Журнал неорганической химии, 2022, T. 67, № 10, стр. 1498-1504
Формуемость, фазовый состав и микроструктура материалов на основе TiC–(5–50 мас. %) NiCr, полученных в условиях свободного СВС-сжатия
М. С. Антипов a, *, П. М. Бажин a, А. П. Чижиков a, А. С. Константинов a, А. М. Столин a, Н. Ю. Хоменко a
a Институт структурной макрокинетики и проблем материаловедения им. А.Г. Мержанова РАН
142432 Московская обл., Черноголовка, ул. Академика Осипьяна, 8, Россия
* E-mail: mora1997@mail.ru
Поступила в редакцию 23.03.2022
После доработки 31.03.2022
Принята к публикации 04.04.2022
- EDN: DKLYWI
- DOI: 10.31857/S0044457X22100361
Аннотация
Методом свободного СВС-сжатия, реализуемого в условиях, сочетающих процессы горения и высокотемпературного сдвигового деформирования, экспериментально исследовано влияние времени задержки перед приложением давления на формуемость материала на основе TiC–(5–50 мас. %) NiCr, его фазовый состав, размер элементарной кристаллической ячейки и микроструктуру. Показано, что с увеличением относительной плотности исходной заготовки температура горения вначале повышается, а затем резко снижается. Определен механизм формования изучаемых материалов в зависимости от количественного содержания нихрома в смеси. Установлено, что 20–40 мас. % нихрома – это оптимальное содержание в смеси, соответствующее максимальной степени деформации материала. На основе проведенных исследований установлен химический маршрут при синтезе исходных реагентов титана, сажи и нихрома в условиях свободного СВС-сжатия. Установлено, что синтезированный материал состоит из частиц TiC, расположенных в матрице из Cr1.12Ni2.88 и Cr2Ni3. При содержании в смеси >30 мас. % нихрома наблюдается небольшое количество непрореагировавшего титана, которое можно регулировать условиями синтеза.
ВВЕДЕНИЕ
Материалы на основе TiC–NiCr [1, 2] обладают повышенными физико-механическими свойствами (твердость, микротвердость, прочность на сжатие и изгиб, ударная вязкость и др.) по сравнению с аналогичными сплавами на безвольфрамовой основе [3, 4]. Металлокерамические материалы на основе TiC–NiCr применяются в виде защитных покрытий [5–7], в машиностроении, авиа- и судостроении для изготовления деталей и узлов, работающих в зонах повышенного износа, а также в медицине для изготовления имплантатов [8].
Для получения изделий из металлокерамических материалов наиболее известными методами порошковой металлургии являются литье [9] и высокотемпературное спекание [10–12]. К энергоэффективным методам получения металлокерамических материалов на основе TiC–NiCr можно отнести метод самораспространяющегося высокотемпературного синтеза (СВС) [13–17], который заключается в проведении экзотермической реакций в режиме послойного распространения волны горения с образованием продуктов горения в виде соединений. Метод СВС позволяет получать порошки и спеки, которые необходимо диспергировать и в дальнейшем длительное время консолидировать при высоких температурах. Для получения компактных материалов и изделий с минимальной пористостью перспективными методами являются свободное СВС-сжатие [18–22] и СВС-экструзия [23–26], сочетающие процессы горения и высокотемпературного сдвигового деформирования. Формуемость продуктов синтеза определяется комплексом реологических, теплофизических и физико-механических свойств [27, 28]. Для определения степени деформации, при которой изучаемые материалы обладают способностью к формованию, предложен метод свободного СВС-сжатия. Результаты, полученные в ходе свободного СВС-сжатия, способствуют решению проблем получения изделий методом СВС в условиях высокотемпературного сдвигового деформирования.
Цель настоящей работы – изучение влияния времени задержки перед приложением внешнего давления на формуемость, фазовый состав и микроструктуру металлокерамических материалов на основе TiC–(5–50 мас. %) NiCr, полученных в условиях свободного СВС-сжатия.
ЭКСПЕРИМЕНТАЛЬНАЯ ЧАСТЬ
В качестве исходных реагентов использовали коммерческие порошки Ti (60 мкм, 99.1%), C (1 мкм, 99.1%) и NiCr (70 мкм, 99.9%) с учетом того, что после синтеза образуется 50–95 мас. % TiC с 5–50 мас. % NiCr (табл. 1).
Таблица 1.
Содержание реагентов и параметры исходной заготовки
Расчетный состав | Содержание, мас. % | Параметр исходной заготовки | ||||
---|---|---|---|---|---|---|
Ti | C | NiCr | m, г | h, мм | d, мм | |
TiC–5 мас. % NiCr | 76 | 19 | 5 | 16.45 | 15 | 25 |
TiC–10 мас. % NiCr | 72 | 18 | 10 | 16.62 | 15 | 25 |
TiC–20 мас. % NiCr | 64 | 16 | 20 | 16.82 | 15 | 25 |
TiC–30 мас. % NiCr | 56 | 14 | 30 | 21.50 | 15 | 25 |
Порошки предварительно перемешивали, просушивали, из них были спрессованы заготовки цилиндрической формы высотой 15 мм и диаметром 25 мм. В зависимости от массового соотношения реагентов цилиндрические заготовки имели относительную плотность 0.55–0.67.
Изучены температуры и скорости горения исходных заготовок в зависимости от массового содержания NiCr в исходной смеси. Схема измерения температуры и скорости горения представлена на рис. 1.
Рис. 1.
Схема измерения температуры и скорости горения: 1 – исходная заготовка, 2 – ЭВМ, 3 – отверстие для термопар, 4 – инициирующее устройство, 5 – термопары ВР5-ВР20.
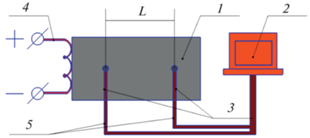
Расчет скорости горения исходной заготовки проводили по формуле А.Г. Мержанова (1) [29]:
где L – расстояние между термопарами, мм; ∆L – величина деформации заготовки после СВС; ${{{{\tau }}}_{1}}$ и ${{{{\tau }}}_{2}}$ – время регистрации максимальной температуры первой и второй термопары.Исследование формуемости материалов проводили на основе метода свободного СВС-сжатия. Давление плунжера пресса составляло 5 МПа, временной интервал задержки перед приложением давления – 0, 1 и 2 с. Сущность проведения СВС-сжатия заключается в следующем: в верхней части исходной заготовки помещали вольфрамовую спираль, на которую подавали электрический ток, в результате инициировался послойный процесс горения в режиме СВС (рис. 2). После того, как волна горения доходила до нижней части образца, отсчитывали время задержки с последующим приложением давления плунжера пресса.
В качестве основного критерия оценки формуемости выбирали степень деформации синтезированного материала, которую определяли по формуле (2) [30]:
где ψ – степень деформации синтезированного материала, Sн – площадь поперечного сечения исходной заготовки, мм2, Sк – площадь поперечного сечения деформированного материала, мм2.Рентгенофазовый анализ (РФА) [31] проводили на порошковом рентгеновском дифрактометре Arl X’tra с угловым разрешением 2θ = 20°–80°. Микроструктуру полученных изделий исследовали на растровом электронном микроскопе LEO-1450 [32, 33].
РЕЗУЛЬТАТЫ И ОБСУЖДЕНИЕ
Температура и скорость горения исходных заготовок являются одними из ключевых параметров для проведения экспериментов, в которых горение протекает в режиме СВС и высокотемпературного сдвигового деформирования. С увеличением температуры горения смеси повышается температурно-временной интервал, при котором СВС-материалы обладают способностью к формованию. На температуру и скорость горения существенным образом влияет относительная плотность исходных заготовок (рис. 3).
Установлено, что с увеличением относительной плотности исходной заготовки температура горения вначале повышается, а затем резко снижается. Это связано с тем, что увеличение относительной плотности приводит к увеличению контакта между частицами и повышению теплоотвода в зоне реакции. Скорость горения выбранных составов, начиная с содержания в смеси 30 мас. % NiCr, резко снижается с 50 до 5 мм/с (табл. 2). Таким образом, для каждого состава была определена оптимальная относительная плотность, при которой температура горения максимальна. Следует отметить, что увеличение содержания нихрома в смеси приводит к необходимости повышения относительной плотности исходной заготовки с целью увеличения температуры горения.
Таблица 2.
Характеристики исходных заготовок и параметры горения
Состав | Оптимальная относительная плотность | tгорения, °C | V, мм/с |
---|---|---|---|
TiC–5 мас. % NiCr | 0.60 | 2314 | 50 |
TiC–10 мас. % NiCr | 0.55 | 2313 | 50 |
TiC–20 мас. % NiCr | 0.62 | 2246 | 50 |
TiC–30 мас. % NiCr | 0.65 | 2050 | 16.6 |
TiC–40 мас. % NiCr | 0.67 | 1841 | 5 |
TiC–50 мас. % NiCr | 0.64 | 1568 | 5 |
Для изучения формуемости готовили исходные заготовки с оптимальной относительной плотностью. Установлено, что увеличение массового соотношения NiCr в исходной смеси ведет к повышению степени деформации, а при достижении максимального значения 30 мас. % NiCr – к ее снижению. Такую зависимость можно связать с двумя факторами. Первый – повышение пластичности синтезированного материала за счет увеличения содержания металлической связки. Второй – снижение пластичности синтезированного материала за счет того, что металлическая связка не участвует в химической реакции и забирает часть теплоты на нагрев и расплавление, что приводит к снижению температуры синтезированного материала. При содержании в исходной смеси до 30 мас. % NiCr первый фактор превалирует, температура горения и скорость высокие (табл. 2), и степень деформации материла повышается. Увеличение содержания NiCr в исходной смеси >30 мас. % приводит к существенному снижению температуры и скорости горения (превалирует второй фактор), что резко уменьшает степень деформации синтезированного материала. Установлено, что содержание 20–40 мас. % NiCr является оптимальным, при котором достигается максимальное значение степени деформации синтезированного материала. На степень деформации также оказывает влияние время задержки перед приложением давления. Из рис. 4 видно, что с увеличением времени задержки (от 0 до 2 с) степень деформации снижается. Увеличение времени задержки приводит к значительным теплопотерям материала после прохождения фронта горения, в результате чего материал остывает и теряет способность к сдвиговому деформированию. При этом следует иметь в виду, что время задержки влияет и на фазовый состав синтезированного материала. Исходя из вышеизложенного, полученные зависимости следует рассматривать, учитывая результаты РФА. Для составов, которые имеют оптимальное массовое содержание 20–40 мас. % NiCr, полученных при СВС-сжатии c временем задержки 0, 1 и 2 с, проведен РФА (рис. 5).
Рис. 5.
РФА образцов состава TiC–20, 30 и 40 мас. % NiCr в зависимости от времени задержки перед приложением давления.

Установлено, что состав TiC–20 мас. % NiCr состоит из трех фаз: TiC, Cr1.12Ni2.88 и Cr2Ni3, это подтверждает отсутствие химического реагирования металлической связки NiCr с исходными реагентами и продуктами синтеза. Температуры горения для всех составов выше температуры плавления металлической связки, поэтому в условиях эксперимента наблюдается ее плавление. Последующая кристаллизация происходит с образованием Cr1.12Ni2.88 и Cr2Ni3. Об этом свидетельствует расщепление дифракционного пика, характерного для NiCr, при 2θ = 44° (рис. 5). С изменением времени задержки от 0 до 2 с размер кристаллической ячейки каждой фазы не меняется. Увеличение доли NiCr до 30 и 40 мас. % приводит к снижению температуры горения состава, в результате в синтезированном материале отмечается наличие непрореагировавшего Ti. Для состава с 30 мас. % NiCr с увеличением времени задержки перед приложением давления происходит полное реагирование Ti с C. За счет более низкой температуры горения при 40 мас. % NiCr непрореагировавший Ti наблюдается при всех временах задержки. Можно отметить, что изменение массового соотношения NiCr в смеси приводит к изменению параметров кристаллической решетки TiC (табл. 3).
Таблица 3.
Параметры элементарной кристаллической ячейки
Состав | Фаза | Время задержки, с | ||
---|---|---|---|---|
0 | 1 | 2 | ||
а, Å (с, Å) | ||||
TiC–20 мас. % NiCr | TiC | 4.3178 | 4.3178 | 4.3178 |
Cr1.12Ni2.88 | 3.54 | 3.54 | 3.54 | |
Cr2Ni3 | 3.579 | 3.579 | 3.579 | |
TiC–30 мас. % NiCr | TiC | 4.322 | 4.322 | 4.322 |
Ti | 2.9505, с = 4.6826 | – | – | |
Cr1.12Ni2.88 | 3.54 | 3.54 | 3.54 | |
Cr2Ni3 | 3.579 | 3.579 | 3.579 | |
TiC–40 мас. % NiCr | TiC | 4.316 | 4.316 | 4.316 |
Ti | 2.9505, с = 4.6826 | 2.9505, с = 4.6826 | 2.9505, с = 4.6826 | |
Cr1.12Ni2.88 | 3.54 | 3.54 | 3.54 | |
Cr2Ni3 | 3.579 | 3.579 | 3.579 |
В качестве модельного состава для исследования микроструктуры синтезированного материала был выбран состав TiC–30 мас. % NiCr, для которого установлена наибольшая степень деформации при свободном СВС-сжатии (рис. 6).
Рис. 6.
СЭМ-фотографии образцов состава TiC–30 мас. % NiCr, полученных при времени задержки: a – 0 с, б – 1 с, в – 2 с.
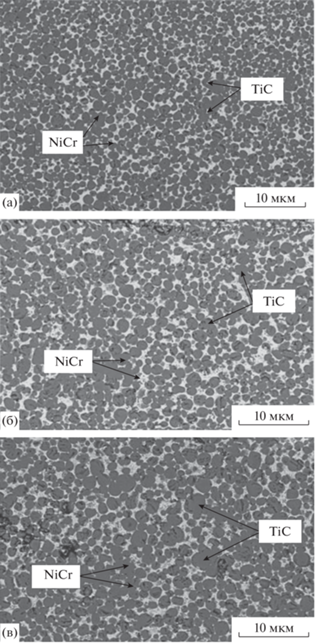
В полученных материалах при времени задержки от 0 до 2 с присутствует три вида структурных составляющих. Основной фазой являются зерна TiC, которые имеют округлую форму. Эти зерна расположены в матрице из NiCr (Cr1.12Ni2.88), локально наблюдается фаза Cr2Ni3. Установлено, что с увеличением времени задержки размер зерен TiC увеличивается, так как синтезированный материал за счет более позднего контакта с плунжером пресса находится более длительное время при высокой температуре. Так, без времени задержки средний размер зерна TiC составляет 1.8 мкм, для 1 с – 2.0 мкм, 2 с – 2.6 мкм [34]. Следует отметить, что при большем времени задержки наблюдаются зерна TiC с размерами до 5 мкм. При меньшем времени задержки формирование структуры материала происходит в условиях более интенсивного теплоотвода, так как взаимодействие синтезированного материала с поверхностью плунжера пресса происходит раньше. При этом образованные зерна TiC не успевают вырасти до более крупных размеров.
На основе полученных данных СЭМ и РФА можно сделать вывод, что синтез исходных реагентов проходит по следующему химическому маршруту, представленному реакциями (3)–(5):
(3)
$\begin{gathered} {\text{Ti}} + {\text{C}} + {\text{NiCr}}\xrightarrow{{600^\circ {\text{C}}}} \\ \to \,\,{\text{TiC}} + {\text{C}}{{{\text{r}}}_{{1.12}}}{\text{N}}{{{\text{i}}}_{{2.88}}} + {\text{C}}{{{\text{r}}}_{2}}{\text{N}}{{{\text{i}}}_{{3{\text{\;}}}}} + {\text{Q}}, \\ \end{gathered} $(5)
${\text{C}}{{{\text{r}}}_{{1.12}}}{\text{N}}{{{\text{i}}}_{{2.88}}} \to {\text{C}}{{{\text{r}}}_{{1.12}}}{\text{N}}{{{\text{i}}}_{{2.88}}} + {\text{C}}{{{\text{r}}}_{2}}{\text{N}}{{{\text{i}}}_{3}}.$Происходит прямое экзотермическое взаимодействие титана с сажей с образованием TiC и выделением большого количества тепла (Q = = 3480 кДж/кг [35]). Исходный порошок NiCr во всех случаях являлся инертным к исходным реагентам и продуктам синтеза. За счет того, что температура горения выбранных составов лежит в диапазоне от 2314 до 1568°C (в зависимости от массового содержания NiCr), металлический порошок NiCr плавится (tпл(NiCr) = 1400°C). После прохождения волны горения происходит его кристаллизация с образованием NiCr как исходной стехиометрии Cr1.12Ni2.88, так и Cr2Ni3.
ЗАКЛЮЧЕНИЕ
Экспериментально установлена оптимальная плотность исходных заготовок для каждого состава системы TiC–(5–50 мас. %) NiCr, соответствующим максимальным температуре и скорости горения.
На основе метода свободного СВС-сжатия исследовано влияние времени задержки перед приложением давления на формуемость материала на основе системы TiC–(5–50 мас. %) NiCr. Установлено, что 20–40 мас. % нихрома являются оптимальным содержанием в исходной смеси, соответствующим максимальной степени деформации синтезированного материала при высокотемпературном сдвиговом деформировании.
Определен химический маршрут при синтезе исходных реагентов титана, сажи и нихрома в условиях горения и высокотемпературного сдвигового деформирования. Показано, что время задержки перед прессованием оказывает влияние на фазовый состав, размер элементарной кристаллической ячейки и структуру синтезированного материала.
Список литературы
Solonenko O.P., Smirnov A.V., Chesnokov A.E. // AIP Conf Proc. 2017. V. 1893. № 1. P. 030003-1. https://doi.org/10.1063/1.5007461
Solonenko O.P., Ovcharenko V.E., Ulianitsky V.Y. et al. // J. Surf. Investig. 2016. V. 10. № 5. P. 1040. https://doi.org/10.1134/S1027451016050402
Markelova O.A., Koshuro V.A., Fomin A.A. et al. // J. Phys. Conf. Ser. 2021. V. 2086. № 1. P. 012188. https://doi.org/10.1088/1742-6596/2086/1/012188
Aramian A., Sadeghian Z., Razavi S.M.J. et al. // J. Mater. Eng. Perform. 2021. V. 30. № 9. P. 6777. https://doi.org/10.1007/s11665-021-05995-8
Chesnokov A.E., Smirnov A.V., Batraev I.S. // J. Synch. Investig. 2019. V. 13. № 4. P. 628. https://doi.org/10.1134/S1027451019030248
Bolelli G., Colella A., Lusvarghi L. et al. // Wear. 2020. V. 450–451. P. 203273. https://doi.org/10.1016/j.wear.2020.203273
Sytchenko A.D., Sheveyko A.N., Levashov E.A. et al. // Russ. J. Non-Ferr. Metals. 2020. V. 61. № 3. P. 325. https://doi.org/10.3103/S1067821220030177
Chandel R., Sharma N., Bansal S.A. // Emergent Mater. 2021. V. 4. № 5. P. 1243. https://doi.org/10.1007/s42247-021-00186-6
Heidari E., Boutorabi S.M.A., Honaramooz M.T. et al. // Int. J. Met. 2021. V. 16. № 1. P. 166. https://doi.org/10.1007/s40962-021-00579-7
Zhong Q., Liu H., Xu L. et al. // J. Iron Steel. Res. Int. 2021. V. 28. № 11. P. 1366. https://doi.org/10.1007/s42243-021-00576-4
Byun J.M., Lee E.S., Heo Y.J. et al. // Int. J. Refract. Hard. Met. 2021. V. 99. P. 105602. https://doi.org/10.1016/j.ijrmhm.2021.105602
Lapshin O.V., Boldyreva E.V., Boldyrev V.V. // Russ. J. Inorg. Chem. 2021. V. 66. № 3. P. 433. [Лапшин О.В., Болдырева Е.В., Болдырев В.В. // Журн. неорган. химии. 2021. Т. 66. № 3. С. 402.] https://doi.org/10.1134/S0036023621030116
Tomilin O.B., Muryumin E.E., Fadin M.V. et al. // Russ. J. Inorg. Chem. 2022. V. 67. № 4. P. 431. [Томилин О.Б., Мурюмин Е.Е., Фадин М.В. и др. // Журн. неорган. химии. 2022. Т. 67. № 4. С. 457.] https://doi.org/10.1134/S0036023622040192
Radishevskaya N.I., Nazarova A.Y., L’vov O.V. et al. // Inorg. Mater. 2020. V. 56. № 2. P. 142. [Радишевская Н.И., Назарова А.Ю., Львов О.В. и др. // Неорган. материалы 2020. Т. 56. № 2. С. 151.] https://doi.org/10.1134/S0020168520010112
Nakashima Y., Kamiya R., Hyuga H. et al. // Ceram. Int. 2020. V. 46. № 11. P. 19228. https://doi.org/10.1016/j.ceramint.2020.04.260
Resnina N., Rubanik Jr., Rubanik V. et al. // Mater. Lett. 2021. V. 299. P.130047. https://doi.org/10.1016/j.matlet.2021.130047
Chizhikov A.P., Konstantinov A.S., Bazhin P.M. // Russ. J. Inorg. Chem. 2021. V. 66. № 8. P. 1115. [Чижиков А.П., Константинов А.С., Бажин П.М. // Журн. неорган. химии. 2021. Т. 66. № 8. С. 1002.] https://doi.org/10.1134/S0036023621080039
Stolin A.M., Kozlov V.V., Kalugin A.V. // Dokl. Akadem. Nauk. 1999. V. 365. № 2. P. 225.
Prokopets A.D., Bazhin P.M., Konstantinov A.S. et al. // Mater. Lett. 2021. V. 301. P. 130331. https://doi.org/10.1016/j.matlet.2021.130165
Stolin A.M., Bazhin P.M., Konstantinov A.S. et al. // Refract. Ind. Ceram. 2019. V. 60. № 3. P. 261. https://doi.org/10.1007/s11148-019-00348-4
Bazhin P.M., Konstantinov A.S., Chizhikov A.P. et al. // Ceram. Int. 2021. V. 47. № 2. P. 1513. https://doi.org/10.1016/j.ceramint.2020.08.292
Prokopets A.D., Bazhin P.M., Konstantinov A.S. et al. // Inorg. Mater. 2021. V. 57. № 9. P. 937. [Прокопец А.Д., Бажин П.М., Константинов А.С. и др. // Неорган. материалы. 2021. Т. 57. № 9. С. 986.] https://doi.org/10.1134/S0020168521090132
Bazhin P.M., Chizhikov A.P., Stolin A.M. et al. // Ceram. Int. 2021. V. 47. № 20. P. 28444. https://doi.org/10.1016/j.ceramint.2021.06.262
Antipov M.S., Chizhikov A.P., Konstantinov A.S. et al. // Refract. Ind. Ceram. 2021. V. 62. № 2. P. 208. [Антипов М.С., Чижиков А.П., Константинов А.С. и др. // Новые огнеупоры. 2021. Т. 4. С. 34.] https://doi.org/10.1007/s11148-021-00584-7
Bazhin P.M., Kostitsyna E.V., Stolin A.M. et al. // Ceram. Int. 2019. V. 45. P. 7. P. 9297. https://doi.org/10.1016/j.ceramint.2019.01.188
Подлесов В.В., Радугин А.В., Столин А.М. и др. // Инженерно-физический журн. 1997. Т. 63. № 5. С. 525.
Shi X.L., Jiang Y.H. // J. Alloys Compd. 2020. V. 816. P. 152681. https://doi.org/10.1016/j.jallcom.2019.152681
Rajak S.K., Aherwar A., Pruncu C.I. // Mater. Res. Express. 2019. V. 7. № 1. P. 016543. https://doi.org/10.1088/2053-1591/ab6534
Мержанов А.Г. Закономерности и механизм горения пиротехнических смесей титана и бора. Черноголовка, 1978. 450 с.
Галышев С.Н., Зарипов Н.Г., Бажин П.М. и др. // Перспективные материалы. 2015. № 11. С. 63.
Tsoutsouva M.G., Regula G., Ryningen B. et al. // Acta Mater. 2021. V. 210. P. 116819.https://doi.org/10.1016/j.actamat.2021.116819
Bao Y., Zhou J.P., Zhang Y. et al. // Mater. Lett. 2021. V. 287. P. 129312. https://doi.org/10.1016/j.matlet.2021.129312
Jiang P., Huang H., Ren W. et al. // Rare Metal Mater. Eng. 2021. V. 50. № 8. P. 3035.
Stel’makh L.S., Stolin A.M., Bazhin P.M. // Inorg. Mater. 2020. V. 56. № 7. P. 695. [Стельмах Л.С., Столин А.М., Бажин П.М. // Неорган. материалы. 2020. Т. 56. № 7. С. 732.] https://doi.org/10.1134/S0020168520070158
Амосов А.П., Боровинская И.П., Мержанов А.Г. Порошковая технология самораспространяющегося высокотемпературного синтеза. М., 2007. С. 471.
Дополнительные материалы отсутствуют.
Инструменты
Журнал неорганической химии