Журнал неорганической химии, 2022, T. 67, № 12, стр. 1728-1736
Синтез наноразмерного Co3O4 и его применение для формирования миниатюрных планарных структур с помощью микроплоттерной печати
Т. Л. Симоненко a, *, Н. П. Симоненко a, Я. Р. Топалова b, Ф. Ю. Горобцов a, Е. П. Симоненко a, Н. Т. Кузнецов a
a Институт общей и неорганической химии им. Н.С. Курнакова РАН
119991 Москва, Ленинский пр-т, 31, Россия
b Национальный исследовательский университет “Высшая школа экономики”
109028 Москва, ул. Мясницкая, 21, Россия
* E-mail: egorova.offver@gmail.com
Поступила в редакцию 14.07.2022
После доработки 04.08.2022
Принята к публикации 09.08.2022
- EDN: QOGAHA
- DOI: 10.31857/S0044457X22601298
Аннотация
Изучен процесс формирования нанокристаллического Co3O4 с помощью метода химического осаждения. С помощью синхронного термического анализа, ИК-спектроскопии и рентгенофазового анализа проведена аттестация полученного полупродукта, а также исследован процесс его термического разложения с образованием целевого продукта, представляющего собой высокодисперсный порошок (средний размер области когерентного рассеяния 17 ± 2 нм), не содержащий примесей. Предложен подход к микроплоттерной печати миниатюрных планарных наноструктур Co3O4 различной геометрии на поверхности кремневых подложек с применением функциональных чернил, изготовленных на основе полученного нанопорошка. Исследованы особенности микроструктуры сформированных тонкопленочных структур. Показано, что при этом практически отсутствует эффект “кофейного пятна”. В рамках исследования локальных электрофизических характеристик полученных образцов построены карты распределения поверхностного потенциала и градиента емкости, а также рассчитано значение работы выхода электрона с их поверхности. В результате исследования показана возможность использования разработанной технологии для изготовления электродных структур Co3O4 для суперконденсаторов планарного типа.
ВВЕДЕНИЕ
Оксид кобальта(II,III) представляет собой классический р-полупроводник с шириной запрещенной зоны порядка 1.6–2.2 эВ, который благодаря высокой окислительно-восстановительной активности и удельной емкости, низкой токсичности и коммерческой доступности является широко востребованным материалом в области катализа (гетерогенные катализаторы) [1, 2], медицины (противогрибковые и антибактериальные препараты) [3], оптики (“умные” окна) [4], электроники [5], сенсорики (рецепторный материал для резистивных газовых сенсоров [6] и электрохимических сенсоров [7]) и альтернативной энергетики (суперконденсаторы, литий-ионные аккумуляторы) [8, 9]. На сегодняшний день в рамках общей тенденции к миниатюризации устройств для описанных приложений требуется создание планарных структур Co3O4. Так, описано значительное количество методов и подходов к получению покрытий из данного материала различной морфологии и толщины, таких как: атомно-слоевое осаждение [10, 11], спрей-пиролиз [12–14], гидротермальный синтез [15–17], а также методы погружения и вращения подложки (так называемые методы dip- и spin-coating), комбинированные с золь-гель технологией [18–21]. Кроме того, активно используется такой технологический прием, как трафаретная печать (screen printing) [22–24]. Существенно повысить адресность нанесения, а также разрешение и воспроизводимость при автоматизированном формировании планарных структур, в том числе в ходе создания устройств альтернативной энергетики, становится возможным благодаря активному развитию современных аддитивных технологий: струйной [25–27], аэрозольной [28, 29], микроплоттерной [30–32], микроэкструзионной [33–35] и перьевой плоттерной печати [36–38]. Функциональные свойства напечатанных миниатюрных структур на основе Co3O4 будут во многом определяться параметрами микроструктуры дисперсной фазы (в первую очередь дисперсностью и формой частиц) в составе коллоидных растворов, используемых в качестве функциональных чернил для печати. В свою очередь микроструктура порошков, применяемых для создания чернил, во многом зависит от метода синтеза оксида соответствующего состава [39]. Среди наиболее распространенных подходов к получению нанокристаллического оксида кобальта(II,III) в виде порошков можно выделить гидротермальный синтез [40–42], золь-гель технологию [43, 44], темплатный синтез [45, 46], электроспиннинг [47, 48], а также химическое осаждение гидроксидов [49], оксалатов [50] или карбонатов [51]. При этом нужно отметить, что метод химического осаждения является удобным и масштабируемым, позволяющим получать материалы требуемого состава с необходимой дисперсностью и микроструктурой благодаря возможности контроля широкого спектра параметров синтеза (типа и концентрации реагентов, в том числе осадителей, величины рН, скорости и температуры осаждения) [52–54].
В настоящей работе изучен процесс микроплоттерной печати планарных наноструктур Co3O4. Исследован процесс синтеза иерархически организованного оксида кобальта(II,III) методом химического осаждения гидроксидов металлов в виде нанопорошка, подходящего по своим характеристикам для использования в качестве дисперсной фазы при изготовлении соответствующих функциональных чернилах. Кроме того, изучено влияние параметров синтеза и печати на микроструктурные особенности напечатанных миниатюрных структур.
ЭКСПЕРИМЕНТАЛЬНАЯ ЧАСТЬ
Синтез оксида кобальта(II,III) проводили методом химического осаждения. К разбавленному (0.05 моль/л) водному раствору нитрата кобальта при непрерывном перемешивании по каплям добавляли 5%-ный водный раствор гидрата аммиака со скоростью 1 мл/мин до достижения рН 9.2 (рис. 1, рН-метр Hanna HI 98127 pHep 4) с целью обеспечения полноты осаждения гидроксида кобальта. Сформировавшуюся в процессе синтеза дисперсную фазу отделяли от маточного раствора и промывали дистиллированной водой путем циклического центрифугирования. Далее проводили сушку (100°С, 3 ч) с целью удаления остаточного растворителя и дополнительную термическую обработку для кристаллизации целевого оксида Co3O4.
Рис. 1.
Зависимость уровня pH реакционной системы от объема добавляемого к реакционной системе водного раствора гидрата аммиака.
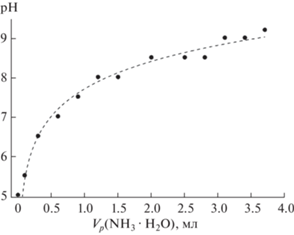
Синхронный (ТГА/ДСК) термический анализ проводили с помощью термоанализатора SDT Q-600 (TA Instruments), контролируемый нагрев осуществляли в Al2O3-микротиглях в диапазоне температур 25–1000°С со скоростью 10 град/мин в токе воздуха, скорость потока газа составляла 250 мл/мин. Масса навески исследуемого порошка – 10.504 мг. На основании результатов термического анализа определяли оптимальный режим дополнительной термообработки (400°С, 1 ч) для разложения гидроксида кобальта при сохранении наноразмерного состояния оксида кобальта(II,III).
Порошки после сушки и дополнительной термообработки анализировали с помощью ИК-спектроскопии в интервале волновых чисел 350–4000 см–1 (время накопления сигнала – 15 с, разрешение – 1 см–1) с помощью ИК-Фурье-спектрометра ИнфраЛЮМ ФТ-08. Перед записью спектров пропускания готовили соответствующие суспензии в вазелиновом масле, которые в виде пленки помещали между стеклами из бромида калия.
Полученный оксидный нанопорошок применяли для получения стабильной дисперсной системы, подходящей по реологическим характеристикам для применения в качестве функциональных чернил при формировании миниатюрных планарных наноструктур Co3O4 на поверхности полированной кремниевой подложки (латеральные размеры 10 × 10 мм) с помощью микроплоттерной печати. Порошок массой 0.015 г помещали в 1.585 г этиленгликоля, после чего систему обрабатывали в ультразвуковой ванне в течение 3 ч до образования стабильного коллоидного раствора. В качестве дозатора применяли стеклянный капилляр с овальным профилем торцевого отверстия размером 20 × 70 мкм. Печать отдельных миниатюрных планарных оксидных наноструктур и их организованных массивов на поверхности Si-подложки проводили с использованием автоматизированной трехкоординатной системы позиционирования путем последовательного перемещения капилляра со скоростью 100 мм/мин в соответствии с заданной программой при касании подложки мениском чернил. Далее подложку с нанесенными структурами подвергали термообработке при 300°С (1 ч) с целью удаления растворителя.
Рентгенофазовый анализ (РФА) полученных порошков проводили с помощью дифрактометра Bruker D8 Advance (CuKα-излучение 1.5418 Å, Ni-фильтр, E = 40 кэВ, I = 40 мА, диапазон 2θ – 10°–80°, разрешение – 0.02°, время накопления сигнала в точке 0.3 с).
Микроструктуру полученных образцов исследовали методами растровой (РЭМ; трехлучевая рабочая станция Carl Zeiss NVision 40, оснащенная энергодисперсионным микрозондовым анализатором Oxford Instruments X-MAX 80) и просвечивающей электронной микроскопии (ПЭМ; JEOL JEM-1011 с цифровой фотокамерой ORIUS SC1000W).
Полученные планарные нанострукуры оксида кобальта на поверхности кремниевых подложек исследовали методом атомно-силовой микроскопии. В результате проведенных измерений получили данные о микроструктуре образцов и их локальных электрофизических свойствах, таких как работа выхода электрона с поверхности материала, распределение носителей заряда, градиента емкости конденсатора острие зонда-микрообласть образца. Указанные исследования выполняли на сканирующем зондовом микроскопе Solver Pro-M (производство NT-MDT) с использованием зондов Etalon HA-HR с проводящим покрытием на основе W2C (резонансная частота ~367 кГц, радиус скругления <35 нм) в режимах полуконтактной АСМ, кельвин-зондовой сканирующей микроскопии (КЗСМ) и сканирующей емкостной микроскопии (СЕМ) на воздухе.
РЕЗУЛЬТАТЫ И ОБСУЖДЕНИЕ
Термическое поведение полученного методом химического осаждения полупродукта (после его сушки при 100°С) изучали с применением синхронного термического анализа (рис. 2). Как видно из термограмм, в интервале 25–1000°С для порошка имеет место многоступенчатая потеря массы, на разных этапах сопровождающаяся тепловыми эффектами разного знака. Так, в диапазоне 25–150°С наблюдается уменьшение массы на 1%, связанное с удалением остаточного растворителя и сорбированных атмосферных газов. При дальнейшем нагревании (150–200°С) происходит более резкое снижение массы (Δm = 8%), сопровождающееся экзотермическим эффектом с максимумом при 180°С, вероятно, относящимся к окислению катионов кобальта(II) с одновременным разложением гидроксида. В интервале 200–280°С наблюдается ступень с более низкой скоростью уменьшения массы (3%), а соответствующий эндотермический эффект с минимумом при 250°С свидетельствует о продолжении процесса разложения гидроксида кобальта. Масса образца стабилизируется при температуре ~400°С (Δm в диапазоне 280–400°С составила ~2.5%) с образованием устойчивой весовой формы вещества (предположительно Co3O4). В узкой высокотемпературной области (900–930°С) происходит характерное для оксида кобальта(II,III) очередное резкое уменьшение массы (на 6%), относящееся к разложению данного вещества и образованию оксида кобальта(II), что проявляется соответствующем эндотермическим тепловым эффектом с минимумом при 919°С. Таким образом, общая потеря массы при нагревании порошка во всем исследуемом температурном диапазоне составила 20.85%. С учетом полученных результатов выбран оптимальный режим (400°С, 1 ч) дополнительной термообработки полупродукта с целью его полного разложения и формирования высокодисперсного оксидного порошка.
Рис. 2.
Кривые ТГА (черная) и ДСК (красная) гидроксида кобальта, полученного в результате химического осаждения и последующей сушки при 100°С (3 ч).
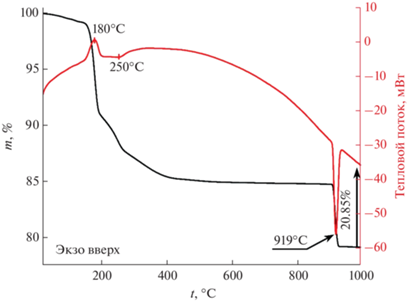
Полупродукт и полученный в результате дополнительной термообработки оксидный порошок изучали с помощью ИК-спектроскопии (рис. 3а). Как видно из спектра пропускания полупродукта, присутствует узкая полоса поглощения с максимумом ~3700 см–1, относящаяся к колебаниям OH-групп и характерная для гидроксида кобальта. Кроме того, полученные результаты свидетельствуют об отсутствии в его составе побочных продуктов (в частности, нитрата аммония). В результате термообработки при 400°С данная полоса поглощения полностью исчезает, что свидетельствует о завершении процесса разложения гидроксида. При этом наблюдается появление двух характерных для Co3O4 полос поглощения с максимумами ~560 и 700 см–1, относящихся к колебаниям химических связей Co–O и O–Со–O соответственно.
Рис. 3.
Результаты ИК-спектроскопии (а) и рентгенофазового анализа (б) гидроксида кобальта и полученного в результате его дополнительной термообработки при 400°С оксида Co3O4.
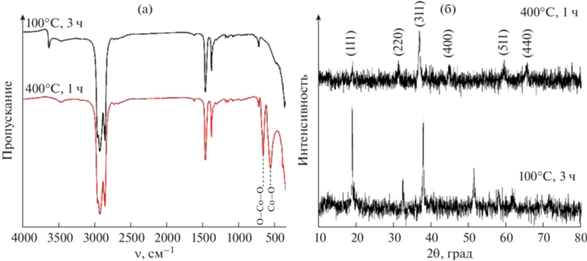
Кристаллическую структуру полупродукта и ее трансформация в ходе дополнительной термообработке изучали с использованием РФА. Из результатов анализа полученных рентгенограмм (рис. 3б) следует, что путем химического осаждения в выбранных условиях формируется β-Co(OH)2. Термообработка порошка при 400°С приводит к полному разложению гидроксида кобальта, что проявляется в исчезновении соответствующих рефлексов, и формированию оксида кобальта(II,III) со структурой типа шпинели, не содержащего каких-либо кристаллических примесей. При этом средний размер области когерентного рассеяния для данного порошка составил 17 ± 2 нм, что подтверждает образование нанокристаллического порошка Co3O4. Таким образом, полученные результаты РФА хорошо согласуются с данными ИК-спектроскопии.
Морфологию полученного нанопорошка Co3O4 изучали с помощью РЭМ (рис. 4а–4г). Видно, что порошок имеет несколько уровней организации. Так, первичные частицы размером до 50 нм образуют нанолисты шириной ~1.5–2 мкм, которые самоорганизуются в иерархические слоистые агломераты диаметром ~10 мкм и толщиной ~1.5–3 мкм. Таким образом, полученный методом химического осаждения порошок оксида кобальта(II,III) является наноразмерным и имеет однородную микроструктуру, а сформированные из первичных частиц иерархически организованные агломераты характеризуются близкими размерами и единым характером микроструктуры. Результаты рентгеноспектрального элементного микроанализа свидетельствуют об отсутствии в составе материала каких-либо примесей.
По данным ПЭМ (рис. 4д, 4е), сформированные оксидные агломераты во время ультразвуковой обработки соответствующей дисперсии частично разрушаются с образованием первичных частиц Co3O4 размером 23 ± 2 нм. Как видно, данная величина является близкой к среднему размеру области когерентного рассеяния полученного нанопорошка, что, вероятно, свидетельствует о формировании монокристаллических оксидных частиц, покрытых рентгеноаморфной оксидной оболочкой. Таким образом, использованная в рамках исследования методика позволяет синтезировать наноразмерный оксид кобальта(II,III), представляющий собой многоуровневую иерархически организованную систему из оксидных наночастиц.
Полученный оксидный нанопорошок далее применяли для получения стабильной дисперсной системы, подходящей по реологическим характеристикам для применения в качестве функциональных чернил при формировании миниатюрных планарных наноструктур методом микроплоттерной печати на полированной Si-подложке. Полученный коллоидный раствор помещали в стеклянный капилляр, после чего на поверхность подложки путем автоматического прикосновения мениска жидкости при различных режимах дискретно наносили отдельные капли чернил различного размера. Помимо отдельных миниатюрных структур аналогично были сформированы их массивы в виде квадратов и чередующихся рядов, внешний вид которых изучали с помощью оптической микроскопии (врезки на рис. 5). Как видно из микрофотографий, во время микроплоттерной печати воспроизводится круглая форма и латеральные размеры (диаметр составляет ~200 мкм) получаемых структур. Установлено, что в зависимости от условий печати (положение мениска чернил по вертикали во время касания поверхности подложки) диаметр отдельных пикселей может варьировать от 100 до 300 мкм. Геометрические параметры и микроструктуру оксидных покрытий более детально изучали с помощью РЭМ (рис. 5). Так, полученные результаты подтверждают воспроизводимость микроструктурных характеристик сформированных миниатюрных планарных структур и отсутствие эффекта “кофейного пятна”. Определено, что с использованием соответствующих функциональных чернил образуются пористые тонкопленочные структуры, состоящие из частиц, средний размер которых аналогичен параметрам первичных частиц используемого порошка Co3O4.
Рис. 5.
РЭМ-изображения полученных миниатюрных планарных наноструктур Co3O4 (на врезках представлены оптические микрофотографии аналогичных участков).
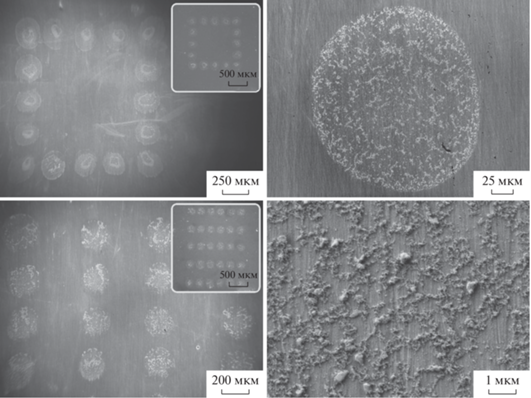
Анализ микроструктурных и локальных электрофизических свойств сформированных миниатюрных планарных наноструктур Co3O4 проводили с использованием различных методик атомно-силовой микроскопии (рис. 6). Показано, что отдельный напечатанный элемент имеет островковую структуру и состоит из агломератов размером от 300 нм (рис. 6а, 6б). При этом пленка является тонкой, так как для крупных агломератов (длиной >1 мкм) толщина составляет 100–200 нм, а для субмикронных –15–40 нм. Частицы Co3O4, образующие агломераты, являются наноразмерными, имеют чуть вытянутую округлую форму и диаметр в диапазоне 20–40 нм, что хорошо согласуется с ранее приведенными результатами электронной микроскопии. Толщина небольших агломератов сравнима с размерами отдельных наночастиц, что говорит о том, что они в основном представляют собой монослои оксидных частиц. Сканирование различных участков пленки показывает, что к ее краю наблюдается плавное увеличение пористости.
Рис. 6.
Результаты АСМ миниатюрных планарных наноструктур Co3O4: топография (а, б), а также карты распределения поверхностного потенциала (в) и емкости (г).
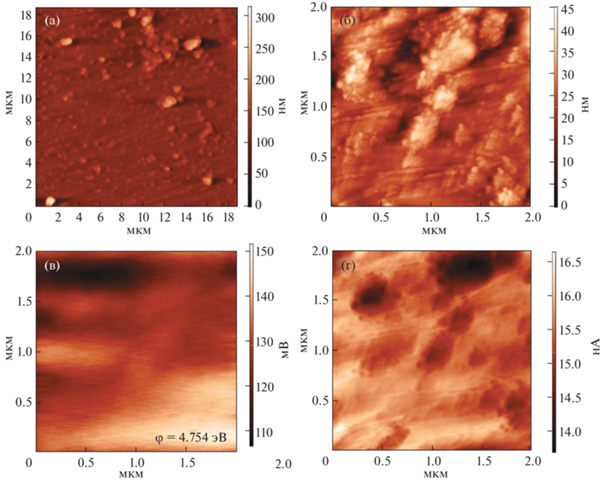
В ходе изучения поверхности полученных миниатюрных планарных наноструктур методом АСМ помимо топографических изображений составляли карты распределения поверхностного потенциала (рис. 6в, по данным КЗСМ) и градиента емкости (рис. 6г, по данным СЕМ). Поверхностный потенциал на исследованном участке покрытия колеблется в довольно узком интервале значений (контактная разность потенциалов между зондом и образцом изменяется в диапазоне 107–157 мВ), однако четко наблюдается контраст потенциала. В среднем значение контактной разности потенциалов между зондом и оксидной пленкой составляет 127 мВ на участках образца, покрытых агломератами Co3O4, однако вокруг них встречаются как близкие к самим агломератам значения потенциалов, так и значительно бóльшие и меньшие. Это может говорить о том, что в силу островковой структуры пленки, носители заряда недостаточно равномерно распределены по ее поверхности, и встречаются флуктуации в их плотности. Яркого контраста между поверхностью кремниевой подложки и агломератами Co3O4 на картах поверхностного потенциала не наблюдается, что может объясняться близкими значениями работы выхода электрона с поверхности материалов. Однако, карта распределения градиента емкости демонстрирует более яркий контраст – более темные области, где градиент принимает меньшие значения, явно относятся к частицам оксида кобальта, а более светлые – к кремниевой подложке. При этом изменения в высоте на соответствующем топографическом изображении невелики и сравнимы с размерами наночастиц, поэтому можно предположить, что вклад особенностей рельефа в изображение, полученное методом СЕМ, минимален. Более светлые области соответствуют большему градиенту емкости, а значит, на непокрытой поверхности подложки градиент и, вероятно, величина самой емкости выше. Это объясняется бóльшей электропроводностью кремния по сравнению с частицами Co3O4. По результатам КЗСМ было рассчитано значение работы выхода электрона с поверхности сформированных методом микроплоттерной печати миниатюрных планарных наноструктур Co3O4, составившее 4.754 эВ.
ЗАКЛЮЧЕНИЕ
В ходе проведенного исследования показаны перспективные возможности технологии микроплоттерной печати при формировании планарных миниатюрных наноструктур Co3O4 на поверхности кремневых подложек. Изучен процесс синтеза методом химического осаждения иерархически организованного нанокристаллического (средний размер области когерентного рассеяния составил 17 ± 2 нм, средний размер частиц – 23 ± ± 2 нм) оксида аналогичного состава, используемого в качестве дисперсной фазы при изготовлении функциональных чернил с оптимальными реологическими свойствами для решения описанной задачи. Исследован процесс трансформации промежуточного продукта синтеза (β-Co(OH)2) с образованием целевого продукта, который имеет кубическую кристаллическую структуру типа шпинели (Fd3m), а также не содержит примесных включений. Дополнительно исследованы особенности микроструктуры, а также локальные электрофизические свойства напечатанных миниатюрных наноструктур. Показано, что отдельный напечатанный элемент в составе паттерна имеет островковую структуру, состоящую из агломератов размером 100–300 нм, толщина которых не превышает 200 нм. В ходе анализа поверхности полученных структур методом СЭМ установлено, что наблюдаемый контраст распределения потенциала по поверхности может свидетельствовать о флуктуациях концентрации носителей заряда на границах и основных участках единичных элементов напечатанных фигур.
По результатам проведенного исследования можно предположить, что предложенный подход синтеза Co3O4 позволяет получать нанопорошки, которые могут эффективно использоваться при создании функциональных чернил для микроплоттерной печати соответствующих полупроводниковых миниатюрных наноструктур, которые в дальнейшем могут быть использованы в качестве компонентов планарных суперконденсаторов.
Список литературы
Wang Z., Meng C., Zhang W. et al. // Sci. Total Environ. 2022. V. 814. P. 152698. https://doi.org/10.1016/j.scitotenv.2021.152698
Cai H., Li J., Yin H. et al. // Water Environ. Res. 2020. P. 1324. https://doi.org/10.1002/wer.1324
Waris A., Din M., Ali A. et al. // Open Life Sci. 2021. V. 16. № 1. P. 14. https://doi.org/10.1515/biol-2021-0003
Chaudhary A., Pathak D.K., Ghosh T. et al. // ACS Appl. Electron. Mater. 2020. V. 2. № 6. P. 1768. https://doi.org/10.1021/acsaelm.0c00342
Wang P., Jin C., Zheng D. et al. // ACS Appl. Mater. Interfaces. 2021. V. 13. № 22. P. 26621. https://doi.org/10.1021/acsami.1c05748
Xu J.M., Cheng J.P. // J. Alloys Compd. 2016. V. 686. P. 753. https://doi.org/10.1016/j.jallcom.2016.06.086
Zhe T., Li M., Li F. et al. // Food Chem. 2022. V. 367. P. 130666. https://doi.org/10.1016/j.foodchem.2021.130666
Deng X., Zhang H., Zhang J. et al. // RSC Adv. 2020. V. 10. № 71. P. 43825. https://doi.org/10.1039/D0RA08319D
Shi Y., Pan X., Li B. et al. // Chem. Eng. J. 2018. V. 343. P. 427. https://doi.org/10.1016/j.cej.2018.03.024
Kalam K., Seemen H., Mikkor M. et al. // Thin Solid Films. 2019. V. 669. P. 294. https://doi.org/10.1016/j.tsf.2018.11.008
Holden K.E.K., Conley J.F. // J. Vac. Sci. Technol. A. 2019. V. 37. № 2. P. 020903. https://doi.org/10.1116/1.5064469
Yin X., Wang Z., Wang J. et al. // Mater. Lett. 2014. V. 120. P. 73. https://doi.org/10.1016/j.matlet.2014.01.011
Ambare R.C., Bharadwaj S.R., Lokhande B.J. // Appl. Surf. Sci. 2015. V. 349. P. 887. https://doi.org/10.1016/j.apsusc.2015.04.175
Yadav A.A., Chavan U.J. // Electrochim. Acta 2017. V. 232. P. 370. https://doi.org/10.1016/j.electacta.2017.02.157
Hao J., Peng S., Li H. et al. // J. Mater. Chem. A. 2018. V. 6. № 33. P. 16094. https://doi.org/10.1039/c8ta06349d
Shen S.F., Xu M.L., Lin D.B. et al. // Appl. Surf. Sci. 2017. V. 396. P. 327. https://doi.org/10.1016/j.apsusc.2016.10.147
Simonenko T.L., Bocharova V.A., Gorobtsov P.Y. et al. // Russ. J. Inorg. Chem. 2020. V. 65. № 9. P. 1304. https://doi.org/10.1134/S0036023620090181
Abdelhak L., Amar B., Bedhiaf B. et al. // High Temp. Mater. Process. 2019. V. 38. № 2019. P. 237. https://doi.org/10.1515/htmp-2017-0185
Lakehal A., Benrabah B., Bouaza A. et al. // Chinese J. Phys. 2018. V. 56. № 5. P. 1845. https://doi.org/10.1016/j.cjph.2018.08.012
Chougule M.A., Pawar S.G., Godse P.R. et al. // J. Mater. Sci. Mater. Electron. 2012. V. 23. № 3. P. 772. https://doi.org/10.1007/s10854-011-0491-x
Lagerqvist U. // Adv. Mater. 2014. V. 3. № 5. P. 52. https://doi.org/10.11648/j.am.20140305.14
Zhang M.M., Jiang G.S. // Chinese J. Chem. Phys. 2007. V. 20. № 3. P. 315. https://doi.org/10.1088/1674-0068/20/03/315-318
Choi U.S., Sakai G., Shimanoe K. et al. // Sensors Actuators, B Chem. 2005. V. 107. P. 397. https://doi.org/10.1016/j.snb.2004.10.033
Bashir A., Shukla S., Lew J.H. et al. // Nanoscale. 2018. V. 10. № 5. P. 2341. https://doi.org/10.1039/c7nr08289d
Simonenko E.P., Mokrushin A.S., Simonenko N.P. et al. // Thin Solid Films. 2019. V. 670. P. 46. https://doi.org/10.1016/j.tsf.2018.12.004
Yadav B.S., Dey S.R., Dhage S.R. // Sol. Energy. 2019. V. 179. P. 363. https://doi.org/10.1016/j.solener.2019.01.003
Newhouse P.F., Parkinson B.A. // J. Mater. Chem. A. 2015. V. 3. № 11. P. 5901. https://doi.org/10.1039/c4ta05671j
Jing Q., Choi Y.S., Smith M. et al. // Adv. Mater. Technol. 2019. V. 4. № 7. P. 1. https://doi.org/10.1002/admt.201900048
Volkov I.A., Simonenko N.P., Efimov A.A. et al. // Appl. Sci. 2021. V. 11. № 2. P. 526. https://doi.org/10.3390/app11020526
Sobolewski P., Goszczynska A., Aleksandrzak M. et al. // Beilstein J. Nanotechnol. 2017. V. 8. № 1. P. 1508. https://doi.org/10.3762/bjnano.8.151
Fedorov F.S., Simonenko N.P., Trouillet V. et al. // ACS Appl. Mater. Interfaces. 2020. V. 12. № 50. P. 56135. https://doi.org/10.1021/acsami.0c14055
Simonenko T.L., Simonenko N.P., Gorobtsov P.Y. et al. // J. Colloid Interface Sci. 2021. V. 588. P. 209. https://doi.org/10.1016/j.jcis.2020.12.052
Simonenko T.L., Simonenko N.P., Gorobtsov P.Y. et al. // Ceram. Int. 2022. V. 48. № 15. P. 22401. https://doi.org/10.1016/j.ceramint.2022.04.252
Mokrushin A.S., Simonenko T.L., Simonenko N.P. et al. // Appl. Surf. Sci. 2022. V. 578. P. 151984. https://doi.org/10.1016/j.apsusc.2021.151984
Simonenko N.P., Kadyrov N.S., Simonenko T.L. et al. // Russ. J. Inorg. Chem. 2021. V. 66. № 9. P. 1283. https://doi.org/10.1134/S0036023621090126
Soum V., Cheong H., Kim K. et al. // ACS Omega 2018. V. 3. № 12. P. 16866. https://doi.org/10.1021/acsomega.8b02592
Simonenko T.L., Simonenko N.P., Gorobtsov P.Y. et al. // J. Alloys Compd. 2020. V. 832. P. 154957. https://doi.org/10.1016/j.jallcom.2020.154957
Simonenko T.L., Simonenko N.P., Gorobtsov P.Y. et al. // Russ. J. Inorg. Chem. 2021. V. 66. № 9. P. 1416. https://doi.org/10.1134/S0036023621090138
Wang X., Hu A., Meng C. et al. // Molecules. 2020. V. 25. № 2. https://doi.org/10.3390/molecules25020269
Liu F., Zhang B., Su H. et al. // Nanotechnolog.y 2016. V. 27. № 35. P. 355603. https://doi.org/10.1088/0957-4484/27/35/355603
Wang X., Xia H., Wang X. et al. // J. Alloys Compd. 2016. V. 686. P. 969. https://doi.org/10.1016/j.jallcom.2016.06.156
Venkatachalam V., Alsalme A., Alswieleh A. et al. // J. Mater. Sci. Mater. Electron. 2018. V. 29. № 7. P. 6059. https://doi.org/10.1007/s10854-018-8580-8
Peterson G.R., Hung-Low F., Gumeci C. et al. // ACS Appl. Mater. Interfaces 2014. V. 6. № 3. P. 1796. https://doi.org/10.1021/am4047969
Lakehal A., Bedhiaf B., Bouaza A. et al. // Mater. Res. 2018. V. 21. № 3. https://doi.org/10.1590/1980-5373-mr-2017-0545
Zhu Z., Han C., Li T.-T. et al. // CrystEngComm. 2018. V. 20. № 27. P. 3812. https://doi.org/10.1039/C8CE00613J
Xiao Z., Fan L., Xu B. et al. // ACS Appl. Mater. Interfaces. 2017. V. 9. № 48. P. 41827. https://doi.org/10.1021/acsami.7b10309
Guan H., Shao C., Wen S. et al. // Mater. Chem. Phys. 2003. V. 82. № 3. P. 1002. https://doi.org/10.1016/j.matchemphys.2003.09.003
Hu D., Wang R., Du P. et al. // Ceram. Int. 2022. V. 48. № 5. P. 6549. https://doi.org/10.1016/j.ceramint.2021.11.202
Lu S., Jing X., Liu J. et al. // J. Solid State Chem. 2013. V. 197. P. 345. https://doi.org/10.1016/j.jssc.2012.09.020
Anuradha C.T., Raji P. // Int. J. Nanosci. 2019. V. 18. № 5. P. 1950002. https://doi.org/10.1142/S0219581X19500029
Zhang W., Lassen K., Descorme C. et al. // Appl. Catal. B Environ. 2021. V. 282. P. 119566. https://doi.org/10.1016/j.apcatb.2020.119566
Simonenko T.L., Kalinina M.V., Simonenko N.P. et al. // Glas. Phys. Chem. 2018. V. 44. № 4. P. 314. https://doi.org/10.1134/S1087659618040144
Kalinina M.V., Morozova L.V., Egorova T.L. et al. // Glas. Phys. Chem. 2016. V. 42. № 5. P. 505. https://doi.org/10.1134/S1087659616050060
Egorova T.L., Kalinina M.V., Simonenko E.P. et al. // Russ. J. Inorg. Chem. 2017. V. 62. № 10. P. 1275. https://doi.org/10.1134/S0036023617100072
Дополнительные материалы отсутствуют.
Инструменты
Журнал неорганической химии