Теплоэнергетика, 2022, № 10, стр. 64-70
Мониторинг технического состояния котлов-утилизаторов как основа для разработки технологического регламента их эксплуатации
Ю. А. Радин a, *, А. Э. Зелинский b, Т. С. Конторович a, **
a ПАО “Мосэнерго”
119526 Москва, просп. Вернадского, д. 101/3, Россия
b АО “Машиностроительный завод “ЗиО-Подольск””
142103 Московская обл., г. Подольск, Железнодорожная ул., д. 2, Россия
* E-mail: vti-unit@yandex.ru
** E-mail: kontorovich_ts@mail.ru
Поступила в редакцию 20.12.2021
После доработки 09.03.2022
Принята к публикации 23.03.2022
- EDN: PSJPGV
- DOI: 10.56304/S004036362210006X
Аннотация
Представлены результаты анализа эффективности использования непрерывного мониторинга технического состояния котлов-утилизаторов парогазовых установок (ПГУ) в целях оказания помощи персоналу тепловых электрических станций для корректного определения основных причин отклонений или нарушений режимов эксплуатации котлов-утилизаторов (КУ) и предупреждения возникновения в дальнейшем повреждений оборудования. Техническое состояние котлов-утилизаторов ПГУ оценивается по накопленной поврежденности при отклонении режима их эксплуатации от оптимального, которая количественно выражается через накопленные эквивалентные часы эксплуатации. Рассмотрены примеры влияния на поврежденность деталей КУ эффективности системы дренажей, в особенности с учетом повышенного риска появления повреждений в местах приварки дренажных линий к паропроводам и коллекторам. Показана необходимость использования на практике специальных программ технического обслуживания оборудования котлов-утилизаторов, для которых в качестве критерия оценки технического состояния предлагается анализ накопленных ими эквивалентных часов эксплуатации или эквивалентного количества пусков. Вместе с пусковыми режимами учитываются режимы изменений нагрузки в пределах регулировочного диапазона нагрузок, сопровождающихся изменением параметров пара, а также нерасчетные режимы, характеризующиеся большими возмущениями по температуре газов и пара, таких как сбросы нагрузки. Использование таких программ позволит в дальнейшем сократить затраты на регламентные работы при техническом обслуживании оборудования, а также своевременно обнаруживать его повреждения и предотвращать тем самым возникновение аварийных ситуаций.
Накопленные в течение длительного времени статистические данные обследований технического состояния котлов-утилизаторов парогазовых установок различной мощности позволили определить в качестве основных причин возникновения повреждений в деталях их оборудования все виды коррозии и термическую усталость, кроме дефектов, допущенных при проектировании, изготовлении и монтаже оборудования [1, 2]. При этом если расчет на термическую усталость является обязательным для оценки циклической прочности, то увеличение напряжений в процессе эксплуатации вследствие утонения стенок коллекторов и паропроводов в результате коррозии во внимание не принимается. В данной работе предпринимается попытка учесть этот фактор.
ВИДЫ КОРРОЗИИ ЭЛЕМЕНТОВ КОТЛОВ-УТИЛИЗАТОРОВ
Один из характерных видов коррозии – коррозия под воздействием скоростного потока теплоносителя. Она проявляется преимущественно в экономайзерах и испарителях низкого давления котлов-утилизаторов всех видов, увеличивая риск возникновения в них повреждений, проявляющихся при температурах теплоносителя 140–170°С, характерных для контуров низкого давления [3].
Важной причиной возникновения повреждений также является коррозия под отложениями испарительных труб низкого и высокого давления [2]. В этом случае часть реагентов, недоиспользованных при коррекционной обработке воды, может концентрироваться внутри отложений, что ускоряет процесс коррозии.
Значительное влияние на интенсивность коррозии оказывает исходная загрязненность теплообменных труб, определяемая, как правило, путем анализа вырезок или визуальным контролем их внутренних поверхностей (например, бороскопированием). В этом случае критерием коррозии является загрязненность, устанавливаемая по количеству отложений, отнесенному к 1 м2 площади внутренней поверхности трубы, которое не должно превышать 70 г/м2 при использовании аммиачной обработки [4]. Места вырезки образцов труб, соответствующие зонам максимальных термических напряжений, должны выявляться для каждого КУ по результатам теплотехнических испытаний и расчетов.
Питтинг как вид коррозии может возникнуть в трубной системе любого контура КУ вследствие нарушения режима эксплуатации и почти во всех случаях при отсутствии мероприятий по коррекции водно-химического режима и консервации КУ при остановах в резерв. В котлах-утилизаторах встречаются повреждения испарителей и пароперегревателей высокого давления от стояночной коррозии и значительно реже от водородного охрупчивания [2].
Основным показателем интенсивности коррозии является ее скорость V, г/(м2 · ч), определяемая по выражению
где Δm – убыль (увеличение) массы материала; S – площадь поверхности; τ – время.ПРИЧИНЫ ПОВРЕЖДЕНИЯ ДЕТАЛЕЙ КОТЛА-УТИЛИЗАТОРА
Дренажи пароперегревателей (высокого) ВД и (среднего) СД давления КУ зачастую не обеспечивают удаление всего конденсата, образующегося при прогреве пароперегревателей во время пуска. Пароперегреватели подвержены воздействию циклически меняющихся значительных температурных напряжений, которые с учетом конструктивных концентраторов напряжений от сварных швов в зоне соединения паропроводов с дренажными линиями увеличивают риск возникновения повреждений толстостенных коллекторов от термоусталостных явлений. При применении в некоторых случаях дренажных линий большого диаметра (до 0.5–0.6 диаметра коллектора или паропровода) с датчиками температуры или уровня и регулирующими клапанами на отводе конденсата можно решить проблему, однако при этом увеличивается риск повреждений при некорректной работе регулирующего клапана.
Некоторое количество конденсата может образовываться в пароперегревателях во время предпусковой вентиляции газового тракта (рис. 1), в особенности при пусках с отрицательными температурами наружного воздуха.
Рис. 1.
Изменение показателей металла ПГУ во времени при пуске КУ с вентиляцией газового тракта. 1 – активная мощность генератора Р; 2 – частота вращения ротора газовой турбины n; температура металла t: 3 – в выходной камере перегревателя; 4, 5 – трубопровода пара ВД КУ со стороны паровой турбины; 6–8 – паропровода ВД со стороны КУ (6 – низ, 7 – верх); 9 – давление р пара ВД на выходе из КУ; 10 – температура насыщения пара ВД
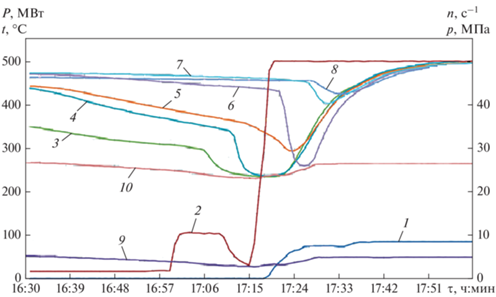
При всех пусках КУ в период между зажиганием в камере сгорания и установлением первоначального расхода пара из КУ на начальной нагрузке газотурбинной установки (ГТУ) трубы пароперегревателя нагреваются до температуры, близкой к температуре выхлопных газов. Конденсат при этом будет мигрировать через трубы выборочно, охлаждая их вследствие значительных теплогидравлических разверок. Температурное сжатие этих труб по отношению к еще горячим соседним трубам пакета приводит к большим напряжениям в гибах, соединениях труб с коллектором с последующими термоусталостными повреждениями.
При пусках с первоначальным высоким сохранившимся давлением клапаны дренажей не могут быть оставлены открытыми без риска снижения давления пара ВД, а применение термопар в дренажных трубопроводах бесполезно на этапах, когда конденсат и пар близки к состоянию насыщения при текущем давлении пара в трубопроводе.
Во время пусков после коротких простоев при выпаривании конденсат, находящийся в коллекторах, охлаждает их нижнюю часть, что вызывает возникновение в ней напряжений сжатия [3, 5, 6]. Конденсат, не способный достичь дренажа, располагается в центре коллектора и при появлении и нарастании потока пара будет мигрировать по соседним трубам, приводя в конечном итоге к их деформации.
Надежность высокотемпературных элементов КУ во многом определяется зависимостью температуры газов на входе в котел от мощности ГТУ. В частности, для КУ, которые эксплуатируются с газовыми турбинами классов F и Н фирмы General Electric (GE), требуются высокоэффективные пароохладители КУ, расположенные перед выходными пакетами пароперегревателя ВД и промежуточного перегрева пара. Это вызвано уникальной зависимостью температуры выхлопных газов ГТУ фирмы GЕ от мощности ГТУ (рис. 2) [6].
При мощности ГТУ около 35–40 МВт температура выхлопных газов превышает 500°С, а при нагружении ГТУ до 75 МВт быстро возрастает до 650°С, остается на этом уровне, пока мощность ГТУ не достигнет 160 МВт, и плавно снижается до номинальной (около 580°С) при дальнейшем нагружении.
Наиболее нагретые толстостенные коллекторы пароперегревателя ВД и промежуточного перегрева КУ требуют особого внимания во время пуска и останова, чтобы исключить их повреждение из-за больших скоростей прогрева/охлаждения [2]. Быстрое охлаждение толстостенных элементов, находящихся под давлением, вызывает накопление большего количества эквивалентных часов эксплуатации, нежели при нагреве.
При вращении ротора турбины с помощью валоповоротного устройства после ее останова температура воздуха после ГТУ быстро снижается до температуры наружного воздуха, что приводит при последующем пуске, в особенности после короткого по времени простоя, к глубокому расхолаживанию паропроводов (рис. 3).
Рис. 3.
Зависимость показателей ПГУ-450 при пуске из горячего состояния от времени. 1, 2 – температура металла нижней и верхней образующей паропровода; 3 – активная мощность генератора; 4 – частота вращения ротора газовой турбины; 5 – разность температур верхней и нижней образующих паропровода
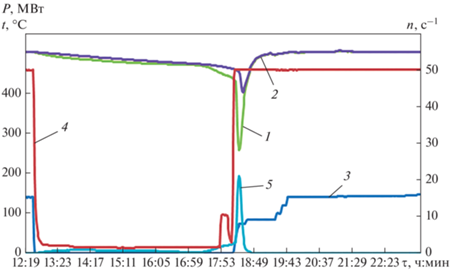
Термическая усталость – одна из важнейших причин повреждений высокотемпературных деталей котлов-утилизаторов, таких как пароперегреватели ВД и СД. Усталостные повреждения встречаются также в экономайзерах высокого и среднего давления, особенно в их входных коллекторах, в местах приварки дренажных линий к коллекторам и паропроводам ВД и горячего промежуточного перегрева, реже в барабанах высокого и среднего давления. Ползучесть оказывает влияние на долговечность деталей котлов-утилизаторов, работающих при температурах более 450°С, увеличивая риск появления повреждений независимо от циклического характера режимов эксплуатации [3].
ПРОФИЛАКТИЧЕСКИЕ РАБОТЫ НА КОТЛЕ-УТИЛИЗАТОРЕ
Профилактические работы имеют самостоятельное значение для получения информации о состоянии наружных и внутренних поверхностей КУ и его теплообменных труб. Для своевременного выполнения профилактических работ составляется график проведения инспекций КУ, совмещаемый по времени с аналогичными профилактическими процедурами на оборудовании ГТУ, основанный на анализе поврежденности высоконагруженных деталей котла и результатах расчетов эквивалентных часов эксплуатации на период времени между капитальными ремонтами. К таким профилактическим работам следует отнести химическую обработку поверхностей нагрева (дозирование реагентов при останове и в течение некоторого времени в процессе остывания в соответствии с рекомендациями [2, 6, 7], консервацию оборудования КУ при остановах на время большее 1 сут), ультразвуковой контроль толщины гибов теплообменных труб, в особенности испарителей, и др.
Актуальность задачи планирования технического обслуживания оборудования ПГУ заключается в том, что ее решение позволит увеличить продолжительность эксплуатации КУ до следующего капитального ремонта и снизить риск внеплановых остановов оборудования.
Профилактическое техническое обслуживание КУ включает в себя следующие процедуры.
Техническое обслуживание первого уровня состоит из таких мероприятий:
визуального осмотра газоходов КУ со стороны выходного диффузора ГТУ и в районе дождевой заслонки, барабанов, тепловой изоляции, компенсаторов и других элементов газового и пароводяного трактов;
бороскопирования теплообменных труб и коллекторов;
ультразвуковой толщинометрии гибов теплообменных труб, ближайших к выходному коллектору испарителей;
тестирования автоматических защит;
других работ по замечаниям персонала.
Продолжительность инспекции первого уровня с указанным объемом работ составляет до 7 рабочих дней (без учета продолжительности остывания), сроки проведения – 1 раз в 6–9 мес или при накоплении более 1000 эквивалентных часов (при среднем количестве пусков 15 за 9 мес с количеством эквивалентных часов за пуск 20 и примерно 700 эквивалентных часов путем разгрузок и сбросов нагрузки в течение контрольного периода времени). Останов КУ для выполнения инспекций следует выполнять с принудительным расхолаживанием.
Техническое обслуживание второго уровня включает в себя:
частичную замену наружной тепловой изоляции котла и паропроводов (при необходимости);
ревизию трубопроводной арматуры и регулирующих клапанов;
неразрушающий контроль всех приварных штуцеров барабанов котла; анализ вырезок теплообменных труб (наиболее повреждаемых поверхностей нагрева) и технического состояния оборудования питательных и циркуляционных насосов КУ;
наладку автоматических регуляторов питания, клапанов впрысков, непрерывных продувок;
необходимые замены деталей оборудования;
тестирование автоматических защит и дождевой заслонки;
гидравлические испытания;
отмывку КУ перед пуском и водно-химическую промывку в процессе пуска ГТУ.
Продолжительность инспекции – до 20 дней, периодичность проведения – каждые 1.0–1.5 года в зависимости от режимов эксплуатации КУ или по накопленным эквивалентным часам (2500–3000 экв. ч).
Обязательными являются тепловые испытания КУ в составе ПГУ после инспекций (ремонта), паспортизация тепловой изоляции и шумовых характеристик после пуска. Решение о проведении инспекции принимается по накопленным оборудованием эквивалентным часам из расчета, что период между капитальными ремонтами – не менее 5000 эквивалентных часов, с обязательным учетом необратимых изменений (деградации) характеристик оборудования.
Учет скорости коррозии при анализе напряженного состояния высоконагруженных толстостенных деталей оборудования котлов-утилизаторов можно выполнять с помощью увеличения напряжений в стенке, вызванного ее утонением вследствие коррозии и уноса материала.
Допускаемое число циклов N рассчитывается по амплитуде условно-упругих эквивалентных напряжений σeqv, которые, в свою очередь, представляют собой алгебраическую сумму напряжений от внутреннего давления σeqv(p) и перепада температур σeqv(t). Возрастание напряжений от внутреннего давления вследствие утонения стенки при коррозии учитывается с помощью коэффициента $K_{\sigma }^{p}$ (рис. 4).
Рис. 4.
Зависимость коэффициента увеличения напряжений от внутреннего давления для коллектора типоразмером 426 × 34 мм от времени и скорости коррозии. V, мкг/(см2 · ч): 1 – 10; 2 – 200; 3 – 1000
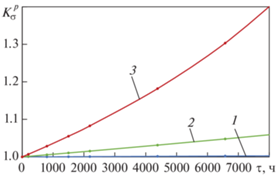
При вычислении эквивалентных часов эксплуатации КУ повреждаемость от коррозии должна учитываться при пусках после простоев ПГУ в резерве более 14 ч, когда происходит частичная расконсервация внутренних поверхностей оборудования паровой части, а реагенты теряют свои свойства образовывать защитные пленки. Тогда выражение для расчета эквивалентных часов Teqv эксплуатации КУ принимает следующий вид:
Этот показатель является основным при техническом обслуживании вспомогательного оборудования, для которого определяются:
суммарная длительность работы;
дата следующего профилактического обслуживания;
длительность непрерывной работы после последней по времени профилактической работы;
дата последнего переключения и число переключений (включений);
потребление энергии на собственные нужды;
теплотехнические характеристики (КПД, температура уходящих газов).
Согласно опубликованным в [1, 6, 8] результатам обследований зарубежных парогазовых установок различной мощности существующие программы технического обслуживания котельного оборудования не оптимальны. В них, как правило, отсутствуют критерии оценки технического состояния КУ, на основании которых определяются профилактические мероприятия (инспекции) того или иного вида. Ситуация усугубляется тем, что в большинстве случаев при контроле технического состояния газотурбинного оборудования (как правило, импортного) заказчик не имеет возможности оценивать принимаемые поставщиком решения.
Анализ возникновения повреждений во время эксплуатации должен проводиться еще на стадии проектирования КУ, должны предусматриваться рекомендации по их минимизации или исключению с учетом того, что при длительной (более 2 лет) эксплуатации дефекты в КУ проявляются, главным образом, вследствие недостаточного качества водно-химического режима и нарушений технологии эксплуатации [2]. Мероприятия, направленные на предупреждение возникновения повреждений, должны быть основаны на непрерывном мониторинге и диагностике состояния основного и вспомогательного оборудования.
Программа технического обслуживания должна опираться на результаты выполнения следующих ключевых мероприятий:
непрерывного анализа качества и параметров теплоносителя;
анализа продолжительности эксплуатации с отклонениями параметров от их допустимых значений;
ведения статистики переменных режимов и изменений параметров в этих режимах;
фиксации скорости изменения нагрузки, параметров и т.п.;
определения технико-экономических показателей при всех режимах и нагрузках в пределах регулировочного диапазона;
толщинометрии теплообменных труб и гибов, анализа вырезок или бороскопирования теплообменных труб и коллекторов;
анализа термонапряженного состояния толстостенных высокотемпературных деталей;
определения количества пусков/остановов, продолжительности простоев в резерве и ремонте;
анализа характеристик вспомогательного оборудования и основных причин для каждого из обнаруженных повреждений КУ;
металлографического анализа вырезок поврежденных участков;
разработки рекомендаций по устранению дефектов и коррекции технологии эксплуатации в связи с их возникновением;
ведения централизованной базы данных повреждаемости оборудования ПГУ, которая должна накапливаться централизованно.
ВЫВОДЫ
1. Мониторинг и диагностика технического состояния оборудования котлов-утилизаторов должны являться основой для составления программ технического обслуживания и регулярных обследований.
2. Обязательным является формирование централизованной базы данных о повреждениях оборудования, составляемой на основании всесторонней его диагностики с самого начала эксплуатации.
3. Программы технического обслуживания основного и вспомогательного оборудования должны базироваться на непрерывном подсчете эквивалентных часов эксплуатации с учетом количества пускоостановочных режимов, режимов глубоких разгрузок и сбросов нагрузки, отличающихся изменениями температуры.
4. Для подсчета эквивалентных часов эксплуатации предложено соотношение, учитывающее влияние коррозии на циклическую прочность детали.
Список литературы
Dooley B.R., Paterson S.R., Pearson J.M. HRSG Dependability // Power Plant Chem. 2003. V. 5. Is. 12. P. 727–732.
Богачев А.Ф., Радин Ю.А., Герасименко О.Б. Особенности эксплуатации и повреждаемость котлов-утилизаторов бинарных парогазовых установок. М.: Энергоатомиздат, 2008.
Anderson F., Jacson P., Moelling D. HRSG tube failure diagnostic guide. 2nd ed. Tetra Engineering Group Inc., 2004.
РД 34.37.403-91. Методические указания по эксплуатационной химической очистке котлов энергоблоков сверхкритического давления. М.: ОРГРЭС, 1991.
Радин Ю.А., Конторович Т.С. Использование принципа эквивалентной наработки для оценки надежности оборудования ПГУ // Электрические станции. 2012. № 1. С. 25–30.
Pasha A., Allen R. Design and modification of heat recovery steam generators for cycling operations. Louisville: Vogt-NEM Inc., 2003.
СО 153-34.20.501-2003. Правила технической эксплуатации электрических станций и сетей Российской Федерации. М.: Энергосервис, 2003.
Moelling D., Jackson P., Malloy J. Protecting steam cycle components during low-load operation of combined cycle gas turbine plants // Power. 2015. V. 159. Is. 3. P. 42–45.
Дополнительные материалы отсутствуют.
Инструменты
Теплоэнергетика