Теплоэнергетика, 2022, № 2, стр. 23-32
Окислительная торрефикация в кипящем слое некоторых видов биомассы
В. С. Кох-Татаренко a, *, С. Н. Кузьмин a, А. В. Небываев a, Р. Л. Исьёмин b, А. В. Михалёв b, О. Ю. Милованов b
a Тамбовский государственный технический университет
392000 Тамбов, ул. Советская, д. 106, Россия
b ООО “Чистая энергия”
392032 Тамбов, Мичуринская ул., д. 112, к. И, оф. 1, Россия
* E-mail: penergy@list.ru
Поступила в редакцию 17.03.2021
После доработки 22.04.2021
Принята к публикации 19.05.2021
- EDN: MAQFUS
- DOI: 10.1134/S0040363622020023
Аннотация
В настоящее время все большее внимание уделяется декарбонизации энергетики и снижению в связи с этим потребления ископаемых топлив. Поскольку одной из насущных проблем современности является утилизация отходов, немалую часть которых составляет биомасса, актуальным становится повышение эффективности ее использования в качестве топлива. Торрефикация – одна из наиболее приемлемых технологий получения качественного топлива из биомассы, позволяющая при относительно небольших энергозатратах увеличить теплоту сгорания биотоплива, снизить его гидрофильность и повысить размолоспособность. Усовершенствовать процесс торрефикации можно при ее проведении в газовой среде с небольшим содержанием кислорода. Это позволит сократить как энергозатраты на процесс, так и его продолжительность. В работе представлены результаты исследования окислительной торрефикации трех видов мелкодисперсной биомассы: измельченной лузги подсолнечника, куриного помета и древесных опилок. Процесс проводится в кипящем слое с переходом биомассы в псевдоожиженное состояние при воздействии дымовых газов температурой 250°С и с содержанием кислорода 2–3% (по объему). Исследования показали, что полидисперсный состав и сложная форма частиц биомассы позволяют обеспечить устойчивое псевдоожижение в довольно узком диапазоне скоростей газа. Сам процесс окислительной торрефикации занимает от 5 до 15 мин в зависимости от вида биомассы. Столь широкий интервал времени обусловлен наличием или практическим отсутствием развития экзотермических реакций в зависимости от вида используемого сырья. Максимальный экзотермический эффект проявляется при окислительной торрефикации лузги подсолнечника, минимальный – куриного помета.
При сжигании растительной биомассы выделяется такое же количество углекислого газа (CO2), какое было поглощено растением за весь период его вегетации. Этот углекислый газ представляет собой углеродно-нейтральное легкодоступное топливо [1, 2], поскольку период выращивания растительной биомассы до ее сжигания не превышает нескольких десятилетий, в отличие от ископаемого топлива, формировавшегося миллионы лет. Однако биомасса в исходном состоянии имеет значительно более низкую теплоту сгорания, значительно более высокую влажность и небольшую насыпную плотность в сравнении с ископаемым топливом [3, 4], что ограничивает ее энергетическое использование. Пеллетизированная биомасса лишена некоторых из перечисленных недостатков, но и она остается гидрофильной, что осложняет ее перевозку и хранение. К тому же пеллеты, несмотря на их широкое использование в бытовом теплоснабжении, не могут в больших масштабах применяться на крупных энергетических установках из-за высокой стоимости.
Влажность биомассы и содержание в ней летучих веществ можно понизить, а теплоту сгорания, гидрофобность и размолоспособность повысить путем термической обработки биомассы в бескислородной среде при температуре 200–300°C. Данный процесс называется торрефикацией. В процессе торрефикации из исходной биомассы удаляется влага, в результате чего содержание кислорода в ней значительно уменьшается, поэтому при газификации торрефицированной биомассы образуются газообразные продукты с большей теплотой сгорания, чем при газификации исходной биомассы. Торрефицированная биомасса имеет более низкую скорость горения, чем исходная биомасса, что позволяет завершить процесс сжигания в топке котла и исключить возможность горения в притопочных дымоходах, минимизировав при этом опасность расплавления золы и образования плотных золовых отложений на конвективных поверхностях нагрева котла. Благодаря повышенной гидрофобности торрефицированной биомассы ее можно складировать не в закрытых помещениях, а на открытом воздухе под навесом, что существенно сокращает затраты на хранение такого биотоплива и упрощает работу с ним.
Имеются данные, что энергоресурсы, направленные на измельчение биомассы, в 3.5–4.0 раза превышают таковые при обработке угля [5]. Повысив размолоспособность торрефицированной биомассы, эти расходы можно сократить. Таким образом, на основании вышеперечисленных факторов можно заключить, что торрефицированная биомасса является более подходящим продуктом для совместного сжигания с углем, нежели исходная [6–10].
Торрефикация – это довольно энергозатратный процесс. Снизить расходы на эксплуатацию установок для нее можно путем использования воздуха и газообразных продуктов торрефикации вместо азота. Такой процесс носит название окислительной торрефикации. Проведенные исследования влияния концентрации кислорода в газе, подаваемом в реактор, и температуры торрефикации на свойства биомассы [11] показали, что изменение содержания O2 в диапазоне от 2 до 21% (по объему) не оказывает значительного влияния на состав твердого продукта при низких температурах (менее 280°С). Это предотвращает окисление летучих веществ, выделяющихся в процессе торрефикации.
Авторы [12–14] определили, что характеристики окислительной торрефикации (массовый выход и свойства твердого продукта) существенно зависят от природы исходного сырья. В частности, они установили, что окислительная торрефикация является более подходящей для обработки древесной биомассы, нежели волокнистой (недревесной). Кроме формы частиц на процесс окислительной торрефикации влияет их размер, в том числе площадь поверхности обрабатываемых частиц, контактирующей с газовой средой [12].
Цель настоящей работы – исследование процесса окислительной торрефикации различных видов биомассы: древесных отходов, лузги подсолнечника и куриного помета. Причем для максимального увеличения площади поверхности контакта биомассы с кислородсодержащим газом ее предложено измельчать, а процесс торрефикации осуществлять в кипящем слое [15, 16].
ЭКСПЕРИМЕНТАЛЬНАЯ УСТАНОВКА
Для исследования процесса окислительной торрефикации измельченной биомассы была создана экспериментальная установка (рис. 1). Она состоит из реактора с кипящим слоем, покрытого “рубашкой”, в которую подается жидкий теплоноситель (термомасло ТЛВ-330), нагреваемый в электрокотле. Реактор представляет собой стальную трубу диаметром 108 мм (толщина стенки 4 мм) и высотой 1000 мм. Сверху в реактор порциями через патрубок вводится исходная биомасса, снизу выводится торрефицированная биомасса.
Рис. 1.
Схема экспериментальной установки для исследования процесса окислительной торрефикации биомассы. 1 – реактор; 2 – электрокотел; 3 – дымосос; 4 – теплообменник; 5 – бак – аккумулятор воды; 6 – циклон; 7 – электрохимический сенсор
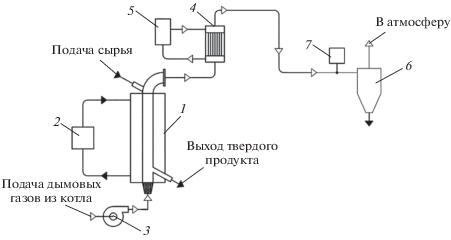
Согласно результатам исследований [15, 16], в кипящем слое инертного материала обеспечить однородность частиц биомассы при торрефикации невозможно. Трудно также отделить частицы биомассы от инертного материала. Поэтому было принято решение отказаться от применения последнего.
В данной работе использовался реактор периодического действия, в котором кипящий слой образовывали измельченные частицы самой биомассы. Слой биомассы в реакторе переводился в псевдоожиженное состояние дымовыми газами от котла, в котором сжигалось биотопливо (гранулы из лузги подсолнечника). Дымовые газы поступали в нижнюю часть реактора с помощью дымососа (на рис. 1 не показан). Для генерации дымовых газов использовался жаротрубно-дымогарный водогрейный котел мощностью 500 кВт, оборудованный топкой для сжигания гранул из лузги подсолнечника в кипящем слое.
Выходящие из реактора газы содержали конденсирующиеся и неконденсирующиеся газообразные продукты торрефикации биомассы. Эти газы охлаждались в теплообменнике водой, циркулирующей с помощью насоса (на рис. 1 не показан) между теплообменником и баком – аккумулятором воды. Образующийся конденсат удалялся из системы. Затем неконденсирующиеся газообразные продукты торрефикации механически очищались в циклоне и выбрасывались в атмосферу.
Перед началом экспериментов установка продувалась дымовыми газами, которые охлаждались в теплообменнике и после удаления из них влаги подвергались химическому анализу с помощью газоанализатора проточного типа Vario Plus Industrial (погрешность показаний составляет 5–10% измеренного значения в зависимости от задействованного электрохимического сенсора).
Характеристики исследованных видов биомассы представлены в табл. 1.
Таблица 1.
Характеристика исследованных видов биомассы
Характеристика биомассы | Лузга подсолнечника | Древесные опилки | Куриный помет |
---|---|---|---|
Доля частиц размером, %: | |||
менее 0.09 мм | 0 | 1.83 | 3.76 |
0.09–0.20 мм | 2.40 | 20.88 | 7.50 |
0.2–0.4 мм | 9.72 | 47.60 | 16.19 |
0.4–1.0 мм | 50.54 | 26.02 | 37.62 |
1.0–2.0 мм | 30.84 | 3.04 | 33.13 |
2.0–5.0 мм | 30.84 | 0.35 | 1.80 |
более 5.0 мм | 0.02 | 0.29 | 0 |
Влажность, % | 10.60 | 19.00 | 6.00 |
Масса измельченных частиц лузги подсолнечника, помета и древесных опилок до и после торрефикации измерялась с помощью лабораторных весов Acom JW-1-200 RS 232 C (максимальная масса – 200 г, минимальная – 0.2 г, дискретность – 0.01 г). Влажность лузги определялась анализатором влажности Ohaus MB45 (погрешность ±0.05%).
Для определения доли летучих веществ проводили термогравиметрический анализ (ТГА) с использованием термоанализатора NETSCH STA 409 PC/PG (чувствительность 0.002 мг). Зольность измеряли путем выжигания образца в муфельной печи при температуре 600°С до выхода на постоянную массу. Перед определением зольности, содержания летучих веществ и элементного состава образцы высушивали до относительной влажности 0.1%.
Анализ элементного состава (C, H, N, S) исследуемой биомассы до и после термической обработки осуществлялся на анализаторе Elementar Vario Macro Cube (погрешность 0.1%). Содержание кислорода CO, % по массе в пересчете на сухое вещество определяли, исходя из следующего материального баланса:
После первых экспериментов по окислительной торрефикации биомассы выяснилось, что колпачок газораспределительной решетки, расположенной в нижней части реактора, забивается плотными отложениями, которые представляют собой сконденсировавшиеся серосодержащие вещества, выделившиеся из газообразных продуктов сжигания гранул лузги подсолнечника. Проблему удалось решить путем изменения конструкции колпачка.
Исследуемая биомасса представляла собой полидисперсную смесь частиц сложной геометрической формы. Для более детального изучения процесса их псевдоожижения была создана установка, основным элементом которой был реактор диаметром 108 мм (внутренним диаметром 100 мм) и высотой 2000 мм. Стенки реактора были выполнены из акрилового стекла. Процесс псевдоожижения в реакторе осуществлялся воздухом при комнатной температуре.
Установка дала возможность определить диапазон скоростей воздуха, при которых слой частиц биомассы находится в состоянии устойчивого псевдоожижения. При исследовании процесса замена дымовых газов с t = 200°С на воздух с t = 20°С вполне оправдана, так как, согласно [17], соотношение между числами псевдоожижения при 20 и 200°С можно оценить по значению корня квадратного из отношения плотностей газов при соответствующих температурах. Это соотношение для плотностей воздуха и дымовых газов при указанной температуре равно 1.23. Таким образом, можно заключить, что псевдоожижение воздухом и дымовыми газами в данном случае происходит при примерно одинаковых числах псевдоожижения. Результаты наблюдений приведены в табл. 2–4.
Таблица 2.
Результаты наблюдений за переходом в псевдоожиженное состояние слоя частиц измельченной лузги подсолнечника
Состояние слоя частиц биомассы по результатам визуальных наблюдений | Масса материала, загруженного в реактор, г | Высота слоя биомассы в реакторе, мм | Перепад давления в слое, Па | Скорость воздуха, отнесенная к поперечному сечению пустого реактора, м/с | |
---|---|---|---|---|---|
неподвиж-ного | в состоянии псевдоожи-жения | ||||
Начало псевдоожижения | 218 | 100 | 220 | 226 | 0.75 |
Развитое псевдоожижение | 218 | 100 | 350 | 220 | 0.92 |
327 | 160 | 370 | 360 | 0.80 | |
436 | 220 | 610 | 490 | 0.81 | |
763 | 370 | 900 | 940 | 1.40 | |
Поршнеобразование | 545 | 270 | 420 | 630 | 0.80 |
654 | 320 | 630 | 750 | 0.75 | |
872 | 420 | 690 | 1030 | 1.14 |
Таблица 3.
Результаты наблюдений за переходом в псевдоожиженное состояние слоя частиц измельченного помета
Состояние слоя частиц биомассы по результатам визуальных наблюдений | Масса материала, загруженного в реактор, г | Высота слоя биомассы в реакторе, мм | Перепад давления в слое, Па | Скорость воздуха, отнесенная к поперечному сечению пустого реактора, м/с | |
---|---|---|---|---|---|
неподвиж-ного | в состоянии псевдоожи-жения | ||||
Развитое псевдоожижение | 270 | 100 | 160 | 290 | 0.57 |
405 | 160 | 200 | 420 | 0.42 | |
540 | 215 | 300 | 580 | 0.62 | |
675 | 255 | 400 | 780 | 0.62 | |
Поршнеобразование | 810 | 300 | 600 | 950 | 1.40 |
945 | 350 | 500 | 1080 | 0.65 | |
Нестабильное псевдоожижение | 1080 | 450 | 600 | 1270 | 0.60 |
Таблица 4.
Результаты наблюдений за переходом в псевдоожиженное состояние слоя древесных опилок
Состояние слоя частиц биомассы по результатам визуальных наблюдений | Масса материала, загруженного в реактор, г | Высота слоя биомассы в реакторе, мм | Перепад давления в слое, Па | Скорость воздуха, отнесенная к поперечному сечению пустого реактора, м/с | |
---|---|---|---|---|---|
неподвиж-ного | в состоянии псевдоожи-жения | ||||
Стабильное псевдоожижение | 200 | 160 | 330 | 210 | 0.65 |
200 | 170 | 350 | 216 | 0.80 | |
310 | 180 | 400 | 287 | 0.87 | |
Начало поршнеобразования | 413 | 250 | 530 | 330 | 0.95 |
Поршнеобразование | 512 | 320 | 690 | 480 | 1.05 |
630 | 420 | 976 | 570 | 1.15 | |
715 | 520 | 1350 | 660 | 1.27 |
Анализ этих данных показал, что мелкодисперсные частицы биомассы, имеющие малую массу и сложную форму, стабильно псевдоожижаются в довольно узких диапазонах значений отношения начальной высоты слоя к диаметру реактора и скоростей газа. По этой причине в экспериментах по торрефикации высота неподвижного слоя частиц биомассы в реакторе составляла 100–170 мм, а скорость газа, отнесенная к сечению пустого реактора для торрефикации, – от 0.67 до 0.85 м/с при комнатной температуре.
Согласно данным, представленным в табл. 2–4, при поддержании скорости газа в диапазоне 0.67–0.85 м/с кипящий слой для всех трех видов биомассы (лузги подсолнечника, измельченного помета, древесных опилок) находится в состоянии стабильного псевдоожижения. Поэтому в экспериментах по торрефикации скорость газа поддерживалась именно в этом диапазоне. При более высоких скоростях газа псевдоожижение частиц того или иного вида биомассы становилось нестабильным. Поскольку скорость газа в слое может оказывать влияние на скорость торрефикации, для исключения влияния этого параметра было решено при псевдоожижении частиц всех трех видов биомассы поддерживать скорость газа в слое одинаковой.
Температура теплоносителя, подаваемого в “рубашку” реактора, составляла 250°C, а температура дымовых газов, направляемых в реактор, – 200°С. Дымовые газы в кипящем слое содержали примерно 8.5% паров воды и имели следующий химический состав, % (по объему):
Кислород .......................................................2–3 | |
Диоксид углерода .................................16.0–17.3 | |
Азот ..................................................................70 | |
Оксид углерода ....................................0.75–1.25 |
Высокое содержание оксида углерода объясняется тем, что подачу дутьевого воздуха в котел ограничивали, чтобы снизить концентрацию кислорода в дымовых газах и исключить воспламенение биотоплива при торрефикации. Однако по выбросам оксида углерода работа котла соответствовала требованиям ГОСТ 30735-2001 [18], который устанавливает максимальное значение выбросов CO 24 000 мг/м3 (в данной работе с учетом коэффициента разбавления 1.17, рассчитываемого как отношение массы растворенного вещества к массе растворителя, максимальная концентрация CO не превышала 14 625 мг/м3).
В рассматриваемом диапазоне температур диоксид углерода не взаимодействует с углеродом и поэтому наличие в дымовых газах CO2 не должно было оказывать влияния на интенсивность процесса торрефикации.
Биомасса в реакторе выдерживалась в течение заданного времени, после чего термообработанные образцы выгружались в герметично закрываемую емкость для последующего анализа. Время нахождения биомассы в реакторе менялось и составляло 3, 5, 10 и 15 мин.
В ходе экспериментов непрерывно определялись температура кипящего слоя и перепад давления в нем с учетом сопротивления газораспределительной решетки (измерение проводилось с использованием дифференциального микроманометра Testo 521 с погрешностью ±0.4%).
Что касается газообразных продуктов, то газоанализатор Vario Plus Indusrial опционально имеет возможность определять состав измеряемой среды температурой до 1700°С. Однако при торрефикации в газообразных продуктах может содержаться большое количество влаги, поэтому дымовые газы перед газоанализатором охлаждались в кожухотрубном теплообменнике в течение примерно 2 с до температуры ниже 100°С, что позволяло удалять из них влагу и обеспечивало стабильную работу газоанализатора. Из объема данных, выдаваемых газоанализатором, в дальнейшем анализе процесса торрефикации использовались только те, что свидетельствовали об изменении концентрации оксида углерода.
РЕЗУЛЬТАТЫ И ИХ ОБСУЖДЕНИЕ
На рис. 2 показано изменение во времени τ температуры кипящего слоя помета, лузги и опилок в процессе торрефикации. Термопара, измеряющая температуру кипящего слоя, была установлена на несколько миллиметров выше слоя неподвижных частиц биомассы. При переходе в псевдоожиженное состояние слой относительно сухих частиц куриного помета быстро прогревается и термопара фиксирует монотонный рост температуры до t = 235°С – некоего среднего значения между температурами псевдоожижающего газа и горячего жидкого теплоносителя (см. рис. 2, а).
Рис. 2.
Изменение во времени температуры кипящего слоя частиц биомассы. Биомасса: а – помет; б – лузга подсолнечника; в – опилки в процессе торрефикации

Для более влажных частиц лузги переход слоя в псевдоожиженное состояние и его прогрев сопровождаются подсушиванием частиц и температура слоя остается постоянной в течение τ = 3.5 мин, а затем начинается ее быстрый рост до t = 350°С (см. рис. 2, б).
Для еще более влажных частиц опилок псевдоожиженное состояние влечет за собой обильное выделение паров воды. Температура слоя при этом падает и только через τ = 1.5 мин после начала процесса начинает расти и достигает 220°С (см. рис. 2, в).
Как известно из [19–24], при нагреве биомассы возникают экзотермические реакции, в результате которых происходит разрушение входящих в состав биомассы гемицеллюлозы, целлюлозы и лигнина. Применительно к древесине эти реакции протекают в температурном диапазоне 200–500°С, но максимальное количество теплоты выделяется при 370°С [19], при температуре 230°С оно составляет от 425 до 1113 кДж/кг, при 250°С – от 22 до 1375 кДж/кг, а при 280°С – от 1160 до 1516 кДж/кг [25].
Поскольку в данной работе процесс торрефикации осуществлялся при температуре до 250°С, то заметный экзотермический эффект не наблюдался, что и подтверждает график изменения температуры кипящего слоя древесных частиц (см. рис. 2, в).
В представленных экспериментах использовались сосновые опилки, которые содержат 42–43% целлюлозы, 29–30% лигнина и 18–25% гемицеллюлозы [26].
Лузга подсолнечника содержит 23% целлюлозы, 18% гемицеллюлозы и 29% лигнина [24], т.е. по содержанию указанных веществ лузга подсолнечника близка к сосновым опилкам. Однако, как это видно из рис. 2, б, при торрефикации лузги подсолнечника наблюдается заметный экзотермический эффект, который позволяет слою частиц нагреваться до температуры, превышающей температуру ожижающего агента на 150°С, а жидкого теплоносителя – на 100°С. Можно предположить, что этот эффект обеспечивают эфирные масла, которые выделяются из частиц лузги при нагреве.
В куриный помет лигнин, целлюлоза и гемицеллюлоза могут попасть с кормом или при смешивании его с подстилкой (древесными опилками либо измельченной соломой). Поэтому содержание этих веществ в нем намного меньше, чем в древесных опилках или в лузге подсолнечника. Так, куриный помет содержит всего 3.4% лигнина [27], поэтому экзотермический эффект при его торрефикации не наблюдается, что подтверждается данными, приведенными на рис. 2, а.
Анализ графиков изменения во времени τ концентрации CO в газообразных продуктах торрефикации (рис. 3) и изменения перепада давления (рис. 4) в слое торрефицируемых частиц биомассы показывает, что данный процесс происходит в две стадии. После начала процесса торрефикации в течениие 2 мин для слоя древесных опилок (см. рис. 3, а), частиц лузги подсолнечника (см. рис. 3, б) и помета (см. рис. 3, в) наблюдается резкое падение концентрации оксида углерода в газообразных продуктах. Это может быть связано с доокислением СО до СО2 при температурах менее 200°С. Затем концентрация СО начинает расти и превышает концентрацию оксида углерода в дымовых газах, подаваемых на псевдоожижение. Повышение содержания CO связано с процессами деструкции биомассы, приводящими к разрыву химических связей в макромолекулах и выходу летучих веществ при прогреве материала в процессе окислительной торрефикации.
Рис. 3.
Изменение во времени концентрации оксида углерода в неконденсирующихся газообразных продуктах в процессе окислительной торрефикации. Биомасса: а – опилки; б – лузга подсолнечника; в – помет в кипящем слое
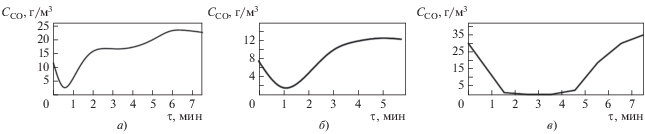
Рис. 4.
Изменение во времени перепада давления в слое частиц при окислительной торрефикации. Биомасса: а – лузга подсолнечника; б – опилки; в – помет

Торрефикация биомассы сопровождается выделением влаги и части летучих веществ, что вызывает потерю массы обрабатываемой частицы. Эту потерю можно оценить по изменению перепада давления в кипящем слое частиц биомассы, подвергаемых торрефикации. Завершение процесса происходит при неизменном значении перепада давления.
Исходя из этих соображений, можно предположить, что торрефикация завершается, когда перепад давления в слое перестает меняться. Для опилок данный процесс прекращается примерно через 1.5–2 мин (см. рис. 4, а), для частиц лузги – в основном через 7 мин (см. рис. 4, б), а для помета – через 9 мин (см. рис. 4, в) после начала опыта.
По изменению перепада давления в кипящем слое можно оценить степень завершенности процесса торрефикации биомассы. Этот факт подтверждается анализом данных, представленных в табл. 5, в которой отражены результаты измерения влажности, зольности и теплоты сгорания образцов исходной биомассы трех видов и извлеченного из них биоугля.
Таблица 5.
Результаты анализа влажности, зольности и теплоты сгорания образцов исходной биомассы (лузга подсолнечника/помет/древесные опилки) и продуктов их торрефикации
Показатель | Биомасса | |||
---|---|---|---|---|
исходная | торрефицированная | |||
Время, прошедшее с начала процесса, мин | – | 3 | 5 | 10 |
Влажность, % | 10.6/12.0/8.0 | 9.3/11.3/7.4 | 3.2/11.1/7.0 | 3.0/7.2/6.8 |
Зольность (при 550°С), % | 3.7/16.6/0.5 | 4.9/17.8/0.54 | 6.1/18.1/0.6 | 6.6/28.9/0.6 |
Низшая теплота сгорания, МДж/кг | 16.0/16.7/22.3 | 18.4/17.7/24.1 | 20.7/18.2/24.7 | 20.9/18.7/24.9 |
Характеристики исследованных образцов твердых продуктов торрефикации близки к характеристикам подобных образцов, полученных в плотном, плотном движущемся и плотном перемешиваемом слоях. Так, в работе [28] описывается твердый продукт торрефикации гранул из лузги подсолнечника, который имел следующие характеристики:
Влажность, % .................................................6.7 |
Зольность, % ..................................................6.1 |
Низшая теплота сгорания, МДж/кг ............20.7 |
Данный продукт был получен в плотном, движущемся сверху вниз слое гранул при торрефикации в течение 45 мин, но его характеристики близки к характеристикам полученного авторами данной статьи твердого продукта торрефикации из лузги подсолнечника.
В работе [29] при торрефикации древесных опилок (зольность исходного вещества – 1.3%, влажность – 7.72%) в среде азота были определены значения высшей теплоты сгорания при различных временах выдержки в реакторе с кипящим слоем и температурах процесса (табл. 6).
Таблица 6.
Высшая теплота сгорания биомассы (древесные опилки), МДж/кг, при различных временах выдержки в реакторе с кипящим слоем и температурах процесса
Температура процесса, °C | Время выдержки | |
---|---|---|
30 мин | 60 мин | |
200 | 17.66 | 21.30 |
300 | 18.39 | 24.07 |
При торрефикации помета в бескислородной среде высшая теплота сгорания повышается с 17.03 до 19.07 МДж/кг (при протекании процесса в течение 60 мин при 220°С [30]).
ВЫВОДЫ
1. Окислительная торрефикация различных видов биомассы в кипящем слое, сформированном частицами самой измельченной биомассы и продуваемом дымовыми газами с низким содержанием кислорода, представляется возможной. Однако с учетом сложной формы частиц и низкой насыпной плотности биомассы стабильное псевдоожижение может осуществляться в довольно узком диапазоне значений скоростей газа.
2. При окислительной торрефикации лузги подсолнечника наблюдается экзотермический эффект, связанный с выделением эфирных масел и их неполным сгоранием. При торрефикации древесных опилок и куриного помета данная особенность либо отсутствует, либо проявляется очень слабо.
3. Окислительная торрефикация в кипящем слое в среде дымовых газов позволяет осуществить процесс за 2–10 мин и получить при этом твердый продукт, по характеристикам сопоставимый с продуктом торрефикации, получаемым в плотном движущемся слое.
4. Продолжительность окислительной торрефикации в кипящем слое можно контролировать изменением перепада давления в слое: прекращение его снижения свидетельствует о завершении процесса. Это утверждение относится, однако, к реакторам периодического действия.
Список литературы
An assessment of the torrefaction of North American pine and life cycle greenhouse gas emissions / P. McNamee, P.W.R. Adams, M.C. McManus, B. Dooley, L.I. Darvell, A. Williams, J.M. Jones // Energy Convers. Manage. 2016. V. 113. P. 177–188. https://doi.org/10.1016/j.enconman.2016.01.006
A comparative study of biomass pellet and biomass-sludge mixed pellet: energy input and pellet properties / L. Jiang, X. Yuan, Z. Xiao, J. Liang, H. Li, L. Cao, H. Wang, X. Chen, G. Zeng // Energy Convers. Manage. 2016. V. 126. P. 509–515. https://doi.org/10.1016/j.enconman.2016.08.035
Lignocellulosic biomass pyrolysis mechanism: A state-of-the-art review / S. Wang, G. Dai, H. Yang, Z. Luo // Prog. Energy Combust. Sci. 2017. V. 62. P. 33–86. https://doi.org/10.1016/j.pecs.2017.05.004
Pelletization of torrefied sawdust and properties of torrefied pellets / H. Li, X. Liu, R. Legros, X.T. Bi, C.J. Lim, S. Sokhansanj // Appl. Energy. 2012. V. 93. P. 680–385. https://doi.org/10.1016/j.apenergy.2012.01.002
Biomass torrefaction process review and moving bed torrefaction system model development / J.S. Tumuluru, S. Sokhansanj, T.W. Christopher, D.B. Richard. Idaho National Laboratory, 2010. https://doi.org/10.2172/1042391
Chen W.-H., Peng J., Bi X.T. A state-of-the-art review of biomass torrefaction, densification and applications // Renewable Sustainable Energy Rev. 2015. V. 44. P. 847–866. https://doi.org/10.1016/j.rser.2014.12.039
A review of torrefaction of oil palm solid wastes for biofuel production / M.A. Sukiran, F. Abnisa, W.M.A. Wan Daud, N. Abu Bakar, S.K. Loh // Energy Convers. Manage. 2017 V. 149. P. 101–120. https://doi.org/10.1016/j.enconman.2017.07.011
Investigation of biomass torrefaction based on three major components: hemicellulose, cellulose, and lignin / D. Chen, A. Gao, K. Cen, J. Zhang, X. Cao, Z. Ma // Energy Convers. Manage. 2018. V. 169. P. 228–237. https://doi.org/10.1016/j.enconman.2018.05.063
Effect of torrefaction pretreatment and catalytic pyrolysis on the pyrolysis poly-generation of pine wood / D. Chen, Y. Li, M. Deng, J. Wang, M. Chen, B. Yan, Q. Yuan // Bioresour. Technol. 2016. V. 214. P. 615–622. https://doi.org/10.1016/j.biortech.2016.04.058
Combined pretreatment with torrefaction and washing using torrefaction liquid products to yield upgraded biomass and pyrolysis products / D. Chen, J. Mei, H. Li, Y. Li, M. Lu, T. Ma, Z. Ma // Bioresour. Technol. 2017. V. 228. P. 62–68. https://doi.org/10.1016/j.biortech.2016.12.088
Biomass torrefaction under different oxygen concentrations and its effect on the composition of the solid by-product / P. Rousset, L. Macedo, J.-M. Commandré, A. Moreira // J. Anal. Appl. Pyrolysis. 2012. V. 96. P. 86–91. https://doi.org/10.1016/j.jaap.2012.03.009
Non-oxidative and oxidative torrefaction characterization and SEM observations of fibrous and ligneous biomass / W.H. Chen, K.M. Lu, W.J. Lee, S.H. Liu, T.C. Lin // A-ppl. Energy. 2014. V. 114. P. 104–113. https://doi.org/10.1016/j.apenergy.2013.09.045
Torrefaction and low-temperature carbonization of woody biomass: evaluation of fuel characteristics of the products / S.W. Park, C.H. Jang, K.R. Baek, J.K. Yang // Energy. 2012. V. 45. P. 676–685. https://doi.org/10.1016/j.energy.2012.07.024
Torrefaction and low temperature carbonization of oil palm fiber and eucalyptus in nitrogen and air atmospheres / K.M. Lu, W.J. Lee, W.H. Chen, S.H. Liu, T.C. Lin // Bioresour. Technol. 2012. V. 123. P. 98–105. https://doi.org/10.1016/j.biortech.2012.07.096
Oxidative torrefaction of spruce-pine-fir sawdust in a slot-rectangular spouted bed reactor / Z. Wang, H. Li, C.J. Lim, J.R. Grace // Energy Convers. Manage. 2018. V. 174. P. 276–287. https://doi.org/10.1016/j.enconman.2018.08.035
Wang Z. Biomass torrefaction in slot-rectangular spouted beds: Dis. for the degree of doctor of philosophy (chemical and biological engineering). Vancouver: University of British Columbia, 2017. https://doi.org/10.14288/1.0362042
Забродский С.С. Высокотемпературные установки с псевдоожиженным слоем. М.: Энергия, 1971.
ГОСТ 30735-2001. Котлы отопительные водогрейные теплопроизводительностью от 0.1 до 4.0 МВт. Общие технические условия. Бишкек: Межгосударственный Совет по стандартизации, метрологии и сертификации, 2001.
Крылова А.Ю., Горлов Е.Г., Шумовский А.В. Получение биоугля пиролизом биомассы // Химия твердого топлива. 2019. № 6. С. 55–64. https://doi.org/10.1134/S0023117719060100
Соколовская Ю.Г., Фалюшин П.Л. Пиролиз отходов мебельного производства // Природопользование. 2011. № 20. С. 143–146.
Characteristics of hemicellulose, cellulose and lignin pyrolysis / H. Yang, R. Yan, H. Chen, D. Lee, C. Zheng // Fuel. 2007. V. 86. P. 1781–1788. https://doi.org/10.1016/j.fuel.2006.12.013
Influence of secondary reactions on the heat of pyrolysis of biomass / C. Gomez, E. Velo, F. Barontini, V. Cozzani // Ind. Eng. Chem. Res. 2009. V. 48. Is. 23. P. 10222–10233. https://doi.org/10.1021/ie9007985
Milosavljevic I., Oja V., Suuberg E.M. Thermal effects in cellulose pyrolysis: relationship to char formation processes // Ind. Eng. Chem. Res. 1996. V. 35. Is. 3. P. 653–662. https://doi.org/10.1021/ie950438l
Ohliger A., Förster M., Kneer R. Torrefaction of beechwood: A parametric study including heat of reaction and grindability // Fuel. 2013. V. 104. P. 607–613. https://doi.org/10.1016/j.fuel.2012.06.112
Shevchenko A.L., Sytchev G.A., Zaichenko V.M. Possibility of the use of exothermic-reactions heat from thermal destruction of biomass to increase the energy efficiency of the torrefaction process // J. Phys.: Conf. Ser. 2019. V. 1147. P. 012093. https://doi.org/10.1088/1742-6596/1147/1/012093
Синицин А.П., Синицина О.А. Биоконверсия возобновляемой растительной биомассы на примере биотоплива второго поколения: предобработка, ферменты, процессы, экономика, поколения // Успехи биол. химии. 2021. Т. 61. С. 347–414.
Корзникова М.В., Блохин А.Ю., Козлов Ю.П. Оценка степени конверсии органического вещества отходов животноводства и птицеводства в биогаз (на примере РФ) // Вестник ВГУ. Сер.: Химия. Биология. Фармация. 2008. № 2. С. 108–111.
Applicability of torrefied sunflower husk hellets in small and medium scale furnaces / N. Kienz, N. Margaritis, R. Isemin, V. Zaychenko, C. Strasser, D.-S. Kourkoumpas, P. Grammelis, D. Klimov, O. Larina, S. Sytc-hev, A. Mikhalev // Waste Biomass Valorization. 2021. V. 12. P. 2579–2596. https://doi.org/10.1007/s12649-020-01170-7
Product characteristics of torrefied wood sawdust in normal and vacuum environments / Y.-K. Chih, W.-H. Chen, H.C. Ong, P.L. Show // Energies. 2019. V. 12. Is.20/3844. https://doi.org/10.3390/en12203844
Pudova Ya.D., Larina O.M., Zaichenko V.M. Effect of temperature process at chicken litter torrefaction on properties of products obtained: Report on the XXXIV Intern. Conf. on Interaction of Intense Energy Fluxes with Matter. Elbrus, Kabardino-Balkaria, Russian Federation, 1–6 March 2019 // J. Phys.: Conf. Ser. 2019. V. 1556. https://doi.org/10.1088/1742-6596/1556/1/012020
Дополнительные материалы отсутствуют.
Инструменты
Теплоэнергетика