Журнал неорганической химии, 2021, T. 66, № 8, стр. 1086-1091
Влияние газовой атмосферы на образование волокон SiC при силицировании углеродного войлока
М. Г. Фролова a, *, А. С. Лысенков a, Д. Д. Титов a, К. А. Ким a, А. Ю. Иванников а, С. Н. Перевислов b, Ю. Ф. Каргин a
a Институт металлургии и материаловедения им. А.А. Байкова РАН
119334 Москва, Ленинский пр-т, 49, Россия
b Институт химии силикатов им. И.В. Гребенщикова РАН
199034 Санкт-Петербург, Университетская наб., 7-9, Россия
* E-mail: frolovamarianna@bk.ru
Поступила в редакцию 19.02.2021
После доработки 03.03.2021
Принята к публикации 17.03.2021
Аннотация
Представлены экспериментальные данные по влиянию газовой атмосферы (вакуум или аргон) на фазовый состав волокон карбида кремния, образующихся при силицировании углеродного войлока. Установлено, что основной фазой при силицировании углеродного войлока в вакууме является β-SiC (3C), в атмосфере аргона – α-SiC (6H). При силицировании углеродного войлока в вакууме на поверхности волокон карбидокремниевого войлока присутствует остаточный кремний. Показано, что газовая атмосфера определяет характер процесса силицирования при температуре 1650°С: в вакууме SiC образуется за счет взаимодействия с расплавом кремния, смачивающего волокна углерода, в аргоне – преимущественно за счет реакции с парообразным кремнием.
ВВЕДЕНИЕ
Керамоматричные композиты на основе карбида кремния перспективны для применения в различных отраслях промышленности благодаря высокому уровню эксплуатационных характеристик: высокой химической и коррозионной стойкости, высокой температуре плавления, прочности.
Наиболее актуальные области применения армированных карбидокремниевых композитов на сегодняшний день – авиационная и ядерная промышленность, машиностроение [1–3]. Для армирования композитов основе карбида кремния в качестве армирующей фазы могут применяться различные компоненты, содержащие волокна карбида кремния [4, 5]. Как правило, волокна карбида кремния используют в виде непрерывных или дискретных волокон, переплетенных волокон (тканей) или их комбинаций.
Преимуществом волокон на основе карбида кремния является их совместимость с матрицами различной природы: металлической, полимерной, керамической [6]. Часто карбидокремниевые волокна сочетают с углеродными или карбидокремниевыми матрицами.
В течение последних нескольких лет ведутся активные разработки в области получения и исследования армирующих карбидокремниевых компонентов и материалов на их основе [7–9]. Ключевыми факторами, влияющими на свойства полученных продуктов, являются: температура синтеза, свойства исходных компонентов, степень конверсии и количество остаточного кремния в полученных армирующих компонентах, а также вид атмосферы – аргон, азот, вакуум [7–10].
Существует несколько основных способов получения армирующих материалов на основе карбида кремния, каждый из которых имеет свои преимущества и недостатки. Один из методов – CVD – основывается на химическом осаждении метилхлорсиланов (CH3SiCl3, CH3SiHCl2, (CH3)2SiCl2) с водородом либо с другим газом-носителем на вольфрамовую (или углеродную) нить-подложку. Такие волокна имеют сравнительно большой диаметр (70–120 мкм), и их обычно используют в сочетании с металлической матрицей [1]. Для керамических матриц используют волокна без вольфрамовой сердцевины. Диаметр таких волокон <20 мкм. Их получают пиролизом полимерных нитей на основе поликарбоксиланов (PCS) [1]. Существуют также комбинированные методы синтеза армирующих компонентов и методы, применяемые для синтеза порошков карбида кремния. Авторами [11–16] изучен класс материалов, полученных пропиткой волокнистой углерод-углеродной основы кремнием в жидкой и газообразной фазе.
Обычно порошок SiC получают взаимодействием SiO2 с C в соответствии со следующими реакциями [11]:
(1)
${\text{Si}}{{{\text{O}}}_{2}} + {\text{C}} = {\text{SiO}}\left( {\text{г}} \right) + {\text{CO(г)}},$Изменение свободной энергии Гиббса системы SiO2–C (реакция (3)) в интервале температур от 1200 до 1400°C имеет положительное значение (ΔG ≈ 104–37 кДж), напротив, изменение свободной энергии Гиббса системы Si–C (реакция (4)) в том же диапазоне температур – отрицательное значение (ΔG ≈ −61 кДж).
(6)
${\text{C}} + {\text{ }}1{\text{/}}2{{{\text{O}}}_{2}}\left( {\text{г}} \right) = {\text{CO}}\left( {\text{г}} \right),~$Следовательно, образование SiC в результате реакции Si с C может происходить при более низкой температуре, чем при взаимодействии SiO2 с C [11].
Как правило, синтез порошка карбида кремния осуществляют в атмосфере инертных газов (азот, аргон) или в вакууме. Авторами [11] описан способ синтеза карбида кремния по реакции кремния (Si) с сажей (С). В работе [11] смеси Si и C готовили в мольном соотношении 1 : 1, затем проводили сушку смеси, формование под давлением 43 МПа (размеры заготовок 12 × 3.6 мм). Заготовки помещали в закрытые углеродные тигли и обжигали в печи в атмосфере аргона и в вакууме при температурах 1250, 1300 и 1350°C. Установлено, что повышение температуры синтеза свыше 1350°С позволяет снизить содержание кремния. Кроме того, проведение синтеза SiC в вакууме также способствует снижению уровня Si, однако синтез в вакууме приводит и к увеличению потери массы. Авторами [16] получены карбидокремниевые волокнистые материалы методом силицирования: углеродные волокна засыпали техническим кремнием КР00 с содержанием основного вещества не менее 99.0 мас. %. Заготовку пропитывали расплавом кремния, синтез проводили в печи сопротивления в вакууме со скоростью нагревания 8 град/мин до температуры 1440 ± 10°С и выдержкой при конечной температуре в течение 3 мин. В работе [17] описан способ получения β-SiC с размерами зерен 0.1–0.3 мкм в потоке аргона при температуре 1600°С. В работе [7] изложены результаты карботермического синтеза SiC из природного графита и кварца в реакторе с самоорганизующейся защитной атмосферой CO–SiO и в аргоне при температуре 1600–1650°С.
Цель настоящей работы – изучение влияния газовой атмосферы (вакуум, аргон) на образование волокон SiC при силицировании углеродного войлока кремнием.
ЭКСПЕРИМЕНТАЛЬНАЯ ЧАСТЬ
В качестве исходных компонентов использовали промышленный порошок кремния с содержанием примесей не более 0.01% (ООО “Платина”), углеродный войлок Карбопон В-22 с содержанием углерода не менее 99.9%.
Схема расположения образцов в экспериментах по силицированию углеродного войлока показана на рис. 1. В качестве контейнеров использовали графитовые тигли, которые изнутри выстилали углеродной фольгой для предотвращения взаимодействия тигля с жидким кремнием. На дно тигля помещали диск из углеродного войлока, соответствующий диаметру тигля. Из углеродного войлока вырезали квадратные образцы размером 3 × 3 × 0.8 см, которые устанавливали вертикально. В тигель засыпали порошок кремния так, чтобы он полностью покрывал образцы. Тигель помещали в вакуумную печь. Получение войлока SiC проводили в вакууме. Скорость нагревания до температуры 1100°С составляла 5 град/мин, затем повышение температуры до 1650°С продолжали либо в вакууме (1 × 10–5 мбар), либо в атмосфере аргона (при давлении 1.2 атм).
Процесс силицирования образцов углеродного войлока проводили в вакуумной шахтной электрической резистивной печи. Фазовый состав образцов определяли при помощи дифрактометра XRD ДРОН-3 (CoKα-излучение, λ = 1.79020 Å, скорость сканирования 2θ = 2 град/мин). Идентификацию фаз осуществляли с помощью базы данных COD [18]. Морфологические особенности образцов изучали на оптическом микроскопе Altami MET 5T с увеличением ×50–2000, позволяющем наблюдать методом ярких и темных полей, а также в поляризованном свете. Микроскоп оснащен двумерным каскадом; в качестве стабилизированного источника света использовали галогенную лампу 12 В–100 Вт, специализированную цифровую видеокамеру Altami U3CMOS14000KA высокого разрешения (14 мегапикселей). Для анализа изображений и изучения структуры применяли лицензионную программу Altami Studio 4.0 Pro с фильтром “Мультифокус”, позволяющим собирать одну картинку из изображений с разными фокусными расстояниями так, чтобы все ее элементы находились в фокусе.
РЕЗУЛЬТАТЫ И ОБСУЖДЕНИЕ
На рис. 2 представлены СЭМ-изображения исходного углеродного войлока и войлока SiC, полученного силицированием в вакууме и в аргоне. Образцы войлока SiC, полученного как в вакууме (рис. 2в, 2г), так и в аргоне (рис. 2д, 2е), сохраняют целостность и форму исходного углеродного войлока. При этом на рис. 2г отчетливо видно, что на поверхности волокон SiC полученного в вакууме войлока имеются частицы не вступившего в реакцию кремния, в то время как на волокнах SiC, полученных в аргоне, они отсутствуют (рис. 2е). По-видимому, в зависимости от газовой атмосферы реализуются различные по характеру процессы: в вакууме силицирование определяется взаимодействием углеродных волокон с расплавом кремния [11], в то время как в атмосфере аргона происходит парофазное силицирование [19]. Процесс парофазного силицирования основан на испарении паров кремния и их осаждении на поверхности и в объеме пористого углеродного войлока, сопровождающемся образованием карбида кремния. Помимо массопереноса паров кремния в [19] отмечают также возможность взаимодействия остаточного кислорода с расплавом кремния и углеродом с образованием SiO и CO, участвующих в массопереносе и образовании SiC (реакции (2), (6) и SiO(г) + CO(г) = Si(тв) + CO2(г), 2Si(тв) + CO(г) = = SiC + SiO(г)). Следует также учесть, что в вакууме смачиваемость углерода расплавом кремния выше, чем в аргоне: соответствующие краевые углы смачивания составляют 50° в вакууме и 120° в атмосфере аргона [20, 21]. Поэтому в вакууме большее количество кремния проникает во внутренний объем углеродного войлока, реагирует с ним, а избыток непрореагировавшего кремния остается на поверхности волокон карбида кремния (рис. 2г). Войлок карбида кремния, полученный в вакууме, имеет черный цвет, а войлок, полученный в среде аргона, – зеленоватый оттенок (рис. 3). Войлок карбида кремния, полученный в вакууме, представлен тремя фазами: β-SiC (3C) – 68%, α-SiC (6H) – 14.7%, кремний – 17.3% (рис. 4, а). Войлок карбида кремния, полученный в аргоне, состоит из двух фаз карбида кремния: α-SiC (6H) и β-SiC (3C) (рис. 4, б), причем содержание α-фазы карбида кремния (57.4%) превышает содержание β-фазы (42.6%). Содержание полиморфных форм карбида кремния в волокнах, образующих войлок, рассчитано при помощи метода Ритвельда.
Рис. 2.
СЭМ образцов: а, б – исходный углеродный войлок; в, г – SiC (синтез в вакууме); д, е – SiC (синтез в аргоне).

Рис. 3.
Фотографии: а – углеродный войлок, б – войлок SiC (обжиг в вакууме), в – войлок SiC (обжиг в аргоне).
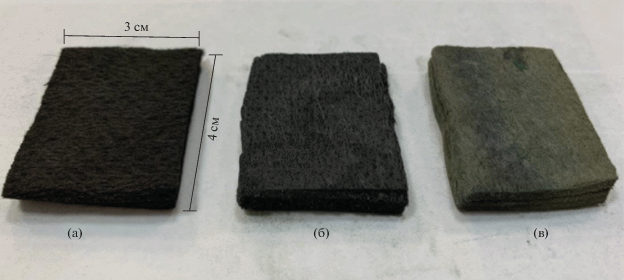
Согласно визуальной оценке, войлок карбида кремния, полученный в аргоне, обладает такой же гибкостью, как и исходный войлок углерода (рис. 5). В свою очередь, образцы войлока, полученного в вакууме, очевидно, вследствие наличия остатков кремния на поверхности волокон SiC были очень хрупкими и крошились при изгибе.
ЗАКЛЮЧЕНИЕ
Силицированием углеродного войлока при температуре 1650°С в вакууме и в аргоне получен карбидокремниевый войлок. Установлено, что в зависимости от газовой атмосферы меняется фазовый состав волокон карбидокремниевого войлока. Волокна войлока карбида кремния, полученного в вакууме, состоят из смеси β-SiC, α-SiC и остаточного кремния в количестве 17.3% на поверхности волокон с преобладанием фазы β-SiC (68%). Волокна карбидокремниевого войлока, полученного в аргоне, образованы смесью α-SiC и β-SiC с преобладанием фазы α-SiC (57.4%). Показано, что вследствие изменения смачиваемости углеродного волокна кремнием (в атмосфере аргона краевой угол смачивания существенно выше, чем в вакууме) изменяется характер процесса силицирования: расплавом кремния (вакуум) или его парами (аргон). Полученные результаты показывают, что для получения пористых материалов SiC, таких как карбидокремниевый войлок, более предпочтительным является парофазное силицирование в атмосфере аргона.
Список литературы
Lisenko A.A., D’yachkov P.N. // Russ. J. Inorg. Chem. 2009. V. 54. № 8. P. 1286. https://doi.org/10.1134/S0036023609080178
Utkin A.V., Matvienko A.A., Titov A.T. et al. // Inorg. Mater. 2011. V. 47. № 10. P. 1176. https://doi.org/10.1134/S0020168511090238
Frolova M.G., Kargin Yu.F., Lysenkov A.S. et al. // Inorg. Mater. 2020. V. 56. № 9. P. 987. https://doi.org/10.1134/S0020168520090058
Christin F. // Adv. Eng. Mater. 2002. V. 4. № 12. P. 903. https://doi.org/10.1002/adem.200290001
Istomina E.I., Istomin P.V., Nadutkin A.V. et al. // IOP Conference Series: Materials Science and Engineering. 2019. T. 525. № 1. P. 012059. https://doi.org/10.1088/1757-899X/525/1/012059
Levy A., Papazian J.M. // Metall. Trans. A. 1990. T. 21. № 1. P. 411. https://doi.org/10.1007/BF02782421
Lebedev A.S., Suzdal’tsev A.V., Anfilogov V.N. et al. // Inorg. Mater. 2020. V. 56. № 1. P. 22. https://doi.org/10.1134/S0020168520010094
Qian J.M., Jin Z.H., Wang X.W. // Ceram. Int. 2004. V. 30. № 6. P. 947. https://doi.org/10.1016/j.ceramint.2003.11.001
Qian J., Wang J., Jin Z. // Mater. Sci. Eng., A. 2004. V. 371. № 1–2. P. 229. https://doi.org/10.1016/j.msea.2003.11.051
Hou G., Jin Z., Qian J. // J. Mater. Process. Technol. 2007. V. 182. № 1–3. P. 34. https://doi.org/10.1016/j.jmatprotec.2006.07.003
Larpkiattaworn S. // Ceram. Int. 2006. V. 32. № 8. P. 899. https://doi.org/10.1016/j.ceramint.2005.06.011
Брантов С.К., Гуржиянц П.А., Татарченко В.А. // Изв. АН СССР. Сер. физ. 1988. Т. 52. № 10. С. 2029.
Костиков В.И., Демин А.В., Колесников С.А. и др. Пат. RU 92015952 C1. Заявка. 1992. 92015952/33.
Бушуев В.М., Удинцев П.Г., Чунаев В.Ю., Дувалов А.В. Пат. RU 2194683 C2. Заявка. 2001. 2001100721/03.
Емяшев А.В., Костиков В.И., Колесников С.А. Пат. RU 2058964 С1. 1992.
Сапронов Р.Л., Мех В.А., Румянцев В.И. // Физика и химия стекла. 2011. № 5. С. 770.
Koc R., Cattamanchi S.V. // J. Mater. Sci. 1998. V. 33. № 10. P. 2537.
Downs R.T., Hall-Wallace M. // Am. Mineral. 2003. V. 88. № 1. P. 247.
Кулик В.И., Нилов А.С. // Актуальные вопросы технических наук в современных условиях. М., 2018. 30 с.
Narayan J., Raghunathan R., Chowdhury R. et al. // J. Appl. Phys. 1994. V. 75. P. 7252. https://doi.org/10.1063/1.356660
Whalen T.J., Anderson A.T. // J. Am. Ceram. Soc. 1975. V. 58. P. 9.
Дополнительные материалы отсутствуют.
Инструменты
Журнал неорганической химии