Журнал неорганической химии, 2021, T. 66, № 8, стр. 1120-1125
Влияние комплексных добавок на основе оксидов железа, кобальта, марганца и силиката натрия на спекание и свойства низкотемпературной керамики 3Y–TZP–Al2O3
Т. О. Оболкина a, *, М. А. Гольдберг a, О. С. Антонова a, С. В. Смирнов a, Ю. Б. Тютькова a, А. А. Егоров a, И. В. Смирнов a, А. А. Коновалов a, С. М. Баринов a, В. С. Комлев a
a Институт металлургии и материаловедения им. А.А. Байкова РАН
119334 Москва, Ленинский пр-т, 49, Россия
* E-mail: tobolkina@imet.ac.ru
Поступила в редакцию 10.02.2021
После доработки 19.03.2021
Принята к публикации 22.03.2021
Аннотация
Изучено влияние комплексных добавок на основе оксидов кобальта, железа, марганца и силиката натрия на фазовый состав, микроструктуру, механические свойства и спекание керамики на основе тетрагонального диоксида циркония, стабилизированного 3 мол. % оксида иттрия, с 10 мас. % оксида алюминия (3Y–TZP–10Al2O3). Показано, что введение комплексных добавок существенно влияет на спекание керамики – открытая пористость менее 1% после обжига при 1250°С. Использование в качестве спекающей добавки Na2Si2O5–0.33% Mn позволило обеспечить минимальную пористость при температуре спекании 1300°С. Получена керамика с прочностью на изгиб 500 ± 16 МПа и микротвердостью 10 ГПа.
ВВЕДЕНИЕ
Оксидная керамика на основе стабилизированного иттрием тетрагонального поликристаллического диоксида циркония (Y–TZP), характеризующаяся трансформационным упрочнением [1], и композиционные материалы на ее основе нашли широкое применение в различных областях техники благодаря высоким физико-химическим свойствам (прочности, трещиностойкости и коррозионной стойкости). Однако высокая температура обжига для получения керамики (1600–1750°С) ограничивает применение изделий из Y–TZP, так как требует использования дорогостоящего и энергоемкого термического оборудования, например, методов горячего и изостатического прессования. Это приводит к существенному повышению стоимости изделий из данных материалов.
Температуру спекания керамики на основе диоксида циркония можно понизить путем введения модифицирующих добавок [2–4]. В работе [4] исследовано влияние введения до 5 мас. % различных катионов металлов (Zn, Co, Ni, Fe, Li, Bi, Mn и др.) на спекание кубического диоксида циркония, стабилизированного 8 мол. % оксида иттрия. Авторами было показано, что интенсификация кинетики спекания связана с образованием дефектов кристаллической решетки при введении катиона с другим ионным радиусом и валентностью по сравнению с матрицей ZrO2. Многие авторы [2, 3, 5, 6] указывают также на влияние модифицирующих добавок на морфологию, рост механических характеристик и другие свойства керамических материалов на основе диоксида циркония.
В наших предыдущих работах [7–9] была установлена способность добавок оксидов переходных металлов (железа и кобальта) снижать температуру обжига и обеспечивать высокие механические свойства керамики для экспериментальных составов 3Y–TZP–5Al2O3, 3Y–TZP–10Al2O3 и 3Y–TZP–20Al2O3.
Известно, что для интенсификации процесса спекания используются добавки, образующие жидкую фазу [10–13]. Авторами [11] показано, что введение оксида кремния (SiO2) способствует увеличению скорости спекания кубического диоксида циркония, стабилизированного 8 мол. % Y2O3 (8YCSZ). В результате введения SiO2 спекание проходит по жидкофазному механизму. Жидкая фаза, образующаяся на границе зерен в результате реакции SiO2 с диоксидом циркония и иттрием, способствует снижению температуры обжига до 1300°С. В работе [14] изучено влияние SiO2 на микротвердость, шероховатость поверхности, трещиностойкость, микроструктуру, а также на температурный коэффициент линейного расширения материала 5Y–TZP с 20 мас. % Al2O3 и различным содержанием SiO2 (5, 10, 15 мас. %) при температуре спекания 1600°С. Для такого материала, содержащего 15 мас. % SiO2, получена прочность при трехточечном изгибе 366 ± 9 МПа и трещиностойкость 5.21 МПа м1/2. В то же время силикат натрия рассматривается как перспективный материал для формирования жидкой фазы при спекании композиционного материала Al2O3–ZrO2 [15] и кубического диоксида циркония [16].
Значительный интерес представляет разработка комплексных добавок, способных не только понижать температуру обжига за счет легкоплавкого компонента, но и оказывать стабилизирующее воздействие на фазовый состав.
Целью настоящей работы является исследование влияния состава комплексной добавки на основе силиката натрия и оксидов переходных металлов (кобальта (Co), железа (Fe), марганца (Mn)) на спекание, фазовый состав, микроструктуру и механические свойства тетрагонального диоксида циркония (3Y–TZP), содержащего 10 мас. % оксида алюминия (Z–A).
ЭКСПЕРИМЕНТАЛЬНАЯ ЧАСТЬ
Порошки тетрагонального диоксида циркония, стабилизированного 3 мол. % (5.4 мас. %) оксида иттрия, с 10 мас. % оксида алюминия (Z–A) синтезировали методом химического осаждения [3, 4] из водных растворов соответствующих солей. Использовали химические реактивы ZrOCl2 · · 8H2O, АlCl3 · 6H2O, YCl3 · 6H2O, NH4HCO3 квалификации “х. ч.”, NH4OH марки “ос. ч.” (ООО “СИГМА ТЕК”, Россия). В полученный порошок вводили силикат натрия (Na2Si2O5), а также комплексные добавки на его основе с добавлением катионов переходных металлов (Co, Fe, Mn). Обозначение составов приведено в табл. 1.
Таблица 1.
Состав керамических материалов 3Y–TZP–10Al2O3 (Z–A)
Состав | Na2Si2O5, мас. % | Со | Fe | Mn |
---|---|---|---|---|
мол. % | ||||
Z–A | – | – | – | – |
Z–A–N | 5 | – | – | – |
Z–A–N–Co | 5 | 0.33 | – | – |
Z–A–N–Fe | 5 | – | 0.33 | – |
Z–A–N–Mn | 5 | – | – | 0.33 |
Полученную шихту формовали в виде балочек размером 30 × 4 × 4 мм в металлической пресс-форме при давлении 100 МПа одноосным прессованием. Затем образцы обжигали в печах с силитовыми нагревателями в воздушной атмосфере при температурах 1250–1450°С.
Рентгенофазовый анализ (РФА) керамических материалов проводили в CrKα-излучении с помощью дифрактометра Дифрей 401 (Россия). Полученные дифрактограммы анализировали с использованием данных картотеки JCPDS и программы PCPDFWIN. Для идентификации фазового состава использовали карточки JCPDS # 42-1164 диоксида циркония тетрагональной модификации (t-ZrO2), JCPDS # 37-1484 диоксида циркония моноклинной модификацией (m-ZrO2), JCPDS #10-0173 α-оксида алюминия тригональной сингонии (α-Al2O3, корунд).
Открытую пористость испытуемых образцов определяли в соответствии с требованиями ГОСТ 2409-2014.
Микроструктуру обожженных образцов исследовали методом растровой электронной микроскопии (РЭМ) на микроскопе Tescan Vega II (Чехия) и с помощью компьютерной микротомографии (микроКТ) Skyscan 1275 фирмы Bruker (Бельгия) с номинальной разрешающей способностью 4 мкм. Для анализа образцов было выбрано ускоряющее напряжение 80 кВ и ток 120 мкА.
Для исследования механических свойств обожженные материалы полировали алмазной пастой. Прочность материалов при трехточечном изгибе определяли на разрывной машине Instron 3382 (США), статистика по пяти образцам. Микротвердость образцов определяли на микротвердомере 401/402-MVD фирмы Instron (США) методом Виккерса, трещиностойкость – по геометрическим размерам отпечатка в соответствии с формулой [17]:
где Е – модуль Юнга, ГПа, Н – микротвердость, ГПа, Р – прикладываемая нагрузка, МПа, с – среднее расстояние от центра отпечатка до конца вершины, мкм.РЕЗУЛЬТАТЫ И ОБСУЖДЕНИЕ
По данным РФА, керамика без добавок (Z–A), обожженная при 1450°С, состоит преимущественно из t-ZrO2 и незначительного количества (до 5 мас. %) m-ZrO2 (рис. 1). На рис. 2 представлены дифрактограммы образцов с комплексной добавкой на основе силиката натрия. Все составы в интервале 1250–1270°С характеризуются формированием t-ZrO2 и корунда. Отсутствие пиков фазы m-ZrO2 свидетельствует о стабилизации t-ZrO2 при введении комплексных добавок Na2Si2O5 с катионами Mn, Fe и Со. Повышение температуры обжига до 1300°С приводит к формированию незначительного количества (не более 3 мас. %) m-ZrO2 для всех составов.
Рис. 1.
Дифрактограмма керамического материала Z–A, обожженного при 1450°С, где t – t-ZrO2, m – m-ZrO2, A – Al2O3.
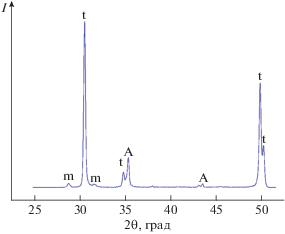
Рис. 2.
Дифрактограммы керамических материалов Z–A–N, обожженных при 1250 (а) и 1300°С (б) в зависимости от состава: 1 – Z–A–N, 2 – Z–A–N–Co, 3 – Z–A–N–Fe, 4 – Z–A–N–Mn, где t – t-ZrO2, m – m-ZrO2, A – Al2O3.
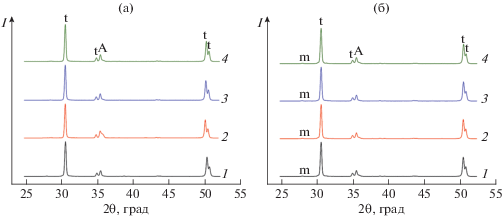
Данные по открытой пористости представлены в табл. 2. Введение комплексной добавки оказывает существенное влияние на открытую пористость образцов – уже при 1250°С она ниже 1%, в то время как для материалов, содержащих только Na2Si2O5, она снижается от 18.97 до 3.29% по мере роста температуры. В материале Z–A при 1450°С она составляет 7.77%. Наименьшая пористость выявлена для состава Z–A–N–Mn во всем диапазоне температур.
Таблица 2.
Открытая пористость образцов керамики 3Y–TZP–10Al2O3 в зависимости от температуры обжига
Образец | Пористость, % | ||
---|---|---|---|
1250°С | 1270°С | 1300°С | |
Z–A–N | 18.97 | 15.47 | 3.29 |
Z–A–N–Co | 0.18 | 0.36 | 0.82 |
Z–A–N–Fe | 0.41 | 0.06 | 0.53 |
Z–A–N–Mn | 0.06 | 0.06 | 0.36 |
Согласно исследованиям методом микроКТ, в образцах состава Z–A–N (t = 1300°С), Z–A–N–Mn (t = 1300°С), Z–A–N–Mn (t = 1250°С) не выявлено внутренней пористости и скрытых дефектов крупнее 4 мкм. При этом образцы состава Z–A–N, обожженные при 1300°С, характеризуются меньшей степенью однородности по плотности по сравнению с образцами состава Z–A–N–Mn (рис. 3).
Рис. 3.
Изображения, полученные с помощью компьютерной микротомографии керамических материалов: а, б, в – Z–A–N (t = 1300°С); г, д, е – Z–A–N–Mn (t = 1300°С); ж, з, и – Z–A–N–Mn (t = 1250°С).
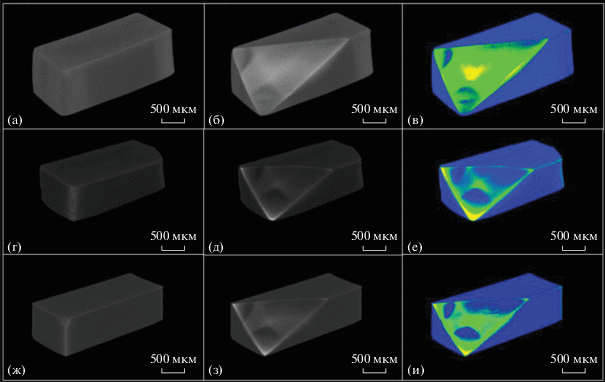
Анализ микроструктуры, по данным РЭМ, показал, что материал Z–A, обожженный при 1450°С, характеризуется пористой структурой, состоящей из равномерно распределенных крупных кристаллов до 1.0–1.5 мкм и мелких кристаллов размером 100–200 нм (рис. 4). Введение силиката натрия в Z–A приводит к формированию равномерной микроструктуры с размером зерен <100 нм при обжиге при 1250°С. При этом в материале наблюдаются закрытые поры размером до 1–2 мкм (рис. 5).
В керамических материалах Z–A–N, обожженных при 1300°С, размер зерна возрастает до 100–200 нм, при этом сохраняются закрытые поры размером до 2 мкм. Введение комплексных добавок (составы Z–A–N–Co, Z–A–N–Fe, Z–A–N–Mn) приводит к формированию однородной плотной микроструктуры после обжига при 1250°С (рис. 6). Материалы состоят преимущественно из зерен округлой формы размером <100 нм. Кристаллы Al2O3, имеющие более темный оттенок на микрофотографии, также состоят из мелких зерен размером 50–100 нм и равномерно распределены в матрице из ZrO2. Повышение температуры обжига до 1300°С приводит к незначительному росту зерен по сравнению с материалами, обожженными при 1250°С. Полученные материалы имеют однородную и практически беспористую структуру.
Рис. 6.
Микроструктура керамики Z–A–N, обожженной при 1250°С: а – Z–A–N–Co, б – Z–A–N–Fe, в – Z–A–N–Mn.
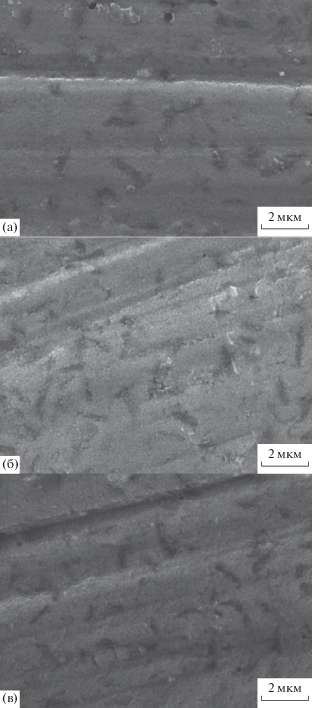
По результатам исследования механических свойств, прочность на изгиб керамики Z–A, обожженной при 1450°С, составляет 530 ± 27 МПа. Керамика состава Z–A–N–Mn при 1250°С характеризуется прочностью на изгиб 420 ± 23 МПа, а при 1300°С – до 500 ± 16 МПа, что превышает прочность образцов, содержащих только Na2Si2O5, практически в 2 раза (рис. 7). Микротвердость таких материалов также является максимальной и возрастает от 9.2 до 10.0 ГПа по мере роста температуры от 1250 до 1300°С (рис. 8). Необходимо отметить, что комплексные добавки, содержащие катионы Co и Fe, также обеспечивают значительный рост прочности и микротвердости по сравнению с Z–A–N.
Рис. 7.
Прочность при трехточечном изгибе керамических материалов Z–A–N, обожженных при 1250–1300°С, в зависимости от состава спекающей добавки.
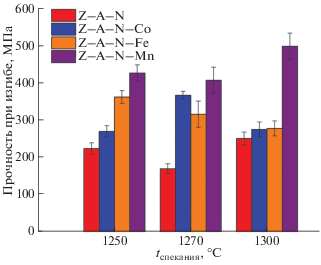
Рис. 8.
Микротвердость керамических материалов Z–A–N, обожженных при 1250–1300°С, в зависимости от состава спекающей добавки.
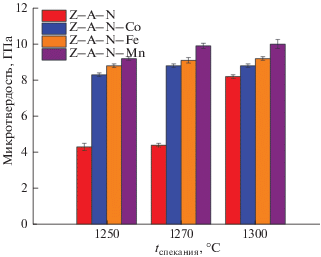
Трещиностойкость материалов состава Z–A, обожженных при 1450°С, составляет 5.20 МПа м1/2, для материалов Z–A–N, обожженных при 1250°С, – 4.04 МПа м1/2. Введение комплексной добавки на основе дисиликата натрия и катионов кобальта (состав Z–A–N–Co) способствует росту K1c до 5.05 МПа м1/2 после обжига при 1250°С. Для керамических образцов Z–A–N–Fe, обожженных при 1250°С, трещиностойкость достигает величины 4.92 МПа м1/2, а прочность при трехточечном изгибе снижается в температурном диапазоне 1250–1300°С от 360 ± 24 до 280 ± 27 МПа. Уменьшение прочности при изгибе обусловлено формированием моноклинной фазы выше 1250°С (рис. 2) и ростом зерен для составов с добавкой. Наибольшую трещиностойкость (до 5.13 МПа м1/2) имеют образцы состава Z–A–N–Mn, обожженные при 1250°С. Высоким показателем трещиностойкости обладают также образцы Z–A–N–Mn, обожженные при 1300°С (5.10 МПа м1/2).
Следует отметить, что полученные значения прочности и трещиностойкости керамики состава Z–A–N–Mn достаточно близки к соответствующим величинам для керамик на основе 3Y–TZP–Al2O3 [14, 18–20]. Авторами [18] получена керамика при 1400°С состава 3Y–TZP–20 об. % Al2O3 с боросиликатным стеклом лантана с прочностью 449.6 МПа и трещиностойкостью 5.92 ± ± 0.51 МПа м1/2.
ЗАКЛЮЧЕНИЕ
В результате проведенных исследований выявлено, что введение комплексных добавок в 3Y–TZP–10Al2O3 (Z–A) оказывает существенное влияние на процессы спекания, обеспечивая открытую пористость менее 0.1% уже при температуре обжига 1250°С. Использование в качестве спекающей добавки Na2Si2O5–0.33% Mn позволило обеспечить отсутствие открытой пористости и механические свойства (прочность 500 ± 16 МПа, трещиностойкость 5.10 МПа м1/2) керамики при температуре 1300°С, сопоставимые с результатами, достигнутыми на обожженных при 1450°С образцах без применения добавок (прочность 530 ± 27 МПа, трещиностойкость 5.20 МПа м1/2). Подобное снижение температуры обжига позволит обеспечить переход на менее дорогостоящее оборудование, в том числе проводить обжиг в печах с силитовыми нагревателями.
Список литературы
Chevalier J., Gremillard L., Virkar A.V. et al. // J. Am. Ceram. Soc. 2009. V. 92. № 9. P. 1901. https://doi.org/10.1111/j.1551-2916.2009.03278.x
Marcomini R.F., Souza D.M.P.F. // Materials Research. 2016. V. 19. № 1. P. 45. https://doi.org/10.1590/1980-5373-MR-2015-0161
Chong F.D., Tan C.Y., Singh R. et al. // Mater. Charact. 2016. V. 120. P. 331. https://doi.org/10.1016/j.matchar.2016.09.001
Flegler A.J., Burye T.E., Yang Q. et al. // Ceram. Int. 2014. V. 40. № 10. P. 16323. https://doi.org/10.1016/j.ceramint.2014.07.071
Folomeikin Y.I., Karachevtsev F.N., Stolyarova V.L. // Russ. J. Inorg. Chem. 2019. V. 64. № 7. P. 934. https://doi.org/10.1134/S0036023619070088
D’yachkov E.P., D’yachkov P.N. // Russ. J. Inorg. Chem. 2019. V. 64. № 5. P. 637. https://doi.org/10.1134/S003602361905005X
Goldberg M., Obolkina T., Smirnov S. et al. // Materials. 2020. V. 13. № 12. P. 2789. https://doi.org/10.3390/ma13122789
Obolkina T.O., Goldberg M.A., Smirnov S.V. et al. // Dokl. Chem. 2020. V. 493. № 1. C. 99. https://doi.org/10.1134/S0012500820070010
Obolkina T.O., Goldberg M.A., Smirnov S.V. et al. // Inorg. Mater. 2020. T. 56. № 2. C. 182. https://doi.org/10.1134/S0020168520020156
Santos C., Souza R.C., Habibe A.F. et al. // Mater. Sci. Eng., A. 2008. V. 478. № 1–2. P. 257. https://doi.org/10.1016/j.msea.2007.06.009
Tekeli S., Erdogan M., Aktas B. // Mater. Sci. Eng., A. 2004. V. 386. № 1-2. P. 1. https://doi.org/10.1016/j.msea.2004.07.057
Lakusta M., Danilenko I., Konstantinova T. et al. // Nanoscale Res. Lett. 2017. V. 12. № 1. P. 1. https://doi.org/10.1186/s11671-017-2178-6
Ghyngazov S.A., Shevelev S.A. // J. Therm. Anal. Calorim. 2018. V. 134. № 1. P. 45. https://doi.org/10.1007/s10973-018-7249-0
Rahimi S., SharifianJazi F., Esmaeilkhanian A. et al. // Ceram. Int. 2020. V. 46. № 8. P. 10910. https://doi.org/10.1016/j.ceramint.2020.01.105
Aravindan S., Krishnamurthy R. // Mater. Lett. 1999. V. 38. № 4. P. 245. https://doi.org/10.1016/S0167-577X(98)00166-9
Belykh D.B., Zhabrev V.A., Zaitsev S.V. // Glass Phys. Chem. 2003. V. 29. № 1. P. 75. https://doi.org/10.1023/A:1022365927875
Баринов С.М., Шевченко В.Я. Прочность технической керамики. М.: Наука, 1996. 159 с.
Sheng X.J., Xu H., Jin Z.H. et al. // Mater. Lett. 2004. V. 58. № 11. P. 1750. https://doi.org/10.1016/j.matlet.2003.10.062
Wu Z.K., Li N., Jian C. et al. // Ceram. Int. 2013. V. 39. № 6. P. 7199. https://doi.org/10.1016/j.ceramint.2013.02.065
Jing Q., Bao J., Ruan F. // Ceram. Int. 2019. V. 45. № 5. P. 6066. https://doi.org/10.1016/j.ceramint.2018.12.078
Дополнительные материалы отсутствуют.
Инструменты
Журнал неорганической химии