Теплоэнергетика, 2022, № 2, стр. 33-41
Новые возможности для совместного расчета котла и его пылесистем
В. М. Супранов a, *, Г. И. Доверман b, **, И. Г. Петров b, К. А. Плешанов a
a Национальный исследовательский университет “Московский энергетический институт”
111250 Москва, Красноказарменная ул., д. 14, Россия
b OOO “OПТСИМ-K”
117534 Москва, ул. Академика Янгеля, д. 8, оф. 72, Россия
* E-mail: svm-mpei@mail.ru
** E-mail: doverman@optsim-k.com
Поступила в редакцию 03.06.2021
После доработки 24.06.2021
Принята к публикации 26.06.2021
- EDN: ULTNQE
- DOI: 10.1134/S0040363622020060
Аннотация
Современные пылеугольные котлы и обслуживающие их индивидуальные системы пылеприготовления отличаются высокой сложностью, большой металлоемкостью и широким спектром протекающих в них физико-химических процессов. Компоненты сушильного агента или транспортирующей среды формируются из теплоносителей, используемых в котле. Отбор части теплоносителей из трактов котла в системы пылеприготовления влияет на протекание процессов теплообмена и, в конечном счете, на КПД котла и расход топлива. В результате пылесистемы оказывают существенное влияние на тепловую работу котла, а сам котел – на работу пылесистем. Если проводить тепловой расчет котла без учета этого обстоятельства, ошибка по температуре уходящих газов может достигать 25–30°C, а по КПД – 1.5–2.0%. Поэтому при проектировании новых или при исследовании работы уже существующих котельных установок актуальной задачей является проведение совместного теплового расчета пылеугольного котла и его пылесистем, что практически невозможно без использования компьютерных программ. До настоящего времени в России для этого применяли две программы: одну для тепловых расчетов котла, другую – для расчета пылесистем, а коммуникацию между ними осуществлял пользователь. Но такая технология проведения совместного расчета имеет много недостатков, они указаны в статье. Анализ этих недостатков показывает, что большинство из них можно устранить, если совместный расчет котла и пылесистем выполнять в одной программе. Программный комплекс Boiler Designer, широко используемый как в России, так и за рубежом, построен по объектно-ориентированному принципу, позволяющему проводить его расширение благодаря созданию новых элементов. Был разработан элемент “Пылесистема” и выпущена новая версия программы, позволяющая выполнять этот совместный расчет. Масштабное тестирование программы прошло успешно и показало, что проводить расчет стало проще, удобнее и быстрее, чем по старой технологии с использованием двух программ. При этом трудоемкость снижается не менее чем в 2 раза.
Котельные установки с пылеугольными котлами и индивидуальными системами пылеприготовления отличаются высокой сложностью, большими габаритами и металлоемкостью. По данным [1] общая масса металла котла П-67 энергоблока 800 МВт составляет 19 320 т, из них элементов конструкции, изготовленных из легированных сталей, – 8480 т. Оборудование систем пылеприготовления тоже весьма сложное и металлоемкое. Так, например, по данным [2] масса шаровой барабанной мельницы ШБМ-400/1000 (Ш-70) равна 247 т, а вместе с загружаемыми шарами на 138 т больше. Поэтому ошибки при расчетах и проектировании обходятся очень дорого как из-за стоимости металла, так и из-за частичной неработоспособности котельной установки.
В то же время работа пылеугольных котлов и обслуживающих их систем пылеприготовления обусловлена широким спектром протекающих в них физико-химических процессов. Основные из них – размол и сушка топлива, пневмотранспортировка пыли в топку, воспламенение и горение топлива, радиационный и конвективный теплообмен, а также движение теплоносителей по трактам котла, в том числе с изменением фазового состояния. Разнообразие и сложность протекания этих процессов и сложность конструкции самих установок требуют использования для их расчетов современных средств компьютерной техники и программного обеспечения. Основным из этих расчетов можно считать тепловой расчет котла, так как его результаты используются в качестве исходных данных для всех остальных расчетов. А с тепловым расчетом котла в большинстве случаев неразрывно связан тепловой расчет систем пылеприготовления.
В СССР, а позднее и в России для теплового расчета котлов широко использовали программу Trakt. Для своего времени это был качественный программный продукт. Но сейчас можно констатировать, что он имеет как минимум следующие недостатки: ограниченное число элементов в расчетной схеме трактов котла, невозможность корректного расчета котлов-утилизаторов и устаревший интерфейс. Для проведения теплового и аэродинамического расчетов пылесистем совместно с программой Trakt применяли программу Trap, которая также имеет неудобный интерфейс. Кроме того, в случаях сложной организации сушки топлива ее не всегда удобно было использовать.
В настоящее время вместо программы Trakt часто применяют программу Boiler Designer [3], которая разработана специалистами OПТСИМ-K и KED и поддерживается в России фирмой OПТСИ-М-K. Она может быть использована для теплового, гидравлического и аэродинамического расчетов котлов на органическом топливе и котлов-утилизаторов. В программе предусмотрены расчет естественной и принудительной циркуляций в барабанных котлах и проверка надежности циркуляции. Возможно выполнение расчета тепловой схемы любого энергоблока, а также электростанций с поперечными связями, в том числе расчеты внедренных в эти схемы котлов. Помимо статических расчетов, можно моделировать переходные процессы при переменных режимах работы объекта исследования. Количество элементов в расчетной схеме не ограничено, что является безусловным достоинством.
Программа Boiler Designer построена по объектно-ориентированному принципу. Расчетные схемы объектов моделирования создаются из стандартных элементов. Отдельные элементы являются иерархическими, т.е. включают группы, в которые могут быть помещены другие элементы. Количество иерархических уровней не ограничено, что позволяет адекватно смоделировать тепловые схемы и конструктивные особенности сложных современных котлов. Использование объектно-ориентированного принципа дает возможность проводить укрупнение – из моделей энергоблоков составлять модель электростанции, а в принципе, и модель энергосистемы, если позволяют вычислительные мощности.
Появились и новые программы для расчета систем пылеприготовления. Одна из них представлена в [4].
АКТУАЛЬНОСТЬ СОВМЕСТНОГО РАСЧЕТА КОТЛА И ПЫЛЕСИСТЕМ
При выполнении теплового расчета любой системы пылеприготовления необходимо учитывать целый ряд ограничений. Температура за пылесистемой t2 ограничена по верхнему пределу по условиям взрывобезопасности и надежности работы оборудования, по нижнему пределу – по условиям отсутствия конденсации. При использовании газовой или газовоздушной сушки топлива нужно следить, чтобы объемная концентрация кислорода в сушильном агенте (СА) удовлетворяла требованиям [5]. Если пыль транспортируется в горелки СА, необходимо, чтобы доля первичного воздуха соответствовала рекомендациям [2] или других регламентирующих документов.
Мельница должна обеспечивать определенную по условиям работы котла размольную производительность Bм, при этом остаток пыли R90 на сите с ячейкой 90 мкм должен удовлетворять рекомендациям [2]. Помимо конструктивных характеристик мельницы размольная производительность обеспечивается вентиляционным расходом за пылесистемой V2, который нужно поддерживать на требуемом уровне. Но влажность пыли Wпл тоже должна удовлетворять рекомендациям [2]. А она при t2 = const зависит и от V2, и от начальной температуры сушильного агента t1.
Обычно применяется как минимум двухкомпонентный сушильный агент. Если температура горячего компонента СА достаточно высока, можно, изменяя доли компонентов, обеспечить такие условия сушки топлива, при которых значение Wпл за пылесистемой соответствует рекомендациям [2], а вентиляционный расход V2 поддерживается постоянным по условиям размола. При этом сушильная производительность системы пылеприготовления Bсуш будет равна размольной производительности Bм. Поэтому тепловой расчет пылесистемы в большинстве случаев проводится именно для того, чтобы в рамках перечисленных выше ограничений определить расходы (или массовые доли) компонентов СА, при которых Bсуш = Bм.
Однако компоненты сушильного агента или транспортирующей среды формируются из теплоносителей, используемых в котле. Отбор части теплоносителей из трактов котла в системы пылеприготовления влияет на процессы теплообмена и, в конечном счете, на КПД котла и расход топлива. Поэтому расходы компонентов сушильного агента, полученные в результате теплового расчета пылесистем, должны быть учтены при проведении тепловых расчетов котла. Таким образом, системы пылеприготовления являются важнейшими элементами котельной установки и оказывают огромное влияние на работу пылеугольного котла. Единственным исключением являются пылесистемы с сушкой горячим воздухом и рециркуляцией СА, потому что холодный компонент (рециркулирующий СА) не отбирается из котла.
Результаты расчета котла ТП-14А и его пылесистем по двум программам (2014 г.) и новой версии Boiler Designer (2021 г.)
Параметр | 2014 г. | 2021 г. |
---|---|---|
Паропроизводительность D, т/ч | 220 | 220 |
Температура перегретого пара tпе, °C | 540 | 540 |
Расход на впрыск Dвпр, т/ч | 0.049 | 0 |
Полный расход угля B, т/ч | 31.107 | 31.096 |
Расход природного газа при нормальных условиях Bг, тыс. м3/ч | 3.481 | 3.479 |
Доля газа по теплоте bг | 0.2 | 0.2 |
КПД котла η, % | 89.855 | 89.887 |
Температура, °C: | ||
газов за топкой $\vartheta _{{\text{т}}}^{{''}}$ | 1100 | 1099 |
уходящих газов ϑух | 165 | 164 |
воздуха перед трубчатым воздухоподогревателем $t_{{{\text{ТВП}}}}^{'}$ | 52 | 52 |
за пылесистемами t2 | 200 | 200 |
горячего воздуха tг.в | 434 | 432 |
Число работающих мельниц Zм | 4 | 4 |
Вентиляционный расход V2, тыс. м3/ч | 50 | 50 |
Массовое количество сушильного агента, кг/кг: | ||
на входе в пылесистему g1 | 3.524 | 3.442 |
на выходе из пылесистемы g2 | 4.767 | 4.661 |
Тепло, кДж/кг (ккал/кг): | ||
сушильного агента qс.а | 1662.2 (396.70) | 1664.8 (397.34) |
выделившееся при работе мелющих агрегатов qмех | 25.9 (6.19) | 25.9 (6.19) |
внесенное с присосом qприс | 32.1 (7.67) | 31.5 (7.52) |
затраченное на испарение влаги qисп | 536.3 (128.0) | 538.0 (128.4) |
уносимое из пылесистемы с сушильным агентом и присосом q2 | 915.9 (218.60) | 916.9 (218.83) |
затраченное на подогрев топлива qтоп | 262.3 (62.60) | 261.8 (62.49) |
Тепловые потери пылесистемы q5, кДж/кг (ккал/кг) | 5.6 (1.33) | 5.6 (1.33) |
Содержание кислорода на выходе пылесистемы, % | 19.20 | 18.87 |
Доля первичного воздуха r1 | 0.624 | 0.590 |
Присос в пылесистемах Δαпл | 0.151 | 0.148 |
На работу самих систем пылеприготовления также влияет режим работы котла. Условия сушки топлива зависят от температуры компонентов сушильного агента. Важна и топливная загрузка пылесистем, которая определяется расходом топлива в котел B. Поэтому значения B и температуры компонентов СА, полученные при расчетах котла, являются исходными данными для теплового расчета пылесистем.
Влияние систем пылеприготовления на работу котла можно продемонстрировать на примере расчета корпуса котла ПК-39 при сжигании экибастузского угля марки 2СС на номинальной нагрузке. Каждый корпус котла укомплектован четырьмя пылесистемами с прямым вдуванием и воздушной сушкой с мельницами ММТ-2000/2600/596. Основной компонент СА – горячий воздух, отобранный после регенеративных воздухоподогревателей (РВП), второй компонент – холодный воздух.
При выполнении совместного расчета корпуса котла и пылесистем по программам Boiler Designer и рассмотренной в [4] температура уходящих газов равна 156.5°C, КПД котла составляет 90.294%. Если не учитывать влияние пылесистем и выполнить только тепловой расчета корпуса котла по программе Boiler Designer, получится соответственно 128.7°C и 91.946%. Рассмотрим, чем обусловлено такое существенное различие (рис. 1). Для простоты на рис. 1 не показано распределение пылевоздушной смеси и вторичного воздуха по отдельным горелкам.
Рис. 1.
Схема отбора воздуха в пылесистемы корпуса котла ПК-39. 1 – корпус котла; 2 – регенеративный воздухоподогреватель; 3 – дутьевой вентилятор; 4 – клапан
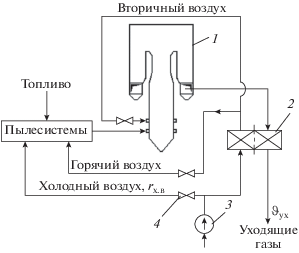
Если в пылесистемы не подается холодный воздух, то его доля в СА составляет rх.в = 0 и весь организованно подаваемый в топку воздух проходит через РВП. Так было бы, если бы не учитывалась работа систем пылеприготовления. Но если выполнить тепловой расчет пылесистем, то из условия равенства сушильной и размольной производительностей получается, что rх.в > 0. Тогда, согласно проводимому тепловому расчету корпуса котла, через РВП будет протекать меньше воздуха, его скорость снизится, а коэффициенты теплоотдачи α2 и теплопередачи k станут меньше. В результате дымовые газы будут хуже охлаждаться в РВП, поэтому температура уходящих газов ϑух возрастет, а КПД корпуса котла снизится.
Если используется двухкомпонентная газовая сушка топлива, то в зависимости от массовых долей горячих rг.г и холодных rх.г газов в СА будут изменяться их коэффициенты рециркуляции в котле. Поэтому условия протекания радиационного и конвективного теплообменов на участках газового тракта, охваченных рециркуляцией, будут зависеть от работы систем пылеприготовления. При использовании газовоздушной сушки топлива сушильный агент обычно формируется из продуктов сгорания, отбираемых из газового тракта, и горячего воздуха. Значит, и в этом случае от условий сушки топлива зависят доля газов в СА и коэффициент их рециркуляции в газовом тракте. Поэтому совместный расчет котла и пылесистем необходим практически во всех случаях. Исключение составляют только системы пылеприготовления с сушкой горячим воздухом при наличии рециркуляции сушильного агента.
СУЩЕСТВУЮЩАЯ СХЕМА РЕАЛИЗАЦИИ СОВМЕСТНОГО РАСЧЕТА И ЕЕ НЕДОСТАТКИ
Обычно для проведения совместных тепловых расчетов котла и систем пылеприготовления использовали две разные программы. Взаимодействие их приходилось организовывать пользователю примерно так, как это показано на рис. 2.
Расчет выполняли итерационным способом. Сходимость расчета контролировали по расходу топлива B, температурам ti и расходам Vi компонентов сушильного агента на предыдущей и текущей итерациях. Как показывает опыт, расчет можно прекращать, когда при переходе на следующую итерацию изменение B составляет не более 0.05%, температур ti – не более 1°C, расходов Vi – не более 0.05%. Обычно для того, чтобы добиться сходимости расчета, требуются три-четыре итерации.
Многовариантные совместные расчеты котлов и пылесистем, выполненные по такой схеме, описаны в работах [6–8]. В [6] использовали программы Boiler Designer и Trap, а в [7] – Boiler Designer и программу, представленную в [4]. В [8] приведены результаты расчетных исследований работы пылеугольного котла энергоблока 600 МВт с организацией сжигания по технологии Oxyfuel Combustion. При этом в топку вместо воздуха подается другая среда, содержащая окислитель (ССО) и состоящая из газов рециркуляции и кислорода, концентрация которого обычно больше, чем в воздухе. Это позволяет практически исключить азот из состава газов, уменьшить их расход за котлом, повысить в них концентрацию углекислого газа и тем самым облегчить выделение, транспортировку и захоронение углекислого газа. Для расчетов котла использовали программу Boiler Designer, которая без проблем позволила смоделировать технологию Oxyfuel Combustion. Но применить описанные выше программы расчета систем пылеприготовления не удалось из-за их существенного недостатка – они позволяют работать только с одной ССО – воздухом. Поэтому для теплового расчета пылесистем пришлось разработать модуль в среде Mathcad, который использовал методику [2], но был адаптирован к технологии Oxyfuel Combustion. В остальном расчеты также проводили по схеме, представленной на рис. 2.
Определенные сложности при выполнении совместных расчетов котла и пылесистем возникают также в том случае, когда для снижения выбросов вредных веществ на стадии сжигания топлива применяется Reburning Technology [9]. Так, например, случилось при расчетах котла Е‑320-13.8-560КТ, который обслуживался тремя системами пылеприготовления с прямым вдуванием, укомплектованными мельницами МВС-195 с динамическими сепараторами. Две пылесистемы обслуживали два основных яруса горелок. Их суммарная размольная производительность составляла 75% полного расхода топлива в котел, и они вырабатывали пыль с R90 = 10% при организации воздушной сушки. Третья пылесистема, в которой размалывалось еще 25% топлива при газовоздушной сушке, что обусловлено выбранной схемой низкоэмиссионного сжигания, обслуживала восстановительный ярус горелок. Тонкость помола R90 составляла 6%. Расчеты выполняли с использованием программ Boiler Designer и представленной в [4] по схеме, приведенной на рис. 2. Проблема заключалась в том, что совместно с котлом рассчитывали две группы систем пылеприготовления. При этом добиться сходимости теплового расчета котла и двух тепловых расчетов пылесистем оказалось гораздо сложнее.
Анализируя накопленный опыт проведения совместных расчетов котла и систем пылеприготовления с использованием двух программ, можно отметить следующие недостатки:
трудоемкость выполнения итераций;
возрастание вероятности ошибок из-за участия человека в обмене данными между программами;
увеличение количества файлов исходных данных в 2 раза (а иногда и более) и необходимость проведения работ по их синхронизации;
невозможность применения существующих программ теплового расчета пылесистем при использовании новых технологий сжигания (Oxyfuel Combustion) или значительное усложнение расчетов (Reburning Technology).
СПОСОБ РЕШЕНИЯ ПРОБЛЕМ
Первые три недостатка могут быть устранены, если тепловые расчеты котла и его систем пылеприготовления будут выполняться в одной программе. Для устранения последнего недостатка нужно, чтобы в этой программе была предусмотрена возможность моделирования работы пылесистем при использовании новых технологий сжигания. В программе Boiler Designer многие возможности для этого уже существуют [8]. Объектно-ориентированный принцип построения программы Boiler Designer позволяет создавать и внедрять в нее новые элементы, способные работать совместно с уже существующими. Для реализации возможности проведения совместных расчетов котла и систем пылеприготовления был создан элемент “Пылесистема”, который в дальнейшем можно совершенствовать.
Этот элемент может применяться для моделирования работы одной реально существующей системы пылеприготовления (мельница и обслуживающее ее оборудование) и нескольких систем, работающих с одинаковыми эксплуатационными параметрами. Поэтому можно учесть особенности работы отдельных мельниц (в том числе разного типа) при использовании Reburning Technology или в других случаях. В зависимости от способа сушки топлива (воздушная, газовая, газовоздушная) элемент “Пылесистема” включается в структуру воздушного, газового тракта или в схемы их обоих.
Количество исходных данных, которые необходимо ввести для нового элемента, невелико. К ним относятся влажность пыли W пл, %, количество мельниц Zм, затраты электроэнергии на размол Эрзм, кВт ⋅ ч/т, коэффициент присоса Kприс, коэффициент Kмех, который учитывает долю энергии, переходящей в тепло при работе мелющих органов, абсолютные потери тепла в окружающую среду Q5, кДж/ч (ккал/ч). Все они подготавливаются или принимаются по рекомендациям [2]. Но для выполнения расчета пылесистемы нужно знать и другие данные, например влажность топлива на рабочую массу Wr и размольную производительность мельницы Bм. Эта проблема решена за счет объектно-ориентированного принципа построения программы. Элемент “Пылесистема” является иерархическим и содержит группу, в которую просто копируется ранее созданный элемент “Топливо”. Благодаря этому становятся известны значения W r и B и возможно определение Bм.
Тепловой баланс системы пылеприготовления описывается уравнениями, представленными в [2]. Постановка задачи ее теплового расчета обычно заключается в определении состава сушильного агента при V2 = const и t2 = const. Для выполнения этих условий необходимо применять два элемента “Регулятор расхода” в программе Boiler Designer. На рис. 3 показан пример использования этих элементов.
Рис. 3.
Структура воздушного тракта котла с элементом “Пылесистема” (фрагмент программы с монитора компьютера). 1 – элемент “Пылесистема”; 2 – смеситель; 3, 5 – регуляторы вентиляционного расхода и температуры t2; 4 – клапан подачи горячего воздуха; 6 – клапан присадки холодного воздуха
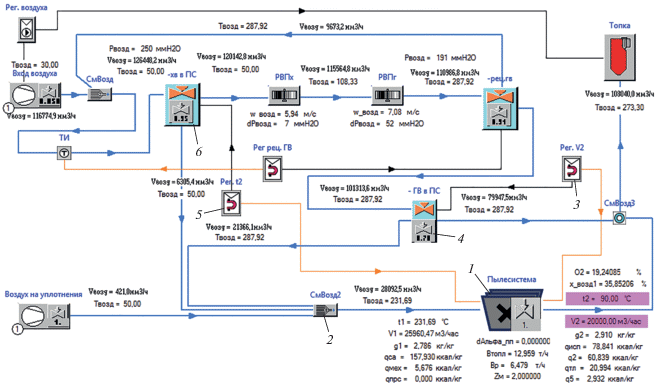
В данном случае применяется воздушная сушка топлива, поэтому элемент “Пылесистема” 1 вставлен в структуру воздушного тракта котла. Перед ним расположен смеситель 2, в который поступают компоненты сушильного агента. Сушильный агент состоит из горячего воздуха, который отбирается за регенеративным воздухоподогревателем, присадки холодного воздуха, отобранного до РВП, и той части воздуха, подаваемого на уплотнение мельниц, которая попадает в них. Регулятор 3 обеспечивает выполнение условия V2 = const, воздействуя на клапан подачи горячего воздуха на сушку 4. Регулятор 5 поддерживает постоянную температуру на выходе из пылесистем, для этого используется клапан присадки холодного воздуха 6.
При совместном расчете котла и пылесистем в одной программе удается повысить точность теплового расчета пылесистем. Это обеспечивается благодаря тому, что расчет ведется по фактическим значениям энтальпий потоков СА на входе в систему пылеприготовления и выходе из нее, а в [2] теплоемкости этих потоков определяются приближенно. Правда, и в программе, описанной в [4], теплоемкости вычисляются по фактическому составу сред, но некоторые температуры, необходимые для их определения и полученные из теплового расчета котла, приходится вводить как исходные данные.
Элемент “Пылесистема” позволяет довольно просто смоделировать рециркуляцию СА в любой системе пылеприготовления. Как было показано в [7, 10], рециркуляция сушильного агента может быть полезна не только для пылесистем с промежуточным бункером и шаровыми барабанными мельницами. В [10] описан опыт внедрения данного мероприятия на действующем котле, укомплектованном мельницами-вентиляторами.
Системы пылеприготовления с промежуточными бункерами тоже можно моделировать с помощью элемента “Пылесистема”, но только при работе с коэффициентом запаса Kзап = 1. Это означает, что суммарная размольная производительность всех мельниц по сырому топливу должна быть равна расходу топлива в котел, так как в текущей версии программы Boiler Designer не учитываются накопление топлива в промежуточном бункере и передача пыли из одной пылесистемы в другую. Полный расход топлива в котел определяется исходя из уравнения его теплового баланса. Но чаще всего встречаются системы пылеприготовления с промежуточным бункером, воздушной сушкой и рециркуляцией СА. Они обладают тем преимуществом, что практически не влияют на работу котла независимо от значения Kзап. Но если все-таки необходимо выполнить тепловой расчет пылесистемы с Kзап ≠ 1, в программе предусмотрена и такая возможность, так как можно проводить расчет системы пылеприготовления любого типа отдельно от котла (рис. 4).
На рис. 4 показаны расчетная схема и результаты теплового расчета пылесистемы с промежуточным бункером, воздушной сушкой и рециркуляцией СА. Элемент “Рег. V2” обеспечивает V2 = const, но для поддержания t2 = const в этом случае использовать отдельный регулятор не нужно, потому что с элементом “Пылесистема” совмещен клапан рециркуляции сушильного агента (Кл. рецирк.). В окошке клапана можно задать нужное значение t2 (в данном случае 140°C), включить опцию “Регулирование”, и программа обеспечит коэффициент рециркуляции СА, при котором температура за системой пылеприготовления поддерживается на заданном уровне.
Новая версия программы Boiler Designer, позволяющая проводить совместный расчет котла и его пылесистем, была протестирована. При этом рассматривали прямоточные котлы и котлы с естественной циркуляцией, в которых сжигаются разные угли (в двух случаях совместно с природным газом). Они были укомплектованы системами пылеприготовления различного типа с разными способами организации сушки топлива. В каждом случае сравнивались результаты двух расчетов. Первый был выполнен по схеме использования двух программ (см. рис. 2), второй – по новой версии Boiler Designer.
Результаты одного из вариантов тестирования для режима работы котла ТП-14А при совместном сжигании угля и природного газа приведены в таблице. Из представленных данных видно, что в целом совпадение результатов хорошее, но по ряду параметров наблюдается небольшое расхождение. Это может быть связано с тем, что в программе, представленной в [4], и в Boiler Designer физические свойства продуктов сгорания определяются по разным методикам. А при совместном сжигании угля и природного газа это наиболее заметно.
Не исключено и влияние человеческого фактора, потому что расчет по двум программам при совместном сжигании угля и газа сводить сложнее. В новой версии Boiler Designer это происходит без участия пользователя и с большей точностью. Процесс тестирования подтвердил, что выполнять совместный расчет котла и пылесистем по новой версии программы проще, удобнее и быстрее, чем старым способом с использованием двух программ. При этом трудоемкость снижается не менее чем в 2 раза. В этом заключается практическая ценность выполненной работы.
ВЫВОДЫ
1. В подавляющем большинстве случаев работа систем пылеприготовления оказывает существенное влияние на работу котла. Поэтому задача совместного расчета котла и пылесистем с помощью современного программного обеспечения является актуальной.
2. Анализ существующей схемы реализации этого совместного расчета показал, что она обладает рядом недостатков. По сути, все они обусловлены тем обстоятельством, что для расчета котла и пылесистем используются две разные программы, а коммуникацию между ними осуществляет пользователь.
3. Тестирование новой версии Boiler Designer показало, что задача совместного расчета котла и его систем пылеприготовления может быть успешно решена с использованием одной программы. При этом удалось устранить недостатки, присущие старой схеме выполнения этого расчета.
Список литературы
Тепловые и атомные электрические станции: справочник. Т. 3 / под ред. А.В. Клименко, В.М. Зорина. М.: Энергоатомиздат, 2003.
Расчет и проектирование пылеприготовительных установок котельных агрегатов (нормативные материалы). Руководящие указания. Л.: НПО ЦКТИ, 1971.
Расчет котельных агрегатов с использованием современных программных продуктов / Г.И. Доверман, Б.Л. Шелыгин, А.В. Мошкарин, Ю.В. Мельников. Иваново: Ивановский гос. энергет. ун-т, 2007.
Майданик М.Н., Тугов А.Н., Супранов В.М. Тепловой расчет систем пылеприготовления котельных установок: новый подход // Теплоэнергетика. 2021. № 6. С. 25–32. https://doi.org/10.1134/S0040363621060059
РД 153-34.1-03.352-99. Правила взрывобезопасности топливоподачи и установок для приготовления и сжигания пылевидного топлива. М.: ВТИ, 2000.
Изюмов М.А., Супранов В.М., Росляков П.В. Исследование возможности перевода котлов ТП-92 Яйвинской ГРЭС на непроектные виды углей // Теплоэнергетика. 2008. № 9. С. 7–18.
Супранов В.М., Штегман А.В., Фоменко Е.А. Оценка возможности перевода котлов ТП-14А Кумертауской ТЭЦ на сжигание угля марки Б3 Верхне-Сокурского месторождения // Теплоэнергетика. 2016. № 4. С. 50–59. https://doi.org/10.1134/S0040363616040081
Исследование возможности и целесообразности работы котла Пп-1900-25-570КТ в режиме кислородного сжигания топлива / В.М. Супранов, В.А. Баторшин, А.В. Штегман, Д.А. Мельников // Теплоэнергетика. 2012. № 8. С. 10–18.
Росляков П.В. Методы защиты окружающей среды. М.: Издательский дом МЭИ, 2007.
Кириллов М.В., Сафронов П.Г. Технические и организационные решения по улучшению технико-экономических показателей работы котла ТПЕ-216 с мельницами-вентиляторами МВ-3300/800/490 // Теплоэнергетика. 2014. № 7. С. 11–17. https://doi.org/10.1134/S0040363614070054
Дополнительные материалы отсутствуют.
Инструменты
Теплоэнергетика