Журнал неорганической химии, 2022, T. 67, № 12, стр. 1858-1865
Получение и свойства графитовых нанокомпозитов методом низкотемпературной каталитической графитизации целлюлозы
А. Н. Прусов a, *, С. М. Прусова a, М. В. Радугин a, А. В. Базанов a
a Институт химии растворов им. Г.А. Крестова РАН
153045 Иваново, ул. Академическая, 1, Россия
* E-mail: anp@isc-ras.ru
Поступила в редакцию 28.04.2022
После доработки 14.06.2022
Принята к публикации 15.06.2022
- EDN: CTWWWA
- DOI: 10.31857/S0044457X22700118
Аннотация
Методом одностадийного пиролиза в среде азота синтезированы магнитные композиты из микрокристаллической целлюлозы костры льна, модифицированной лимонной кислотой и гомогенно пропитанной Fe(NO3)3. Механизм каталитической графитизации изучен методом термогравиметрического анализа. С помощью адсорбции–десорбции азота, рентгеноструктурного анализа и сканирующей электронной микроскопии выполнен анализ морфологической структуры, распределения пор по размерам и химии поверхности углеродных композитов. Определена адсорбционная емкость полученных материалов по отношению к анионному красителю метиловому оранжевому и катионному – метиленовому синему.
ВВЕДЕНИЕ
В течение последних десятилетий одним из направлений инновационных технологий является переработка целлюлозосодержащей растительной биомассы в активированные [1–3] и наноструктурированные графитовые [6–8] углеродные материалы. Наноструктурированные углеродные материалы используют для очистки сточных вод [1–3], в качестве аккумуляторных электродов, катализаторов [5–7], адсорбентов [8, 9].
Применение целлюлозы в качестве матриц позволяет использовать эффекты самосборки и самоорганизации для синтеза металл- и оксидсодержащих углеродных материалов [10–12]. Карбоксильные и гидроксильные группы целлюлозной матрицы фиксируют и стабилизируют ионы металлов на целлюлозных волокнах за счет ион-дипольных взаимодействий, препятствуя образованию агрегатов [8, 9]. Увеличение количества карбоксильных групп в результате взаимодействия ангидридов органических кислот с гидроксильными группами глюкопиранозного кольца целлюлозы способствует равномерному распределению ионов металлов в целлюлозной матрице [12, 13].
Наиболее распространенным методом получения наноструктурированных графитовых углеродных материалов из целлюлозной биомассы является каталитическая графитизация, которая осуществляется с использованием вспомогательных веществ – солей Fe, Co, Ni, Mn и др. [5, 14–16].
Цель исследования – синтез наноструктурированных графитовых углеродных материалов из микрокристаллической целлюлозы (МКЦ), модифицированной лимонной кислотой (MКЦЛ), исследование их свойств, а также изучение процесса каталитической графитизации с использованием Fe(NО3)3 и оценка адсорбционной способности полученных углеродов относительно красителей метиленового синего (МС) и метилового оранжевого (МО).
ЭКПЕРИМЕНТАЛЬНАЯ ЧАСТЬ
В работе использовали нитрат железа (Fe(NO3)3⋅9H2O) аналитической чистоты (Sigma-Aldrich), моногидрат лимонной кислоты аналитической чистоты, MС (C16H18ClN3S⋅3H2O) и МО (C14H14O3N3SNa) (Sigma-Aldrich).
Получение металл-углеродных композитов. Сухую льняную костру измельчали на двухшнековом экструдере и отбирали фракцию с размером частиц ~0.6 мм. Отобранную фракцию гидролизовали 10%-ным водным раствором азотной кислоты в течение 4 ч при 98°С, промывали и отбеливали щелочным раствором, содержащим Н2О2. Модификацию MКЦ раствором лимонной кислоты проводили согласно работам [12, 17]. МКЦ (50 г) смешивали с раствором лимонной кислоты (200 г/л) в соотношении 1 : 3, перемешивали в течение 30 мин при 20°C. После перемешивания сушили при 50°C в сушильном шкафу с принудительной подачей воздуха. Через 24 ч реакцию между кислотой и МКЦ продолжали путем повышения температуры печи до 120°С на 12 ч. После охлаждения продукт реакции заливали 0.6 л дистиллированной воды и перемешивали. Избыток воды, содержащей непрореагировавшую лимонную кислоту, удаляли фильтрацией. Затем МКЦЛ промывали дистиллированной водой до нейтральной реакции и центрифугировали при 3000 об/мин. Обезвоженную МКЦЛ сушили на воздухе. Образование сложноэфирной связи в целлюлозе происходит за счет взаимодействия ангидридов органических кислот (образуются при повышенной температуре) с гидроксильными группами глюкопиранозного кольца целлюлозы [12].
MКЦЛ пропитывали катализатором: 50.0 г MКЦЛ смешивали с 100 мл 0.6 M раствора Fe(N03)3 и выдерживали в течение 12 ч. Полученные образцы (Fe@MКЦЛ) сушили при температуре 105°С до постоянной массы.
Для проведения каталитической графитизации образцы Fe@MКЦЛ подвергали пиролизу в горизонтальном реакторе непрерывного действия в среде чистого азота согласно [10]. После охлаждения до комнатной температуры образцы подвергали воздействию окружающей атмосферы. В результате пиролиза получены графитовые углеродные композиты Fe@С-600, Fe@С-700, Fe@С-800, Fe@С-900 и Fe@С-1000.
Методы анализа. Адсорбционные свойства графитовых углеродных материалов изучали с использованием красителей MС и МО. Равновесное количество МС и МО (мг/г), поглощенное композитом, определяли с использованием спектрофотометра Specord при максимальной длине волны λ = 668 и 464 нм соответственно. Методика проведения экспериментов по адсорбции МО аналогична таковой для МС и представлена в статье [18].
Данные рентгеновской дифракции получали на дифрактометре Bruker D8 Advance согласно [10].
Размеры кристаллитов рассчитывали по формуле Шеррера:
Уравнение Брэгга использовали для расчета межплоскостного расстояния d(002):
Степень графитизации является структурным параметром и используется для количественной характеристики степени сходства между углеродным материалом и идеальным монокристаллом графита. Для расчета степени графитизации использовали уравнение [15]:
Количество наложенных друг на друга плоскостей углеродного слоя (n) рассчитывали по формуле [15]: n = L/d002.
Площадь поверхности по BЭT измеряли с помощью прибора для определения площади поверхности (NOVAtouch NT LX) методом физической сорбции N2 при 77 K. Распределение пор по размерам углеродных композитов оценивали с помощью метода функционала плотности (DFT) [19].
Термогравиметрический анализ (ТГ/ДТГ) проводили на термомикровесах TG 209 F1 Iris фирмы Netzsch (Германия).
Морфологию поверхности композитов изучали с использованием сканирующего электронного микроскопа Carl Zeiss NVision 40 и Vega3 Tescan.
РЕЗУЛЬТАТЫ И ОБСУЖДЕНИЕ
Рентгеноструктурный анализ
Единственная кристаллическая фаза, образовавшаяся в углеродном композите при температуре около 500°C – это магнетит, оксид железа(II, III) (рис. 1). Полученный углеродный композит обладает магнитными свойствами.
Образование магнетита в инертной среде при температуре пиролиза 600°C (рис. 2) происходит вследствие карботермического восстановления гематита [20]. Кроме того, при этих условиях происходит восстановление магнетита Fe3O4 до наночастиц Fe0, а также становятся заметными дифракционные пики, характерные для графита (2θ = 26.25°) и метастабильного карбида железа (Fe3C).
Рис. 2.
Рентгенограммы образцов Fe@MКЦЛ после пиролиза при 600 (1), 700 (2), 800 (3), 900 (4) и 1000°С (5).
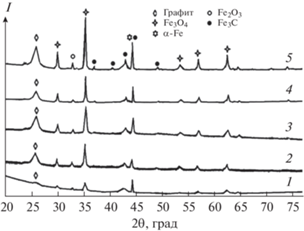
Наличие более интенсивного пика при 2θ = = 44.52° в углеродном материале предполагает, что в этой системе присутствует смесь Fe и Fe3C. Наночастицы Fe0 растворяют аморфный углерод, полученный пиролизом целлюлозы, и перекристаллизовывают его в виде хорошо упорядоченных графитовых наноструктур. Факт того, что металлические частицы катализируют превращение неорганизованного углерода в графитовый углерод в соответствии с механизмом растворения-осаждения, подтверждают работы многих авторов [15, 21, 22]. Размер кристаллитов Fe3O4 при температуре 600, 700, 800, 900 и 1000°C равен 19.1, 48.0, 36.4, 44.6 и 42.1 нм соответственно. Межплоскостное расстояние кристаллитов Fe3O4L = = 9.3 нм.
Следует отметить, что Fe3O4 является доминирующей разновидностью кристаллического железа независимо от температуры пиролиза, что обеспечивает магнитные свойства всех углеродных композитов. Размер кристаллитов Fe2O3 при температуре 600, 700, 800, 900 и 1000°C равен 2.93, 48.0, 56.0, 42.3 и 48.1 нм соответственно. Сосуществование Fe3O4, Fe2O3 и Fe0 объясняется большим (объемным) размером частиц, содержащих железо, что замедляет восстановление, а также воздействием окружающей атмосферы [7]. Кроме того, отсутствие FeO указывает на наличие окислительно-восстановительного диспропорционирования вюстита [23].
При повышении температуры от 600 до 1000°С пик при 2θ = 26.3° становиться более интенсивным, что означает увеличение отношения графитовый углерод/аморфный углерод. Структурные характеристики d002, Gp не изменяются по мере повышения температуры. При этом размер кристаллита графита увеличивается от 2.94 до 13.74 нм, а количество наложенных друг на друга плоскостей углеродного слоя – с 8.68 до 40.58 (табл. 1).
Таблица 1.
Результаты расчетов
Образец | 2θ, град | d002 (межплоскостное расстояние, нм) | L (размер кристаллитов, нм) | Gp (уровень графитизации, %) | n = L/d002 (количество наложенных друг на друга плоскостей углеродного слоя) |
---|---|---|---|---|---|
Fe@С-600 | 26.3 | 0.3386 | 2.94 | 62.8 | 8.68 |
Fe@С-700 | 26.3 | 0.3386 | 11.07 | 62.8 | 32.69 |
Fe@С-800 | 26.3 | 0.3386 | 10.94 | 62.8 | 32.31 |
Fe@С-900 | 26.3 | 0.3386 | 12.72 | 62.8 | 37.57 |
Fe@С-1000 | 26.3 | 0.3386 | 13.74 | 62.8 | 40.58 |
Степень графитизации образованной графитовой структуры, равная 62.8%, близка к степени графитизации коммерческого графита (58.14%) [24]. Следует отметить, что при графитизации МКЦЛ снижается температура начала графитизации с 700–800°С [9, 10, 28] до 600°C.
Термогравиметрический анализ
Кривые TГ и ДTГ образцов MКЦЛ (рис. 3) имеют типичный вид термического разложения лигноцеллюлозной биомассы в инертной среде [18, 25].
Термическое разложение MКЦЛ характеризуется наличием трех стадий, а Fe@MКЦЛ – пяти стадий. Первая стадия всех образцов характеризуется потерей массы из-за испарения воды, оставшейся в предварительно высушенных образцах. Вторая стадия потери массы MКЦЛ в интервале температур 220–350°C обусловлена деградацией гемицеллюлозы и целлюлозы. Температура начала и конца термического разложения MКЦЛ равна 317.1 и 358.0°C соответственно. Третий этап деградации MКЦЛ при температурах выше 350–400°C обусловлен непрерывным разложением лигнина и других компонентов с высокой молекулярной массой [1, 25].
Термогравиметрический анализ образца Fe@МКЦЛ показывает начальную потерю массы 5.9%, обусловленную удалением воды (пик: 68.9°C, ДТГ), оставшейся в предварительно высушенном образце. Второй этап потери массы протекает в интервале температур 138.6–196°C (пик: 174.7°C, ДТГ). В этом интервале температур происходит разложение Fe(NO3)3⋅9H2O по уравнению:
Согласно литературным данным, термическое разложение чистого Fe(NO3)3⋅9H2O с образованием гематита происходит при температуре ~200°C [20, 26]. Третий этап потери массы (44.6%) (302.4–344.3°C, пик: 330.8°C, ДТГ) обусловлен деградацией гемицеллюлозы и целлюлозы (рис. 2).
Четвертый этап потери массы происходит в интервале температур 393.2–464.4°C (пик: 413.2°C, ДТГ). Потеря массы образца Fe@MКЦЛ (9.47%) обусловлена восстановлением аморфным углеродом Fe2O3 до магнетита:
Наличие ярко выраженной ступеньки в интервале 593.8–607.2°C (пик: 599.1°C, ДТГ) на графике ТГ свидетельствует о высокой скорости протекания карботермического восстановления. В этом интервале температур протекают процессы восстановления оксидов железа углеродом до наночастиц Fe0, образующих метастабильные карбиды металла (Fe3С). Последняя стадия потери массы (10.3%) при температуре выше 600°C обусловлена процессами дальнейшей карбонизации и графитизации.
Морфология поверхности композитов
Образец Fe@С-600 имеет относительно гладкую поверхность, покрытую равномерным слоем частиц, имеющих в основном размер ~10 нм (рис. 4). При этом на поверхности углеродного материала имеются и более крупные частицы (~100 нм). Fe@С-700 еще сохраняет относительно гладкую поверхность, покрытую равномерным слоем железосодержащих частиц размером 15–100 нм. Напротив, Fe@С-800 имеет морщинистую поверхность. Дальнейшее увеличение температуры пиролиза способствует образованию более крупных агломератов на всей поверхности Fe@С-900 и Fe@С-1000. На поверхности этих нанокомпозитов равномерный слой железосодержащих частиц имеет размеры 20–300 нм.
Рис. 4.
SEM Fe@С-600 (а), Fe@С-700 (б), Fe@С-800 (в), Fe@С-900 (г), Fe@С-1000 (д) и энергодисперсионный спектр Fe@C-900 (е).
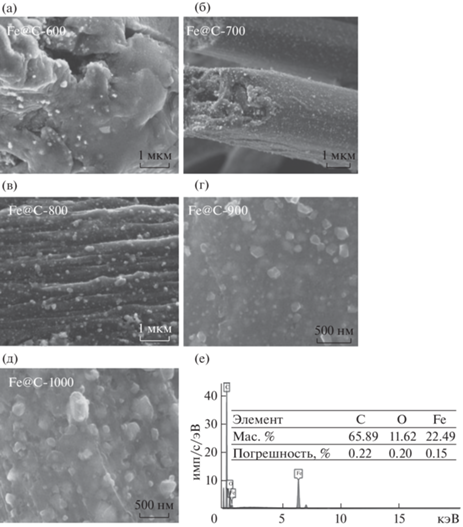
Наличие элементов железа и кислорода в углеродной матрице подтверждается методом энергодисперсионной рентгеновской спектроскопии на примере Fe@C-900 (рис. 4е).
Адсорбционные характеристики
Изотермы адсорбции-десорбции азота всех образцов нанокомпозитов (рис. 5) можно отнести к адсорбции IV типа, обусловленной капиллярной конденсацией азота, имеющей место в мезопорах (2–50 нм) [27]. Присутствие плато при высоких значениях P/Po позволяет квалифицировать изотерму для Fe@С-600, Fe@С-700 и Fe@С-800 как близкую к стандартной изотерме типа IV с гистерезисом H2. Наличие петли гистерезиса H2 свидетельствует о том, что поры имеют узкую форму горловины. Присутствие таких пор в углеродном материале приводит к задержке десорбции азота. Изотерма адсорбции азота для образцов Fe@С-900 и Fe@С-1000 относится к типу IV с петлей гистерезиса, показывающей характеристики как H2, так и H3. Гистерезис типа H3 связан, по-видимому, с пластинчатыми агрегатами и щелевидными порами [4].
Площадь поверхности (SBET) при температуре пиролиза 600°C равна 300.9 м2/г (табл. 2). При 700–800°C площадь поверхности Fe@С-700 и Fe@С-800 уменьшается до 222.7 и 227.3 м2/г соответственно, что, очевидно, связано с ростом количества наложенных друг на друга плоскостей графитового слоя и уменьшением количества аморфного углерода (табл. 1). При этом наблюдается увеличение удельной площади мезопор (Sмезо) до 150.2 и 192.7 м2/г соответственно.
Таблица 2.
Характеристики углеродных композитов
Образец | SBET | Sмикро | Sмезо | Vобщ | Vмикро | Vмезо | Средний размер пор, нм | qа(МС) | qа(МО) | S(МС) | S(МО) |
---|---|---|---|---|---|---|---|---|---|---|---|
м2/г | см3/г | мг/г | м2/г | ||||||||
Fe@С-600 | 300.9 | 162.7 | 138.2 | 0.34 | 0.070 | 0.27 | 4.51 | 87.3 | 19.7 | 323.8 | 33.9 |
Fe@С-700 | 222.7 | 72.55 | 150.2 | 0.262 | 0.032 | 0.23 | 4.71 | 113.3 | 26.4 | 420.3 | 46.5 |
Fe@С-800 | 227.3 | 34.6 | 192.7 | 0.292 | 0.017 | 0.275 | 5.13 | 118.3 | 24.9 | 438.8 | 42.8 |
Fe@С-900 | 126.3 | 13.7 | 112.6 | 0.188 | 0.008 | 0.18 | 5.96 | 82.3 | 18.8 | 305.3 | 33.1 |
Fe@С-1000 | 89.1 | 4.3 | 84.8 | 0.161 | 0.008 | 0.158 | 7.21 | 63.6 | 14.6 | 235.9 | 25.7 |
На кривых распределения пор по размерам (рис. 6) образец Fe@С-600 имеет микропоры (~1.8 нм) и мезопоры (3–5 нм). Кривые распределения пор по размерам Fe@С-700 и Fe@С-800 практически идентичны. Оба образца имеют три группы пор: 1 – около 1.8 нм; 2 – 2.8–3.5 нм; 3 – 3.5–4.7 нм. Данный эффект обусловлен графитизацией в результате которой микропоры расширяются и превращаются в мезопоры [7]. При этом не исключено влияние закупорки микропор железосодержащими частицами из-за образования агломератов.
Увеличение температуры пиролиза до 900 и 1000°C вызывает дальнейшее уменьшение удельной площади поверхности до 126.3 и 89.1 м2/г соответственно. Кривые распределения пор по размерам в этих образцах характеризуются наличием трех групп пор: 1 – около 1.6 нм; 2 – 2.7–3.5 нм; 3 – 3.5–4.8 нм (рис. 6).
Относительно небольшая удельная площадь внешней поверхности Fe@С-900 и Fe@С-1000 обусловлена, вероятно, покрытием поверхности композита равномерным слоем железосодержащих частиц, что подтверждают СЭМ-фотографии (рис. 4), а также ростом количества наложенных друг на друга плоскостей графитового слоя.
Полученные ферромагнитные пористые углеродные материалы исследованы на возможность их использования в качестве адсорбентов катионного МС и анионного МО. Соотношение H+/OH– в водном растворе влияет на структуру молекул красителя МО. Молекулы МО существуют в своей отрицательно заряженной форме при растворении в воде при pH 7, а в кислой среде H+ присоединяется к атому азота азогруппы МО и молекула становится заряженной как положительно, так и отрицательно [28]. В связи с этим адсорбционная емкость полученных материалов по отношению к МО и МС определена при pH 7.
Поскольку поверхность углеродных композитов характеризуется наличием небольшого количества гидроксильных и карбонильных групп, на адсорбционную способность красителей может оказывать электростатическое взаимодействие между адсорбатом и адсорбентом [29, 30].
С другой стороны, МС и МО представляют собой плоские молекулы, которые могут легко адсорбироваться на углеродных композитах за счет взаимодействия между делокализованными π-электронами на поверхности нанокомпозита и свободными электронами в ароматических кольцах молекул красителей [31].
Однако при адсорбции красителей помимо электростатического и π–π-взаимодействий имеются адсорбционные силы взаимодействия, которые зависят от пористой структуры углеродных композитов [30, 31].
Кроме того, при температурах пиролиза выше 700°C увеличивается отношение графитовый углерод/аморфный углерод, что способствует возрастанию π–π-взаимодействия графитовой структуры с ароматическими кольцами красителей. С другой стороны, происходит уменьшение площади поверхности и объема пор, доступных молекулам красителей.
Данные, приведенные в табл. 2, свидетельствуют о том, что механизм поглощения MС и МО включает электростатические, неэлектростатические и адсорбционные взаимодействия. При этом отсутствуют закономерности зависимости адсорбционной емкости красителей от одного типа взаимодействий. По-видимому, соотношение вкладов разных взаимодействий, влияющих на равновесную адсорбционную емкость композитов по отношению к МС и МО, меняется с повышением температуры пиролиза. Путем оценки площади поверхности по величине адсорбции МС и МО в предположении, что молекулы красителя адсорбируются на поверхности углеродного материала в мономерной форме, можно определить степень покрытия поверхности [32].
Для этого величины поверхности полученных композитов были рассчитаны по адсорбции красителей МС и МО по уравнениям:
При площади поверхности 1 моля молекул МО 563.2 × 103 м2 степень покрытия углеродных композитов не превышает 29%. Такое покрытие, вероятно, можно считать монослойным. Напротив, при площади поверхности 1 моля молекул МО 1186.53 м2 только образцы Fe@С-500 и Fe@С-600, возможно, характеризуются монослойным покрытием. Площадь поверхности, рассчитанная для Fe@С-700, Fe@С-800, Fe@С-900 и Fe@С-1000 по адсорбции МС, значительно превышает доступную площадь, рассчитанную по сорбции азота, что указывает на многослойную адсорбцию на поверхности адсорбента. Многослойная адсорбция красителей на магнитных углеродных композитах установлена в работе [33].
ЗАКЛЮЧЕНИЕ
Впервые с помощью простого одностадийного метода синтезированы графитные магнитные материалы с использованием в качестве прекурсора целлюлозы костры льна, модифицированной лимонной кислотой, что позволило снизить температуру начала процесса графитизации до 600°С. Сделано заключение, что механизм поглощения MС и МО включает электростатические, неэлектростатические и адсорбционные взаимодействия. Простая процедура синтеза, возможность удаления в магнитном поле магнитных углеродных частиц и высокая адсорбционная способность делают магнитные материалы Fe@С-700 и Fe@С-800 привлекательными кандидатами для борьбы с загрязнением окружающей среды красителями МС и МО. Равновесные адсорбционные емкости Fe@С-700, Fe@С-800 для МС и МО при pH 7 составляют 113.3, 26.4 и 118.3, 24.9 мг/г соответственно.
Список литературы
Khiari B., Ferjani A.I., Azzaz A.A. et al. // Biomass. Conv. Bioref. 2021. V. 11. P. 325. https://doi.org/10.1007/s13399-020-00641-0
Prusov A.N., Prusova S.M., Radugin M.V. et al. // Fuller. Nanotub. Car. N. 2021. V. 29. № 9. P. 685. https://doi.org/10.1080/1536383X.2021.1881063
Wang C., Yang Q., Ren N. et al. // Chem. Eng. Commun. 2020. https://doi.org/10.1080/00986445.2020.1826940
Thompson E., Danks A.E., Bourgeois L. et al. // Green Chem. 2015. V. 17. P. 551. https://doi.org/10.1039/c4gc01673d
Wu F., Huang R., Mu D. et al. // Electrochim. Acta. 2016. V. 187. P. 508. https://doi.org/10.1016/j.electacta.2015.11.108
Hoekstra J., Beale A.M., Soulimani F. et al. // J. Phys. Chem. C. 2015. V. 119. № 19. P. 10653. https://doi.org/10.1021/acs.jpcc.5b00477
Hoekstra J., Beale M., Soulimani F. et al. // Carbon. 2016. V. 197. P. 248. https://doi.org/10.1016/j.carbon.2016.05.065
Xu Z., Zhou Y., Sun Z. et al. // Chemosphere. 2020. V. 241. P. 125120. https://doi.org/10.1016/j.chemosphere.2019.125120
Xu Y., Luo G., He S. et al. // Fuel. 2019. V. 239. P. 982. https://doi.org/10.1016/j.fuel.2018.11.102
Prusov A.N., Prusova S.M., Bazanov A.V. et al. // Russ. J. Inorg. Chem. 2019. V. 64. P. 431. [Прусов А.Н., Прусова С.М., Базанов А.В. и др. // Журн. неорган. химии. 2019. Т. 64. С. 431.] https://doi.org/10.1134/S003602361904017X
Prusov A.N., Prusova S.M., Zakharov A.G. et al. // Fibre Chem. 2018. V. 50. P. 154. [Прусов А.Н., Прусова С.М., Захаров А.Г. и др. // Хим. волокна. 2018. Т. 15. С. 154.] https://doi.org/10.1007/s10692-018-9952-9
McSweeny J.D., Rowell R.M., Min S.-H. // J. Nat. Fibers. 2006. V. 3. P. 43. https://doi.org/10.1300/J395v03n01_05
Li X., Tang Y., Xuan Z. et al. // Sep. Purif. Technol. 2007. V. 55 P. 69. https://doi.org/10.1016/j.seppur.2006.10.025
Ma B., Huang Y., Zhu C. et al. // J. Alloys Compd. 2016. V. 687. P. 741. https://doi.org/10.1016/j.jallcom.2016.06.187
Destyorini F., Irmawati Y., Hardiansyah A. et al. // Eng. Sci. Technol. Int. J. 2021. V. 24. P. 514. https://doi.org/10.1016/j.jestch.2020.06.011
Hoekstra J., Versluijs-Helder M., Vlietstra E.J. et al. // ChemSusChem. 2015. V. 8. P. 985. https://doi.org/10.1002/cssc.201403364
Vaughana T., Seoa C.W., Marshall W.E. // Bioresour. Technol. 2001. P. 78. P. 133. https://doi.org/10.1016/S0960-8524(01)00007-4
Prusov A.N., Prusova S.M., Radugin M.V. et al. // Fuller. Nanotub. Car. N. 2021. V. 29. P. 232. https://doi.org/10.1080/1536383X.2020.1832994
Shi Q., Zhang J., Zhang C. et al. // J. Environ. Sci. 2010. V. 22. P. 91. https://doi.org/10.1016/S1001-0742(09)60079-6
Gallego J., Tapia J., Vargas M. et al. // Carbon. 2017. V. 111. P. 393. https://doi.org/10.1016/j.carbon.2016.10.014
Barnakov C.N., Khokhlova G.P., Popova A.N. et al. // Euras. Chem. J. 2015. V. 17. P. 87. https://doi.org/10.18321/ectj198
Krivoruchko O.P., Zaikovskii V.I. // Mendeleev Commun. 1998. V. 8. № 3. P. 97. https://doi.org/10.1070/MC1998v008n03ABEH000944
Jozwiak W.K., Kaczmarek E., Maniecki T.P. et al. // Appl. Catal. A: General. 2007. V. 326. P. 17. https://doi.org/10.1016/j.apcata.2007.03.021
Li H., Zhang H., Li K. et al. // Fuel. 2020. V. 279. https://doi.org/10.1016/j.fuel.2020.118531
Sgriccia N., Hawley M.C., Misra M. // Compos. Part A. 2008. V. 39. P. 1632. https://doi.org/10.1016/j.compositesa.2008.07.007
Melnikov P., Nascimento V.A., Arkhangelsky I.V. et al. // J. Therm. Anal. Calorim. 2014. V. 115. P. 145. https://doi.org/10.1007/s10973-013-3339-1
Thommes M., Kaneko K., Neimark A.V. et al. // Pure Appl. Chem. 2015. V. 87. № 9-10. P. 1051. https://doi.org/10.1515/pac-2014-1117
Akama Y., Tong A., Ito M. et al. // Talanta. 1999. V. 48. P. 1133. https://doi.org/10.1016/s0039-9140(98)00331-2
Udayakumar M., Mrabate B.E., Koós T. et al. // Arabian J. Chem. 2021. V. 14. P. 103214. https://doi.org/10.1016/j.arabjc.2021.103214
Prusov A.N., Prusova S.M., Radugin M.V. et al. // Fuller. Nanotub. Car. N. 2021. V. 30. P. 89. https://doi.org/10.1080/1536383X.2021.1989413
Istratie R., Stoia M., Păcurariu C. et al. // Arabian J. Chem. 2019. V. 12. P. 3704. http://dx.doi.org/10.1016/j.arabjc.2015.12.012
Pittman C.U., He G.R., Wu B. et al. // Carbon. 1997. V. 35 № 3. P. 317. https://doi.org/10.1016/S0008-6223(97)89608-X
Hermosa G.C., Liao C.-S., Wang S.-F. et al. // J. Nanosci. Nanotechnol. 2021. V. 21. P. 5756. https://doi.org/10.1166/jnn.2021.19494
Дополнительные материалы отсутствуют.
Инструменты
Журнал неорганической химии