проводимость керамики снижает в основном моноклинная фаза [6]. Из всего вышесказанного следует, что изменение условий подготовки твердотельного материала и его обработки существенно влияет на электропроводность. В нашем случае максимальную проводимость должен иметь образец, спекаемый 3–4 ч при 1100°С из рентгеноаморфного порошка, полученного при 600°С на одном из этапов синтеза.
Таблица 2.
Результаты исследования электрической проводимости твердотельных образцов NAS1 и NAS2
Образец | Прессование образца, МПа | Длительность спекания, ч | Удельная электропроводность, См/см |
Диапазон частот расчета Rb, кГц |
---|---|---|---|---|
NAS2 | 140 | 0 | 1.23 × 10–5 | 15.8–630.9 |
NAS2 | 140 | 4 | 2.42 × 10–5 | 25.1–794.3 |
NAS2 | 300 | 4 | 4.55 × 10–5 | 39.8–630.9 |
NAS1 | 300 | 0 | 4.46 × 10–5 | 12.6–398.1 |
ЗАКЛЮЧЕНИЕ
Впервые синтезирован NASICON состава Na3Zr2Si2PO12 методом пиролиза смеси органических растворов. Образование NASICON с минимальным количеством примесных фаз происходит при следующих условиях: мольные соотношения компонентов Na : Zr : Si : P соответствуют интервалу 3.2 : 2.1 : 2 : 1.4–3.6 : 2.4 : 2 : 1.4; температура колеблется в пределах 1000–1100°С; длительность спекания составляет 0.5–3 ч. В результате экспериментов получен порошок со средним размером зерна 0.2 мкм и примесью тетрагонального диоксида циркония. Наличие ZrO2 тетрагональной сингонии вместо моноклинной предотвратит фазовый переход при производстве твердотельного электролита из порошкового материала.
Предложенный метод позволяет получать мелкодисперсные гомогенные порошки, способствующие более высокому уплотнению материала, что считается предпосылкой хорошей ионной проводимости NASICON. Время синтеза продукта составляет в среднем 9 ч и является минимальным из всех известных методов производства материала. Альтернативные методы уступают представленному по длительности процесса, энергоемкости и трудозатратам.
Список литературы
Wang H., Zhao G., Wang S. et al. // Nanoscale. 2022. V. 14. № 3. P. 823. https://doi.org/10.1039/d1nr06959d
Rao Y.B., Bharathi K.K., Patro L.N. // Solid State Ionics. 2021. V. 366–377. P. 115671. https://doi.org/10.1016/j.ssi.2021.115671
Майоров П.А., Асабина Е.А., Петьков В.И. и др. // Журн. неорган. химии. 2020. Т. 65. № 5. С. 660. https://doi.org/10.31857/S0044457X2005013X
Kim H.J., Choi J.W., Kim S.D., Yoo K.S. // Mater. Sci. Forum. 2007. V. 544–545. P. 925. https://doi.org/10.4028/www.scientific.net/MSF.544-545.925
Tetsuya K., Miyachi Y., Shimanoe K., Yamazoe N. // Sens. Actuators, B: Chem. 2001. V. 80. № 1. P. 28. https://doi.org/10.1016/S0925-4005(01)00878-4
Paściak G., Mielcarek W., Prociów K., Warycha J. // Ceram. Int., Part. B. 2014. V. 40. № 8. P. 12783. https://doi.org/10.1016/j.ceramint.2014.04.132
Jalalian-Khakshour A., Phillips Ch., Jackson L. et al. // J. Mater. Sci. 2020. V. 55. P. 2291. https://doi.org/10.1007/s10853-019-04162-8
Naqash S., Sebold D., Tietz F., Guillon O. // J. Am. Ceram. Soc. 2019. V. 102. № 3. P. 1057. https://doi.org/10.1111/jace.15988
Yang G., Zhai Y., Yao J. et al. // Chem. Commun. 2021. V. 57. P. 4023. https://doi.org/10.1039/d0cc07261c
Zhang S., Quan B., Zhiyong Z., Zhao B. // Mater. Lett. 2004. V. 58. № 1. P. 226. https://doi.org/10.1016/S0167-577X(03)00450-6
Porkodi P., Yegnaraman V., Kamaraj P. et al. // Chem. Mater. 2008. V. 20. № 20. P. 6410. https://doi.org/10.1021/cm800208k
Shimizu Y., Azuma Y., Michishita S. // J. Mater. Chem. 1997. V. 7. P. 1487.
Zhou M. // Sens. Actuators, B: Chem. 2007. V. 122. № 2. P. 419. https://doi.org/10.1016/j.snb.2006.06.011
Ignaszak A., Pasierb P., Gajerski R., Komornicki S. // Thermochim. Acta. 2005. V. 426. № 1–2. P. 7. https://doi.org/10.1016/j.tca.2004.07.002
Fuentes R.O., Figueiredo F., Soares M.R., Marques F.-M.B. // J. Eur. Ceram. Soc. 2005. V. 25. № 4. P. 455. https://doi.org/10.1016/j.jeurceramsoc.2004.02.019
Fuentes R.O., Marques F.M.B., Franco J.I. // Bol. Soc. Esp. Cerám. Vidrio. 1999. V. 38. № 6. P. 631.
Fuentes R.O., Figueiredo F., Marques F.-M.B., Franco J.I. // Solid State Ionics. 2001. V. 139. № 3–4. P. 309. https://doi.org/10.1016/S0167-2738(01)00683-X
Narayanan S., Reid S., Butler S., Thangadurai V. // Solid State Ionics. 2019. V. 331. P. 22. https://doi.org/10.1016/j.ssi.2018.12.003
Naqash S., Ma Q., Tietz F., Guillon O. //Solid State Ionics. 2017. V. 302. P. 83. https://doi.org/10.1016/j.ssi.2016.11.004
Oh J.A.S., He L., Plewa A. et al. // ACS Appl. Mater. Interfaces. 2019. V. 11. № 43. P. 40125. https://doi.org/10.1021/acsami.9b14986
Fuentes R.O., Figueiredo F.M., Marques F.M.B., Franco J.I. // Solid State Ionics. 2001. V. 140. № 1–2. P. 173. https://doi.org/10.1016/S0167-2738(01)00701-9
Lee J.S., Chang C.M., Lee Y.I. et al. // J. Am. Ceram. Soc. 2004. V. 87. № 2. P. 305. https://doi.org/10.1111/j.1551-2916.2004.00305.x
Дополнительные материалы отсутствуют.
Инструменты
Журнал неорганической химии