Теплофизика высоких температур, 2021, T. 59, № 5, стр. 755-761
Закалка жидкого углерода на поверхности алмазной подложки
В. С. Дождиков 1, *, А. Ю. Башарин 1, **, П. Р. Левашов 1
1 Объединенный институт высоких температур РАН
Москва, Россия
* E-mail: vdozh@mail.ru
** E-mail: abasharin@bk.ru
Поступила в редакцию 22.03.2021
После доработки 28.05.2021
Принята к публикации 29.05.2021
Аннотация
Впервые получен аморфный углерод при закалке жидкого углерода. Реализация лазерного плавления чешуек графита, напрессованных на алмазную подложку, позволила осуществить схему падения капли жидкого углерода на холодный алмаз. Алмаз обеспечивал быстрое охлаждение полученного расплава за счет своей уникально высокой теплопроводности. Скорость закалки является одним из важнейших параметров, влияющих на образование и свойства аморфных материалов. Для расчета реальных значений скорости закалки, полученных в эксперименте, решено нестационарное одномерное уравнение теплопроводности с учетом геометрических размеров экспериментальных образцов. Получено распределение скоростей закалки жидкого углерода в диапазоне 1014–1012 К/с в зависимости от расстояния до подложки. Результаты исследований показали, что алмаз может служить уникальной закалочной средой для жидкого углерода с экстремально высокой температурой 5000–6000 К.
ВВЕДЕНИЕ
Аморфный углерод (a-C) вызывает огромный интерес у исследователей во всем мире благодаря его уникальным физическим свойствам [1]. Он обладает широким спектром применений, начиная от низкотеплопроводных теплозащитных экранов [2, 3] на основе a-C с малой плотностью и заканчивая высокотвердыми химически инертными и оптически прозрачными покрытиями [4, 5] и магнитными системами хранения информации [6]. Исследования а-С осложняются трудностями, возникающими при описании и анализе его структуры [7], поскольку у него, как и у любого аморфного материала, нет определенной кристаллической решетки, и по своей природе он является метастабильным материалом. Известные экспериментальные методы получения а-С-пленок основаны на осаждении высокоэнергетических ионных или атомных пучков [1] и лазерном нагреве графита.
В настоящих экспериментах исследовано поведение расплава графита на поверхности холодной алмазной подложки при его охлаждении и затвердевании вблизи тройной точки углерода графит–жидкость–пар. Для этого дисперсный графит был нанесен на алмазную подложку и расплавлен лазерным импульсом. После эксперимента было обнаружено, что поверхность алмазной подложки на некоторых участках покрыта a-C. Причем сама алмазная подложка в этих местах осталась практически неповрежденной. Предполагается, что a-C мог образоваться в результате закалки жидкого углерода на поверхности холодной алмазной подложки.
Известно, что в основе многих методов получения новых материалов с уникальными свойствами лежит как раз закалка из жидкого состояния [1, 8, 9]. Несмотря на то, что жидкий углерод детально исследовался в литературе, например в [10–13], постановка эксперимента с закалкой жидкого углерода была осуществлена впервые.
Незначительное количество а-С, образовавшегося при закалке жидкого углерода в эксперименте, не позволило применить имеющиеся в распоряжении инструментальные средства для детального изучения его структуры, поэтому для этого использовалось компьютерное моделирование. Существуют разные методы для моделирования аморфных систем, но одним из самых популярных методов компьютерного моделирования а-С является молекулярно-динамическая закалка жидкого углерода [1]. Как известно [1], скорость закалки – это один из определяющих параметров для получения модельного а-С в методе молекулярной динамики (МД), существенно влияющий на его свойства. Оценка скорости закалки позволяет не только лучше понять механизмы возникновения той или иной структуры а-С, но, возможно, поможет спланировать дальнейшие эксперименты по созданию а-С.
В данной работе выполнена оценка скорости закалки путем решения одномерного нестационарного уравнения теплопроводности для двухслойной модели алмаз–жидкий углерод с учетом реальных размеров объектов, участвующих в экспериментах. Используя методы МД и полученные таким образом скорости закалки, можно численно воспроизвести модельные образцы a-C. Предполагается, что свойства модельных образцов a-C достаточно близки к свойствам реального a-C, полученного в экспериментах.
ЭКСПЕРИМЕНТЫ ПО ЗАКАЛКЕ ЖИДКОГО УГЛЕРОДА
Эксперименты проводились на базе экспериментальной установки [10]. Исследовался специально изготовленный двухслойный образец, состоящий из алмазной подложки с напрессованными на нее чешуйками дисперсного графита. Такие чешуйки формировались путем измельчения в вибрационной мельнице высоко ориентированного пиролитического графита (ВОПГ). Двухслойный образец помещался в газостат, наполненный гелием с давлением 25 МПа. Со стороны графита в пятне диаметром около 1 мм образец облучался импульсом Nd твердотельного лазера с длиной волны 1.06 мкм, длительностью 0.4 мс и энергией ~3 Дж. Под воздействием импульса лазера происходило плавление дисперсного графита. Затем из-за контакта жидкого углерода с холодной алмазной подложкой при комнатной температуре происходила его закалка. Рекордно высокая теплопроводность алмаза, превышающая для природного алмаза при комнатной температуре 2000 Вт/(м К) [14], и существенно больший объем холодного алмаза по сравнению с объемом капли жидкого углерода обеспечили реальную закалку жидкой капли углерода вблизи границы алмаз–жидкий углерод. Методом микроспектроскопии комбинационного рассеяния было обнаружено [15], что переплав графита, затвердевшего на поверхности изначально холодной алмазной подложки, представляет собой а-С.
Кроме микроспектроскопии комбинационного рассеяния, были проведены дополнительные исследования структуры застывшего жидкого углерода методом просвечивающей микроскопии. В просвечивающем электронном микроскопе высокого разрешения TITAN 200/300 проводились исследования тонких слоев, вырезанных из экспериментального образца в направлении, перпендикулярном алмазной подложке, с использованием техники “фрезерования” сфокусированным ионным пучком [16]. Данные исследования также подтвердили наличие областей с аморфной структурой. Галло на фурье-образе, показанное на рис. 1а, подтверждает спектроскопические данные об аморфизации переплавленного углерода вблизи поверхности алмаза. От подложки, контактировавшей с переплавом, получены только точечные рефлексы алмаза (фурье-образ на рис. 1б). Это свидетельствует о том, что алмаз не был графитизирован. Энергия активации спонтанной графитизации алмаза при T > 2000 К скачкообразно уменьшается, что приводит к взрывоподобной деструкции алмаза [17]. Очевидно, что температура алмаза в эксперименте была ниже данного значения.
МД-МОДЕЛИРОВАНИЕ ЗАКАЛКИ ЖИДКОГО УГЛЕРОДА
Для изучения процесса закалки и образования а-С авторами были проведены многочисленные расчеты с помощью МД-моделирования экспериментов [15, 18, 19], но эти расчеты не позволили воссоздать структуры a-C, полученные экспериментально.
Были предприняты попытки воспроизвести в рамках МД-расчетов закалку тонкого слоя жидкого углерода на холодной алмазной подложке [18, 19] в двухслойной ячейке моделирования: алмаз–жидкий углерод. В работе [18] в ячейке моделирования было всего 20 328 атомов углерода, в [19] ячейка моделирования была существенно больше и состояла из 90 852 атомов, что позволило уточнить скорость закалки, рассчитанную в [18]. Скорость закалки, полученная в [19], уменьшалась с 1.0 × 1015 до 5.4 × 1013 К/с по мере удаления от поверхности контакта слоя жидкого углерода с алмазом. Толщина слоя жидкого углерода в [19] составила 0.01 мкм, тогда как в реальном эксперименте она была примерно 0.1 мкм, т.е. в 10 раз больше. Поэтому полученные в [19] значения скорости закалки должны быть дополнены расчетами для реальной толщины слоя жидкого углерода, образованного в эксперименте при расплаве графита лазерным импульсом. Использовать при МД-моделировании реальные размеры объектов, как в эксперименте, где был получен а-С, ‒ на сегодняшний день достаточно сложная задача, требующая очень большого времени моделирования и огромных вычислительных ресурсов.
РЕШЕНИЕ ЗАДАЧИ ТЕПЛОПРОВОДНОСТИ
Оценка скорости закалки получена на макроскопическом уровне путем численного решения нестационарного уравнения теплопроводности в одномерной постановке для двух соприкасающихся плоских слоев: алмазной подложки и жидкого углерода (рис. 2).
Алмаз – оптически прозрачный материал в широкой области спектра излучения. Поэтому в начальный момент закалки граница жидкого углерода на алмазной подложке остывает из-за радиационного и кондуктивного теплообмена (КТ). Это приводит к очень быстрому снижению температуры поверхности жидкого углерода, примыкающей к подложке, и превращению жидкого углерода в тонком поверхностном слое в а-С. Как показал анализ моделирования [18], температура приграничного слоя жидкого углерода снижается за 1 пс до 1500 К благодаря очень высокому коэффициенту теплопроводности алмаза (даже без учета радиационной составляющей теплового потока). В реальных условиях радиационно-кондуктивного теплообмена приграничный слой жидкого углерода остывает за время менее 1 пс до температуры не более 1500 К и дальнейшее остывание приграничного слоя происходит, в основном, путем КТ. Поскольку сам жидкий углерод – оптически непрозрачный материал [20], то температурные поля внутри слоя жидкого углерода во время его закалки определяются только кондуктивной теплопроводностью. Таким образом, радиационная составляющая влияет только на температуру приграничного слоя жидкого углерода и только в самый начальный момент закалки. Это позволяет упростить задачу и сосредоточиться только на решении задачи КТ.
Форма лазерного импульса, облучающего образец, в относительных единицах приведена в [10]. Длительность лазерного импульса была примерно 400 мкс. В работе [10] импульсом энергии лазера плавился образец ВОПГ. В экспериментах, описанных в настоящей статье, происходило плавление “островка”, образованного из напрессованных на алмазную подложку чешуек из ВОПГ. Полагается, что поскольку излучательная и отражательная способности в обоих случаях примерно одинаковы, то термограммы, подробно описанные в [10], можно в начальном приближении использовать и для анализа процесса плавления при лазерном нагреве, описанном в данной статье.
Динамика нагрева была следующей. Примерно через 100 мкс после начала облучения мощность лазерного импульса достигала максимума и затем плавно снижалась. Плавление на поверхности напрессованных чешуек дисперсного графита происходило примерно через 120–150 мкс после начала воздействия лазерным импульсом. Плато плавления на поверхности составило примерно 50–80 мкс. После начала плавления на поверхности волна плавления распространялась вглубь островка из чешуек. Из-за низкой теплопроводности дисперсного графита тепловая волна хоть и опережала немного волну плавления, но не успевала прогревать алмаз до прихода волны плавления. В некоторый момент времени плавление достигало поверхности алмазной подложки, и сразу начиналась “лавинная” закалка жидкого углерода. По сути, такой ход эксперимента можно представить как падение капельки жидкого углерода на поверхность холодной алмазной подложки. В процессе закалки мощность лазерного импульса была ниже своего максимального значения [10] и компенсировала в какой-то степени отток тепла с поверхности. Поэтому в первом приближении считалось, что свободная поверхность слоя жидкого углерода во время закалки была адиабатной – граничные условия второго рода: ∂T/∂x = 0 (см. рис. 2).
Нестационарное одномерное уравнение теплопроводности без внутренних источников тепла и при условии постоянства коэффициента теплопроводности имеет хорошо известный вид [21]
(1)
$\frac{{\partial T}}{{\partial \tau }} = \frac{{{\lambda }}}{{{{\rho }}c}}\frac{{{{\partial }^{2}}T}}{{\partial {{x}^{2}}}},$Геометрические размеры в постановке задачи соответствовали реальным размерам объектов в эксперименте. Толщина алмазной подложки – 1 мм, слоя жидкого углерода – 0.1 мкм (см. рис. 2). На свободной поверхности алмазной подложки – граничные условия первого рода, т.е. T1 = 300 К, а на свободной поверхности слоя жидкого углерода ‒ граничные условия второго рода: ∂T/∂x = 0. Полагалось, что жидкий углерод имеет хороший контакт с подложкой, а контактное сопротивление между слоями принималось равным rc = 10–10 м2 К/Вт. В начальный момент времени слои изотермичны, причем жидкий углерод имеет температуру 6000 К, а алмазная подложка – 300 К. Выбор начальной температуры жидкого слоя углерода можно объяснить двумя причинами. Во-первых, чтобы иметь возможность сравнить результаты расчетов со скоростями закалки, полученными в [19], где начальная температура была 6500 К. А во-вторых, по последним данным верхний диапазон температуры плавления графита, определенный экспериментально, составляет 6300–6500 К [22].
На сегодняшний день в литературе почти нет данных о физических свойствах жидкого углерода. Это объясняется, с одной стороны, сложностью проведения эксперимента при очень высоких температурах (5000–6000 К), а с другой – отсутствием математической модели, адекватно описывающей жидкий углерод. Последнее, скорее всего, обусловлено очень сложной и плохо изученной структурой жидкого углерода и отсутствием надежных экспериментальных данных для построения модели. В работе [23] предполагалось, что жидкий углерод имеет металлическую природу. На основе теории жидких металлов были получены следующие свойства жидкого углерода: λ = 290 Вт/(м К), c = 2167 Дж/(кг К), ρ = = 1600 кг/м3. В экспериментальной работе [24] приведены данные для удельной теплоемкости жидкого углерода c = 4000 Дж/(кг К). Авторы [25] на основании экспериментальных данных и математической модели сделали оценку коэффициента теплопроводности для жидкого углерода примерно λ = 5 Вт/(м К), что почти в 60 раз меньше значения теплопроводности, приведенного в [23]. Оценки в [19] дают значение около 90 Вт/(м К). По-видимому, значение коэффициента теплопроводности λ = 290 Вт/(м К), полученное в [23], завышено. Как показано в обзоре [26], коэффициент теплопроводности углеродных материалов сильно зависит от структуры и минимальные значения λ характерны для неупорядоченных структур, например для а-С λ = 2 Вт/(м К) при температуре 500 К.
Входящие в уравнение теплопроводности физические свойства (λ, ρ, c) алмаза взяты из литературных данных при температуре 300 К. Для алмаза: λ = 2000 Вт/(м К) [27], c = 518.75 Дж/(кг К) [28], ρ = 3515 кг/м3. На первом этапе для решения задачи КТ использовались следующие физические свойства жидкого углерода: λ = 5 Вт/(м К) [25], c = 2300 Дж/(кг К) [23, 24], ρ = 1200 кг/м3 [29]. Предполагалось, что при переходе жидкого углерода в аморфное состояние физические свойства не изменяются, и считалось, что они не зависят от температуры. Строго говоря, в реальной системе такие предположения неверны, но здесь считается, что для оценки скорости закалки на макроуровне такой подход вполне допустим.
Задача, описываемая нестационарным дифференциальным уравнением теплопроводности (1), решалась численным методом. По сути, исходное дифференциальное уравнение, граничные и начальные условия задачи были заменены системой алгебраических уравнений (дискретными аналогами). Двухслойная система (алмазная подложка–жидкий углерод) была разделена на элементы (контрольные объемы), в каждом элементе выбрана основная узловая точка. Считалось, что температура контрольного объема равна температуре основной узловой точки. Алмазная подложка была разбита на два контрольных объема одинаковой толщины, причем две основные узловые точки 1 и 2 размещались на границах подложки (см. рис. 2). Точка 1 находилась на свободной поверхности подложки, а точка 2 на поверхности, граничащей с жидким углеродом. На границе жидкого углерода, примыкающей к подложке, введена дополнительная узловая точка 3. Эта точка позволяла контролировать температуру на границе жидкого углерода с алмазной подложкой со стороны жидкого углерода. Граница между точками 2 и 3 характеризовалась контактным сопротивлением rc. Слой жидкого углерода был разбит на 11 контрольных объемов равной толщины. Основные узловые точки с 4 по 14 располагались в геометрических центрах контрольных объемов слоя жидкого углерода. Такое разбиение сделано, прежде всего, для исследования температурных полей именно в слое жидкого углерода.
Для численного решения уравнения (1) выбрана неявная конечно-разностная схема [30]. Несмотря на некоторое усложнение решения системы алгебраических уравнений, неявная конечно-разностная схема абсолютно устойчива и позволяет использовать любой шаг по времени. Это очень важно, поскольку процесс закалки, когда весь объем жидкого углерода переходит в а-С, происходит всего за 2 нс. Поэтому в данной задаче использовался шаг по времени 0.050 нс (5 × 10–11 с). Для всех узловых точек на основании уравнений теплового баланса были рассчитаны коэффициенты, входящие в систему дискретных уравнений, которая может быть представлена в виде трехдиагональной матрицы. Для решения такой матрицы использовался метод прогонки. Трехдиагональная матрица преобразуется в двухдиагональную, состоящую из прогоночных коэффициентов. Расчет прогоночных коэффициентов проводился в процессе прямой прогонки, при этом определялась температура в последней узловой точке. Температуры в остальных узловых точках определялись в процессе обратной прогонки. На каждом шаге по времени рассчитывался дискретный профиль температур. Процесс расчета останавливался, когда разность температур для двух соседних шагов по времени в четвертой узловой точке не превышала 0.01 К.
ОБСУЖДЕНИЕ РЕЗУЛЬТАТОВ
Результаты расчетов представлены в виде графиков на рис. 3–5. На рис. 3 показан начальный этап закалки в период от 0 до 0.4 нс с момента начала закалки. На рис. 4 показан этап закалки от 0 до 1.8 нс с начала закалки, когда практически весь слой жидкого углерода превращается в a-C. Поскольку толщина слоя жидкого углерода в 10000 раз меньше толщины алмазной подложки, то для удобства представления профилей температуры в жидком углероде по оси абсцисс выбран диапазон от 999.94 до 1000.1 мкм. В момент времени τ = 0.00 нс на рис. 3 и 4 виден исходный профиль температуры в двухслойной системе. Хорошо видно, что из-за большого объема холодной алмазной подложки и высокого значения коэффициента теплопроводности алмаза температура на границе алмаза во время закалки практически не повышается. Температура жидкого углерода на границе с подложкой мгновенно опускается до достаточно низких значений. Происходит как бы скачок температуры, после которого запускается процесс закалки жидкого углерода. Примерно через 0.35 нс (рис. 3) с начала закалки фронт охлаждения доходит до свободной поверхности жидкого углерода, и закалка начинает идти во всем его объеме. Если считать, что при температуре 3000 К жидкий углерод превращается в a-C [31], то, как видно из рис. 4, практически весь объем жидкого углерода переходит в аморфное состояние за время примерно 1.80–2.00 нс, считая с начала закалки. На рис. 5 показан график изменения скорости закалки для середины слоя жидкого углерода. Хорошо виден короткий начальный участок, когда скорость возрастает до 3 × 1012 К/с.
Рис. 3.
Изменение профиля температуры в слое жидкого углерода в течение 0.40 нс с начала закалки: 1 – τ = 0 нс, 2 – 0.05, 3 – 0.10, 4 – 0.15, 5 – 0.20, 6 – 0.25, 7 – 0.30, 8 – 0.35, 9 – 0.40.
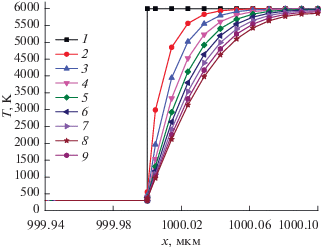
Рис. 4.
Изменение профиля температуры в слое жидкого углерода в течение 1.80 нс после начала закалки: 1 – τ = 0 нс, 2 – 0.20, 3 – 0.40, 4 – 0.60, 5 – 0.80, 6 – 1.00, 7 – 1.20, 8 – 1.40, 9 – 1.60, 10 – 1.80.
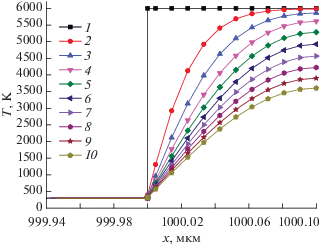
Далее скорость закалки начинает экспоненциально уменьшаться и снижается до нуля через 16.5 нс. Поскольку через 1.80–2.00 нс весь слой жидкого углерода превращается в a-C, из рис. 5 можно сделать вывод, что во время закалки жидкого углерода скорость закалки в середине слоя на расстоянии 0.05 мкм от алмазной подложки не опускается ниже 1012 К/с. Если проанализировать изменение скорости закалки вдоль слоя жидкого углерода при расстояниях от подложки менее 0.05 мкм, то оказывается, что примерно на расстоянии 0.02 мкм скорость закалки увеличивается до 1013 К/с. На расстоянии 0.005 мкм скорость увеличивается примерно до 1014 К/с. При расстояниях более 0.05 мкм скорость закалки сохраняется примерно на уровне 1012 К/с, немного снижаясь по мере приближения к свободной границе жидкого углерода, максимально удаленной от границы с алмазом (см. рис. 2).
В настоящей работе температура поверхности алмаза практически не изменялась, хотя в [18] показано, что она достигает 1500 К. Это противоречие объясняется следующими причинами. Поскольку целью исследования были температурные поля именно в слое жидкого углерода, то этот слой был разбит на 11 контрольных объемов равной толщины, а алмазная подложка всего на два контрольных объема одинаковой толщины по 0.5 мм. Поэтому температура Т2 в контрольной точке 2 на границе алмазной подложки (см. рис. 2) является не температурой граничной поверхности, а некоторой средней температурой слоя алмаза толщиной 0.5 мм. Причем этот слой контактирует с соседним слоем толщиной 0.5 мм с постоянной температурой T1 = 300 К – граничные условия первого рода на свободной поверхности алмазной подложки. Из-за очень высокого значения коэффициента теплопроводности алмаза – 2000 Вт/(м К) ‒ разница между средней температурой Т2 и средней температурой T1 очень мала. По сути, Т2 → T1 = 300 К. Можно считать, что это допущение не привело к искажению результатов расчетов, поскольку скорости закалки, полученные в данной работе, хорошо согласуются с расчетами [19].
Таким образом, как показали расчеты на макроуровне, скорость закалки увеличивается с 1012 до 1014 К/с по мере приближения к границе жидкий углерод–алмаз. С учетом полученной зависимости скорости закалки внутри слоя жидкого углерода результаты континуального моделирования хорошо согласуются с результатами атомистического МД-моделирования двухслойной ячейки [19]. Как показано в [19], скорость закалки жидкого углерода на расстоянии 0.01 мкм от границы с алмазной подложкой составляла 5.4 × 1013 К/с, а при приближении к границе, примерно на расстояниях не более 0.005 мкм, скорость закалки увеличивалась до 1014–1015 К/с.
СРАВНЕНИЕ РЕЗУЛЬТАТОВ С ЛИТЕРАТУРНЫМИ ДАННЫМИ
На сегодняшний день в литературе есть, пожалуй, только одна работа [31], где для оценки скорости закалки жидкого углерода используются методы теории теплопроводности. В этой работе фактически изложены физические основы закалки жидкого углерода в экспериментах по получению а-С при осаждении ионов углерода с достаточно большой энергией на холодную подложку из a-C. Автор [31] рассмотрел образование локальных “всплесков” температуры при соударении ионов с энергией от 40 до 400 эВ с поверхностью подложки. При проникновении ионов вглубь подложки происходит практически мгновенное плавление углерода (за время, существенно меньшее 1 пс) и последующее быстрое охлаждение с превращением в a-C. Такой процесс может происходить, например, при применении технологии нанесения алмазоподобных аморфных покрытий на изделия во время плазменного импульсного распыления графита в вакуумной камере. На основе использования комбинации МД и аналитических методов теории теплопроводности в [31] была получена достаточно высокая скорость закалки жидкого углерода, примерно равная 2 × 1016 К/с. Для сравнения при получении аморфных металлов и сплавов типичные скорости закалки – 106–1010 К/с. Характерные геометрические размеры объектов в [31] составляют 0.6–1.2 нм, что существенно меньше характерных размеров в данных экспериментах. Для сравнения в [18] толщина жидкого слоя углерода составляла примерно 4 нм, а скорость закалки была около 1015 К/с, что неплохо согласуется с работой [31].
ЗАКЛЮЧЕНИЕ
Оригинальная постановка эксперимента позволила получить а-С методом закалки жидкого углерода на холодной алмазной подложке. Благодаря использованию дисперсного, а не сплошного образца графита, удалось реализовать схему падения капли жидкого углерода на холодную подложку. Несмотря на экстремально высокую температуру жидкого углерода (примерно 5000 К), удивительным фактом явилось то, что алмаз играет роль закалочной среды и, благодаря своим уникальным физическим свойствам, не разрушается при взаимодействии с жидким углеродом.
Использование при постановке задачи нестационарного КТ расчетной схемы с размерами, соответствующими реальным размерам образцов, исследованных в эксперименте, позволило получить оценку скоростей закалки жидкого углерода на холодной алмазной подложке.
Рассчитанные профили температуры в слое жидкого углерода толщиной 0.1 мкм, приведенного в соприкосновение с алмазной подложкой комнатной температуры толщиной 1 мм, позволили установить, что скорость закалки жидкого углерода изменялась в зависимости от удаления от границы алмаз–жидкий углерод. На расстоянии 0.005 мкм скорость закалки была максимальной – 1014 К/с, затем на расстоянии 0.02 мкм она снижалась до 1013 К/с, и далее, по мере удаления от границы – на расстояниях более 0.05 мкм – скорость закалки достигала наименьшего значения 1012 К/с. Уменьшение скорости закалки в жидком углероде по мере удаления от границы с алмазом может привести к неоднородности структуры полученного в эксперименте а-С.
Работа выполнена при финансовой поддержке Министерства науки и высшего образования РФ (госзадание № 075-00460-21-00) и связана с разработкой базовых принципов получения новых материалов и исследованием проблемы поведения метастабильного алмаза под воздействием сверхвысоких температур. Благодарим М.Ю. Преснякова и А.Л. Васильева (НИЦ “Курчатовский институт”, Москва) за исследование образцов с помощью просвечивающей электронной микроскопии высокого разрешения.
Список литературы
Marks N.A. Amorphous Carbon and Related Materials // Computer-based Modeling of Novel Carbon Systems and Their Properties: Beyond Nanotubes. Carbon Materials: Chemistry and Physics / Eds. Colombo L., Fasolino A. V. 3. Ch. 5. Berlin: Springer, 2010. P. 129.
Tran H.K., Johnson C.E., Rasky D.J., Hui F.C.L., Hsu M.-T., Chen Y.K. Phenolic Impregnated Carbon Ablators (PICA) for Discovery Class Missions // AIAA Paper 96-1911. 1996.
Pulickel S.V.A, Chaudhari M.B. Pyrolysis Modelling and Experimentation for Thermophysical Properties of Char Formed from Ablative Material // Int. J. Appl. Res. Mech. Eng. 2011. V. 1. № 2. P. 97.
Liu Y., Erdemir A., Meletis E.I. A Study of the Wear Mechanism of Diamond-like Carbon Films // Surf. Coatings Technol. 1996. V. 82. P. 48.
Robertson J. Diamond-like Amorphous Carbon // Mater. Sci. Eng. R: Rep. 2002. V. 37. P. 129.
Tsai H., Bogy D.B. Characterization of Diamondlike Carbon Films and Their Application as Overcoats on Thin-film Media for Magnetic Recording // J. Vac. Sci. Technol. A. 1987. V. 5. № 6. P. 3287.
Computer-Based Modeling of Novel Carbon Systems and Their Properties: Beyond Nanotubes, Carbon Materaials Chem. Phys. / Eds. Colombo L., Fasolino A. Berlin: Springer, 2010. 250 p.
Sung J.C., Lin J. Diamond Nanotechnology: Synthesis and Applications. CRC Press. Taylor & Francis Group, 2010. 249 p.
Башарин А.Ю., Дождиков В.С., Дубинчук В.Т., Кириллин А.В., Лысенко И.Ю. Турчанинов М.А. Фазы быстрой закалки жидкого углерода // Письма в ЖТФ. 2009. Т. 35. Вып. 9. P. 84.
Башарин А.Ю., Брыкин М.В., Марин М.Ю., Пахомов И.С., Ситников С.Ф. Пути повышения точности измерений при экспериментальном определении температуры плавления графита // ТВТ. 2004. Т. 42. № 1. С. 64.
Орехов Н.Д., Стегайлов В.В. Молекулярно-динамическое моделирование плавления графита // ТВТ. 2014. Т. 52. № 2. С. 220.
Онуфриев С.В., Савватимский А.И. Особенности высокотемпературных свойств графита HAPG в области плавления // ТВТ. 2016. Т. 54. № 4. С. 536.
Полищук В.П., Самойлов И.С., Амиров Р.Х., Кириллин А.В., Киселев В.И. Плавление графита при “низкой” температуре // ТВТ. 2020. Т. 58. № 2. С. 215.
Wei L., Kuo P.K., Thomas R.L., Anthony T.R., Banholzer W.F. Thermal Conductivity of Isotopically Modified Single Crystal Diamond // Phys. Rev. Let. 1993. V. 70. P. 3764.
Dozhdikov V.S., Basharin A.Yu., Levashov P.R. Structure of Amorphous Carbon Quenched from Liquid in the Pressure Range 1–40 GPa: Molecular Dynamic Modeling // J. Phys.: Conf. Ser. 2018. V. 946. 012086.
Giannuzzi L.A., Stevie F.A. A Review of Focused Ion Beam Milling Techniques for TEM Specimen Preparation // Micron. 1999. V. 30. № 3. P. 197.
Андреев В.Д. Спонтанная графитизация и термодеструкция алмаза при T > 2000 K // ФТТ. 1999. Т. 41. № 4. С. 695.
Dozhdikov V.S., Basharin A.Yu., Levashov P.R. Quenching of Liquid Carbon under Intensive Heat Transfer to the Cold Diamond Substrate: Molecular-dynamic Simulation // J. Phys.: Conf. Ser. 2015. V. 653. 012091.
Dozhdikov V.S., Basharin A.Yu., Levashov P.R. Liquid Carbon Quenching on a Cold Diamond Layer: Multiparticle Molecular Dynamics Simulation // J. Phys.: Conf. Ser. 2019. V. 1147. 012008.
Savvatimskiy A.I. Measurements of the Melting Point of Graphite and the Properties of Liquid Carbon (a Review for 1963–2003) // Carbon. 2005. V. 43. P. 1115.
Bergman T.L., Lavine A., Incropera F.P., Dewitt D.P. Fundamentals of Heat and Mass Transfer. N.Y.: John Wiley & Sons, 2017.
Kondratyev A.V., Rakhel A.D. Melting Line of Graphite // Phys. Rev. Lett. 2019. V. 122. P. 175702.
Steinbeck J., Dresselhaus G., Dresselhaus M.S. The Properties of Liquid Carbon // Int. J. Thermophys. 1990. V. 11. № 4. P. 789.
Korobenko V.N., Savvatimski A.I., Cheret R. Graphite Melting and Properties of Liquid Carbon // Int. J. Thermophys. 1999. V. 20. № 4. P. 1247.
Musella M., Ronchi C., Brykin M., Sheindlin M. The Molten State of Graphite: An Experimental Study // J. Appl. Phys. 1998. V. 84. P. 2530.
Balandin A.A. Thermal Properties of Graphene and Nanostructured Carbon Materials // Nat. Mater. 2011. V. 10. P. 569.
Noda T., Araki H., Suzuki H., Yang W., Ishikura T. Isotopic Effect on Thermal Conductivity of Diamond Thin Films // Mater. Trans. 2005. V. 46. № 8. P. 1807.
Vasiliev O.O., Muratov V.B., Duda T.I. The Study of Low-Temperature Heat Capacity of Diamond: Calculation and Experiment // J. Superhard Mater. 2010. V. 32. № 6. P. 375.
Dozhdikov V.S., Basharin A.Yu., Levashov P.R., Minakov D.V. Atomistic Simulations of the Equation of State and Hybridization of Liquid Carbon at a Temperature of 6000 K in the Pressure Range of 1–25 GPa // J. Chem. Phys. 2017. V. 147. P. 214302.
Patankar S. Numerical Heat Transfer and Fluid Flow. N.Y.: Hemisphere Publ. Corp., 1980.
Marks N.A. Evidence for Subpicosecond Thermal Spikes in the Formation of Tetrahedral Amorphous Carbon // Phys. Rev. B. 1997. V. 56. № 5. P. 2441.
Дополнительные материалы отсутствуют.
Инструменты
Теплофизика высоких температур