Теплофизика высоких температур, 2021, T. 59, № 3, стр. 330-336
Исследование эрозии электродов в мощных однокамерных трехфазных плазмотронах переменного тока
А. А. Сафронов 1, В. Е. Кузнецов 1, Ю. Д. Дудник 1, *, В. Н. Ширяев 1, О. Б. Васильева 1, В. Б. Ковшечников 1
1 ФГБУН Институт электрофизики и электроэнергетики РАН
Санкт-Петербург, Россия
* E-mail: julia_dudnik-s@mail.ru
Поступила в редакцию 02.07.2020
После доработки 12.10.2020
Принята к публикации 22.12.2020
Аннотация
Рассматриваются два типа плазмотронов переменного тока разной мощности, принципиально различающиеся конструкцией электродов, работающие с такими плазмообразующими газами, как воздух, азот, углекислый газ, метан, водород, гелий и др., и имеющие различное применение. Работа посвящена экспериментальным исследованиям процессов эрозии материала электродов плазмотронов, предназначенных для нагрева различных газов (воздух, азот и др.) при давлении до 8 МПа до среднемассовых температур 6000 К с тепловым КПД 60–85%.
ВВЕДЕНИЕ
Одним из основных аспектов, определяющих рабочие характеристики и надежность работы плазмотрона, является конструкция электрода. Электродная система испытывает значительные термические нагрузки, электроэрозионное воздействие, влияние коррозии со стороны элементов плазмообразующего газа, и прежде всего кислорода. Эрозионный износ материала электродов определяется мощностью плазмотрона (величиной рабочего тока), режимом работы электрода (анод или катод), свойствами плазмообразующего газа и составом материала электрода [1].
Тепловой поток электрической дуги в точке привязки на поверхности электрода приводит к плавлению материала, возникновению “ванны” расплава, при этом некоторая его часть может быть унесена с поверхности под воздействием газодинамических и электромагнитных сил. При перемещении опорного пятна дуги на поверхности электродов возможно появление кратеров и их комплексов, появление и развитие трещин и отколов, как следствие термических и усталостных напряжений. В зоне непосредственного воздействия электрической дуги на поверхность электрода возможны локальный нагрев до температуры 15 000–20 000°С и появление локальных напряжений до 1000 МПа [1, 2]. В случае остановки или уменьшения скорости движения точки привязки по поверхности электрода процесс эрозии становится интенсивнее.
Отличительной особенностью работы электродов плазмотрона переменного тока является периодическая смена полярности, приводящая к изменению механизма взаимодействия их поверхности с дугой, а также изменение тока и, соответственно, наличие переменной составляющей теплового потока в электрод.
Анализ механизма работы материалов электродов в условиях повышенной температуры показывает, что ресурс работы может быть увеличен за счет введения определенных добавок, снижающих интенсивность разрушения основного материала электрода в процессе создания плазмы, и (или) максимально равномерного распределения теплового потока по поверхности электрода.
В настоящей статье рассмотрены два типа электродной системы мощных плазмотронов переменного тока, где электрод в некотором приближении можно представить в виде цилиндра с рабочей зоной на торце, либо расположенной вдоль образующей цилиндра.
Целью работы является исследование эрозии материалов и конструкций электродных блоков мощных однокамерных трехфазных плазмотронов переменного тока в зависимости от мощности, расхода и вида рабочего газа, в том числе для диапазона давлений, превышающих атмосферное. Для определения эрозии использовался гравиметрический метод: определялась потеря массы электрода его взвешиванием до и после эксперимента. В качестве характеристики эрозии была выбрана удельная эрозия – потеря массы электрода при протекании единичного заряда через электрод.
ТРЕХФАЗНЫЙ ПЛАЗМОТРОН ПЕРЕМЕННОГО ТОКА СО СТЕРЖНЕВЫМИ ЭЛЕКТРОДАМИ
Конструктивно трехфазные плазмотроны состоят из следующих основных узлов: дуговой камеры, камеры тангенциальной закрутки подачи рабочего газа, электродного блока с электроизоляционной высокотемпературной вставкой и корпуса. Электродуговая камера трехфазного однокамерного плазмотрона со стержневыми электродами состоит из цилиндрического и сужающегося конического участков [3, 4]. В цилиндрическом участке камеры три стержневых электрода располагаются параллельно ее оси. В стенках этого участка выполнен ряд отверстий, через которые в электродуговую камеру тангенциально либо под определенным углом поступает рабочий газ.
Плазмотрон предназначен для работы на инертных газах, азоте и водороде и рассчитан на стационарный режим работы. Дуговая камера плазмотрона и электроды охлаждаются водой. Дуговая камера и корпус плазмотрона выполнены как единое целое из нержавеющей стали, имеют рубашку охлаждения, в которой расположены спиральные направляющие, организующие поток охлаждающей жидкости. Подвод охлаждающей жидкости производится в наиболее термически напряженный участок дуговой камеры, т.е. на ее срез. Компенсация термических напряжений, возникающих за счет нагрева электродуговой камеры, осуществляется гофрой, выполненной по типу сильфонной и расположенной на охлаждающей рубашке.
Принцип работы плазмотрона заключается в следующем: между торцами стержневых электродов горят дуги переменного тока, сдвинутые по фазе, величина сдвига может быть различной и определяется условиями горения дуги в электродуговой камере. Поступающий через отверстия тангенциальный поток рабочего газа образует у стенок электродуговой камеры относительно холодный слой, частично защищающий их от конвективного теплового потока. Кроме того, в зоне холодного слоя концентрация заряженных частиц резко падает, создается изолирующая область, вследствие чего столб дуги не касается стенок.
Для получения высокого теплового КПД форма камеры выбрана близкой к шарообразной: отношение длины камеры к ее среднему диаметру во всех конкретных моделях близко к единице. Существенно облегчает согласование работы плазмотрона с системой его электропитания параллельное расположение электродов, которое обеспечивает при некотором изменении длины электродов, возникающем из-за уноса электродного материала при эксплуатации, сохранение неизменными межэлектродного расстояния и, как следствие, внешних характеристик плазмотрона.
Объединение в одну камеру всех трех фаз обеспечивает постоянное горение в камере “дежурной” дуги, а вместе с ней и достаточное количество носителей зарядов (nе) для повторного зажигания дуги между парами электродов без заметных пиков напряжения при смене полярности напряжения.
КОНСТРУКЦИИ СТЕРЖНЕВЫХ ЭЛЕКРОДОВ И РЕЗУЛЬТАТЫ ИССЛЕДОВАНИЙ
В качестве рабочего материала для изготовления электродов использован вольфрам с присадками. В режиме катода присадки снижают работу выхода электронов, т.е. режим термоэмиссии наступает при более низкой температуре рабочей поверхности, а в режиме анода тугоплавкий вольфрам обеспечивает наибольшую термостойкость электрода. В экспериментах использовался вольфрам с добавками оксидов редкоземельных элементов, но необходимо заметить, что при температурах, превышающих 3200 К, оксидные соединения разрушаются и эмитировать начинает вольфрам (работа выхода для вольфрама – 4.52 эВ, для вольфрама с добавками оксида лантана(III) – около 2.6 эВ).
Длина электродов обусловлена размером камеры, необходимостью обеспечить расстояние между дугой и электроизоляционной шайбой, предотвращающее ее повреждение и разрушение. Для эффективного отвода теплового потока от рабочей поверхности электрода вода должна как можно ближе подходить к этой поверхности. Технически удается подвести воду до места крепления вольфрамовых стержней в электрододержатель. При работе на давлениях 0.1−0.5 МПа и токах до 1 кА этого оказывается достаточно для поддержания температуры поверхностных слоев электрода ниже температуры плавления, что обеспечивает термоэмиссионный режим его работы без оплавления поверхности и механического разрушения.
При возрастании тока и увеличении давления в камере плазмотрона до 1−5 МПа значительно возрастает омический тепловой нагрев электродов в зоне электродных пятен, а также лучистый тепловой поток из плазмы, и такая конструкция электрода не обеспечивает отвод избыточного тепла. Электроды начинают интенсивно разогреваться с образованием жидкой фазы и выносом расплава в электродуговую камеру и далее с потоком нагретого газа. Вольфрамовые стержни выпадают из электрододержателей, и электрод разрушается. Кроме того, значительно возрастает концентрация паров металла в дуге, что приводит к снижению напряженности электрического поля и уменьшению энерговклада. Для эффективного охлаждения электрода была разработана конструкция электрода с комбинированными водяным и газовым охлаждениями.
Электрод состоит из цилиндрического медного охлаждаемого электрододержателя и наконечника. Типы наконечников:
стержень (вольфрам–рений) диаметром 40 мм и длиной 30 мм;
стержень (вольфрам–рений) диаметром 40 мм и длиной 30 мм с рядом отверстий диаметром 2–3 мм для продува газа (рис. 1);
Рис. 1.
Электрод с наконечником (вольфрам–рений) с рядом отверстий для продува газом: 1 – электрододержатель, 2 – рубашка охлаждения, 3 – канал для подачи газа, 4 – наконечник, 5 – отверстия для продува газа.
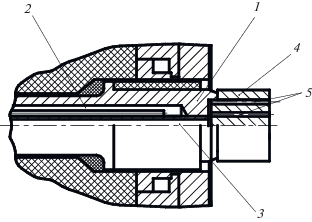
сборка стержней из лантанированного и иттрированного вольфрама диаметром 10 мм и длиной 40 мм, запаянных в медную втулку с отверстиями для продува газа (рис. 2);
Рис. 2.
Наконечник из лантанированного или иттрированного вольфрама с отверстиями для продува газа: 1 – втулка медная, 2 – стержень диаметром 10 мм, 3 – отверстия для продува газа.
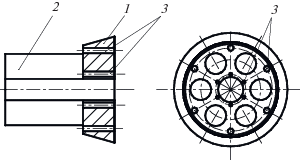
стержень из сплава вольфрам–никель–медь диаметром 40 мм и толщиной 30 мм;
сборка из вольфрамовой проволоки диаметром 1 и 2.5 мм, запрессованная в медную обойму с продувом газа через нее (рис. 3).
Рис. 3.
Электрод с наконечником из вольфрамовой проволоки с продувом газа: 1 – электрододержатель, 2 – рубашка охлаждения, 3 – канал для подачи газа, 4 – обойма медная, 5 – стержни.
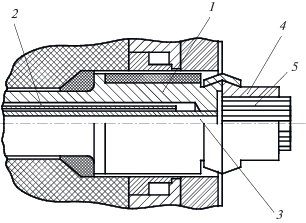
Газ подается через отверстия в вольфрамовом стержне, если наконечник в виде одного стержня, или между стержнями, если наконечник наборный. Как показали испытания, такое решение позволяет обеспечить работу электрода до давления 8 МПа при токе до 2 кА. При этом было обнаружено, что газовое охлаждение электрода примерно в 1.5 раза повышает напряжение на дуге и увеличивает мощность плазмотрона. Столб дуги становится диффузным, а рабочая поверхность электрода изнашивается более равномерно, что, по-видимому, обусловлено дестабилизацией привязки электродного пятна на поверхности. Эксплуатационные величины разрушения материала электродов и соответствующего изменения характерного показателя удельного износа (грамм на кулон) для разных температурных и тепловых режимов приведены в табл. 1.
Таблица 1.
Эксплуатационные величины разрушения материала электродов
Материал электрода | Ток, кА | Давление, МПа | Расход, кг/с | Эрозия электрода, г/Кл | |
---|---|---|---|---|---|
общий | через электрод | ||||
Вольфрам–рений, диаметр – 40 мм, W ~ 73%, Re ~ 27% |
2–3 | 1.5–2.5 азот |
0.6–1 | 2 × 10–2 | |
Вольфрам, диаметр – 40 мм | 2 | 2 азот |
0.6–1 | 10–2 | |
Вольфрам–никель–медь, диаметр – 40 мм, W ~ 80%, Ni+Cu ~ 20% |
1 | 1 азот |
0.5 | 10–3 | |
Вольфрам–никель–медь, диаметр – 40 мм, с отверстиями, W ~ 80%, Ni+Cu ~ 20% | 0.8 | 8 азот |
0.7 | 0.1 | 10–3 |
Вольфрам иттрированный, диаметр – 10 мм, с продувом, W ~ 97.6%, Y ~ 2.3% | 0.9 | 6 | 0.5 | 0.015 | 10–3 |
Вольфрам, диаметр – 2.5 мм, с продувом | 0.7 | 5 | 0.5 | 0.08 | 10–3 |
Вольфрам лантанированный, W ~ 98.9%, La ~ 1.1% |
1.0 | 0.1 водород | 0.05 | 10–3 | |
Вольфрам лантанированный, W ~ 98.9%, La ~ 1.1% |
1.0 | 0.1 гелий |
0.015 | 10–4 |
Как видно из табл. 1, определяющим фактором, влияющим на износ стержневых вольфрамовых электродов, является величина тока и давление в камере плазмотрона. Продув газа через электрод позволяет примерно на порядок уменьшить эрозию по сравнению с тем же режимом, но без продува.
ТРЕХФАЗНЫЙ ПЛАЗМОТРОН ПЕРЕМЕННОГО ТОКА С РЕЛЬСОВЫМИ ЭЛЕКТРОДАМИ
Плазмотрон с рельсовыми электродами состоит из следующих основных элементов: корпуса, выходного фланца с соплом, системы электродов и инжектора [5]. Корпус изготовлен из нержавеющей стали и представляет собой цилиндр, переходящий в усеченный конус. Охлаждение корпуса – водяное. Одним из достоинств многофазных однокамерных плазмотронов с электродами рельсового типа является достаточно низкий уровень напряжения на основных электродах. Параметры питающей сети: напряжение – 380/480 В, частота – 50/60 Гц. Электроды в разрядной камере установлены с минимальным межэлектродным расстоянием от 8−2 мм. Чтобы обеспечить надежное зажигание дуги в межэлектродном промежутке при сравнительно низком напряжении питания, в состав плазмотрона вводится однофазный высоковольтный плазмотрон в качестве инжектора носителей зарядов [6]. При работе инжектора в зоне минимального расстояния между основными электродами плазмотрона устанавливается поток плазмы с концентрацией электронов ne = 1014−1016 см–3, достаточной для зажигания основных дуг. Инициированные дуги перемещаются по расходящимся электродам со скоростью 10−30 м/с, зависящей от тока, угла наклона электродов, а также расхода и способа подачи рабочего газа. Дуги заполняют большую часть разрядной камеры, совершая движение в продольном и поперечном направлениях. Благодаря этому можно получить сравнительно большой тепловой КПД плазмотрона (до 85%) [7]. В пристеночной зоне, куда подается холодный газ, создающий изолирующий слой, концентрация заряженных частиц резко падает и происходит погасание дуги. Описанный процесс непрерывно повторяется, в результате чего на выходе из сопла плазмотрона образуется струя плазмы со среднемассовой температурой порядка 1500−5500 К.
В основу работы плазмотронов с электродами рельсового типа положен принцип электродинамического движения дуг в поле собственного тока (рельсотронный эффект). Быстрое перемещение точки привязки дуги по электроду под действием электродинамических и газодинамических сил распределяет тепловую нагрузку по длине электрода.
РЕЛЬСОВЫЕ ЭЛЕКТРОДЫ И РЕЗУЛЬТАТЫ ЭКСПЕРИМЕНТОВ
Электроды имеют изогнутую форму и могут быть выполнены из медного прутка диаметром 20−40 мм с внутренним отверстием для протекания охлаждающей жидкости (рис. 4). На каждом электроде есть два штуцера с резьбой, они позволяют зафиксировать положение электрода в разрядной камере плазмотрона. Таким образом, установленный электрод имеет одну степень свободы для перемещения в радиальном направлении. Это позволяет быстро изменять межэлектродный зазор.
Рис. 4.
Рельсовый электрод с углом раскрытия 15°: 1, 2, 3 – соответственно инжекторный, основной и сопловой вводы рабочего газа.
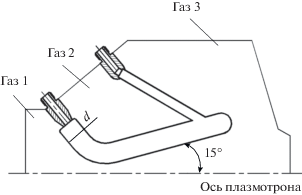
Поскольку эрозия электродов зависит как от мощности теплового источника, так и от длительности его приложения, то создание благоприятных условий для направленного перемещения опорных точек электрической дуги должно привести к снижению времени теплового воздействия и, соответственно, эрозии электродов.
В результате исследований скорости перемещения дуги [8] можно выделить наиболее важные параметры, влияющие на нее: расстояние между электродами, величину тока, состояние поверхности электродов, их материал, конструктивные особенности.
В ходе выполнения экспериментов были проведены исследования взаимосвязи следующих параметров: длительности работы, величины тока, угла раскрытия электродов, материала и конструктивных особенностей электродов. Данные, полученные при различных режимах работы плазменной системы, представлены в табл. 2.
Таблица 2.
Экспериментальные данные при различных режимах работы
Угол раскрытия электродов, град | Ток короткого замыкания, А | Средняя мощность, кВт | Суммарный расход рабочего газа, г/с | Среднее значение эрозии, г/Кл |
---|---|---|---|---|
75 | 700 | 180 | 28.7 | 4.3 × 10–6 |
30 | 500 | 285 | 26.8 | 6.6 × 10–6 |
30 | 700 | 298 | 34.8 | 7.7 × 10–6 |
30 | 700 | 278 | 32.7 | 6.6 × 10–6 |
30 | 700 | 228 | 34.8 | 3.7 × 10–6 |
45 | 1000 | 299 | 24.9 | 4.1 × 10–6 |
15 | 500 | 154 | 34.2 | 5.4 × 10–6 |
15 | 500 | 140 | 37.8 | 4.8 × 10–6 |
В экспериментах по определению удельной эрозии медных электродов в зависимости от тока, угла раскрытия, диаметра электродов и теплового потока в электроды рабочим газом был воздух. Время проведения экспериментов составляло от 2 до 40 ч. Полученные зависимости являются интегральными и не затрагивают роль микропроцессов на поверхности электродов. Как известно [9], эрозия электродов проходит в газовой, жидкой и твердой фазах. Причем до сих пор не ясен вопрос о соотношении долей каждой фазы. На рис. 5 представлены экспериментальные данные по эрозии медных электродов в зависимости от угла их раскрытия $\alpha ,$ действующего значения тока дуги I, расхода плазмообразующего газа G и суммарных тепловых потерь в электроды Q.
Рис. 5.
Зависимость величины эрозии от угла раскрытия электродов (а), тока дуги (б), расхода плазмообразующего газа (в), суммарных тепловых потерь в электроды (г).
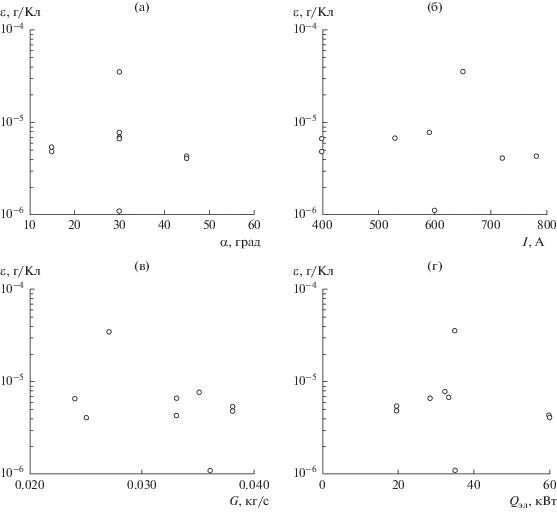
Из рисунков видно, какой-либо зависимости удельной эрозии от перечисленных выше факторов не прослеживается. В инженерных расчетах приближенно можно считать, что удельная эрозия является величиной постоянной и с некоторой степенью запаса для данных плазмотронов составляет около 10−5 г/Кл, достигая такого значения за счет того, что тепловая нагрузка от опорных пятен дуги распределяется по рабочей поверхности электрода.
На рис. 6 приведены данные по удельной эрозии медных электродов плазмотронов постоянного и переменного тока, выполненные различными исследователями [9]. Эксперименты проводились на разных по конструкции плазмотронах, при разных токах разряда и расходах плазмообразующего газа. Так же, как и в нашем случае, можно считать, что удельная эрозия является приближенно постоянной величиной, но приводимые данные по эрозии на порядок меньше.
Следует отметить, что при использовании в качестве плазмообразующего газа воздуха по мере образования слоя окалины (теплопроводность этого слоя ниже, чем у чистой меди) время, в течение которого пятно привязки дуги остается неподвижным, увеличивается; в силу этого вероятность образования каверн в металле возрастает, что увеличивает массу выносимого материала. На поверхности электрода появляются трещины, приводящие к прорыву жидкости из канала охлаждения электрода в электродуговую камеру плазмотрона (рис. 7). За время работы поверхность электродов в месте контакта с дугой становится неровной и приобретает форму сливающихся между собой полусфер диаметром 1−3 мм, на границах между которыми виден тонкий слой окислов меди.
Таким образом, в первом приближении расход материала электродов можно представить в виде
где k = 10−5 г/(А с).Для теплового потока в электроды не удалось подобрать сколько-нибудь приемлемую зависимость. Теоретическое решение задачи теплообмена также пока не представляется возможным в связи со сложным характером течения вблизи электродов. Поэтому представляется целесообразным использовать эмпирические выражения. Тепловой поток в один электрод, отнесенный к мощности плазмотрона, можно записать как
Данное соотношение, полученное в работе [10], было проверено для углов раскрытия, не превышающих 75°.
ЗАКЛЮЧЕНИЕ
Анализ результатов экспериментов позволяет сделать вывод о том, что при работе плазмотрона материалы электродов подвергаются электрической эрозии, химической эрозии, и механическому износу. В ходе исследований опробованы различные конструкции электродных систем плазмотрона переменного тока высокой мощности с торцевыми и рельсовыми электродами, получены данные по удельному эрозионному износу использованных электродных материалов.
Для стержневых электродов, изготовленных из материалов на основе вольфрама, удельная эрозия изменялась от 10−2 до 10−4 г/К, максимальный износ зафиксирован при токе 2 кА и использовании азота в качестве рабочего газа. Это может быть связано с величиной тока и присутствием некоторого количества примесей кислорода в рабочем газе, так как использовался азот технической чистоты. Минимальный износ зафиксирован в экспериментах с гелием.
Для рельсовых медных электродов установлено, что минимальный уровень удельного износа составляет 3.7 × 10−6 г/Кл при рабочем токе порядка 700 А и угле раскрытия электродов 30°. При этом во всех экспериментах удельная эрозия составляла ~10−6 г/Кл. Это достигалось вследствие равномерного распределения тепловой нагрузки по поверхности электрода, при этом выход из строя электрода происходил из-за механического разрушения (трещин до канала охлаждения), а не из-за полного износа материала.
Можно предположить, что при увеличении силы тока и преодолении некоторой, для каждой конструкции электрода своей, величины воспринимаемого теплового потока в механизме разрушения электродов начинают интенсивно проявляться процессы, не связанные напрямую с эрозией, и фактор механического разрушения становится более значимым.
Список литературы
Виноградов С.Е., Васильева О.Б., Кузнецов В.Е., Кузьмин К.А., Сафронов А.А., Овчинников Р.В., Шекалов В.И., Ширяев В.Н. Исследование влияния субмикронных частиц хрома на свойства материалов электродов низкотемпературных плазмотронов из сплавов на основе меди // Вопросы материаловедения. 2010. № 4(64). С. 111.
Хольм Р. Электрические контакты. М.: Изд-во иностр. лит., 1991. 462 с.
Сафронов А.А., Васильева О.Б., Дудник Ю.Д., Кузнецов В.Е., Ширяев В.Н. Анализ высокочастотных процессов в электроразрядной камере трехфазного плазмотрона при высоком давлении рабочего газа // ТВТ. 2017. Т. 55. № 5. С. 656.
Сафронов А.А., Ковшечников В.Б., Васильева О.Б., Дудник Ю.Д., Кузнецов В.Е., Ширяев В.Н. Исследование процессов теплообмена в трехфазном однокамерном плазмотроне с торцевыми электродами // ТВТ. 2019. Т. 57. № 6. С. 846.
Сафронов А.А., Кузнецов В.Е., Васильева О.Б., Дудник Ю.Д., Ширяев В.Н. Плазмотроны переменного тока. Системы инициирования дуги. Особенности конструкции и применения // ПТЭ. 2019. № 2. С. 58.
Dudnik Yu.D., Borovskoy A.M., Shiryaev V.N., Safronov A.A., Kuznetsov V.E., Vasilieva O.B., Pavlov A.V., Ivanov D.V. Plasma Injector for a Three-phase Plasma Torch with Rail Electrodes and Some Results of Its Investigation // J. Phys.: Conf. Ser. 2018. V. 946. № 1. P. 012 167.
Рутберг Ф.Г., Сафронов А.А., Попов С.Д., Суров А.В., Наконечный Г.В. Многофазные электродуговые плазмотроны переменного тока для плазменных технологий // ТВТ. 2006. Т. 44. № 2. С. 205.
Kuznetsov V.E., Safronov A.A., Shiryaev V.N., Vasilieva O.B., Pavlov A.V., Dudnik Y.D., Kuchina Y.A. Application Field and Ways to Control ac Plasma Torch with Rail Electrodes // J. Phys.: Conf. Ser. 2018. V. 946. № 1. P. 012166.
Теория термической электродуговой плазмы / Под ред. Жукова М.Ф. Ч. 2. Новосибирск: Наука, 1987. 286 с.
Ковшечников В.Б., Антонов Г.Г., Уфимцев А.А. Об эффективности нагрева газа трехфазным плазмотроном переменного тока со скользящими дугами // ИФЖ. 2007. Т. 80. № 6. С. 57.
Дополнительные материалы отсутствуют.
Инструменты
Теплофизика высоких температур