Журнал неорганической химии, 2019, T. 64, № 11, стр. 1229-1236
Получение функционально-градиентного керамического материала SiC-TiC золь-гель методом
Е. П. Симоненко 1, *, Н. П. Симоненко 1, В. А. Николаев 1, Е. К. Папынов 2, 3, О. О. Шичалин 2, 3, Е. А. Гридасова 3, В. Ю. Майоров 3, А. В. Гришин 3, В. Г. Севастьянов 1, Н. Т. Кузнецов 1
1 Институт общей и неорганической химии им. Н.С. Курнакова РАН
119991 Москва, Ленинский пр-т, 31, Россия
2 Институт химии ДВО РАН
690022 Владивосток, пр-т 100-летия Владивостока, 159, Россия
3 Дальневосточный федеральный университет
690091 Владивосток, ул. Суханова, 8, Россия
* E-mail: ep_simonenko@mail.ru
Поступила в редакцию 24.04.2019
После доработки 30.04.2019
Принята к публикации 13.05.2019
Аннотация
Изучен процесс получения функционально-градиентных композиционных материалов SiC-TiC, перспективных для применения в авиакосмической промышленности в качестве сравнительно низкоплотных материалов, при золь-гель синтезе высокодисперсной матрицы карбида титана в объеме порового пространства SiC-каркасов. Показано, что путем изменения состава координационной сферы прекурсоров можно влиять на характер распределения матрицы TiC в объеме SiC-каркаса. Установлено, что после восьми циклов гидролиза титансодержащих прекурсоров в присутствии фенолформальдегидной смолы с последующей карбонизацией и карботермией (1400°С, динамический вакуум, 2 ч) прирост массы образцов значительно различается: для прекурсора [Ti(OC4H9)2.05(O2C5H7)1.95], более чувствительного к влаге, он составляет 23%, а для комплекса [Ti(OC4H9)1.95(O2C5H7)2.05] – 37%. При этом в первом случае преимущественно происходит уплотнение приповерхностных областей материала. Отмечено, что с повышением количества модифицирующей фазы TiC увеличивается прочность при сжатии и снижается удельная площадь поверхности (по данным низкотемпературной сорбции азота и ртутной порометрии). Полученный градиент состава керамики SiC-TiC по глубине подтвержден методом рентгеновской компьютерной микротомографии: общая пористость приповерхностных регионов керамики различается в 2.9 раз.
ВВЕДЕНИЕ
Пористые керамические материалы на основе карбида кремния находят широкое и разнообразное применение благодаря совокупности таких свойств, как высокая температура разложения и теплопроводность, неплохие механические свойства и наибольшая среди тугоплавких карбидов окислительная стойкость. Так, повышенная теплопроводность необходима для применения карбидокремниевых материалов в качестве носителей катализаторов при сильно экзотермических реакциях [1–5]. Коррозионная стойкость SiC востребована при получении керамических фильтров для расплавов и раскаленных газов [4, 6–10]. Благодаря хорошим механическим характеристикам, биосовместимости и заданной пористости (особенно при наличии анизотропных каналов) SiC-керамика имеет перспективы при создании протезов и имплантов [11–14]. Сочетание высокой теплопроводности, низкого коэффициента термического расширения, окислительной стойкости и оптических свойств позволяет предложить карбидокремниевую керамику с высокой пористостью в качестве поглотителя солнечной энергии [15–18].
Широчайшее применение карбидокремниевых керамических и керамоматричных материалов в авиа- и ракетостроении, двигателестроении, атомной энергетике обусловлено также и низкой плотностью карбида кремния – 3.2 г/см3 [19]. Повышение пористости SiC-керамики позволяет дополнительно снизить плотность соответствующих деталей, однако отрицательно сказывается на механических свойствах.
Немногочисленные работы по введению в состав карбидокремниевой керамики карбида титана, в том числе путем совместного синтеза нанокомпозитов золь-гель методом [20, 21], показали, что это позволяет повысить трещиностойкость и прочность на изгиб [22], однако при этом происходит неизбежное увеличение плотности.
Создание функционально-градиентных материалов с градиентом плотности по глубине, для которых преимущественно модифицируется приповерхностная область, а состав и структура в объеме изменяются незначительно [23, 24], позволяет решить проблему значительного повышения плотности керамического материала при введении второго компонента в поры исходного образца карбидокремниевой керамики.
Золь-гель технология благодаря наличию растворной стадии, которая может быть применена для многократной пропитки исходного пористого материала SiC-керамики, очень эффективна при создании такого рода материалов, модифицированных как оксидными, так и карбидными компонентами. В наших предыдущих работах [25–28] показано, что благодаря контролируемому гидролизу металлсодержащих прекурсоров в присутствии фенолформальдегидной смолы (источника углерода) после гелеобразования и карбонизации формируются высокодисперсные и реакционноспособные составы MOx–C (M = Si, Ta, Ti, Zr, Hf), позволяющие осуществить карботермический синтез при минимальных температурах.
Известно [29], что структура титансодержащего прекурсора самым непосредственным образом влияет на скорость процесса формирования геля. Это выражается в различной кинетике образования вязких гелей, которые становятся неспособными к дальнейшей пропитке более глубоких слоев исходного пористого карбидокремниевого каркаса [23, 24].
Целью настоящей работы является изучение влияния состава прекурсоров – координационных соединений титана класса алкоксоацетилацетонатов – на структуру получаемых функционально-градиентных композиционных материалов состава SiC-TiC, фазовый состав и объемное взаимное распределение фаз карбида кремния, карбида титана и порового пространства.
ЭКСПЕРИМЕНТАЛЬНАЯ ЧАСТЬ
Используемые реактивы: тетрабутоксититан Ti(OC4H9)4 (99%), ацетилацетон C5H8O2 “ч.”, н-бутанол C4H10O “ос. ч.”, лак бакелитовый ЛБС-1 (применялся раствор в 1-бутаноле).
Получение раствора гетеролигандных гидролитически активных комплексов состава [Ti(OC4H9)2.05(O2C5H7)1.95] (1) и [Ti(OC4H9)1.95(O2C5H7)2.05] (2) осуществляли добавлением к тетрабутоксититану необходимого количества ацетилацетона. Это приводило к частичному замещению алкоксильных групп хелатными фрагментами и уменьшению гидролитической активности комплексов. Затем в качестве растворителя добавляли 1-бутанол в объеме, позволяющем получить с(Ti4+) = 0.75 моль/л.
Для изготовления пористых SiC-каркасов c применением золь-гель метода синтезировали нанокристаллический порошок соответствующего состава. Карботермический синтез проводили при температуре 1550°С в течение 5 ч в условиях динамического вакуума. Керамические материалы получали на прессе горячего прессования Thermal Technology Inc. HP20-3560-20 по методике, описанной в [30].
Изменение реологических свойств коллоидного раствора во время гидролиза прекурсоров в присутствии фенолформальдегидной смолы и поликонденсации изучали с помощью ротационного вискозиметра Брукфильда Fungilab Smart L (скорость сдвига 100 об./мин, шпиндель L2).
Рентгенофазовый анализ проводили на рентгеновском дифрактометре Bruker D8 Advance (излучение CuKα, разрешение 0.02°).
Изучение структуры пор в интервале 1–200 нм и определение удельной площади поверхности осуществляли по методу низкотемпературной сорбции азота (77 K) на измерителе удельной поверхности ASAP 2020 V3.04H (Micromeritics, USA).
Распределение по размеру более крупных пор исследовали методом ртутной порометрии на поромере AutoPore IV 9500 V1.07 (Micromeritics, USA).
Предел прочности при сжатии полученных образцов керамики определяли на разрывной машине Shimadzu Autograph AG-X plus (50 кН).
Компьютерная микротомография выполнена на настольном рентгеновском микротомографе SkyScan 1172 с компьютерным кластером. Трехмерные модели образца, отражающие его внутреннее строение, построены с использованием специализированного программного обеспечения, позволяющего получать различные срезы виртуальной модели образца и выполнять их математическую обработку.
РЕЗУЛЬТАТЫ И ОБСУЖДЕНИЕ
Для создания функционально-градиентных материалов состава SiC-TiC путем модифицирования порового пространства пористых карбидокремниевых керамических материалов использовали два раствора титансодержащих прекурсоров с различным соотношением алкоксо- и ацетилацетонатных лигандов: [Ti(OC4H9)2.05(O2C5H7)1.95] (1) и [Ti(OC4H9)1.95(O2C5H7)2.05] (2). Растворы комплексов титана в заданных соотношениях смешивали с раствором фенолформальдегидной смолы, которая после гидролиза, гелеобразования, сушки и карбонизации являлась источником необходимого углерода для протекания карботермического синтеза TiC. Далее инициировали гидролиз прекурсоров путем введения раствора воды в этаноле, что с течением времени приводило (за счет реакций поликонденсации) к формированию титан-полимерсодержащего геля. Полученными непосредственно после добавления гидролизующего состава коллоидными растворами (до их гелеобразования) пропитывали при пониженном давлении образцы пористой SiC-керамики, изготовленной путем горячего прессования нанокристаллического порошка карбида кремния.
Поскольку в прекурсоре 1 содержание хелатных лигандов меньше, гидролитическая активность данного комплекса в присутствии полимерного источника углерода (фенолформальдегидной смолы), а следовательно, и скорость формирования геля выше. При концентрации титана c(Ti4+) = 0.75 моль/л и соотношениях n(H2O)/n(Ti4+) = 1, n(HCOOH)/n(Ti4+) = 2 (муравьиную кислоту добавляли для предотвращения высаливания фенолформальдегидной смолы) в результате процессов гидролиза и поликонденсации время достижения динамической вязкости 40 сП для первой системы составило 22 мин, для второй – 45 мин (рис. 1).
Рис. 1.
Кривые изменения динамической вязкости во времени при гидролизе в присутствии фенолформальдегидной смолы титансодержащих прекурсоров [Ti(OC4H9)2.05(O2C5H7)1.95] (1) и [Ti(OC4H9)1.95(O2C5H7)2.05] (2).
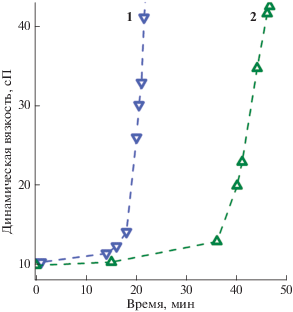
Столь значительная разница в реакционной способности прекурсоров должна приводить к тому, что из-за динамического роста вязкости глубина проникновения в объем образца титансодержащих составов, а также пористость приповерхностной модифицируемой области должны существенно различаться (рис. 2).
Рис. 2.
Схематическая зависимость глубины модифицирования приповерхностной области пористых керамических материалов при создании функционально-градиентных материалов от чувствительности к влаге металлсодержащего прекурсора.
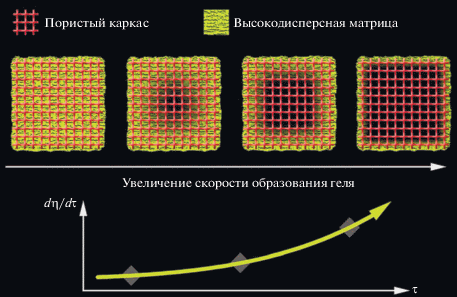
После гелеобразования модифицированные керамические образцы сушили до прекращения изменения массы, подвергали карбонизации в условиях динамического вакуума, в результате чего в порах SiC-керамики образовывался исходный химически активный состав TiO2-C, а далее осуществляли карботермический синтез при температуре 1400°С (выдержка в течение 2 ч). В рамках эксперимента цикл “гидролиз–пропитка–сушка–карбонизация–карботермический синтез” выполнен 8-кратно.
Прирост массы образцов (рис. 3) свидетельствует о том, что при применении алкоксоацетилацетоната титана 1, для которого характерно более быстрое гелеобразование, заполнение порового пространства карбидокремниевых образцов происходит менее активно, т.е. каналы и поры SiC-керамики в результате гидролиза с гелеобразованием блокируются на меньшей глубине, создавая препятствия для дальнейшей пропитки материала титан-полимерсодержащим коллоидным раствором. При этом значительные отличия в плотности наблюдаются уже на третьем цикле пропитки.
Рис. 3.
Прирост массы образцов SiC-керамики за счет введения TiC-матрицы в зависимости от количества циклов пропитки и состава прекурсора: [Ti(OC4H9)2.05(O2C5H7)1.95] (1) и [Ti(OC4H9)1.95(O2C5H7)2.05] (2).
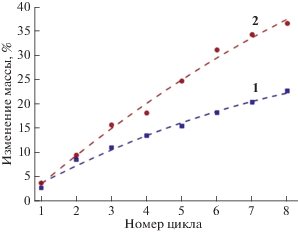
Рентгенофазовый анализ образцов (рис. 4) показал, что на поверхности в обоих случаях образуется монокарбид титана – помимо рефлексов кубического карбида кремния [31] появляются рефлексы и фазы TiC [32], примесных фаз не наблюдается.
Рис. 4.
Рентгенограммы поверхности образцов SiC-TiC, полученных после модификации пористых SiC-каркасов с применением прекурсоров [Ti(OC4H9)2.05(O2C5H7)1.95] (1) и [Ti(OC4H9)1.95(O2C5H7)2.05] (2).
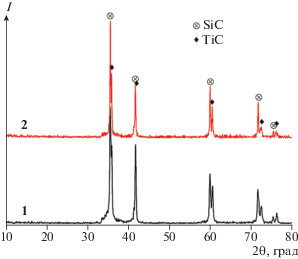
Для полученных композиционных материалов определена прочность на сжатие, а также удельная площадь поверхности и средний размер пор с помощью сорбции азота и ртутной порометрии (табл. 1). Установлено, что с увеличением количества введенной TiC-матрицы в объем пористого SiC-каркаса закономерно возрастают прочностные характеристики и снижаются удельная площадь поверхности и размер пор, определенный методом низкотемпературной сорбции азота. Вид изотерм адсорбции и десорбции азота (рис. 5) свидетельствует о том, что при увеличении количества введенной TiC-матрицы происходит уменьшение объема пор при сохранении их формы. Ртутная порометрия (рис. 6) также показала некоторое снижение пористости при использовании прекурсора 2, для которого свойственно более медленное гелеобразование при гидролизе. При этом средний размер пор остается неизменным (~250–260 нм).
Таблица 1.
Предел прочности при сжатии (σ), удельная площадь поверхности, определенная по данным низкотемпературной сорбции азота (${{S}_{{{{{\text{N}}}_{2}}}}}$) и ртутной порометрии (SHg), а также соответствующие величины средних диаметров пор (D) полученной керамики в зависимости от условий заполнения
Прекурсор | σ, МПа | ${{S}_{{{{{\text{N}}}_{2}}}}},$ м2/г | $D_{{{{{\text{N}}}_{2}}}}^{*},$ нм | SHg, м2/г | DHg, нм |
---|---|---|---|---|---|
[Ti(OC4H9)2.05(O2C5H7)1.95] | 27 | 3.3 | 5.1 | 5.4 | 254 |
[Ti(OC4H9)1.95(O2C5H7)2.05] | 31 | 2.7 | 4.1 | 4.7 | 255 |
Рис. 5.
Кривые низкотемпературной адсорбции и десорбции азота для керамических материалов SiC-TiC, полученных после модификации пористых SiC-каркасов с применением прекурсоров [Ti(OC4H9)2.05(O2C5H7)1.95] (а) и [Ti(OC4H9)1.95(O2C5H7)2.05] (б); на врезках представлены соответствующие кривые распределения пор по размерам (BJH).
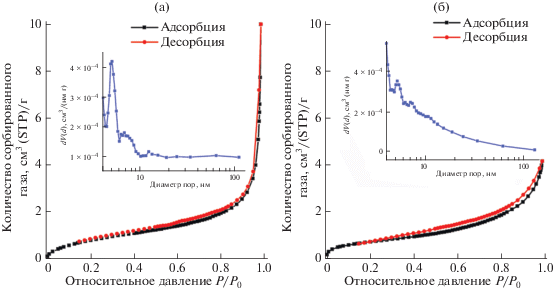
Рис. 6.
Кривые интрузии/экструзии ртути в образцах SiC-TiC, полученных в результате модификации пористых SiC-каркасов с применением прекурсоров [Ti(OC4H9)2.05(O2C5H7)1.95] (а) и [Ti(OC4H9)1.95(O2C5H7)2.05] (б); на врезках представлены соответствующие кривые распределения пор по размерам (ртутная порометрия).
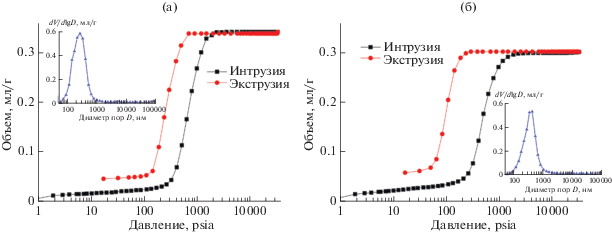
Подробный анализ объемной микроструктуры полученных композитов выполнен с помощью рентгеновской компьютерной микротомографии. На рис. 7 представлены рентгеновские плоскостные срезы функционально-градиентных композиционных материалов SiC-TiC. Видно, что для второго образца, полученного с применением в качестве прекурсора [Ti(OC4H9)1.95(O2C5H7)2.05], в приповерхностной области пористость значительно меньшая, а глубина проникновения уплотняющей фазы – бóльшая.
Рис. 7.
Рентгеновские плоскостные срезы образцов SiC-TiC-керамики после восьми циклов модифицирования в зависимости от состава прекурсора: [Ti(OC4H9)2.05(O2C5H7)1.95] (1) и [Ti(OC4H9)1.95(O2C5H7)2.05] (2); красным показаны центральные участки, выделенные для расчета статистических параметров, синим – приповерхностные.
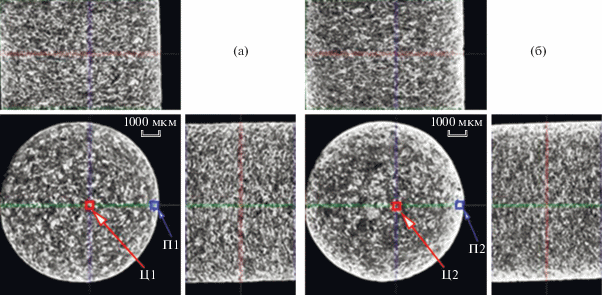
Для количественного анализа структуры на основании объемного сканирования модифицированной керамики выделены характерные области материала с целью выполнения расчетов его статистических параметров в центральной и приповерхностной областях – куб с ребром 500 мкм (рис. 7, на проекции xy синим отмечена выделенная область в приповерхностном слое, красным – в центральной области). В этих объемах были выделены также кубические области (с ребром 250 мкм) для построения модели пустотного пространства композита.
Построенные объемные модели для приповерхностных областей обоих композитов наглядно демонстрируют различия в степени заполнения порового пространства SiC-каркасов нанокристаллической матрицей карбида титана (рис. 8). Как видно из реконструированных моделей, в случае быстрого гелеобразования (прекурсор 1, рис. 3) раствор не успевает пройти на достаточно большую глубину в объем SiC-каркаса, о чем свидетельствует бóльший объем пор в указанной на плоскостных срезах приповерхностной области.
Рис. 8.
Объемная модель строения пустотного пространства, твердой фазы и их совмещение в приповерхностной зоне образцов SiC-TiC, полученных в результате модификации пористых SiC-каркасов с применением прекурсоров [Ti(OC4H9)2.05(O2C5H7)1.95] (сверху) и [Ti(OC4H9)1.95(O2C5H7)2.05] (снизу).
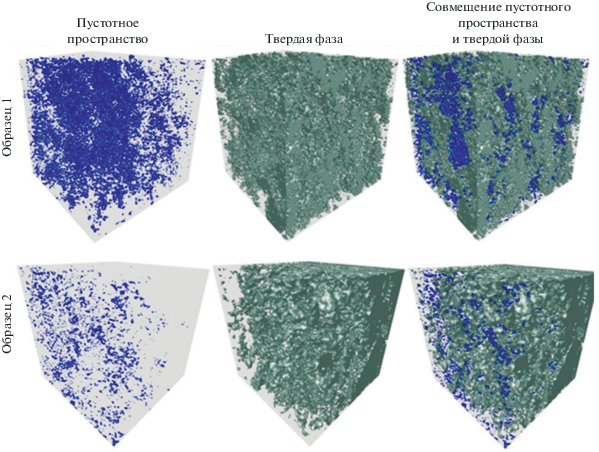
Поровое пространство в приповерхностной и центральной областях при моделировании было представлено в виде модели шаров и цилиндров (рис. 9), что позволяет количественно оценить структуру пор и соединяющих их каналов.
Рис. 9.
Строение порового пространства в виде модели шаров и цилиндров приповерхностной (а, в) и центральной областей (б, г) образцов SiC-TiC, полученных в результате модификации пористых SiC-каркасов с применением прекурсоров [Ti(OC4H9)2.05(O2C5H7)1.95] (а, б) и [Ti(OC4H9)1.95(O2C5H7)2.05] (в, г).
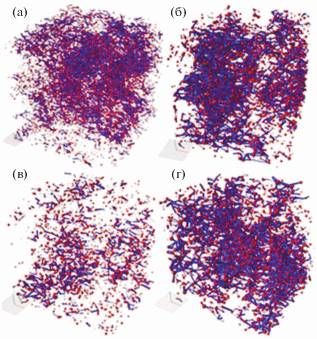
По результатам количественного анализа объемной микроструктуры образцов установлено, что в приповерхностной области происходит снижение числа пор и каналов, их размер также уменьшается по сравнению с центральными областями композитов (табл. 2). Для приповерхностной области образца 2 (модифицирование с использованием прекурсора [Ti(OC4H9)1.95(O2C5H7)2.05]) наблюдается меньшее количество пор и каналов, чем для образца 1 (прекурсор [Ti(OC4H9)2.05(O2C5H7)1.95]). Известно, что метод рентгеновской томографии позволяет определить пористость материала, основываясь на рентгеновской плотности материала. Так, видно, что композит SiC-TiC (образец 2) обладает пористостью в приповерхностной области ∼2.9%, что почти в 3 раза меньше, чем для образца 1 (8.3%) (табл. 2). Наблюдается снижение пористости и в центральной зоне для образца функционально-градиентной керамики SiC-TiC (образец 2), что свидетельствует о более существенном заполнении внутреннего объема композита. Однако в целом внутреннее поровое строение для полученных материалов имеет схожие параметры, а отклонения находятся в пределах погрешности измерений и метода вычисления.
Таблица 2.
Структурные параметры центральной и приповерхностной областей полученных композитов (по данным рентгеновской компьютерной микротомографии)
Поб, % | Пз, % | Nп, ед. | Nк, ед. | Nф.и.э., ед. | lк/rк | Vп, мкм3 | Vк, мкм3 | rп, мкм | rк, мкм | lк, мкм | |
---|---|---|---|---|---|---|---|---|---|---|---|
Ц1 | 12.74 | 2.12 | 63 499 | 76 014 | 27 902 | 15.86 | 5284 | 584 | 4.23 | 2.20 | 33.01 |
Ц2 | 11.86 | 1.97 | 63 207 | 74 523 | 27 941 | 16.16 | 5312 | 594 | 4.24 | 2.19 | 33.41 |
П1 | 8.26 | 3.97 | 60 315 | 54 338 | 46 944 | 15.73 | 3847 | 534 | 3.79 | 2.02 | 30.24 |
П2 | 2.86 | 2.26 | 29 226 | 15 692 | 38 485 | 14.64 | 2724 | 461 | 3.35 | 1.92 | 26.86 |
Примечание. Буквами Ц и П обозначены центральные и приповерхностные области соответственно (рис. 7). Поб – общая пористость, Пз – закрытая пористость, Nп – количество пор, Nк – количество каналов, Nф.и.э – число физически изолированных элементов, lк/rк – среднее отношение длины каналов к их радиусу, Vп и Vк – средние объемы пор и каналов, rп и rк – средние радиусы пор и каналов, а также lк – средняя длина каналов.
Таким образом, изучение объемной структуры пор полученных образцов показало, что применение растворов гетеролигандных комплексов [Ti(OC4H9)4– x(O2C5H7)x] различного состава с заданной реакционной способностью при гидролизе позволяет направленным образом заполнять поровое пространство пористых SiC-каркасов высокодисперсной TiC-матрицей с необходимой глубиной ее проникновения в объем материала, что определяет конструкционные и функциональные свойства целевых функционально-градиентных керамических материалов SiC-TiС.
ЗАКЛЮЧЕНИЕ
В рамках исследований разработаны новые подходы к получению керамических композиционных материалов состава SiC-TiC с заданным градиентом распределения нанокристаллической фазы карбида титана по глубине. Показано, что состав титансодержащих прекурсоров [Ti(OC4H9)4– x(O2C5H7)x], где х = 1.95 и 2.05, с заданной реакционной способностью при их гидролизе в присутствии полимерного источника углерода (фенолформальдегидной смолы) позволяет направленным образом заполнять поровое пространство SiC-каркасов высокодисперсной TiC-матрицей с необходимой глубиной проникновения в объем материала, что определяет конструкционные и функциональные свойства получаемых керамоматричных функционально-градиентных композитов SiC-TiC без значимого повышения плотности.
Список литературы
Fernández A., Arzac G.M., Vogt U.F. et al. // Appl. Catal. B-Environ. 2016. V. 180. P. 336. https://doi.org/10.1016/j.apcatb.2015.06.04
Cong H., Wang C., Gao X. et al. // J. Eng. Thermophys. 2016. V. 25. № 3. P. 301. https://doi.org/10.1134/S1810232816030012
Liu H., Li C., Ren X. et al. // Sci. Rep. 2017. V. 7. № 1. P. 1. https://doi.org/10.1038/s41598-017-16833-0
Sugiyama S., Tsuchiya Y., Gasmalla R.H.E. et al. // J. Ceram. Soc. Jpn. 2018. V. 126. № 9. P. 714. https://doi.org/10.2109/jcersj2.18069
Quintanilla A., Casas J.A., Miranzo P. et al. // Appl. Catal., B. 2018. V. 235. P. 246. https://doi.org/10.1016/j.apcatb.2018.04.066
Schaafhausen S., Yazhenskikh E., Heidenreich S., Mueller M. // J. Eur. Ceram. Soc. 2014. V. 34. № 3. P. 575. https://doi.org/10.1016/j.jeurceramsoc.2013.10.011
Bao S., Syvertsen M., Kvithyld A. et al. // Trans. Nonferrous Met. Soc. China. 2014. V. 24. P. 3922. https://doi.org/10.1016/S1003-6326(14)63552-4
Bakshi A.K., Ghimire R., Sheridan E., Kuhn M. // Ceram. Eng. Sci. Proc. 2016. V. 36. № 5. P. 89. https://doi.org/10.1002/9781119211624.ch9
Gómez-Martín A., Orihuela M.P., Becerra J.A. et al. // Mater. Des. 2016. V. 107. P. 450. https://doi.org/10.1016/j.matdes.2016.06.060
Xu C., Xu C., Han F. et al. // Ceram. Int. 2018. V. 44. № 15. P. 17792. https://doi.org/10.1016/j.ceramint.2018.06.247
Faldu N., Pinank K., Rathod K.N. et al. // J. Nanosci. NanoEng. Appl. 2015. V. 5. № 3. P. 11.
Gryshkov O., Klyui N.I., Temchenko V.P. et al. // Mater. Sci. Eng. C. 2016. V. 68. P. 143. https://doi.org/10.1016/j.msec.2016.05.113
Yan X., Sahimi M., Tsotsis T.T. // Microporous Mesoporous Mater. 2017. V. 241. P. 338. https://doi.org/10.1016/j.micromeso.2016.12.027
Walkiewicz-Pietrzykowska A., Uznanski P., Wrobel A.M. // Curr. Org. Chem. 2017. V. 21. № 22. P. 2229. https://doi.org/10.2174/138527282166617031716030
Mey-Cloutier S., Caliot C., Kribus A. et al. // Solar Energy. 2016. V. 136. P. 226. https://doi.org/10.1016/j.solener.2016.06.066
Leray C., Ferriere A., Toutant A. et al. // AIP Conf. Proc. 2017. V. 1850. № 1. P. 030032/1. https://doi.org/10.1063/1.4984375
Parvanian A.M., Salimijazi H.R., Fathi M., Saadatfar M. // J. Am. Ceram. Soc. 2019. V. 102. № 4. P. 2009. https://doi.org/10.1111/jace.16007
Silvestroni L., Sciti D., Zoli L. et al. // Renewable Energy. 2019. V. 133. P. 1257. https://doi.org/10.1016/j.renene.2018.08.036
Kawamura T. // Mineral. J. 1965. V. 4. P. 333. https://doi.org/10.2465/minerj1953.4.333
Arena H., Coulibaly M., Soum-Glaude A. et al. // Sol. Energy Mater. Sol. Cells. 2019. V. 191. P. 199. https://doi.org/10.1016/j.solmat.2018.11.018
Gadiou R., Serverin S., Gibot P., Vix-Guterl C. // J. Eur. Ceram. Soc. 2008. V. 28. P. 2265. https://doi.org/10.1016/j.jeurceramsoc.2008.02.022
Luo Y., Li S., Pan W., Li L. // Mater. Lett. 2003. V. 58. P. 150. https://doi.org/10.1016/S0167-577X(03)00434-8
Симоненко Е.П., Симоненко Н.П., Севастьянов В.Г. и др. // Композиты и наноструктуры. 2011. Т. 4. С. 52.
Севастьянов В.Г., Симоненко Е.П., Симоненко Н.П. и др. // Композиты и наноструктуры. 2014. Т. 6. № 4. С. 198.
Севастьянов В.Г., Симоненко Е.П., Игнатов Н.А. и др. // Журн. неорган. химии. 2011. Т. 56. № 5. С. 707.
Симоненко Е.П., Игнатов Н.А., Симоненко Н.П. и др. // Журн. неорган. химии. 2011. Т. 56. № 11. С. 1763.
Симоненко Е.П., Симоненко Н.П., Дербенев А.В. и др. // Журн. неорган. химии. 2013. Т. 58. № 10. С. 1279. https://doi.org/10.7868/S0044457X1310022X
Simonenko E.P., Simonenko N.P., Papynov E.K. et al. // J. Sol-Gel Sci. Technol. 2017. V. 82. P. 748. https://doi.org/10.1007/s10971-017-4367-2
Симоненко Е.П., Николаев В.А., Симоненко Н.П. и др. // Журн. неорган. химии. 2016. Т. 61. № 8. С. 975. https://doi.org/10.7868/S0044457X1608016X
Симоненко Е.П., Дербенев А.В., Симоненко Н.П. и др. // Журн. неорган. химии. 2017. Т. 62. № 7. С. 879. https://doi.org/10.7868/S0044457X17070236
Wyckoff R.W.G. ZnS structure, sphalerite structure. Crystal Structures 1. 85-237. New York: Interscience Publishers, 1963.
Wyckoff R.W.G. Rocksalt structure. Crystal Structures 1. P. 85-237. New York: Interscience Publishers, 1963.
Дополнительные материалы отсутствуют.
Инструменты
Журнал неорганической химии