Химическая физика, 2021, T. 40, № 9, стр. 64-71
Математическое моделирование физико-химических свойств теплозащитного материала из высоконаполненных эластомеров
В. Ф. Каблов 1, *, В. Л. Страхов 2, В. О. Каледин 2, Н. А. Кейбал 1
1 Волжский политехнический институт (филиал)
Волгоградского государственного технического университета
Волжский, Россия
2 Центральный научно-исследовательский институт специального машиностроения
Хотьково, Московская обл., Россия
* E-mail: vkablov5@gmail.ru
Поступила в редакцию 30.10.2020
После доработки 16.03.2021
Принята к публикации 22.03.2021
Аннотация
На основании анализа и обобщения результатов теоретических и экспериментальных исследований сформулированы математическая и компьютерная модели изменения физико-химических свойств теплозащитного материала (ТЗМ) из высоконаполненных эластомеров при высокотемпературном нагреве и давлении. Результаты численных расчетов находятся в удовлетворительном согласии с экспериментальными данными.
ВВЕДЕНИЕ
Композитные корпуса современных изделий, работающих при высоких температурах, отличаются от металлических корпусов повышенной деформативностью [1]. Это обусловило необходимость применения для их теплозащиты эластичных теплозащитных материалов (высоконаполненных эластомеров). Для обеспечения требуемых технологических и эксплуатационных качеств теплозащитных материалов (ТЗМ) в состав резиновых смесей вводят порошковые и волокнистые наполнители [1–3]. При изготовлении теплозащитного покрытия (ТЗП) важно учитывать влияние режима термообработки силовой оболочки корпуса и изделия в целом на физико-химические свойства материала, а также их изменение в процессе работы ТЗП в горячем газовом потоке.
В данной работе изложены результаты комплексного математического моделирования поведения ТЗМ на всех этапах жизненного цикла изделия: от изготовления до основной работы в горячем газовом потоке с учетом изменения его свойств. Такой подход позволяет оптимизировать режимы термообработки ТЗМ при изготовлении и учитывать влияние технологии изготовления на его поведение при основной работе изделия.
Проблемы экспериментального определения и математического моделирования пористых материалов рассмотрены в ряде работ, в частности была рассмотрена применимость разных математических моделей для пористых керамических материалов [4–6]. Так, было показано влияние пористости на теплопроводность муллитовых материалов, рассчитанную с использованием моделей с последовательным и параллельным расположениями пор – Максвелла–Эйкена и уравнения EMT [6]. Экспериментальные данные лежат между кривыми, полученными по первой модели Максвелла–Эйкена и уравнению EMT. Данный результат объясняется зависимостью эффективной теплопроводности для двухфазной системы от пористости и микроструктуры. В данных материалах плотный муллитовый керамический скелет представляет собой дисперсионную непрерывную фазу, а воздух является диспергированной фазой. Из-за наличия большого числа взаимосвязанных пор и небольшого числа изолированных пор модели Максвелла–Эйкена не идеально подходят к описанию данных материалов. Однако в результате не полностью произвольного распределения керамического скелета и воздуха в ТЗП уравнение EMT также неприменимо к данным случаям. Карсон с соавт. [4] предложили возможность разделения изотропных пористых материалов на материалы с “внутренней пористостью” (например, губки и пены) и “внешней пористостью” (например, зерна и частицы) в соответствии с различным механизмом теплопереноса в них. В дальнейшем это было подкреплено экспериментальными данными, показавшими, что эффективная теплопроводность материала с внутренней пористостью имеет промежуточное значение между данными, полученными по первой модели Максвелла–Эйкена и уравнению EMT, а эффективная теплопроводность материала – промежуточное значение между данными, полученными по второй модели Максвелла–Эйкена и уравнению EMT [6].
Вопросы моделирования высокопористой теплозащиты на основе базальтового волокна рассмотрены в работе [7]. Предложенная математическая модель теплопередачи в высокопористых материалах на основе волокон дает объяснение природы стационарного режима процесса, учитывает излучение Стефана–Больцмана в порах высокопористого материала, толщину стенки теплозащиты и температуру горячей стенки. Получена зависимость коэффициента теплопроводности высокопористого теплозащитного материала от температуры. Проведенный анализ углубляет представления о параметрах пространства пор волокнистого материала в процессах кондуктивного теплообмена.
В работах [8, 9] исследовано влияние наноразмерных наполнителей разного типа на механизм термодеструкции полиэтилена. Различное влияние углеродных наполнителей на процесс пиролиза объяснено с точки зрения различий в дефектности поверхности наполнителей и их специфического влияния на сегментарную подвижность макрорадикалов полиэтилена.
Математическая модель для полимерных теплозащитных материалов построена на основе общего теоретического описания происходящих в них процессов [10, 11]. В предлагаемой в настоящей работе модели использованы результаты экспериментальных и теоретических исследований, выполненных в последующие годы авторами работ [12–15]. Однако в ранее полученных моделях не учитывается процесс “вспучивания” – порообразования исходно монолитного материала при нагреве высокотемпературным газовым потоком. В результате этого процесса толщина материала многократно возрастает, что обеспечивает его пониженную теплопроводность. В процессе высокотемпературного нагрева в материале протекают физико-химические превращения – пиролиз полимерной матрицы, диффузия газов пиролиза через поры, процессы коксования и др. Важную роль при высоких температурах играет лучистый перенос тепла в порах материала. Кроме того, резиноподобные теплозащитные материалы испытывают большие деформации. Существенным фактором является и внешнее давление, которое может оказать влияние на процесс порообразования.
Целью работы было построение математических моделей поведения зависимостей свойств наполненных эластомерных теплозащитных материалов, испытывающих физико-химические превращения от высокотемпературного воздействии в условиях повышенного давления.
ЭКСПЕРИМЕНТАЛЬНАЯ ЧАСТЬ
Материалы
Объектами исследования служили материалы на основе СКЭПТ (синтетический каучук этилен-пропиленовый тройной). Последний отличается низкой плотностью и имеет одну из самых высоких температур термического разложения среди каучуков. Каучуки вулканизовали серой с ускорителями. Кроме того, в состав материалов в качестве наполнителя вводили тонкодисперсные наполнители – технический углерод и оксид кремния.
Подготовительная обработка
Смешение каучуков с компонентами проводили на лабораторных вальцах в течение 30 мин. Вулканизацию осуществляли в прессе с электрообогревом плит при 165 °С в течение 40 мин.
Определение характеристик
Температуропроводность материала определяли с помощью прибора LFA 467. Испытания по определению огнетеплозащитных свойств ОТЗМ проводили по специально разработанным методикам под действием высокотемпературного газового потока, создаваемого с помощью плазменного аппарата “Мультиплаз 3500”, и контролем температуры на поверхности образца с использованием пирометра С-300.3 “Фотон”. Исследование процессов пиролиза и вспучивания проводили по разработанной нами методике.
Изучение поведения резиноподобного материала при нагреве до температуры 600 °С под давлением до 40 атм проводили на специально изготовленной установке, в которой исследуемый образец находился в цилиндре с поршнем под заданным давлением при заданной температуре.
Для изучения термических превращений использовали методы дифференциальной сканирующей калориметрии.
Результаты и их обсуждение
На основе результатов экспериментальных исследований методами дифференциальной сканирующей калориметрии, динамического механического анализа и лабораторно-стендовых испытаний образцов теплозащитных материалов разработана комплексная математическая модель поведения ТЗМ из резиновых смесей с порошковыми и волокнистыми наполнителями.
К числу отличительных особенностей принятой математической модели поведения ТЗМ относится возможность учета следующих факторов [12–15]:
– тепломассопереноса в слое ТЗП при его изготовлении и основной работе;
– кинетики пиролиза ТЗМ при основной работе ТЗП;
– влияния температуры и степени пиролиза на теплофизические характеристики ТЗМ при основной работе;
– влияния усадки или вспучивания ТЗП на параметры пористого обугленного слоя (ОС), образующегося под его рабочей поверхностью;
– кинетики химического взаимодействия углерода ОС с активными компонентами продуктов сгорания N, N2 (наряду с известными реакциями углерода с O, O2, CO2, H2O);
– кинетики сублимации при повышенных температурах основных компонентов обугленного слоя (углерода и наполнителей ТЗМ).
В состав модели входят уравнения тепломассопереноса в слое теплозащитного покрытия при его изготовлении и основной работе:
$\dot {R} = {{\rho }_{0}}\frac{{\partial \beta }}{{\partial t}}$ для стадии изготовления,
$\dot {R} = \frac{{{{\rho }_{0}}}}{{1 \pm {{\varepsilon }_{V}}}}\frac{{\partial \chi }}{{\partial t}}$ для стадии основной работы.
Здесь T – температура; t – время; φ – пористость материала; c' и ρ' – теплоемкость и плотность каркаса, зависящие от температуры и входящие в уравнение
как функции температуры (ниже, на рис. 3б приведена зависимость теплоемкости от температуры); λΣ – эффективная (суммарная) теплопроводность материала; I'' – энтальпия газа, заполняющего поры; m – массовая скорость фильтрации газа; Q – теплота вулканизации или пиролиза ТЗМ; $\dot {R}$ – объемная скорость газовыделения при вулканизации или при пиролизе ТЗМ; β – степень
вулканизации; χ – степень пиролиза; – массовая доля газов, выделяющихся из ТЗМ при полной вулканизации или пиролизе;
ρ0 – начальная плотность материала; εV – относительная деформация вспучивания (плюс) или усадки (минус).
Уравнения (1), (2) получены из общей системы уравнений тепломассопереноса [6] с учетом результатов работ Димитриенко с соавт. [15] при следующих допущениях:
а) теплообмен между газом (жидкостью), движущимся в сообщающихся порах, и каркасом достаточно интенсивен, и их температуры одинаковы;
б) гетерогенные процессы на поверхности каркаса несущественны;
в) диффузия в порах пренебрежимо мала по сравнению с конвекцией, и массоперенос квазистационарен;
г) скорость перемещения каркаса мала по сравнению со скоростью фильтрации газа (жидкости);
д) значения времени релаксации теплового потока и напряжений в каркасе пренебрежимо малы.
Уравнения (1), (2) решаются совместно с уравнениями кинетики пиролиза ТЗМ [15, 16]:
(3)
$\frac{{d{{\chi }_{i}}}}{{dT}} = {{A}_{{Ti}}}\exp \left( {{{ - {{E}_{i}}} \mathord{\left/ {\vphantom {{ - {{E}_{i}}} {RT}}} \right. \kern-0em} {RT}}} \right)f\left( {{{\chi }_{i}}} \right),$где χi(t) – степень завершенности i-той стадии процесса; ${{A}_{T}} = {A \mathord{\left/ {\vphantom {A {{{b}_{T}}}}} \right. \kern-0em} {{{b}_{T}}}}$; ${{b}_{T}} = \frac{{\partial T}}{{\partial t}}$ – скорость нагрева; t – время; Т – температура; А – предэкспонента (1/с); E – энергия активации (Дж/моль); R – универсальная газовая постоянная (8.314 Дж/моль ⋅ К); f(χi) – модель реакции, представляющая собой набор параметров, позволяющих полностью описать протекание процесса на каждой стадии в зависимости от температуры, скорости нагрева и т.п.
В результате проведенных параметрических расчетов в качестве основной модели реакции f(χi) была выбрана известная модель Праута–Томкинса:
(4)
$f\left( {{{\chi }_{i}}} \right) = {{\left[ {1 - {{\chi }_{i}}\left( T \right)} \right]}^{{{{a}_{i}}}}}{{\left[ {{{\chi }_{i}}\left( T \right)} \right]}^{{{{b}_{i}}}}}.$Температурная зависимость степени завершенности i-той стадии процесса пиролиза определяется из очевидного соотношения:
(5)
${{\chi }_{i}} = \frac{{{{m}_{{0i}}} - {{m}_{i}}\left( T \right)}}{{{{m}_{{0i}}} - {{m}_{{ei}}}}} = \frac{{1 - {{{\bar {m}}}_{i}}\left( T \right)}}{{1 - {{K}_{i}}}},$где $\bar {m}\left( Т \right) = {{m\left( T \right)} \mathord{\left/ {\vphantom {{m\left( T \right)} {{{m}_{0}}}}} \right. \kern-0em} {{{m}_{0}}}}$ – относительное изменение (убыль) массы деструктирующего материала, Ki – массовые доли конденсированного остатка в продуктах пиролиза на i-той стадии процесса, индексы “0” и “e” – начальное и конечное значения.
На основании проведенных исследований для математического моделирования кинетики процесса пиролиза высоконаполненных эластомеров в широком диапазоне условий нагрева предложено использовать следующую систему обыкновенных дифференциальных уравнений:
(6)
$\begin{gathered} \frac{{d{{\chi }_{1}}}}{{dT}} = {{A}_{{T1}}}K\left( T \right)\exp \left( {{{{{E}_{1}}} \mathord{\left/ {\vphantom {{{{E}_{1}}} {RT}}} \right. \kern-0em} {RT}}} \right) \times \\ \times \,\,{{\left[ {1 - \left( {1 - {{\chi }_{1}}} \right){{{\bar {\mu }}}_{{с0}}}} \right]}^{n}}\left( {1 - {{\chi }_{1}}} \right){{{\bar {\mu }}}_{{с0}}}, \\ \frac{{d{{\chi }_{2}}}}{{dT}} = {{A}_{{T2}}}\exp \left( {{{{{E}_{2}}} \mathord{\left/ {\vphantom {{{{E}_{2}}} {RT}}} \right. \kern-0em} {RT}}} \right){{\left( {1 - {{\chi }_{2}}} \right)}^{n}}\chi _{2}^{m}, \\ \frac{{d{{\chi }_{3}}}}{{dT}} = {{A}_{{T3}}}\exp \left( {{{{{E}_{3}}} \mathord{\left/ {\vphantom {{{{E}_{3}}} {RT}}} \right. \kern-0em} {RT}}} \right){{\left( {1 - {{\chi }_{3}}} \right)}^{n}}\chi _{3}^{m}. \\ \end{gathered} $Эта система решается численно методом Рунге–Кутта при следующих начальных условиях: Т = Т0, χ1 = χ2 = χ3 = 0.
Резкий подъем скорости термического разложения при приближении к температуре достижимого перегрева полимера Т* обьясняется тем, что вблизи этой температуры процессы химического и фазового превращения сливаются в единый одностадийный процесс хемофазового превращения полимера, сопровождающийся первоначальным переводом достаточно больших блоков (олигомеров) в газовую фазу и протеканием дальнейших реакций деструкции уже в ней.
При построении математической модели кинетики пиролиза ТЗП, работающих при повышенном уровне давления, необходимо учитывать влияние давления на протекание пиролиза полимерной части композита. С этой целью можно воспользоваться результатами экспериментальных исследований поведения типичного резиноподобного материала при нагреве до температуры 600 °С под давлением до 40 атм, которые показали, что увеличение давления приводит к замедлению выхода продуктов пиролиза из слоя материала.
Для учета влияния давления на кинетику процесса пиролиза в уравнение кинетики первой стадии процесса пиролиза (термической деструкции полимерной части ТЗМ) может быть введена поправка $\Delta E$:
где ${{E}_{{1a}}}$ – энергия активации первой стадии процесса пиролиза при атмосферном давлении. Эта поправка может быть определена на основе экспериментальных данных.
Объяснить закономерность влияния давления на кинетику пиролиза удается с помощью известного уравнения Клапейрона–Клаузиуса, устанавливающего зависимость температуры кипения (Tb) жидкости от давления (p):
(8)
${{T}_{b}} = {{\left( {\frac{1}{{{{T}_{{ba}}}}} - \frac{{R\ln \left( {{p \mathord{\left/ {\vphantom {p {{{p}_{a}}}}} \right. \kern-0em} {{{p}_{a}}}}} \right)}}{{\Delta {{H}_{b}}}}} \right)}^{{ - 1}}},$где ΔHb – теплота кипения, кДж/моль; индекс “a” – атмосферное давление.
Результаты термогравиметрического и газового анализа процесса деструкции ТЗМ при нормальном давлении показывают, что вначале из полимерной части материала выделяются пары́ адсорбированной влаги и летучих растворителей (в незначительном количестве). Затем при температурах, превышающих 150 °С, начинается выход в основном углеводородов различной молекулярной массы.
В работе [17] были исследованы процессы пиролиза высоконаполненных полимеров и оценены молярные энтальпии (теплоты) испарения ряда органических веществ (ΔHb) при температуре кипения (Тb) и давлении 101.325 кПа. Для углеводородов с температурой кипения 130–150 °С теплота испарения имеет значение ≈35 кДж/моль. Температуры начала кипения углеводородных смесей имеют близкие значения.
Из расчета по формуле (8) при указанном значении теплоты испарения следует, что температура начала кипения углеводородных смесей при давлении 30–40 атм увеличивается до 370 °С. Этот факт подтверждает вывод о влиянии давления на кинетику пиролиза ТЗМ. Таким образом, уравнение Клапейрона–Клаузиуса можно использовать для экстраполяции экспериментальных данных по кинетике пиролиза ТЗМ, полученных при нормальном давлении, в область высоких давлений.
Математическая модель, описывающая высокотемпературные теплофизические характеристики резиноподобных теплозащитных материалов, построена в соответствии с показанной на рис. 1 схемой превращений ТЗМ в подповерхностном слое ТЗМ, работающей при интенсивном одностороннем нагреве [12].
Рис. 1.
Схема превращений ТЗМ в подповерхностном слое ТЗМ при одностороннем высокотемпературном нагреве: I – неразложившийся материал, II – зона термического разложения (пиролиза), III – обугленный слой, IV – углеродный слой; 1 – поры, 2 – связующее (каучук со смолой), 3 – частицы неразлагающегося при нагреве наполнителя; 4 – каркас, состоящий из связующего, конденсированного углерода и наполнителя; 5 – каркас, состоящий из конденсированного углерода и наполнителя; 6 – каркас, состоящий из углерода; Т – температура; t – время; х – поперечная координата; ε – степень черноты; индексы: “f” – поток продуктов сгорания, “w” – нагреваемая поверхность ТЗП, “u” – испарение минерального наполнителя, “н.р” и “к.р” – начало и конец термического разложения, “н.п” и “к.п” – начало и конец пластичности, “гр” – граница слоя теплозащиты и силовой оболочки, “доп” – допускаемая температура на границе между ТЗМ и силовой оболочкой корпуса.
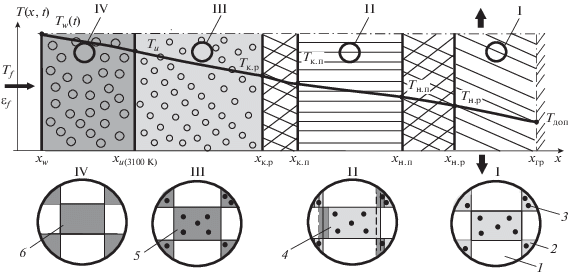
Расчет пористости ТЗМ проводили по формулам [10]
(9)
$\varphi = \left\{ \begin{gathered} 1 - \frac{{\left[ {1 - \chi \left( {1 - K} \right)} \right]{\text{ }}\left( {1 - {{\varphi }_{0}}} \right)}}{{\bar {\rho }\left( {1 \pm {{\varepsilon }_{V}}} \right)}}\,\,{\text{при}}\,\,T < {{T}_{{{\text{исп}}}}}, \hfill \\ 1 - \left( {{{{\bar {\mu }}}_{{{\text{к}}{\text{.у}}}}} + {{{\bar {\mu }}}_{{{\text{т}}{\text{.у}}}}} + {{{\bar {\mu }}}_{{{\text{у}}{\text{.в}}}}}} \right)\frac{{(1 - {{\varphi }_{0}})}}{{\bar {\rho }\left( {1 \pm {{\varepsilon }_{V}}} \right)}}\,\,{\text{при}}\,\,Т \geqslant {{T}_{{{\text{исп}}}}}, \hfill \\ \end{gathered} \right.$где K – массовая доля конденсированного остатка при полной деструкции ТЗМ (коксовое число); $\bar {\mu }$ – массовая доля соответствующих компонентов в составе ТЗМ; $\bar {\rho } = {{\rho {\kern 1pt} '} \mathord{\left/ {\vphantom {{\rho {\kern 1pt} '} {\rho _{{{\text{нач}}}}^{'}}}} \right. \kern-0em} {\rho _{{{\text{нач}}}}^{'}}}$ – относительное изменение плотности каркаса прогретого слоя теплозащиты; Тисп – температура сублимации минерального наполнителя; индексы: “к.у” – конденсированный углерод, “т.у” – порошок технического углерода, “у.в” – углеродные волокна; “0” – начальное значение.
Для учета влияния давления на изменение объема подповерхностного слоя ТЗП вследствие усадки или вспучивания в модель введено следующее условие:
(10)
${{\varepsilon }_{V}} = \left\{ \begin{gathered} {{\varepsilon }_{{{\text{д}}{\text{.в}}}}}\,\,{\text{при}}\,\,p \leqslant {{p}_{{{\text{кр}}}}}, \hfill \\ {{\varepsilon }_{{{\text{д}}{\text{.у}}}}}\,\,{\text{при}}\,\,p > {{p}_{{{\text{кр}}}}}, \hfill \\ \end{gathered} \right.$где εд.в – относительная деформация вспучивания; εд.у – относительная деформация усадки; pкр – критическое значение давления, при котором усадка сменяется вспучиванием.
Расчет относительной деформации вспучивания проводится по формулам, приведенным в работе [14], а для расчета относительной деформации усадки используется формула вида
(11)
${{\varepsilon }_{{{\text{д}}{\text{.у}}}}} = \left\{ \begin{gathered} 0\,\,{\text{при}}\,\,Т \leqslant {{Т}_{{{\text{н}}{\text{.п}}}}}, \hfill \\ \varepsilon _{{{\text{д}}{\text{.у}}}}^{{max}}\frac{{Т - {{Т}_{{{\text{н}}{\text{.п}}}}}}}{{{{Т}_{{{\text{к}}{\text{.п}}}}} - {{Т}_{{{\text{н}}{\text{.п}}}}}}}\,\,{\text{при}}\,\,{{Т}_{{{\text{н}}{\text{.п}}}}} < Т < {{Т}_{{{\text{к}}{\text{.п}}}}}, \hfill \\ \varepsilon _{{{\text{д}}{\text{.у}}}}^{{max}}\,\,{\text{при}}\,\,Т \geqslant {{Т}_{{{\text{к}}{\text{.п}}}}}, \hfill \\ \end{gathered} \right.$полученная при допущении о линейном законе изменения относительной деформации усадки по ширине зоны пластичности.
В предположении о том, что сжатие пор при усадке происходит в зоне пластичности до начального уровня, максимальная относительная деформация усадки может быть определена по формуле
Для расчета эффективной теплопроводности деструктирующего ТЗМ в рабочем диапазоне температур используется обоснованная в работах [7, 8] формула вида
где Мк – параметр контактного термического сопротивления между структурными элементами каркаса,
– теплопроводность пор.
Параметр контактного сопротивления между частицами наполнителя и разлагающейся при нагреве матрицей, Мк, зависит от степени разложения, так как в процессе разложения изменяются состав и физические характеристики матрицы. Для учета этой зависимости предложено использовать линейную интерполяцию между значениями данного параметра при температурах начала и конца термического разложения (индексы “н.р” и “к.р” соответственно):
(13)
${{М}_{{\text{к}}}} = \left\{ \begin{gathered} {{М}_{{{\text{к}}{\text{.н}}}}}\,\,{\text{при}}\,\,Т \leqslant {{Т}_{{{\text{н}}{\text{.р}}}}}, \hfill \\ {{М}_{{{\text{к}}{\text{.н}}}}} + \left( {{{М}_{{{\text{к}}{\text{.к}}}}} - {{М}_{{{\text{к}}{\text{.н}}}}}} \right)\frac{{Т - {{Т}_{{{\text{н}}{\text{.р}}}}}}}{{{{Т}_{{{\text{к}}{\text{.р}}}}} - {{Т}_{{{\text{н}}{\text{.р}}}}}}}\,\,{\text{при}}\,\,{{Т}_{{{\text{н}}{\text{.р}}}}} < Т < {{Т}_{{{\text{к}}{\text{.р}}}}}, \hfill \\ {{М}_{{{\text{к}}{\text{.к}}}}}\,\,{\text{при}}\,\,Т \geqslant {{Т}_{{{\text{к}}{\text{.р}}}}}, \hfill \\ \end{gathered} \right.$где Мк.н – начальное значение контактного сопротивления, Мк.к – конечное значение контактного сопротивления. Начальное значение контактного сопротивления выбирается из условия равенства эффективной теплопроводности материала имеющимся экспериментальным (паспортным) данным при нормальной температуре, а конечное значение принимается как параметр согласования расчета с экспериментом при повышенных температурах.
Входящая в формулу (13) теплопроводность пор складывается из кондуктивной и лучистой составляющих. Кондуктивная составляющая определяется по результатам термодинамического расчета равновесного состава. Для лучистой составляющей использована заимствованная из работ [12] формула: $\lambda _{{\text{л}}}^{{''}} = \Theta {{Т}^{3}}$, где $\Theta = 4{{\varepsilon }^{2}}\sigma h$ – коэффициент лучистого переноса теплоты в порах, ε – степень черноты, σ – постоянная Стефана–Больцмана, h – характерный размер пор. Причем параметр $\Theta $ рекомендовано использовать в качестве параметра согласования математической модели с экспериментом [12, 13]. Для учета изменения размеров пор при усадке–вспучивании в эту формулу введена соответствующая поправка [13]: $\lambda _{{\text{л}}}^{{''}} = \Theta \sqrt[3]{{\left( {1 \pm {{\varepsilon }_{V}}} \right)}}{{Т}^{3}}$.
Формулы для расчета теплофизических характеристик каркаса пористого ТЗМ в зависимости от температуры и степени пиролиза приведены в работе [14]. На основе разработанной математической модели создан программный комплекс – система компьютерного моделирования работы внутренней теплозащиты.
Результаты численного анализа
Численные исследования выполнены для типичного резиноподобного ТЗМ на основе этиленпропиленового каучука плотностью 1060 кг/м3. Для серии результатов термического анализа получены значения параметров кинетики и энергетики процесса пиролиза рассматриваемого ТЗМ, приведенные в табл. 1–3. При расчетах учитывались следующие значения среднеквадратичной погрешности измерений соответствующих параметров: Δm = 0.01, ΔТ = 20 К, ΔQ = 20 кДж/кг.
Таблица 2.
Значения кинетических и энергетических параметров процесса пиролиза ТЗМ для вторичной химической реакции между конденсированным углеродом, образующимся на первой стадии, и диоксидом углерода
bТ, К/с | АТ, 1/К | K2 | Q2, кДж/кг |
---|---|---|---|
0.17 | 130 | 0.45 | 1690 |
0.42 | 120 | 0.74 | 799 |
0.83 | 70 | 0.86 | 430 |
Таблица 3.
Значения кинетических и энергетических параметров процесса пиролиза ТЗМ для вторичной химической реакции между конденсированным углеродом и минеральным наполнителем
bТ, К/с | АТ, 1/К | K3 | Q3, кДж/кг |
---|---|---|---|
0.17 | 180 | 0.82 | 1530 |
0.42 | 150 | 0.97 | 253 |
0.83 | 130 | 0.99 | 84 |
На рис. 2 приведена рассчитанная с использованием формул (7)–(10) температурная зависимость степени завершенности первой стадии процесса пиролиза этого материала при атмосферном давлении (Е1a = 40 кДж/моль) и при давлении, превышающем 40 атм (Е1 = Е1a + ΔE = 63 кДж/моль). Можно видеть, что учет влияния давления на кинетику пиролиза приводит к соответствующему смещению термогравиметрических кривых в область повышенных температур.
Рис. 2.
Температурная зависимость степени завершенности первой стадии процесса пиролиза материала на основе этилен-пропиленового каучука при атмосферном давлении (1) и при давлении, превышающем 40 атм (2).
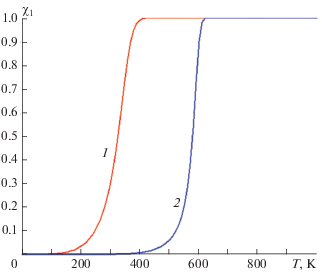
На рис. 3а представлена зависимость от температуры теплопроводности матрицы, которая представляет собой связующее, преобразующееся в зоне пиролиза в кокс, а также эффективной теплопроводности ТЗМ. Можно видеть, что эффективная теплопроводность материала уменьшается в зоне термического разложения и усадки вследствие изменения состава и структуры материала. Ее дальнейший рост обусловлен ростом теплопроводности наполнителя и увеличением лучистого теплопереноса в порах при повышенных температурах.
Рис. 3.
а – Зависимость от температуры теплопроводности кокса (1), теплопроводности матрицы (2), эффективной теплопроводности ТЗМ (3); (б) – зависимость от температуры теплоемкостей матрицы (1), наполнителя (2), каркаса (3).
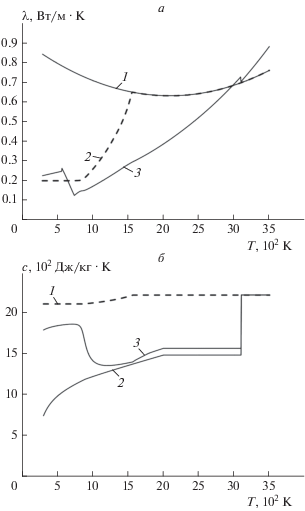
Рисунок 3б иллюстрирует зависимость от температуры теплоемкости разлагающейся при нагреве матрицы, наполнителя и каркаса, состоящего из переходящей в кокс матрицы и неразлагающегося наполнителя. Резкое падение в зоне пиролиза и последующий рост теплоемкости каркаса ТЗМ обусловлены соответствующим изменением состава материала и теплоемкости его компонентов. Резкий скачок теплоемкости при температуре 3100 К связан с испарением наполнителя, имеющего относительно невысокую теплоемкость.
С целью обоснования возможности практического применения разработанной компьютерной модели были проведены расчеты глубины деструкции натурного ТЗП в условиях камеры сгорания двигателя, работающего при высоких температурах. Их результаты представлены на рис. 4 сплошной кривой. На этом же рисунке точками показаны значения глубины деструкции в зависимости от диаметра изделия, определенные по результатам дефектации корпусов после огневых стендовых испытаний двигателя. Сопоставление результатов расчетов и экспериментов показывает, что теоретические и экспериментальные значения глубины деструкции удовлетворительно согласуются между собой. На этом основании можно сделать вывод о правомерности допущений, принятых при разработке математической модели и компьютерной программы.
ВЫВОДЫ
1. Сформулированы математическая и компьютерная модели изменения физико-химических свойств теплозащитных материалов из высоконаполненных эластомеров при высокотемпературном нагреве и давлении. Модели учитывают особенности прогрева и пиролиза наполненных эластомерных материалов, испытывающих значительные деформации и физико-химические превращения по всему объему материала. Полученная в работе информация может служить основой для построения и развития моделей целого класса теплозащитных материалов.
2. Удовлетворительное согласование результатов теоретического моделирования и опытных данных подтверждает справедливость принципов и гипотез, использованных при построении описанных в данной работе моделей.
3. Полученные результаты свидетельствуют о перспективности развиваемого подхода для описания поведения эластомерных теплозащитных материалов в условиях интенсивного теплового воздействия.
Список литературы
Каблов В.Ф., Кейбал Н.А., Новопольцева О.М. Огнетеплозащитные полимерные материалы с функционально-активными компонентами. Волгоград: ВолгГТУ, 2016.
Ahmed A.F., Hoa S.V. // J. Compos. Mater. 2012. V. 46. № 13. P. 1544.
Singh Sangita, Guchhait P.K., Singha N.K., Chaki T.K. // Amer. J. Macromol. Sci. 2014. V. 1. № 1. P. 1.
Carson J.K., Lovatt S.J., Tanner D.J., Cleland A.C. // Intern. J. Heat Mass Transfer. 2005. V. 48. № 11. P. 2150.
Carson J.K., Sekhon J.P. // Intern. Commun. Heat Mass Transfer. 2010. V. 37. № 9. P. 1226.
Gong L., Wang Y., Cheng X., Zhang R., Zhang H. // Intern. J. Heat Mass Transfer. 2013. V. 67. P. 253.
Тарасов В.А., Моисеев В.А., Комков М.А., Боярская Р.В., Филимонов А.С. // Хим. физика. 2016. Т. 35. № 7. С. 92.
Ломакин С.М., Шаулов А.Ю., Коверзанова Е.В., Усачев С.В., Шилкина Н.Г., Берлин А.А. // Хим. физика. 2019. Т. 38. № 4. С. 74.
Коверзанова Е.В., Усачев С.В., Ломакин С.М., Шилкина Н.Г., Шаулов А.Ю., Берлин А.А. // Хим. физика. 2019. Т. 38. № 6. С. 53.
Полежаев Ю.В., Юревич Ф.Б. Тепловая защита. М.: Энергия, 1976.
Панкратов Б.М., Полежаев Ю.В., Рудько А.К. Взаимодействие материалов с газовыми потоками. М.: Машиностроение, 1976.
Страхов В.Л., Гаращенко А.Н., Кузнецов Г.В., Рудзинский В.П. // Мат. моделирование. 2000. Т. 11. № 5. С. 107.
Страхов В.Л., Гаращенко А.Н., Кузнецов Г.В., Рудзинский В.П. // Теплофизика высоких температур. 2000. Т. 38. № 6. С. 958.
Страхов В.Л., Атаманов Ю.М., Кузьмин И.А., Бакулин В.Н. // Теплофизика высоких температур. 2017. Т. 55. № 4. С. 528.
Димитриенко Ю.И., Коряков М.Н., Захаров А.А., Строганов А.С. // Мат. моделирование и численные методы. 2014. № 3. С. 3.
Шленский О.Ф. Горение и взрыв материалов. Новые аспекты. М.: Инновационное машиностроение, 2015.
Lide D.R. // CRC Handbook of Chemistry and Physics. 85th ed. N.Y.: CRCPress, 2004.
Дополнительные материалы отсутствуют.
Инструменты
Химическая физика