Журнал неорганической химии, 2021, T. 66, № 5, стр. 678-681
Разработка функционального композитного каталитического материала на основе Pt@С для электродов твердополимерного топливного элемента
А. Г. Иванова a, *, Н. Н. Губанова a, b, О. А. Загребельный a, Е. Л. Краснопеева a, c, И. Ю. Кручинина a, d, О. А. Шилова a, d, e
a Институт химии силикатов им. И.В. Гребенщикова РАН
199034 Санкт-Петербург, наб. Макарова, 2, Россия
b НИЦ КИ Петербургский институт ядерной физики им. Б.П. Константинова
188300 Гатчина, мкр. Орлова роща, 1, Россия
c Институт высокомолекулярных соединений РАН
199034 Санкт-Петербург, В. О. Большой пр-т, 31, Россия
d Санкт-Петербургский государственный электротехнический университет “ЛЭТИ”
197376 Санкт-Петербург, ул. Профессора Попова, 5, Россия
e Санкт-Петербургский государственный технологический институт (технический университет)
190013 Санкт-Петербург, Московский пр-т, 26, Россия
* E-mail: agp-13@inbox.ru
Поступила в редакцию 22.12.2020
После доработки 29.12.2020
Принята к публикации 30.12.2020
Аннотация
Жидкофазным методом синтеза получен и исследован каталитический композитный материал, содержащий высокопроводящую сажу Carbon black, Super P и наночастицы платины. Выявлено увеличение электроактивности наночастиц Pt в присутствии высокопроводящей сажи по сравнению с эталонным образцом – платинированной углеродной сажей E-tek, где в качестве углеродного материала используется сажа Vulcan XC-72. Показано влияние природы углеродного материала на каталитическую активность наночастиц платины. Методом циклической вольтамперометрии определено значение электрохимически активной площади поверхности разработанного каталитического материала и каталитического материала на основе катализатора Etek, которое составляет 54 и 20 м2/г соответственно.
ВВЕДЕНИЕ
Одной из важнейших задач электрокатализа является сокращение количества платины в каталитическом слое электродов твердополимерного топливного элемента (ТПТЭ) [1]. Другой серьезной проблемой ТПТЭ является быстрое разрушение (коррозия) катализатора на электродах (особенно на катоде) в процессе его эксплуатации [2–4].
В последние десятилетия активно ведутся научные исследования высокодисперсных платиносодержащих катализаторов, проявляющих существенно более высокую каталитическую активность, чем металлическая платина, при меньших концентрациях.
Помимо этого, усиливается интерес к коррозионно-устойчивым композитным материалам – дисперсным осадкам Pt и/или Pd, осажденным на различные носители – оксиды, карбиды переходных металлов (титана, церия, железа, вольфрама и т.д.) – и на проводящий углеродный материал [10–15].
Более того, ведутся исследования, направленные на частичную или полную замену платины на наночастицы других переходных металлов (Ni, Co, Ag, Cu и т.д.), их композиты и комплексы на их основе [16, 17].
Перечисленные композитные материалы, в особенности те, в состав которых входят оксиды, способствуют созданию электрохимической стабильности катализатора. Композиты на основе оксидов и карбидов переходных металлов уступают композитам на основе углеродных материалов по величине их электропроводности. Наночастицы металлов неплатиновой группы, входящие в состав композитов, в процессе работы ТПТЭ подвержены быстрому окислению. Углеродсодержащие материалы корродируют лишь при длительной эксплуатации топливного элемента.
Коммерческий каталитический углеродсодержащий композитный материал E-teK на основе углеродной сажи и платиновой черни, используемый в ТПТЭ, является недостаточно электроактивным материалом, в особенности для реакции восстановления молекулярного кислорода, проходящей на катоде ТПТЭ. Возможный путь устранения этого недостатка – разработка новых углеродсодержащих композитных каталитических материалов, что предполагает поиск оптимального сочетания и соотношения функциональных компонентов этих материалов. Таким образом, целью настоящей работы является разработка и исследование каталитического композитного материала электрода ТПТЭ, содержащего новый катализатор Pt@C-Supercarbon, где С-Supercarbon – коммерческая высокопроводящая сажа.
ЭКСПЕРИМЕНТАЛЬНАЯ ЧАСТЬ
Синтез каталитического композитного порошка Pt@C-supercarbon проводили путем восстановления гексахлорплатиновой кислоты (H2PtCl6 · 6H2O) в присутствии C-supercarbon – высокопроводящей сажи Alfa AesarTM Carbon black, Super PTM Conductive, 99+% (metals basic).
Для этого к свежеприготовленному водному раствору гексахлорплатиновой кислоты (х. ч., производитель Merck) добавляли сажу (С-supercarbon) в массовом соотношении Pt : сажа = 20 : 80 и восстановитель – концентрированную муравьиную кислоту в мольном соотношении Pt : HCOOH = = 1 : 200. Соотношение Pt : сажа = 20 : 80 cоответствует соотношению платиновой черни к проводящей саже Vulcan XC-72 в коммерческом катализаторе E-teK. Реакцию восстановления проводили при постоянном перемешивании в течение 5 сут при комнатной температуре. Затем образовавшийся осадок отфильтровывали, промывали дистиллированной водой и сушили при комнатной температуре.
Для приготовления каталитических “чернил”, согласно методике [18], использовали композитный каталитический порошок Pt@C-supercarbon и ионпроводящий и одновременно связующий материал смолу Нафион®. Полученные “чернила” наносили лакокрасочным способом на углеродную подложку (углеродная бумага Torаy®). Образец высушивали до постоянной массы при температуре 70 и 130°С. Аналогичным способом был приготовлен эталонный электрод с каталитическим слоем на основе коммерческого катализатора E-teK.
Электрохимические испытания проводили в трехэлектродной ячейке с помощью метода циклической вольтамперометрии, где электрод с катализатором Pt@C-supercarbon использовали как рабочий. Измерение потенциала рабочего электрода осуществляли относительно псевдоэлектрода сравнения – серебряной проволоки. В качестве вспомогательного электрода применяли платиновую пластину или платиновую сетку. Трехэлектродная ячейка была подключена к потенциостату-гальваностату P-8S. Скорость развертки напряжения составляла 100 мВ/с. В качестве электролита использовали 1 М раствор серной кислоты.
Исследование состава каталитического материала осуществляли методом рентгенофазового анализа (D8 Advance, счетчик Vantec). Расчет размеров областей когерентного рассеяния (ОКР) катализатора Pt@C-supercarbon проводили по формуле Шеррера, ошибка при определении ОКР кристалла размерами до 200 нм составляла ~20% [19].
РЕЗУЛЬТАТЫ И ОБСУЖДЕНИЕ
Анализ рентгенограммы электрода c катализатором Pt@C-supercarbon подтвердил восстановление платины и образование наночастиц Pt0 с размером областей когерентного рассеяния 7 нм (рис. 1).
Рис. 1.
Рентгенограмма электрода с каталитическим слоем на основе композита Pt@C-supercarbon после термообработки при температуре 130°С.
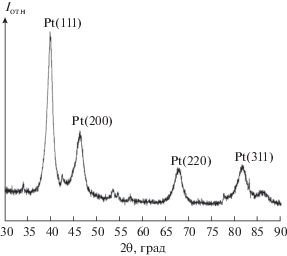
Каталитическую активность электродов с катализаторами Pt@C-supercarbon и E-teK оценивали косвенно по их адсорбционной емкости с помощью метода циклической вольтамперометрии (рис. 2). Площадь циклической вольтамперограммы разработанного электрода в несколько раз больше площади циклической вольтамперограммы электрода, являющегося эталоном. Это указывает на более высокую электроактивность и адсорбционную емкость каталитического материала, что соответствует большей каталитической активности Pt@C-supercarbon по сравнению с катализатором E-teK.
Рис. 2.
Циклические вольтамперограммы электродов с каталитическим слоем на основе катализаторов E-teK (1) и Pt@C-supercarbon (2), измеренные относительно псевдоэлектрода сравнения – серебряной проволоки в 1 М растворе H2SO4 при скорости развертки напряжения 100 мВ/с.
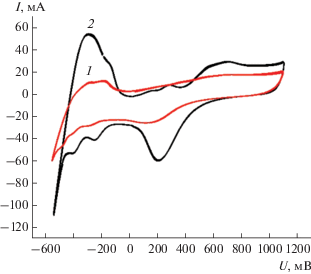
Электрохимически активная область на вольтамперограммах определяется пиками, интенсивность которых указывает на эффективность адсорбции/десорбции атомарного водорода и кислорода на поверхности наночастиц платиновых металлов, и пропорциональна количеству генерируемой энергии. На каждом поверхностном атоме в наночастицах платины или палладия адсорбируется один атом водорода или кислорода.
В результате электрохимически активная площадь поверхности катализатора (ESA, м2/г) может быть оценена через отношение [20]:
(1)
${\text{ESA}} = {{{{Q}_{{\text{H}}}}} \mathord{\left/ {\vphantom {{{{Q}_{{\text{H}}}}} {m \times 2.1}}} \right. \kern-0em} {m \times 2.1}},$(2)
${\text{ESA}} = {{{{Q}_{{\text{O}}}}} \mathord{\left/ {\vphantom {{{{Q}_{{\text{O}}}}} {m \times 4.2}}} \right. \kern-0em} {m \times 4.2}},$Как видно из табл. 1, значение ESA немонотонно изменяется с увеличением массовой загрузки Pt на электроде. Это значение зависит от равномерности распределения каталитических наночастиц на углеродном материале и по поверхности электропроводящей подложки, что обусловлено их формой и размером [23], поэтому при практически равной массовой загрузке Pt на разработанном (0.68 мг) и эталонном (0.65 мг) электродах значение ESA катализатора Pt@C-supercarbon в 2.7 раз больше, чем на ESA E-teK.
Таблица 1.
Сравнительная таблица характеристик катализаторов
Тип катализатора | Размер частиц углеродного материала, нм | Удельная площадь поверхности углеродного материала Sуд, м2/г | Массовая загрузка Pt на единицу площади электрода, мг/см2 | ESA, м2/г |
---|---|---|---|---|
Pt@C-supercarbon | 27 [21] | 62 [21] | 0.226 | 54 |
E-teK коммерческий | 501 | 270–2902 | 0.216 | 20 |
Pt@CNT* [22] | – | 50–60 | 0.5 | 48 |
* Pt@CNT – композит, состоящий из наночастиц Pt и нанотрубок углерода. Примечание. ЕSA оценивали по количеству электричества, затраченному на электрохимическую адсорбцию и десорбцию атомарного водорода (1). 1URL: http://www.epsilonpigments.com/inorganic-pigment/carbon-black/Super-Conductive-Carbon-Black.htm/ сайт фирмы “Epsilonl”, 2020 (дата обращения: 6.12.2020). 2URL: https://www.fuelcellstore.com/vulcan-xc-72r/ сайт фирмы “Fuellcellstore”, 2020 (дата обращения: 5.12.2020).
ESA катализатора Pt@CNT меньше ESA катализатора Pt@C-supercarbon, несмотря на то что массовая загрузка платины для него выше. Это указывает на менее равномерное распределение платины по поверхности нанотрубок углерода в катализаторе Pt@CNT.
Интересно отметить, что преимущество сажи Vulcan XC-722 (Sуд, 270–290 м2/г) катализатора E-teK перед сажей C-supercarbon (Sуд, 62 м2/г) катализатора Pt@C-supercarbon и нанотрубками углерода (Sуд, 50–60 м2/г) катализатора Pt@CNT не способствовало увеличению электроактивности наночастиц Pt.
По-видимому, высокая электропроводность проводящей сажи повышает электроактивность и, соответственно, каталитическую активность наночастиц Pt.
В дальнейшем планируется исследовать циклируемость и электропроводность разработанного каталитического материала, сравнить с полученными биметаллическими катализаторами, не содержащими платину, а также испытать их в составе мембранно-электродного блока ТПТЭ.
ЗАКЛЮЧЕНИЕ
Таким образом, в работе получен и исследован каталитический композитный материал для электродов твердополимерного топливного элемента, содержащий высокопроводящую сажу C-supercarbon и наночастицы платины и обладающий высокой электрохимической активностью. На основании анализа литературных и полученных нами экспериментальных данных выявлено, что электрохимическая и каталитическая активность наночастиц платины прежде всего зависит от природы углеродсодержащего материала, морфологии его поверхности и электрофизических свойств. Разработанный каталитический композитный материал пригоден для использования в составе мембранно-электродного блока водородно-воздушного твердополимерного топливного элемента, а также в качестве каталитического материала катода микробиологического топливного элемента.
Список литературы
Carrette L., Friedrich K.A., Stimming U. // Fuel Cells. 2001. V. 1. № 1. P. 5. https://doi.org/10.1002/1615-6854(2001et 05)1:1<5::AID- FUCE5>3.0.CO;2-G
Yu K., Groom D.J., Wang X. et al. // Chem. Mater. 2014. V. 26. № 19. P. 5540. https://doi.org/10.1021/cm501867c
Rabis A., Rodriguez P., Schmidt T. // J. ACS Catal. 2012. V. 2. P. 864. https://doi.org/10.1021/cs3000864
Witte K.J., Bongard H.J., Topalov A.A. et al. // J. Nanotechnol. 2014. V. 5. P. 44. https://doi.org/10.3762/bjnano.5.5
Ganesan A., Narayanasamy M. // Materials for Renewable and Sustainable Energy. 2019. V. 8. № 18. P. 2. https://doi.org/10.1007/s40243-019-0156-x
Shilova O.A., Gubanova N.N., Matveev V.A. et al. // Glass Phys. Chem. 2016. V. 42. № 1. P. 78. https://doi.org/10.1134/s1087659616010168
Shilova O.A., Gubanova N.N., Ivanova A.G. et al. // Russ. J. Inorg. Chem. 2017. V. 62. № 5. P. 645. https://doi.org/10.1134/S0036023617050230
Mayorova N.A., Zhigalina O.M., Zhigalina V.G., Khazova O.A. // Russ. J. Electrochem. 2014. V. 50. № 3. P. 223. https://doi.org/10.1134/S1023193514030082
Stolarov I.P., Cherkashina N.V., Yakushev I.A. et al. // Russ. J. Inorg. Chem. 2020. V. 65. № 4. P. 507. https://doi.org/10.1134/S003602362004021X
Ren X., Lv Q., Liu L. et al. // Sustainable Energy Fuels. 2020. V. 4. P. 15. https://doi.org/10.1039/c9se00460b
Zhanga Z., Liua J., Gua J. et al. // Energy Environ. Sci. 2014. V. 7. P. 2535. https://doi.org/10.1039/C3EE43886D
Brandão L., Passeira C., Gattia D.M., Mendes A.J. // Mater. Sci. 2011. V. 46. P. 7198. https://doi.org/10.1007/s10853-010-4638-6
Shrestha S., Mustain W.E. // J. Electrochem. Soc. 2010. V. 157. P. B1665. https://doi.org/110.1149/1.3489412
Borisov R.V., Belousov O.V., Zhizhaev A.M. // Russ. J. Inorg. Chem. 2020. V. 65. № 5. P. 1623. https://doi.org/10.1134/S0036023620100034
Shishmakov A.B., Mikushina Y.V., Koryakova O.V. et al. // Russ. J. Inorg. Chem. 2019. V. 64. № 7. P. 864. https://doi.org/10.1134/S0036023619070155
Rajapakse R.M.G., Senarathna K.G.C., Kondo A. et al. // Adv. Automob. Eng. 2015. V. 4. № 1. P. 1. https://doi.org/10.4172/2167-7670.1000121
Khrizanforova V.V., Budnikova Y.G., Strelnik I.D. et al. // RUCB. 2013. T. 62. № 4. C. 1003. https://doi.org/10.1007/s11172-013-0131-0
Litster S., McLean G. // J. Power Sources. 2004. V. 130. P. 61. https://doi.org/10.1016/j.jpowsour.2003.12.055
Яценко Д.А., Цыбуля С.В. // Вестн. НГУ, сер. физ. 2008. Т. 3. № 4. С. 47. [Yatsenko D.A., Tsybulya S.V. // Bull. Nsu. Ser. Phys. 2008. V. 3. № 4. Р. 47.]
Trasatti S., Petrii O.A. // Pure Appl. Chem. 1991. V. 63. P. 711. https://doi.org/10.1351/pac199163050711
Xu Z., Zhang H., Zhong H. et al. // Appl. Catal. B: Environ. 2012. V. 111. P. 264. https://doi.org/10.1016/j.apcatb.2011.10.007
Bharti A., Cheruvally G., Muliankeezhu S. // Int. J. Hydrogen Energy. 2017. V. 42. № 16. P. 11622. https://doi.org/10.1016/j.ijhydene.2017.02.109
Dicks A.L. // J. Power Sources. 2006. V. 156. P. 128. https://doi.org/10.1016/S0378-7753(97)02753-5
Дополнительные материалы отсутствуют.
Инструменты
Журнал неорганической химии