Теплофизика высоких температур, 2022, T. 60, № 5, стр. 657-665
Плазменное алитирование стали фольгой при температуре ниже температуры плавления алюминия
H. Mahmoudi 1, S. M. M. Hadavi 1, 2, *, Y. Palizdar 1
1 Materials and Energy Research Center
Karaj, Iran
2 Tarbiat Modares University
Tehran, Iran
* E-mail: s.hadavi@modares.ac.ir
Поступила в редакцию 08.08.2019
После доработки 08.08.2019
Принята к публикации 19.05.2021
- EDN: EVXLGE
- DOI: 10.31857/S0040364422050088
Аннотация
В работе исследуется алитирование стали AISI 4340, когда образец покрывался алюминиевой фольгой (Al–1.6 мас. % Si) толщиной 50 мкм и помещался на место катода генератора тлеющего разряда. Образец нагревался при повышении силы тока и постепенном повышении давления и напряжения. Установка рассчитана на обработку образца при 600°С (температура плавления алюминия). Для сравнения проведен эксперимент при 750°С. Алюминирование проводилось в течение примерно 5 мин при рабочей температуре. Характеристики покрытия исследованы с помощью автоэмиссионной сканирующей электронной микроскопии, энергодисперсионной спектроскопии и рентгеновской дифракции. Покрытие состояло из двойного слоя толщиной 90 мкм из богатых алюминием фаз FeAl3 и Fe2Al5 под алюминием в процессе обработки при 600°C. Сделан вывод о том, что воздействие плазмы заключалось не только в нагреве образца, но и в обеспечении диффузионной пары Al–сталь и усилении взаимной диффузии элементов железа и алюминия в алюминидах железа с высоким содержанием алюминия. Плазменное алитирование фольгой при 750°С привело к формированию многослойного покрытия, состоящего из фаз алюминида железа (Fe2Al5 и FeAl) толщиной ~140 мкм. Сравнение толщины покрытия, полученного в данном исследовании, с толщиной покрытия, полученного при горячем алитировании погружением, показало, что бомбардировка ионами поверхности образца во время плазменного процесса увеличивает толщину покрытия за счет активации поверхности и усиления взаимной диффузии железа и алюминия в алюминидах.
ВВЕДЕНИЕ
Алитирование – обработка поверхности для повышения стойкости подложки к высокотемпературному окислению и коррозии [1–3]. Фактически во время эксплуатации при высоких температурах на алитированной поверхности образуется относительно плотный оксид алюминия, который действует как пассивный слой для дальнейшей диффузии анионов и/или катионов. Алюминидные покрытия изготавливаются с использованием различных диффузионных и диффузионно-наплавочных процессов. Пакетное алитирование, заключающееся в диффузии алюминия в ходе реакции галогенидных активаторов с алюминиевым порошком, является основной технологией обработки в диффузионных процессах. Горячее алитирование, т.е. погружение основного металла в расплавленный алюминий при последующей диффузионной обработке, является широко используемым методом среди диффузионно-наплавочных технологий. Интерес представляет получение адгезивных алюминидных фаз в качестве слоя покрытия с высоким содержанием алюминия. Также ценность представляет процесс, позволяющий сократить время нанесения покрытия и снизить рабочую температуру как с технической, так и с экономической точки зрения.
Помимо традиционных диффузионных и диффузионно-наплавных методов, в последнее время практикуется плазменно-пастовое алитирование титановых сплавов [4] и сталей [5, 6]. В этом методе алюминиевый порошок в качестве прекурсора помещается на поверхность основного металла, где алюминий диффундирует в поверхность подложки с помощью энергии, вырабатываемой при ионной бомбардировке из плазмы тлеющего разряда. Однако введение других легирующих элементов совместно с алюминием затруднено из-за неравномерности распределения порошковых добавок на поверхности подложки. В [7] использовалась алюминиевая фольга для алитирования углеродистой стали. Пять листов алюминиевой фольги толщиной 20 мкм прессовались на верхнюю часть стальной подложки, чтобы получить источник Al общей толщины 100 мкм для диффузионной пары. Перед диффузионной обработкой образцы нагревались до 650°С и выдерживались в течение 1 ч в вакууме (10–3 Па). Микроструктура образца состояла из одного слоя Al толщиной 100 мкм. Затем применялась диффузион-ная обработка при температурах 700, 800, 900, 1000°C.
Цель данной работы – исследовать новый процесс, называемый одностадийным плазменным алитированием фольгой, протекающий при температуре 600°C (ниже температуры плавления алюминия). Для выяснения влияния плазмы проведена еще одна серия экспериментов при 750°C, т.е. с плавлением алюминиевой фольги.
ЭКСПЕРИМЕНТ
Прокатный цилиндр из стали AISI 4340 имеет следующий состав: содержание C – 0.37, Ni – 2.0, Cr – 1.0, Mo – 0.3, Mn – 0.6, Si – 0.3, P – 0.015, S – 0.01 мас. %. Цилиндр из данной стали разрезался на образцы диаметром 12 мм и высотой 2 мм. Перед нанесением покрытия поверхность образцов шлифовывалась до средней шероховатости Ra = 0.3 мкм, обезжиривалась и очищалась этанолом. Затем образцы покрывались алюминиевой фольгой толщиной 50 мкм номинального состава Al–1.6 мас. % Si. Плазменное алитирование фольгой проводилось в плазменном реакторе, схема которого показана на рис. 1.
Рис. 1.
Схематическое изображение плазменного реактора: 1 – камера, 2 – вход для газа, 3 – пластина-анод, 4 – пластина-катод, 5 – образец, 6 – алюминиевая фольга, 7 – тлеющий разряд, 8 – термопара, 9 – выход для газа.
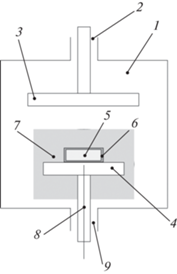
После откачки камеры (объемом 2.7 л) до давления около 0.1 мбар в камеру нагнетался аргон в качестве рабочего газа до давления около 0.5 мбар. Плазма тлеющего разряда инициировалась вокруг катодной пластины путем подачи на цепь напряжения 250 В от источника постоянного тока максимальной мощностью 2 кВт. Для нагрева образцы помещались на катодную пластину, где температура увеличивалась за счет постепенного увеличения давления рабочего газа, а также потенциала между катодом и анодом. Поверхность образца достигала заданной температуры 600 и 750°С примерно через 30 и 45 мин соответственно. По достижении образцом температуры эксперимента давление газа и напряжение выдерживались фиксированными в течение 5 мин. По истечении времени нагрева образец охлаждался отключением потенциала и пропусканием через камеру газообразного аргонa до достижения комнатной температуры.
Поперечные сечения и элементный состав образцов с покрытием исследовались с помощью сканирующей электронной микроскопии с полевой эмиссией (СЭМ-ПЭ) совместно с энергодисперсионной спектроскопией (ЭДС). Фазовая структура поверхностного слоя алитированных образцов анализировалась методом рентгеновской дифракции (РФА) с использованием CuKα-излучения. Микротвердость каждого слоя покрытия измерялась по поперечному сечению образца при нагрузке 100 г в течение 10 с.
РЕЗУЛЬТАТЫ И ОБСУЖДЕНИЕ
Микроструктуры поперечного сечения образцов, алюминированных при 600 и 750°С, представлены на рис. 2. Слой покрытия в образце, алитированном при 600°С, состоял из двойного слоя алюминидов железа и небольшого количества алюминия поверх алюминидов общей толщиной около 90 мкм (рис. 2а). Слой покрытия, полученный на образцe, алитированном при 750°С, состоял из четырех дискретных слоев общей толщиной около 125–150 мкм (рис. 2б). При этом покрытие, полученное при 750°С, более однородно, чем покрытие, сформированное при 600°С.
Поверхность раздела подложка–покрытие относительно плоская у образца, полученного при 750°С, тогда как для образца, обработанного при 600°С, граница раздела неровная (рис. 2).
Химические составы в точкак А–D, отмеченных на рис. 2а, в диффузионном слое образца, алитированного при 600°С, приведены в табл. 1. Химический состав в точке А на верхней части покрытия соответствует алюминиевой фольге, содержащей примерно 1.7 ат. % кремния. В точке В на границе слоев 1 и 2 соотношение концентраций алюминия и железа составляет 70.5/22.5. Наложение этого соотношения без учета содержания кремния на фазовую диаграмму Fe–Al позволило уточнить состав фаз. На рис. 3 показана система Fe–Al и насыщенная Al часть фазовой диаграммы, опубликованная в [8, 9]. В точке B на рис. 2а образец может состоять из богатых алюминием фаз алюминида железа FeAl3 и/или Fe2Al5, тогда как согласно рис. 3б возможно образование Fe4Al13, в котором больше алюминия, чем в FeAl3. Это согласуется с измеренным содержанием алюминия в точке B.
Таблица 1.
Результаты ЭДС в рассматриваемых точках в поперечных сечениях покрытия (ат. %)
Элемент | Обработка при 600°C | Обработка при 750°C | ||||||
---|---|---|---|---|---|---|---|---|
точка A | точка B | точка C | точка D | область A | область B | область C | область D | |
Al | 98 | 70.59 | 73.08 | 71.99 | 68.79 | 65.73 | 48.50 | 50.76 |
Fe | – | 22.5 | 25.26 | 25.71 | 29.23 | 31.98 | 48.83 | 46.08 |
Ni | 0.2 | 0.38 | 0.31 | 0.54 | 0.55 | 0.90 | 1.45 | 1.35 |
Cr | 0.1 | 0.17 | 0.17 | 0.20 | 0.18 | 0.23 | 0.33 | 0.40 |
Si | 1.7 | 6.36 | 1.18 | 1.56 | 1.25 | 1.16 | 0.89 | 1.42 |
В [10] обобщены диапазоны стабильности и плотности фаз в системе железо–алюминий (табл. 2). На основании яркости фаз на изображениях электронной микроскопии обратного рассеяния и с учетом плотностей фаз вместе с ЭДС-анализом можно выделить фазы Al–Fe.
Таблица 2.
Диапазон стабильности Al в различных фазах системы Al–Fe и их плотность [10]
Фаза | Диапазон стабильности, ат. % Al | Плотность, г/см3 |
---|---|---|
Твердый раствор Fe | 0–45 | |
γ-Fe | 0–1.3 | |
FeAl | 23–55 | 5.37 |
Fe3Al | 23–34 | 6.67 |
Fe2Al3 | 58–65 | |
FeAl2 | 66–66.9 | 4.36 |
Fe2Al5 | 70–73 | 4.11 |
FeAl3 | 74.5–76.5 | 3.95 |
Твердый раствор Al | 99.998–100 |
В [11] исследованы интерметаллические соединения, образующиеся в системе Fe–Al–Si, и приведен средний состав различных фаз (табл. 3) и максимальной растворимости кремния в различных фазах Fe–Al (табл. 4). Показано, что при 600°С кремний растворялся в Fe2Al5 примерно до 1.47 ат. %, тогда как при 800°С в закаленных образцах растворимость увеличивается примерно до 2 ат. %. О какой-либо растворимости кремния в FeAl2 и Fe2Al3 не сообщается. В работе [12] низкоуглеродистая сталь погружалась в ванну расплава Al–7Si–2Cu при 690°C на 5, 10, 15, 25 и 40 мин. Большое количество кремния в ванне расплава привело к образованию интерметаллидов, таких как τ1-Al2Fe3Si3, тогда как в текущем исследовании только 1.6 ат. % кремния присутствовало в алюминиевой фольге, поэтому ожидалось отсутствие τ1-Al2Fe3Si3.
Таблица 3.
Средний состав фаз (ат. %) в системе Fe–Al–Si [11]
Фаза | Обработка при 800°C | Обработка при 600°C | ||||
---|---|---|---|---|---|---|
Fe | Al | Si | Fe | Al | Si | |
FeAl3 | 22.62 | 72.19 | 5.19 | |||
Fe2Al5 | 28.0 | 70.0 | 2.0 | 26.87 | 71.65 | 1.47 |
FeAl | 51.2 | 38.41 | 10.38 | |||
Fe3Al | 76.77 | 19.55 | 3.65 |
Таблица 4.
Растворимость Si в фазах Fe–Al (ат. %) при разных температурах после закалки образца [11]
Фаза | 1115°C | 1020°C | 900°C | 800°C | 600°C |
---|---|---|---|---|---|
FeAl3 | 5.42 | 5.64 | 5.86 | 5.19 | |
Fe2Al5 | 7.57 | 4.4 | 4.66 | 2.0 | 1.48 |
FeAl | 11.58 | 16.24 | 16.3 | 10.38 | |
Fe3Al | 2.45 | 5.31 | 7.44 | 5.60 | |
Fe2Al3 | 11.31 |
В слое 2 на рис. 2а концентрация алюминия и железа в покрытии постоянна, и, судя по соотношению концентраций Al к Fe (72 : 25), по-видимому, образовалась фаза алюминида железа Fe2Al5, насыщанная алюминием. Кроме того, отсутствие других фаз в диффузном слое указывает на то, что легирующие элементы основного металла стали, такие как Ni, Cr и Mo, растворены в образовавшейся фазе алюминида железа. Результаты ЭДС-анализа четырех участков диффузионного слоя 1–4 в алитированном образце при 750°С (рис. 2б) также представлены в табл. 2. Фазовый состав не может быть установлен на основе общих концентраций Al и Fe. Но судя по соотношению концентраций Al и Fe в слое 2, можно оценить, что этот слой состоял из богатого алюминием алюминида железа Fe2Al5.
На рис. 4 и 5 показаны слои 1 и 4 (см. рис. 2б) при большем увеличении. Светлые осадки (точка А) распределены в слое 1. Химический состав в точкe А, полученный с помощью ЭДС, следующий (в ат. %): Fe – 28.9, Al – 64.4, Ni – 2.9, Cr – 0.6, Si – 3.3. Oн соответствует фазе FeAl2. Кремний вводился в покрытие из исходной фольги алюминия. Как показано на рис. 6, а также в табл. 3 и 4, растворимость кремния в алюминидах железа достаточно высока и составляет 3.3 ат. % кремния. В слое 3 (рис. 2б, область С) атомарные концентрации алюминия и железа практически одинаковы, что свидетельствует об образовании фазы FeAl. Так как растворимость легирующих элементов стали (Ni, Cr, Mo) в фазе FeAl составляла около 5 ат. % [13], что превышает их концентрации в стали, можно сделать вывод, что легирующие элементы стали растворены в этой фазе. ЭДС-анализ слоя 4 (рис. 2б, область D) показал, что этот слой состоит из Fe (50.7 ат. %), Al (46.0), Ni (1.3), Cr (0.4), Si (1.4), что близко к фазе FeAl. На рис. 5 показан слой 4 при большем увеличении, в котором обнаружены темные осадки, богатые углеродом. ЭДС-анализ показал, что эти осадки содержат Fe (31.1 ат. %), Al (12.2), Ni (0.5), Cr (0.3), Si (1.2), C (54.5), которые, вероятно, представляли собой карбиды некоторых легирующих элементов стали.
Результаты РФА поверхностей образцов, алитированных при 600 и 750°С, представлены на рис. 7. Для покрытия, синтезированного при 600°С, наблюдались картины чистого алюминия, Fe4Al13 (FeAl3) и Fe2Al5, тогда как в покрытии, синтезированном при 750°С, обнаружены пики чистого алюминия, фаз Fe2Al5 и FeAl2. Следует отметить, что в обоих образцах преобладает фаза Fe2Al5.
Результаты измерений микротвердости диффузионных слоев образцов, алитированных при 600 и 750°С, представлены в табл. 5. Поскольку слой 1 покрытия, полученного при 600°С, относительно пористый, точно измерить твердость не удалось. Твердость слоя 2 этого покрытия по толщине почти не изменялась. Твердость покрытия, алитированного при 750°С, постепенно снижается при переходе от поверхностного слоя к междиффузионному. С другой стороны, в [14, 15] сообщается о твердости алюминидов железа для фаз FeAl3, Fe2Al5, FeAl2, FeAl и Fe3Al по Виккерсу, которая составляет 990, 820, 1030, 640 и 350 соответственно. При сравнении измеренной микротвердости с твердостью алюминидов железа подтверждаются результаты ЭДС и РФА покрытий, полученных плазменным алитированием фольги при 600 и 750°С.
Таблица 5.
Микротвердость по Виккерсу различных слоев алитированных покрытий методом плазменного алитирования фольги
Обработка при 600°C | Обработка при 750°C | |||||
---|---|---|---|---|---|---|
Твердость (HV) | Cлой 1 | Cлой 2 | Cлой 1 | Cлой 2 | Cлой 3 | Cлой 4 |
– | 933 | – | 920 | 894 | 536 |
Во время плазменного алитирования фольги бомбардировка высокоэнергетическими ионами аргона и ускоренными атомами поверхности алюминиевой фольги приводит к преобразованию кинетической энергии в тепловую. По достижении поверхностью образцов температуры 600°С, при размягчении фольги и ее прилипании к стали происходила твердотельная диффузия между сталью и наложенной алюминиевой фольгой.
С другой стороны, из-за низкой скорости диффузии при данной температуре образовывались богатые алюминием алюминиды железа FeAl3 и Fe2Al5 с преобладанием фазы Fe2Al5. В [16] экспериментально и теоретически показано, что константа скорости роста фазы Fe2Al5 примерно в 20 раз больше, чем фазы FeAl3. Авторы [17] связали причину такого большого различия с относительно большим количеством вакансий на оси c кристаллической структуры Fe2Al5. Кроме того, в [18] проанализированы работы других исследователей и сделан вывод, что коэффициенты диффузии Fe и Al в Fe3Al, Fe2Al и FeAl в твердом состоянии не сильно различаются.
В процессе плазменного алитирования фольги при 750°С происходит плавление алюминия на поверхности образца. При этом возможны следующие процессы. Во-первых, свободные атомы расплавленного алюминия могут диффундировать в объем стали, во-вторых, железо и легирующие элементы стали могут растворяться в расплавленном алюминии, оставляя Al + Fe2Al5, согласно рис. 3. Коэффициент диффузии жидкого алюминия в твердое железо зарегистрирован со значением 1.8 × 10–4 м2/с (1003–1673 К), а железа в расплавленный алюминий – 53 × 10–4 м2/с (793–922 К) [19]. Согласно уравнению Аррениуса, ожидается, что коэффициент диффузии железа будет выше при температуре 750°С (1023 К). Это означает, что алюминий диффундирует в железо со значительно меньшей скоростью, чем железо в расплавленный алюминий.
Как сообщалось в [19, 20], при увеличении концентрации железа в алюминиевом расплаве на границе твердое тело–жидкость избыточные растворенные вещества образовывают различные фазы алюминида железа, богатые алюминием. Более того, по мере того, как диффузия продолжается, образуются другие железо-алюминидные фазы, самодиффузия железа и/или алюминия в этих фазах вызывала беспокойство. Энергии активации Q и Do Fe и Al в FeAl и FeAl3 в интервале температур 1173–1358 К приведены в [18]. Уравнение Аррениуса для коэффициента диффузии учитывается в виде
где R – газовая постоянная, Дж/К, T – температура, К. Тогда коэффициенты диффузии Al в Fe3Al и FeAl при 1173 К равны 8.2 × 10–15 и 6.3 × 10–16 м2/с соответственно, а для диффузии железа 9.3 × 10–15 и 1.0 × 10–13 м2/с соответственно. Так, видно, что диффузия железа происходит быстрее, чем Al в железо-алюминидах, и, следовательно, преобладает диффузия железа наружу. Это приводит к фазовому переходу на границе раздела покрытие–подложка в соответствии с реакциейДальнейшая диффузия железа в матрицу покрытия вдали от границы раздела покрытие–подложка приводит к гетерогенному зарождению и росту промежуточной фазы FeAl2 в матрице покрытия Fe2Al5 согласно
В [21] исследована система Fe–Al при высоких температурах с использованием метода DCSC и сообщается, что экзотермические реакции идут в следующем порядке: FeAl3–Fe2Al5–FeAl2–FeAl.
Для выяснения влияния плазмы на микроструктуру покрытия выполнeно сравнение между горячим алитированием и плазменным алитированием фольги. В табл. 6 обобщены данные из литературы о толщине и микроструктуре покрытия во время горячего алитирования погружением. Плазменное алитирование фольги при 600°C привело к образованию относительно толстого слоя алюминида FeAl3–Fe2Al5, насыщенного алюминием. Это показало уникальную роль плазмы в создании пары алюминий–сталь и дальнейшей взаимной диффузии железа и алюминия в формировании слоев алюминида с высоким содержанием алюминия. Сформированное за 5 мин покрытие толщиной около 100 мкм показывает роль ионной бомбардировки во время плазменной обработки в процессе плазменного алитирования фольги.
Таблица 6.
Сравнение горячего погружения и алитирования фольгой с плазменным алитированием фольгой
Рабочая пара | Температура погружения, время последующей обработки | Микроструктура (толщина, мкм) | Источник |
---|---|---|---|
Al на конструкционной углеродистой стали | 700°C, 5 мин | Al (82)–Fe2Al5 (27) | [20] |
700°C, 5 мин с последующей диффузионной обработкой при 600°C в течение 20 мин | Al (71)–Fe2Al5 (35) | ||
700°C, 5 мин с последующей диффузионной обработкой при 600°C в течение 60 мин | Al (65)–Fe2Al5 (47) | ||
700°C, 5 мин с последующей диффузионной обработкой при 600°C в течение 60 мин | Fe2Al5 (117) | ||
750°C, 5 мин | Al (90)–Fe2Al5 (70) | ||
750°C, 5 мин с последующей диффузионной обработкой при 600°C в течение 60 мин | Al (105)–Fe2Al5 (58) | ||
750°C, 5 мин с последующей диффузионной обработкой при 800°C в течение 60 мин | Fe2Al5 (125) | ||
800°C, 5 мин | Al (130)–Fe2Al5 (200) | ||
Al на Fe | 700°C, 30 с | Очень тонкий FeAl3–Fe2Al5 (65) | [16] |
700°C, 15 мин | Очень тонкий FeAl3–Fe2Al5 (170) | ||
800°C, 30 с | FeAl3 (6)–Fe2Al5 (120) | ||
800°C, 15 мин | FeAl3 (10)–Fe2Al5 (205) | ||
900°C, 30 с | Очень тонкий FeAl3–Fe2Al5 (220) | ||
900°C, 15 мин | Очень тонкий FeAl3–Fe2Al5 (230) | ||
Al–10% Si на низкоуглеродистой стали | 700°C, 16 с | Al–FeAl3–Fe2Al5 (25) с частицами эвтектического Si на поверхности | [22] |
Фольга из Al, напрессованная на простую углеродистую сталь | Преддиффузионная обработка при 650°C в течение 1 ч | Al (100) | [7] |
Диффузионная обработка при 700°C в течение 60 мин | Fe2Al5 (120) | ||
Диффузионная обработка при 800°C в течение 60 мин | Fe2Al5 (130) | ||
Диффузионная обработка при 1000°C в течение 60 мин | Fe2Al5 (50)–FeAl (75)–диффузионный слой Al (110) | ||
Al–1.6 мас. % Si на стали 4340 | Плазменное алитирование фольгой при 600°C в течение 5 мин | Al–FeAl3 (20–40)–Fe2Al5 (50–70) | Данная работа |
Плазменное алитирование фольгой при 750°C в течение 5 мин | Fe2Al5 + FeAl2 (33–53)–Fe2Al5 (30)–FeAl (60) |
Слой покрытия, сформированный при 750°C, также отличался от слоев, полученных при горячем алитировании погружением, по толщине и фазам. При данной температуре и всего за 5 мин обработки образовался относительно толстый слой алюминида Fe2Al5. Поскольку процесс алитирования является контролируемым диффузией, влияние плазмы на толщину и микроструктуру покрытия должно быть связано с усилением дефектов кристалла. Считается, что, когда энергичные тяжелые ионы бомбардируют кристалл, они создают узлы с беспорядком решетки [23]. Даже когда ионы замедляются в кристаллической решетке, они сталкиваются с атомами решетки, что в свою очередь дает энергию для смещения атомов из их узлов решетки. Эти первичные выбивные атомы могут вытеснять другие атомы и создавать вторичные, тройные и выбивные атомы (рис. 8) и, как результат, могут создавать кристаллические дефекты, такие как вакансии и междоузельные атомы. Увеличение количества дефектов в решеткe облегчает диффузию частиц и, следовательно, увеличивает толщину покрытия, как и происходит при плазменном алитировании стали фольгой.
Рис. 8.
Схема формирования дефектов решетки столкновительными каскадами [23]: 1 – смещенный атом, 2 – вакансия.
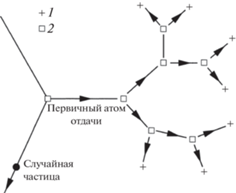
ЗАКЛЮЧЕНИЕ
• Для обогащения алюминием поверхности стали AISI 4340 использовался одностадийный процесс плазменного алитирования фольгой при температуре 600°C, т.е. ниже точки плавления алюминия.
• Хотя при 600°С алюминий находится в твердом состоянии, уже через 5 мин выдержки на поверхности образца вместе со слоями Al и FeAl3 образуется относительно толстый слой интерметаллида Fe2Al5.
• Плазма не только обеспечивает источник нагрева, но также активирует поверхность для твердотельной диффузии.
• Для сравнения также проведено плазменное алитирование фольгой при 750°С в течение ~5 мин, в результате чего образовалось многослойное покрытие, состоящее из Fe2Al5, FeAl2 и FeAl.
• Независимо от температуры процесса Fe2Al5 является преобладающей фазой в микроструктуре покрытия.
Список литературы
Bates B.L., Wang Y.Q., Zhang Y., Pint B.A. Formation and Oxidation Performance of Low-temperature Pack Aluminide Coatings on Ferritic–Martensitic Steels // Surf. Coating Tech. 2009. V. 204. P. 766.
Muralidharan G., Blue C.A., Sikka V.K., Dahotre N.B. Surface Modification of 4340 Steel with Iron Aluminides using High-energy-density Processes // Engineered Steel Surfaces, Proc. MS&T-04, New Orleans, September 2004. Materials Science and Technol. Conf. Proc., 2004. V. 2. P. 357.
Badaruddin M., Wang C.J., Wardono H., Tarkono T., Asmi D. High-temperature Oxidation Behavior of Aluminized AISI 4130 Steel // AIP Conf. Proc. 2016. V. 1711. № 1. 04002.
Rastkar A.R., Paresh P., Darvishnia N., Hadavi S.M.M. Microstructural Evolution and Hardness of TiAl3 and TiAl2 Phases on Ti–45Al–2Nb–2Mn–1B by Plasma Pack Aluminizing // Appl. Surf. Sci. 2013. V. 276. P. 112.
Yuan G., Zhiyong H., Chong X. Paste Plasma Aluminizing by Hollow Cathode Discharge // J. Chinese Soc. Corr. Protect. 1997. V. 17. P. 286.
Rastkar A.R., Rezvani N. The Effects of Processing Time on the Microstructure and Composition of Plasma Pack-aluminized and Oxidized Surface Layers on Low Carbon Steel // Metall. Mater. Trans. A. 2015. V. 46(9). P. 4132.
Sasaki T., Yakou T. Features of Intermetallic Compounds in Aluminized Steels Formed Using Aluminum Foil // Surf. Coatings Tech. 2006. V. 201. P. 2131.
Henager C.H. Hydrogen Permeation Barrier Coatings. N.Y., 2008.
Li X., Scherf A., Heilmaier M., Stein F. The Al-rich Part of the Fe–Al Phase Diagram // J. Phase Equilib. Diff. 2016. V. 37. № 2. P. 162.
Atabaki M.M., Nikodinovski M., Chenier P., Ma J., Harooni M., Kovacevic R. Welding of Aluminum Alloys to Steels: An Overview // J. Manuf. Sci. Prod. 2014. V. 14. № 2. P. 59.
Maitra T., Gupta S.P. Intermetallic Compound Formation in Fe–Al–Si Ternary System: Part II // Mater. Charact. 2002. V. 49. № 4. P. 293.
Huilgol P., Bhat S., Bhat K.U. Hot-dip Aluminizing of Low Carbon Steel Using Al-7Si-2Cu Alloy Baths // J. Coatings. 2013. V. 2013. https://doi.org/10.1155/2013/180740
Titran R.H., Vedula K.M., Anderson G.G. High Temperature Properties of Equiatomic FeAl with Ternary Additions. In: High-temperature Ordered Intermetallic Alloys: Symposium, November 26–28 1984. Boston, Massachusetts: Materials Research Society Proc., 1984. P. 309.
Bahadur A., Mohanty O.N. Structural Studies of Hot Dip Aluminized Coatings on Mild Steel // Mater. Trans., JIM. 1991. V. 32. № 11. P. 1053.
Yajiang L., Juan W., Yonglan Z., Holly X. Fine Structures in Fe3Al Alloy Layer of a New Hot Dip Aluminized Steel // Bull. Mater. Sci. 2002. V. 25. P. 635.
Bouché K., Barbier F., Coulet A. Intermetallic Compound Layer Growth Between Solid Iron and Molten Aluminium // Mater. Sci. Eng. A. 1998. V. 249. P. 167.
Cheng W.J., Wang C.J. Growth of Intermetallic Layer in the Aluminide Mild Steel During Hot-dipping // Surf. Coat. Tech. 2009. V. 204. P.824.
Landolt−Börnstein: Numerical Data and Functional Relationships in Science and Technology, New Series, Group III: Crystal and Solid State Physics. V. 26. Diffusion in Metals and Alloys / Ed. Mehrer H. Berlin: Springer, 1990.
Deqing W., Ziyuan S., Longjiang Z. A Liquid Aluminum Corrosion Resistance Surface on Steel Substrate // A-ppl. Surf. Sci. 2003. V. 214. P. 304.
Kobayashi S., Yakou T. Control of Intermetallic Compound Layers at Interface Between Steel and Aluminum by Diffusion-treatment // Mater. Sci. Eng. A. 2002. V. 338. P. 44.
Chojnacki M., Józwiak S., Karczewski K., Bojar Z. Modification of Fe and Al Elemental Powders’ Sintering with Addition of Magnesium and Magnesium Hydride // Intermetallics. 2011. V. 19. P. 1555.
Wang C.J., Chen S.M. The High-temperature Oxidation Behavior of Hot-dipping Al–Si Coating on Low Carbon Steel // Surf. Coat. Tech. 2006. V. 200. P. 6601.
Nastasi M., Mayer J.W., Hirvonen J.K. Ion-Solid Interactions: Fundamentals and Applications. N.Y.: Cambridge University Press, 1996.
Дополнительные материалы отсутствуют.
Инструменты
Теплофизика высоких температур