Журнал неорганической химии, 2022, T. 67, № 7, стр. 1000-1006
Экстракционная переработка Ni-MH аккумуляторов с использованием систем с полипропиленгликолем 425
М. И. Федорова a, А. В. Левина a, Ю. А. Заходяева a, *, А. А. Вошкин a
a Институт общей и неорганической химии им. Н.С. Курнакова РАН
119991 Москва, Ленинский пр-т, 31, Россия
* E-mail: yz@igic.ras.ru
Поступила в редакцию 14.12.2021
После доработки 01.02.2022
Принята к публикации 07.02.2022
- EDN: FDKIWA
- DOI: 10.31857/S0044457X22070091
Аннотация
Показана перспективность совместной переработки катодного и анодного материалов Ni-MH аккумулятора. Проведено растворение в соляной кислоте элементов Ni-MH аккумулятора с последующим экстракционным разделением ионов Ni(II), Co(II), Mn(II), La(III), Al(III) и Zn(II) в двухфазных водных системах на основе полипропиленгликоля 425 с введением ди(2-этилгексил)фосфорной кислоты из солянокислых растворов выщелачивания. Установлено, что рассматриваемые системы позволяют с высокой эффективностью (от 60 до 90%) извлекать ионы Zn(II), Al(III), La(III). Полученные количественные характеристики экстракции исследуемых ионов металлов позволили разработать новую принципиальную технологическую схему переработки функциональных материалов Ni-MH аккумуляторов, позволяющую получать концентраты отдельных ионов металлов.
ВВЕДЕНИЕ
Перезаряжаемые аккумуляторы являются одним из наиболее перспективных источников энергии, их применяют повсеместно: в портативных электронных устройствах, электромобилях и т.д. [1]. Такие аккумуляторы включают в себя литий-ионные (Li-ion), никель-кадмиевые (Ni-Cd), свинцово-кислотные и никель-металлогидридные (Ni-MH) батареи [2]. Они содержат тяжелые металлы, классифицированные как канцерогены и мутагены, а при неправильной утилизации эти металлы могут нанести серьезный ущерб здоровью человека и окружающей среде [3]. Кроме того, некоторые металлы в составе аккумуляторов имеют высокую стоимость. Например, кобальт является стратегически важным металлом: он выступает незаменимым катодным материалом в Li-ion батареях [4], ключевым компонентом сплава Sm-Co магнитов [5], а поскольку его содержание в земной коре сопоставимо с запасами редкоземельных элементов (РЗЭ), возникает угроза выработки первичных источников кобальта, в связи с чем цена на него с каждым годом увеличивается. РЗЭ, входящие в состав аккумуляторных батарей, являются “критическими металлами”, они имеют огромное значение во всем мире, поскольку характеризуются низкой скоростью переработки [6], высокой стоимостью [7] и отсутствием металлов-заменителей [8].
Созданные и коммерциализированные в Японии в 1989 г. Ni-MH аккумуляторы являются наиболее широко используемыми перезаряжаемыми аккумуляторами, применяемыми в настоящее время [9]. Ni-MH батареи имеют ряд преимуществ: низкую скорость саморазряда, широкий диапазон рабочих температур, высокую электрохимическую емкость, длительный срок службы и экологическую безопасность [10]. Все это позволило им заменить более дешевые, но менее экологичные Ni-Cd аккумуляторы [11].
Переработка аккумуляторов включает два этапа: механическую обработку и выделение компонентов. Основными составляющими Ni-MH батарей являются катод, анод и анодная сетка. Катод в основном состоит из никеля и покрыт Ni(OH)2, в то время как анод представляет собой сплав никеля и мишметалла (церия, лантана и др.) [12]. Элементный состав Ni-MH аккумуляторов достаточно широк и включает в себя следующие элементы (мас. %): 17–63 Ni, 8–30 Fe, 12–17 редкоземельные металлы (La, Ce, Nd, Pr, Y), 3.7–5 Co, 1.7–3.1 K, 0.8–2.2 Zn, 0.7–2.3 Mn, 0.2–1.1 Al и другие металлы (Na, Ca, Ag, Pb, Cr, Cu, Ti, V), содержание которых составляет <1% [13]. После механической обработки применяют пирометаллургические [14, 15] или гидрометаллургические [16, 17] процессы, например, выщелачивание минеральными кислотами [18–21] или глубокими эвтектическими растворителями [22]. Известны работы, в которых переработку и извлечение металлов проводят, используя растворение целой батарейки [23], однако переработка отдельных составляющих может быть более эффективной [12]. Дальнейшее разделение и выделение металлов из полученных после выщелачивания растворов проводят при помощи осаждения [21, 24], методов жидкостной экстракции [16, 21, 25] и/или их комбинацией.
Жидкостная экстракция является энергосберегающим и дешевым методом концентрирования и разделения металлов с возможностью регенерации и повторного использования компонентов [26]. Традиционно для извлечения металлов из водных растворов в качестве экстрагентов применяют фосфорорганические (2-этилгексиловый эфир-2-этилгексилфосфорной кислоты [27], ди(2-этилгексил)фосфорная кислота (Д2ЭГФК) [28–30], бис(2,4,4-триметилфенил)фосфиновая кислота (Cyanex 272) [31]) или карбоновые [32] кислоты, соли четвертичных аммониевых оснований [33] и пр., растворенные в органических разбавителях. Поскольку данные экстрагенты обладают не только высокой эффективностью, но и селективностью по отношению к металлам, удается разделить даже близкие и сложно разделимые металлы. В работе [34] показано, что Д2ЭГФК при рН 2.5 способен извлекать около 75% Fe и 96% Zn; LIX 984 экстрагирует 99.9% Zn при рН 2–3, а Cyanex 302 способен извлекать ~97% Ni при рН 4.
Несмотря на то, что традиционные экстракционные методы имеют ряд преимуществ, они зачастую связаны с использованием органических растворителей, которые, в свою очередь, являются токсичными и пожароопасными [35]. Альтернативой растворителям служат системы на основе водорастворимых полимеров [36–38]. Водорастворимые полимеры биоразлагаемы, не токсичны и уже показали свою эффективность при экстракции ионов металлов из водных растворов [39]. Более того, двухфазные водные системы могут применяться в качестве экологичного разбавителя [40]. Отмечается, что со степенью извлечения >95% удается извлечь Fe(III) и Zn(II) из солянокислых водных растворов при введении Aliquat 336 в двухфазную водную систему на основе полипропиленгликоля 425. Также при введении в данную двухфазную водную систему роданида калия удается ступенчато разделить группу переходных металлов [41]. Степень извлечения не снижается при замене органического разбавителя на двухфазную водную систему.
Настоящая работа является продолжением исследований по экстракционному разделению металлов из солянокислых растворов выщелачивания элементов Ni-MH аккумуляторов. Ее цель заключается в разработке экстракционной системы на основе полипропиленгликоля 425 с добавлением органической кислоты и роданида калия для извлечения и разделения ионов металлов, содержащихся в составе катодного и анодного материалов Ni-MH аккумуляторов, а также в создании принципиальной технологической схемы на основании полученных экспериментальных данных.
ЭКСПЕРИМЕНТАЛЬНАЯ ЧАСТЬ
В экспериментах использовали цилиндрические Ni-MH аккумуляторы типоразмера АА емкостью 1900 мА ч и напряжением 1.2 В. Из одной батарейки массой 26.7 г после снятия внешнего корпуса были выделены активные элементы: катод (9.2 г), анодный порошок (9.2 г) и анодная сетка (0.9 г).
Растворение катодного и анодного порошка проводили 4 М соляной кислотой при 90°С в течение 6 ч в круглодонной колбе с обратным холодильником.
Разделение ионов металлов из раствора выщелачивания проводили в экстракционной системе на основе полипропиленгликоля 425 (Acros Organics, CAS № 25322-69-4) при температуре 25°С в градуированных пластиковых пробирках в термостатированном шейкере Enviro-Genie (Scientific Industries, Inc.) при скорости вращения 30 об/мин до установления термодинамического равновесия (30 мин).
Концентрацию ионов Ni(II), Co(II), Mn(II), La(III), Al(III) и Zn(II) в растворах выщелачивания и солевых и полимерных фазах после экстракции определяли методом атомно-эмиссионной спектрометрии с индуктивно связанной плазмой (Thermo Electron Corp., США).
Представленные экспериментальные данные являются результатом серии трех экспериментов и обработаны с использованием методов математической статистики.
РЕЗУЛЬТАТЫ И ОБСУЖДЕНИЕ
На первом этапе было проведено растворение катодного и анодного материала Ni-MH аккумуляторов в среде 4 М соляной кислоты. Условия эксперимента были следующие: 1) массовое соотношение кислота : тв. материал = 6 : 1 (для катода) и 8 : 1 (для анода); 2) время растворения 6 ч; 3) температура 90°С. Составы полученных растворов выщелачивания представлены в табл. 1. В виду того, что элементные составы растворов выщелачивания катода и анода близки, они были объединены в один для дальнейшей экстракционной переработки.
Таблица 1.
Элементный состав растворов выщелачивания катодного и анодного материалов Ni-MH аккумуляторов
Раствор выщелачивания | С(HCl), моль/л | Концентрации металлов, моль/л | |||||
---|---|---|---|---|---|---|---|
Ni(II) | La(III) | Zn(II) | Co(II) | Mn(II) | Al(III) | ||
Катод | 0.6 | 2.343 | – | 0.104 | 0.048 | 0.00699 | 0.00849 |
Анод | 2 | 1.983 | 0.292 | – | 0.321 | 0.104 | 0.0982 |
Объединенный раствор | 1.4 | 2.191 | 0.123 | 0.0605 | 0.163 | 0.048 | 0.0463 |
В качестве экстрагентов нами были выбраны ди(2-этилгексил)фосфорная кислота и роданид калия ввиду их высокой экстракционной эффективности по отношению к исследуемым металлам.
На первом этапе было предложено провести электроосаждение Ni и Co из объединенного раствора выщелачивания. Полученный раствор, содержащий Zn(II) (0.0605 моль/л), La(III) (0.123 моль/л), Mn(II) (0.048 моль/л) и Al(III) (0.0463 моль/л), вводили в экстракционную систему полипропиленгликоль 425–хлорид натрия–вода. Для определения наиболее благоприятных условий экстракции нами была проведена серия экспериментов по варьированию содержания хлорида натрия от 6 до 15 мас. % в экстракционной системе полипропиленгликоль 425 (30 мас. %)–NaCl–вода. На рис. 1 представлены зависимости степеней извлечения исследуемых ионов металлов от начального содержания соли в системе. Из рис. 1 видно, что при содержании соли 15 мас. % Е(Zn) = 60%, а степени извлечения других металлов не превышают 1%. Таким образом, двухфазная водная система полипропиленгликоль 425 (30 мас. %)–хлорид натрия (15 мас. %)–вода решает задачу отделения ионов цинка от ионов лантана, марганца и алюминия.
Рис. 1.
Зависимость степени извлечения исследуемых ионов металлов от начального содержания соли в системе полипропиленгликоль 425 (30 мас. %)–хлорид натрия–вода.
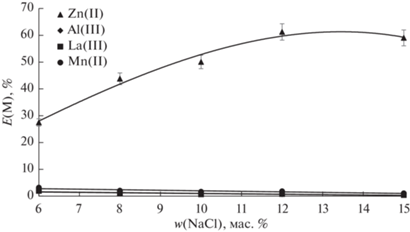
Рафинат, содержащий La(III), Mn(II) и Al(III), подвергали дальнейшему экстракционному разделению с использованием системы полипропиленгликоль 425 (38 мас. %)–NaCl (6 мас. %)–H2O с введением ди(2-этилгексил)фосфорной кислоты (1.36 моль/л), объемное соотношение полимерной и солевой фаз во всех экспериментах составляло 3 : 1. Концентрация экстрагента и соотношение фаз были выбраны для повышения растворимости образуемых экстрагируемых соединений лантана и алюминия. На первом этапе было исследовано влияние кислотности солевой фазы на экстракцию ионов La(III), Mn(II) и Al(III). На рис. 2 приведена зависимость степени извлечения металлов от рН равновесной солевой фазы. Из рис. 2 видно, что при повышении рН солевой фазы происходит увеличение степеней извлечения лантана и алюминия, что характерно для катионообменной экстракции [42]. Степень извлечения марганца во всем исследуемом диапазоне рН не превышает 7%.
Рис. 2.
Зависимость степени извлечения металлов от равновесного значения рН солевой фазы в системе полипропиленгликоль 425 (38 мас. %)–NaCl (6 мас. %)–H2O, С(Д2ЭГФК) = 1.36 моль/л.
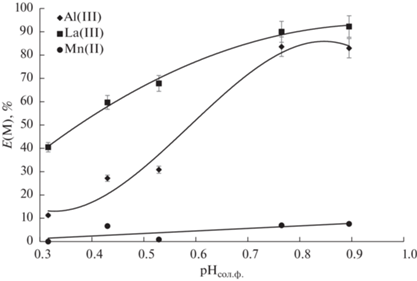
Далее было исследовано влияние концентрации Д2ЭГФК от 1.36 до 2.00 моль/л на экстракцию ионов La(III) (0.123 моль/л), Mn(II) (0.048 моль/л) и Al(III) (0.0463 моль/л) с равновесным значением рН 0.8–0.9. Поскольку исследуемые системы склонны к образованию третьей фазы (плохо растворимые комплексы металлов с Д2ЭГФК, растворимость которых повышается за счет введения избыточного количества экстрагента), нами не рассматривались меньшие количества кислоты. Необходимое значение кислотности солевой фазы поддерживалось путем введения 1 М раствора NaOH. На рис. 3 представлена зависимость степени извлечения ионов La(III), Mn(II) и Al(III) от концентрации Д2ЭГФК. Полученные зависимости линейно возрастают с увеличением концентрации экстрагента: для La(III) – от 90 до 99%, для Al(III) – от 83 до 97%, для Mn(II) – от 7 до 40%. Таким образом, для задачи отделения ионов лантана и алюминия от ионов марганца необходимо использовать систему с наименьшим возможным содержанием Д2ЭГФК, а именно 1.36 моль/л.
Рис. 3.
Зависимость степени извлечения металлов от кислотности солевой фазы в системе полипропиленгликоль 425 (38 мас. %)–NaCl (6 мас. %)–H2O, рНсол.ф. 0.8.
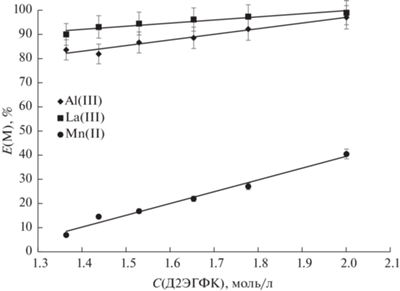
Исследуемые металлы извлекаются в системах с Д2ЭГФК в виде ди(2-этилгексил)фосфатов (уравнение (1)), сольватированных недиссоциированными молекулами кислоты с возможным включением хлорид-ионов, что характерно для лантаноидов [42]:
(1)
$\begin{gathered} {\text{M}}_{{{\text{сол}}.{\text{ф}}.}}^{{3 + }} + x{\text{H}}{{{\text{A}}}_{{{\text{пол}}.{\text{ф}}.}}} + y{\text{Cl}}_{{{\text{сол}}.{\text{ф}}.}}^{ - } \leftrightarrows \\ \leftrightarrows {\text{MC}}{{{\text{l}}}_{y}}{{{\text{A}}}_{{3 - y}}}{{\left( {{\text{HA}}} \right)}_{{\left( {x - 3 + y} \right){\text{пол}}.{\text{ф}}.}}} + \left( {3 - y} \right){\text{H}}_{{{\text{сол}}.{\text{ф}}.}}^{ + }. \\ \end{gathered} $Тогда константа экстракции по уравнению (1) будет иметь вид:
Путем логарифмирования полученного выражения, получим:
Для определения составов экстрагируемых комплексов нами были построены билогарифмические зависимости коэффициентов распределения металлов от рН и концентрации экстрагента. В табл. 2 представлены параметры уравнений полученных прямых и их коэффициенты детерминации. Тангенс угла наклона полученных в билогарифмических координатах прямых для зависимости коэффициента распределения La(III) и Al(III) от концентрации экстрагента равен 6 в обоих случаях. Это свидетельствует об участии в образовании экстрагируемых соединений металлов шести молекул Д2ЭГФК. Для зависимостей коэффициентов распределения лантана и алюминия от значений рН солевой фазы тангенсы углов наклона равны 2 и 3 соответственно. На основании полученных данных предложены следующие механизмы экстракции:
Таблица 2.
Параметры уравнений (y = ax + b) билогарифмических зависимостей коэффициентов распределения лантана и алюминия от кислотности равновесной солевой фазы и концентрации Д2ЭГФК (моль/л) и их коэффициенты детерминации
Ион | рНсол.ф. | С(Д2ЭГФК) | ||||
---|---|---|---|---|---|---|
a | b | R2 | a | b | R2 | |
Al(III) | 2.99 | –2.29 | 0.95 | 5.88 | –0.79 | 0.96 |
La(III) | 2.26 | –1.33 | 0.99 | 5.98 | –0.34 | 0.98 |
Разделение ионов кобальта и никеля возможно с использованием роданида калия, так как ионы Co(II) способны образовывать тиоцианатные анионные комплексы с бόльшими константами устойчивости, чем ионы Ni(II) (Kуст(Сo(II)) = 200, Kуст(Ni(II)) = 64.5). Исследование межфазного распределения Ni(II) и Co(II) в системах с полипропиленгликолем 425 и KSCN было проведено ранее [41]. При введении в систему полипропиленгликоль 425 (30 мас. %)–NaCl (8 мас. %)–H2O роданида калия (1 мас. %) в полимерную фазу количественно извлекаются ионы кобальта и не экстрагируются ионы никеля. Таким образом может быть решена задача разделения ионов никеля и кобальта в предложенной “зеленой” экстракционной системе.
На основании экспериментальных данных нами была разработана принципиальная технологическая схема переработки отработанных Ni-MH аккумуляторов (рис. 4). Созданная схема позволяет получить концентраты отдельных металлов, входящих в состав Ni-MH аккумуляторов, используя экологически безопасную экстракционную систему на основе полипропиленгликоля 425 и хлорида натрия с минимальным количеством экстрагентов (KSCN и Д2ЭГФК).
ЗАКЛЮЧЕНИЕ
В ходе проведенного исследования показано, что целесообразна совместная переработка катодного и анодного материалов ввиду схожести их элементного состава. Подобраны условия, позволяющие разделить ионы Ni(II), La(III), Zn(II), Co(II), Mn(II) и Al(III) с использованием двухфазной водной системы на основе полипропиленгликоля 425 и минимального количества экстрагентов (Д2ЭГФК и роданид калия). По полученным экспериментальным данным разработана оригинальная принципиальная технологическая схема переработки отработанных химических источников тока.
Список литературы
Innocenzi V., Ippolito N.M., De Michelis I. et al. // J. Power Sources. 2017. V. 362. P. 202. https://doi.org/10.1016/j.jpowsour.2017.07.034
Assefi M., Maroufi S., Yamauchi Y. et al. // Curr. Opin. Green Sustain. Chem. 2020. V. 24. P. 26. https://doi.org/10.1016/j.cogsc.2020.01.005
Zhang X., Li L., Fan E. et al. // Chem. Soc. Rev. 2018. V. 47. № 19. P. 7239. https://doi.org/10.1039/C8CS00297E
Chagnes A., Pospiech B. // J. Chem. Technol. Biotechnol. 2013. V. 88. № 7. P. 1191. https://doi.org/10.1002/jctb.4053
Orefice M., Audoor H., Li Z. et al. // Sep. Purif. Technol. 2019. V. 219. P. 281. https://doi.org/10.1016/j.seppur.2019.03.029
Gunn G. (ed.) Critical Metals Handbook. Oxford: John Wiley & Sons, 2014. https://doi.org/10.1002/9781118755341
Silvas F.P.C., Jiménez Correa M.M., Caldas M.P.K. et al. // Waste Manag. 2015. V. 46. P. 503. https://doi.org/10.1016/j.wasman.2015.08.030
Omodara L., Pitkäaho S., Turpeinen E.-M. et al. // J. Clean. Prod. 2019. V. 236. P. 117573. https://doi.org/10.1016/j.jclepro.2019.07.048
Nitta N., Wu F., Lee J.T. et al. // Mater. Today. 2015. V. 18. № 5. P. 252. https://doi.org/10.1016/j.mattod.2014.10.040
Xu Y., Mulder F.M. // Int. J. Hydrogen Energy. 2021. https://doi.org/10.1016/j.ijhydene.2021.03.073
Hazotte C., Leclerc N., Meux E. et al. // Hydrometallurgy. 2016. V. 162. P. 94. https://doi.org/10.1016/j.hydromet.2016.02.019
Larsson K., Ekberg C., Ødegaard-Jensen A. // Waste Manag. 2013. V. 33. № 3. P. 689. https://doi.org/10.1016/j.wasman.2012.06.001
Fedorova M.I., Zakhodyaeva Y.A., Baranchikov A.E. et al. // Russ. J. Inorg. Chem. 2021. V. 66. № 2. P. 266. [Федорова М.И., Заходяева Ю.А., Баранчиков А.Е. и др. // Журн. неорган. химии. 2021. Т. 66. № 2. С. 274. https://doi.org/10.31857/S0044457X21020082]https://doi.org/10.1134/S003602362102008X
Müller T., Friedrich B. // J. Power Sources. 2006. V. 158. № 2. P. 1498. https://doi.org/10.1016/j.jpowsour.2005.10.046
Tang K., Ciftja A., Van D. et al. // J. Min. Metall., Sect. B: Metall. 2013. V. 49. № 2. P. 233. https://doi.org/10.2298/JMMB120808004T
Larsson K., Ekberg C., Ødegaard-Jensen A. // Hydrometallurgy. 2013. V. 133. P. 168. https://doi.org/10.1016/j.hydromet.2013.01.012
Zhang P., Yokoyama T., Itabashi O. et al. // Hydrometallurgy. 1998. V. 50. № 1. P. 61. https://doi.org/10.1016/S0304-386X(98)00046-2
Gharabaghi M., Irannajad M., Azadmehr A.R. // Chem. Eng. Res. Des. 2013. V. 91. № 2. P. 325. https://doi.org/10.1016/j.cherd.2012.11.016
Meshram P., Pandey B.D., Mankhand T.R. // Hydrometallurgy. 2015. V. 158. P. 172. https://doi.org/10.1016/j.hydromet.2015.10.028
Meshram P., Pandey B.D., Mankhand T.R. // Waste Manag. 2016. V. 51. P. 196. https://doi.org/10.1016/j.wasman.2015.12.018
Fernandes A., Afonso J.C., Dutra A.J.B. // Hydrometallurgy. 2013. V. 133. P. 37. https://doi.org/10.1016/j.hydromet.2012.11.017
Landa-Castro M., Aldana-González J., Montes de Oca-Yemha M.G. et al. // J. Alloys Compd. 2020. V. 830. P. 154650. https://doi.org/10.1016/j.jallcom.2020.154650
Zhang P., Yokoyama T., Itabashi O. et al. // J. Power Sources. 1999. V. 77. № 2. P. 116. https://doi.org/10.1016/S0378-7753(98)00182-7
Bertuol D.A., Bernardes A.M., Tenório J.A.S. // J. Power Sources. 2009. V. 193. № 2. P. 914. https://doi.org/10.1016/j.jpowsour.2009.05.014
Innocenzi V., Vegliò F. // J. Power Sources. 2012. V. 211. P. 184. https://doi.org/10.1016/j.jpowsour.2012.03.064
Wilson A.M., Bailey P.J., Tasker P.A. et al. // Chem. Soc. Rev. 2014. V. 43. № 1. P. 123. https://doi.org/10.1039/C3CS60275C
Tanaka M., Narita H. // Hydrometallurgy. 2021. V. 201. P. 105588. https://doi.org/10.1016/j.hydromet.2021.105588
Sun M., Liu S., Zhang Y. et al. // J. Mol. Liq. 2019. V. 280. P. 252. https://doi.org/10.1016/j.molliq.2019.02.025
Lupi C., Pilone D. // Miner. Eng. 2020. V. 150. P. 106278. https://doi.org/10.1016/j.mineng.2020.106278
Mishra B.B., Devi N. // Mater. Today Proc. 2020. V. 30. P. 254. https://doi.org/10.1016/j.matpr.2020.01.355
Guimarães A.S., Silva L.A., Pereira A.M. et al. // Sep. Purif. Technol. 2020. V. 239. P. 116570. https://doi.org/10.1016/j.seppur.2020.116570
Deng Y., Ding Y., Huang Z. et al. // J. Mol. Liq. 2021. V. 329. P. 115549. https://doi.org/10.1016/j.molliq.2021.115549
Wu X., Zhang G., Zeng L. et al. // Hydrometallurgy. 2020. V. 195. P. 105401. https://doi.org/10.1016/j.hydromet.2020.105401
Soeezi A., Abdollahi H., Shafaei S.Z. et al. // Trans. Nonferrous Met. Soc. China. 2020. V. 30. № 2. P. 518. https://doi.org/10.1016/S1003-6326(20)65232-3
Huang Y., Chen D., Chen S. et al. // J. Clean. Prod. 2021. V. 297. P. 126452. https://doi.org/10.1016/j.jclepro.2021.126452
Fedorova M.I., Zinov’eva I.V., Zakhodyaeva Y.A. et al. // Theor. Found. Chem. Eng. 2020. V. 54. № 2. P. 313. [Федорова М.И., Зиновьева И.В., Заходяева Ю.А. и др. // Теорет. основы хим. технологии. 2020. Т. 54. № 2. С. 202. https://doi.org/10.31857/S0040357120020037]https://doi.org/10.1134/S0040579520020037
Zakhodyaeva Y.A., Rudakov D.G., Solov’ev V.O. et al. // Theor. Found. Chem. Eng. 2019. V. 53. № 2. P. 159. [Заходяева Ю.А., Рудаков Д.Г., Соловьев В.О. и др. // Теорет. основы хим. технологии. 2019. Т. 53. № 2. С. 131. https://doi.org/10.1134/S0040357119020180.]https://doi.org/10.1134/S0040579519020180
Zakhodyaeva Y.A., Rudakov D.G., Solov’ev V.O. et al. // J. Chem. Eng. Data 2019. V. 64. № 3. P. 1250. https://doi.org/10.1021/acs.jced.8b01138
de Oliveira W.C.M., Rodrigues G.D., Mageste A.B. et al. // Chem. Eng. J. 2017. V. 322. P. 346. https://doi.org/10.1016/j.cej.2017.04.044
Fedorova M.I., Zakhodyaeva Y.A., Voshkin A.A. // Theor. Found. Chem. Eng. 2020. V. 54. № 3. P. 425. [Федорова М.И., Заходяева Ю.А., Вошкин А.А. // Теорет. основы хим. технологии. 2020. Т. 54. № 3. С. 304. https://doi.org/10.31857/S0040357120030021]https://doi.org/10.1134/S0040579520030021
Voshkin A.A., Zakhodyaeva Y.A., Zinov’eva I.V. // KnE Mater. Sci. 2020. https://doi.org/10.18502/kms.v6i1.8072
Lee G.S., Uchikoshi M., Mimura K. et al. // Sep. Purif. Technol. 2009. V. 67. № 1. P. 79. https://doi.org/10.1016/j.seppur.2009.03.033
Дополнительные материалы отсутствуют.
Инструменты
Журнал неорганической химии