Журнал неорганической химии, 2022, T. 67, № 12, стр. 1839-1850
Влияние добавки 2 об. % графена на теплообмен керамического материала в недорасширенных струях диссоциированного воздуха
Е. П. Симоненко a, *, Н. П. Симоненко a, А. Ф. Колесников b, А. В. Чаплыгин b, В. И. Сахаров c, А. С. Лысенков d, И. А. Нагорнов a, Н. Т. Кузнецов a
a Институт общей и неорганической химии им. Н.С. Курнакова РАН
119991 Москва, Ленинский пр-т, 31, Россия
b Институт проблем механики им. А.Ю. Ишлинского РАН
119526 Москва, пр-т Вернадского, 101, корп. 1, Россия
c Институт механики МГУ им. М.В. Ломоносова
119192 Москва, Мичуринский пр-т, 1, Россия
d Институт металлургии и материаловедения им. А.А. Байкова РАН
119334 Москва, Ленинский пр-т, 49, Россия
* E-mail: ep_simonenko@mail.ru
Поступила в редакцию 15.07.2022
После доработки 25.08.2022
Принята к публикации 26.08.2022
- EDN: FIMXSS
- DOI: 10.31857/S0044457X22601523
Аннотация
С использованием индукционного высокочастотного плазмотрона изучены особенности поведения ультравысокотемпературных керамических материалов (UHTC) HfB2–30 об. % SiC и (HfB2–30 об. % SiC)–2 об. % CG под воздействием недорасширенных струй диссоциированного воздуха. Измеренные на финальной стадии эксперимента значения тепловых потоков составили 120 и 111 Вт · см–2 соответственно. Установлено, что для модифицированной графеном керамики температура поверхности незначительно меньше (на 35–75°С) по сравнении с базовым UHTC, однако микроструктура, элементный и фазовый состав окисленной поверхности сильно различались: для (HfB2–30 об. % SiC)–2 об. % CG, помимо снижения количества сферических выпуклых частиц, образовавшихся при выходе на поверхности боросиликатного расплава, отмечено формирование ажурных слоистых образований, предположительно, борной кислоты. Для оцененных интегральных коэффициентов излучения отмечена тенденция к уменьшению в ходе термохимического воздействия. Установлено, что в условиях обтекания сверхзвуковой струей воздушной плазмы исследованные материалы проявляют себе как низкокаталитичные.
ВВЕДЕНИЕ
Керамические материалы на основе диборидов циркония и гафния, допированные карбидом кремния, выдерживающие в том числе длительные термохимические воздействия потоков диссоциированного воздуха с разогревом до температур >2000°С [1–11], признаны чрезвычайно перспективными, прежде всего, в области создания новых моделей авиа-космической техники [12–24].
При всем уникальном комплексе свойств ультравысокотемпературных керамических материалов (UHTC) на основе ZrB2(HfB2)–SiC остро стоят задачи дополнительного повышения их стойкости к окислению (прежде всего, препятствованию реализации негативного эффекта резкого роста температуры поверхности с ~1750–1900 до >2500°С, что приводит к серьезной деградации материала), а также улучшения их трещиностойкости. В связи с этим очень широко развиваются исследования, направленные на разработку методов получения и изучения влияния добавок различной химической природы, преимущественно сверхтугоплавких карбидов [25–36], нитридов [37–44], силицидов металлов [35, 45–48], собственно металлических компонентов [49–55], а также углеродных материалов различного рода – углеродных волокон и нанотрубок, нанопластинок графита и графена [4, 52, 56–64].
Несмотря на имеющиеся в литературных источниках данные об эффективности введения графеновых нанопластинок на улучшение трещиностойкости UHTC, данные по изучению поведения таких керамических материалов в высокоэнтальпийных газовых потоках практически отсутствуют. Недостаточно информации об экспериментальном определении таких важнейших свойств ультравысокотемпературных материалов на основе ZrB2(HfB2)–SiC, как коэффициент излучения и коэффициент гетерогенной рекомбинации атомов кислорода и азота, присутствующих в набегающей высокоэнтальпийной струе воздуха. Присутствуют отрывочные сведения по результатам экспериментов с различными условиями (давление в камере, энтальпия и скорость газового потока, время воздействия) для системы ZrB2–SiC [53, 65–75]. Для керамики HfB2–SiC имеются лишь единичные данные, полученные в статичном нагреве [6, 76].
В предыдущих исследованиях нашей группой разработаны методики изучения данных характеристик под воздействием сверхзвуковых потоков диссоциированного азота на примере материалов различной природы – графите [77], керамики HfB2–SiC, HfB2–SiC–CG (где CG – восстановленный оксид графена) [78], а также ZrB2–HfB2–SiC и ZrB2–HfB2–SiC–CCNT (где CCNT – многослойные углеродные нанотрубки) [79]. На примере графена установлено, что при использованных относительно низкой измеренной плотности теплового потока (q = 244–290 Вт · cм–2) допирование углеродным компонентом практически не сказывается на поведении и свойствах (коэффициент излучения, эффективный коэффициент гетерогенной рекомбинации атомов азота). В то время как в исследованиях [80, 81], выполненных в сверхзвуковых потоках диссоциированного воздуха (q = 363–779 Вт · cм–2) показано принципиальное влияние введения незначительного количества восстановленного оксида графена как на температуру, устанавливающуюся на поверхности, так и на химический, и фазовый состав окисленной поверхности.
Целью настоящей работы является исследование влияния введения 2 об. % графена на теплообмен керамического материала в недорасширенных струях диссоциированного воздуха при относительно низких тепловых потоках, оценка изменения коэффициента излучения и каталитического поведения по отношению к процессам поверхностной рекомбинации атомов кислорода.
ЭКСПЕРИМЕНТАЛЬНАЯ ЧАСТЬ
Методика получения UHTC на основе HfB2–30 об. % SiC, модифицированных восстановленным оксидом графена, подробно описана в [80, 81]. Для этого твердые материалы – порошки HfB2 (>98%, размер частиц 2–3 мкм, а размер агрегатов 20–60 мкм, “Тугоплавкие материалы”) и оксида графена (размер пластинок ≤3 мкм, число графеновых слоев ≤2, “АккоЛаб”) диспергировались в растворе фенолформальдегидной смолы (“Карболит”). В полученную дисперсию вводили катализатор гидролиза муравьиную кислоту (>99%, “Спектр-Хим”) и тетраэтоксисилан (ос. ч., “ЭКОС-1”) с последующим гидролизом водой. После сушки полученный ксерогель карбонизировали с формированием исходного композиционного порошка HfB2–(SiO2–C)–rGO (где rGO – восстановленный оксид графена), который подвергали реакционному горячему прессованию в графитовых пресс-формах с применением пресса горячего прессования Thermal Technology Inc. (модель HP20-3560-20) при температуре 1800°С (скорость нагрева 10 град/мин, время выдержки 15 мин) и давлении 30 МПа. Перед термохимическим воздействием выполняли шлифовку поверхности образцов.
Исследование поведения керамических материалов HfB2–30 об. % SiC и (HfB2–30 об. % SiC)–2 об. % CG при воздействии сверхзвукового потока недорасширенных высокоэнтальпийных струй воздуха, истекающих из водоохлаждаемого конического сопла с диаметром выходного сечения 50 мм, осуществляли на 100-киловаттном высокочастотном индукционном плазмотроне ВГУ-4. Расстояние от сопла до образца фиксировали на значении 30 мм, расход воздуха составлял 3.6 г/с (контролировали электронным газовым ротаметром Bronkhorst MV-306), давление в камере находилось в интервале (8.1–9.4) × 102 Па, целевое значение составляло 8.5 × 102 Па. Цилиндрические образцы диаметром 15 мм и толщиной 3.1–3.7 мм вводили в высокоэнтальпийную струю при заданной мощности анодного питания плазмотрона (N) 64 ± 0.6 кВт, которая оставалась постоянной (в пределах погрешности) в течение всего эксперимента. Суммарное время воздействия составляло 10 мин (600 с). Геометрия модели, в которой закрепляли образцы, подробно описана в работах [77, 78, 82]: образцы устанавливали на трении в гнезде водоохлаждаемого калориметра, зазор заполняли гибкой теплоизоляцией на основе SiC и углевойлока с целью минимизации тепловых потерь. Расход охлаждающей воды в калориметре измеряли ультразвуковым жидкостным расходомером Bronkhorst ES-FLOW. Разность температур охлаждающей воды на выходе и входе из калориметра измеряли экранированной дифференциальной термопарой хромель-алюмель.
Среднюю температуру поверхности нагретого образца в центральной его области (диаметр области визирования составлял ~5 мм) измеряли с применением инфракрасного пирометра Mikron M-770S в режиме пирометра спектрального отношения (температурный интервал 1000–3000°C). Изучение распределения температур по поверхности образца производили с использованием термовизора Тандем VS-415U. Термоизображения записывали при установленном значении спектрального коэффициента излучения ε на длине волны 0.9 мкм, равном 1, поскольку в ходе воздействия предполагалось изменение ε. Коррекция к реальным значениям средних температур центральной области, определенных с использованием инфракрасного пирометра, позволила оценить значение спектрального коэффициента излучения и его изменение для обоих материалов в ходе термохимического воздействия. Методика определения теплового потока к лицевой поверхности образца подробно описана в [78].
Для условий экспериментов на установке ВГУ-4 провели численное моделирование неравновесного течения плазмы воздуха в разрядном канале, в истекающих недорасширенных струях воздушной плазмы и при обтекании державки с образцом. Геометрия расчетной области и использованные расчетные методы аналогичны применявшимся в [77] для графитовых образцов, нагретых в сверхзвуковых струях азотной плазмы. Расчет был основан на комплексе программ численного интегрирования уравнений Навье–Стокса [83].
В табл. 1 приведены значения тепловых потоков к нагретым поверхностям образцов, полученные в экспериментах. На рис. 1 показаны расчетные плотности тепловых потоков в точке торможения в зависимости от величины эффективного коэффициента гетерогенной рекомбинации атомов азота и кислорода γw на поверхности керамики при температуре поверхности, измеренной в эксперименте. Там же точкой 3 отмечено значение теплового потока, полученное в эксперименте.
Таблица 1.
Экспериментальные значения тепловых потоков и цветовой температуры в центре лицевой поверхности образцов
Образец | Tw, K | Тепловой поток, Вт/см2 |
---|---|---|
HfB2–30 об. % SiC | 1750 | 120 |
(HfB2–30 об. % SiC)–2 об. % CG | 1716 | 111 |
Рис. 1.
Рассчитанные зависимости плотностей тепловых потоков в критической точке цилиндрической модели Qw с керамическими образцами от эффективного коэффициента каталитической рекомбинации атомов азота и кислорода γ; маркером 3 на кривой отмечены экспериментальные данные.
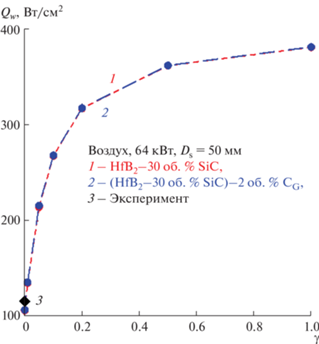
Как видно из табл. 1 измеренные значения тепловых потоков при одинаковом режиме обтекания для обоих керамических образцов практически совпадают, но температура поверхности модифицированного графеном образца керамики оказалась ниже.
Рентгенограммы полученных керамических материалов, а также их поверхности после воздействия недорасширенных струй диссоциированного воздуха записывали на рентгеновском дифрактометре Bruker D8 Advance (излучение CuKα, разрешение 0.02° при накоплении сигнала в точке в течение 0.3 с). Рентгенофазовый анализ выполняли с применением программы MATCH! – Phase Identification from Powder Diffraction, Version 3.8.0.137 (Crystal Impact, Germany), база данных Crystallography Open Database.
Исследование особенностей микроструктуры окисленной поверхности материалов после воздействия на них сверхзвукового потока диссоциированного воздуха выполняли методом растровой электронной микроскопии (РЭМ) на трехлучевой рабочей станции NVision 40, Carl Zeiss с ускоряющим напряжением 1 и 20 кВ. Элементный состав областей определяли с помощью приставки для энергодисперсионного анализа EDX Oxford Instrumets.
РЕЗУЛЬТАТЫ И ОБСУЖДЕНИЕ
Рентгенограммы исходных материалов HfB2–30 об. % SiC и (HfB2–30 об. % SiC)–2 об. % CG, записанные перед воздействием недорасширенных струй диссоциированного воздуха (рис. 2, кривые 1 и 2), подтвердили полную конверсию состава SiO2–C в нанокристаллический кубический SiC [84] (средний размер области когерентного рассеяния, оцененный по методу Шеррера, составил 42–48 нм), как это отмечалось ранее [80, 81]. Основной фазой остается гексагональный диборид гафния [85].
Рис. 2.
Рентгенограммы образцов полученных образцов HfB2–30 об. % SiC (1, 3) и (HfB2–30 об. % SiC)–2об. % CG (2, 4) до (1, 2) и после термохимического воздействия (3, 4).
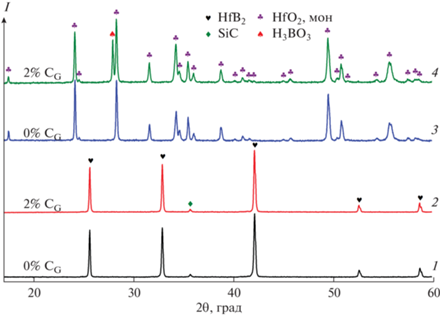
Для изучения особенностей окисления данных керамических материалов закрепленный в водоохлаждающей модели образец вводили в сверхзвуковую струю с заданной мощностью анодного питания (64 кВт), после чего выдерживали в течение 10 мин. Охлаждение происходило после отключения питания плазмотрона при обтекании воздухом.
Данные ИК-пирометра спектрального отношения (рис. 3) показали, что для недопированного материала HfB2–30 об. % SiC отмечается повышенная по сравнению с допированным графеном материалом температура поверхности, особенно в начале эксперимента – в конце первой минуты воздействия она составляет 1530°С. По мере изменения состава поверхности под действием окисления происходит существенное снижение температуры поверхности до ~1480°С. При этом на второй половине шестой минуты эксперимента происходит стабилизация температуры поверхности в интервале 1478–1482°С. Суммарный перепад температур за 10 мин воздействия при фиксированной мощности составил около 50°С.
Рис. 3.
Изменение средней температуры в центре лицевой поверхности образца (Т), определенной с помощью ИК-пирометра, мощности генератора плазмотрона по анодному питанию (N) и давления в барокамере (Р) в эксперименте по теплообмену образцов HfB2–30 об. % SiC (а) и (HfB2–30 об. % SiC)–2 об. % CG (б) в недорасширенной высокоэнтальпийной воздушной струе.
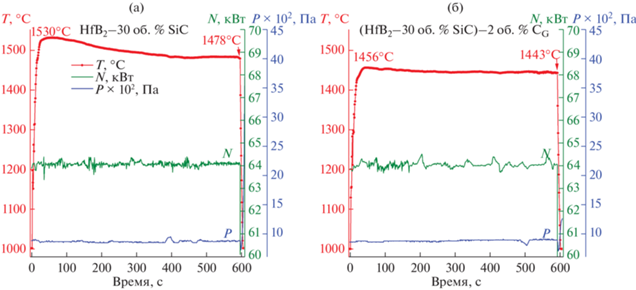
Для образца ультравысокотемпературного керамического материала, допированного 2 об. % графена, уже на первых минутах воздействия на поверхности установилась температура 1456°С, что на ~75°С ниже по сравнению с таковой для образца HfB2–30 об. % SiC. Однако и снижение данного параметра за время эксперимента также отмечалось гораздо меньшее: за 10 мин окисления она уменьшилось до 1443°С.
Анализ данных термовизора (рис. 4) показал, что для обоих керамических материалов характерно достаточно равномерное распределение температуры по всей лицевой поверхности. На поверхности отсутствуют отдельные яркие точки, обычно связанные с перегретыми участками поверхности, от которых начинается резкий рост температуры (“скачок температуры” [86]), наблюдавшийся в том числе для материалов, допированных графеном, при длительном (33 мин) воздействии со ступенчатым увеличением мощности и соответствующим повышением теплового потока с 363 до 779 Вт · см–2 в другой конфигурации закрепления керамических образцов в модели [80, 81]. Тем не менее, на температурных профилях видно, что для материала HfB2–30 об. % SiC наблюдается несколько больший перепад температур (~55–60°C) по сравнению с таковым для модифицированного графеном материала (~35–40°C), что может объясняться более высокой теплопроводностью последнего.
Рис. 4.
Тепловые изображения на различных стадиях воздействия и типичные распределения температуры вдоль диаметра на 1, 5 и 10 мин эксперимента образцов HfB2–30 об. % SiC (а) и (HfB2–30 об. % SiC)–2 об. % CG (б).
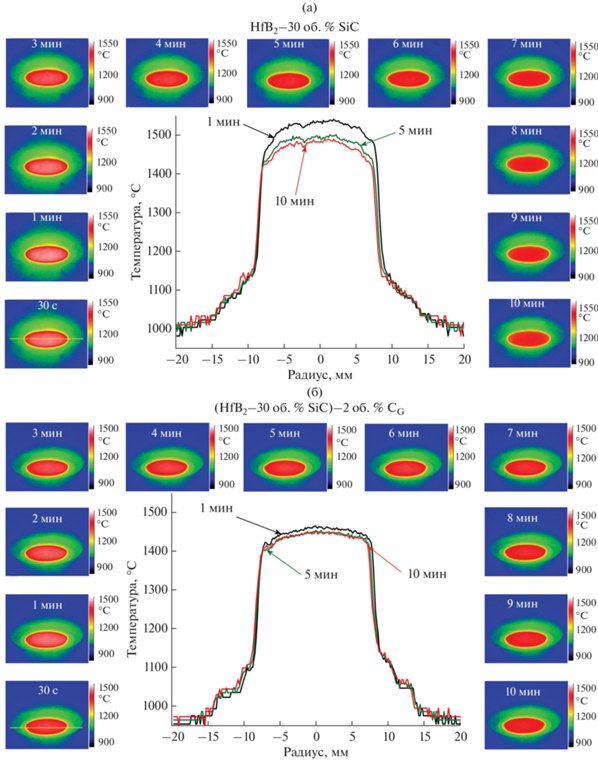
Изменение массы образцов после воздействия на них сверхзвуковых потоков диссоциированного воздуха в обоих случаях чрезвычайно мало: для материала HfB2–30 об. % SiC наблюдался прирост массы ~0.09%, а для (HfB2–30 об. % SiC)–2 об. % CG – унос составил 0.04%, что свидетельствует о малой деградации, вероятно, преимущественно на поверхности.
Определенные тепловые потоки для обоих образцов, измеренные непосредственно перед завершением воздействия, очень близки и составили 120 (для HfB2–30 об. % SiC) и 111 Вт см–2 (для (HfB2–30 об. % SiC)–2 об. % CG).
Оценка интегрального коэффициента излучения εt показала, что по мере воздействия и, соответственно, окисления поверхности материалов происходит систематическое снижение данного показателя: с 0.61 до 0.53 для керамики HfB2–30 об. % SiC и с 0.50 до 0.45 для материала (HfB2–30 об. % SiC)–2 об. % CG. Такое поведение характерно для ультравысокотемпературных керамических материалов на основе ZrB2–SiC (для составов на основе HfB2–SiC исследований зависимости излучательных свойств от состава поверхности нами не найдено). Так, в исследовании [72] для образцов состава ZrB2–15 об. % SiC и ZrB2–10 об. % HfB2–15 об. % SiC при давлении 10 и 200 Па установлено, что при температуре <1500 K интегральный полусферический коэффициент излучения (0.6–40 мкм) составляет 0.7–0.75, а при более высокой температуре определяется оксидным составом поверхности. В работе [65] показано, что при давлении в камере 200 Па и ступенчатом нагреве с 1300 до 1800°С (суммарное время воздействия 10 мин) для керамических изделий полусферической формы и в виде закругленного конуса (состав ZrB2–20 об. % SiC) под воздействием потока диссоциированного воздуха (q = 4.7–11 МВт · м–2) спектральный коэффициент излучения (1 мкм) уменьшается с ~0.8 до 0.63–0.66 (в зависимости от формы детали). В исследовании [73] показано, что на температурную зависимость излучательных свойств существенное влияние оказывает не только соотношение основных компонентов, но и химическая природа, и содержание спекающей добавки (на примере Si3N4 и ZrSi2). В работах [67] и [68] экспериментально изучено влияние состояния поверхности (в том числе химический состав, толщина оксидного слоя, шероховатости) образца ZrB2–20 об. % SiC на коэффициенты излучения; подтвержден факт, что наличие на поверхности стекловидного силикатного слоя приводит к их увеличению. Присутствие на поверхности пористого ZrO2 повышает спектральный коэффициент излучения в ~1.5 раза по сравнению с образцом, поверхность которого покрыта силикатным стеклом (в результате предварительного окисления) [68]. Единственный найденный источник [70], в котором изучены оптические свойства керамики, модифицированной углеродным материалом – графитом, состава ZrB2–15 об. % SiC–15 об. % C также свидетельствует о том, что предварительное окисление в стоячем воздухе приводит к снижению интегрального нормального коэффициента излучения с 0.91 до 0.66 по мере увеличения температуры окисления с 1100 до 1800°С и, следовательно, изменения состава окисленной поверхности.
Несмотря на то, что корректное определение излучательной способности поверхности материала, нагретого до высокой температуры реакционно способным высокоэнтальпийным потоком газа, представляет собой отдельную сложную задачу, которая не была целью настоящей работы, в данном случае на основе оценок значений εt для материалов разного состава можно сделать общий вывод о существующей тенденции к их снижению по мере окисления в результате модификации состава поверхности. При этом разница в полученных величинах может быть связана с различием в химическом составе окисленной поверхности UHTC.
Из сравнений величин плотностей тепловых потоков, полученных в расчетах и экспериментах, можно заключить, что эффективный коэффициент гетерогенной рекомбинации атомов азота и кислорода γw меньше 0.01. Таким образом, в условиях обтекания сверхзвуковой струей воздушной плазмы образцы керамики проявляют себе как низкокаталитичные материалы.
Рентгенофазовый анализ окисленной поверхности (рис. 2, кривые 3 и 4) показал, что несмотря на незначительную разницу и в температуре поверхности, установившейся в результате нагрева недорасширенной высокоэнтальпийной воздушной струей, и в тепловых потоках, ее фазовый состав различается. Основным кристаллическим продуктом окисления (а для образца HfB2–30 об. % SiC – единственным) является моноклинный оксид гафния [87]. В то время как для модифицированного 2 об. % графена образца на поверхности присутствует большое количество борной кислоты [88], которая образуется при хранении материала, содержащего оксид бора, при обычной атмосферной влажности.
Исследование особенностей микроструктуры поверхности методом РЭМ с локальным EDX-анализом подтверждает значительное различие в химическом составе и морфологии окисленной поверхности образцов HfB2–30 об. % SiC и (HfB2–30 об. % SiC)–2 об. % CG (рис. 5–8). Так, для немодифицированного UHTC (рис. 5) поверхность покрыта пористой керамической коркой, которая преимущественно состоит из оксида гафния, о чем свидетельствуют данные EDX-анализа (табл. 2, n(Hf) : n(Si) ≈ 9) и картирования распределения элементов Hf и Si (рис. 6). Причем, слой HfO2 является нанопористым (размер пор варьируется в интервале 15–50 нм). По поверхности достаточно равномерно распределены выступающие сферические образования – пузырьки на основе боросиликатного стекла, обогащенного кремнием, размер которых находится в интервале от 4 до 40 мкм. Несмотря на то, что в местах их локализации на рис. 6 очень заметно снижение содержания гафния, а, по данным EDX анализа, n(Hf) : n(Si) составляет 0.2, анализ микрофотографий, полученных в режиме контраста по среднему атомному номеру (рис. 5г), показывает, что при формировании таких пузырьков в результате нагрева образца происходит также захват высокодисперсных частиц HfO2 (размер ~50–300 нм), образующих внешнюю сферическую поверхность.
Рис. 5.
Микроструктура окисленной поверхности образца HfB2–30 об. % SiC по данным РЭМ: а, б, в, д – по данным детектора вторичных электронов; г, е – в режиме контраста по среднему атомному номеру, ускоряющее напряжение 1 кВ; на врезке – распределение по размерам диаметров пузырьков на поверхности.
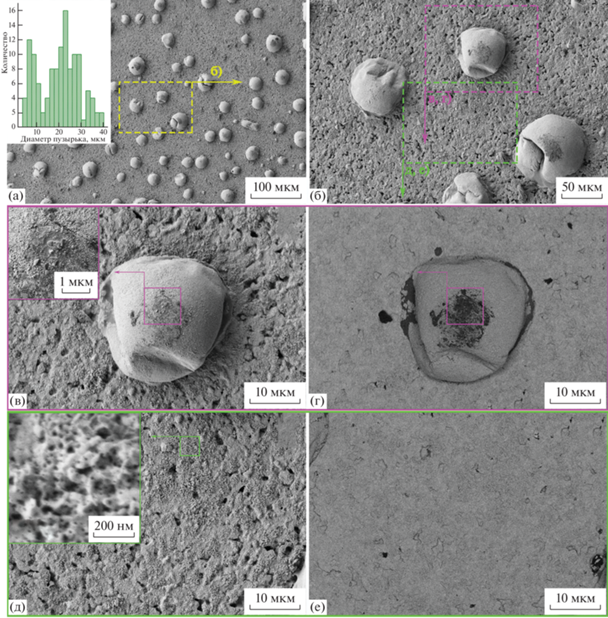
Рис. 6.
Микроструктура (РЭМ, ускоряющее напряжение 20 кВ) и соответствующее картирование распределения элементов на окисленной поверхности образца HfB2–30 об. % SiC.
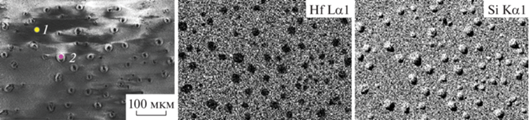
Рис. 7.
Микроструктура окисленной поверхности образца (HfB2–30 об. % SiC)–2 об. % СG по данным РЭМ: а, б, в, д, ж – по данным детектора вторичных электронов; г, е, з – в режиме контраста по среднему атомному номеру, ускоряющее напряжение 1 кВ; на врезке – распределение по размерам диаметров пузырьков на поверхности.
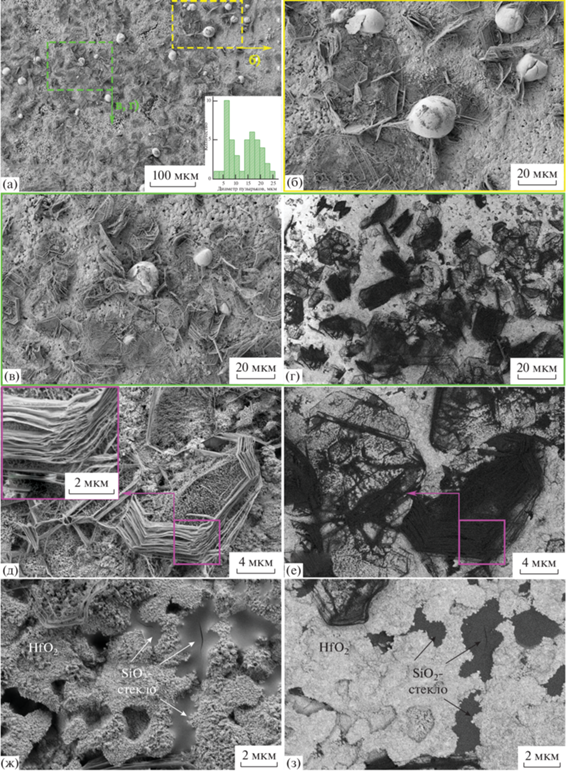
Рис. 8.
Микроструктура (РЭМ, ускоряющее напряжение 20 кВ) и соответствующее картирование распределения элементов на окисленной поверхности образца (HfB2–30 об. % SiC)–2 об. % СG.
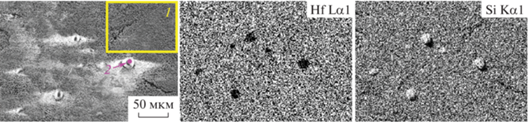
Таблица 2.
Мольное соотношение гафния и кремния на окисленной поверхности (данные EDX)
Область | n(Hf) : n(Si) |
---|---|
Образец HfB2–30 об. % SiC* | |
Полная область микрофотографии | 2.18 |
Точка 1 (между пузырьками) | 9.24 |
Точка 2 (пузырек) | 0.22 |
Образец (HfB2–30 об. % SiC)–2 об. % CG** | |
Полная область микрофотографии | 3.35 |
Область 1 (между пузырьками) | 4.90 |
Точка 2 (пузырек) | 0.05 |
Для образца (HfB2–30 об. % SiC)–2 об. % CG над преимущественно керамической поверхностью HfO2 также выступают пузырьки (рис. 7), которые образовали капли проступающего силикатного расплава. Однако их количество существенно меньше (рис. 8), о чем свидетельствует увеличение отношения n(Hf) : n(Si), полученное для всей области сканирования. Кроме того, заметно (рис. 7з), что сплошность керамического верхнего слоя на основе HfO2 значительно меньше по сравнению с образцом HfB2–30 об. % SiC – между островками пористого диоксида гафния встречаются области силикатного расплава на основе SiO2.
Необходимо отметить присутствие на поверхности образца (HfB2–30 об. % SiC)–2 об. % CG после термохимического воздействия большого количества объемных ажурных структур, ранее отнесенных полимерному SiO [89]. Однако более тщательное исследование, в том числе анализ морфологии частиц, позволяет предположить, что эти образования относятся скорее к частицам борной кислоты (рефлексы которой присутствуют на рентгенограмме окисленной поверхности (рис. 2, кривая 4)), которая образуется при хранении оксида бора в газовой среде, содержащей атмосферную влагу. Таким образом, можно косвенно сказать, что образование подобных объемных структур H3BO3 является маркером повышенного содержания оксида бора в составе боросиликатного стекла на поверхности керамики. Вероятно, это вызвано меньшей температурой, установившейся на поверхности в результате нагрева высокоэнтальпийным потоком воздуха.
ЗАКЛЮЧЕНИЕ
Для ультравысокотемпературных керамических материалов HfB2–30 об. % SiC и (HfB2–30 об. % SiC)–2 об. % CG выполнено экспериментальное и численное исследование течений и теплообмена в недорасширенных струях диссоциированного воздуха для условий, которые реализуются на 100-киловаттном ВЧ-плазмотроне ВГУ-4.
Несмотря на достаточно близкие значения температур, установившиеся на поверхности в результате нагрева высокоэнтальпийным потоком диссоциированного воздуха (для немодифицированного образца температура превысила таковую для образца, содержащего графен, лишь на 35–75°С) и близость измеренных тепловых потоков (111 и 120 Вт см–2), отмечены значительные различия в микроструктуре, элементном и фазовом составе окисленной поверхности.
Вероятно, с этим связано и различие значений оцененного интегрального коэффициента излучения для этих керамических материалов. Однако для обоих UHTC отмечена общая тенденция к снижению εt по мере окисления, что соответствует описанной в литературе ситуации. Так, для керамического материала HfB2–30 об. % SiC установлено уменьшение данного параметра в результате термохимического воздействия с 0.61 до 0.53, а для керамики (HfB2–30 об. % SiC)–2об. % CG – с 0.50 до 0.45.
Установлено, что в условиях обтекания сверхзвуковой струей воздушной плазмы исследованные образцы керамики проявляют себе как низкокаталитичные материалы.
Список литературы
Sevast’yanov V.G., Simonenko E.P., Gordeev A.N. et al. // Russ. J. Inorg. Chem. 2013. V. 58. № 11. P. 1269. https://doi.org/10.1134/S003602361311017X
Sevastyanov V.G., Simonenko E.P., Gordeev A.N. et al. // Russ. J. Inorg. Chem. 2014. V. 59. № 11. P. 1298. https://doi.org/10.1134/S0036023614110217
Sevastyanov V.G., Simonenko E.P., Gordeev A.N. et al. // Russ. J. Inorg. Chem. 2014. V. 59. № 12. P. 1361. https://doi.org/10.1134/S0036023614120250
Dubey S., Ariharan A., Nisar A. et al. // Scr. Mater. 2022. V. 218. P. 114776. https://doi.org/10.1016/j.scriptamat.2022.114776
Liégaut C., Bertrand P., Maillé L. et al. // J. Eur. Ceram. Soc. 2022. V. 42. № 7. P. 3168. https://doi.org/10.1016/j.jeurceramsoc.2022.02.029
Pellegrini C., Balat-Pichelin M., Rapaud O. et al. // Ceram. Int. 2022. V. 48. № 2. P. 2177. https://doi.org/10.1016/j.ceramint.2021.09.310
Simonenko E.P., Simonenko N.P., Papynov E.K. et al. // Russ. J. Inorg. Chem. 2018. V. 63. № 1. P. 1. https://doi.org/10.1134/S0036023618010187
Simonenko E.P., Simonenko N.P., Gordeev A.N. et al. // J. Sol-Gel Sci. Technol. 2019. V. 92. № 2. P. 386. https://doi.org/10.1007/s10971-019-05029-9
Han J., Hu P., Zhang X. et al. // Compos. Sci. Technol. 2008. V. 68. № 3–4. P. 799. https://doi.org/10.1016/j.compscitech.2007.08.017
Potanin A.Y., Astapov A.N., Pogozhev Y.S. et al. // J. Eur. Ceram. Soc. 2021. V. 41. № 16. P. 34. https://doi.org/10.1016/j.jeurceramsoc.2021.09.018
Симоненко Е.П., Симоненко Н.П., Севастьянов В.Г. et al. Ультравысокотемпературные керамические материалы: современные проблемы и тенденции. М.: ИП Коняхин А.В. (Book Jet), 2020.
Nisar A., Hassan R., Agarwal A. et al. // Ceram. Int. 2022. V. 48. № 7. P. 8852. https://doi.org/10.1016/j.ceramint.2021.12.199
Aguirre T.G., Lamm B.W., Cramer C.L. et al. // Ceram. Int. 2022. V. 48. № 6. P. 7344. https://doi.org/10.1016/j.ceramint.2021.11.314
Squire T.H., Marschall J. // J. Eur. Ceram. Soc. 2010. V. 30. № 11. P. 2239. https://doi.org/10.1016/j.jeurceramsoc.2010.01.026
Fahrenholtz W.G., Hilmas G.E. // Int. Mater. Rev. 2012. V. 57. № 1. P. 61. https://doi.org/10.1179/1743280411Y.0000000012
Savino R., Criscuolo L., Di Martino G.D. et al. // J. Eur. Ceram. Soc. 2018. V. 38. № 8. P. 2937. https://doi.org/10.1016/j.jeurceramsoc.2017.12.043
Parthasarathy T.A., Petry M.D., Cinibulk M.K. et al. // J. Am. Ceram. Soc. 2013. V. 96. № 3. P. 907. https://doi.org/10.1111/jace.12180
Paul A., Jayaseelan D.D., Venugopal S. et al. // Am. Ceram. Soc. Bull. 2012. V. 91. № 1. P. 22.
Justin J.F., Jankowiak A. // J. AerospaceLab 2011. V. 3. № AL03-08. P. 11.
Parthasarathy T.A., Rapp R.A., Opeka M. et al. // J. Am. Ceram. Soc. 2012. V. 95. № 1. P. 338.
Opeka M.M., Talmy I.G., Zaykoski J.A. // J. Mater. Sci. 2004. V. 39. № 19. P. 5887. https://doi.org/10.1023/B:JMSC.0000041686.21788.77
Eakins E., Jayaseelan D.D., Lee W.E. // Metall. Mater. Trans. A 2011. V. 42. № 4. P. 878. https://doi.org/10.1007/s11661-010-0540-8
Pogozhev Y.S., Potanin A.Y., Rupasov S.I. et al. // Russ. J. Non-Ferrous Met. 2020. V. 61. № 6. P. 704. https://doi.org/10.3103/S1067821220060164
Justin J.-F., Julian-Jankowiak A., Guérineau V. et al. // CEAS Aeronaut. J. 2020. V. 11. № 3. P. 651. https://doi.org/10.1007/s13272-020-00445-y
Simonenko E.P., Simonenko N.P., Sevastyanov V.G. et al. // Russ. J. Inorg. Chem. 2019. V. 64. № 14. P. 1697. https://doi.org/10.1134/S0036023619140079
Jarman J.D., Fahrenholtz W.G., Hilmas G.E. et al. // J. Eur. Ceram. Soc. 2022. V. 42. № 5. P. 2107. https://doi.org/10.1016/j.jeurceramsoc.2022.01.019
Liu C., Yuan X., Wang W. et al. // Ceram. Int. 2022. V. 48. № 3. P. 4055. https://doi.org/10.1016/j.ceramint.2021.10.195
Silvestroni L., Gilli N., Migliori A. et al. // Compos. Part B Eng. 2020. V. 183. P. 107618. https://doi.org/10.1016/j.compositesb.2019.107618
Ghassemi Kakroudi M., Dehghanzadeh Alvari M., Shahedi Asl M. et al. // Ceram. Int. 2020. V. 46. № 3. P. 3725. https://doi.org/10.1016/j.ceramint.2019.10.093
Silvestroni L., Mungiguerra S., Sciti D. et al. // Corros. Sci. 2019. V. 159. P. 108125. https://doi.org/10.1016/j.corsci.2019.108125
Ma H.-B., Zou J., Zhu J.-T. et al. // Scr. Mater. 2018. V. 157. P. 76. https://doi.org/10.1016/j.scriptamat.2018.07.038
Zou J., Rubio V., Binner J. // Acta Mater. 2017. V. 133. P. 293. https://doi.org/10.1016/j.actamat.2017.05.033
Ma H.-B., Zou J., Zhu J.-T. et al. // Acta Mater. 2017. V. 129. P. 159. https://doi.org/10.1016/j.actamat.2017.02.052
Monteverde F., Silvestroni L. // Mater. Des. 2016. V. 109. P. 396. https://doi.org/10.1016/j.matdes.2016.06.114
Liu Z., Bu H., Zhang W. et al. // Ceram. Int. 2022. V. 48. № 15. P. 21162. https://doi.org/10.1016/j.ceramint.2022.04.009
Mohammadzadeh B., Jung S., Lee T.H. et al. // Ceram. Int. 2021. V. 47. № 8. P. 11438. https://doi.org/10.1016/j.ceramint.2020.12.271
Wei C., Zhang Z., Ma X. et al. // Corros. Sci. 2022. V. 197. P. 110051. https://doi.org/10.1016/j.corsci.2021.110051
Zhang J., Chen H., Xiao G. et al. // Ceram. Int. 2022. V. 48. № 6. P. 8097. https://doi.org/10.1016/j.ceramint.2021.12.011
Golla B.R., Thimmappa S.K. // J. Alloys Compd. 2019. V. 797. P. 92. https://doi.org/10.1016/j.jallcom.2019.05.097
Ahmadi Z., Nayebi B., Shahedi Asl M. et al. // Ceram. Int. 2017. V. 43. № 13. P. 9699. https://doi.org/10.1016/j.ceramint.2017.04.144
Xia C., Delbari S.A., Ahmadi Z. et al. // Ceram. Int. 2020. V. 46. № 18. P. 29334. https://doi.org/10.1016/j.ceramint.2020.08.054
Nguyen V.-H., Ali Delbari S., Ahmadi Z. et al. // Results Phys. 2020. V. 19. P. 103348. https://doi.org/10.1016/j.rinp.2020.103348
Zhang Z., Wei C., Liu R. et al. // Ceram. Int. 2021. V. 47. № 9. P. 11973. https://doi.org/10.1016/j.ceramint.2021.01.039
Pourmohammadie Vafa N., Ghassemi Kakroudi M., Shahedi Asl M. // Ceram. Int. 2020. V. 46. № 13. P. 21533. https://doi.org/10.1016/j.ceramint.2020.05.255
Yang Y., Qian Y., Xu J. et al. // Ceram. Int. 2018. V. 44. № 14. P. 16150. https://doi.org/10.1016/j.ceramint.2018.05.075
Jaberi Zamharir M., Zakeri M., Razavi M. et al. // Int. J. Refract. Met. Hard Mater. 2022. V. 103. P. 105775. https://doi.org/10.1016/j.ijrmhm.2021.105775
Zhu M., Zhang L., Li N. et al. // Ceram. Int. 2022. https://doi.org/10.1016/j.ceramint.2022.05.378
Gui K., Liu F., Wang G. et al. // J. Adv. Ceram. 2018. V. 7. № 4. P. 343.
Bai Y., Ma Y., Sun M. et al. // J. Eur. Ceram. Soc. 2019. V. 39. № 14. P. 3938. https://doi.org/10.1016/j.jeurceramsoc.2019.06.005
Gopinath N.K., Jagadeesh G., Basu B. // J. Am. Ceram. Soc. 2019. V. 102. № 11. P. 6925. https://doi.org/10.1111/jace.16548
Purwar A., Thiruvenkatam V., Basu B. // J. Am. Ceram. Soc. 2017. V. 100. № 10. P. 4860. https://doi.org/10.1111/jace.15001
Bai Y., Zhang B., Du H. et al. // J. Am. Ceram. Soc. 2021. V. 104. № 4. P. 1841. https://doi.org/10.1111/jace.17610
Li N., Hu P., Xing P.F. et al. // IOP Conf. Ser. Mater. Sci. Eng. 2019. V. 479. P. 012067. https://doi.org/10.1088/1757-899X/479/1/012067
Bannykh D.A., Lozanov V.V., Baklanova N.I. // Inorg. Mater. 2021. V. 57. № 4. P. 343. https://doi.org/10.1134/S0020168521040026
Bannykh D., Utkin A., Baklanova N. // Int. J. Refract. Met. Hard Mater. 2019. V. 84. P. 105023. https://doi.org/10.1016/j.ijrmhm.2019.105023
Simonenko E.P., Simonenko N.P., Sevastyanov V.G. et al. // Russ. J. Inorg. Chem. 2018. V. 63. № 14. P. 1772. https://doi.org/10.1134/S003602361814005X
Liu Y., Cheng Y., Ma D. et al. // J. Eur. Ceram. Soc. 2022. V. 42. № 9. P. 3699. https://doi.org/10.1016/j.jeurceramsoc.2022.03.045
Shahedi Asl M., Sabahi Namini A., Delbari S.A. et al. // Mater. Chem. Phys. 2022. V. 275. P. 125322. https://doi.org/10.1016/j.matchemphys.2021.125322
Zhang D., Yu H., Wang A. et al. // Corros. Sci. 2021. V. 190. P. 109706. https://doi.org/10.1016/j.corsci.2021.109706
Popov O., Vleugels J., Zeynalov E. et al. // J. Eur. Ceram. Soc. 2020. V. 40. № 15. P. 5012. https://doi.org/10.1016/j.jeurceramsoc.2020.07.039
Nisar A., Bajpai S., Khan M.M. et al. // Ceram. Int. 2020. V. 46. № 13. P. 21689. https://doi.org/10.1016/j.ceramint.2020.05.276
Cao J., Wang M., Wang L. et al. // Int. J. Appl. Ceram. Technol. 2022. V. 19. № 4. P. 2285. https://doi.org/10.1111/ijac.14014
Nguyen V.-H., Delbari S.A., Shahedi Asl M. et al. // Ceram. Int. 2021. V. 47. № 9. P. 12459. https://doi.org/10.1016/j.ceramint.2021.01.103
Nguyen V.-H., Delbari S.A., Shahedi Asl M. et al. // Int. J. Refract. Met. Hard Mater. 2021. V. 95. P. 105457. https://doi.org/10.1016/j.ijrmhm.2020.105457
Monteverde F., Savino R., Fumo M.D.S. et al. // J. Eur. Ceram. Soc. 2010. V. 30. № 11. P. 2313. https://doi.org/10.1016/j.jeurceramsoc.2010.01.029
Fisenko A.I., Lemberg V. // Int. J. Thermophys. 2013. V. 34. № 3. P. 486. https://doi.org/10.1007/s10765-013-1429-8
Wang F., Cheng L., Xie Y. et al. // J. Alloys Compd. 2015. V. 625. P. 1. https://doi.org/10.1016/j.jallcom.2014.09.191
Li N., Xing P., Li C. et al. // Appl. Surf. Sci. 2017. V. 409. P. 1. https://doi.org/10.1016/j.apsusc.2017.02.266
Liu L., Yang L., Ma H. et al. // J. Asian Ceram. Soc. 2021. V. 9. № 4. P. 1506. https://doi.org/10.1080/21870764.2021.1999559
Meng S., Chen H., Hu J. et al. // Mater. Des. 2011. V. 32. № 1. P. 377. https://doi.org/10.1016/j.matdes.2010.06.007
Scatteia L., Borrelli R., Cosentino G. et al. // J. Spacecr. Rockets 2006. V. 43. № 5. P. 1004. https://doi.org/10.2514/1.21156
Scatteia L., Alfano D., Monteverde F. et al. // J. Am. Ceram. Soc. 2008. V. 91. № 5. P. 1461.
Balat-Pichelin M., Bêche E., Sciti D. et al. // Ceram. Int. 2014. V. 40. № 7. P. 9731. https://doi.org/10.1016/j.ceramint.2014.02.059
Mungiguerra S., Di Martino G.D., Cecere A. et al. // Int. J. Heat Mass Transf. 2020. V. 156. P. 119910. https://doi.org/10.1016/j.ijheatmasstransfer.2020.119910
Zhang Y., Sanvito S. // Appl. Surf. Sci. 2021. V. 566. P. 150622. https://doi.org/10.1016/j.apsusc.2021.150622
Marschall J., Chamberlain A., Crunkleton D. et al. // J. Spacecr. Rockets 2004. V. 41. № 4. P. 576. https://doi.org/10.2514/1.2879
Kolesnikov A.F., Lukomskii I.V., Sakharov V.I. et al. // Fluid Dyn. 2021. V. 56. № 6. P. 897. https://doi.org/10.1134/S0015462821060070
Kolesnikov A.F., Kuznetsov N.T., Murav’eva T.I. et al. // Fluid Dyn. 2022. V. 57. № 4. P. 513. https://doi.org/10.1134/S0015462822040061
Simonenko E.P., Simonenko N.P., Kolesnikov A.F. et al. // Vacuum. 2023.
Simonenko E.P., Simonenko N.P., Kolesnikov A.F. et al. // J. Eur. Ceram. Soc. 2022. V. 42. № 1. P. 30. https://doi.org/10.1016/j.jeurceramsoc.2021.09.020
Simonenko E.P., Simonenko N.P., Kolesnikov A.F. et al. // Russ. J. Inorg. Chem. 2021. V. 66. № 9. P. 1405. https://doi.org/10.1134/S003602362109014X
Лукомский И.В., Чаплыгин А.В., Колесников А.Ф. Устройство для измерения теплового потока к поверхности материала, нагретого в струе высокоэнтальпийного газа до высоких температур. Пат. RU 205572. 2021.
Afonina N.E., Gromov V.G., Sakharov V.I. // Proc. 5th Eur. Symp. Aerothermodyn. Spase Veh. 2004. P. 323.
Burdick C.L., Owen E.A. // J. Am. Chem. Soc. 1918. V. 40. № 12. P. 1749. https://doi.org/10.1021/ja02245a001
Holleck H. // J. Nucl. Mater. 1967. V. 21. № 1. P. 14.
Marschall J., Pejakovic D., Fahrenholtz W.G. et al. // J. Thermophys. Heat Transf. 2012. V. 26. № 4. P. 559. https://doi.org/10.2514/1.T3798
Whittle K.R., Lumpkin G.R., Ashbrook S.E. // J. Solid State Chem. 2006. V. 179. № 2. P. 512. https://doi.org/10.1016/j.jssc.2005.11.011
Shuvalov R.R., Burns P.C. // Acta Crystallogr. Sect. C Cryst. Struct. Commun. 2003. V. 59. № 6. P. I47. https://doi.org/10.1107/S0108270103009685
Simonenko E.P., Simonenko N.P., Lysenkov A.S. et al. // Russ. J. Inorg. Chem. 2020. V. 65. № 3. P. 446. https://doi.org/10.1134/S0036023620030146
Дополнительные материалы отсутствуют.
Инструменты
Журнал неорганической химии