Журнал неорганической химии, 2022, T. 67, № 7, стр. 1032-1038
Исследование влияния температуры отжига на кристаллизацию наночастиц Nd2O3, синтезированных методом осаждения
О. Э. Абдурахмонов a, *, М. Э. Алисултанов a, Д. А. Вертаева a, А. Г. Мурадова a
a Российский химико-технологический университет им. Д.И. Менделеева
125047 Москва, Миусская пл., 9, Россия
* E-mail: odilzhon.abdurakhmonov@mail.ru
Поступила в редакцию 14.02.2022
После доработки 15.03.2022
Принята к публикации 16.03.2022
- EDN: XLOHTA
- DOI: 10.31857/S0044457X22070029
Аннотация
Химическим методом осаждения синтезированы наностержни Nd(OH)3. Термическим отжигом Nd(OH)3 получен Nd2O3. Для определения термических эффектов, при которых проходят фазовые переходы, проведены термический и рентгенофазовый анализы. По определенным термическим эффектам проведен отжиг образца при температурах 330, 635, 794°С. С помощью сканирующей и просвечивающей электронной микроскопии определены размеры полученных наностержней соединений неодима. Методом инфракрасной спектроскопии изучен процесс дегидратации OH-групп при температурном отжиге. Во время отжига аморфного порошка при температуре 330°С получены наностержни Nd(OH)3 со средней длиной 29 нм и диаметром 4 нм. Выявлено, что при температуре 794°С образовывались наностержни Nd2O3 с гексагональной кристаллической структурой. Средний размер наностержней в длине увеличился до 118 нм, в диаметре – до 28 нм.
ВВЕДЕНИЕ
На сегодняшний день наблюдается тенденция развития рынка электродвигателей и электроники в общем. Для миниатюризации электродвигателей и электроники требуется использование постоянных магнитов с высокими магнитными характеристиками и маленьким размером, этим обусловлен рост рынка постоянных магнитов [1]. Во многих электронных устройствах используются компоненты хранения информации, динамики и т.д., они требуют использования постоянных магнитов с высокими магнитными характеристиками [2, 3]. Важными характеристиками являются коэрцитивная сила и намагниченность, на них влияют такие факторы, как размер, форма и ориентация частиц [4].
На сегодняшний день постоянные магниты на основе сплава Nd–Fe–B имеют наибольшие значения коэрцитивной силы и магнитной энергии, что позволяет эффективно использовать их в устройствах, подверженных воздействию высоких внешних размагничивающих магнитных полей [5].
Физические методы – основные способы получения постоянных магнитов Nd–Fe–B, в их основе лежит процесс получения сплава Nd–Fe–B с последующим измельчением до порошков. Далее проводят ориентацию полученных порошков в магнитном поле и спекание [6–9]. Однако физические методы имеют множество недостатков таких, как высокая энергозатратность, сложность контроля размера получаемых частиц, использование в качестве исходного сырья дорогостоящих металлов высокой чистоты, длительное время производства [10]. Все вышеперечисленные факторы влияют на магнитные характеристики и себестоимость получаемой продукции [11]. Следовательно, необходима разработка альтернативного метода получения наноструктурированного сплава Nd–Fe–B.
Химические методы получения наноструктурированного сплава Nd–Fe–B являются многообещающей альтернативой физическим методам из-за их простоты и масштабируемости [12–14]. Они позволяют контролировать размер получаемых наночастиц. Кроме того, химические методы имеют такие преимущества, как контролируемый гранулометрический состав, низкие энергозатраты, что влияет на магнитные характеристики и стоимость готовой продукции [15–17].
Ранее мы сообщали о химическом синтезе наноструктурированного сплава Nd–Fe–B [18]. Для получения которого важна однородность и большая удельной площадь поверхности исходных наночастиц оксида неодима, оксида железа и оксобората железа, используемых в качестве основных компонентов для получения наноструктурированного сплава Nd–Fe–B. Эти факторы очень важны для высокой реакционной способности и низкой температуры образования наноструктурированного сплава Nd–Fe–B.
На сегодняшний день представлено небольшое количество работ по получению наночастиц оксида неодима. Для синтеза наночастиц гидроксида и оксида неодима применяют различные методы: гидротермальный [19–21], золь-гель [22, 23], темплатный [24–26], микроэмульсионный [27], осаждения [28–30], электрохимический [31], плазменный [32] и др. Химический метод осаждения – это один из простых, дешевых, он требует небольшого количества специального оборудования и условий [33]. Имеются сообщения о синтезе наночастиц Nd2O3 этим методом. Например, в работе [28] получили наночастицы Nd2O3 термическим разложением осадка, полученного взаимодействием нитрата неодима с осадителем NH4HCO3. В данной работе не обсуждался процесс разложения полученных наночастиц до Nd2O3 и их фазовый состав.
Цель работы – исследование влияния температуры отжига на кристаллизацию наночастиц Nd2O3. Задачи исследования: синтезировать наностержни (НС) Nd2O3, определить фазовые переходы Nd(OH)3 в NdOOH и Nd2O3.
ЭКСПЕРИМЕНТАЛЬНАЯ ЧАСТЬ
НС Nd(OH)3 получены методом осаждения. В качестве осадителя использовали гидроксид натрия. Синтез НС состоит из двух последовательных стадий. На первой стадии получили промежуточный продукт – наночастицы гидроксида неодима:
(1)
${\text{Nd}}{{\left( {{\text{N}}{{{\text{O}}}_{{\text{3}}}}} \right)}_{{\text{3}}}}{\text{ + 3NaOH }} \to {\text{ Nd}}{{\left( {{\text{OH}}} \right)}_{{\text{3}}}}{\text{ + 3NaN}}{{{\text{O}}}_{{\text{3}}}}{\text{,}}$(2)
${\text{2Nd}}{{\left( {{\text{OH}}} \right)}_{{\text{3}}}} \to {\text{N}}{{{\text{d}}}_{{\text{2}}}}{{{\text{O}}}_{{\text{3}}}} + {\text{3}}{{{\text{H}}}_{{\text{2}}}}{\text{O}}{\text{.}}$Используемые реактивы: гексагидрат нитрата неодима Nd(NO3)3 · 6H2O, гидроксид натрия NaOH с классификацией (х. ч.) и бидистиллированная вода. Готовили 0.02 М водный раствор Nd(NO3)3 и водный раствор NaOH с концентрацией 0.12 М. Термостатирование полученных растворов Nd(NO3)3 и NaOH проводили до температуры 90°С. Затем с помощью перистальтического насоса в раствор Nd(NO3)3 по каплям добавляли водный раствор NaOH. Синтез проводили при интенсивном перемешивании (1200 об./мин) с помощью магнитной мешалки и при поддержании постоянной температуры в растворе 90°С. После смешения исходных растворов полученный раствор выдерживали в течение 15 мин при заданной температуре. Полученный осадок Nd(OH)3 отделяли центрифугированием (3000 об./мин, 5 мин) и промывали 3 раза бидистиллированной водой. Затем осадок высушивали при температуре 100°С в течение 90 мин.
Для определения размера и формы НС использовали просвечивающий электронный микроскоп (ПЭМ) JEM-100CX (Jeol, Япония). Исследование НС методом сканирующей электронной микроскопии (СЭМ) выполняли с помощью JEOL JEM-6510LV. Фазовый состав образцов определяли по дифракционной картине рентгеновского излучения на поликристаллических порошках. Дифрактограммы снимали на приборе D2 Phaser (Bruker-AXS, Германия), излучение CuKa, фильтр – Ni, с графитовым монохроматором (λ = 1.54178 Å). Режим трубки (Cu) 10 мА, 30 кВ. Диапазон значений угла 2θ от 10° до 90°, шаг 0.02°, щель 0.6 мм, выдержка в точке – 1 с, дискриминатор по энергиям – 0.17–0.23 кэВ. Расшифровку спектра и расчет фазового состава осуществляли с помощью библиотеки JCPDS-ICDD с использованием специализированного программного обеспечения. Термический анализатор (STA 449 F5 Jupiter, Netzsch, Германия) использовали для записи профилей термогравиметрической/сканирующей калориметрии (ТГ/ДСК). Для измерений брали свежеприготовленный гидроксид неодима с начальной массой 8.61 мг. Анализ проводили в инертной атмосфере азота, образцы прогревали до 900°С со скоростью увеличения температуры 10 град./мин. ИК-спектры образцов получали с помощью спектрофотометра ИК-Фурье Nicolet 380 (Thermo Scientific, США) в области измерения 400–4000 см–1. Отжиг образцов проводили в муфельной печи Nabertherm (Nabertherm, Германия).
РЕЗУЛЬТАТЫ И ОБСУЖДЕНИЕ
Для изучения изменений в кристаллической структуре с повышением температуры полученные порошки гидроксида неодима исследовали методом ДСК/ТГ (рис. 1). На кривой ДСК анализа можно наблюдать несколько экзотермических эффектов при температурах 330, 559, 635 и 794°С. На производной от кривой ТГ зафиксировано два пика при температуре 330 и 635°С, которые совпадали с двумя термическими эффектами ДСК анализа. По данным ТГ анализа, первая стадия потери веса происходила постепенно, между 29–330°С. Потеря массы составила 8.92%. При последующем изменении температуры в диапазоне 330–635°С наблюдалась потеря массы 12.08%, что связано с частичной дегидратацией гидроксильных групп в Nd(OH)3. В диапазоне температур 635–900°С потеря массы составила 3.43%, это связано с полной дегидратацией. Для подробного изучения изменений, происходящих в образце при выше указанных термических эффектах ДСК/ТГ, проведен отжиг образцов при температурах 330, 635 и 794°С и РФА. На рис. 2 представлена дифракторамма образца после сушки и образцов, отожженных при температурах 330, 635 и 794°С.
Рис. 2.
Дифрактограммы: а – частиц Nd(OH)3, высушенных при 100°С, прокаленных при температуре: б – 330, в – 635, г – 794°С; е – стандартная дифрактограмма Nd(OH)3 JSPDS № 06-0601, д – стандартная дифрактограмма Nd2O3 JSPDS № 43-1023.
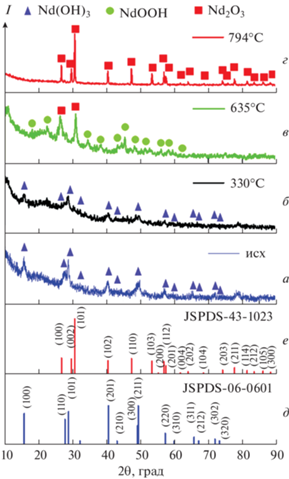
По представленным на рис. 2 дифрактограммам определен фазовый состав полученных образцов в зависимости от температуры отжига. На дифрактограмме исходного образца расположение пиков соответствуют гексагональной структуре Nd(OH)3 с пр. гр. P63/m и параметрами решетки a = b = 6.442, c = 3.756 Å по базе JSPDS № 06-0601 (рис. 2д) [34]. По ширине и высоте дифракционных пиков с помощью формулы Шеррера определен размер кристаллитов, он составлял 10 нм. Степень кристалличности образца определяли по данным РФА расчетным способом по формуле:
где χс – кристалличность образца, Ac – площадь кристаллических пиков, Aа – площадь аморфных пиков.После отжига образца при температуре 330°С можно заметить, что пики стали менее интенсивными по сравнению с исходным. Это можно объяснить тем, что более крупные частицы Nd(OH)3 могли начать рассыпаться при дегидратации, что еще сильнее ухудшило дифракцию. Это подтверждает степень кристалличности данного образца, она составила 28.61%. После отжига образцов неодима при температуре 635°С пики, относящейся к Nd(OH)3, не наблюдались. Но отмечены новые пики, относящиеся к NdOOH и Nd2O3. Образование NdOOH связано со вторым этапом дегидратации: 2Nd(OH)3 → 2NdOOH + 2H2O [35]. После отжига образца при 794°С на дифрактограмме пики, относящейся к NdOOH, не наблюдались. Все полученные пики совпадают с Nd2O3. Все полученные пики по данным JSPDS № 43-1023 [36] относятся к гексагональной структуре Nd2O3 с пр. гр. P6/mmm c параметрами решетки a = b = 6.165, c = 3.217 Å. На основании расшифровки полученных дифрактограмм сделан вывод, что Nd(OH)3 при температуре 635°С образуется смесь NdOOH и Nd2O3, а при повышении температуры до 794°С – Nd2O3.
Морфологию синтезированных частиц гидроксида неодима исследовали с помощью ПЭМ и СЭМ. Можно заметить, что полученные порошки после сушки состоят из агрегатов аморфных частиц Nd(OH)3 (рис. 3).
Рис. 3.
Изображения высушенных после синтеза исходных аморфных частиц неодима Nd(OH)3: а – СЭМ, б – ПЭМ.
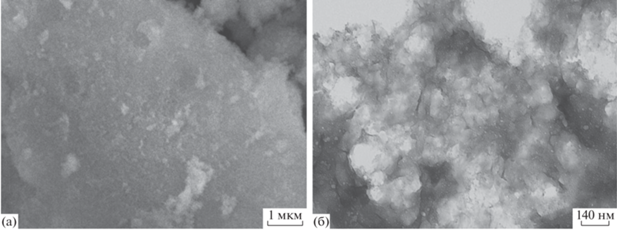
После отжига образца при 330°С (рис. 4а) частицы имели форму НС, длиной 29 нм и диаметром 4 нм. Данные образцы имели характерный для соединения Nd(OH)3 светло-сиреневый цвет. У образцов после отжига при 635°С (рис. 4в) увеличились размеры, длина до 53 нм, а диаметр – до 9 нм. При отжиге образца при 794°С (рис. 4д) средний размер частиц также увеличился: длина до 118 нм, а диаметр до 28 нм. Визуально выявлено, что при увеличении температуры отжига проходило “осветление” образца. Отожженный образец имел голубовато-серый цвет, характерный для Nd2O3.
Рис. 4.
Изображение с электронного микроскопа и распределение частиц по размерам: а – ПЭМ изображение Nd(OH)3, б – распределение наностержней Nd(OH)3 по размерам для образца, прокаленного при 330°С; в – ПЭМ изображение NdOOH, г – распределение наностержней NdOOH по размерам для образца, прокаленного при 635°С; в – ПЭМ изображение Nd2O3, е – распределение наностержней Nd2O3 по размерам для образца, прокаленного при 794°С.
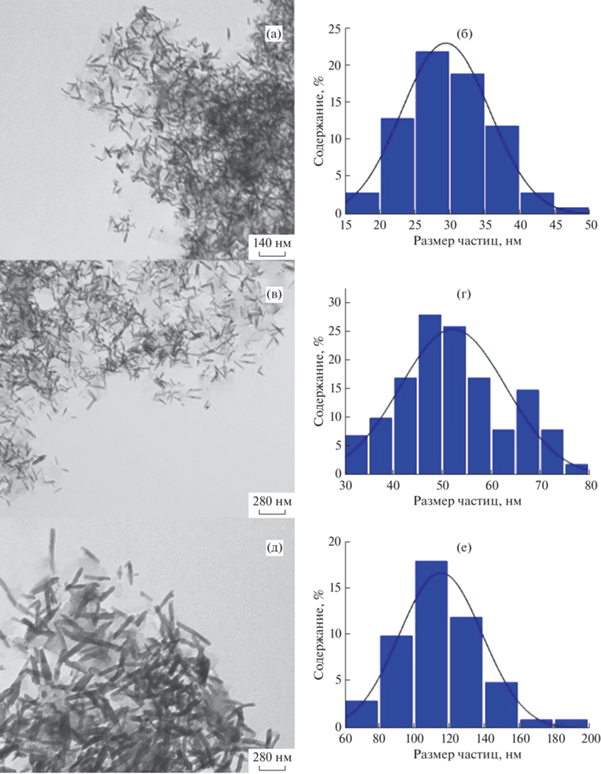
Для дальнейшего изучения структуры проанализировали ИК-спектры образцов (рис. 5). В спектре исходного образца обнаружено несколько пиков, в том числе узкий пик при 3608 см–1 и более широкий пик 3450 см–1, который можно отнести к валентному колебанию OH-группы в Nd(OH)3 [37, 38]. Пики при 684 и 847 см–1 относятся к колебаниям связи OH-группы в Nd(OH)3 [39]. Два пика при 1388 и 1495 см–1 относятся к связям соединений OH-группы в Nd(OH)3 соответственно [35].
Рис. 5.
ИК-спектры синтезированных частиц Nd(OH)3 после осаждения (а), прокаленных при 330 (б), 450 (в), 635 (г), 794°С (д).
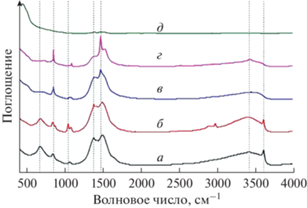
Для образцов, отожженных при температурах 330 и 450°С (рис. 5б, 5в), интенсивность колебания связей OH-группы уменьшилась. При температуре 450°C (рис. 5в) в спектре образца наблюдалось появление интенсивных пиков 857 и 1474 см–1, которые относятся к колебаниям связи OH-группы в NdOOH [33]. После отжига при температуре 635°С (рис. 5г) интенсивность пиков 857 и 1474 см–1 увеличивается. В образцах после отжига при 794°С (рис. 5е) пики, относящиеся к колебаниям связи OH-группы, не наблюдались, но появились пики области поглощения 412 и 450 см–1, они относятся к колебаниям связи Nd–O [40] из-за образования нового соединения Nd2O3.
ЗАКЛЮЧЕНИЕ
Методом химического осаждения с последующим отжигом получены НС Nd2O3 с гексагональной кристаллической структурой. Средний размер составлял 118 нм в длину и 28 нм в диаметре. Выявлено, что при повышении температуры отжига от 330 до 794°С наблюдается структурно-фазовый переход. Показано, что при 330°С происходит частичная дегидратация Nd(OH)3 с образованием смеси аморфной и кристаллической структур. Средний размер полученных НС Nd(OH)3 составлял 29 нм в длину и 4 нм в диаметре. При увеличении температуры до 635°С по данным РФА наблюдалось образование НС смеси NdOOH и Nd2O3. Средний размер НС составлял 53 нм в длину и 9 нм в диаметре. При температуре 794°С наблюдается полное образование Nd2O3. Полученные НС Nd2O3 применяли в качестве основного компонента для химического синтеза наноструктурированного сплава Nd–Fe–B.
Список литературы
Coey J.M.D. // Eng. 2020. V. 6. № 2. P. 119. https://doi.org/10.1016/j.eng.2018.11.034
An X., Jin K., Abbas N. et al. // J. Magn. Magn. Mater. 2017. V. 442. P. 279. https://doi.org/10.1016/j.jmmm.2017.06.071
Harimoto D., Matsuura Y., Hosokawa S. // J. Jpn. Soc. Powder Powder Metallurgy. 2006. V. 53. № 3. P. 282. https://doi.org/10.2497/jjspm.53.282
Skomski R., Coey J.M.D. // Permanent Magnetism. 1999. https://doi.org/10.1201/9780203743829
München D.D., Veit H.M. // Waste Manag. 2017. V. 61. P. 372. https://doi.org/10.1016/j.wasman.2017.01.032
Levingston J.M., Pozo-López G., Condo A.M. et al. // Mater. 2018. V. 2. P. 122. https://doi.org/10.1016/j.mtla.2018.07.016
Hussain M., Liao X., Akram R. et al. // J. Alloys Compd. 2020. V. 845. P. 156292. https://doi.org/10.1016/j.jallcom.2020.156292
Zha W., Liu J., Song T. et al. // J. Rare Earths. 2011. V. 29. № 1. P. 94. https://doi.org/10.1016/S1002-0721(10)60408-5
Savchenko A.G., Menushenkov V.P., Plastinin A.Yu. et al. // Russ. Metall. 2018. V. 2018. № 4. P. 354. https://doi.org/10.1134/S0036029518040134
Rahimi H., Ghasemi A., Mozaffarinia R. et al. // J. Magn. Magn. Mater. 2017. V. 444. P. 111. https://doi.org/10.1016/j.jmmm.2017.08.011
Wakayama H., Yonekura H. // Mater. Chem. Phys. 2019. V. 227. P. 265. https://doi.org/10.1016/j.matchemphys.2019.01.073
Tan X., Parmar H., Zhong Y. et al. // IEEE Magn. Lett. 2017. V. 8. P. 5508805. https://doi.org/10.1109/LMAG.2017.2746039
Tan X., Parmar H., Zhong Y. et al. // J. Magn. Magn. Mater. 2019. V. 471. P. 278. https://doi.org/10.1016/j.jmmm.2018.09.017
Rahimi H., Ghasemi A., Mozaffarinia R. et al. // J Supercond. Nov. Magn. 2016. V. 29. № 8. P. 2041. https://doi.org/10.1007/s10948-016-3508-0
Deheri P.K., Swaminathan V., Bhame S.D. et al. // Chem. Mater. 2010. V. 22. № 24. P. 6509. https://doi.org/10.1021/cm103148n
Zhang Q., Jiang Z., Yan B. // Inorg. Chem. Front. 2014. V. 1. № 5. P. 384. https://doi.org/10.1039/C4QI00049H
Yonekura H., Wakayama H. // Mater. Sci. Eng. B. 2019. V. 244. P. 38. https://doi.org/10.1016/j.mseb.2019.04.021
Abdurakhmonov O.E., Yurtov E.V., Savchenko E.S. et al. // J. Phys.: Condens. Matter. 2020. V. 1688. № 1. P. 012001. https://doi.org/10.1088/1742-6596/1688/1/012001
Arunpandian M., Selvakumar K., Raja A. et al. // Colloids Surf. A. 2019. V. 567. P. 213. https://doi.org/10.1016/j.colsurfa.2019.01.058
Phuruangrat A., Thongtem S., Thongtem T. // Ceram. Int. 2012. V. 5. № 38. P. 4075. https://doi.org/10.1016/j.ceramint.2012.01.065
Simonenko T.L., Bocharova V.A., Gorobtsov Ph.Yu. et al. // Russ. J. Inorg. Chem. 2020. V. 65. № 9. P. 1292. https://doi.org/10.1134/s0036023620090193
Sreethawong T., Chavadej S., Ngamsinlapasathian S. et al. // Eur. J. Solid State Inorg. Chem. 2008. V. 10. № 1. P. 20. https://doi.org/10.1016/j.solidstatesciences.2007.08.010
Yang W., Qi Y., Ma Y. et al. // Mater. Chem. Phys. 2004. V. 84. № 1. P. 52. https://doi.org/10.1016/j.matchemphys.2003.09.042
Huang B., Huang C., Chen J. et al. // J. Alloys Compd. 2017. V. 712. P. 164. https://doi.org/10.1016/j.jallcom.2017.04.009
Mohamed R.M., Ismail A.A., Kadi M.W. et al. // Catal. Today. 2021. V. 380. P. 259. https://doi.org/10.1016/j.cattod.2020.11.002
Sharapaev A.I., Kuznetsova S.A., Norenko A.N. et al. // Russ. J. Inorg. Chem. 2021. V. 66. № 5. P. 740. https://doi.org/10.1134/S003602362105017X
Zhu W., Ma J., Xu L. et al. // Mater. Chem. Phys. 2010. V. 122. № 2–3. P. 362. https://doi.org/10.1016/j.matchemphys.2010.03.004
Malekfar R., Arabgari S., Motamedi K. et al. // Am. Instit. Physics Conf. Proceed. 2007. V. 929. № 1. P. 162. https://doi.org/10.1063/1.2776708
Intaphong P., Phuruangrat A., Yeebu H. et al. // Russ. J. Inorg. Chem. 2021. V. 66. № 14. P. 2123. https://doi.org/10.1134/S0036023621140047
Shilova O.A., Nikolaev A.M., Kovalenko A.S. et al. // Russ. J. Inorg. Chem. 2020. V. 65. № 3. P. 426. https://doi.org/10.1134/S0036023620030134
Rahman M.M., Wahid A., Alam M.M. et al. // Mater. Today. 2018. V. 16. P. 307. https://doi.org/10.1016/j.mtcomm.2018.07.009
Dhamale G.D., Mathe V.L., Bhoraskar S.V. et al. // Nanotechnology. 2016. V. 27. № 8. P. 085603. https://doi.org/10.1088/0957-4484/27/8/085603
Guire M.R.D., Bauermann L.P., Parikh H. et al. // Chemical Solution Deposition of Functional Oxide Thin Films. 2013. P. 319. https://doi.org/10.1007/978-3-211-99311-8_14
Shi W., Yu J., Wang H. et al. // J. Nanosci. Nanotech. 2006. V. 6. № 8. P. 2515. https://doi.org/10.1166/jnn.2006.540
Nagao M., Hamano H., Hirata K. et al. // J. Langmuir. 2003. V. 19. № 22. P. 9201. https://doi.org/10.1021/la020954y
García A., Llusar M., Sorlí S. et al. // Br. Ceram. Trans. 2013. V. 101. № 6. P. 242. https://doi.org/10.1179/096797802225008078
Kępiński L., Zawadzki M., Miśta W. // Solid State Sci. 2004. V. 6. № 12. P. 1327. https://doi.org/10.1016/j.solidstatesciences.2004.07.003
Zinatloo-Ajabshir S., Mortazavi-Derazkola S., Salavati-Niasari M. // J. Mol. Liq. 2017. V. 234. P. 430. https://doi.org/10.1016/j.molliq.2017.03.115
Abu-Zied B.M., Khan A. // J. Mater. Res. 2020. V. 9. № 5. P. 10478. https://doi.org/10.1016/j.jmrt.2020.07.006
El-Deen L.M.S., Salhi M.S.A., Elkholy M.M. // J. Alloys Compd. 2008. V. 1–2. № 465. P. 333. https://doi.org/10.1016/j.jallcom.2007.10.104
Дополнительные материалы отсутствуют.
Инструменты
Журнал неорганической химии