Теплофизика высоких температур, 2022, T. 60, № 5, стр. 781-788
Гидротермальное окисление алюминия и металлогидридное компримирование водорода
А. З. Жук 1, В. И. Борзенко 1, П. П. Иванов 1, *
1 Объединенный институт высоких температур РАН
Москва, Россия
* E-mail: peter-p-ivanov@yandex.ru
Поступила в редакцию 29.11.2021
После доработки 11.03.2022
Принята к публикации 07.06.2022
- EDN: TSKPHA
- DOI: 10.31857/S0040364422050180
Аннотация
Предложена схема производства водорода методом гидротермального окисления алюминия в сочетании с технологией утилизации тепла реакции окисления алюминия в металлогидридных циклах. Металлогидридные циклы используются для сжатия водорода до давления 90 МПа и производства электроэнергии. Методом термодинамического моделирования рассчитаны энергетические и материальные балансы процессов. Расчеты показали, что использование метода гидротермального окисления алюминия в сочетании с металлогидридными утилизационными циклами позволяет увеличить эффективность использования энергоносителя на 14%.
ВВЕДЕНИЕ
В настоящее время в большинстве экономически развитых стран активно реализуются программы широкого внедрения водородных энергетических технологий. При этом одной из наиболее актуальных задач является организация экономически эффективного массового производства высококачественного, химически чистого водорода, не сопровождающегося массированным выбросом в атмосферу парниковых газов. С этой точки зрения весьма перспективной оказывается технология гидротермального окисления алюминия (ГТОА).
В работе [1] показано, что стоимости водорода, полученного электролизом воды, и водорода, полученного методом гидротермального окисления алюминия, оказываются сопоставимыми, если цена электроэнергии в регионах производства энергоносителей находится на уровне 1–3 цента за кВт ч. При цене электроэнергии ниже двух центов за кВт ч водород, полученный методом гидротермального окисления алюминия, оказывается дешевле, чем водород, полученный методом электролиза воды. Такое соотношение затрат на производство водорода обусловлено тем, что суммарный расход электроэнергии при производстве водорода методом ГТОА (около 130 кВт ч/кг H2) выше, чем для электролиза воды (около 66 кВт ч/кг H2), а приведенные капитальные затраты для технологии ГТОА в три раза ниже. Соответственно, производство водорода по технологии ГТОА целесообразно в регионах, где имеется или может быть создано производство алюминия, использующее дешевую электроэнергию, получаемую, например, на крупных ГЭС или АЭС. При этом непосредственно на месте производства водорода наличия развитой энергетической инфраструктуры не требуется. К месту производства водорода алюминий может доставляться любым видом наземного или водного транспорта. Авторы [1] предложили использовать тепло, выделяющееся в реакции гидротермального окисления алюминия, для компримирования водорода, что повышает энергоэффективность процесса.
Низкая стоимость реактора ГТОА, его энергонезависимость, а также возможность получения сжатого водорода в едином технологическом цикле делает технологию гидротермального окисления привлекательной при создании локальных источников водорода в районах со слаборазвитой энергетической инфраструктурой. Например, для создания сети станций для заправки водородного транспорта, а также на объектах инфраструктуры, где необходимо экологически чистое совместное производство тепловой и электрической энергии.
В настоящей работе методами термодинамического моделирования исследуются следующие физико-химические процессы:
– реакция гидротермального окисления алюминия, дающая на выходе паро-водородную газовую смесь и конденсированную смесь воды и бемита;
– получение окиси алюминия ${\text{A}}{{{\text{l}}}_{2}}{{{\text{O}}}_{3}}$ из бемита для последующего восстановления алюминия в процессе Холла–Эру;
– получение водорода из паро-водородной смеси, состоящей из химически чистого водорода и пара; сконденсированная вода возвращается в цикл ГТОА;
– компримирование водорода до уровня 90 МПа за счет теплового эффекта реакции гидротермального окисления алюминия с помощью металлогидридного термосорбционного компрессора;
– преобразование излишков низкотемпературного тепла в электроэнергию с помощью металлогидридного утилизационного цикла.
Моделирование производилось с помощью программы расчета термодинамического равновесия в многокомпонентной гетерогенной системе с использованием свойств индивидуальных веществ из базы данных ИВТАНТЕРМО [2]. Тексты программ на языке Delphi7SE выложены в Mendeley Data [3].
РЕАКЦИЯ ГИДРОТЕРМАЛЬНОГО ОКИСЛЕНИЯ АЛЮМИНИЯ
В представленных ниже расчетах материальных и энергетических балансов используются экспериментальные данные, получение в работах [1, 4, 5]. При температуре реагентов 300 К и давлении в реакторе 15 МПа реакция гидротермального окисления алюминия происходит с образованием бемита:
(1)
$\begin{gathered} {\text{Al}} + 2{{{\text{H}}}_{2}}{\text{O}} \to {\text{AlOOH}} + \\ + \,\,1.5{{{\text{H}}}_{2}} + 415.24{\text{ кДж/моль}}{\text{.}} \\ \end{gathered} $Температура в реакторе и, соответственно, фазовый состав продуктов реакции зависят от соотношения расходов воды и алюминия mw. Опыт эксплуатации установок ГТОА [4, 5] показывает, что при mw = 6.1 окисление алюминия идет по реакции (1) [6, 7].
Из реактора выводится смесь бемитa с водой (конденсированная фаза) и смесь водорода с водяным паром – газовая фаза.
Для конкретизации масштаба технологических циклов выбрана производительность по водороду 0.01 кг/c (36 кг/ч), что приблизительно соответствует параметрам перспективных модулей электролизных установок [8–10]). Расходы реагентов в г/с, требуемые для этой производительности, показаны на схеме рис. 1. Расход алюминия составляет 320 кг/ч, и при среднем удельном расходе энергии на получение алюминия из глинозема с помощью электролиза (процесс Холла–Эру) 14 кВт·ч/кг Al требуемая мощность электролизера составляет 4498 кВт.
Рис. 1.
Расходные и энергетические характеристики комплекса для производства водорода 36 кг/ч: 1 – электролизер для производства алюминия, 2 – реактор ГТОА, 3 – печь для кальцинации бемита, 4 – теплообменник/конденсатор; в квадратных скобках даны значения расходов.
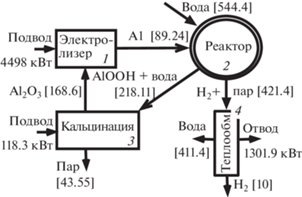
Для расхода алюминия 89.2 г/с стехиометрический расход воды по реакции (1) составляет 119 г/с. Избыток воды позволяет контролировать температуру и давление в реакторе в диапазоне 573–623 К и 12–16 МПа [4, 5]. При расходе воды 544.4 г/с температура реакции равна 598.4 К. Состав продуктов реакции в весовых долях: пар – 0.65, вода – 0.022, бемит – 0.31, H2 – 0.016.
На выходе образуются два продукта: газообразный, состоящий из водорода и водяного пара, доля которого в общем расходе составляет 0.666, и конденсированный, состоящий из бемита и воды, доля которого в общем расходе составляет 0.334. В газообразном продукте весовая доля водяного пара составляет 0.98, а в конденсированном весовая доля бемита составляет 0.94.
Следует отметить, что установка ГТОА расходует некоторое количество электроэнергии на собственные нужды. Перед началом работы реактор ГТОА прогревается до 300°С с помощью электронагревателя. После первого впрыска нагрев отключается, и температура поддерживается за счет теплового эффекта реакции окисления. После выхода на режим электроэнергия продолжает расходоваться на привод насоса высокого давления, электромагнитных клапанов и работу контрольно-измерительной аппаратуры. Для выработки электроэнергии, расходуемой на собственные нужды, авторы [4, 5] использовали воздушно-водородные топливные элементы. Эксперименты показали, что расход электроэнергии на собственные нужды составляет не более 2% от установленной мощности установок ГТОА.
ВОССТАНОВЛЕНИЕ ОКИСИ АЛЮМИНИЯ Al2O3 ИЗ КОНДЕНСИРОВАННОГО ПРОДУКТА
В рассматриваемом случае из реактора выходит 212.2 г/с конденсированной смеси, состоящей из бемита и воды, при температуре 598.4 К и под давлением 15 МПа. Процесс получения γ-Al2O3 из этой смеси состоит из нескольких простых термодинамических процессов.
1) Приведение давления к 1 атм. Температура снижается до 507.1 К. Состав (в весовых долях) следующий: пар – 0.06, бемит – 0.94.
2) Сепарация пара (выход пара – 13.75 г/с). Остается один бемит с расходом 198.4 г/с при температуре 507.1 К.
3) Изотермический подвод тепла – 118.3 кВт. Бемит разлагается на окись алюминия γ-Al2O3 (0.85) и водяной пар (0.15).
4) Сепарация пара (выход пара – 29.8 г/с). Остается 168.6 г/с γ-Al2O3 при температуре 507.1 К. Таким образом, для утилизации также доступно тепло, содержащееся в 43.55 г/с пара с температурой 507.1 К и давлением 1 атм. В турбине с конденсатором при выходном давлении 0.1 атм можно получить дополнительную мощность 15.36 кВт.
ОБРАБОТКА ПАРО-ВОДОРОДНОЙ СМЕСИ
Схема обработки паро-водородной смеси представлена на рис. 2. Она включает в себя вымораживание водяного пара с помощью охлаждения смеси до 290 К, возврат в цикл конденсата с расходом 411.4 г/с, сжатие чистого водорода при расходе 10 г/с до 90 МПа с помощью термосорбционного компрессора водорода (ТСКВ). Преобразование 1120.7 кВт тепла от охлаждения паро-водородной смеси в электроэнергию осуществляется в металлогидридном утилизационном блоке (МГУБ). МГУБ представляет собой металлогидридный компрессор, сопряженный с машиной расширения водорода.
Рис. 2.
Схема получения сжатого водорода и электроэнергии из паро-водородной смеси с помощью металлогидридной технологии: 1 – теплообменник, 2 – металлогидридный утилизационный блок, 3 – термосорбционный компрессор водорода; в квадратных скобках даны значения расходов.
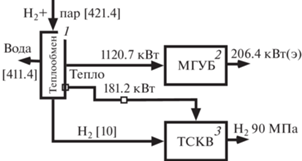
Состав паро-водородной смеси при 290 К и 15 МПа: пар – 2.8 × 10–5, вода – 0.976, H2 – 0.024. После вывода конденсата состав чистого водорода такой: пар – 0.0012, H2 – 0.9988 (объемное содержание водорода – 0.9999).
При охлаждении паро-водородной смеси выделяется 1301.9 кВт тепла. Из этого количества 181.2 кВт используется для компримирования водорода до 90 МПа с помощью ТСКВ, остальные 1120.7 кВт преобразуются в электричество в другом ТСКВ, работающем в режиме металлогидридного утилизационного блока.
Компримирование водорода до давления 90 МПа. Товарный водород, например для применения на водородных заправочных станциях, должен иметь давление до 90 МПа. При использовании механических компрессоров затраты электроэнергии на сжатие до этого уровня давления оказываются не менее 4.0 кВт ч/кг Н2 [11, 12]. Для компримирования водорода, полученного в процессе ГТОА, целесообразно использовать металлогидридный ТСКВ [13, 14], который позволяет осуществить прямое преобразование низкопотенциального тепла реакции окисления в механическую энергию сжатого водорода.
Четырехтактный металлогидридный термосорбционный цикл для повышения давления водорода с 15 до 90 МПа рассчитан по модели, подробно описанной в Приложении. Для одноступенчатого металлогидридного компрессора выбран сплав TiCr1.5Mn0.25Fe0.25 [14].
Предельные значения насыщенности ${{X}_{1}}$ и ${{X}_{2}}$ в модели выбраны как границы линейного участка изобар $T = f\left( X \right)$ (см. уравнение (4) Приложения). На рис. 3 представлены такие изобары для двух сплавов: TiCr1.5Mn0.25Fe0.25 [14] и LaFe0.5Mn0.3Ni4.8 [15]. Для каждого сплава выбраны характерные значения давления в цикле их использования – 15, 90 МПа и 15, 0.1 МПа. Выбор 0.15 и 0.75 в качестве предельных значений насыщенности представляется приемлемым для всех четырех вариантов. Температура холодильника (охлаждающей воды) принята равной 283 К. Температурный напор при охлаждении принят равным 5 К, при нагреве – 35 К. Температура нагревателя равна 506 К. Это результат последующей подгонки равновесного давления в конце третьего такта (табл. 1) – оно должно быть на 10% больше номинального давления 90 МПа.
Таблица 1.
Параметры ТСКВ на концах тактов цикла
№ такта | Длительность, с | Насыщенность водородом | Температура, К | Давление, МПа | Тепло, кДж |
---|---|---|---|---|---|
1 | 674.0 | 0.75 | 288.1 | 8.35 | –434.8 |
2 | 97.0 | 0.75 | 471.3 | 191.7 | 381.1 |
3 | 748.0 | 0.15 | 471.3 | 99.7 | 435.2 |
4 | 192.0 | 0.15 | 288.1 | 4.34 | –381.2 |
Данные о четырех тактах работы одноступенчатого металлогидридного компрессора сведены в табл. 1 в виде итогов в конце такта (подробнее см. Приложение). Это значит, что начальное состояние перед первым тактом по насыщенности, температуре и давлению можно видеть в строке для четвертого такта. Во время такта № 1 происходит сорбция водорода при охлаждении металлогидрида при постоянной температуре 288.1 К, насыщенность растет от 0.15 до 0.75, равновесное давление – от 4.34 до 8.35 МПа. Во время такта № 2 происходит нагрев системы до 471.3 К с повышением равновесного давления до 191.7 МПа при постоянной насыщенности. Изотермическая десорбция водорода происходит в такте № 3 при температуре 471.3 К. Такт № 4 – возвращение системы к температуре 288.1 К при минимальной насыщенности водородом.
Длительность цикла составляет 1711 с. За один цикл подводится 816.3 кДж тепла и сжимается 45.05 г водорода. Интерес представляют цифры для стационарного режима, которые получаются в результате осреднения за цикл тепловой мощности и расхода водорода, т.е. в результате деления количеств тепла и водорода на длительность цикла – 0.477 кВт и 0.02633 г/с. Пренебрегая нелинейностью зависимости характеристик от единичной мощности, находим, что для сжатия водорода расходом 10 г/с (рис. 2) нужна установка в 10/0.02633 = 379.8 раз большей производительности, чем рассмотренная, которая будет потреблять 0.477 × 379.8 = 181.2 кВт тепла.
Утилизация тепла паро-водородной смеси в электроэнергию. На рис. 2 показано, что 1120.7 кВт потока тепла, выносимого из реактора с паро-водородной смесью, преобразуются в электричество в МГУБ. В данном блоке водород сжимается в термосорбционном компрессоре за счет тепла реакции окисления и далее производит работу в процессе возвращения параметров водорода к исходному состоянию. В проведенных расчетах не рассматривается конкретный тип механизма расширения, однако предполагается, что его КПД составляет 85%. Это типичный уровень внутреннего КПД паровых и газовых турбин.
В утилизационном блоке не требуются высокие давления, поэтому для термосорбционного цикла в данном случае выбран хорошо изученный гидридообразующий материал – LaFe0.5Mn0.3Ni4.8 [15]. Для предельных значений насыщенности ${{X}_{1}}$ и ${{X}_{2}}$, температуры холодильника и температурных напоров в расчетах использованы те же исходные данные, что и в предыдущем разделе для цикла компримирования. Температура нагревателя 550 К подобрана для получения максимума генерируемой электрической мощности. Для цикла компримирования температура нагревателя подбиралась по величине давления в конце третьей фазы и оказалась равной 506 К. Дополнительной иллюстрацией этой разницы температур служит рис. 3, где изобара 15 МПа для сплава LaFe0.5Mn0.3Ni4.8 выше по температуре, чем для сплава TiCr1.5Mn0.25Fe0.25.
Аналогично предыдущему циклу результаты для четырех тактов данного сведены в табл. 2 в виде итогов в конце такта. В такте № 3 выход водорода равен ${{\rho }_{{{{{\text{H}}}_{2}}}}}{{V}_{{{\text{max}}}}}\left( {{{X}_{2}} - {{X}_{1}}} \right)$ = 0.04 кг при изменении давления от 25 до 13 МПа. При расширении водорода в турбине с внутренним КПД 85% до максимального давления первой фазы цикла 0.042 МПа (в расчетах принят запас давления в 10%, что дает 0.05 МПа) может быть получена полезная мощность 208.1 кДж. Суммарный подвод тепла во втором и третьем тактах составляет 1176.3 кДж. Четырехтактный термосорбционный цикл длится 1607 с.
Таблица 2.
Параметры металлогидридного термосорбционного цикла в конце каждого такта
№ такта | Длительность, с | Насыщенность водородом | Температура, К | Давление, МПа | Тепло, кДж |
---|---|---|---|---|---|
1 | 624 | 0.75 | 288.1 | 0.042 | –702.9 |
2 | 107 | 0.75 | 515.5 | 25.06 | 473.0 |
3 | 673 | 0.15 | 515.5 | 13.04 | 703.3 |
4 | 203 | 0.15 | 288.1 | 0.022 | –473.1 |
Если перейти к условным характеристикам стационарного режима, которые получаются в результате осреднения электрической и тепловой мощности за один цикл, т.е. в результате деления значений энергии на длительность цикла, то получаем следующие данные: 208.1/1607 = 0.1295 кВт электрических и 1176.3/1607 = 0.732 кВт тепловых.
Схему рис. 2 можно рассматривать как схему гибридной энергетической установки для преобразования тепловой энергии в электрическую с одновременным использованием части тепла для компримирования водорода. Основным источником тепла является паро-водородная смесь. Каждая из двух металлогидридных установок представляeт собой источник и сток тепла с T–Q-диаграммами (Q – объемный расход водорода, м3/с), которые легко рассчитать с помощью табл. 1, 2. Мощность утилизационного блока в гибридной энергетической установке определяется из условия, чтобы минимальный температурный напор между суммарными T–Q-диаграммами для источников и стоков тепла (рис. 4) равнялся заданному минимуму (здесь 35 К – часто используемое в литературе значение для сравнения циклов газотурбинных установок). В данном случае это условие достигается увеличением тепловой мощности утилизационного блока в 1594 раза. При этом генерируемая электрическая мощность становится равной 1594 × 0.1295 = 206.4 кВт. Соответственно КПД утилизационного блока по отношению к утилизируемой тепловой мощности 1120.7 равен 18.4%.
РАСХОДНО-ЭНЕРГЕТИЧЕСКИЕ ХАРАКТЕРИСТИКИ УСТАНОВКИ ПОЛУЧЕНИЯ ВОДОРОДА ПО ТЕХНОЛОГИИ ГТОА + ТСКВ + МГУБ
Расходы реагентов и продуктов реакции комплекса ГТОА + ТСКВ производительностью водорода 36 кг/ч приведены в табл. 3. Электрическая мощность потребляется только электролизером. Сжатие водорода в ТСКВ производится за счет тепла паро-водородной смеси из реактора ГТОА. Утилизация избытка тепла ГТОА производится с помощью МГУБ. Учтена также возможность утилизации пара от кальцинации.
Таблица 3.
Расходные и энергетические характеристики комплекса для производства водорода 36 кг/ч
Расход алюминия, г/с | 89.24 |
Расход воды в реактор, г/с | 544.4 |
Выход водорода, г/с | 10 |
Возврат воды, г/с | 454.9 |
Возврат окиси алюминия, г/с | 168.6 |
Мощность электролизера, кВт (14 кВт ч/кг Al) | 4498 |
Расход энергии на кальцинацию, кВт | 118.3 |
Утилизация пара при кальцинации, кВт | 15.36 |
Утилизация тепла паро-водородной смеси, кВт | 206.4 |
Табл. 4 иллюстрирует ступени преобразования теплотворной способности алюминия в теплотворную способность водорода. В колонке “Формулы” приведены функциональные соотношения между процессами из колонки “Идентификаторы” (там, где это возможно без увеличения числа строк в таблице).
Таблица 4.
Эффективность преобразования теплотворной способности алюминия в теплотворную способность водорода
Идентификаторы | Описание | Формулы | Значения |
---|---|---|---|
A | Мощность в реакции окисления алюминия в кислороде, кВт | 2769.3 | |
B | Мощность сгорания водорода (высшая), кВт | 1428.8 | |
C | Мощность реакции окисления алюминия в воде, кВт | C = D + E | 1385.9 |
D | Выход тепла с паро-водородной смесью, кВт | 1301.9 | |
E | Выход тепла со смесью бемита с водой, кВт | 84 | |
F | Тепло, использованное в металлогидридном компрессоре, кВт | 181.2 | |
G | Утилизация остатка тепла паро-водородной смеси (D – F) с КПД 18.4%, кВт | G = 0.184(D – F) | 206.4 |
H | Утилизация пара при кальцинации, кВт | 15.36 | |
I | Коэффициент преобразования в теплоту сгорания водорода (без утилизации тепла) | I = B/A | 0.516 |
J | Коэффициент преобразования в теплоту сгорания водорода (c утилизацией тепла) | J = (B + F + G + H)/A | 0.661 |
ЗАКЛЮЧЕНИЕ
Предложена схема производства водорода методом гидротермального окисления алюминия в сочетании с технологией утилизации тепла реакции окисления алюминия в металлогидридных циклах. Металлогидридные циклы используются для сжатия водорода до давления 90 МПа и производства электроэнергии. Методом термодинамического моделирования рассчитаны энергетические и материальные балансы процессов.
Термодинамическое моделирование технологических процессов выполнено для производительности водорода 36 кг/ч. Преобразование теплотворной способности алюминия в теплотворную способность водорода происходит с КПД 51.6%.
Паро-водородная смесь выносит из реактора 1301.9 кВт тепла. Часть низкопотенциального тепла мощностью 181.2 кВт используется для компримирования водорода до давления 90 МПа с помощью металлогидридного термосорбционного компрессора. Остаток тепла, полученного от паро-водородной смеси, с помощью металлогидридного утилизационного цикла преобразуется в электрическую мощность 206.4 кВт. Использование металлогидридных компрессоров для утилизации тепла реакции ГТОА позволяет увеличить эффективность технологического процесса получения сжатого водорода на 14%.
Список литературы
Жук А.З., Борзенко В.И., Бузоверов Е.А., Иванов П.П. Оценка конкурентоспособности технологий получения “зеленого” водорода: “безуглеродный” алюминий и электролиз воды // Вестник ОИВТ РАН. 2021. Т. 6. С. 21.
Белов Г.В., Иориш В.С., Юнгман В.С. Моделирование равновесных состояний термодинамических систем с использованием ИВТАНТЕРМО для Windows // ТВТ. 2000. Т. 38. № 2. С. 209.
Ivanov P. AL_H2_Soft // Mendeley Data. 2021. V. V1. https://data.mendeley.com/datasets/g6pp9cpfc9/1
Grigorenko A.V., Shkolnikov E.I., Zhuk A.Z., Vlaskin M.S. Experience in Creation and Exploitation of Energetic and Energy-technological Plants Based on Hydrothermal Oxidation of Aluminum // IOP Conf. Ser.: Mater. Sci. Eng. 2018. V. 381. 012049.
Vlaskin M.S., Shkolnikov E.I., Bersh A.V. et al. An Experimental Aluminum-fueled Power Plant // J. Power Sources. 2011. V. 196. P. 8828.
Laubengayer A.W., Weisz R.S. A Hydrothermal Study of Equilibria in the System Alumina–Water // J. Amer. Chem. Soc. 1943. V. 65. № 2. P. 247.
Kennedy G.C. Phase Relations in the System of Al2O3–H2O at High Temperatures and Pressures // Amer. J. Sci. 1959. V. 257. № 8. P. 563.
Green Hydrogen Cost Reduction: Scaling up Electr-olysers to Meet the 1.5°C Climate Goal. Abu Dhabi: International Renewable Energy Agency, 2020. https://clck.ru/334UfY
Christensen A. Assessment of Hydrogen Production Costs from Electrolysis: United States and Europe. Final Release. June 18, 2020. https://theicct.org/sites/default/files/icct2020_assessment_of_hydrogen_production_costs_v1.pdf
Air Liquide Inaugurates 20MW PEM Electrolyser in Québec, Canada // NS Energy. 2021. https://www.nsenergybusiness.com/news/air-liquide-quebec-pem-electrolyser/#
Parks G., Boyd R., Cornish J., Remick R. Hydrogen Station Compression, Storage, and Dispensing. Technical Status and Costs. Tech. Rep. NREL/BK-6A10-58564. May 2014.
Penev M., Zuboy J., Hunter Ch. Economic Analysis of a High-pressure Urban Pipeline Concept (HyLine) for Delivering Hydrogen to Retail Fueling Stations // Transportation Research. Part D: Transport and Environment. 2019. V. 77. P. 92. https://doi.org/10.1016/j.trd.2019.10.005
Glagoleva-Khayrullina A., Blinov D., Borzenko V. Novel kW Scale Hydrogen Energy Storage System Utilizing Fuel Cell Exhaust Air for Hydrogen Desorption Process from Metal Hydride Reactor // Energy. 2019. V. 183. P. 1244.
Lototskyy M.V., Yartys V.A., Pollet B.G., Bowman R.C. Jr. Metal Hydride Hydrogen Compressors: A Review // Int. J. Hydrogen Energy. 2014. V. 39. P. 5818.
Blinov D.V., Borzenko V.I., Dunikov D.O., Romanov I.A. Experimental Investigations and a Simple Balance Model of a Metal Hydride Reactor // Int. J. Hydrogen Energy. 2014. V. 39. P. 19361.
Бочарников М.С. Разработка и исследование металлогидридных компрессоров водорода высокого давления для систем аккумулирования энергии. Дис. … канд. техн. наук. Черноголовка: Ин-т проблем хим. физики РАН, 2019.
Дополнительные материалы отсутствуют.
Инструменты
Теплофизика высоких температур