Журнал неорганической химии, 2021, T. 66, № 8, стр. 1150-1155
Синтез, фазовый состав и свойства керамических материалов AlMgB14, полученных методом искрового плазменного спекания
П. Ю. Никитин a, *, И. А. Жуков a, М. С. Болдин b, С. Н. Перевислов c, В. Н. Чувильдеев b
a Томский государственный университет
634050 Томск, пр-т Ленина, 36, Россия
b Нижегородский государственный университет им. Н.И. Лобачевского, Научно-исследовательский физико-технический институт
603950 Нижний Новгород, пр-т Гагарина, 23, корп. 3, Россия
c Институт химии силикатов им. И.В. Гребенщикова РАН
199034 Санкт-Петербург, наб. Макарова, 2, Россия
* E-mail: upavelru@yandex.ru
Поступила в редакцию 04.02.2021
После доработки 11.03.2021
Принята к публикации 12.03.2021
Аннотация
Методом искрового плазменного спекания порошковой смеси Al12Mg17-B при температурах спекания 1300 и 1400°C получены материалы на основе AlMgB14. Проведены исследования фазового состава, структуры и свойств материалов. Согласно результатам рентгеноструктурных исследований, в процессе искрового плазменного спекания формируется фаза AlMgB14 и шпинель MgAl2O4. Содержание фазы AlMgB14 в полученных материалах составляет ~95 мас. %. При температуре спекания 1400°C твердость и относительная плотность образца составляют 30.1 ГПа и 90.3% соответственно. Установлено, что основным источником кислорода в порошковой смеси является оксидная пленка B2O3 на поверхности порошка бора. Таким образом, при использовании интерметаллического порошка Al12Mg17 в качестве исходного прекурсора шпинель MgAl2O4 формируется в результате реакции интерметаллидов AlxMgy и оксида B2O3.
ВВЕДЕНИЕ
AlMgB14, известный также как борид алюминия-магния (БАМ), – орторомбическое соединение на основе связанных алюминием и магнием икосаэдров бора B12, обладающее рядом потенциально значимых для промышленного использования свойств. Хотя первые исследования монокристаллов AlMgB14 проводились с 1969 г. [1, 2], о физико-механических свойствах поликристаллических материалов AlMgB14 стало известно лишь в 2000 г. Группой ученых лаборатории Ames под руководством B. Cook было обнаружено, что поликристаллические материалы на основе AlMgB14, полученные методом горячего прессования механоактивированных смесей порошков алюминия, магния и бора, имеют значение твердости 32 ГПа (в композитах с 30 мас. % TiB2 твердость достигает 46 ГПа [3]), низкий коэффициент трения, равный 0.02 [4], и коэффициент теплового расширения (КТР), близкий к КТР стали [5]. Благодаря уникальному сочетанию этих свойств поликристаллические материалы на основе AlMgB14 стали объектом активных исследований ученых из Америки, Китая, Японии и стран Европы.
Обычно для получения AlMgB14 порошки алюминия, магния и бора различной дисперсности смешиваются в атомном соотношении Al : Mg : B = = 1 : 1 : 14, а затем спекаются методами высокотемпературного вакуумного спекания [6, 7], горячего прессования [3, 8–10], искрового плазменного спекания [11, 12]. Для интенсификации процессов синтеза AlMgB14 используется предварительная механическая активация порошковой смеси [13]. Для получения композиционного порошка AlMgB14-TiB2 авторами [14] был также применен метод термохимически сопряженного самораспространяющегося высокотемпературного синтеза (СВС). После СВС-синтеза полученный порошок был консолидирован методом искрового плазменного спекания.
Основная проблема получения БАМ связана с формированием примесных фаз, в особенности шпинели MgAl2O4, значительно снижающей свойства AlMgB14 [15]. В процессе спекания AlMgB14 шпинель формируется по реакции кислорода с алюминием и магнием. Основным источником кислорода являются оксидные пленки на поверхности частиц бора (B2O3) и алюминия (Al2O3). Учеными из Словении предложено использовать в качестве исходных прекурсоров порошки боридов AlB12 и MgB2 вместо порошков алюминия, магния и бора [7]. Ими обнаружено, что для образования AlMgB14 необходимо наличие свободного бора в смеси, поэтому получение БАМ из порошков AlB12 и MgB2 оказалось безрезультатным. Синтез материалов на основе AlMgB14 из смесей AlB2, MgB2 и бора проведен в [6]. В результате получены материалы с содержанием фазы AlMgB14 ~85 мас. %. Во избежание контакта исходных порошков с кислородом синтез исходной порошковой смеси и ее спекание осуществляли в условиях высокого вакуума. В работе также предложено проводить предварительный высокотемпературный отжиг порошка бора в вакууме. Это позволило сократить содержание шпинели до 3.3 мас. %, а содержание фазы AlMgB14 в полученном материале составило 92.6 мас. %. В этой связи особый интерес представляет использование интерметаллических порошков алюминия и магния в качестве исходного прекурсора для получения материалов на основе AlMgB14. Это может повысить эффективность получения AlMgB14, поскольку магний не испаряется из соединения, как при использовании отдельных порошков. Для компенсации испарения магния из порошковой смеси Al-Mg-B в процессе спекания AlMgB14 авторы [16] предложили использовать смесь с избытком магния, в которой атомное соотношение Al : Mg : B = 1 : 6 : 14. В полученных материалах было обнаружено высокое содержание фазы AlMgB14, однако предложенный авторами метод требует использования порошков с минимальным содержанием примесей и спекания в условиях высокого вакуума, что значительно увеличивает трудоемкость и стоимость изготовления. Более того, использование порошка интерметаллического сплава для синтеза БАМ может снизить содержание шпинельной фазы в спеченных образцах. Это связано с тем, что оксидная пленка интерметаллического соединения не такая плотная, как у алюминия [17]. В нашей предыдущей работе [18] предложен механизм формирования AlMgB14 в процессе горячего прессования порошковой смеси интерметаллического сплава Al12Mg17 и бора. Установлено, что для достижения плотности материала, близкой к теоретической, и увеличения содержания фазы AlMgB14 необходимо оптимизировать процесс спекания порошковой смеси. При этом по сравнению с технологиями высокотемпературного вакуумного спекания и горячего прессования метод искрового плазменного спекания является более эффективным как за счет сокращения длительности спекания, так и за счет возможности точного контроля и управления параметрами процесса: температурой спекания, временем изотермической выдержки, скоростью нагрева и давлением [19, 20].
Цель настоящей работы – исследование фазового состава, структуры и физико-механических свойств материалов AlMgB14, полученных методом искрового плазменного спекания порошковой смеси Al12Mg17-B.
ЭКСПЕРИМЕНТАЛЬНАЯ ЧАСТЬ
В качестве исходных веществ использовали порошок интерметаллического сплава Al12Mg17 и порошок аморфного черного бора. Интерметаллический порошок получали сплавлением слитков алюминия и магния чистотой 99.9% в графитовом тигле в среде аргона. Для этого на первом этапе расплавляли 1 кг алюминия при температуре 720°C, затем в расплав алюминия добавляли магний в массовом соотношении Al : Mg = 1 : 1. Для достижения гомогенности расплава смешивание осуществляли с помощью устройства, описанного в [21]. Полученный расплав выливали в стальной кокиль при температуре 670°C с одновременным вибрационным воздействием на кристаллизатор [22]. На втором этапе полученный сплав механически измельчали в щековой дробилке, а затем подвергали обработке в планетарной мельнице в среде аргона. В качестве мелющих тел использовали стальные шары диаметром 8.7 мм. Массовое соотношение шаров к порошковой смеси составляло 2 : 1, частота вращения барабанов – 12 Гц. Механическую обработку проводили в течение 5 ч.
Полученный порошок интерметаллического сплава Al12Mg17 (средний размер частиц 20 мкм) смешивали с аморфным черным бором (средний размер частиц 2.1 мкм) в атомном соотношении Al12Mg17 : B = 2 : 14. Полученную смесь механически активировали в планетарной мельнице в среде аргона с частотой вращения барабанов 14 Гц. В качестве мелющих тел использовали стальные шары диаметром 4.5 мм. Массовое соотношение мелющих тел к порошковой смеси составляло 3 : 1, продолжительность механической активации 3 ч.
Спекание керамических образцов из полученной порошковой смеси Al12Mg17-B проводили методом искрового плазменного спекания (установка DR. SINTER model SPS-625 Spark Plasma Sintering System) в графитовой пресс-форме диаметром 12.8 мм. Для отделения порошковой навески от стенок графитовой пресс-формы использовали графитовую бумагу. Для обеспечения однородности температурного поля внутри пресс-формы при спекании и уменьшения риска возникновения остаточных термических напряжений в спекаемом образце при остывании графитовую матрицу покрывали графитовым войлоком толщиной 4 мм. Порошковую смесь спекали при давлении 70 МПа, скорости нагрева 50 град/мин и температурах 1300 и 1400°C. После завершения спекания подачу тока прекращали, образцы охлаждали в режиме выключенной установки. Для удаления с поверхности образца остатков графитовой бумаги использовали отжиг в муфельной печи при температуре 700°C в течение 2–4 ч. Для проведения дальнейших исследований поверхность образца полировали при помощи станка Buehler Ecomet 250 алмазными пастами с финишной обработкой на пасте 5/3.
Для оценки параметров микроструктуры полученных образцов и их элементного состава использовали метод сканирующей электронной микроскопии и энергодисперсионного анализа на растровом электронном микроскопе JEOL JSM-6490 с рентгеновским микроанализатором Oxford Instruments INCA-350. Зеренную структуру оценивали по фрактографии излома. Рентгенофазовый анализ образцов проводили с помощью рентгеновского дифрактометра Shimadzu XRD-7000 при следующих параметрах сканирования: диапазон углов 20°–90°; шаг сканирования 0.04°; длительность экспозиции в каждой точке 3 c. Качественный фазовый анализ выполняли в программе Diffrac.EVA по полученным в ходе экспериментов дифрактограммам с использованием базы данных PDF 4. Количественный фазовый анализ проводили по методу Ритвельда с моделированием полученных дифрактограмм в программе Topas. Количество кислорода в исходных порошках определяли с помощью прибора Leco ONH. Плотность спеченных образцов измеряли методом гидростатического взвешивания в дистиллированной воде. Твердость по Виккерсу (HV) определяли по измерению длин диагоналей отпечатка алмазной пирамидки (индентора) на полированной поверхности образца при нагрузке 1 кг (9.8 Н). Время нагружения составляло 10 с.
РЕЗУЛЬТАТЫ И ОБСУЖДЕНИЕ
Микроструктура поверхности разрушения спеченных образцов приведена на рис. 1. Искровое плазменное спекание порошковой смеси Al12Mg17-B приводит к формированию плотной зеренной структуры. Согласно результатам элементного анализа (рис. 2), основными элементами в полученных образцах являются алюминий, магний, бор и кислород. Средний размер зерен в спеченной керамике составляет 3 мкм.
Рис. 1.
РЭМ-изображения поверхности излома образцов, спеченных при температурах 1300 (а, б) и 1400°C (в, г).
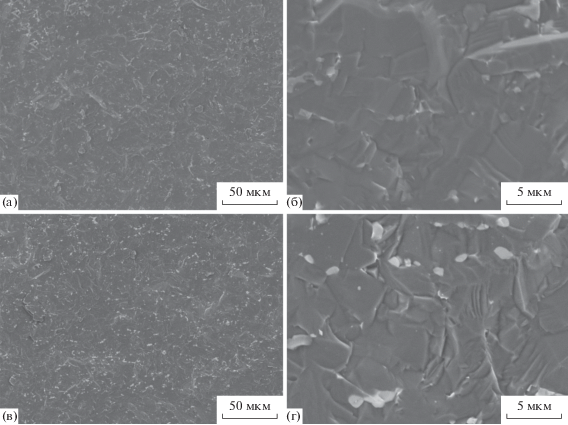
Рис. 2.
Данные качественного рентгеноспектрального микроанализа образца, спеченного при температуре 1300°C.
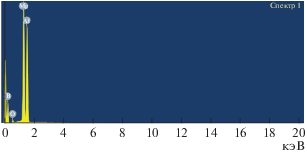
Согласно исследованиям фазового состава полученных образцов керамики (рис. 3), в процессе искрового плазменного спекания формируются фазы AlMgB14 и MgAl2O4. Количественный анализ с использованием метода Ритвельда показал, что содержание фазы AlMgB14 в полученных образцах составляет ~95 мас. % независимо от температуры спекания. Относительная плотность образца, полученного при температуре спекания 1300°C, составляет 96.3%. Увеличение температуры спекания до 1400°C приводит к повышению относительной плотности образца до 99.3%.
Результаты измерения твердости приведены в табл. 1. Согласно полученным данным, средняя микротвердость образца, спеченного при температуре 1300°C, составляет 22.2 ГПа. С увеличением температуры спекания до 1400°C средняя микротвердость полученного образца увеличивается до 30.1 ГПа.
Таблица 1.
Результаты измерения твердости спеченных образцов
tспек, °C | Микротвердость HV, ГПа | |||||||||
---|---|---|---|---|---|---|---|---|---|---|
№ измерения | ||||||||||
1 | 2 | 3 | 4 | 5 | 6 | 7 | 8 | 9 | 10 | |
1300 | 27.1 | 26.8 | 25.2 | 22.5 | 21.8 | 21.8 | 20.0 | 19.9 | 18.6 | 18.0 |
1400 | 32.4 | 32.3 | 31.8 | 30.9 | 30.7 | 29.6 | 29.0 | 28.9 | 28.5 | 27.0 |
Следует отметить, что спекание при температуре 1400°C позволяет получать керамику с наибольшими значениями микротвердости (30.1 ГПа) и плотности (99.3%). Полученные результаты согласуются с данными работ [3, 6, 7]. При этом на дифрактограмме образца, полученного при температуре 1300°C (рис. 3а), наблюдается более высокий фон при малых углах дифракции, по-видимому, указывающий на содержание аморфных боридных соединений или аморфного бора. В работе [18] установлено, что в процессе горячего прессования AlMgB14 формируется из промежуточной фазы диборида Al0.5Mg0.5B2. При этом на первой стадии происходит прямое борирование интерметаллического соединения до диборидов AlxMg1 –xB2, тогда как при использовании отдельных порошков сначала происходит образование интерметаллического соединения AlxMgy, а затем борирование. В табл. 2 приведены результаты измерения содержания кислорода в исходных порошках интерметаллического сплава Al12Mg17 и бора. Установлено, что основным источником кислорода является порошок бора (1.1 мас. %). Таким образом, несмотря на равное содержание фазы AlMgB14 в полученных образцах керамики, обнаруженные аморфные структуры в образце, спеченном при 1300°C, могут являться источником формирования шпинели MgAl2O4. В процессе искрового плазменного спекания шпинель MgAl2O4 формируется в результате реакции между интерметаллическим сплавом AlxMgy и оксидной пленкой B2O3 на поверхности свободного бора.
Таблица 2.
Результаты исследований содержания кислорода
Порошок | Содержание кислорода, мас. % |
---|---|
Бор | 1.1 |
Al12Mg17 | 0.07 |
Таким образом, использование интерметаллического сплава Al12Mg17 в качестве исходного прекурсора имеет ряд преимуществ. Во-первых, плотность образца, полученного методом искрового плазменного спекания смеси Al12Mg17-B при температуре 1400°C, близка к теоретической. Во-вторых, согласно результатам элементного анализа (табл. 2), Al12Mg17 меньше подвержен окислению, чем отдельные порошки алюминия и магния. В-третьих, Al12Mg17 не является источником кислорода, следовательно, не может служить источником формирования шпинели (при использовании отдельных порошков алюминия и магния шпинель формируется в результате реакции между оксидами алюминия и магния (Al2O3 + + MgO → MgAl2O4)).
ЗАКЛЮЧЕНИЕ
В результате проведенного исследования получены материалы на основе AlMgB14 методом искрового плазменного спекания порошковой смеси Al12Mg17-B. Обнаружено, что увеличение температуры спекания порошковой смеси Al12Mg17-B от 1300 до 1400°C приводит к повышению относительной плотности (99.3%) и твердости (30.1 ГПа) образца. При этом уменьшается содержание свободного бора. Показана эффективность использования интерметаллического порошка Al12Mg17 в качестве исходного прекурсора вместо отдельных порошков алюминия и магния. Порошок интерметаллического сплава меньше подвержен окислению, чем отдельные порошки алюминия и магния. Установлено, что основным источником кислорода является порошок бора. В процессе искрового плазменного спекания шпинель MgAl2O4 формируется в результате реакции между оксидной пленкой B2O3 и интерметаллидами AlxMgy.
Список литературы
Matkovich V., Economy J. // Acta Crystallogr., Sect. B. 1970. V. 26. № 5. P. 616. https://doi.org/10.1107/S0567740870002868
Higashi I., Ito T. // J. Less Common. Metals. 1983. V. 92. № 2. P. 239. https://doi.org/10.1016/0022-5088(83)90490-3
Cook B.A., Harringa J.L., Lewis T.L. et al. // Scripta Mater. 2000. V. 42. № 6. https://doi.org/10.1016/S1359-6462(99)00400-5
Cook B.A., Harringa J.L., Anderegg J. et al. // Surf. Coat. Technol. 2010. V. 205. № 7. P. 2296. https://doi.org/10.1016/j.surfcoat.2010.09.007
Russell A.M., Cook B.A., Harringa J.L. et al. // Scripta Mater. 2002. V. 46. № 9. P. 629. https://doi.org/10.1016/S1359-6462(02)00034-9
Xie Z., DeLucca V., Haber R.A. et al. // Adv. Appl. Ceram. 2017. V. 116. № 6. P. 341. https://doi.org/10.1080/17436753.2017.1317116
Kevorkijan V., Škapin S.D., Jelen M. et al. // J. Eur. Ceram. Soc. 2007. V. 27. № 2–3. P. 493. https://doi.org/10.1016/j.jeurceramsoc.2006.04.114
Liu W., Wu Y.T., Mao S.H. et al. // J. Mater. Eng. Perform. 2013. V. 22. № 4. P. 983. https://doi.org/10.1007/s11665-012-0370-5
Zhuang L., Lei Y., Chen S. et al. // Appl. Surf. Sci. 2015. V. 328. P. 125. https://doi.org/10.1016/j.apsusc.2014.11.127
Liu W., Miao Y., Meng Q. et al. // J. Mater. Sci. Technol. 2013. V. 29. № 1. P. 77. https://doi.org/10.1016/j.jmst.2012.12.008
Nikitin P.Y., Zhukov I.A., Vorozhtsov A.B. // J. Mater. Res. Technol. 2021. V. 11. P. 687. https://doi.org/10.1016/j.jmrt.2021.01.044
Roberts D.J., Zhao J., Munir Z.A. // Int. J. Refract. Met. Hard Mater. 2009. V. 27. № 3. P. 556. https://doi.org/10.1016/j.ijrmhm.2008.07.009
Жуков И.А., Зиатдинов М.Х., Дубкова Я.А. и др. // Известия высших учебных заведений. Физика. 2018. Т. 61. № 8. С. 87. [Zhukov I.A., Ziatdinov M.K., Dubkova Y.A. et al. // Russ. Phys. J. 2018. V. 61. № 8. P. 1466.] https://doi.org/10.1007/s11182-018-1557-5
Nikitin P.Y., Zhukov I.A., Matveev A.E. et al. // Ceram. Int. 2020. V. 46. № 14. P. 22733. https://doi.org/10.1016/j.ceramint.2020.06.039
Lewis T.L., Cook B.A., Harringa J.L. et al. // Mater. Sci. Eng., A. 2003. V. 351. № 1–2. P. 117. https://doi.org/10.1016/S0921-5093(02)00835-3
Li C.S., Yang F., Yan G. et al. // J. Alloys Compd. 2014. V. 587. P. 790. https://doi.org/10.1016/j.jallcom.2013.11.013
Комаров В.Ф., Комарова М.В., Ворожцов А.Б. и др. // Известия высших учебных заведений. Физика. 2012. Т. 55. № 10. С. 13. [Komarov V., Komarova M.V., Vorozhtsov A.B. et al. // Russ. Phys. J. 2013. V. 55. № 10.] https://doi.org/10.1007/s11182-013-9931-9
Zhukov I.A., Nikitin P.Y., Vorozhtsov A.B. et al. // Mater. Today Comm. 2020. V. 22. P. 100848. https://doi.org/10.1016/j.mtcomm.2019.100848
Чувильдеев В.Н., Болдин М.С., Дятлова Я.Г. и др. // Журн. неорган. химии. 2015. Т. 60. № 8. С. 1088. [Chuvil’deev V.N., Boldin M.S., Dyatlova Ya.G. et al. // Russ. J. Inorg. Chem. 2015. V. 60. № 8. P. 987.] https://doi.org/10.1134/S0036023615080057
Шичалин О.О., Фролов К.Р., Буравлев И.Ю. и др. // Журн. неорган. химии. 2020. Т. 65. № 8. С. 1119. [Shichalin O.O., Frolov K.R., Buravlev I.Y. et al. // Russ. J. Inorg. Chem. 2020. V. 65. № 8. P. 1245. https://doi.org/10.1134/S0036023620080148]
Vorozhtsov S., Minkov L., Dammer V. et al. // JOM. 2017. V. 69. № 12. P. 2653. https://doi.org/10.1007/s11837-017-2594-1
Promakhov V.V., Khmeleva M.G., Zhukov I.A. et al. // Metals. 2019. V. 9. № 1. P. 87. https://doi.org/10.3390/met9010087
Дополнительные материалы отсутствуют.
Инструменты
Журнал неорганической химии