Микроэлектроника, 2019, T. 48, № 1, стр. 31-37
Травление карбида кремния в индуктивно-связанной плазме при малой мощности
А. А. Осипов 1, *, С. Е. Александров 1, Ю. В. Соловьев 1, А. А. Уваров 2, А. А. Осипов 3
1 Федеральное государственное автономное образовательное учреждение высшего образования
“Санкт-Петербургский политехнический университет Петра Великого”
195251 Санкт-Петербург, ул. Политехническая, д. 29, Россия
2 CORIAL, 266 chemin des Franques
38190 Bernin, France
3 Институт минералогии УрО РАН
456317 г. Миасс, Челябинская обл., Россия
* E-mail: tema.osipov@mail.ru
Поступила в редакцию 14.06.2018
После доработки 14.06.2018
Принята к публикации 14.06.2018
Аннотация
Рассмотрены особенности травления 4Н-SiC во фторсодержащей индуктивно-связанной плазме при пониженных значениях мощности, поглощаемой в ВЧ-разряде. Наиболее перспективные результаты, с точки зрения достижения бездефектной морфологии поверхности травления карбида кремния, были получены при использовании в качестве исходной газовой смеси SF6/O2. Определен характер влияния напряжения смещения, прикладываемого к держателю подложки, на скорость травления. Максимальная скорость травления, достигнутая в проведенных экспериментах, составила 840 нм/мин. Показано, что дополнительная последующая обработка поверхности SiC в плазме аргона положительно влияет на морфологию поверхности травления, минимизируя поверхностную плотность присутствующих на ней разнообразных дефектов.
ВВЕДЕНИЕ
В настоящее время карбид кремния широко используется при создании разнообразных полупроводниковых устройств таких, как мощные транзисторы, сверхбыстрые интегральные схемы, устройства оптоэлектроники, а также применяется в качестве подложек для эпитаксиального роста полупроводниковых материалов AIIIBV (например, нитрида галлия) [1–5]. Использование карбида кремния позволяет повысить максимально допустимые рабочие температуры полупроводниковых устройств и значительно увеличить их быстродействие [4–6]. Вместе с тем, применение подложек из карбида кремния выдвигает особые требования к используемым технологическим процессам и оборудованию. В частности, жидкостные методы обработки и травления таких подложек при формировании глубокого вертикального рельефа поверхности или сквозном размерном травлении не могут быть использованы в силу низких скоростей и изотропного характера травления. В связи с этим наиболее перспективной технологией травления карбида кремния с целью формирования бездефектного рельефа его поверхности на текущий момент является плазмохимическое травление (ПХТ), как правило, осуществляемое при пониженном давлении [7, 8]. Особенно актуальными являются задачи по разработке высокоскоростного формирования сквозных отверстий в пластинах карбида кремния, требующихся при создании ряда приборов и изделий микросистемной техники [9, 10]. Сквозные отверстия в пластинах предназначаются для формирования заземляющих контактов за счет заполнения их металлом [8], вследствие чего процесс ПХТ SiC должен удовлетворять требованиям по минимизации дефектообразования по всей поверхности профиля травления.
К настоящему времени наилучшие, с точки зрения величины скорости травления, результаты были получены при использовании плазмохимического травления в газовых смесях на основе гексафтрорида серы (SF6) с добавками O2 и/или Ar (1–2 мкм/мин [7, 8, 11]). В свою очередь, при травлении карбида кремния в хлоросодержащей плазме образуются очень гладкие поверхности профиля травления (RMS = 0.3 нм, RMS – Root Mean Square), но процесс характеризуется невысокими скоростями (280 нм/мин) [9]. Следует отметить, что максимально высокие скорости травления карбида кремния во фторосодержащих плазмах были достигнуты при величинах мощности, поглощаемой в ВЧ-разряде индуктивно-связанной плазмы (ИСП), 2000 и 2500 Вт. Травление SiC при относительно низких (менее 1000 Вт) значениях ВЧ-мощности, поглощаемой в разряде ИСП, происходит при существенно меньших значениях скоростей. Например, в работе [10] приведены следующие значения скоростей травления: 350 (750), 500 нм/мин (950 Вт). В работе [12] сообщалось о достижении скорости травления ~500 нм/мин (1000 Вт) и аналогичное значение было получено в [13], где мощность ВЧ-разряда также составляла 1000 Вт. Наконец, существенный прогресс в направлении увеличения скорости травления карбида кремния при низких мощностях ВЧ-разряда (1000 Вт) был продемонстрирован в [8], где авторам удалось достичь скоростей порядка 1 мкм/мин. Очевидно, что с точки зрения совершенствования данных технологий в плане снижения энергозатрат, большой интерес представляет разработка процессов, реализуемых при низких значениях ВЧ-мощности разряда ИСП, но обеспечивающих сопоставимые величины скоростей травления при минимальном развитии различных морфологических дефектов. Исходя из этого, данная работа преследовала целью изучить возможность реализации процесса ПХТ подложек SiC во фторосодержащей индуктивно-связанной плазме при пониженных (менее 1000 Вт) значениях ВЧ-мощности разряда, обеспечивающего скорости травления, сопоставимые со значениями, достигаемыми при высоких уровнях (2000 и более) поглощаемой ВЧ-мощности.
ЭКСПЕРИМЕНТАЛЬНАЯ ЧАСТЬ
Работа выполнялась на специально созданной оригинальной установке плазмохимического травления (рис. 1) [14]. Плазмохимический реактор установки основан на использовании цилиндрического источника индуктивно-связанной плазмы. Индуктор плазмогенератора располагался вне рабочей камеры и был отделен от нее стенкой, выполненной из алюмооксидной керамики, что позволило избежать распыления материала индуктора в ходе технологического процесса. Для минимизации эрозии стенок реактора и снижения потенциала плазмы использовался многощелевой электростатический экран, который был установлен между индуктором и керамической стенкой реактора. В верхний охлаждаемый фланец реактора было интегрировано газораспределительное устройство. В нижней части плазмогенератора располагался механический держатель подложек, охлаждаемый проточной водой для эффективного отвода тепла.
Мощность (до 1000 Вт) от высокочастотного генератора, работающего на частоте 6.78 МГц, подводилась к плазмогенератору через резонансное согласующее устройство. Формирование постоянного напряжения смещения на подложкодержателе обеспечивалось подачей на держатель образца ВЧ-мощности на частоте 13.56 МГц от отдельного генератора. Система вакуумирования состояла из турбомолекулярного насоса (Edwards STP-301C) со скоростью откачки 300 л/с. Регулировка давления в реакторе в ходе процесса производилась за счет изменения проходного сечения высоковакуумного тракта. Предварительная откачка объема реактора и удаление газов с выхлопа турбомолекулярного насоса осуществлялась пластинчато-роторным насосом 2НВР-5ДМ (скорость откачки 5.5 л/с). Диапазон рабочих давлений установки составлял 0.3–10 Па.
В качестве основного газа-травителя использовали гексафторид серы SF6 повышенной чистоты 99.998 (ГОСТ ТУ 6-02-1249-83). Травление проводилось в трех газовых смесях: SF6/Ar, SF6/O2 и SF6/O2/Ar. Рабочие газы в разрядную камеру подавались с помощью регуляторов расхода газа РРГ-10 (Элточприбор), обеспечивающих необходимую величину расхода газа с точностью ±0.25%. Давление в камере измеряли вакуумметром фирмы MKS Instruments с точностью измерения ±0.001% (для прецизионного контроля давления в процессе травления), показания которого не зависят от состава газовой среды. В качестве образцов использовались пластины 4Н-SiC диаметром 76 мм и толщиной 430 мкм с сформированной на поверхности металлической маской в виде слоя Ni толщиной 7 мкм, в котором были созданы окна диаметром от 1 до 3 мм (рис. 2).
Для определения состава и расхода газовой смеси, пригодных для процесса травления, была проведена предварительная серия экспериментов, в которой изучалась возможность минимизации поверхностной плотности морфологических дефектов за счет изменения соотношения химических компонентов травящей смеси. Значения технологических параметров в предварительных экспериментах представлены в табл. 1. Анализ состава поверхности травления после процесса проводился c помощью рентгеновской фотоэлектронной спектроскопии (РФЭС). Измерения выполнялись на многофункциональной установке “Нанофаб 25” с интегрированным в нее аналитическим комплексом фотоэлектронной спектроскопии фирмы SPECS (Германия), погрешность измерений составляла ±0.5%. После выбора оптимального, с точки зрения качества профиля травления, соотношения газов были проведены эксперименты по повышению скорости травления за счет изменения напряжения смещения, подаваемого на держатель подложки. Скорость травления карбида кремния рассчитывалась по результатам измерения глубины травления (h), которая, в свою очередь, определялась по микрофотографиям, полученным с помощью растрового электронного микроскопа Supra 55VP, фирмы Carl Zeiss с точностью ±4 нм.
Таблица 1.
Значения технологических параметров в предварительных экспериментах
Эксперимент, № |
Газовая смесь | Процентное отношение газа- разбавителя, % | Мощность, Вт | Давление, Па | Напряжение смещения, В | Время травления, мин |
---|---|---|---|---|---|---|
1 | SF6/Ar | 25 (Ar) | 800 | 0.75 | –50 | 30 |
2 | SF6/O2/Ar | 25(Ar)/15(O2) | 800 | 0.9 | –50 | 30 |
3 | SF6/O2 | 25(О2) | 800 | 0.75 | –50 | 30 |
Во всех опытах перед началом травления поверхность пластин обрабатывалась в аргоновой плазме в течение 10 мин (расход аргона – 1.305 л/ч при давлении в реакторе – 0.7 Па, уровень поглощаемой ВЧ мощности составлял 750 Вт, а потенциал смещения – –25 В) с целью ее очистки от нежелательных загрязнений.
РЕЗУЛЬТАТЫ И ИХ ОБСУЖДЕНИЕ
Микрофотографии поверхностей подложек SiC, образующихся при травлении в различных газовых смесях (предварительные эксперименты), показаны на рис. 3. Как видно, травление в смесях SF6/Ar и SF6/O2/Ar характеризуется достаточно высоким уровнем дефектообразования на поверхности травления, тогда как наименьшая плотность дефектов была достигнута после процесса травления в газовой смеси SF6/O2. Необходимо отметить, что микрофотографии рис. 3a, рис. 3б делались вблизи центра открытой части пластины, а изображение, представленное на рис. 3в было получено у края пластины, так как в последнем случае дефекты наблюдались только вблизи границы раздела маскированной и открытой частей подложки. Вероятнее всего, наличие дефектов у края пластины связано с переосаждением никелевой маски на открытую поверхность SiC в процессе его травления, что соответствует так называемому эффекту микромаскирования [15].
Рис. 3.
Микрофотографии поверхности окон травления после ПХТ процесса в различных газовых смесях: a – SF6/Ar, б – SF6/O2/Ar и в – SF6/O2.
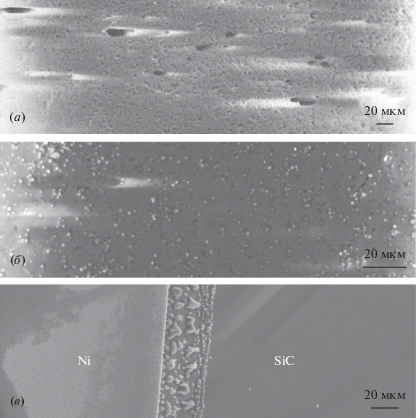
Для того, чтобы проверить это предположение, был изучен элементный состав поверхности травления методом рентгеновской фотоэлектронной спектроскопии. Как видно из рис. 4, на поверхности образца были обнаружены следующие элементы: Si ~ 28.8, C ~ 35.0, O ~ 7.9, F ~ 20.2 и Ni ~ ~ 8.1%, что подтверждает гипотезу о переосаждении частиц никелевой маски, возникающем при ее распылении высокоэнергичными ионами и приводящем к эффекту микромаскирования травящейся поверхности.
Рис. 4.
Рентгеновский фотоэлектронный спектр поверхности окна травления, зарегистрированный после завершения процесса ПХТ.
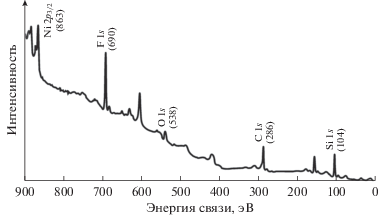
Принимая во внимание результаты предварительных экспериментов, дальнейшие опыты по травлению карбида кремния проводились в плазме смеси SF6/O2, т.к. в этом случае качество поверхности после процесса ПХТ было наилучшим. Известно, что увеличение потенциала смещения на подложке позволяет значительно повышать скорость травления при неизменных величинах остальных технологических параметров [7, 9, 16, 17]. Это обусловлено ростом энергии ионов, бомбардирующих подложку, что приводит к более эффективному распылению материала. Поэтому, в серии последующих контрольных экспериментов изучалось влияние напряжения смещения на скорость травления SiC. Значения технологических параметров в контрольных экспериментах приведены в табл. 2, а на рис. 5 показана зависимость скорости травления от напряжения смещения, прикладываемого к подложке. Как видно из этого рисунка, увеличение напряжения смещения приводит к значительному росту скорости травления (вплоть до 840 нм/мин), причем полученная зависимость носит практически линейный характер.
Таблица 2.
Значения технологических параметров контрольных экспериментов
Эксперимент, № |
Мощность, Вт | Давление, Па | Напряжение смещения, В | Время травления, мин |
---|---|---|---|---|
1 | 800 | 0.75 | –50 | 60 |
2 | 800 | 0.75 | –100 | 60 |
3 | 800 | 0.75 | –150 | 60 |
В качестве примера, на рис. 6 показаны микрофотографии поверхностей травления после проведения контрольных экспериментов № 1 и № 2. Видно, что в обоих случаях на поверхности окон травления наблюдались, так называемые, пиллары – вертикально возвышающиеся над поверхностью травления структуры. Механизмы образования пилларов были изучены в работах [11, 15, 18, 19], где было показано, что их появление может быть связано как с самоорганизацией нелетучих частиц, возникающих в процессе травления, или образованием соединений SiOx, SiFxOy или CFx, скорость травления которых существенно ниже скорости травления SiC в SF6/O2 плазме, так и несовершенством кристаллической структуры карбида кремния.
Рис. 6.
Микрофотографии поверхностей травления: a – контрольный эксперимент № 1, б – контрольный эксперимент № 2.
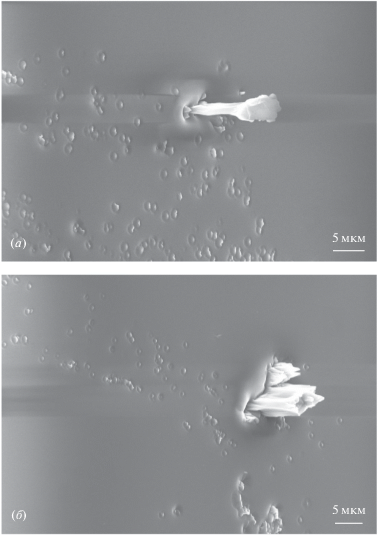
Для борьбы с этими нежелательными дефектами было принято решение обработать образец, который использовался в контрольном эксперименте № 3, дополнительно в аргоновой плазме. Предполагалось, что такая операция позволит устранить нежелательные образования на дне профиля травления за счет их распыления высокоэнергичными ионами аргона. Эта дополнительная процедура выполнялась при следующих технологических параметрах: ВЧ-мощность, поглощаемая в разряде составляла 800 Вт, давление в реакционной камере было равным 0.75 Па, напряжение смещения на держателе подложки было увеличено до –250 В, а время процесса обработки равнялось 5 мин. Результат такой процедуры показан на рис. 7. Как видно из этого рисунка, дополнительная обработка образца в аргоновой плазме способствовала исчезновению пилларов, и получению более гладкой, без эффектов микромаскирования, поверхности травления карбида кремния.
ЗАКЛЮЧЕНИЕ
В результате выполненных экспериментальных исследований по плазмохимическому травлению пластин 4H-SiC в газовых смесях SF6/Ar, SF6/O2 и SF6/O2/Ar установлено, что наиболее перспективным с точки зрения получения бездефектной морфологии поверхности травления карбида кремния, является использование смеси SF6/O2. Использование этой смеси в сочетании с повышенными значениями потенциала смещения на держателе подложки позволило достичь средней скорости травления 840 нм/мин при длительности процесса ПХТ 60 мин и давлении в реакционной камере 0.75 Па. Показано, что перспективным методом устранения, образующихся на поверхности травления пилларов, является дополнительная, кратковременная обработка поверхности в аргоновой плазме.
Список литературы
Иванов П.А., Челноков В.Е. Полупроводниковый карбид кремния – технология и приборы, обзор // Физика и техника полупроводников. 1995. Т. 29. № 11. С. 1921–1943.
Туркин А. Обзор развития технологии полупроводниковых гетероструктур на основе нитрида галлия (GAN) // Полупроводниковая светотехника. 2011. Т. 6. № 14. С. 6–9.
Гольцова М. Силовая полупроводниковая электроника: многообещающие технологии становятся реальностью // Электроника: НТБ. 2014. № 4. С. 54–71.
Rosker M., Bozada C., Deitrich H., Hung A., Via D., Binari S., Vivierios E., Cohen E., Hodiak J. The DARPA wide band gap semiconductors for RF applications (WBGS-RF) program: Phase II results // Proc. Int. CS MANTECH Conference. May 18th–21st. 2009. Tampa, Florida, USA.
Jin H., Qin L., Zhang L., Zeng X., Yang R. Review of wide band-gap semiconductors technology // MATEC Web of Conferences. 2016. V. 40 (ICMES 2015). P. 01006.
Capano M.A., Trew R.J. Silicon carbide electronic materials and devices // MRS Bulletin. 1997. V. 22. № 3. P. 19–23.
Сейдман Л.А. Формирование трехмерных структур в подложках карбида кремния плазмохимическим травлением // Известия высших учебных заведений. Материалы электронной техники. 2015. Т. 18. № 3. С. 157–171.
Осипов К.Ю., Великовский Л.Э. Технология формирования щелевых сквозных металлизированных отверстий к истокам мощных GaN/SiC-транзисторов с высокой подвижностью электронов // Физика и техника полупроводников. 2012. Т. 46. № 9. С. 1239–1243.
Ekinci H., Kuryatkov V.V., Mauch D.L., Dickens J.C., Nikishin S.A. Plasma etching of n-type 4H-SiC for photoconductive semiconductor switch applications // J. Electronic Materials. 2015. V. 44. № 5. P. 1300–1305.
Voss. L.F., Ip K., Pearton S.J., Shul R.J., Overberg M.E., Baca A.G., Sanchez C., Stevens J., Martinez M., Armendariz M.G., Wouters G.A. SiC via fanrication for wide-band-gap high electron mobility transistor/microwave monolithic integrated circuit devices // J. Vac. Sci. Technol. B. 2008. V. 26. № 2. P. 487–494.
Okamoto N., Ohki T., Masuda S., Kanamura M., Inoue Y., Makiyama K., Imanishi K., Shigematsu H., Kikkawa T., Joshin K., Hara N. SiC backside via-hole process for GaN HEMT MMICs using high etch rate ICP etching // Proc. Int. CS MANTECH Conference. May 18th–21st. 2009. Tampa, Florida, USA.
Jiang L., Cheung R., Brown R., Mount A. Inductively coupled plasma etching of SiC in SF6/O2 and etch-induced chemical bonding modifications // J. Appl. Phys. 2003. V. 93. № 3. P. 1376–1383.
Jiang L., Cheung R. Impact of Ar addition to inductively coupled plasma etching of SiC in SF6/O2 // Microelectronic Engineering. 2004. V. 73–74. P. 306–311.
Osipov A.A., Alexandrov S.E., Osipov Ar.A. Optimization of Technological Parameters in Plasma Chemical Etching of Quartz Single Crystals // Russian J. Applied Chemistry. 2016. V. 89. № 6. P. 865–870.
Kathalingam A., Kim M.-R., Chae Y.-S., Sudhakar S., Mahalingam T., Rhee J.-K. Self assembled micro masking effect in the fabrication of SiC nanopillars by ICP-RIE dry etching // Applied Surface Science. 2011. V. 257. № 9. P. 3850–3855.
Kim D.W., Lee H.Y., Park B.J., Kim H.S., Sung Y.J., Chae S.H., Ko Y.W., Yeom G.Y. High rate etching of 6H-SiC in SF6-based magnetically-enhanced inductively coupled plasmas // Thin Solid Films. 2004. V. 447–448. P. 100–104.
Plank N.O.V., Blauw M.A., van der Drift E.W.J.M., Cheung R. The etching of silicon carbide in inductively coupled SF6/O2 plasma // J. Phys. D: Appl. Phys. 2003. V. 36. № 5. P. 482–487.
Okamoto N. Elimination of pillar associated with micropipe of SiC in high-rate inductively coupled plasma etching // J. Vac. Sci. Technol. A. 2009. V. 27. № 2. P. 295–300.
Choi J.H., Latu-Romain L., Bano E., Dhalluin F., Chevolleau T., Baron T. Fabrication of SiC nanopillars by inductively coupled SF6/O2 plasma etching // J. Phys. D: Appl. Phys. 2012. V. 45. № 23. P. 235204.
Дополнительные материалы отсутствуют.
Инструменты
Микроэлектроника