Теплоэнергетика, 2022, № 10, стр. 17-31
Экономические характеристики технологий улавливания и захоронения диоксида углерода (обзор)
С. П. Филиппов *
Институт энергетических исследований РАН
117186 Москва, Нагорная ул., д. 31/2, Россия
* E-mail: fil_sp@mail.ru
Поступила в редакцию 27.02.2022
После доработки 27.02.2022
Принята к публикации 23.03.2022
- EDN: DPHTLR
- DOI: 10.56304/S0040363622100022
Аннотация
Применение технологий улавливания и захоронения CO2 (carbon capture and storage – CCS) способно обеспечить достижение углеродной нейтральности при использовании органических топлив в больших масштабах. Выполненные исследования показали, что технологии CCS являются довольно энергозатратными и дорогостоящими. Прежде всего, это касается оборудования для улавливания CO2, на которое приходится 60–80% суммарных затрат на CCS. С уменьшением парциального давления CO2 в газовой смеси и производительности улавливающей установки затраты на выделение CO2 резко возрастают. В первую очередь это относится к тепловым электростанциям (ТЭС). При оснащении их системами очистки от CO2 удельные капитальные затраты увеличиваются в 1.6–2.3 раза, а стоимость производимой электроэнергии ‒ в 1.4–1.6 раза. На функционирование таких систем расходуется около 9–12% мощности электростанции, в некоторых технологиях ‒ до 20%. Удельные затраты на извлечение CO2 существенно возрастают при мощности электрогенерирующей установки менее 200 МВт. Формирование индустрии CCS потребует создания разветвленной трубопроводной системы для транспортирования больших объемов CO2, сопоставимой с газотранспортной системой. Это позволит расширить потенциал применения технологий CCS. Удельные затраты на транспортирование CO2 по трубопроводам определяются передаваемыми объемами и фазовым состоянием CO2. При увеличении объемов передачи CO2 от 0.1 до 5.0 млн т/год удельная стоимость транспортирования уменьшается почти на порядок. Затраты на захоронение CO2 в решающей степени зависят от характеристик геологического резервуара. Самым дешевым вариантом является захоронение CO2 в истощенные нефтегазовые месторождения на суше. Для создания технологической основы CCS требуется весомая государственная поддержка.
Конференция ООН по климату в Глазго в 2021 г. (COP-26) показала, что декарбонизация становится основным направлением развития мировой экономики и энергетики на обозримую перспективу [1]. Абсолютное большинство стран мира присоединилось к Парижскому соглашению по климату 2015 г. [2]. Наметился переход к практическому осуществлению его целей. Ширится круг стран, объявивших о стремлении достичь углеродной нейтральности к 2050–2060 гг. нынешнего века, т.е. через 30–40 лет. Это примерно соответствует одному инвестиционному циклу в энергетике.
По оценкам Международного энергетического агентства, для достижения глобальной углеродной нейтральности к 2050 г. требуются огромные инвестиции [3]. Уже к 2030 г. они должны достичь 5 трлн дол/год, что более чем в 2 раза превышает ежегодные вложения в мировую энергетику в период 2016–2020 гг. (в среднем около 2.3 трлн дол/год). Это соответствует 4.5% мирового ВВП. Потребности в инвестициях будут оставаться высокими и в последующие 20 лет. В 2050 г. они составят 4.5 трлн дол/год, или 2.5% возросшего к тому времени ВВП. Это означает, что при ожидаемых в среднем за этот период годовых темпах прироста глобального ВВП примерно 3% практически всю получаемую добавленную стоимость нужно будет направлять на цели декарбонизации. Следствием станет “заморозка” роста жизненного уровня населения. Это вполне приемлемо для развитых стран, где он высок, и едва ли станет возможным для развивающихся стран без соответствующих социальных потрясений.
Согласно данным Мирового валютного фонда, основными источниками финансирования мероприятий по декарбонизации экономики должны стать плата за выбросы CO2, государственные субсидии, направляемые в настоящее время на развитие энергетики на органических топливах, и, конечно же, средства бизнеса [4]. Осуществить декарбонизацию предполагается в возможно короткие сроки посредством выполнения политических решений и изменений в регуляторных механизмах. В частности, может быть запрещено банкам финансировать новые проекты по добыче органических топлив и сооружению тепловых электростанций. Плата за выбросы CO2 должна составить в 2030 г. в развитых странах 130 дол/т CO2, а в развивающихся, в том числе в Китае и России, 90 дол/т CO2. К 2050 г. ее следует увеличить соответственно до 250 и 200 дол/т CO2 [3]. Реализация данных предложений означает довольно быструю потерю традиционной энергетикой конкурентоспособности и резкое сокращение ее доли в мировом энергетическом балансе.
Среди имеющихся конкурирующих направлений в декарбонизации особого внимания заслуживают технологии улавливания и захоронения CO2 (carbon capture and storage – CCS). Это, по сути, единственное направление, обеспечивающее достижение углеродной нейтральности при сохранении использования органических топлив в энергетике на длительный период. Как показано в [5], имеющиеся на Земле ресурсы подземных геологических структур для захоронения CO2 огромны и не станут ограничивающим фактором для создания глобальной индустрии CCS. Крупномасштабное применение CCS позволит плавно перейти от энергетики на органическом топливе к безуглеродной энергетике, базирующейся на возобновляемых и ядерных источниках энергии. К настоящему времени в мире накоплен большой опыт разработки и реализации проектов CCS, и глобальная индустрия CCS уже сейчас может быть построена на основе промышленно освоенных технологий. В то же время продолжаются разработки большого числа новых технологий. Их главной целью является снижение затрат на CCS.
Данная работа посвящена анализу имеющихся и предлагаемых технологий CCS и их экономических показателей. Рассмотрены технологии выделения CO2 из газовых смесей, транспортирования CO2 на дальние расстояния и последующего надежного захоронения в подземных геологических структурах на длительную перспективу (столетия).
ТЕХНОЛОГИИ УЛАВЛИВАНИЯ CO2
В связи с наращиванием усилий по декарбонизации во всем мире активизировались работы по совершенствованию имеющихся технологий извлечения CO2 из газовых смесей и созданию новых. В частности, в сентябре 2020 г. Департамент энергетики США (US Department of Energy) выделил на эти цели 72 млн дол. [6]. Из них 51 млн дол. направлено на реализацию девяти проектов по извлечению CO2 из уходящих газов электростанций и промышленных печей. Ставится задача снизить стоимость извлечения CO2 на электростанциях с нынешних 60–70 до 40 дол/т CO2 при степени извлечения CO2 из дымовых газов не ниже 90% [7]. Это позволит продолжить использование органических топлив в стране в условиях декарбонизации. Еще 21 млн дол. направляется на 18 проектов по извлечению CO2 из атмосферы (direct air capture).
Затраты на извлечение CO2 из газовой смеси З в решающей мере зависят от его парциального давления ${{р}_{{{\text{С}}{{{\text{О}}}_{{\text{2}}}}}}}$ и производительности установки G (рис. 1). Со снижением парциального давления CO2 в газовой смеси затраты на выделение CO2 резко возрастают. В зоне низкого парциального давления (менее 10 кПа) затраты на выделение CO2 существенно зависят от производительности установки, в зоне высоких значений (свыше 40 кПа) это влияние становится несущественным. Рисунок 1 построен на основе данных из [8] применительно к традиционной технологии абсорбции CO2 из газовых потоков с использованием химического растворителя моноэтаноламина.
Рис. 1.
Зависимость удельных затрат на извлечение CO2 из газовой смеси от его парциального давления. G, Мт СО2/год: 1 – 2 и более; 2 – 0.2–0.3
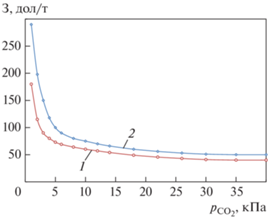
Крупнейшими источниками выбросов CO2 являются тепловые электростанции, котельные и промышленные печи, для которых характерно невысокое парциальное давление CO2 в уходящих газах. В парогазовых установках (ПГУ) на природном газе (natural gas combined cycle – NGCC) оно обычно равняется 4–5 кПа, в угольных паротурбинных установках (ПТУ) (coal steam turbine cycle – CSTC) ‒ примерно 12–14 кПа, в газотурбинных установках малой мощности ‒ менее 4 кПа. Для разных промышленных процессов характерны различные значения парциального давления CO2 в газовых смесях, кПа [8]:
Выплавка алюминия ...............................0.8–1.1 |
Производство железного агломерата ...............................................3.7–4.2 |
Производство цемента ..............................17–19 |
Выплавка стали .........................................24–28 |
Паровой риформинг метана ...............Более 300 |
Парокислородная газификация угля ................................Более 750 |
Имеются следующие возможности для увеличения парциального давления CO2 в газовой смеси:
применение окислителя без балластного азота, в частности, при сжигании топлива в среде кислорода (oxy-fuel combustion) и в химическом цикле (chemical looping combustion – CLC), газификация топлив кислородным или парокислородным дутьем;
в аллотермических процессах, т.е. при подводе тепловой энергии извне, которые нашли применение в промышленности, например при паровой конверсии метана;
повышение давления газовой смеси.
Для решения задач декарбонизации желательно обеспечить степень извлечения CO2 из газовых потоков не менее 90%. Однако известно, что с увеличением степени очистки затраты возрастают почти по экспоненте. Фундаментальная взаимосвязь между концентрацией вещества в смеси и стоимостью его удаления раскрыта в [9].
Технологии выделения CO2 из газовых смесей, предназначенные для крупномасштабного применения в индустрии CCS, базируются главным образом на абсорбции, адсорбции, мембранном разделении и конденсации. Эти методы давно используются в промышленности и сейчас стали привлекаться к решению задач декарбонизации. Достижения в разработке данных методов и основанных на них технологиях, их достоинства и недостатки подробно обсуждаются в обзоре [10]. Сравнение различных технологий улавливания CO2 представлено в ряде работ, например в [11].
Областью предпочтительного применения технологий абсорбции на основе химических реагентов (водных растворов аминов и др.) являются газовые смеси с невысоким парциальным давлением CO2, прежде всего дымовые газы электростанций. Регенерация реагентов обычно производится путем повышения их температуры, что требует дополнительных затрат тепловой энергии. Абсорбционные технологии на основе физических растворителей используются преимущественно для разделения газовых смесей с высоким парциальным давлением CO2, в частности, в химической промышленности [10]. Широкое применение получили процессы Selexol (на основе гликолей) и Rectisol (на базе метанола), в частности, для очистки продуктов газификации угля. Регенерация растворителей производится путем снижения их давления. Для повторного использования регенерированных растворителей необходимо затратить электрическую энергию на их сжатие. В отличие от технологий химической абсорбции, технологии физической абсорбции обычно характеризуются более низкой скоростью извлечения CO2. Следовательно, они более капиталоемкие. Но при этом на регенерацию растворителя требуется меньший расход энергии, а значит, меньшие эксплуатационные затраты [8].
При использовании классических химических абсорбентов (водных растворов аминов) степень извлечения CO2 из дымовых газов (при давлении CO2 10–15 кПа) достигает 90%. При этом типичное потребление тепловой энергии для регенерации реагентов составляет 3.6–4.0 ГДж/т извлеченного CO2 [10]. При развитии абсорбционных технологий ставится задача создать долговечные, недорогие, не коррозионно-активные растворители и снизить энергоемкости процессов [12]. Тестируются разнообразные абсорбенты нового поколения (на основе безводных смесей аминов, пиперазина, ионных жидкостей и т.д.). При использовании новых растворителей потребление тепловой энергии для регенерации реагентов сокращается до 3 ГДж/т CO2. Ожидается, что в будущем удастся снизить ее до 2.0–2.5 ГДж/т CO2 [10].
Технологии химической и физической адсорбции активно адаптируются для выделения CO2 из газовых потоков. Первые применяются преимущественно для разделения газовых смесей с низким, а вторые с высоким парциальным давлением CO2. Восстановление свойств сорбента производится соответственно путем повышения температуры или снижения давления в регенераторе. Исследуются как классические адсорбенты (активированный уголь, оксиды алюминия, кремнеземы, цеолиты и т.д.) и их модификации, так и новые вещества (оксиды металлов, металлорганические соединения, полимеры и др.). Работы в области новых адсорбционных технологий для улавливания CO2 сосредоточены, во-первых, на разработке эффективных сорбентов с высокой термической и химической стабильностью и низкой стоимостью, во-вторых, на сокращении потерь сорбентов в процессе очистки и регенерации и, в-третьих, на снижении расхода энергии на регенерацию сорбента.
Привлекательность технологий адсорбции обусловлена широкими возможностями для подбора адсорбентов под условия конкретных производств (температура и давление газового потока, его компонентный состав и др.). Такие технологии проще совместить с производственными процессами, оборудование для них более компактное и его проще разместить на действующих предприятиях. Затраты тепловой энергии на регенерацию адсорбентов составляют около 2–3 ГДж/т извлеченного CO2. С использованием передовых адсорбционных технологий можно добиться степени извлечения CO2 из газовых потоков до 90–95% и чистоты извлеченного CO2 до 93–98%. Во многих случаях они обеспечивают более низкие затраты на извлечение CO2, чем абсорбционные технологии. Ожидается, что стоимость очистки газовых смесей с высоким парциальным давлением CO2, например продуктов газификации угля или паровой конверсии метана, приблизится к 30 дол/т CO2, что на 40% ниже по сравнению с применением известной абсорбционной технологии Selexol (очистка аминами) [10].
Для газовых потоков, находящихся под высоким давлением и имеющих высокую концентрацию CO2, эффективным оказывается метод короткоцикловой адсорбции CO2 (pressure swing adsorption – PSA) [13]. Компания Linde Engineering предлагает PSA-установки производительностью по очищаемому газу от 1 до 30 тыс. м3/ч. Они обеспечивают удаление до 90% CO2 и его чистоту до 95%. Давление очищаемого газа должно быть в диапазоне 0.7–3.5 МПа [14]. Регенерация адсорбента осуществляется сбросом давления.
Большой интерес в мире стал проявляться к улавливанию CO2 с использованием кальциевого цикла (calcium looping combustion – CaLC) [15, 16]. Он основан на обратимой реакции разложения реагента (известняка)
Реакция требует значительных затрат энергии. Достоинством данной технологии являются доступность, дешевизна и безопасность при обращении с известняком. Он более чем в 100 раз дешевле аминовых абсорбентов [17]. Технология доведена до уровня TRL 6. Существуют крупные пилотные установки в Германии и Испании, а также значительное количество небольших установок в других странах. Для улавливания CO2 и регенерации адсорбента используются аппараты кипящего слоя. Регенерация осуществляется при высокой температуре (более 850°C) в среде кислорода, что необходимо для предотвращения разбавления выделяемого CO2 балластным азотом.
Ожидается, что при использовании технологии CaLC можно снизить стоимость извлечения CO2 из уходящих газов до 30 дол/т CO2 [10]. Однако на пути к ее промышленной реализации предстоит преодолеть ряд серьезных технических проблем. Прежде всего, это касается довольно быстрой дезактивации сорбента и его механического истирания. Правда, отработанный сорбент может использоваться в производстве цемента, а также в металлургии. Требуются большие расходы топлива для регенерации сорбента и электроэнергии для производства кислорода. Масштабы применения технологии CaLC будут ограничиваться спросом на отработанный сорбент и затратами на его перевозку.
Комбинирование технологии CaLC с угольной электростанцией и оптимизация интегрированной технологической схемы позволяют увеличить КПД установки с 38.0 до 38.9%. При этом стоимость производимой электроэнергии возрастает всего на 19.3%, что в 3 раза меньше по сравнению с применением традиционной абсорбционной технологии извлечения CO2 на основе аминов. В последнем случае стоимость электроэнергии возрастает на 62% [16].
Мембранные технологии основаны на различии скоростей диффузии разных газов через пористые материалы. Такие технологии были разработаны в 80-х годах прошлого века и нашли применение при переработке природного газа. Они применимы к газовым смесям с широким диапазоном парциальных давлений CO2. При низких скоростях диффузии CO2 неизбежно возникает потребность в большой площади поверхности мембран. Увеличение этой скорости путем повышения разности давлений на мембране ведет к росту энергетических потерь. Для угольной электростанции мощностью 240 МВт с улавливанием 1.4 млн т CO2/год нужны мембраны площадью 200–400 тыс. м2 [8]. Этим объясняется высокая стоимость извлечения CO2 с помощью традиционных мембранных технологий. Необходимая площадь мембран и стоимость очистки существенно зависят от степени извлечения CO2 [17].
В настоящее время многие исследовательские центры и компании ведут разработки новых типов недорогих, долговечных мембран с улучшенной проницаемостью и селективностью, тепловой и физической стабильностью и устойчивостью к загрязняющим веществам в продуктах сгорания топлив. Так, в Институте газовых технологий США (Gas Technology Institute) испытывается инновационная мембранная технология, обеспечивающая 95% улавливания CO2 из дымовых газов угольной электростанции при стоимости 30 дол/т CO2 [6].
Выделение CO2 из газовой смеси методом конденсации привлекает внимание возможностью получения CO2 в жидком виде непосредственно в процессе очистки. Это позволит в последующем сократить затраты на компримирование CO2 и транспортирование его на дальние расстояния. Согласно работе [10] применение технологии конденсации экономически целесообразно при концентрации CO2 в газовой смеси свыше 70%. Для осуществления конденсации требуется довольно сильно охладить газовый поток (до температуры ниже точки конденсации CO2 при данном давлении). Для этого нужны природные источники охлаждающего агента или криогенная система.
Примером применения метода конденсации CO2 может служить предложенная в Объединенном институте высоких температур Российской академии наук (ОИВТ РАН) схема бескомпрессорной парогазовой установки с кислородным сжиганием топлива [18]. В ней CO2 выделяется путем конденсации из продуктов сгорания непосредственно в цикле энергетической установки. Расчетная степень извлечения CO2 превышает 95%. Источником холода является криогенная воздухоразделительная установка. Электрический КПД энергоустановки при температуре продуктов сгорания перед газовой турбиной 1100°C и давлении 20 МПа составляет примерно 51.6% (по низшей теплоте сгорания) [19]. Это относительно невысокая температура, позволяющая использовать хорошо освоенные и недорогие материалы. При повышении ее до 1200°C КПД установки возрастет до 54.5–55.0%. В случае направления тепловой энергии уходящих потоков для целей теплоснабжения полезное использование энергии топлива достигнет 95%. Разработчики технологии предлагают построить демонстрационную установку электрической мощностью 60 МВт и затем промышленный прототип на 300 МВт.
Компании Orbital ATK и ACENT Laboratories разрабатывают систему инерционного осаждения CO2 (Inertial CO2 Extraction System) из дымовых газов электростанций [20]. Дымовые газы после энергоустановки охлаждаются и обезвоживаются до остаточного содержания влаги 10 ppmv. После сжатия компрессором до 0.2–0.5 МПа они направляются в сопло Лаваля (De Laval nozzle), где расширяются до сверхзвуковой скорости и охлаждаются. При этом CO2 конденсируется и замерзает. Твердые частицы CO2 отделяются от газов в циклонах. Преимущества данной технологии: большая производительность, простота конструкции и небольшие габариты. Для ее размещения требуется площадь в 2–3 раза меньше, чем для традиционной абсорбционной очистки аминами. При реконструкции действующих электростанций этот фактор часто является определяющим. Оснащение установками улавливания CO2 действующих газовых электростанций оказывается примерно на 11% дороже, чем новых. Для угольных электростанций это различие выше и составляет около 18% [21].
Все более популярной становится идея комбинировать различные технологии улавливания CO2, используя их достоинства и нивелируя недостатки. Целью является снижение затрат на извлечение CO2. В частности, комбинирование мембранных и криогенных технологий позволяет сократить потребление энергии до 1.4 ГДж/т CO2 при суммарной степени улавливания CO2 около 89% [22].
Улавливание CO2 с использованием рассмотренных ранее методов может осуществляться:
после сжигания топлива (post-combustion capture), что характерно для традиционных энергетических установок;
до сжигания топлива (pre-combustion capture), например, в парогазовых установках (ПГУ) с газификацией угля;
непосредственно в цикле энергетической установки (inherent CO2 capture).
Повышенное внимание уделяется технологиям выделения CO2 непосредственно в цикле энергетической установки. Это объясняется надеждами уменьшить затраты на выделение CO2. Представителями данного направления являются установка ОИВТ РАН, цикл Аллама (Allam cycle), иногда его называют цикл Аллама ‒ Фетведта (Allam ‒ Fetvedt cycle), а также энергоустановки с топливными элементами с расплавом карбонатов (molten carbonate fuel cells – MCFC).
В энергоустановке на основе цикла Аллама сжигание топлива осуществляется в среде чистого кислорода под высоким давлением [23–25]. Продукты сгорания направляются в газовую турбину и затем при повышенном давлении охлаждаются. При конденсации воды и CO2 происходит их разделение. Одна часть CO2 направляется обратно в камеру сгорания для снижения в ней температуры, а вторая – на захоронение. Эффективность удаления CO2 из дымовых газов превышает 97%. При этом отсутствует необходимость размещать дополнительное оборудование для выделения CO2. Температура в камере сгорания достигает 727°C. Давление продуктов сгорания перед газовой турбиной составляет 30 МПа, а на выходе ‒ 3 МПа [24]. Расчетный КПД нетто установки электрической мощностью 250 МВт равен 59% при ее работе на природном газе и 51% при использовании угля, включая его предварительную кислородную или парокислородную газификацию. Проектные значения капиталовложений в установку на газе были оценены в 800–1000, а на угле 1500–1800 дол/кВт [23]. Стоимость электроэнергии, производимой данной установкой при ее работе на природном газе, на 22% выше по сравнению со стоимостью электроэнергии от традиционной ПГУ без очистки от CO2 [8]. Для сопоставления, при оборудовании ПГУ абсорбционной системой удаления CO2 стоимость электроэнергии возрастает на 50–70% [26].
Продолжается разработка технологий со сжиганием топлива в химическом цикле CLC, позволяющих получать дымовые газы с высоким парциальным давлением CO2. В них предполагается наличие восстановителя (reduser) и оксидайзера (oxidizer), между которыми организована циркуляция твердого реагента, являющегося переносчиком кислорода. В качестве такого реагента могут использоваться оксиды некоторых металлов (Cu, Fe, Ni, Mn, Co) и другие вещества. В первом аппарате осуществляется сжигание топлива в присутствии кислорода, выделяющегося из твердого реагента (RO2), при одновременном восстановлении последнего (R):
Во втором аппарате происходит окисление твердого реагента при контакте его с кислородом воздуха:
Обычно в обоих аппаратах используются технологии циркуляционного кипящего слоя. В результате в продуктах сжигания топлива накапливается CO2 высокой концентрации, поскольку отсутствует балластный азот. Извлечение CO2 из газовой смеси осуществляется с использованием рассмотренных ранее методов.
Согласно [27] в 2018 г. в мире имелось 19 экспериментальных установок CLC тепловой мощностью от 0.5 кВт до 4.0 МВт. Технологии CLC достигли уровня технической готовности TRL 6. В [28] рассмотрена схема угольной ТЭС мощностью 420 МВт с CLC-циклом и горячей очисткой уходящих газов. Согласно расчетам, КПД нетто ТЭС может составить 45.4%, а эффективность улавливания CO2 ‒ 95%. Расход электроэнергии на собственные нужды довольно высок и равен 7.6%.
Довольно много экспериментов по сжиганию газообразных и твердых топлив проведено на установках CLC в Германии, США, Китае и других странах [29]. Они показали, что может быть обеспечена степень удаления CO2 на уровне 82–96%. Но выявлен целый ряд трудно решаемых проблем. В частности, сложно добиться высокой полноты сжигания топлива (более 90%) в одном реакторе, особенно при использовании твердых топлив. Зафиксированы большие потери твердого реагента в результате его истирания в кипящем слое. Наблюдается значительная эрозия оборудования реакторов.
Технологии CLC не получили коммерческого применения также из-за сложности и дороговизны технологической схемы. Кроме того, для их реализации требуются большие объемы кислорода, производство которого традиционным методом (в криогенном процессе) является капитало- и энергоемким. Для снижения затрат на извлечение CO2 из газовой смеси желательно иметь кислород с чистотой не менее 95%. Для повышения чистоты кислорода обычно требуется его дополнительная очистка (от азота, аргона и других газов), что, естественно, приводит к его удорожанию.
В применяемых криогенных установках удельный расход электроэнергии составляет 0.3–1.1 кВт · ч/кг O2 в зависимости от их производительности и технического совершенства. В перспективных криогенных установках расход кислорода может быть снижен до 0.2 кВт · ч/кг O2. Для криогенного завода производительностью 10.4 тыс. т/сут при чистоте кислорода 95% требуется электрическая мощность 87 МВт. Основным потребителем электроэнергии является воздушный компрессор, который имеет адиабатический КПД свыше 90%. Удельные капиталовложения в такой завод составляют 24.9 тыс. дол/(т/сут) (2007 г.). Затраты на электроэнергию достигают 65% стоимости производимого кислорода [30].
Больших резервов для повышения энергоэффективности криогенной технологии и снижения стоимости кислорода не осталось, поэтому делаются попытки найти новые способы получения более дешевого кислорода. Например, при химическом цикле разделения воздуха (chemical looping air separation) с помощью соединений марганца предполагается снизить энергетические затраты на 9% и капиталовложения на 10–18% [31]. Разрабатываются новые мембраны для разделения воздуха [32]. Компания Linde предлагает установки на основе вакуумной цикловой адсорбции (vacuum pressure swing adsorption – VPSA) производительностью по кислороду 0.3–10.0 тыс. м3/ч при чистоте кислорода 90–95% [33].
В табл. 1 представлены экономические показатели ПГУ большой мощности (600–900 МВт) на природном газе с различными технологиями улавливания СО2 в процессе эксплуатации [11]. Улавливание CO2 на электростанциях оказывается энергозатратным и дорогостоящим мероприятием. При оснащении ПГУ абсорбционной очисткой от CO2 (как традиционной, так и перспективной) электрический КПД уменьшается на 14–17%, капитальные затраты возрастают примерно в 2 раза, а стоимость производимой электроэнергии – в 1.4–1.5 раза.
Таблица 1.
Экономические показатели ПГУ на природном газе с различными технологиями улавливания СО2
Технология улавливания | КПД, % | Удельные капитало-вложения, дол/кВт | Стоимость производства электроэнергии, дол/(МВт · ч) | Удельный расход энергии на улавливание CO2, ГДж/т | Стоимость улавливания CO2, дол/т |
---|---|---|---|---|---|
Без улавливания CO2 | 58.3 | 1059 | 45.0 | – | – |
Абсорбция CO2: | |||||
традиционная (аминами) | 49.9 | 2181 | 68.6 | 3.34 | 75 |
перспективная (пиперазином) | 51.3 | 2079 | 65.0 | 2.73 | 68 |
аминами под давлением | 39.6 | 1767 | 71.0 | 9.79 | 87 |
Мембранная очистка | 48.0 | 2131 | 71.4 | 4.34 | 86 |
Осаждение CO2 в ультразвуковом потоке | 46.2 | 1767 | 74.8 | 5.22 | 87 |
Схема с топливными элементами: | |||||
традиционная | 52.7 | 1950 | 66.1 | 2.38 | 76 |
интегрированная | 57.5 | 1731 | 58.8 | 0.31 | 49 |
Наиболее дорогими установками очистки дымовых газов от CO2 оказались ПГУ с осаждением CO2 в ультразвуковом потоке, а также ПГУ с многовальной газовой турбиной и абсорбционной очисткой при высоком давлении. В последнем случае дымовые газы после газовой турбины высокого давления (0.8 МПа, 800°C) охлаждаются и направляются в абсорбер с аминовым поглотителем. Очистка газовой смеси осуществляется при высоком парциальном давлении CO2, что удешевляет ее. После очистки и подогрева дымовые газы подаются в газовую турбину низкого давления [11]. В этой схеме экономия на очистке дымовых газов от CO2 оборачивается большими затратами на теплообменное оборудование и значительными потерями энергии в нем.
В табл. 1 включены данные по ПГУ с топливными элементами на основе расплавов карбонатов (MCFC). Топливные элементы такого типа обладают уникальной способностью концентрировать CO2 [34]. Это обусловлено тем, что в качестве электролита в них используются расплавы карбонатов лития, калия, натрия. Переносчиками кислорода, необходимого для окисления топлива, и заряда выступают карбонат-ионы ${\text{CO}}_{3}^{{2 - }}.$ Поэтому CO2 является неотъемлемым компонентом следующих электрохимических реакций:
на катоде
на аноде
в суммарном процессе
Потребление CO2 в рассматриваемом процессе очень большое: по массе в 2.75 раза больше, чем кислорода, и в 22 раза больше, чем водорода. Высокая температура процесса (600–700°C) обеспечивает высокие скорости реакций на электродах, возможность использования дешевых катализаторов (никельалюминиевых, хромоникелевых), низкую чувствительность к содержанию монооксида углерода в составе топлива. На основе MCFC могут создаваться энергоустановки мегаваттного уровня. Недостатками MCFC являются низкая чувствительность к соединениям серы в составе топлива, что требует их предварительного удаления, и высокая коррозионная активность электролита, требующая применения дорогих нержавеющих сталей.
В традиционной технологической схеме ПГУ и MCFC объединены тепловыми потоками и организована рециркуляция CO2 между анодом и катодом. Выбросы CO2 от ПГУ улавливаются традиционными способами. Вторая (интегрированная) схема предусматривает глубокую интеграцию ПГУ и MCFC, в том числе по CO2 (рис. 2). Дымовые газы ПГУ направляются в топливный элемент со стороны катода, где смешиваются с окислителем. В MCFC на аноде происходит концентрирование CO2, который после отделения воды может направляться на захоронение.
Интегрирование ПГУ и MCFC представляется наиболее эффективным способом декарбонизации на тепловых электростанциях, при котором улавливается более 90% CO2, чистота CO2 превышает 95% [11]. Одновременно в 5 раз сокращаются выбросы оксидов азота и в 3 раза выбросы твердых частиц при практически полном исключении выбросов соединений серы [35]. Стоимость извлечения CO2 в этом случае составляет 49 дол/т CO2 при расходе энергии на очистку 0.31 ГДж/т CO2 (см. табл. 1). Это много лучше, чем ПГУ с традиционной аминовой очисткой (75 дол/т CO2, 3.34 ГДж/т CO2).
Существенное ухудшение экономических характеристик электростанций при оснащении их абсорбционными системами улавливания CO2 отмечается в работе [36] (табл. 2). Удельные капиталовложения в ПГУ на газе увеличиваются в 2.3 раза, а в ПТУ на угле ‒ в 1.6 раза. Примерно в 2 раза возрастают удельные эксплуатационные затраты (без учета топлива). На функционирование абсорбционной установки расходуется около 9–10% установленной мощности газовой ПГУ и 11–12% мощности угольной ПТУ [37].
Таблица 2.
Сравнение экономических характеристик газовых и угольных электростанций с улавливанием СО2
Технология | Электрическая мощность, МВт | КПД (нетто), % |
Удельные капитало-вложения, дол/кВт | Эксплуатационные расходы | |
---|---|---|---|---|---|
постоянные, дол/(кВт · год) | переменные, дол/(МВт · ч) | ||||
ПГУ на газе: | |||||
без улавливания CO2 | 1100 | 58.9 | 957 | 12.2 | 1.88 |
430 | 58.4 | 1082 | 14.2 | 2.56 | |
с улавливанием CO2 | 430 | 52.7 | 2471 | 27.7 | 5.87 |
ПТУ на угле*: | |||||
без улавливания CO2 | 650 | 41.0 | 3672 | 40.8 | 4.5 |
с улавливанием CO2** | 650 | 28.3 | 5861 | 59.9 | 11.0 |
Удельные затраты на декарбонизацию дымовых газов электростанций, имеющих низкое парциальное давление CO2, существенно зависят от производительности G системы улавливания (рис. 3). Особенно сильно это проявляется при улавливании менее 0.4 Мт CO2/год, что соответствует мощности электрогенерирующей установки до 200 МВт.
Рис. 3.
Зависимость удельных затрат на улавливание CO2 от производительности улавливающей установки. 1 – ПТУ на угле; 2 – ПГУ на природном газе

На основе данных [37] и рис. 3 рассчитаны удельные затраты на улавливание CO2 для ПГУ на природном газе и ПТУ на угле в зависимости от их электрической мощности (табл. 3). Коэффициент использования установленной мощности электростанций был принят равным 0.6. В табл. 3 приведены принятые значения КПД нетто электрогенерирующих установок без улавливания. Затраты на улавливание отнесены на единицу выработанной электроэнергии. Из результатов расчетов следует, что при снижении мощности электрогенерирующих установок с 1000 до 25 МВт удельные затраты на улавливание CO2 возрастают для ПГУ на газе в 2.4 раза и для ПТУ на угле в 1.8 раза. Это означает сокращение масштабов развития индустрии CCS вследствие снижения конкурентоспособности технологий улавливания CO2 на установках малой мощности.
Таблица 3.
Влияние мощности электростанции на удельные затраты на улавливание CO2
Мощность, МВт | ПГУ на природном газе | ПТУ на угле | ||
---|---|---|---|---|
КПД (нетто)*, % | удельные затраты, дол/(МВт · ч) | КПД (нетто)*, % | удельные затраты, дол/(МВт · ч) | |
25 | 44 | 57.7 | 35 | 74.3 |
50 | 46 | 39.2 | 36 | 56.4 |
100 | 50 | 29.8 | 37 | 65.3 |
200 | 52 | 26,9 | 38 | 48.4 |
300 | 54 | 25.4 | 39 | 46.0 |
500 | 56 | 24.8 | 40 | 44.8 |
800 | 58 | 24.4 | 41 | 43.7 |
1000 | 59 | 24.0 | 42 | 42.6 |
1200 | 60 | 24.0 | 43 | 42.0 |
Улавливание CO2 на угольных электростанциях обходится существенно дороже (примерно в 1.6–1.8 раза), чем на газовых, при отнесении затрат на очистку к единице выработанной электроэнергии. Это объясняется более высоким содержанием углерода в угле, по сравнению с природным газом, на единицу энергии (примерно в 1.72 раза) и меньшим КПД угольных электростанций.
Между тем, в мире и в России получила развитие распределенная генерация электроэнергии, базирующаяся на установках мощностью менее 25 МВт, использующих органическое топливо [38, 39]. В России таких электростанций насчитывается около 40 тысяч суммарной электрической мощностью более 34 ГВт и выработкой электроэнергии около 58 ТВт · ч/год [40]. Кроме того, в России в больших масштабах применяется централизованное теплоснабжение на основе котельных, работающих на природном газе и угле [41]. По данным Росстата, в 2021 г. ими было произведено 2596 ТДж тепловой энергии против 2541 ТДж на теплоэлектроцентралях (ТЭЦ). Среди действующих ТЭЦ имеется много установок малой мощности, для которых характерны низкая энергетическая эффективность и, следовательно, большие расходы топлива и выбросы CO2 [42].
Возможным решением в повышении экономической эффективности декарбонизации на небольших электростанциях может стать комбинирование их с топливными элементами на основе расплавов карбонатов. Американская компания FuelCell Energy Inc. – мировой лидер в области MCFC ‒ поставляет на рынок под брендом SureSource MCFC единичной мощностью 1.5–3.7 МВт с КПД 50%. При их использовании могут создаваться электростанции мощностью до 100 МВт и более, в том числе с комбинированной выработкой электрической и тепловой энергии. Такие электростанции, работающие на угле, при улавливании 90% CO2 обеспечивают рост стоимости производимой электроэнергии не более 33% [примерно на 20 дол/(МВт · ч)]. При серийном внедрении таких установок стоимость улавливания CO2 в них может составить 40 дол/т CO2 [43]. В настоящее время MCFC производятся в небольшом объеме. В 2017–2018 гг. их установленная мощность составляла около 25–26 МВт/год [44].
ТРАНСПОРТИРОВАНИЕ И ЗАХОРОНЕНИЕ CO2
Обычно центры производства больших объемов CO2 и удобные места для его захоронения разнесены в пространстве. Поэтому неизбежным станет сооружение крупных трубопроводных систем для транспортирования CO2 на большие расстояния. Такие системы могут иметь статус национальных и транснациональных. Важной задачей является обеспечение экономически эффективного транспортирования CO2 из места его улавливания к местам хранения.
Удельная стоимость транспортирования CO2 по трубопроводам существенно зависит от передаваемого объема и фазового состояния CO2, что хорошо иллюстрирует рис. 4, построенный по данным [8]. При увеличении объемов передачи CO2 с 0.1 до 5.0 Мт/год удельная стоимость транспортирования уменьшается почти на порядок. Дальнейший рост производительности трубопроводов слабо сказывается на удельной стоимости передачи CO2. При передаче более 5 Мт CO2/год (более 10 млрд м3 CO2/год) затраты на передачу составят около 25 дол/(кт · км), или 50 дол/(млн м3 · км). Это достаточно близко к стоимости передачи природного газа по магистральным трубопроводам для новых проектов – около 30–50 дол/(млн м3 · км).
Рис. 4.
Удельные затраты на транспортирование CO2 Зтр по трубопроводам в газообразном (1) и жидком (2) виде в зависимости от объема передачи

Нелинейная зависимость затрат на транспортирование от объемов передачи означает, что должна создаваться разветвленная трубопроводная система для сбора потоков CO2 от отдельных предприятий с дальнейшей передачей их к местам захоронения по мощным трубопроводам. В таком случае экономически оправданным может стать применение технологий улавливания CO2 на небольших предприятиях. Это существенно увеличит объемы CO2, которые можно будет направить на захоронение, и расширит потенциал применения технологий CCS. Трубопроводная сеть CO2 по своей структуре является обратной по отношению к традиционной газотранспортной системе.
Потери давления в магистральном трубопроводе производительностью 5 Мт CO2/год (диаметр 400 мм, давление 10–14 МПа) составляют около 35 кПа/км. Для их компенсации требуются бустерные компрессоры удельной мощностью примерно 8.2 кВт/км с годовым расходом электроэнергии 14.3 Вт · ч/(т · км) [45]. В разветвленной транспортной системе CO2 расход электроэнергии будет выше. Так, по данным Росстата, в газотранспортной системе России удельное потребление природного газа в 2019 г. составило 627 Дж/(м3 · км) и электроэнергии 13.4 Дж/(м3 · км). При транспортировании аналогичного объема CO2 по этой системе и использовании электрического привода удельное потребление электроэнергии равнялось бы примерно 32 Вт · ч/(т · км).
Капитальные затраты на линейную часть магистрального трубопровода производительностью 5 Гт CO2/год составляют приблизительно 100, а на бустерный компрессор ‒ 20 дол/[кт/(год · км)] [45]. Структура капитальных затрат, %, выглядит следующим образом:
Оборудование и материалы .........................19 |
Оплата труда .................................................50 |
Землеустройство ............................................9 |
Прочие (накладные и непредвиденные |
расходы, надзор, налоги и др.) .....................22 |
Ежегодные эксплуатационные расходы (без энергетических нужд) составляют для линейной части трубопровода 6%, а для бустерного компрессора 1.5% капиталовложений в них, или 6.0 и 0.3 дол/(кт · км) соответственно.
Важно отметить, что практически все варианты глубокой декарбонизации связаны с расширением действующей и созданием новой транспортной инфраструктуры. Можно предположить, что формирование трубопроводной сети CO2 окажется много проще, дешевле и быстрее, чем водородной инфраструктуры [46].
В мире уже накоплен значительный опыт разработки и эксплуатации трубопроводов CO2, в том числе подводных. В настоящее время в США эксплуатируется около 50 трубопроводов CO2 суммарной протяженностью более 3.1 тыс. км, по которым передается примерно 68 млн т CO2/год [26]. Они используются в основном для повышения добычи нефти. Трубопроводный и морской транспорты CO2 при соблюдении штатных регламентов эксплуатации не являются более опасными, чем аналогичный транспорт углеводородов, таких как природный газ и нефть. Разрабатываются соответствующие международные стандарты, внедрение которых будет содействовать безопасному и эффективному функционированию инфраструктуры CO2.
Затраты на захоронение CO2 в решающей степени зависят от характеристик геологического резервуара [47, 48]. Самым дешевым вариантом является захоронение CO2 в истощенные нефтегазовые месторождения на суше при использовании существующих скважин (табл. 4). Но в [48] предупреждается, что существующие скважины можно будет использовать для инжекции CO2 в очень ограниченном количестве, поскольку они конструировались и сооружались для других целей – для извлечения углеводородов, а не для нагнетания в них CO2. Кроме того, может оказаться сложным и дорогим обеспечение газовой плотности покрывающих пород, перфорированных многочисленными добычными и разведочными скважинами. Захоронение в морских резервуарах обходится много дороже, особенно в случае необходимости сооружения новых скважин.
Таблица 4.
Удельные капиталовложения и затраты на захоронение CO2
Резервуар | Удельные капитало-вложения, дол/(т CO2/год) | Средние удельные затраты, дол/т CO2 | Структура удельных затрат, % | Диапазон изменения удельных затрат, % | |
---|---|---|---|---|---|
капитало-вложения | эксплуата-ционные расходы | ||||
Истощенные нефтегазовые | |||||
месторождения на суше: | |||||
существующие скважины | 17.4 | 4.3 | 18.2 | 81.8 | От –70 до 110 |
новые скважины | 31.0 | 5.6 | 37.2 | 62.8 | От –77 до 130 |
Истощенные нефтегазовые | |||||
месторождения на море: | |||||
существующие скважины | 32.3 | 8.0 | 24.2 | 75.8 | От –68 до 45 |
новые скважины | 77.4 | 12.8 | 48.5 | 51.5 | От –70 до 40 |
Подземные водные растворы | |||||
солей с сооружением новых | |||||
скважин: | |||||
на суше | 45.2 | 7.0 | 59.3 | 40.7 | От –63 до 120 |
под морским дном | 128.4 | 18.5 | 69.2 | 30.8 | От –58 до 40 |
Оценки в табл. 4 получены на основе данных [49] и приведены к курсу доллара в 2020 г. Большие различия в характеристиках резервуаров являются причиной широкого диапазона изменения удельных затрат на захоронение CO2. В работе [48] удельные затраты на морское захоронение CO2 оценены следующим образом (при выражении их в долларах по курсу 2020 г.): в истощенные нефтегазовые месторождения 16–24 дол/т CO2, в подземные растворы солей 18–26 дол/т CO2. Захоронение предусматривает сооружение новых скважин. Данные оценки укладываются в диапазоны затрат, представленные в табл. 4.
В табл. 5 на основе данных [44], а также табл. 4, рис. 1, 2 и 4 приведены оценки затрат на отдельные компоненты CCS при использовании освоенных технологий. Затраты на транспортирование CO2 морскими судами включают все погрузочно-разгрузочные операции. Захоронение CO2 предполагает сооружение новых скважин.
Таблица 5.
Затраты на компоненты CCS, дол/т CO2
Компонент CCS | Производительность CCS, Мт/год | |
---|---|---|
0.5 | 5.0 | |
Извлечение CO2 из газовой смеси парциальным | ||
давлением, кПа: | ||
5–10 | 100 | 70 |
более 40 | 50 | 40 |
Транспортирование CO2 по трубопроводам сетей: | ||
собирающих (50 км) | 5 | 0 |
магистральных (300 км) | 7.5 | 7.5 |
Транспортирование CO2 морскими судами | ||
на расстояние, км: | ||
180 | 22 | 22 |
1500 | 15 | 15 |
Захоронение CO2 в истощенные нефтегазовые | ||
месторождения: | ||
на суше | 6 | 6 |
на море | 13 | 13 |
Захоронение CO2 в подземные водные растворы солей: | ||
на суше | 7 | 7 |
под морским дном | 19 | 19 |
Мониторинг геологического резервуара | 2–4 | 2–4 |
Оценки суммарных затрат на декарбонизацию с использованием имеющихся технологий CCS даны в табл. 6. Предполагается транспортирование CO2 по трубопроводам. Нижние оценки относятся к захоронению CO2 в истощенные нефтегазовые месторождения на суше при использовании существующих скважин. Верхние оценки отражают удельные затраты на захоронение CO2 в нефтегазовые месторождения и водные соляные горизонты под морским дном. При захоронении CO2 в горные породы затраты существенно возрастут и будут определяться местными факторами (глубиной залегания, составом пород, проницаемостью и т.д.).
Таблица 6.
Суммарные удельные затраты на декарбонизацию выбросов CO2 с использованием CCS, дол/т захороненного CO2
Источник выбросов CO2 | Производительность CCS, Мт/год | |
---|---|---|
0.5 | 5.0 | |
С высоким парциальным давлением CO2 в газовом потоке | 75–85 | 60–70 |
В том числе улавливание CO2 | 50 | 40 |
С низким парциальным давлением CO2 в газовом потоке | 120–130 | 85–95 |
В том числе улавливание CO2 | 100 | 70 |
Декарбонизация источников с небольшой эмиссий CO2 будет обходиться дороже в 1.4 раза и более по сравнению с декарбонизацией крупных источников. В суммарных затратах CCS основная доля приходится на установки улавливания CO2, которая достигает 60–70% для источников с высоким парциальным давлением CO2 в газовом потоке и 75–80% для источников с низким парциальным давлением CO2.
В будущем можно ожидать сокращения затрат на CCS благодаря накоплению опыта их сооружения (эффект “обучения”), увеличению масштабов внедрения (эффект масштаба) и применению новых технологий (технологический фактор). Только за счет накопления производственного опыта затраты на CCS могут быть снижены не менее чем на 20% [8]. Однако основные надежды на сокращение затрат связываются с разработкой новых технологий. Важной остается задача уменьшения расходов энергии на функционирование CCS.
Как показали выполненные исследования, технологии CCS являются очень капиталоемкими. Поэтому их конкурентоспособность и скорость формирования индустрии CCS будут во многом определяться доступностью дешевых финансовых ресурсов. По этим причинам создание технологической основы CCS осуществляется в мире при весомой государственной поддержке. Например, Конгресс США выделил на 2021–2025 гг. более 6 млрд дол. на программы исследований, разработок и демонстрации CCS. В их числе 1 млрд дол. на реализацию крупных пилотных проектов, 910 млн дол. на исследования и разработки технологий с низким уровнем готовности (TRL не выше 3) и 800 млн дол. на работы по захоронению CO2, включая выявление и оценку подходящих геологических ресурсов [50, 51]. Технологиям CCS отведено важное место в программе развития водородной энергетики в США [52]. Ожидается, что сеть транспортных трубопроводов CO2 в Северной Америке вырастет с нынешних 8 до 43 тыс. км к 2050 г. [50].
Государства предлагают различные меры для привлечения бизнеса к разработке необходимых технологий и участию в формировании инфраструктуры CCS. В США важным стимулом считается налоговый кредит на захоронение CO2. В 2019 г. его размер составил 19 дол/т CO2 при направлении CO2 в отработанные газовые и нефтяные месторождения и 31 дол/т CO2 при захоронении CO2 в другие подземные геологические структуры. К 2026 г. размер данного налогового кредита возрастет соответственно до 35 и 50 дол/т CO2 [50]. Операторы CCS могут претендовать на такой кредит в течение 12 лет.
ВЫВОДЫ
1. При применении технологий CCS можно достичь углеродной нейтральности экономики страны при сохранении использования органических топлив в больших масштабах.
2. Технологии CCS оказываются довольно энергозатратными и дорогостоящими. Это касается прежде всего оборудования для улавливания CO2, на которое приходится 60–80% суммарных затрат на CCS.
3. При оснащении тепловых электростанций системами очистки от CO2 удельные капитальные вложения увеличиваются в 1.6–2.3 раза, а стоимость производимой электроэнергии ‒ в 1.4–1.6 раза. На собственные нужды таких систем расходуется от 9–12 до 20% мощности электростанции.
4. Формирование индустрии CCS потребует создания разветвленной трубопроводной системы для транспортирования больших объемов CO2, сопоставимой с газотранспортной системой.
5. Затраты на захоронение CO2 в решающей степени зависят от характеристик подземного резервуара. Самым дешевым вариантом является захоронение CO2 в истощенных нефтегазовых месторождениях.
6. Создание технологической основы CCS осуществляется в мире при весомой государственной поддержке. Предлагаются различные меры для привлечения бизнеса к разработке необходимых технологий и участию в формировании инфраструктуры CCS.
7. В России разработки технологий CCS ведутся в очень небольших объемах. Отсутствие отечественных технологий может стать серьезным препятствием для создания индустрии CCS в стране.
Список литературы
Glasgow Climate Pact. United Nations. N.Y., 2021. https://unfccc.int/sites/default/files/resource/cop26_ auv_2f_cover_decision.pdf.
Paris Agreement. N.Y., United Nations, 2015.
Net zero by 2050: A roadmap for the global energy sector. Paris: International Energy Agency, Oct. 2021. https://iea.blob.core.windows.net/assets/deebef5d-0c34-4539-9d0c-10b13d840027/NetZeroby2050-ARoadmapfortheGlobalEnergySector_CORR.pdf.
World economic outlook. International Monetary Fund, Washington, DC, Jan. 2022. Edition. https://www.imf.org/en/publications/weo.
Филиппов С.П., Жданеев О.В. Вызовы и возможности использования технологий улавливания и захоронения CO2 (обзор) // Теплоэнергетика. 2022. № 9. C. 5–21.
DOE awarding $72M to 27 projects to develop and advance carbon capture technologies, including direct air capture. Green Car Congress, 3 Sept. 2020. https:// www.greencarcongress.com/2020/09/20200903-ccdac. html.
Toward transformational carbon capture systems / D.C. Miller, J.T. Litynski, L.A. Brickett, B.D. Morreale // AIChE J. 2016. V. 62. Is. 1. P. 2–10. https://doi.org/10.1002/aic.15066
Kearns D., Liu H., Consoli C. Technology readiness and cost of CCS. Melbourne, Australia, Global Carbon Capture and Storage Institute, March 2021.
Economic and energetic analysis of capturing CO2 from ambient air / K.Z. House, A.C. Baclig, M. Ranjan, E.A. van Nierop, J. Wilcox, H.J. Herzog // Proc. National Academy Sci. 2011. No. 108. Is. 51. P. 20428–20433. https://doi.org/10.1073/pnas.1012253108
Carbon capture and storage (CCS): the way forward / M. Bui, C.S. Adjiman, A. Bardow, E.J. Anthony // Energy Environ. Sci. 2018. No. 11. P. 1062–1176.https://doi.org/10.1039/C7EE02342A https://pubs.rsc.org/en/content/articlelanding/2018/EE/ C7EE02342A.
Preliminary performance and cost evaluation of four alternative technologies for post-combustion CO2 capture in natural gas-fired power plants / M. Gatti, E. Martelli, D. Di Bona, M. Gabba, R. Scaccabarozzi, M. Spinelli, F. Viganò, S. Consonni // Energies. 2020. V. 13. Is. 3. P. 543. https://doi.org/10.3390/en13030543
Carbon capture program. NETL, 2021. https://www.netl.doe.gov/sites/default/files/2021-11/ Program-115.pdf
Riboldi L., Bolland O. Overview on pressure swing adsorption (PSA) as CO2 capture technology: state-of-the-art, limits and potentials // Energy Procedia. 2017. V. 114. P. 2390–2400. https://doi.org/10.1016/j.egypro.2017.03.1385
Carbon dioxide recovery and removal. Linde Engineering, 2021. https://www.linde-engineering.com/ en/process-plants/adsorption-and-membrane-plants/ carbon_dioxide_recovery_removal/index.html.
The calcium-looping technology for CO2 capture: on the important roles of energy integration and sorbent behavior / A. Perejón, L.M. Romeo, Y. Lara, P. Lisbona, A. Martínez, J.M. Valverde // Appl. Energy. 2016. V. 162. P. 787–807. https://doi.org/10.1016/j.apenergy.2015.10.121
Michalski S., Hanak D.P., Manovic V. Advanced power cycles for coal-fired power plants based on calcium looping combustion: A techno-economic feasibility assessment // Appl. Energy. 2020. V. 269. P. 114954. https://doi.org/10.1016/j.apenergy.2020.114954
A twin fluid-bed reactor for removal of CO2 from combustion processes / T. Shimizu, T. Hirama, H. Hosoda, K. Kitano, M. Inagaki, K. Tejima // Chem. Eng. Res. Des. 1999. V. 77. Is. 1. P. 62–68. https://doi.org/10.1205/026387699525882
Концептуальная схема парогазовой установки с полным улавливанием диоксида углерода из продуктов сгорания / А.С. Косой, Ю.А. Зейгарник, О.С. Попель, М.В. Синкевич, С.П. Филиппов, В.Я. Штеренберг // Теплоэнергетика. 2018. № 9. С. 23–32. https://doi.org/10.1134/S0040363618090047
Анализ влияния параметров на эффективность термодинамического цикла бескомпрессорной парогазовой установки / М.В. Синкевич, Э.Р. Рамазанов, Ю.А. Борисов, О.С. Попель, А.А. Косой // ТВТ. 2021. Т. 59. № 5. С. 707–714. https://doi.org/10.31857/S0040364421040190
Supersonic post-combustion inertial CO2 extraction system: Bench scale project status update / V. Balepin, A. Castrogiovanni, A. Robertson, B. Calayag // NETL CO2 Capture Technology Meeting. Pittsburgh, PA, 29 July–1 Aug. 2014. https://netl.doe.gov/sites/default/files/event-proceedings/2014/2014%20NETL%20CO2%20Capture/ A-Castrogiovanni-ATK-Supersonic-Post-Combustion.pdf.
Gerdes K. Incentivizing carbon capture retrofits of the existing PC and NGCC fleet // NETL CO2 Capture Technology Meeting. Pittsburgh, PA, 29 July–1 Aug. 2014.
Multi-objective optimisation of a hybrid vacuum swing adsorption and low-temperature post-combustion CO2 capture / L.Y. Fong, C.J. Anderson, G. Xiao, P.A. Webley, A.F.A. Hoadley // J. Cleaner Production. 2016. Part A. P. 193–203. https://doi.org/10.1016/j.jclepro.2015.08.033
High efficiency and low cost of electricity generation from fossil fuels while eliminating atmospheric emissions, including carbon dioxide / R.J. Allam, M.R. Palmer, G.W. Brown, Jr., J. Fetvedt, D. Freed, H. Nomoto, M. Itoh, N. Okita, C. Jones, Jr. // Energy Procedia. 2013. No. 37. P. 1135–1149. https://doi.org/10.1016/j.egypro.2013.05.211
Demonstration of the Allam cycle: An update on the development status of a high efficiency supercritical carbon dioxide power process employing full carbon capture / R. Allam, S. Martin, B. Forrest, J. Fetvedt, X. Lu, D. Freed, G.W. Brown, T. Sasaki, M. Itoh, J. Manning // Energy Procedia. 2017. V. 114. P. 5948–5966. https://doi.org/10.1016/j.egypro.2017.03.1731
Patel S. UK’s first gas-fired Allam cycle power plant taking shape // POWER Magazine. July 2021. https://www.powermag.com/uks-first-gas-fired-allam-cycle-power-plant-taking-shape/.
Y25. Carbon dioxide capture and storage: IPCC special report / B. Metz, O. Davidson, H. de Coninck, M. Loos, L. Meyer. Cambridge University Press, 2005. https://www.ipcc.ch/site/assets/uploads/2018/03/ srccs_wholereport-1.pdf.
Chemical looping combustion of solid fuels / J. Adánez, A. Abad, T. Mendiara, P. Gayán, F. García-Labiano // Prog. Energy Combust. Sci. 2018. V. 65. P. 6–66. https://doi.org/10.1016/J.PECS.2017.07.005
Integration of chemical looping oxygen production and chemical looping combustion in integrated gasification combined cycles / S. Cloete, A. Giuffrida, R. Matteo, P. Chiesa, M. Pishahang, Y. Larring // Fuel. 2018. V. 220. P. 725–743. https://doi.org/10.1016/j.fuel.2018.02.048
Henderson C. Chemical looping combustion of coal. IEA Clean Coal Centre, 2010. https://usea.org/sites/default/files/122010_Chemical% 20looping%20combustion%20of%20coal_CCC178.pdf.
Allam R.J. Improved oxygen production technologies. International Energy Agency, 2007. https://ieaghg. org/docs/General_Docs/Reports/2007-14.pdf.
Cormos C. Energy and cost efficient manganese chemical looping air separation cycle for decarbonized power generation based on oxy-fuel combustion and gasification // Energy. 2020. V. 191. P. 116579. https://doi.org/10.1016/j.energy.2019.116579
Allam R.J. Improved oxygen production technologies // Energy Procedia. 2009. V. 1. Is. 1. P. 461‒470. https://doi.org/10.1016/j.egypro.2009.01.062
Oxygen generation: By vacuum pressure swing adsorption. The Linde Groupe, 2017. https://www. linde-engineering.com/en/images/26389_LE_Global_ Adsorption_O2_VPSA_Brochure_Update_RZ3_VIEW_ tcm19-160681.pdf.
Assessing the potential of molten carbonate fuel cell-based schemes for carbon capture in natural gas-fired combined cycle power plants / M. Spinelli, D. di Bona, M. Gatti, E. Martelli, F. Viganò, S. Consonni // J. Power Sources. 2020. V. 448. P. 227223. https://doi.org/10.1016/j.jpowsour.2019.227223
Ghezel-Ayagh H. Pilot test of novel electrochemical membrane system for carbon dioxide capture and power generation // Proc. of the 2016 NETL CO2 Capture Technology Meeting. Pittsburgh, PA, USA, 8–12 Aug. 2016.
Cost and performance characteristics of new generating technologies: Annual energy outlook 2021. U.S. Energy Information Administration, Washington, 2021. https://www.eia.gov/outlooks/aeo/assumptions/ pdf/table_8.2.pdf.
Capital cost and performance characteristic estimates for utility scale electric power generating technologies. U.S. Energy Information Administration, Washington, 2020. https://www.eia.gov/analysis/studies/powerplants/capitalcost/pdf/capital_cost_AEO2020.pdf.
Филиппов С.П. Перспективы применения электрогенерирующих установок малой мощности // Атомная энергия. 2011. Т. 111. Вып. 5. С. 255–261.
Филиппов С.П. Малая энергетика в России // Теплоэнергетика. 2009. № 8. С. 38–44.
Филиппов С.П., Дильман М.Д., Илюшин П.В. Распределенная генерация и устойчивое развитие регионов // Теплоэнергетика. 2019. № 12. С. 4–17. https://doi.org/0.1134/S0040363619120038
Филиппов С.П. Развитие централизованного теплоснабжения в России // Теплоэнергетика. 2009. № 12. С. 2–14.
Филиппов С.П., Дильман М.Д. ТЭЦ в России: необходимость технологического обновления // Теплоэнергетика. 2018. № 11. С. 5–22. https://doi.org/10.1134/S0040363618110024
Fuel cell carbon capture. Fuel Cell Energy Inc., 2022. https://www.fuelcellenergy.com/wp-content/uploads/ 2017/02/Fuel-Cells-SureSource-Capture.pdf.
The fuel cell industry review 2020. E4tech, 2021. https://fuelcellindustryreview.com/ (16.02.2022)
Rubin E.S., Berkenpas M.B., McCoy S. The economics of CO2 transport by pipeline and storage in saline aquifers and oil reservoirs / Carnegie Mellon University; Center for Energy and Environmental Studies. Pittsburgh, USA, 2008. https://www.cmu.edu/epp/iecm/IECM_Publications/ 2008ra%20McCoy%20et%20al,%20IECM%20 Trans%20&%20Storage%20Tech.pdf.
Филиппов С.П., Ярославцев А.Б. Водородная энергетика: перспективы развития и материалы // Успехи химии. 2021. Т. 90. № 6. С. 627–643. http://mi.mathnet.ru/rcr4346.
The cost of subsurface storage of CO2: ZEP memorandum – European Zero Emission Technology and Innovation Platform. Brussels, Dec. 2019. https://zeroemissionsplatform.eu/wp-content/uploads/Cost-of-storage.pdf.
Progressing development of the UK’s strategic carbon dioxide storage resources / Pale Blue Dot Axis Well Technology. Costain, 2016. https://onedrive.live. com/?authkey=%21ANk4zmABaDBBtjA&cid= 56FC709A2072366C&id=56FC709A2072366C%211573&parId=56FC709A2072366C%211559&o=OneUp.
The costs of CO2 storage: post-demonstration CCS in the EU. European Technology Platform for Zero Emission Fossil Fuel Power Plants, 2011. https://www.globalccsinstitute.com/archive/hub/publications/119816/costs-co2-storage-post-demonstration-ccs-eu.pdf.
The global status of CCS: 2021. Melbourne, Australia, Global Carbon Capture and Storage Institute, 2021. https://www.globalccsinstitute.com/wp-content/uploads/2021/10/2021-Global-Status-of-CCS-Global-CCS-Institute-Oct-21.pdf.
Consolidated appropriations act, 2021. United States Congress, 2020. https://www.congress.gov/116/bills/ hr133/BILLS-116hr133enr.pdf.
Hydrogen strategy: enabling a low-carbon economy. United States Department of Energy, 2020. https://www.energy.gov/sites/prod/files/2020/07/f76/ USDOE_FE_Hydrogen_Strategy_July2020.pdf.
Дополнительные материалы отсутствуют.
Инструменты
Теплоэнергетика