Микроэлектроника, 2023, T. 52, № 2, стр. 87-95
Измерения на РЭМ размеров рельефных структур в технологическом процессе производства микросхем
Ю. А. Новиков 1, М. Н. Филиппов 2, *
1 Институт общей физики им. А.М. Прохорова РАН
119991 Москва, ул. Вавилова, 38, Россия
2 Институт общей и неорганической химии им. Н.С. Курнакова РАН
119991 Москва, Ленинский пр., 31, Россия
* E-mail: nya@kapella.gpi.ru
Поступила в редакцию 06.10.2022
После доработки 21.12.2022
Принята к публикации 22.12.2022
- EDN: PYQINW
- DOI: 10.31857/S0544126923700254
Аннотация
Рассмотрены проблемы измерения на РЭМ размеров элементов рельефа в технологическом процессе производства микросхем. Первая проблема связана с тем, что увеличение РЭМ в процессе работы может меняться в широких пределах в зависимости от измеряемых размеров. Вторая проблема связана с тем, что диаметр зонда, определенный в процессе калибровки РЭМ, отличается от диаметра, используемого при рабочих измерениях. Третья проблема связана с тем, что неизвестно какой параметр рельефа измеряется в методе дефокусировки РЭМ. Показано, что для решения первой проблемы необходимо калибровать метку на изображении с помощью структур с трапециевидным профилем и большими углами наклона боковых стенок. Решение второй проблемы основано на методе дефокусировки зонда РЭМ – определении зависимости размеров между определенными точками на сигналах РЭМ от диаметра зонда и экстраполяции этой зависимости к нулевому значению диаметра. Третья проблема решается с помощью виртуального растрового электронного микроскопа.
1. ВВЕДЕНИЕ
Современные технологии и особенно нанотехнологии основаны на измерении линейных размеров элементов объектов, создаваемых этими технологиями. В России создана система передачи размера от Первичного эталона длины – метра, в нанодиапазон [1], которая позволяет на растровых электронных микроскопах (РЭМ) проводить измерения размеров рельефных элементов поверхности твердого тела, лежащих в диапазоне 10 нм–100 мкм.
Однако, применение этой системы в технологии производства микросхем встречает ряд трудностей. Это связано с тем, что в основе измерения размеров лежит условие, что увеличение микроскопа и диаметр его зонда остаются такими же, как и в процессе калибровки РЭМ. Но, при переходе от калибровки РЭМ к измерению на нем размеров элементов микросхем требуется смена тест-объекта, с помощью которого калибруется РЭМ, на измеряемый объект. При этом всегда меняется как увеличение микроскопа, так и диаметр его зонда. Кроме того, определение размеров элементов микросхем на растровых электронных микроскопах является в общем случае некорректной задачей. Это приводит к тому, что мы не можем убедительно доказать правильность результатов измерения.
Настоящая работа посвящена описанию методов измерения на РЭМ размеров рельефных структур, которые можно встроить в технологический процесс производства микросхем.
2. ЗАДАЧИ МЕТОДОВ
Изменение увеличения РЭМ в технологическом процессе связано с тем, что элементы микросхем имеют разные размеры, различающиеся в десятки и даже сотни раз. Это требует частой перекалибровки РЭМ под нужный размер, что резко увеличивает время, затрачиваемое на подготовку к рабочему измерению.
Диаметр зонда РЭМ меняется в связи с тем, что при смене тест-объекта на измеряемый объект требуется подфокусировка микроскопа. Это приводит к изменению величины диаметра зонда, который был получен в процессе калибровки РЭМ.
Некорректность решаемой задачи обусловлено тем, что увеличение точности входной информации (например, уменьшение шумов изображения) не гарантирует увеличение точности выходной информации. Точность может увеличиться, уменьшиться или не измениться. При этом мы не знаем, что именно произошло.
Поэтому для применения разработанной системы [1] в технологической линии производства микросхем потребовалось решить 3 задачи. Во-первых, создать метод калибровки РЭМ в широком диапазоне увеличений, который позволял бы произвольно менять увеличение РЭМ и при этом давал возможность всегда знать его величину. Во-вторых, создать метод измерения размеров элементов микросхем при неизвестных величинах диаметра зонда РЭМ. В-третьих, разработать метод убедительного доказательства правильности результатов измерений размеров элементов микросхем.
3. КАЛИБРОВКА РЭМ В ШИРОКОМ ДИАПАЗОНЕ УВЕЛИЧЕНИЙ
Первая задача была решена в работе [2]. Было предложено калибровать не увеличение РЭМ (размер пикселя на изображении), а виртуальный тест-объект (ВТО), который должен иметь следующие свойства:
1) ВТО не связан с реальным тест-объектом и измеряемым объектом,
2) ВТО не зависит от фокусировки зонда,
3) ВТО сохраняет свою величину при изменении увеличения РЭМ,
4) ВТО меняет свою величину при изменении увеличения РЭМ.
На первый взгляд свойства 3 и 4 противоречат друг другу. Однако, такие объекты все-таки существуют. Это, например, метка, впечатываемая в кадр изображения. На рис. 1 приведены изображения меток РЭМ CamScan S-4 при разных увеличениях. Метки имеют один и тот же декларируемый размер ld = 300 нм (свойство 3) и разную длину метки Lm (свойство 4). При сильном изменении увеличения может меняться и декларируемый размер метки при соответствующем изменении длины метки.
Длина метки Lm связана с реальным размером метки lm выражением
(1)
${{L}_{{\text{m}}}} = M{{l}_{{\text{m}}}} + {{L}_{{\text{0}}}} = {{{{l}_{{\text{m}}}}} \mathord{\left/ {\vphantom {{{{l}_{{\text{m}}}}} m}} \right. \kern-0em} m} + {{L}_{{\text{0}}}},$Обычно сигнал метки представляет собой один или несколько трапециевидных сигналов (рис. 1). Где начинается и где кончается длина метки согласно производителю микроскопа (нижнее основание, верхнее основание или средняя линия трапеции) неизвестно. Поэтому в процессе калибровки надо определить значения величин lm и L0 для каждого декларируемого размера метки ld. Тогда, измерив на изображении длину метки Lm и зная величины lm и L0, можно с помощью выражения (1) всегда определить увеличение РЭМ (размер пикселя на изображении).
Для калибровки метки необходимо использовать тест-объект, представляющий собой шаговую структуру с трапециевидным профилем и большими углами φ наклона боковых стенок. Большие углы наклона определяется с помощью выражения [3]
где s – проекция боковой наклонной стенки трапециевидной структуры, h – высота (глубина) рельефа, φ – угол наклона боковой стенки относительно вертикали к основанию рельефа, d – диаметр зонда растрового электронного микроскопа. Поэтому на боковых сторонах сигнала, полученного при сканировании в РЭМ выступа и регистрации вторичных медленных электронов, появляются изломы (см. рис. 2).Рис. 2.
Связь граничных точек выступа (а) с большими углами наклона боковых стенок с контрольными точками схемы ВМЭ сигнала (б), лежащих на середине соответствующих отрезков схемы сигнала.
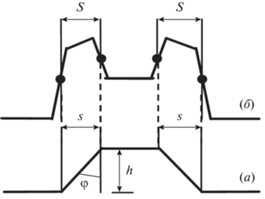
На тест-объекте выбирается один из выступов в середине шаговой структуры и сканируется на РЭМ, работающем в режиме сбора вторичных медленных электронов (ВМЭ), при разных увеличениях (разных декларируемых размерах и разных длинах метки). На рис. 3 показаны изображения в РЭМ CamScan S-4, работающем в режиме сбора ВМЭ, одного и того же места шаговой структуры при разных декларируемых размерах метки. Рис. 4 демонстрирует сигналы, из которых состоят изображения, полученные при разных декларируемых размерах метки и длинах метки.
Рис. 3.
Микрофотографии в РЭМ одного и того же места структуры тест-объекта МШПС-2.0К при разных увеличениях (разных длинах метки и декларируемых размерах метки 300 нм, 1 и 3 мкм ((а), (б) и (в) соответственно)).

Рис. 4.
Сигналы, из которых состоят полученные на РЭМ ВМЭ изображения, при сканировании одного и того же места шаговой структуры тест-объекта МШПС-2.0К с разным увеличением (разной длиной метки) и декларируемых размерах метки 300 нм, 1 и 3 мкм.

На сигналах измеряется размер S (см. рис. 2) – расстояние между точками, лежащими на середине соответствующих прямых линий, аппроксимирующих стороны сигнала. Этот параметр характеризует проекцию s боковой наклонной стенки выступа
и строится зависимость величины S от длины метки Lm для каждого декларируемого размера метки ld (рис. 5), из которой определяются параметры метки: реальный размер метки lm и начальная длина метки L0.Рис. 5.
Зависимость размера S ВМЭ сигналов РЭМ от длины метки для декларируемых размеров метки 300 нм, 1 и 3 мкм. Прямые линии соответствуют линейным приближениям соответствующих данных.
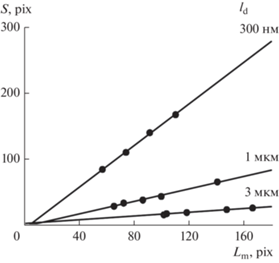
Для перехода от пикселей к микрометрам и нанометрам с помощью аттестованного значения шага t структуры, в который входит выбранный выступ, измеренного на сигналах шага сигнала T и выражения
определяется величина проекции боковой наклонной стенки, которая используется для перехода от пикселей к нанометрам.В экспериментах, представленных в данной работе (см. рис. 3 и 4), использовался тест-объект МШПС-2.0К [4] аттестованное значение шага которого t = 2001 ± 1 нм было определено на электронно-оптической метрологической системе (electron optical metrological system – EOMS (PTB, Braunschweig, Germany)) [5]. Величина проекции боковой наклонной стенки выбранного выступа составила s = 465 ± 2 нм.
В табл. 1 приведены определенные таким образом параметры метки микроскопа CamScan S-4. Работа на РЭМ с откалиброванной меткой в течение длительного времени показала, что параметры метки сохраняют свои значения в течение месяца при ежедневном включении и выключении микроскопа.
Таблица 1.
Параметры метки, полученные в результате ее калибровки
ld | Параметры метки | |
---|---|---|
lm/ld | L0, pix | |
300 нм | 1.104 ± 0.007 | 3.7 ± 0.5 |
1 мкм | 1.104 ± 0.007 | 4.7 ± 0.6 |
3 мкм | 1.224 ± 0.016 | –15.5 ± 1.4 |
Рассмотрим способ применения метки для измерения линейных размеров элементов микро- и наноструктур в широком диапазоне изменения увеличения.
В процессе измерения линейных размеров элементов микро- и наноструктур на сигналах РЭМ изображений измеряются следующие величины:
1) размер Q, представляющий собой расстояние между контрольными точками, ограничивающими измеряемый размер,
2) длину метки Lm, которая определяется по тем же правилам, что и в процессе калибровки метки.
Размер q измеряемого элемента структуры определяется в соответствии с формулой
в которой lm и L0 представляют собой величины, полученные в процессе калибровки метки при том же рабочем отрезке и декларируемом размере метки, что и в процессе измерения размеров элементов структур.Погрешность Δq измерения размера q можно определить с помощью выражения
(6)
${{\left( {{{\Delta q} \mathord{\left/ {\vphantom {{\Delta q} q}} \right. \kern-0em} q}} \right)}^{2}} \approx {{\left( {{{\Delta Q} \mathord{\left/ {\vphantom {{\Delta Q} Q}} \right. \kern-0em} Q}} \right)}^{2}} + {{\left( {{{\Delta {{l}_{{\text{m}}}}} \mathord{\left/ {\vphantom {{\Delta {{l}_{{\text{m}}}}} {{{l}_{{\text{m}}}}}}} \right. \kern-0em} {{{l}_{{\text{m}}}}}}} \right)}^{2}} + {{\left( {{{\Delta {{L}_{0}}} \mathord{\left/ {\vphantom {{\Delta {{L}_{0}}} {{{L}_{{\text{m}}}}}}} \right. \kern-0em} {{{L}_{{\text{m}}}}}}} \right)}^{2}}.$Из трех составляющих погрешности ΔQ определяется в процессе рабочего измерения элемента структуры. В экспериментах ее вклад в полную погрешность лежит в диапазоне
Две остальные (Δlm и ΔL0) определяются в процессе калибровки метки. В экспериментах их вклады лежат в диапазонах
Таким образом, с помощью данного метода измерения линейных размеров элементов микро- и наноструктур можно проводить соответствующие измерения с погрешностью лучше 1.5% от измеряемой величины в широком диапазоне увеличений независимо от того, при каком увеличении проходила калибровка метки микроскопа.
4. МЕТОД ДЕФОКУСИРОВКИ ЗОНДА РЭМ
В технологическом процессе производства микросхем создаются рельефные структуры, имеющие трапециевидную форму профиля с малыми углами наклона боковых стенок
Форма ВМЭ сигналов от таких структур отличается от формы ВМЭ сигналов от структур с большими углами наклона боковых стенок. На рис. 6 приведены схема шаговой структуры (рис. 6а), состоящей из выступов и канавки, и схема ВМЭ сигнала (рис. 6б), полученного на РЭМ при сканировании структуры, состоящей из выступов и канавок с трапециевидным профилем и малыми углами наклона боковых стенок. Параметры структуры и сигнала связаны друг с другом с помощью выражений
(7)
${{b}_{{\text{t}}}} = {{{{B}_{{\text{t}}}}} \mathord{\left/ {\vphantom {{{{B}_{{\text{t}}}}} M}} \right. \kern-0em} M} + d = m{{B}_{{\text{t}}}} + d,$(8)
${{u}_{{\text{t}}}} = {{\left( {2{{U}_{{\text{t}}}} - {{B}_{{\text{t}}}}} \right)} \mathord{\left/ {\vphantom {{\left( {2{{U}_{{\text{t}}}} - {{B}_{{\text{t}}}}} \right)} M}} \right. \kern-0em} M} - d = m\left( {2{{U}_{{\text{t}}}} - {{B}_{{\text{t}}}}} \right) - d,$(9)
${{b}_{{\text{p}}}} = {{{{B}_{{\text{p}}}}} \mathord{\left/ {\vphantom {{{{B}_{{\text{p}}}}} M}} \right. \kern-0em} M} - d = m{{B}_{{\text{p}}}} - d,$(10)
${{u}_{{\text{p}}}} = {{\left( {2{{U}_{{\text{p}}}} - {{B}_{{\text{p}}}}} \right)} \mathord{\left/ {\vphantom {{\left( {2{{U}_{{\text{p}}}} - {{B}_{{\text{p}}}}} \right)} M}} \right. \kern-0em} M} + d = m\left( {2{{U}_{{\text{p}}}} - {{B}_{{\text{p}}}}} \right) + d,$Рис. 6.
Схемы шаговой структуры (а), состоящей из 2 выступов и канавки, и ВМЭ сигнала (б), получаемого при сканировании в РЭМ структуры с трапециевидным профилем и малыми углами наклона боковых стенок, с параметрами, характеризующими структуру и сигнал.

Численные значения коэффициента kb для разных определений диаметра зонда приведены в табл. 2. Поэтому, если используется американское или японское определение диаметра зонда или параметр σ гауссиана, то необходимо после калибровки РЭМ перевести величину диаметра зонда с помощью формулы (11) и табл. 2 в величину американского, японского или гауссовского определения диаметра зонда.
Таблица 2.
Численные значения коэффициента, связывающего разные определения диаметра зонда для гауссовской формы зонда
Диаметр зонда | kb |
---|---|
σ гауссиана | 0.40 |
Американский | 0.67 |
Японский | 1.13 |
Российский | 1 |
Вторая задача – измерение на РЭМ размеров элементов рельефа без знания величины диаметра электронного зонда, была решена в работах [9, 10]. В [9] предложен метод дефокусировки зонда РЭМ. Он основан на том, что на РЭМ производится сканирование рельефа при сфокусированном зонде и нескольких дефокусировках.
На сигналах при разных фокусировках измеряются 7 величин (см. рис. 6б) – расстояния между максимумами (Up, Ut), размер нижнего основания сигнала (Bp, Bt), средние линии сигналов (Lp, Lt) и проекция боковой стороны сигнала (D). Строится зависимость параметров U, B и L от параметра D и проводится линейная аппроксимация этих данных и экстраполяция этих линий к значению D = 0 (см. рис. 7).
Рис. 7.
Зависимости размеров контрольных отрезков, определенных на ВМЭ сигналах РЭМ при сканировании выступа. Прямые линии соответствуют линейным приближениям соответствующих данных.
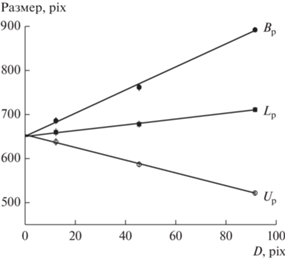
Как оказалось при D = 0 в пределах ошибок все 3 линии пересекаются в одной точке. Это и есть измеряемый размер трапециевидной структуры с малыми углами наклона боковых стенок. Осталось только определить какой же размер трапециевидного рельефа измеряется методом дефокусировки зонда РЭМ – нижнее основание трапеции, верхнее основание, средняя линия или какой другой элемент трапеции?
Решение этого вопроса удалось получить с помощью виртуального растрового электронного микроскопа (ВРЭМ) [11].
5. ВИРТУАЛЬНЫЙ РАСТРОВЫЙ ЭЛЕКТРОННЫЙ МИКРОСКОП
ВРЭМ это компьютерная программа, которая, используя входные данные, воспроизводящие размеры и форму исследуемого на реальном РЭМ объекта, генерирует изображение, аналогичное изображению, полученному на реальном РЭМ. Отличительной особенностью ВРЭМ является то, что мы знаем какие характеристики имеют структуры на входе виртуального микроскопа, а у реального РЭМ мы этого не знаем.
Схема работы виртуального и реального РЭМ в процессе измерения показана на рис. 8 [11]. Она состоит из двух ветвей – реальной и виртуальной.
Реальная ветвь представляет собой стандартную схему измерений. Виртуальная ветвь подобна реальной, но в ней все реальные составляющие заменены на виртуальные. Связь реальной и виртуальной ветвей осуществляется в трех местах (см. рис. 8). Во-первых, выходные данные реальной ветви являются входными данными виртуальной. Во-вторых, метод решения обратной задачи и параметры этого метода являются общими для реальной и виртуальной ветвей схемы измерений. В-третьих, решение о правильности выполнения измерительной задачи осуществляется путем сравнения моделей измеряемого и виртуального объектов. Работает такая общая схема измерений следующим образом.
На реальном РЭМ получают изображение измеряемого объекта. Это изображение является измерительной информацией реального прибора, которая несет в себе информацию об измеряемых характеристиках объекта. Параметры этих характеристик определяют из решения обратной задачи. В результате этого процесса получается модель объекта измерений с его измеренными характеристиками. Так как модель была получена в результате решения в общем случае некорректной задачи, то требуется доказательство правильности модели (правильности решения некорректной задачи). Это доказательство предоставляет работа виртуального растрового электронного микроскопа.
На основе полученной модели объекта измерений создается виртуальный объект (см. рис. 8), который используется виртуальным РЭМ для получения виртуального изображения – виртуальной информации, аналогичной реальной, получаемой на реальном РЭМ. Далее эта виртуальная информация используется для решения обратной задачи тем же методом и при тех же параметрах метода, что и при обработке измерительной информации. В результате этого получается модель виртуального объекта. Сравнивая между собой модели измеряемого и виртуального объектов, принимается решение о достоверности решения задачи определения характеристик измеряемого объекта, если эти модели совпадают.
В противном случае проводится новое решение обратной задачи для измерительной информации другим методом или при других параметрах метода решения обратной задачи и строится новая модель измеряемого объекта и новый виртуальный объект. Далее получается новая виртуальная информация, решается обратная задача при новом методе решения обратной задачи и строится новая модель виртуального объекта. И так проводится до тех пор, пока модели измеряемого и виртуального объектов не совпадут.
Если же совпадений не будет достигнуто, то необходимо менять реальный микроскоп и его виртуальный аналог. Далее вновь проводятся измерения на новом РЭМ и новом ВРЭМ так, как это было показано выше, до тех пор, пока модели реального и виртуального объекта не совпадут.
Таким образом осуществляется определение измеряемой характеристики и доказательство правильности этого результата. Поэтому, для решения третьей задачи – определения какой размер трапециевидного рельефа измеряется методом дефокусировки зонда РЭМ, используется виртуальный растровый электронный микроскоп [11].
На ВРЭМ [10] при разных диаметрах зонда (дефокусировка) были сгенерированы изображения выступов и канавок с трапециевидным профилем с малыми углами наклона боковых стенок и ширинами 100 и 30 нм. На рис. 9 показаны сгенерированные при диаметрах зонда 5 нм (рис. 9а), 10 нм (рис. 9б) и 15 нм (рис. 9в) ВМЭ изображения выступа из кремния с размерами нижнего основания трапеции 31 нм, средней линии 30 нм, верхнего основания 29 нм, высоты 20 нм. Рис. 10 демонстрирует сигналы, из которых состоят изображения выступа на рис. 9.
Рис. 9.
Сгенерированные на ВРЭМ при диаметрах зонда 5, 10 и 15 нм ((а), (б) и (в) соответственно) ВМЭ изображения трапециевидного выступа с малыми углами наклона боковых стенок и шириной средней линии профиля выступа 30 нм. Длина метки 30 нм.
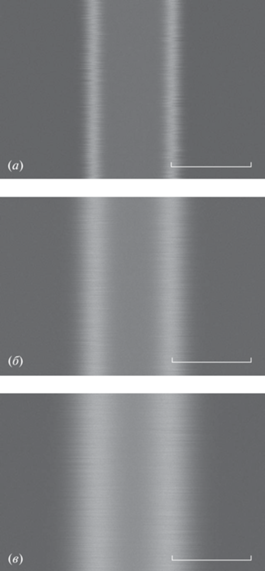
Рис. 10.
Формы сигналов, из которых состоят сгенерированные ВРЭМ при диаметрах зонда 5, 10 и 15 нм (сигналы 1, 2 и 3 соответственно) ВМЭ изображения трапециевидного выступа с малыми углами наклона боковых стенок и шириной 30 нм.
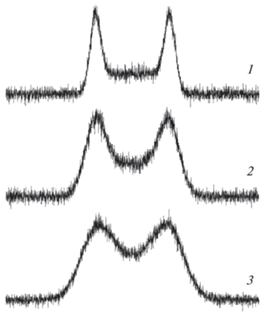
На сигналах ВРЭМ изображений были измерены параметры U, B, L и построены их зависимости от величин D (см. рис. 6б). На рис. 11 показаны зависимости Up, Bp и Lp от D для выступа с шириной средней линии трапеции 30 нм и приведены линии, соответствующие уровням верхнего и нижнего оснований трапеции и средней линии. Видно, что линейные аппроксимации зависимостей хорошо выполняются. Хорошо выполняются и экстраполяции к нулевому значению параметра D. Получаемый при экстраполяции размер структур соответствует нижним основаниям трапециевидного выступа bp (см. рис. 6а). Аналогичный результат был получен и для 100 нм выступов и для 30 и 100 нм канавок [10].
Рис. 11.
Зависимости размеров контрольных отрезков Up, Bp и Lp, определенных на ВМЭ сигналах сгенерированных ВРЭМ изображениях выступа шириной 30 нм, от параметра D.
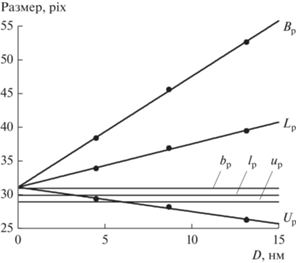
Таким образом, было показано, что измеряемыми параметрами в методе дефокусировки зонда являются нижние основания трапециевидных выступов и канавок.
Необходимо отметить, что размеры нижних оснований выступов и канавок с трапециевидными профилями и малыми углами наклона боковых стенок является главными размерами в технологии микро- и наноэлектроники. Так размер нижнего основания металлического выступа, представляющего собой затвор полевого транзистора, определяет длину канала этого транзистора. Нижнее основание канавки между элементами металлической разводки характеризует емкостную связь между этими линиями и токи утечки элементов металлической разводки.
Список литературы
Gavrilenko V.P., Novikov Yu.A., Rakov A.V., Todua P.A. // Proc. SPIE. 2009. V. 7405. P. 740504. https://doi.org/10.1117/12.826164
Gavrilenko V.P., Novikov Yu.A., Rakov A.V., Todua P.A., Volk Ch.P. // Proc. SPIE. 2009. V. 7272. P. 72720Z. https://doi.org/10.1117/12.813514
Novikov Yu.A., Darznek S.A., Filippov M.N., Mityukhlyaev V.B., Rakov A.V., Todua P.A. // Proc. SPIE. 2008. V. 7025. P. 702511. https://doi.org/10.1117/12.802428
Novikov Yu.A., Gavrilenko V.P., Ozerin Yu.V., Rakov A.V., Todua P.A. // Proc. SPIE. 2007. V. 6648. P. 66480R. https://doi.org/10.1117/12.733134
Häßler-Grohne W., Bosse H. // Measurement science and technology. 1998. V. 9. P. 1120.
Gavrilenko V.P., Novikov Yu.A., Rakov A.V., Todua P.A. // Proc. SPIE. 2008. V. 7042. P. 70420C. https://doi.org/10.1117/12.794891
SEM Performance Standard. Standard Reference Material 2069a. NBS. 1985.
Oho E., Sasaki T., Kanaya K. // Research Reports of Kogakuin University. 1985. № 59. P. 106 (1985).
Gavrilenko V.P., Kalnov V.A., Novikov Yu.A., Orlikovsky A.A., Rakov A.V., Todua P.A., Valiev K.A., Zhikharev E.N. // Proc. SPIE. 2009. V. 7272. P. 727227. https://doi.org/10.1117/12.814062
Новиков Ю.А. // Микроэлектроника. 2017. Т. 46. № 1. С. 61. https://doi.org/10.7868/S0544126917010070
Новиков Ю.А. // Микроэлектроника. 2014. Т. 43. № 6. С. 456. https://doi.org/10.7868/S0544126914060076
Дополнительные материалы отсутствуют.
Инструменты
Микроэлектроника