Журнал неорганической химии, 2022, T. 67, № 2, стр. 139-147
Синтез высокодисперсной порошковой керамической композиции Si3N4–SiC при горении компонентов в системе Si–C–NaN3–NH4F
А. П. Амосов a, *, Г. С. Белова a, Ю. В. Титова a, Д. А. Майдан a
a Самарский государственный технический университет
443100 Самара, ул. Молодогвардейская, 244, Россия
* E-mail: egundor@yandex.ru
Поступила в редакцию 07.08.2021
После доработки 26.08.2021
Принята к публикации 31.08.2021
- EDN: SSRHYR
- DOI: 10.31857/S0044457X22020027
Аннотация
Исследована возможность синтеза высокодисперсной порошковой нитридно-карбидной композиции Si3N4–SiC при сжигании смеси азида натрия (NaN3) с элементными порошками кремния (Si) и сажи (C) и активирующей добавкой фторида аммония (NH4F) в атмосфере азота. Определены параметры горения, химический и фазовый состав, морфология и размеры частиц синтезированных продуктов. Показано, что после водной промывки порошкообразный продукт горения состоит из нитрида кремния двух модификаций (α-Si3N4 и β-Si3N4) с преимущественным содержанием α-Si3N4, карбида кремния (β-SiC) в количестве от 1.6 до 41.8% и незначительного количества свободного кремния (Si). В большинстве случаев полученная нитридно-карбидная композиция Si3N4–SiC представляет собой смесь субмикронных (0.1–0.5 мкм) волокон и равноосных частиц, перспективную для спекания при меньших температурах соответствующих конструкционных композиционных керамических материалов с повышенными механическими свойствами.
ВВЕДЕНИЕ
Нитрид кремния Si3N4 и карбид кремния SiC являются тугоплавкими соединениями, используемыми для изготовления соответствующих неоксидных керамических материалов как конструкционного (благодаря высоким температурам плавления, твердости, износостойкости, жаропрочности, химической стабильности), так и функционального назначения (благодаря электрическим и каталитическим свойствам) [1–5]. Диэлектрик Si3N4 применяется в качестве изолятора в микроэлектронике, а также запоминающей среды в приборах флеш-памяти, а полупроводник SiC – в мощных высокотемпературных транзисторных устройствах и светодиодах, а также в электрических нагревателях. Карбид кремния применяется в качестве катализатора при окислении углеводородов, а нитрид кремния – в качестве носителя катализаторов. Однако эти керамические материалы заметно различаются по некоторым характеристикам. (Конкретные значения характеристик сильно зависят от методов получения керамик, используем усредненные значения характеристик, определенные в основном при комнатной температуре.) Например, керамика Si3N4 не такая хрупкая, как SiC, она демонстрирует высокую вязкость разрушения (в среднем 5.3 МПа м1/2) и хорошую прочность при изгибе (на уровне 750 МПа), но характеризуется низкой стойкостью к окислению при высоких температурах (увеличение массы 1.2 мг/см3 при 1573 K за 100 ч) [1, 4]. Керамика SiC, напротив, демонстрирует высокую стойкость к износу, ползучести и окислению при высоких температурах (увеличение массы 0.02 мг/см3 в тех же условиях), но низкие значения прочности при изгибе (450 МПа) и вязкости разрушения (2.8 МПа м1/2). Карбид кремния является важнейшей составной частью (20–65 об. %) ультравысокотемпературных керамических материалов для достижения их максимальной окислительной стойкости [6–9]. Результаты большого числа исследований показывают, что объединение нитрида и карбида кремния в композиционном материале Si3N4–SiC позволяет использовать достоинства каждой из этих однофазных керамик и получать композиционную керамику со значительно улучшенными свойствами, в первую очередь для высокотемпературного применения [4, 5, 10–15]. Введение всего 5 об. % SiC в матрицу Si3N4 позволяет получить при искровом плазменном спекании композит с повышенной вязкостью разрушения 6.5 МПа м1/2 [15]. Изготовленный горячим изостатическим прессованием композит Si3N4–20 об. % SiC имеет вязкость разрушения 9.5 МПа м1/2 при температуре 1673 K по сравнению с 5.3 МПа м1/2 у однофазной керамики Si3N4 и рассматривается в качестве перспективного материала для газотурбинных двигателей [13]. Этот вывод подтверждается и результатами более поздних исследований, согласно которым горячепрессованные нанокомпозиты Si3N4–(20–30 об. %) SiC имеют прочность при изгибе до 1500 МПа вместо 850 МПа для обычной керамики Si3N4 и сохраняют высокую прочность до 1673 K вместо 1473 K для керамики Si3N4 [5]. Увеличение содержания SiC до 40 мас. % в горячепрессованном композите Si3N4–SiC приводит к увеличению вязкости разрушения до уровня 10.5–12.5 МПа м1/2 [10]. Композиционная керамика Si3N4–SiC имеет большой потенциал для своего дальнейшего развития и применения за счет совершенствования состава, структуры и свойств, разработки новых методов получения и снижения стоимости производства [16, 17].
Известно, что чем больше содержание модификации α-Si3N4 в исходном порошке нитрида кремния, тем выше прочностные свойства керамики Si3N4 благодаря α → β-Si3N4 переходу при спекании материалов, однако не при всех методах получения порошка нитрида кремния удается достичь большого содержания его α-модификации [1]. Весьма существенно могут изменяться все свойства композиционной керамики, в том числе и механические, при повышении дисперсности компонентов композита, при переходе от частиц микронных размеров к высокодисперсным субмикронным (0.1–1 мкм) и наноразмерным (<0.1 мкм = 100 нм), поэтому в настоящее время особое внимание уделяется разработке наноструктурных керамических композитов [5, 12, 16, 17]. Большинство керамических композитов получают методом порошковой технологии, включающей механическое смешивание и измельчение полученных заранее керамических порошков компонентов с последующим компактированием различными методами, например, горячим прессованием. Однако высокодисперсные порошки, особенно нанопорошки, склонны к образованию агломератов при их получении, что препятствует однородному смешиванию порошков различных компонентов и вынуждает заниматься решением задачи дезагломерации нанопорошков [18]. Поэтому в случае высокодисперсных порошков предпочтительны не механические методы смешивания, а химические методы прямого синтеза керамических порошков из смеси исходных реагентов [5, 16]. Субмикронные и нанопорошковые композиции Si3N4–SiC можно синтезировать разными химическими методами, включая покрытие частиц Si3N4 высокодисперсным углеродом в результате пиролиза метана [19], пиролиз органического кремнийсодержащего прекурсора [20], карботермическое восстановление диоксида кремния в присутствии газообразного азота [21], газофазные реакции [22], плазмохимический синтез [23]. Перечисленные химические методы характеризуются большим энергопотреблением из-за необходимости нагрева до высоких температур и использования длительных выдержек, применения дорогостоящего оборудования. Несомненный интерес для получения композиции Si3N4–SiC представляет применение метода самораспространяющегося высокотемпературного синтеза (СВС), известного также как синтез горения (combustion synthesis), который характеризуется малым энергопотреблением, технологичностью, возможностью получать различные керамические порошки, в том числе нанопорошки, из недорогих исходных компонентов [24–26].
Цель настоящей работы – изучение возможности применения метода СВС с использованием азида натрия NaN3 в качестве азотирующего реагента и активирующей добавки галоидной соли NH4F для получения высокодисперсной композиции порошков Si3N4–SiC с различным соотношением фаз.
АНАЛИТИЧЕСКИЙ ОБЗОР
Первые исследования по применению горения для синтеза порошковых композиций Si3N4–SiC основаны на сжигании смесей порошков кремния и технического углерода (сажи) в газообразном азоте при давлении от 1 до 10 МПа [27–29]. Использование газообразного азота в качестве азотирующего реагента приводило сначала к синтезу нитрида кремния с большим тепловыделением, сопровождаемым частичным разложением Si3N4 и последующим синтезом карбида кремния. Смесь порошков Si + C сжигали как в чистом виде, так и с применением порошковых добавок Si3N4 или фторопласта (C2F4)n, что позволяло получить композиции Si3N4–SiC с различным соотношением нитрида и карбида кремния микронного размера с малой долей α-Si3N4, иногда с небольшими примесями непрореагировавшего кремния.
Заметно увеличить долю α-Si3N4 и уменьшить размер частиц композиции Si3N4–SiC позволило применение метода азидного СВС, основанного на использовании порошка азида натрия NaN3 (вместо газообразного азота) в качестве азотирующего реагента и активирующих добавок газифицирующихся галоидных солей [24, 30–33]. Реакция получения Si3N4–SiC выглядит следующим образом:
(1)
$\begin{gathered} 14{\text{Si}} + 6{\text{Na}}{{{\text{N}}}_{3}} + {{({\text{N}}{{{\text{H}}}_{4}})}_{2}}{\text{Si}}{{{\text{F}}}_{6}} + y{\text{C}} = \\ = ((15 - y){\text{/}}3){\text{S}}{{{\text{i}}}_{{\text{3}}}}{{{\text{N}}}_{4}} + y{\text{SiC}} + 6{\text{NaF}} + \\ + \,\,(2y{\text{/}}3){{{\text{N}}}_{2}} + 4{{{\text{H}}}_{2}}, \\ \end{gathered} $Применение другой добавки (галоидной соли NH4F) в значительно большем количестве приводит к получению методом азидного СВС наночастиц кубического нитрида тантала по реакции:
(2)
$\begin{gathered} {{{\text{K}}}_{{\text{2}}}}{\text{Ta}}{{{\text{F}}}_{7}} + (5 + k){\text{Na}}{{{\text{N}}}_{3}} + k{\text{N}}{{{\text{H}}}_{{\text{4}}}}{\text{F}} = \\ = {\text{TaN}} + (5 + k){\text{NaF}} + 2{\text{KF}} + (7 + 2k){{{\text{N}}}_{2}} + 2k{{{\text{H}}}_{2}}, \\ \end{gathered} $ЭКСПЕРИМЕНТАЛЬНАЯ ЧАСТЬ
Для синтеза целевых композиций Si3N4–SiC с мольным соотношением фаз от 1 : 4 до 4 : 1 использовали следующие уравнения химических реакций:
(3)
$\begin{gathered} 4{\text{Si}} + {\text{C}} + {\text{Na}}{{{\text{N}}}_{3}} + {\text{N}}{{{\text{H}}}_{{\text{4}}}}{\text{F}} = \\ = {\text{S}}{{{\text{i}}}_{{\text{3}}}}{{{\text{N}}}_{4}} + {\text{SiC}} + {\text{NaF}} + 2{{{\text{H}}}_{2}}, \\ \end{gathered} $(4)
$\begin{gathered} {\text{5Si}} + 2{\text{C}} + {\text{Na}}{{{\text{N}}}_{3}} + {\text{N}}{{{\text{H}}}_{{\text{4}}}}{\text{F}} = \\ = {\text{S}}{{{\text{i}}}_{{\text{3}}}}{{{\text{N}}}_{4}} + 2{\text{SiC}} + {\text{NaF}} + 2{{{\text{H}}}_{2}}, \\ \end{gathered} $(5)
$\begin{gathered} {\text{7Si}} + 4{\text{C}} + {\text{Na}}{{{\text{N}}}_{3}} + {\text{N}}{{{\text{H}}}_{{\text{4}}}}{\text{F}} = \\ = {\text{S}}{{{\text{i}}}_{{\text{3}}}}{{{\text{N}}}_{4}} + 4{\text{SiC}} + {\text{NaF}} + 2{{{\text{H}}}_{2}}, \\ \end{gathered} $(6)
$\begin{gathered} {\text{7Si}} + {\text{C}} + 2{\text{Na}}{{{\text{N}}}_{3}} + 2{\text{N}}{{{\text{H}}}_{{\text{4}}}}{\text{F}} = \\ = 2{\text{S}}{{{\text{i}}}_{{\text{3}}}}{{{\text{N}}}_{4}} + {\text{SiC}} + 2{\text{NaF}} + 2{{{\text{H}}}_{2}}, \\ \end{gathered} $(7)
$\begin{gathered} {\text{13Si}} + {\text{C}} + 4{\text{Na}}{{{\text{N}}}_{3}} + 4{\text{N}}{{{\text{H}}}_{{\text{4}}}}{\text{F}} = \\ = 4{\text{S}}{{{\text{i}}}_{{\text{3}}}}{{{\text{N}}}_{4}} + {\text{SiC}} + 4{\text{NaF}} + 2{{{\text{H}}}_{2}}. \\ \end{gathered} $В данных уравнениях состав продуктов реакций выражен в молях, при переходе к мас. % получаются следующие соотношения для теоретического состава целевых композиций Si3N4–SiC при условии удаления водорастворимой побочной соли NaF из продуктов реакций:
Для экспериментального исследования в качестве исходного сырья использовали (здесь и далее указаны мас. %) порошок кремния марки “Кр0” (содержание основного вещества ≥98.8%, d0.5 = = 5 мкм), порошок фторида аммония классификации “ч.” (≥99.1%, 20 мкм), порошок азида натрия классификации “ч.” (≥98.71%, 100 мкм), технический углерод марки “П701” (≥88.0%, 70 нм в виде агломератов до 1 мкм). Смесь высушенных исходных порошков, взятых в заданном соотношении, перемешивали вручную в фарфоровой ступке в течение 5–10 мин до визуально равномерного распределения компонентов. Подготовленную смесь порошков (шихту) засыпали в кальковый стаканчик диаметром 30 мм и высотой 45 мм, помещали в фильтрующую сборку из углеткани и вставляли две вольфрам-рениевые термопары. Насыпная относительная плотность порошковых смесей составляла в среднем 40% от максимально возможной плотности беспористых смесей заданных составов. Собранную конструкцию устанавливали на предметную полочку лабораторного реактора СВС-Аз постоянного давления с рабочим объемом 4.5 л [26]. В реакторе создавалось давление газообразного азота 4 МПа и электрической вольфрамовой спиралью накаливания инициировалось горение.
После синтеза образец извлекали из реактора и разрушали вручную до сыпучего порошкообразного состояния в фарфоровой ступке. Затем порошкообразный продукт горения промывали дистиллированной водой от остатка побочного продукта – фторида натрия до кислотно-щелочного баланса промывной воды pH 8.
Исследовали элементный и фазовый состав, микроструктуру и размер частиц продуктов горения. Фазовый состав синтезированных продуктов определяли на порошковом рентгеновском дифрактометре ARL E’trA-138, оснащенном рентгеновской трубкой с медным анодом максимальной мощностью 2200 Вт. Сканирование проводили в диапазоне углов 2θ 20°–80° со скоростью 2 град/мин. Расшифровку дифрактограмм и количественную оценку фазового состава выполняли методом Ритвельда в программе PDXL 1.8 с использованием баз кристаллографических данных PDF-2009 и COD-2019. Исследование морфологии и размера частиц синтезированных композиций проводили по изображениям микроструктуры продуктов горения на растровом электронном микроскопе JSM-6390A фирмы Jeol.
РЕЗУЛЬТАТЫ ИССЛЕДОВАНИЯ
Результаты экспериментального определения параметров горения: максимальной температуры tг, скорости Uг, максимального давления pм, теоретического (Mт) и практического (Mпр) выхода конденсированных продуктов горения шихтовых композиций для синтеза керамических нитридно-карбидных композиций Si3N4–SiC представлены в табл. 1.
Таблица 1.
Параметры горения шихтовых композиций для синтеза Si3N4–SiC
Состав шихтовых композиций в соответствии с реакциями (3)–(7) | tг, °С | Uг, см/с | pм, МПа | mшихты, г | Mт, г | Mпр, г |
---|---|---|---|---|---|---|
4Si + C + NaN3 + NH4F | 1955 | 0.80 | 4.69 | 23.21 | 22.80 | 21.87 |
5Si + 2C + NaN3 + NH4F | 1910 | 0.79 | 4.58 | 23.98 | 23.63 | 22.96 |
7Si + 4C + NaN3 + NH4F | 1902 | 0.76 | 4.53 | 25.08 | 24.79 | 23.18 |
7Si + C + 2NaN3 + 2NH4F | 2098 | 0.83 | 4.81 | 22.73 | 22.29 | 21.34 |
13Si + C + 4NaN3 + 4NH4F | 2225 | 0.85 | 5.03 | 22.46 | 22.01 | 20.13 |
Из анализа приведенных в табл. 1 данных следует, что увеличение количества кремния в шихте при одинаковом количестве углерода, т.е. увеличение доли нитрида кремния в продукте, приводит к увеличению температуры и скорости горения, а увеличение доли карбида кремния в продукте при увеличении количества углерода в шихте приводит к снижению температуры и скорости горения. Видно, что практический выход продукта достаточно близок к теоретическому, разница составляет от 2.8 до 8.5%, и она тем больше, чем больше содержание соли NH4F в шихте.
На рис. 1 и в табл. 2 представлены рентгеновские дифрактограммы и результаты количественного рентгенофазового анализа состава продуктов горения исходных смесей порошков (шихт) согласно реакциям (3)–(7) после водной промывки и удаления NaF.
Рис. 1.
Рентгеновские дифрактограммы продуктов горения шихтовых композиций в соответствии с реакциями (3)–(7): 1 – 4Si + C + NaN3 + NH4F (3); 2 – 5Si + 2C + NaN3 + NH4F (4); 3 – 7Si + 4C + NaN3 + NH4F (5); 4 – 7Si + C + + 2NaN3 + 2NH4F (6); 5 – 13Si + C + 4NaN3 + 4NH4F (7).
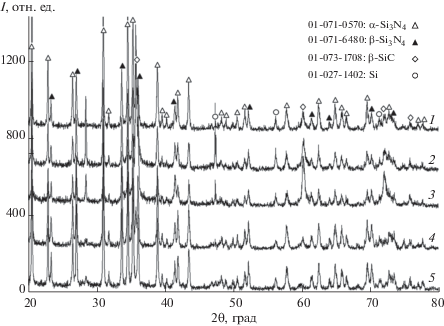
Таблица 2.
Состав продуктов горения шихтовых композиций, мас. %
Шихтовые композиции в соответствии с реакциями (3)–(7) | α-Si3N4 | β-Si3N4 | α-Si3N4 + β-Si3N4 | β-SiC | Siсв |
---|---|---|---|---|---|
4Si + C + NaN3 + NH4F (3) | 70.2 | 19.4 | 89.6 | 9.7 | 0.7 |
5Si + 2C + NaN3 + NH4F (4) | 50.9 | 19.5 | 70.4 | 23.9 | 5.7 |
7Si + 4C+NaN3 + NH4F (5) | 38.2 | 17.6 | 55.8 | 41.8 | 2.4 |
7Si + C + 2NaN3 + 2NH4F (6) | 68.4 | 27.4 | 95.8 | 3.6 | 0.6 |
13Si + C + 4NaN3 + 4NH4F (7) | 69.3 | 28.1 | 97.4 | 1.6 | 1.0 |
Промытые продукты горения всех исследованных шихтовых композиций состоят из четырех фаз: нитрида кремния двух модификаций (α-Si3N4 и β-Si3N4), карбида кремния (β-SiC), а также примеси свободного кремния (Siсв). Отметим, что наличие небольших примесей непрореагировавшего кремния характерно и для других случаев применения процесса горения для получения композиции порошков Si3N4–SiC [27–29]. Другие отличия экспериментально определенного состава продуктов горения от рассчитанного теоретического состава (3)–(7) обсуждаются ниже вместе с микроструктурой продуктов горения.
Экспериментальный состав продуктов горения реакции (3) (89.6% Si3N4 + 9.7% SiC + 0.7% Siсв) отличается от теоретического состава (3) (77.8% Si3N4 + 22.2% SiC) значительно большим содержанием нитрида кремния, почти в два раза меньшим содержанием карбида кремния и наличием небольшой примеси Siсв. При этом нитрид кремния состоит в основном из модификации α-Si3N4, содержание которой в четыре раза превышает содержание β-Si3N4. На показанной на рис. 2 микроструктуре продуктов горения видны типичные для α-Si3N4 волокна диаметром 150–500 нм и длиной до 5 мкм, а также частицы равноосной формы карбида кремния, находящиеся в виде как отдельных частиц, так и агломератов.
Рис. 2.
Микроструктура продуктов горения шихты реакций (3)–(7) при увеличении ×10000 (а) и ×20000 (б).
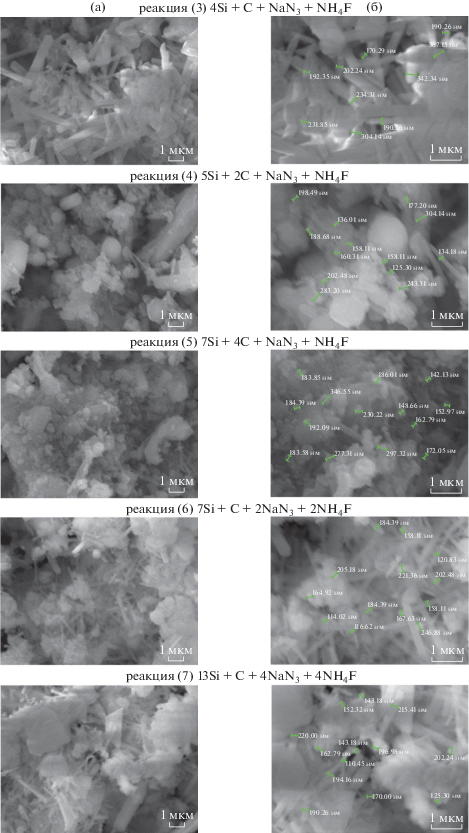
Таким образом, при горении смеси исходных порошков реакции (3) удается получить композицию субмикронных порошков, близкую к составу Si3N4–10% SiC, с преимущественным содержанием α-Si3N4 и небольшим содержанием примеси свободного кремния (0.7%).
В случае реакции (4) при увеличении в шихте содержания кремния от 4 до 5 молей и углерода от 1 до 2 молей по сравнению с шихтой реакции (3) в продуктах горения шихты реакции (4) (табл. 2) наблюдается уменьшенное содержание α-модификации нитрида кремния при увеличенном содержании фаз карбида кремния и свободного кремния: α-Si3N4 – 50.9%, β-Si3N4 – 19.5%, SiC – 23.9%, Siсв – 5.7%. Здесь содержание волокон α-Si3N4 должно составлять ~50% от объема смеси порошков, но на рис. 2 видно значительно меньшее содержание единичных волокон диаметром 100–250 нм при преимущественном содержании частиц равноосной формы размером 100–500 нм в виде отдельных частиц и агломератов, что свидетельствует об образовании значительной части α-Si3N4 (наряду с β-Si3N4 и Siсв) в виде частиц равноосной формы при повышенном содержании углерода в шихте. (Заключение о влиянии именно повышенного содержания углерода, а не кремния объясняется тем, что содержание кремния в шихте реакции (4) увеличилось всего на 25% по сравнению с шихтой реакции (3), а содержание углерода – на 100%, а также тем, что при том же содержании углерода (1 моль), но повышенном содержании кремния (7 молей) в шихте реакции (6) и 13 молей в шихте реакции (7) α-Si3N4 образуется преимущественно в виде волокон.)
В целом состав синтезированной ультрадисперсной порошковой композиции 70.4% Si3N4 + + 23.9% SiC + 5.7% Siсв отличается от теоретического состава (4) 63.6% Si3N4 + 36.4% SiC меньшей разницей в содержании нитрида и карбида кремния, но значительно большим содержанием примеси Siсв, чем в случае реакции (3).
Представленные в табл. 2 результаты РФА продуктов горения шихты реакции (5) 7Si + 4C + + NaN3 + NH4F показывают, что при увеличении содержания углерода в четыре раза и кремния в два раза по сравнению с шихтой реакции (3) продукты горения шихты (5) содержат значительно меньше нитрида кремния и больше карбида кремния: α-Si3N4 – 38.2%, β-Si3N4 – 17.6%, SiC – 41.8%, Siсв – 2.4%. Такой состав композиции отличается от теоретического состава (5) 46.7% Si3N4 + 53.3% SiC также по α-Si3N4 и SiC при сохранении содержания β-Si3N4. Из сравнения микроструктур видно, что продукты горения также состоят преимущественно из частиц равноосной формы, но сильно отличаются по размеру. В случае реакции (5) с большим содержанием кремния и углерода в шихте они представляют собой смесь нитрида и карбида кремния в виде субмикронных частиц размером 150–500 нм и намного более крупных частиц размером до 2 мкм.
Из табл. 2 следует, что в результате горения шихты реакции (6), содержащей в два раза больше кремния по сравнению с шихтой реакции (3) при том же содержании углерода, образуется примерно столько же α-Si3N4 и почти на 20% больше β-Si3N4, почти в три раза меньше карбида кремния и практически столько же примеси свободного кремния: α-Si3N4 – 68.4%, β-Si3N4 – 27.4%, SiC – 3.6%, Siсв – 0.6%. Состав синтезированной композиции отличается от теоретического состава (6) 87.5% Si3N4 + 12.5% SiC заметно большим содержанием нитрида кремния и значительно меньшим (почти в четыре раза) содержанием карбида кремния. Согласно рис. 2, образуются преимущественно характерные для α-Si3N4 волокна диаметром 100–250 нм при длине до 3 мкм и равноосные частицы размером 100–500 нм в виде отдельных частиц и агломератов.
В случае шихты реакции (7) с намного большим содержанием кремния, азида натрия и фторида аммония по сравнению с шихтой (3) при том же содержании углерода получен следующий состав синтезированной композиции (табл. 2): α-Si3N4 – 69.3%, β-Si3N4 – 28.1%, SiC – 1.6%, Siсв – 1.0%, отличающийся от состава композиции по реакции (6) только еще меньшим содержанием карбида кремния, которое в четыре раза меньше теоретического (7): 93.3% Si3N4 + + 6.7% SiC. Согласно рис. 2, как и в предыдущем случае, продукты горения представляют собой преимущественно волокна диаметром 100–250 нм при длине до 3 мкм и равноосные частицы размером 100–500 нм в виде отдельных частиц и агломератов.
ОБСУЖДЕНИЕ РЕЗУЛЬТАТОВ
При реализации процесса азидного СВС для получения высокодисперсной композиции порошков Si3N4–SiC экспериментальный состав композиции заметно отличается от расчетного теоретического состава прежде всего по значительно меньшему содержанию карбида кремния. На рис. 3 показана зависимость найденного в эксперименте содержания карбида кремния SiCэ от теоретического содержания SiCт, построенная по результатам табл. 2 и уравнений (3)–(7).
Рис. 3.
Зависимость экспериментального содержания SiCэ от теоретического SiCт (1) в композиции порошков Si3N4–SiC и ее полиномиальная аппроксимация (2), в которой y = SiCэ, x = Siт, R2 – величина достоверности аппроксимации.
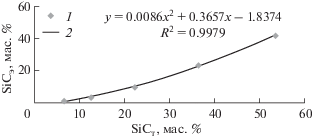
Такое отличие экспериментальных и теоретических результатов можно объяснить особенностями образования карбида кремния при получении композиции порошков Si3N4–SiC путем сжигания смеси порошков кремния и углерода в атмосфере азота [27–29]. Реакция синтеза карбида кремния из элементных порошков: Si + C = = SiC обладает небольшим тепловым эффектом (73 кДж/моль) и не может обеспечить самораспространяющийся режим горения, в то время как реакция синтеза нитрида кремния из порошка кремния в газообразном азоте: 3Si + 2N2 = Si3N4 является сильно экзотермической с тепловым эффектом 756 кДж/моль и может протекать в режиме горения. Поэтому при инициировании горения смеси порошков кремния и углерода сначала происходит синтез нитрида кремния с подъемом температуры до высоких значений, превышающих 2273 K, при которых синтезированный Si3N4 диссоциирует, а затем возникающий кремний реагирует с углеродом, образуя SiC, более стабильный при высоких температурах. Образование SiC идет до полного расходования углерода, а оставшийся неизрасходованным кремний превращается в Si3N4. В случае сжигания шихтовых композиций реакций (3)–(7) нитрида кремния образуется больше, а карбида кремния меньше, чем должно быть по уравнениям реакций (3)–(7), но свободный углерод не обнаруживается в продуктах горения. Причина может заключаться в том, что часть очень мелких легких частиц технического углерода (сажи) удаляется (выдувается) из горящего высокопористого шихтового образца выделяющимися при горении газами и не участвует в превращении Si3N4 в SiC. В результате в продуктах горения нитрида кремния остается больше, а карбида кремния меньше, чем должно быть по уравнениям реакций (3)–(7). Чем меньше содержание углерода в шихте по сравнению с содержанием кремния в этих уравнениях, тем выше температура горения и больше газовыделение, тем больше относительные потери углерода за счет выноса газами и тем сильнее SiCэ отличается от SiCт. Необходимо отметить, что приведенная выше аппроксимационная зависимость SiCэ (SiCт) позволяет прогнозировать действительный состав синтезируемой композиции порошков Si3N4–SiC при использовании уравнений реакций типа (3)–(7) в рассмотренных условиях эксперимента. Для приближения к расчетному составу синтезируемой композиции Si3N4–SiC необходимо провести дальнейшие исследования с возможными технологическими изменениями: использовать избыток порошка углерода, изменять такие параметры, как давление газообразного азота в реакторе, плотность и объем шихтового образца и др.
ЗАКЛЮЧЕНИЕ
Подтверждена эффективность использования активирующей добавки галоидной соли NH4F для получения методом азидного СВС высокодисперсной композиции порошков Si3N4–SiC с различным соотношением фаз в широком диапазоне содержания карбида кремния (от 1.6 до 41.8%). Синтезированные композиции отличаются большим содержанием α-Si3N4 (в 2.17–3.61 раза больше, чем β-Si3N4). При высоком содержании углерода в шихте, приводящем к синтезу 23.9 и 41.8% карбида кремния в композиции, α-Si3N4 образуется преимущественно в виде частиц равноосной, а не волокнистой формы. Содержание примеси свободного кремния не превышает 1.0% для композиций с содержанием SiC до 10%, но достигает 2.4–5.7% при содержании SiC 23.9 и 41.8%, что, очевидно, связано с большим содержанием кремния в исходной шихте и не полностью прошедшей реакцией образования SiC. При содержании SiC от 1.6 до 23.9% композиции Si3N4–SiC являются субмикронными и состоят из волокон диаметром 100–500 нм и длиной до 5 мкм, а также равноосных частиц размером 100–500 нм в виде отдельных частиц и их агломератов. При содержании 41.8% SiC композиция Si3N4–SiC представляет собой смесь субмикронных частиц размером 150–500 нм с намного более крупными частицами размером до 2 мкм. Полученные композиционные порошки Si3N4–SiC отличаются от синтезированных ранее с применением процесса горения как более высокой дисперсностью, так и большим содержанием α-Si3N4, в связи с чем перспективны для использования при изготовлении композиционных керамических материалов с повышенными свойствами при меньших температурах спекания. Но для этого необходима доработка процесса азидного СВС композиции высокодисперсных порошков Si3N4–SiC в отношении технологических изменений для приближения к расчетному составу композиции и уменьшения в ней содержания свободного кремния.
Список литературы
Косолапова Т.Я., Андреева Т.В., Бартницкая Т.Б. и др. Неметаллические тугоплавкие соединения. М.: Металлургия, 1985. 224 с.
Андриевский Р.А., Спивак И.И. Нитрид кремния и материалы на его основе. М.: Металлургия, 1984. 136 с.
Агеев О.А., Беляев А.Е., Болтовец Н.С. и др. Карбид кремния: технология, свойства, применение. Харьков: ИСМА, 2010. 532 с.
Бобович Б.Б. Неметаллические конструкционные материалы. М.: МГИУ, 2009. 384 с.
Basu B., Balani K. Advanced structural ceramics. Hoboken, New Jersey: John Wiley & Sons Inc., 2011. 502 p.
Simonenko E.P., Simonenko N.P., Nikolaev V.A. et al. // Russ. J. Inorg. Chem. 2019. V. 64. № 11. P. 1456. [Симоненко Е.П., Симоненко Н.П., Николаев В.А. и др. // Журн. неорган. химии. 2019. Т. 64. № 11. С. 1229.] https://doi.org/10.1134/S0036023619110202
Simonenko E.P., Simonenko N.P., Sevastyanov V.G., Kuznetsov N.T. // Russ. J. Inorg. Chem. 2019. V. 64. № 14. P. 1697. https://doi.org/10.1134/S0036023619140079
Simonenko E.P., Simonenko N.P., Gordeev A.N. et al. // Russ. J. Inorg. Chem. 2020. V. 65. № 4. P. 606. [Симоненко Е.П., Симоненко Н.П., Гордеев А.Н. и др. // Журн. неорган. химии. 2020. Т. 65. № 4. С. 564.] https://doi.org/10.1134/S0036023620040191
Shapkin N.P., Papynov E.K., Shichalin O.O. et al. // Russ. J. Inorg. Chem. 2021. V. 66. № 5. P. 629. [Шапкин Н.П., Папынов Е.К., Шичалин О.О. и др. // Журн. неорган. химии. 2021. Т. 66. № 5. С. 575.] https://doi.org/10.1134/S0036023621050168
Пилиповский Ю.Л., Грудина Т.В., Сапожникова А.Б. и др. Композиционные материалы в машиностроении. Киев: Техника, 1990. 141 с.
Niihara K., Izaki K., Kawakami T. // J. Mater. Sci. Lett. 1990. V. 10. P. 112.
Niihara K. // J. Ceram. Soc. Jpn. 1991. V. 99. P. 974. https://doi.org/10.2109/jcersj.99.974
Pezzotti G. // J. Am. Ceram. Soc. 1993. V. 76. P. 1313. https://doi.org/10.1002/chin.199330007
Koh Y.-H., Kim H.-W., Kim H.-E. // Scrp. Mater. 2001. V. 44. P. 2069. https://doi.org/10.1016/S1359-6462(01)00885-5
Khajelakzay M., Bakhshi S.R. // Ceram. Int. 2017. V. 43. P. 6815. https://doi.org/10.1016/j.ceramint.2017.02.099
Palmero P. // Nanomaterials. 2015. V. 5. P. 656. https://doi.org/10.3390/nano5020656
Montanaro L., Palmero P. // Ceramics. 2019. V. 2. P. 296. https://doi.org/10.3390/ceramics2020024
Kozerozhets I.V., Panasyuk G.P., Semenov E.A. et al. // Russ. J. Inorg. Chem. 2020. V. 65. № 12. P. 1943. [Козерожец И.В., Панасюк Г.П., Семенов Е.А. и др. // Журн. неорган. химии. 2020. Т. 65. № 12. С. 1705.] https://doi.org/10.1134/S0036023620120086
Yanai T., Ishizaki K. // J. Ceram. Soc. Jpn. 1993. V. 101. P. 764. https://doi.org/10.2109/jcersj.101.764
Riedel R., Seher M., Becker G. // J. Eur. Ceram. Soc. 1989. V. 5. P. 113. https://doi.org/10.1016/0955-2219(89)90018-6
Suri J., Shaw L., Zawrah M.F. // Int. J. Appl. Ceram. Tech. 2012. V. 9. P. 291. https://doi.org/10.1111/j.1744-7402.2011.00710.x
Hojo J., Meada H., Kato A. // Yogyo-Kyokai-Shi. 1987. V. 95. P. 45.
Lee H.J., Eguchi K., Yoshida T. J. Am. Ceram. Soc. 1990. V. 73. P. 3356.
Amosov A.P., Borovinskaya I.P., Merzhanov A.G., Sytchev A.E. // Int. J. Self-prop. High-temp. Synth. 2005. V. 14. № 3. P. 165. [Амосов А.П., Боровинская И.П., Мержанов А.Г., Сычев А.Е. // Изв. вузов. Цвет. металлургия. 2006. Т. 14. № 5. С. 9.]
Rogachev A.S., Mukasyan A.S. Combustion for material synthesis. N.Y.: CRC Press, 2014. 422 p. [Рогачев А.С., Мукасьян А.С. Горение для синтеза материалов. М.: Физматлит, 2012. 400 с.]
Levashov E.A., Mukasyan A.S., Rogachev A.S., Shtansky D.V. // Int. Mater. Rev. 2016. https://doi.org/10.1080/09506608.2016.1243291
Zeng J., Miyamoto Y., Yamada O. // J. Am. Ceram. Soc. 1989. V. 74. P. 2197.
Kata D., Lis J., Pampuch R., Stobierski L. // Int. J. Self-prop. High-temp. Synth. 1998. V. 7. № 4. P. 475.
Khachatryan G.L., Arutyunyan A.B., Kharatyan S.L. // Comb. Expl. Shock Waves. 2006. V. 42. № 5. P. 543. [Хачатрян Г.Л., Арутюнян А.Б., Харатян С.Л. // Физика горения и взрыва. 2006. Т. 42. № 5. С. 56.]
Амосов А.П., Бичуров Г.В. Азидная технология самораспространяющегося высокотемпературного синтеза микро- и нанопорошков нитридов М.: Машиностроение-1, 2007. 526 с.
Бичуров Г.В., Шиганова Л.А., Титова Ю.В. Азидная технология самораспространяющегося высокотемпературного синтеза микро- и нанопорошков нитридных композиций М.: Машиностроение, 2012. 519 с.
Titova Y.V., Amosov A.P., Ermoshkin A.A. et al. // Russ. J. Non-Ferr. Met. 2014. V. 55. № 6. P. 620. [Титова Ю.В., Амосов А.П., Ермошкин А.А. и др. // Изв. вузов. Порошковая металлургия и функциональные покрытия. 2013. Т. 55. № 3. С. 45.]
Bichurov G.V. // Nitride Ceramics: Combustion synthesis, properties, and applications / Eds. Gromov A.A., Chukhlomina L.N. Weinheim: Wiley-VCH, 2015. P. 229.
Lee Y.-J., Kim D.-Y., Lee K.-H. et al. // Nanoscale Res. Lett. 2013. V. 8. P. 126. https://doi.org/10.1186/1556-276X-8-126
Nersisyan H.H., Lee J.H., Ding J.-R. et al. // Prog. Energy Combust. Sci. 2017. V. 63. P. 79. https://doi.org/10.1016/j.pecs.2017.07.002 0360-1285
Дополнительные материалы отсутствуют.
Инструменты
Журнал неорганической химии