Журнал неорганической химии, 2021, T. 66, № 8, стр. 1032-1039
Влияние добавки Sm2O3 на процесс спекания MgAl2O4 из предкерамического Al,Mg-олигомера
Д. Д. Титов a, *, Г. И. Щербакова b, Е. А. Гуменникова a, А. С. Похоренко b, А. С. Лысенков a, М. Г. Фролова a, Ю. Ф. Каргин a
a Институт металлургии и материаловедения им. А.А. Байкова РАН
119334 Москва, Ленинский пр-т, 49, Россия
b Государственный научно-исследовательский институт химии и технологии элементоорганических соединений
105118 Москва, ш. Энтузиастов, 38, Россия
* E-mail: mitytitov@gmail.com
Поступила в редакцию 03.02.2021
После доработки 30.03.2021
Принята к публикации 01.04.2021
Аннотация
Методом соконденсации органоалюмоксана и ацетилацетоната магния получен предкерамический олигомер органомагнийоксаналюмоксан. Пиролизом олигомера при 700 и 1250°С получены порошки алюмомагнезиальной шпинели (АМШ). Изучено влияние температуры пиролиза на физико-химические и реологические свойства порошка. С ростом температуры пиролиза форма частиц становится ближе к изометрической, что приводит к снижению предельного значения линейного участка кривых уплотнения. Для изучения влияния спекающей добавки получен порошок АМШ с 3 мас. % Sm2O3. Дилатометрическим методом изучена кинетика спекания, оценено влияние спекающей добавки Sm2O3 на процесс и механизм массопереноса при спекании шпинели. По данным количественного анализа, величина энергии активации составила Q1250 = 481 и ${{Q}_{{{\text{S}}{{{\text{m}}}_{{\text{2}}}}{{{\text{O}}}_{{\text{3}}}}}}}$ = = 775 кДж/моль для чистой АМШ и АМШ с Sm2O3 соответственно. Спекающая добавка не влияет на механизм массопереноса, однако на 60% повышает энергию активации, увеличивает усадку в 2 раза и снижает температуру начала спекания от 1546 до 1494°С.
ВВЕДЕНИЕ
Алюмомагнезиальная шпинель MgAl2O4 (АМШ), обладающая высокой температурой плавления, механической, термической и химической стойкостью, представляет интерес для высокотемпературного применения. Керамика на основе АМШ используется в радиотехнике, химическом производстве, оптоэлектронике и рассматривается как перспективный бронематериал [1, 2]. АМШ обладает высокой термостойкостью, прочностью, является твердым огнеупорным материалом, устойчивым к воздействию агрессивных сред. Низкая диэлектрическая проницаемость (~8) АМШ позволяет использовать АМШ в качестве диэлектрика в микроволновых приложениях [3]. MgAl2O4 можно синтезировать методами твердофазных реакций [4, 5], ультразвуковой обработки [6], литья из геля [7], соосаждения [8], золь-гель методом [9] и механохимической активацией [10, 11]. В последние годы в ГНИИХТЭОС разработан новый метод синтеза MgAl2O4 из керамообразующего олигомера [12, 13]. Керамообразующие органомагнийоксаналюмоксаны (Al,Mg-олигомер) устойчивы на воздухе и растворимы в органических растворителях. Пиролиз Al,Mg-олигомера приводит к образованию MgAl2O4, который может быть использован для создания термостойкой, оптически прозрачной, коррозионно- и радиационно-стойкой магний-алюминиевой керамики [13]. Преимуществом этого метода является возможность получения фазы, близкой к стехиометрической, благодаря формированию шпинели еще на стадии синтеза олигомера. Хелатированные алкоксиалюмоксановые олигомеры (органоалюмоксаны) легко взаимодействуют с ацетилацетонатами металлов, в частности с ацетилацетонатом магния, и могут включать в свою структуру широкий набор металлов в различных сочетаниях и соотношениях с гомогенным (на молекулярном уровне) распределением в матрице олигомера [14]. Поэтому в процессе пиролиза органомагнийоксаналюмоксан с мольным соотношением Al/Mg = 2/1 трансформируется с образованием нанопорошка шпинели.
Для снижения температуры спекания, увеличения относительной плотности и улучшения оптических свойств MgAl2O4 применяли различные добавки. Например, добавление AlF3 или CaF2 ускоряет образование АМШ за счет замены кислорода в решетке [15]. Добавка Cr2O3 улучшает термостойкость и стойкость периклазошпинелевых кирпичей к горячему шлаку [16]. Применение спекающей добавки TiO2 приводит к повышению относительной плотности MgAl2O4 за счет растворения TiO2 в шпинели [17]. В [18] отмечается влияние редкоземельной добавки CeO2 на шпинель: в шпинели с высоким содержанием глинозема добавка CeO2, прореагировавшая с Al2O3, выделяется с образованием пластинчатых частиц CeAl11O18, кристаллизующихся между зернами шпинели, препятствующих процессу спекания; в шпинели, богатой оксидом магния, присутствие CeO2 ингибирует рекристаллизацию кристаллов АМШ. При введении добавки Sm2O3 образуется алюминат самария, что благодаря синергетическому эффекту благоприятно сказывается на оптических свойствах керамики [19].
Прозрачная керамика из шпинели может быть использована как элемент оптики космических телескопов, защитных обтекателей, колпаков и окон для ракет, выводных окон УФ- и ИК-лазерных устройств. Однако получение материала, соответствующего всем этим требованиям, является сложной задачей, требующей учета всех его этапов: метода синтеза исходного порошка шпинели, влияния спекающей добавки, изучения процесса уплотнения при прессовании и спекании.
Цель настоящей работы – исследование влияния условий синтеза исходного порошка АМШ из предкерамического Al,Mg-олигомера и спекающей добавки Sm2O3 на спекание алюмомагнезиальной шпинели.
ЭКСПЕРИМЕНТАЛЬНАЯ ЧАСТЬ
Синтез предкерамического олигомера – органомагнийоксаналюмоксана проводили в ГНИИХТЭОС по ранее описанной методике [12]. Полученный порошок подвергали пиролизу при 700 и 1250°С в течение 10 ч на воздухе. Измельчение порошка АМШ после пиролиза и смешение со спекающей добавкой оксида самария (Sm2O3, ТУ 48-4-189-72) проводили в планетарной мельнице (Pulverisette 5 фирмы Fritsch GMBH) в течение 2 ч при 250 об/мин в растворе изопропилового спирта. Измельченный порошок сушили при 130°C до полного удаления спирта. Синтез шпинели со спекающей добавкой осуществляли в муфельной печи в течение 10 ч при 1250°С. Полученный порошок шпинели анализировали с помощью гранулометрического (лазерный дифракционный анализатор Fritsch Particle Sizer “analysette 22”) и рентгенофазового анализа (дифрактометр Rigaku D/MAX-2500), сканирующей электронной микроскопии (Tescan Vega II SBU, Tescan), удельная поверхность определена методом Бранауэра–Эммета–Теллера (Micromeritics TriStar) (табл. 1).
Таблица 1.
Основные характеристики исходных порошков
№ | tпиролиза, °С | Спекающая добавка | Средний размер частиц, мкм | Размер кристаллитов (ОКР), нм | Удельная поверхность, м2/г | ∆h/h0, % линейного участка |
---|---|---|---|---|---|---|
1 | 700 | – | 5–10 | 4.6 | 40.3 | 12.4 |
2 | 800 | – | 0.5–5 | 6.2 | – | 11.5 |
3 | 1250 | – | 0.5–5 | 59 | 5.6 | 11.0 |
4 | 1250 | 3 мас. % Sm2O3 | 2–4 | – | – | 10.2 |
Дилатометрические исследования. Образцы для измерения относительной усадки формовали в стальной пресс-форме сухим прессованием при давлении 100 МПа в форме цилиндров, помещали в горизонтальный графитовый держатель дилатометра DIL 402 C с вакуум-плотной печью, оснащенной графитовым толкателем с высокоточным преобразователем смещения (диапазон измерения до 5000 мкм). Печь нагревали со скоростью 5, 10 и 20 град/мин до температуры 1650°С, охлаждение вели до комнатной температуры со скоростью 20 град/мин. При анализе уплотнения всех образцов делается допущение об отсутствии анизотропии. Плотность спеченного образца (ρs) рассчитывали по следующему уравнению [20]:
(1)
$~{{\rho }_{{\text{s}}}} = {{\left[ {\frac{1}{{1 + \frac{{\Delta L}}{{{{L}_{0}}}} - \alpha \left( {T - {{T}_{0}}} \right)}}} \right]}^{3}}{{\rho }_{{\text{g}}}},$Уравнения спекания (2) и (3) для постоянной скорости нагрева получены в работах [23, 24]:
(2)
$\begin{gathered} \ln \left[ {TC\frac{{d\rho }}{{dT}}} \right] = \\ = - \frac{Q}{{RT}} + \ln [f(\rho ) + \ln \left[ {\frac{{K\gamma \Omega {{D}_{0}}}}{{{{k}_{b}}}}} \right] - p\ln (a), \\ \end{gathered} $(3)
$\begin{gathered} \frac{{d({{\Delta L} \mathord{\left/ {\vphantom {{\Delta L} {{{L}_{0}})}}} \right. \kern-0em} {{{L}_{0}})}}}}{{dT}} = \\ = \ln {{\left( {\frac{{K\gamma \Omega {{D}_{0}}R}}{{{{k}_{b}}{{a}^{p}}CQ}}} \right)}^{n}}\exp \left( {\frac{{nQ}}{{R{{T}^{{2 - n}}}}}} \right)\exp \left( { - \frac{{nQ}}{{RT}}} \right), \\ \end{gathered} $Энергию активации (Q) и кажущуюся энергию активации (nQ) начальной стадии спекания оценивали по формулам, представленным в работе [25]. Порядок (n), связанный с механизмом спекания, равен отношению кажущейся энергии активации к энергии активации (уравнение (6)). Определяли значения T и скорости нагрева (dt/dτ) = C при одной и той же относительной плотности образцов для каждой скорости нагревания. Построенные в координатах графики ln[TC(dρ/dT)] от 1/T позволяют определить угол наклона S1. При одинаковом значение плотности энергия активации описывается уравнением:
Угол наклона S2 зависимости ln[T(d∆L/L0)/dT] от 1/T позволяет определить кажущуюся энергию активации следующим образом:
РЕЗУЛЬТАТЫ И ОБСУЖДЕНИЕ
Результаты РФА порошков после пиролиза и помола представлены на рис. 1. После пиролиза при 700°С порошок имеет высокую дисперсность и, по-видимому, заметную долю аморфной фазы. Размер кристаллитов (область когерентного рассеяния (ОКР)) АМШ, оцененный по формуле Шеррера–Селякова, составляет 4 нм. Дальнейшее повышение температуры пиролиза до 1250°С приводит к полной кристаллизации шпинели (рис. 2). Эти данные согласуются с результатами ДСК, представленными в работе [13], где показано, что в области 800°С наблюдается эндотермический эффект, соответствующий образованию кристаллической фазы алюмомагнезиальной шпинели. Исследование морфологии частиц после пиролиза олигомера при 700°С показывает (рис. 2), что порошок состоит преимущественно из крупных агломератов неправильной формы размером 5–10 мкм, включающих наночастицы шпинели (табл. 1). Повышение температуры пиролиза до 1250°С приводит к формированию кристаллических частиц правильной прямоугольной формы; по данным ОКР, размер кристаллитов увеличивается до 59 нм (рис. 2б). В работе [19] отмечается, что оксид самария вступает в реакцию с оксидом алюминия в шпинели в соответствии с реакциями, приведенными ниже:
(7)
${\text{MgO}} + {\text{A}}{{{\text{l}}}_{{\text{2}}}}{{{\text{O}}}_{3}} \to {\text{MgA}}{{{\text{l}}}_{{\text{2}}}}{{{\text{O}}}_{4}},$(8)
${\text{S}}{{{\text{m}}}_{{\text{2}}}}{{{\text{O}}}_{3}} + {\text{A}}{{{\text{l}}}_{{\text{2}}}}{{{\text{O}}}_{3}} \to {\text{2SmAl}}{{{\text{O}}}_{{\text{3}}}}{\text{.}}$Поскольку температура пиролиза влияет на гранулометрический состав порошка, для определения оптимальных условий компактирования исследовано влияние температуры пиролиза на зависимость относительного уплотнения порошка от приложенного давления прессования, полученные данные в дальнейшем использовали для расчета энергии активации начальной стадии процесса спекания. На рис. 3 приведены зависимости относительного уплотнения порошков, полученных при разной температуре пиролиза, от приложенного давления. Видно, что для порошка после пиролиза олигомера при 700°С предельное значение линейного участка уплотнения составляет 12.4% от исходного, а после пиролиза при 1250°С – 11.0%. Это связано с тем, что с ростом температуры пиролиза форма частиц становится близкой к изометричной (рис. 2), вследствие чего частицы быстрее заполняют пустоты при приложении давления. Введение спекающей добавки способствует дальнейшему снижению предельного значения линейного участка уплотнения до 10.2%. По-видимому, добавка может выполнять роль ингибитора роста частиц и их агломерации.
Рис. 3.
Зависимости относительного уплотнения порошка АМШ от приложенного давления при 700 (1), 800 (2), 1250°C (3), 1250°C + 3% Sm2O3 (4).
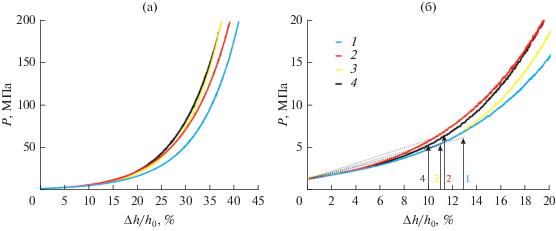
График относительного уплотнения порошка можно разделить на 3 участка: 1 – линейный, рассмотренный выше (0–13%); 2 – параболический (10–30%), на данном этапе происходит аккомодация или приспособление частиц порошка; 3 – экспоненциальный (30–45%), здесь наблюдается значительный рост напряжения при малых изменениях деформации, на этом участке частицы начинают деформироваться, так как свободного пространства в компакте уже не осталось. Попадание именно в третью область деформационной кривой приводит к образованию в образцах перепрессовочных трещин, так как при снижении давления деформированные частицы возвращаются к исходному состоянию и резко снижается площадь контакта между ними. Таким образом, для изучения процессов спекания были выбраны значения давления прессования компактов (сырцов), обеспечивающие близкие значения относительной плотности исследуемых образцов при отсутствии перепрессовочных трещин.
Для дилатометрического анализа использовали образцы компактов с относительной плотностью 55–60%, рассчитанной по геометрическим размерам. Экспериментальные дилатометрические кривые показывают (рис. 4), что на процесс спекания шпинели сильное влияние оказывает температура пиролиза исходного порошка олигомера: порошки, прокаленные при 1250°С, имеют классический ход кривой с началом усадки при 1490–1550°С и усадкой до 8%, в то время как кривые усадки порошка шпинели, полученной после пиролиза при 700–800°С, имеют сложный и многостадийный характер с началом усадки в области 1000–1250°С. Подобный эффект описан в работе [26], авторы предполагают, что двухстадийное спекание связано с образованием перешейков между частицами MgAl2O4, что соответствует первому перегибу на кривой спекания, тогда как второй этап связан с уплотнением материала. Следует также отметить, что в порошках АМШ после осаждения и пиролиза до 1100°С в [26], по данным РФА, регистрируются фазы Al2O3 и MgO.
Рис. 4.
Графики зависимости: a – относительной усадки, б – скорости усадки от температуры пиролиза олигомера: 1 – 700, 2 – 800, 3 – 1250°С, 4 – 1250°С с добавкой Sm2O3.
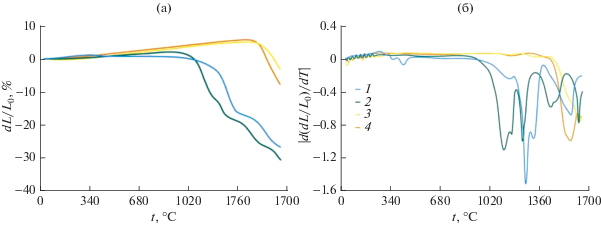
На кривых скорости спекания порошков АМШ, полученных пиролизом при 700 и 800°С, в области температур 1020–1700°С наблюдается последовательность нескольких (от 4 до 6) пиков (рис. 4). Можно предположить, что в этом случае многостадийное спекание обусловлено протеканием ряда последовательных и параллельных процессов: на начальном этапе в области до 1200°С идет процесс кристаллизации аморфной фазы, твердофазный синтез шпинели MgAl2O4, процесс усадки которой происходит в интервале температур 1350–1550°С (рис. 4). По этой причине применение уравнений (5) и (6) для вычисления энергии активации образцов после пиролиза при 700–800°С некорректно. Поэтому все расчеты проводили на образцах порошков шпинели после пиролиза при 1250°С.
Поведение образцов в процессе спекания порошков, полученных пиролизом олигомера при температуре 1250°С, меняется. До 1500°С наблюдается линейное расширение образца, связанное с ТКЛР шпинели. Далее при 1546°С начинается процесс усадки образца АМШ до 3.55% при 1650°С. По данным [18, 27], значение усадки нанопорошка шпинели (полученной другим способом) находится в том же диапазоне, а спекание происходит при более высоких температурах обжига.
Введение спекающей добавки Sm2O3 способствует активации процесса спекания и снижению начала спекания от 1546°С для АМШ до 1494°С для АМШ со спекающей добавкой, при этом усадка образца увеличивается более чем в 2 раза (до 8%) при 1650°С. Исследования образцов шпинели, полученной твердофазной реакцией из оксидов, но с большим содержанием оксида самария (от 5 до 15 мас. %) проводили в работах [28, 29]. Отмечено, что частицы SmAlO3, образующиеся в результате реакции Sm2O3 и Al2O3 в межзеренном пространстве шпинели, повышают коэффициент объемной усадки, насыпную плотность и прочность на сжатие в холодном состоянии. Однако детальные дилатометрические исследования для определения достоверной температуры начала спекания шпинели с добавкой Sm2O3 не проводили.
Измерение усадки и скорости усадки образцов шпинели при неизотермическом спекании проводили при трех скоростях нагревания: 5, 10, 20 град/мин. Установлено, что максимальная скорость усадки зависит от скорости нагревания, и чем выше скорость нагревания, тем больше скорость усадки. Эта тенденция хорошо известна и ранее обнаружена для MoSi2 [25], Al2O3 [30] и 3Y-TZP [31].
Влияние спекающей добавки Sm2O3 на процесс спекания порошков АМШ оценивали по результатам расчетов значений параметра спекания и энергии активации спекания. Построены графики в координатах ln[TC(dρ/dT)] от 1/T и ln[T(d∆L/L0)/dT] от 1/T (рис. 5). Для каждой скорости нагревания (dT/dt) = C определяли значения температуры T при одном и том же значении относительной плотности образцов. Расчеты выполняли для величин относительной плотности ≤71%, что соответствует относительному диапазону усадки <4%, температура пиролиза олигомеров составляла 1250°С при получении порошков шпинели без добавки и со спекающей добавкой 3 мас. % Sm2O3. Видно, что графики для каждого значения относительной плотности образцов имеют линейный характер. Значение энергии активации (Q) процесса спекания при каждой относительной плотности определяли по наклону прямой линии. Полученные данные по энергии активации начала спекания и механизму массопереноса приведены в табл. 2. Изменение параметра спекания n от 0.98 до 0.93 в обоих случаях свидетельствует о том, что доминирующий механизм массопереноса соответствует объемной диффузии как для АМШ без добавки, так и со спекающей добавкой. Спекающая добавка не влияет на механизм спекания. Авторы [31] провели исследования по влиянию оксидных добавок SiO2, SnO2 и GeO2 на процесс массопереноса диоксида циркония и выяснили, что SiO2 и SnO2 увеличивают энергию активации от 667 до 989 кДж/моль, для оксида GeO2 отмечается снижение до 537 кДж/моль при 5 мас. %. Механизм массопереноса ZrO2 изменяется от объемной диффузии для добавки SnO2 до зернограничной диффузии с добавкой SiO2. Однако добавка GeO2 не влияет на механизм. Авторы отмечают, что на механизм массопереноса влияет размер ионов и способность добавки образовывать соединения с основной фазой. В работе [32] для процесса спекания порошка АМШ получено значение энергии активации 37.9 кДж/моль. Поскольку в [32] энергию активации рассчитывали для порошков АМШ, полученной методом совместного обратного осаждения гидроксидов металлов, исходя из среднего размера зерен и плотности заготовок, полученных при разных температурах в вакуумной печи, значения энергии активации значительно отличаются от полученных в данной работе.
Рис. 5.
Графики для определения Q (а) и nQ (б) шпинели после пиролиза при 1250°С: кружки – чистой, треугольники – с 3 мас. % Sm2O3.

Таблица 2.
Параметры спекания n, энергия активации Q процесса спекания и механизмы спекания всех исследованных образцов
№ | Образец | n | Q, кДж/моль | Станд. откл. | Механизм спекания |
---|---|---|---|---|---|
3 | MgAl2O4, пиролиз 1250°С | 0.98 | 481 | 103 | Объемная диффузия |
4 | MgAl2O4 + 3 мас. % Sm2O3, пиролиз 1250°С | 0.93 | 775 | 59 | Объемная диффузия |
ЗАКЛЮЧЕНИЕ
Исследовано влияние температуры пиролиза предкерамического Al,Mg-олигомера и спекающей добавки оксида самария на свойства порошков алюмомагнезиальной шпинели. Показано, что порошки АМШ, полученной пиролизом олигомера при 700°С, состоят из крупных агломератов размером 5–10 мкм, состоящих из наночастиц шпинели с величиной ОКР 4–6 нм и аморфных частиц; повышение температуры пиролиза до 1250°С приводит к формированию изометричных кристаллических частиц, характеризующихся величиной ОКР 50–60 нм.
Рассчитана энергия активации начала спекания порошков алюмомагнезиальной шпинели без добавок и с 3 мас. % Sm2O3 после пиролиза при 1250°С, составляющая Q1250 = 481 и ${{Q}_{{{\text{S}}{{{\text{m}}}_{2}}{{{\text{O}}}_{3}}}}}$ = = 775 кДж/моль соответственно. Значения параметра спекания n от 0.98 до 0.93 показывают, что доминирующий механизм массопереноса соответствует объемной диффузии, а спекающая добавка не влияет на механизм спекания.
Список литературы
Dal Maschio R., Fabbri B., Fiori C. // Ind. Ceram. 1988. V. 8. P. 121.
Sarkar R. // Intercer. Ref. Man. 2011. V. 1. P. 28.
Zegadi A., Kolli M., Hamidouche M. et al. // Ceram. Int. 2018. V. 44. № 15. P. 18828. https://doi.org/10.1016/j.ceramint.2018.07.117
Obradović A., Matić M., Ognjanović B. et al. // Sci. Sint. 2019. V. 51. № 4. P. 363. https://doi.org/10.2174/1871520619666190425180610
Rahmat N., Yaakob Z., Pudukudy M. et al. // Powder. Technol. 2018. V. 329. P. 409. https://doi.org/10.1016/j.powtec.2018.02.007
Raghu R., Nampoothiri J., Satish Kumar T. // Measur. 2018. V. 129. P. 389. https://doi.org/10.1016/j.measurement.2018.07.056
Shahbazi H., Tataei M. // Ceram. Int. 2019. V. 45. P. 8727. https://doi.org/10.1016/j.ceramint.2019.01.196
Saelee A., Jiemsirilers S., Jinawath S. et al. // Key Eng. Mater. 2016. V. 690. P. 224. https://doi.org/10.4028/www.scientific.net/KEM.690.224
Евстропьев С.К., Никоноров Н.В. Жидкостные методы получения оптических наноматериалов: учеб. пособие. СПб.: Университет ИТМО, 2018. 84 с.
Obradović N., Fahrenholtz W.G., Filipović S. et al. // Ceram. Int. 2019. V. 45 № 9. P. 12015. https://doi.org/10.1016/j.ceramint.2019.03.095
Bar-On P., Lin I., Nadiv S. et al. // J. Therm. Anal. Calorim. 1994. V. 42. № 1. P. 207.
Shcherbakova G.I., Pokhorenko A.S., Storozhenko P.A. et al. // Russ. J. Inorg. Chem. 2021. V. 66. № 1. P. 25. https://doi.org/10.1134/S0036023621010083
Shcherbakova G.I., Storozhenko P.A., Apukhtina T.L. et al. // Polyhed. 2017. V. 135. P. 144. https://doi.org/10.1016/j.poly.2017.07.006
Shcherbakova G.I., Storozhenko P.A., Zhigalov D.V. et al. // Russ. Chem. Bull. 2020. V. 69. P. 875. https://doi.org/10.1007/s11172-020-2844-1
Kostic E., Boskovic S., Kis S. // J. Mater. Sci. Lett. 1982. V. 1. P. 507.
Sarkar R., Das S.K., Banerjee G. // J. Eur. Ceram. Soc. 2002. V. 22. P. 1243. https://doi.org/10.1016/S0955-2219(01)00446-0
Naghizadeh R., Rezaie H.R., Golestani-Fard F. // Ceram. Int. 2011. V. 37. № 1. P. 349. https://doi.org/10.1016/j.ceramint.2010.09.016
Quan Z., Wang Z., Wang X. et al. // Ceram. Int. 2019. V. 45. № 1. P. 488. https://doi.org/10.1016/j.ceramint.2018.09.194
Ren X., Ma B., Zhang G. et al. // Mater. Chem. Phys. 2020. V. 252. P. 123309. https://doi.org/10.1016/j.matchemphys.2020.123309
Abbasian A.R., Rahimipour M.R., Hamnabard Z. // Iranian J. Mat. Sci. Eng. 2013. V. 10. № 3. P. 44. http://ijmse.iust.ac.ir/article-1-573-en.html
Mazaheri M., Simchi A., Dourandish M. et al. // Ceram. Int. 2009. V. 35. № 2. P. 547. https://doi.org/10.1016/j.ceramint.2008.01.008
Bernard-Granger G., Guizard C. // J. Am. Ceram. Soc. 2007. V. 90. № 4. P. 1246. https://doi.org/10.1111/j.1551-2916.2006.01415.x
Matsui K., Ohmichi N., Ohgai M. et al. // J. Am. Ceram. Soc. 2005. V. 88. № 12. P. 3346. https://doi.org/10.2109/jcersj.114.763
Matsui K., Tanaka K., Enomoto N. et al. // J. Ceram. Soc. Jpn. 2006. V. 114. № 1333. P. 763. https://doi.org/10.2109/jcersj.114.763
Titov D.D., Miloserdov P.A., Frolova M.G. et al. // Inorg. Mater. 2018. V. 54. № 11. P. 1113. https://doi.org/10.1134/S0020168518110134
Mouyane M., Jaber B., Bendjemil B. et al. // Int. J. App. Cer. Tech. 2019. V. 16. № 3. P. 1138. https://doi.org/10.1111/ijac.13172
Tolstikova D.V., Gol’eva E.V., Lebanin V.S. et al. // J. Opt. Tech. 2014. V. 81. № 12. P. 754. https://doi.org/10.1364/JOT.81.000754
Ma B., Yin Y., Zhu Q. et al. // Ceram. Silik. 2015. V. 59. № 2. P. 109.
Yuan L., Ma B., Zhu Q. et al. // Ceram. Int. 2017. V. 43. № 18. P. 16258. https://doi.org/10.1016/j.ceramint.2017.08.210
Aminzare M., Golestani-Fard F., Guillon O. et al. // Mater. Sci. Eng. A. 2010. V. 527. № 16-17. P. 3807. https://doi.org/10.1016/j.msea.2010.03.051
Lakusta M., Danilenko I., Volkova G. et al. // Int. J. App. Ceram. Tech. 2019. V. 16. № 4. P. 1481. https://doi.org/10.1111/ijac.13215
Габелков С.В., Тарасов Р.В., Полтавцев Н.С. и др. // Вопросы атомной науки и техники. 2014. Т. 90. № 2. С. 107.
Дополнительные материалы отсутствуют.
Инструменты
Журнал неорганической химии