Журнал неорганической химии, 2023, T. 68, № 4, стр. 551-559
Воздействие сверхзвукового потока азота на керамический материал Ta4HfC5–SiC
Е. П. Симоненко a, *, Н. П. Симоненко a, А. Ф. Колесников b, А. В. Чаплыгин b, Е. К. Папынов c, О. О. Шичалин c, А. А. Белов c, И. А. Нагорнов a, А. С. Мокрушин a, Н. Т. Кузнецов a
a Институт общей и неорганической химии им. Н.С. Курнакова РАН
119991 Москва, Ленинский пр-т, 31, Россия
b Институт проблем механики им. А.Ю. Ишлинского РАН
119526 Москва, пр-т Вернадского, 101, корп. 1, Россия
c Дальневосточный федеральный университет
690922 Владивосток, о. Русский, п. Аякс, 10, Россия
* E-mail: ep_simonenko@mail.ru
Поступила в редакцию 02.12.2022
После доработки 23.12.2022
Принята к публикации 25.12.2022
- EDN: FNAYSC
- DOI: 10.31857/S0044457X22602358
Аннотация
Изучено поведение керамического материала Ta4HfC5–30 об. % SiC под воздействием сверхзвукового потока диссоциированного азота, что необходимо для оценки перспектив применения подобных материалов в бескислородных газовых средах при температурах >1800°C. Установлено, что в результате нагрева поверхности до ~2020°C через несколько минут наблюдается уменьшение температуры до ~1915°C с последующим медленным снижением до 1881°С. Вероятно, это связано с протекающими на поверхности химическими процессами и формированием чрезвычайно шероховатой микроструктуры. Определена скорость уноса, показано, что ни при вводе образца в высокоэнтальпийную струю азота, ни при резком охлаждении (падение температуры на ~880°С за 9–10 с) не наблюдается растрескивания образца или отслоения приповерхностной области. Данные РФА и Раман-спектроскопии позволяют говорить о полном удалении из поверхностного слоя карбида кремния и преобразовании сложного карбида тантала-гафния в соответствующий нитрид.
ВВЕДЕНИЕ
В последние годы вновь растет интерес к созданию керамических материалов на основе сверхтугоплавких карбидов, преимущественно монокарбидов (MC) элементов IV и VБ-групп [1–7]. Вероятно, это связано с возможностью повысить трещиностойкость за счет образования так называемых “керамических высокоэнтропийных сплавов” – твердых растворов изоструктурных монокарбидов металлов, число компонентов в которых должно быть >4–5 [8–16]. Тем не менее, высокая практическая значимость для использования в бескислородной среде наблюдается для менее многокомпонентной системы TaC–HfC [17–24], для которой свойственны рекордно высокие температуры плавления [25–28]. В связи с высокими температурами плавления MC (преимущественно в интервале 3000–4000°С [29, 30]) и особенностями химической связи в структуре кубических карбидов для получения достаточно плотных образцов требуется использовать повышенные температуры консолидации (2000–2200°C), что приводит к негативному явлению роста зерен формирующейся керамики. Данное обстоятельство ведет к разработке методов более низкотемпературной реакционной консолидации [22, 31], а также к использованию высокодисперсных спекающих или модифицирующих компонентов, например, нанокристаллического карбида кремния.
Помимо положительного влияния на протекание процесса консолидации [32, 33], введение SiC может способствовать улучшению механических свойств керамических материалов на основе карбидов тантала-гафния [34–38], а также в некоторой мере повысить стойкость такого рода материалов к окислению. Например, в исследовании [34] для материалов Ta4HfC5 показано, что введение в их состав 10 об. % SiC позволяет повысить относительную плотность с 98.8 до 99.6% при их изготовлении методом свободного спекания при температуре 2100°С. Модифицирование же 30 об. % карбида кремния позволяет в 2.2 раза повысить теплопроводность и на 21% – вязкость разрушения. Для образцов состава Ta4HfC5–27 об. % SiC, полученных методом реакционного спекания, отмечено увеличение на 45.9% трещиностойкости и на 23.5% прочности на изгиб [35].
Применение искрового плазменного спекания для изготовления столь тугоплавкой керамики имеет неоспоримые преимущества благодаря высоким скоростям нагрева и свойственному для данного метода механизму спекания [8, 39–42]. Сочетание подходов реакционного искрового плазменного спекания и введения в состав керамики Ta4HfC5 30 об. % нанокристаллического карбида кремния позволило в нашей предыдущей работе улучшить процесс консолидации материала и его стойкость к окислению в потоке воздуха в интервале температур 25–1400°С, а также под воздействием лазерного излучения в воздушной атмосфере [33]. Однако основное применение материалов на основе сверхтугоплавких карбидов металлов системы TaC–HfC предполагается под воздействием высоких температур (>1800–2000°C) в бескислородных газовых средах, включая высокоскоростные газовые потоки. В связи с этим крайне важной является разработка экспериментальных подходов моделирования поведения полученных материалов в результате нагрева сверхзвуковыми потоками условно химически нейтральных газов, например, в потоке частично диссоциированного азота. Особенно перспективными такие исследования выглядят в плане разработки материалов для авиакосмической техники, поскольку состав атмосферы на различных космических телах существенно отличается от атмосферы Земли, например, атмосфера Титана, являющегося спутником Сатурна, на 98.4% состоит из азота [43, 44].
Целью настоящей работы является изучение химических процессов, протекающих на поверхности керамического материала Ta4HfC5–30 об. % SiC под воздействием сверхзвукового потока диссоциированного азота.
ЭКСПЕРИМЕНТАЛЬНАЯ ЧАСТЬ
В работе использовали следующие реактивы: пентахлорид тантала TaCl5 (99.99%, Ланхит, Россия), тетраэтоксисилан Si(OC2H5)4 марки “ос. ч.” (ЭКОС-1, Россия), бакелитовый лак ЛБС-1 (Карболит, Россия), муравьиную кислоту СН2О2 (>99%, Спектр-Хим, Россия), 1-бутанол С4H9OH (>98%, Химмед, Россия), изоамиловый спирт C5H11OH (>98%, ЭКОС-1, Россия).
Керамический материал Ta4HfC5–30 об. % SiC получали с помощью реакционного искрового плазменного спекания композиционного порошка Ta2O5–HfO2–C–SiC, методики получения исходного порошка и керамических образцов подробно описаны в [33]. Контролируемый гидролиз синтезированных прекурсоров (Ta(OC4H9)4 и [Hf(O2C5H7)(OC5H11)3]) осуществляли в присутствии в растворе диспергированного порошка SiC и полимерного источника углерода (фенолформальдегидная смола – бакелитовый лак). После гелеобразования, сушки и карбонизации ксерогеля (600°С, 2 ч, динамический вакуум) полученный высокодисперсный порошок Ta2O5–HfO2–C–SiC загружали в графитовые пресс-формы и направляли на искровое плазменное спекание (ступенчатый нагрев, максимальная температура спекания 1800°С, время выдержки 5 мин, давление 20.7 МПа, динамический вакуум). Относительная плотность керамического материала Ta4HfC5–30 об. % SiC составляла 73 ± 1%.
Реакционное искровое плазменное спекание композиционного порошка проводили на установке SPS-515S фирмы Dr.Sinter·LABTM (Япония).
Рентгенограммы полученного керамического материала и его поверхности после воздействия сверхзвукового потока диссоциированного азота записывали на рентгеновском дифрактометре Bruker D8 Advance (излучение CuKα, разрешение 0.02° при накоплении сигнала в точке в течение 0.3 с). Рентгенофазовый анализ (РФА) выполняли с применением программы MATCH! – Phase Identification from Powder Diffraction, Version 3.8.0.137 (Crystal Impact, Germany), база данных Crystallography Open Database (COD).
Раман-спектры регистрировали на спектрометре комбинационного рассеяния SOL Instruments Confotec NR500 (объектив 40×/0.75, лазер 532 нм). Во избежание окислительных процессов мощность на образцах не превышала 2 мВт.
Исследование поведения керамики при воздействии на нее высокоэнтальпийного сверхзвукового потока азота выполняли на 100-киловаттном высокочастотном индукционном плазмотроне ВГУ-4. Для этого применяли водоохлаждаемое коническое сопло с диаметром выходного сечения 50 мм; расстояние от выходного сечения сопла до образца составляло 30 мм, массовый расход азота – 3.6 г/с. Давление в камере находилось в интервале 8.5–8.8 × 102 Па. Образец, представляющий собой цилиндр диаметром 15 мм и толщиной 2.6 мм, закрепляли в водоохлаждаемой модели, геометрия которой подробно описана в работах [45–48]. Образцы устанавливали на трении в гнезде водоохлаждаемого калориметра, зазор заполняли гибкой теплоизоляцией на основе SiC и углевойлока с целью минимизации тепловых потерь.
Измерение усредненной температуры поверхности нагретого образца в его центральной области (диаметр области визирования ~5 мм) проводили с применением инфракрасного пирометра Mikron M770S в режиме пирометра спектрального отношения (температурный интервал 1000–3000°C). Точность измерений пирометра в этом диапазоне температур составляла ±15°С. Изучение распределения температур по поверхности образца в ходе воздействия на него высокоэнтальпийных струй азота проводили с использованием термовизора Тандем VS-415U. Запись термоизображений выполняли при установленном значении спектрального коэффициента излучения ελ (на длине волны 0.9 мкм), равном 1, поскольку в ходе воздействия предполагали изменение ελ. Коррекция к реальным значениям средних температур центральной области, определенная с использованием пирометра спектрального отношения, позволила оценить значения спектрального коэффициента излучения и его изменение в ходе воздействия. Методика определения теплового потока к лицевой поверхности образца подробно описана в [46].
Исследование особенностей микроструктуры поверхности полученных материалов до и после воздействия сверхзвукового потока диссоциированного азота осуществляли методом растровой электронной микроскопии (РЭМ) на трехлучевой рабочей станции NVision 40 Carl Zeiss с ускоряющим напряжением 1 и 20 кВ.
РЕЗУЛЬТАТЫ И ОБСУЖДЕНИЕ
Закрепленный в водоохлаждаемой модели керамический образец вводили в высокоэнтальпийную струю при мощности анодного питания плазмотрона (N) 45 кВт и далее выдерживали при фиксированных условиях в течение 5 мин (300 с). На рис. 1 показано изменение средней температуры поверхности образца (по данным пирометра спектрального отношения) в ходе воздействия сверхзвуковой струи диссоциированного азота. Видно, что на начальном этапе нагрева (>35–38 с) отмечается установление температуры порядка 1990–2017°С (с небольшой тенденцией к росту), в то время как во временном интервале 100–143 с происходит достаточно резкое уменьшение температуры на 100 град до ~1915°C с последующим медленным снижением до 1881°С (на 300 с воздействия).
Рис. 1.
Изменение средней температуры поверхности образца (t) в ходе термохимического воздействия при фиксированных мощности анодного питания (N) и давлении (P) в барокамере плазмотрона.
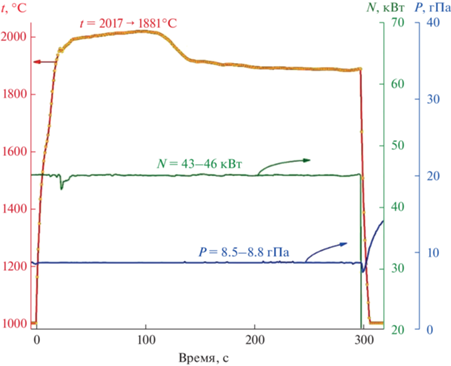
Изучение распределения температуры по поверхности керамического образца (рис. 2) с использованием термовизора показало, что на первых секундах воздействия отмечается большое различие данного параметра в центре и в периферических регионах. Так, на 14 с после введения образца в струю диссоциированного азота перепад температур достигает ~350°С. Однако уже на 22–23 с происходит некоторое выравнивание температурного поля: разница температур между центром и краями образца не превышает 220°С, а на 300 с данный параметр снижается до 145°С.
Рис. 2.
Распределение температуры вдоль диаметра образца и соответствующие тепловые изображения в различные моменты воздействия.
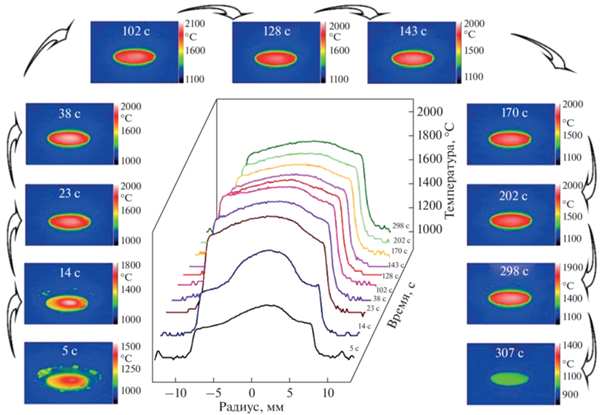
Сопоставление данных по средним температурам в центральной части образца, полученных с применение ИК-пирометра спектрального отношения и термовизора, позволило оценить изменение спектрального коэффициента излучения в ходе воздействия. Установлено, что в начале воздействия (ориентировочно до 100–120 с) значение данного параметра находится в интервале 0.75–0.83, а далее наблюдается рост ελ выше 0.9. Вероятно, это связано с протекающими на поверхности химическими процессами и абляцией.
Тепловой поток к поверхности образца, измеренный с помощью калориметра [47], в момент выключения установки (300 c) составляет 172 Вт/см2, а интегральный коэффициент излучения, полученный из сопоставления данных пирометра полного излучения “Кельвин” и пирометра спектрального отношения Mikron M770S, равен εt = 0.72. Тепловой поток к поверхности образца в момент достижения максимальной температуры 2017°С (106 с) составляет 168 Вт/см2, при этом интегральный коэффициент излучения равен εt = = 0.52. Таким образом, тепловой поток к поверхности образца при постоянной мощности ВЧ-генератора плазмотрона также практически постоянный для характерных точек эксперимента. Аналогично спектральному коэффициенту излучения отмечается тенденция к росту интегрального коэффициента излучения поверхности в ходе воздействия высокоэнтальпийного потока азота.
После завершения процесса нагрева при натекании в барокамеру воздуха происходит охлаждение образца: снижение средней температуры поверхности с 1881 до значения <1000°С происходит в течение 9–10 с. Потеря массы образца в результате воздействия на него сверхзвукового потока диссоциированного азота составляет ~1%, соответствующая скорость уноса – 3.7 × 10–3 г см–2 мин–1.
Рентгенофазовый анализ поверхности образца после термохимического воздействия на нее показал (рис. 3), что в результате эксперимента происходит значительное изменение химического и фазового состава. В частности, отсутствуют рефлексы исходных фаз сложного карбида тантала-гафния состава Ta4HfC5 [20, 49, 50] и карбида кремния [51]. Основной фазой на поверхности керамики Ta4HfC5–30 об. % SiC является нитрид тантала-гафния (на основе высокотемпературной гексагональной фазы TaN [52]). Полнопрофильным методом Ритвельда с применением программного обеспечения TOPAS рассчитаны значения параметров кристаллической решетки TaN на базе пр. гр. симметрии P63mc гексагональной сингонии. Значения составили: a = 3.0523 и c = = 4.9523 Å, что несколько отличается от справочных величин (a = 3.0500 и c = 4.9400 Å). Следует отметить, что расчетное значение параметра a отличается незначительно, в то время как параметр c гораздо больше приведенного в литературе. Данный факт может быть связан с частичной заменой атомов тантала в кристаллической решетке TaN атомами гафния и формированием дефектной структуры по оси c, что подтверждается смещением самого интенсивного рефлекса к рефлексу (200) кубической фазы HfN (~39°). Рефлексов кубических фаз HfN [53], Hf3N4 [54] и сложного нитрида TaHfN2 [55] на рентгенограмме не найдено. Помимо гексагонального (Ta, Hf)N после воздействия на образец потока диссоциированного азота при температуре ~1880–2020°С на поверхности присутствуют примеси оксидов тантала(V) [56] и гафния, причем для HfO2 характерно одновременное присутствие двух кристаллических модификаций – моноклинной [57] и орторомбической [58]. Наличие на поверхности керамического материала Ta2O5 и HfO2, вероятно, связано со взаимодействием не остывшего до конца материала с натекающим в барокамеру плазмотрона воздухом после завершения эксперимента.
Рис. 3.
Рентгенограммы поверхности исходного образца состава Ta4HfC5–30 об. % SiC (1) и после воздействия на него потока диссоциированного азота (2).
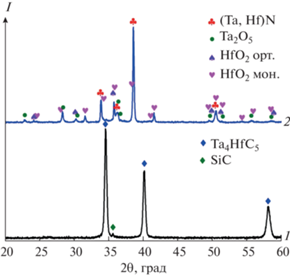
Поскольку внешний вид поверхности образца после воздействия существенно меняется (бронзовый цвет изменился на бархатно-черный), для проверки гипотезы существования на поверхности аморфного углерода, образовавшегося при деструкции карбидов металлов, состав поверхностного слоя был изучен также с помощью Раман-спектрокопии (рис. 4). Исходный образец керамического материала Ta4HfC5–30 об. % SiC имеет характерные Раман-моды карбидов тантала и гафния ω1–ω4, максимумы которых находятся при ~162, 305, 484 и 615 см–1 соответственно, что хорошо согласуется с представленными в [59] данными по характерным наборам мод первого порядка для карбидов тантала и гафния. Дополнительно в Раман-спектрах присутствует мода ωSiC (ТО) при 783 см–1, относящаяся к SiC, а также моды ωD и ωG при 1348 и 1583 см–1, отвечающие различным формам углерода [60]. Полученные D- и G-моды могут относиться как к остаточному аморфному углероду, так и к углероду в составе карбидов кремния, гафния и тантала.
Рис. 4.
Раман-спектры поверхности исходного образца Ta4HfC5–30 об. % SiC (1) и после воздействия на него сверхзвукового потока диссоциированного азота (2).
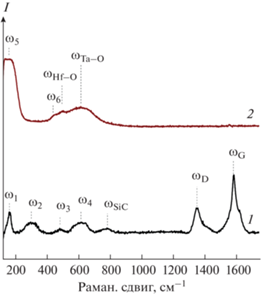
После воздействия на образец струи диссоциированного азота Раман-спектр поверхности претерпевает значительные изменения. Характерные для исходного спектра моды ω1–ω4, ωSiС, ωD и ωG, соответствующие карбидам тантала-гафния, кремния и углероду, отсутствуют. Мода ω1 для керамики Ta4HfC5–30 об. % SiC становится уширенной и трансформируется в моду ω5 с размытым максимумом при 136–177 см–1. Подобные изменения, вероятно, связаны с образованием нитрида тантала-гафния на поверхности образца, для которого характерны моды с максимумами, попадающими в этот диапазон, а также мода ω6 при ~440 см–1 [54, 61, 62]. Дополнительно в спектре присутствуют моды ωHf–O и ωTa–O с максимумами при ~501 и 614 см–1, относящиеся к моноклинному HfO2 [63] и β-Ta2O5 [64]. Наличие большого уширенного гало в диапазоне 400–750 см–1 может быть также связано с образованием нитрида тантала-гафния, для которого характерна уширенная оптическая полоса (О) в указанном диапазоне [61, 62]. Полное отсутствие в спектрах D- и G-мод углерода может свидетельствовать об отсутствии на поверхности аморфного углерода (как продукта взаимодействия карбидов металлов с атомарным азотом).
Исследование микроструктуры поверхности образца Ta4HfC5–30 об. % SiC после воздействия на него сверхзвукового потока диссоциированного азота выполнено с применением растровой электронной микроскопии (рис. 5). Видно, что поверхность претерпела существенные изменения: она полностью покрыта очень пористыми агрегатами, по структуре схожими с кораллами. Размер агрегата можно оценить в интервале 2–5 мкм, что касается пор, то их размер различается от 200–400 до 50–80 нм. Такое увеличение удельной площади поверхности по сравнению с исходным образцом, который при общей пористости 27 ± 1% состоит из плотных спеченных непористых зерен размером <1 мкм, может приводить к значимому изменению оптических свойств, включая и коэффициент излучения.
Рис. 5.
Микроструктура поверхности керамического образца Ta4HfC5–30 об. % SiC после воздействия на него потока диссоциированного азота по данным РЭМ: а–в, д, е – по данным детектора вторичных электронов, г – в режиме контраста по среднему атомному номеру; а–д – ускоряющее напряжение 1 кВ, е – 20 кВ.
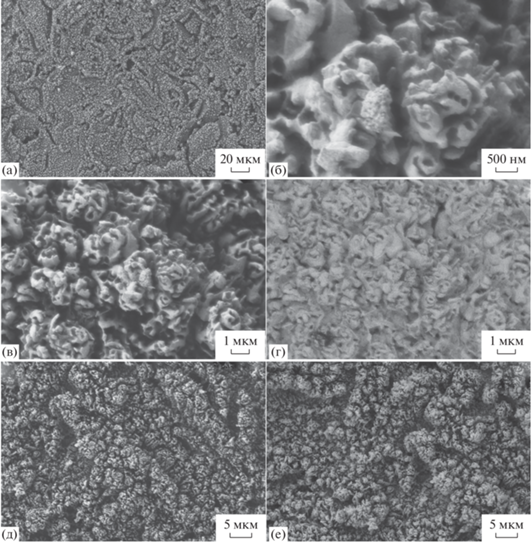
Резюмируя полученные данные, необходимо констатировать, что под воздействием высокоскоростного потока диссоциированного азота, хоть и с низкой скоростью, происходит деградация ультравысокотемпературного керамического материала, связанная не только с абляцией под воздействием плазмы, но и с протекающими химическими процессами. Наиболее вероятные реакции карбида кремния с атомарным азотом (уравнения (1), (2)) отвечают образованию газообразного кремнийсодержащего продукта SiN (присутствие на поверхности твердого Si3N4 не установлено ни с применением РФА, ни с помощью Раман-спектроскопии) и газообразного CN (уравнение (1)). При этом протекание реакции (2) с образованием в конденсированной фазе углерода экспериментально не доказано.
(1)
${\text{SiC}}\left( {\text{к}} \right) + 2{\text{N}}\left( {\text{г}} \right) = {\text{SiN}}({\text{г}}) + {\text{CN}}({\text{г}}),$(2)
${\text{SiC}}\left( {\text{к}} \right) + {\text{N}}\left( {\text{г}} \right) = {\text{SiN}}({\text{г}}) + {\text{C}}({\text{к}}),$(3)
$\begin{gathered} ({\text{Ta}},{\text{Hf}}){\text{C}}\left( {\text{к}} \right) + 2{\text{N}}\left( {\text{г}} \right) = \\ = ({\text{Ta}},{\text{Hf}}){\text{N}}({\text{к}}) + {\text{CN}}({\text{г}}),~ \\ \end{gathered} $(4)
$({\text{Ta}},{\text{Hf}}){\text{C}}\left( {\text{к}} \right) + {\text{N}}\left( {\text{г}} \right) = ({\text{Ta}},{\text{Hf}}){\text{N}}({\text{к}}) + {\text{C}}({\text{к}}).$Взаимодействие сверхтугоплавкого карбида тантала-гафния с атомарным азотом, судя по данным РФА, также связано с формированием нитридной фазы в конденсированном состоянии (уравнения (3), (4)). При этом более вероятно протекание реакции с образованием газообразного циана (уравнение (3)), т. к. на поверхности использованными методами анализа не удалось установить присутствие углерода.
ЗАКЛЮЧЕНИЕ
Изучено поведение керамического материала на основе сверхтугоплавкого карбида тантала-гафния Ta4HfC5, модифицированного 30 об. % высокодисперсного карбида кремния, под воздействием сверхзвукового потока диссоциированного азота с помощью высокочастотного индукционного плазмотрона ВГУ-4. Показано, что на второй–третьей минуте воздействия происходит относительно быстрое (в течение 45 с) уменьшение средней температуры поверхности с 2017 до ~1915°C с последующим медленным снижением до 1881°С, что может быть связано с изменением химического состава поверхности.
Изучение фазового состава методами РФА и Раман-спектроскопии позволяет констатировать удаление карбида кремния из поверхностного слоя керамики Ta4HfC5–30 об. % SiC и превращение кубического сложного карбида тантала-гафния в гексагональную фазу нитрида (Ta, Hf)N благодаря воздействию химически активного атомарного азота при температуре ~1880–2020°С. Формирование в результате такого воздействия на поверхности образца высокопористого слоя продуктов реакции с кораллоподобной микроструктурой может также способствовать повышению спектральной и интегральной излучательной способности, что наблюдалось на третьей минуте эксперимента.
Выполненное исследование показало перспективность полученного керамического материала Ta4HfC5–30 об. % SiC для применения при температурах >1800°C в бескислородных газовых средах.
Список литературы
He R., Fang L., Han T. et al. // J. Eur. Ceram. Soc. 2022. V. 42. № 13. P. 5220. https://doi.org/10.1016/j.jeurceramsoc.2022.06.039
Calzolari A., Oses C., Toher C. et al. // Nat. Commun. 2022. V. 13. № 1. P. 5993. https://doi.org/10.1038/s41467-022-33497-1
Esmaeili M.M., Mahmoodi M., Mokhtarzade A. et al. // J. Mater. Eng. Perform. 2022. V. 31. № 9. P. 7719. https://doi.org/10.1007/s11665-022-06766-9
Kelly J.P., Vakharia V.S., Novitskaya E. et al. // Adv. Eng. Mater. 2022. V. 24. № 8. P. 2200026. https://doi.org/10.1002/adem.202200026
Geng X., Xu W., Huang X. et al. // J. Am. Ceram. Soc. 2022. V. 105. № 7. P. 4942. https://doi.org/10.1111/jace.18416
Savvatimskiy A.I., Onufriev S.V., Valyano G.V. et al. // Ceram. Int. 2022. V. 48. № 14. P. 19655. https://doi.org/10.1016/j.ceramint.2022.03.102
Shcherbakov V.A., Gryadunov A.N., Semenchuk I.E. et al. // Int. J. Self-Propagating High-Temperature Synth. 2022. V. 31. № 2. P. 57. https://doi.org/10.3103/S1061386222020091
Jin X., Hou C., Zhao Y. et al. // Ceram. Int. 2022. V. 48. № 23. P. 35445. https://doi.org/10.1016/j.ceramint.2022.08.147
Wang P., Xu Z., Qin B. et al. // Vacuum. 2022. V. 205. P. 111464. https://doi.org/10.1016/j.vacuum.2022.111464
Cheng Z., Lu W., Chen L. et al. // J. Eur. Ceram. Soc. 2022. V. 42. № 13. P. 5280. https://doi.org/10.1016/j.jeurceramsoc.2022.05.068
Zhao S. // J. Eur. Ceram. Soc. 2022. V. 42. № 13. P. 5290. https://doi.org/10.1016/j.jeurceramsoc.2022.05.046
Li Z., Chen L., Chang F. et al. // Ceram. Int. 2022. V. 48. № 20. P. 30826. https://doi.org/10.1016/j.ceramint.2022.07.036
Xia M., Lu N., Chen Y. et al. // Int. J. Refract. Met. Hard Mater. 2022. V. 107. P. 105859. https://doi.org/10.1016/j.ijrmhm.2022.105859
Mao H.-R., Dong E.-T., Jin S.-B. et al. // J. Eur. Ceram. Soc. 2022. V. 42. № 10. P. 4053. https://doi.org/10.1016/j.jeurceramsoc.2022.03.054
Schwind E.C., Reece M.J., Castle E. et al. // J. Am. Ceram. Soc. 2022. V. 105. № 6. P. 4426. https://doi.org/10.1111/jace.18400
Guo W., Hu J., Ye Y. et al. // Ceram. Int. 2022. V. 48. № 9. P. 12790. https://doi.org/10.1016/j.ceramint.2022.01.149
Wolfe D.E., Albert P.E., Ryan C.J. et al. // J. Eur. Ceram. Soc. 2022. V. 42. № 2. P. 327. https://doi.org/10.1016/j.jeurceramsoc.2021.10.014
Zou X., Ni D., Chen B. et al. // J. Am. Ceram. Soc. 2021. V. 104. № 12. P. 6601. https://doi.org/10.1111/jace.18007
Zhang Y., Li S., Li N. et al. // J. Alloys Compd. 2021. V. 884. P. 161040. https://doi.org/10.1016/j.jallcom.2021.161040
Simonenko E.P., Ignatov N.A., Simonenko N.P. et al. // Russ. J. Inorg. Chem. 2011. V. 56. № 11. P. 1681. https://doi.org/10.1134/S0036023611110258
Simonenko E.P., Simonenko N.P., Petrichko M.I. et al. // Russ. J. Inorg. Chem. 2019. V. 64. № 11. P. 1317. https://doi.org/10.1134/S0036023619110196
Simonenko E.P., Simonenko N.P., Lysenkov A.S. et al. // Russ. J. Inorg. Chem. 2020. V. 65. № 3. P. 446. https://doi.org/10.1134/S0036023620030146
Simonenko E.P., Simonenko N.P., Gordeev A.N. et al. // J. Eur. Ceram. Soc. 2021. V. 41. № 2. P. 1088. https://doi.org/10.1016/j.jeurceramsoc.2020.10.001
Simonenko E.P., Simonenko N.P., Nagornov I.A. et al. // Russ. J. Inorg. Chem. 2021. V. 66. № 12. P. 1887. https://doi.org/10.1134/S0036023621120172
Agte C., Alterthum H. // Z. Techn. Phys. 1930. V. 6. P. 182.
Andrievskii R.A., Strel’nikova N.S., Poltoratskii N.I. et al. // Powder Met. Ceram. 1967. V. 6. № 1. P. 65. https://doi.org/10.1007/BF00773385
Cedillos-Barraza O., Manara D., Boboridis K. et al. // Sci. Rep. 2016. V. 6. № 1. P. 37962. https://doi.org/10.1038/srep37962
Savvatimskiy A.I., Onufriev S.V., Muboyadzhyan S.A. // J. Eur. Ceram. Soc. 2019. V. 39. № 4. P. 907. https://doi.org/10.1016/j.jeurceramsoc.2018.11.030
Pierson H.O. // Handbook of Refractory Carbides and Nitrides: Properties, Characteristics, Processing and Applications, Park Ridge: Noyes Publications, 1996.
Самсонов Г.В. // Тугоплавкие соединения. Справочник по свойствам и применению. M.: Металлургиздат, 1963.
Shapkin N.P., Papynov E.K., Shichalin O.O. et al. // Russ. J. Inorg. Chem. 2021. V. 66. № 5. P. 629. https://doi.org/10.1134/S0036023621050168
Sun J., Zhao J., Chen Y. et al. // Composites, Part B: Eng. 2022. V. 231. P. 109586. https://doi.org/10.1016/j.compositesb.2021.109586
Simonenko E.P., Simonenko N.P., Papynov E.K. et al. // Ceraics. Int. 2023. V. 49. № 6. P. 9691–9701. https://doi.org/10.1016/j.ceramint.2022.11.140
Zhang B., Yin J., Chen J. et al. // J. Eur. Ceram. Soc. 2018. V. 38. № 4. P. 1227. https://doi.org/10.1016/j.jeurceramsoc.2017.10.025
Zhang B., Yin J., Huang Y. et al. // J. Eur. Ceram. Soc. 2018. V. 38. № 16. P. 5610. https://doi.org/10.1016/j.jeurceramsoc.2018.08.021
Zhang H., Akhtar F. // Ceramics. 2020. V. 3. № 3. P. 359. https://doi.org/10.3390/ceramics3030032
Vinci A., Zoli L., Sciti D. et al. // J. Eur. Ceram. Soc. 2019. V. 39. № 4. P. 780. https://doi.org/10.1016/j.jeurceramsoc.2018.11.017
Zhang C., Zhang Y., Cao K. et al. // Ceram. Int. 2021. V. 47. № 5. P. 6463. https://doi.org/10.1016/j.ceramint.2019.09.229
Rana D., Balani K. // Int. J. Refract. Met. Hard Mater. 2023. V. 110. P. 106024. https://doi.org/10.1016/j.ijrmhm.2022.106024
Xu J., Zhao F., He S. et al. // J. Am. Ceram. Soc. 2022. V. 105. № 6. P. 3838. https://doi.org/10.1111/jace.18380
Sharma S.K., Chaudhary K., Gupta Y. et al. // Int. J. Appl. Ceram. Technol. 2022. V. 19. № 3. P. 1691. https://doi.org/10.1111/ijac.13993
Liu C., Wang A., Tian T. et al. // J. Eur. Ceram. Soc. 2021. V. 41. № 15. P. 7469. https://doi.org/10.1016/j.jeurceramsoc.2021.07.047
Gordeev A.N., Kolesnikov A.F., Sakharov V.I. // Fluid Dyn. 2017. V. 52. № 6. P. 786. https://doi.org/10.1134/S0015462817060076
Carandente V., Savino R., Esposito A. et al. // Exp. Therm. Fluid Sci. 2013. V. 48. P. 97. https://doi.org/10.1016/j.expthermflusci.2013.02.012
Kolesnikov A.F., Lukomskii I.V., Sakharov V.I. et al. // Fluid Dyn. 2021. V. 56. № 6. P. 897. https://doi.org/10.1134/S0015462821060070
Kolesnikov A.F., Kuznetsov N.T., Murav’eva T.I. et al. // Fluid Dyn. 2022. V. 57. № 4. P. 513. https://doi.org/10.1134/S0015462822040061
Lukomskii I.V., Chaplygin A.V., Kolesnikov A.F. // A device for measuring the heat flux to the surface of a material heated in a jet of high-enthalpy gas to a high temperature, Patent RU 205572, 2021.
Simonenko E.P., Simonenko N.P., Kolesnikov A.F. et al. // Materials (Basel). 2022. V. 15. № 23. P. 8507. https://doi.org/10.3390/ma15238507
Feng L., Kim J.-M., Lee S.-H. et al. // J. Am. Ceram. Soc. 2016. V. 99. № 4. P. 1129. https://doi.org/10.1111/jace.14144
Jiang J., Wang S., Li W. // J. Am. Ceram. Soc. 2016. V. 99. № 10. P. 3198. https://doi.org/10.1111/jace.14436
Burdick C.L., Owen E.A. // J. Am. Chem. Soc. 1918. V. 40. № 12. P. 1749. https://doi.org/10.1021/ja02245a001
Wyckoff R.W.G. // Cryst. Struct. 1963. V. 1. P. 85.
Rudy E. // Metall. Mater. Trans. B. 1970. V. 1. № 5. P. 1249. https://doi.org/10.1007/BF02900238
Zerr A., Miehe G., Riedel R. // Nat. Mater. 2003. V. 2. № 3. P. 185. https://doi.org/10.1038/nmat836
Gatterer J., Dufek G., Ettmayer P. et al. // Monatsh. Chem. – Chem. Mon. 1975. V. 106. № 5. P. 1137. https://doi.org/10.1007/BF00906226
Aleshina L.A., Loginova S.V. // Crystallogr. Reports. 2002. V. 47. № 3. P. 415. https://doi.org/10.1134/1.1481927
Whittle K.R., Lumpkin G.R., Ashbrook S.E. // J. Solid State Chem. 2006. V. 179. № 2. P. 512. https://doi.org/10.1016/j.jssc.2005.11.011
Ohtaka O., Yamanaka T., Kume S. // J. Ceram. Soc. Japan. 1991. V. 99. № 1153. P. 826. https://doi.org/10.2109/jcersj.99.826
Wipf H., Klein M.V., Williams W.S. // Phys. Status Solid. 1981. V. 108. № 2. P. 489. https://doi.org/10.1002/pssb.2221080225
Tallo I., Thomberg T., Kurig H. et al. // Carbon. 2014. V. 67. P. 607. https://doi.org/10.1016/j.carbon.2013.10.034
Stoehr M., Shin C.-S., Petrov I. et al. // J. Appl. Phys. 2007. V. 101. № 12. P. 123509. https://doi.org/10.1063/1.2748354
Valleti K. // J. Vac. Sci. Technol., A: Vacuum. Surfaces. Film. 2009. V. 27. № 4. P. 626. https://doi.org/10.1116/1.3136858
Wu R., Zhou B., Li Q. et al. // J. Phys. D. Appl. Phys. 2012. V. 45. № 12. P. 125304. https://doi.org/10.1088/0022-3727/45/12/125304
Devan R.S., Ho W.-D., Wu S.Y. et al. // J. Appl. Crystallogr. 2010. V. 43. № 3. P. 498. https://doi.org/10.1107/S002188981000796X
Дополнительные материалы отсутствуют.
Инструменты
Журнал неорганической химии