Микроэлектроника, 2019, T. 48, № 5, стр. 379-388
Разработка тонкопленочного термоэлектрического генератора для маломощных применений
А. С. Коротков 1, *, В. В. Лобода 1, С. В. Дзюбаненко 2, **, Е. М. Бакулин 2
1 Санкт-Петербургский политехнический университет Петра Великого
195251 Санкт-Петербург, ул. Политехническая, 29, Россия
2 ОАО “Авангард”
195271 Санкт-Петербург, Кондратьевский пр., 72, Россия
* E-mail: korotkov@spbstu.ru
** E-mail: dzyubanenko@hotmail.com
Поступила в редакцию 09.01.2019
После доработки 05.02.2019
Принята к публикации 05.02.2019
Аннотация
Представлены результаты разработки термоэлектрического генератора для маломощных приложений, например, для систем мониторинга состояния человека. Принцип действия генератора основан на использовании эффекта Зеебека. Приводится описание технологического процесса изготовления и результаты испытаний тонкопленочного термоэлектрического генератора с выходной мощностью 3–56 мкВт при перепаде температур 25–100 К.
1. ВВЕДЕНИЕ
Перспективным классом устройств сбора энергии (Energy Harvester) для автономного питания электрических и электронных систем являются термоэлектрические генераторы (ТЭГ). Принцип действия ТЭГ основан на использовании эффекта Зеебека, т.е. преобразовании перепада температур в электрический ток. Термоэлектрические генераторы используются во многих практических приложениях при требуемых мощностях от единиц мкВт до единиц Вт [1–3]. ТЭГ широко применяются в схемах питания систем мониторинга состояния двигателей, биомедицинского оборудования, сенсорных сетях [4]. По технологии изготовления ТЭГ классифицируются на два типа: объемные и тонкопленочные. Тонкопленочные ТЭГ изготавливаются по твердотельным полупроводниковым технологиям, совместимым с технологическим процессом микроэлектромеханических систем (МЭМС). При этом рабочие области ТЭГ формируются как субмикронные пленочные слои. Основное преимущество ТЭГ, реализуемых на основе технологии МЭМС, – высокая удельная мощность (мощность, приведенная на единицу площади, P/S), которая в 3–5 раз выше, чем у объемных ТЭГ. ТЭГ на основе МЭМС технологии обеспечивают при перепаде температуры в десятки градусов выходную мощность несколько мкВт при выходном напряжении несколько вольт. На физическом уровне ТЭГ представляет последовательное соединение пар термоэлементов n- и p-типа, расположенных между двумя непроводящими пластинами (горячая и холодная стороны). Термоэлементы соединяются металлическими контактными площадками. Цель данной работы – разработка технологического процесса и изготовление ячейки тонкопленочных ТЭГ с повышенной выходной удельной мощностью для источников питания устройств мониторинга объектов.
Статья построена следующим образом. Во 2-ом разделе, после введения, рассмотрены вопросы построения модели и моделирования ТЭГ на основе метода конечных элементов, в 3-ем разделе описан технологический процесс изготовления чипа ТЭГ, в 4-ом разделе представлены результаты измерений характеристик изготовленных образцов ТЭГ. В заключении даны общие выводы и рекомендации.
2. МОДЕЛИРОВАНИЕ
Моделирование является неотъемлемой частью процесса разработки ТЭГ, поскольку позволяет провести проверку расчетных параметров ТЭГ. Моделирование проводится на основе метода конечных элементов с применением платформы ANSYS Workbench. Процесс моделирования представляется следующими этапами: препроцессорная подготовка (Preprocessing), получение решения (Solving), пост процессорная обработка результатов (Postprocessing). Этап препроцессорной подготовки состоит из пяти шагов: построение геометрической 3D-модели объекта с использованием модуля ANSYS Design Modeler, предназначенного для построения, редактирования геометрии и присвоения атрибутов модели; выбор типа анализа, причем в приложении к моделированию ТЭГ – это термоэлектрический анализ (Thermal-electric); задание физических свойств материалов, из которых состоит моделируемый объект (Engineering data); создание твердотельной модели объекта с использованием модуля ANSYS Mechanical, позволяющего определять поля температур из решения задач стационарной и нестационарной теплопроводности, конвекции, теплообмена излучением; генерация сетки конечных элементов с использованием модуля ANSYS Meshing. Этап получения решения состоит из следующих шагов: выбор вида анализа (Steady-State Analysis) и его опций для типа анализа, выбранного на предыдущем этапе; выбор вида граничных условий – тепловые и электрические; выбор параметров расчета. На последнем этапе осуществляется вывод результатов расчета в графической и табличной формах. Изложенная методология моделирования подробно рассмотрена в работах [5–10].
Ядро микросхемы тонкопленочного ТЭГ состоит из двух пластин, на которых размещаются полупроводниковые термоэлементы с проводимостями n- и p-типов. В качестве пластин используются стандартные кремниевые подложки. Моделирование проводилось с учетом предлагаемого технологического процесса изготовления ТЭГ. Геометрические размеры термоэлементов определяются в соответствии с требуемой выходной мощностью. Проведенная оценка показала, что при выходной мощности 25 мкВт, размеры термоэлемента составят 20 × 60 × 60 мкм при числе элементов 288. Конструкция ТЭГ в корпусе показана на рис. 1. Чип ТЭГ размещается на печатной плате и герметизируется между двумя алюминиевыми частями корпуса. Верхняя часть корпуса цилиндрической формы выполняет функцию радиатора. Нижняя часть корпуса выполнена в форме прямоугольной пластины, к которой прикрепляется печатная плата с чипом и на которой формируются контактные площадки внешних выводов ТЭГ. Диэлектрическое кольцо разделяет верхнюю и нижнюю части корпуса. Размеры чипа ТЭГ составили 3.8 × 2.7 × 0.8 мм, размеры генератора в сборе – 15 × 10 × 0.7 мм.
Рис. 1.
Чертеж термоэлектрического генератора в сборе: 1 – чип термоэлектрического генератора; 2 – печатная плата с алюминиевым основанием; 3 – кольцо-изолятор; 4 – радиатор; 5 – соединительная проволока.
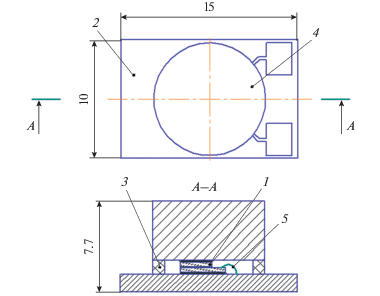
Для изготовления термоэлементов ТЭГ использован теллуриды висмута и сурьмы n-типа и p-типа проводимости, как обеспечивающие в рассматриваемом диапазоне температур наибольший КПД. Исходные данные для моделирования включают следующие физические параметры: коэффициент Зеебека, удельное электрическое сопротивление, удельную теплопроводность. Данные параметры во многом зависят от технологии изготовления и имеют существенный разброс. В этой связи проведены оценки параметров методом наименьших квадратов на основе значений, опубликованных в работах [11–15]. Полученные результаты показаны на рис. 2 и рис. 3. В табл. 1, 2 приведены значения параметров, использованные при моделировании в диапазоне температур 300–500 К.
Таблица 1.
Параметры полупроводникового материала n-типа (Bi2Te3)
T, К | Коэффициент Зеебека, мкВ * К–1 | Удельное сопротивление, мкОм ⋅ м |
Удельная теплопроводность, Вт/м ⋅ К |
---|---|---|---|
300 | –148.24 | 12.02 | 1.03 |
350 | –152.59 | 13.48 | 1.11 |
400 | –156.89 | 15.05 | 1.18 |
450 | –157.64 | 16.61 | 1.23 |
500 | –152.38 | 18.06 | 1.28 |
Таблица 2.
Параметры полупроводникового материала p-типа (Sb2Te3)
T, К | Коэффициент Зеебека, мкВ * К–1 | Удельное сопротивление, мкОм ⋅ м |
Удельная теплопроводность, Вт/м ⋅ К |
---|---|---|---|
300 | 208.25 | 13.33 | 1.07 |
350 | 220.21 | 16.78 | 1.06 |
400 | 219.52 | 19.74 | 1.13 |
450 | 205.78 | 22.19 | 1.27 |
500 | 178.57 | 24.10 | 1.48 |
Таблица 3.
Параметры материалов контактов и подложки (T = 300 K)
Конструктивные части ТЭГ | Материал | Удельное сопротивление, мкОм ⋅ м |
Удельная теплопроводность, Вт/м ⋅ К |
---|---|---|---|
Подложка | Si | – | 148 |
SiO2 | – | 1.5 | |
Контактные площадки | Cr | 0.15 | 89 |
Cu | 0.017 | 406 | |
Ti | 0.47 | 22 |
При моделировании сетка конечных элементов генерировалась автоматически. Сетка состоит из кубических изопараметрических элементов SOLID226 с тремя степенями свободы (термических, электрических и структурных). Полное число ячеек сетки 9142. Температурные граничные условия определялись температурой нижней пластины Th и температурой верхней пластины Tc. Рассмотрены следующие значения температур: Th = 30, 55, 82, 110°C, Tc = 5, 5, 7, 10°C. Данные температуры соответствуют разнице ΔT = 25, 50, 75, 100 K.
Результатом моделирования являются значения выходной мощности ТЭГ на внешней нагрузке. На рис. 4 и рис. 5 приведены вольтамперные характеристик ТЭГ и зависимости выходной мощности от тока в нагрузке для указанных температур.
3. ТЕХНОЛОГИЯ
Технологический процесс изготовления термоэлектрического генератора в сборе включает 4 этапа [18, 19]: изготовление основной (нижней) части ТЭГ; изготовление коммутационной (верхней) части ТЭГ; бондинг; корпусирование. Схема процесса изготовления чипа ТЭГ показана на рис. 6–8.
Рис. 6.
Процесс изготовления нижней части ТЭГ: (а) – подготовка основания; (б) – металлизация; (в) – нанесение фоторезиста; (г) – электрохимическое осаждение TE n-типа; (д) – электрохимическое осаждение TE p-типа; (е) – планаризация поверхности; (ж) – формирование припоя; (з) – травление.
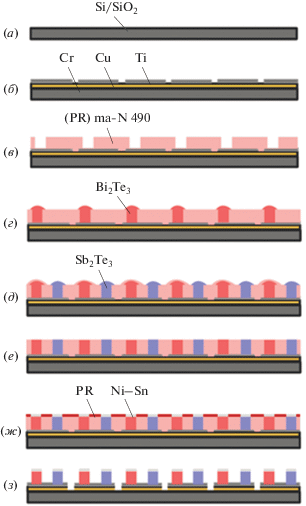
Рис. 7.
Процесс изготовления верхней части ТЭГ: (а) – подготовка основания; (б) – металлизация; (в) – формирование припоя; (г) – травление.
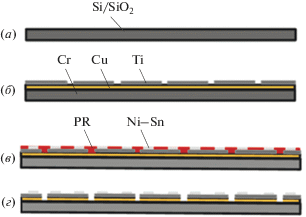
Этап 1. Основание чипа ТЭГ – кремниевая пластина с оксидной пленкой ~0.85 мкм (рис. 6а). Методом магнетронного распыления на поверхности оксидной пленки формируются контактные площадки для соединения полупроводниковых термоэлементов в электрическую цепь, состоящие из трех слоев: Cr (0.05 мкм)–Cu (2 мкм)–Ti (1 мкм) (рис. 6б). Тонкий слой хрома выполняет функцию адгезионного слоя между диоксидом кремния и медью. Слой титана выполняет функцию зародышевого слоя для электрохимического осаждения Bi–Te и Sb–Te полупроводниковых термоэлементов. Титан напыляется по предварительно сформированной фоторезистивной маске с последующим “взрывом”. Для усиления адгезии пластина с медной пленкой подвергается операции декапирования, и титан напыляется с предварительной ионной обработкой. Далее, формируется маска из негативного фоторезиста (PR) ma-N 490 фирмы Micro Resist Technology. Необходимая маска толщиной 30 мкм создается методом фотолитографии, для этого фоторезист наносится в два слоя с экспонированием и проявлением каждого в целях достижения максимально прямого профиля (рис. 6в). По сформированной маске происходит электрохимическое осаждение Bi2Te3 из водного раствора электролита, состоящего из 3.5 М HNO3, 25 мМ Bi, 25 мМ Te в виде оксидов, на плотности тока 5.3 мА/см2 в течение 120 мин с использованием анода из нержавеющей стали 12Х18Н10Т (рис. 6г) для формирования ТЭ n-типа. Процесс фотолитографии повторяется для вскрытия окон, в которых происходит осаждение Sb2Te3. Осаждение происходит из водного раствора электролита, состоящего из 1 М HNO3, 52 мМ C4H6O6, 7 мМ Te, 63 мМ Sb в виде оксидов, на плотности тока 5.3 мА/см2 в течение 120 мин (рис. 6д) для формирования термоэлементов p-типа. Планаризация поверхности осуществляется методом механической полировки, фоторезист при этом не удаляется (рис. 6е). После чего происходит формирование площадок состава Ni–Sn (Ni (1 мкм) адгезионный слой, Sn (3 мкм) соединительный слой) на поверхности осажденных теллуридов висмута и сурьмы методом последовательного магнетронного распыления никеля и олова по предварительно сформированной маске фоторезиста с последующим “взрывом” (рис. 6ж). Формирование нижней пластины заканчивается травлением медного слоя на местах, не защищенных слоем титана (рис. 6з).
Этап 2. Коммутационная (верхняя) часть ТЭГ состоит из кремниевой пластины с оксидной пленкой, контактных площадок. Технология формирования топологии слоев Cr–Cu–Ti с площадками Ni–Sn аналогична основной (нижней) части (рис. 7).
Этап 3. Соединение основной (нижней) и коммутационной (верхней) частей ТЭГ методом перевернутого кристалла сплавлением соответствующих оловянных площадок друг с другом (рис. 8). Совмещение верхней и нижней части осуществлялось с помощью предустановленной системы инфракрасного машинного зрения на установке Dr. Tresky T-3002-FC3. В заключении, полученная конструкция разделяется на чипы алмазным диском, на нижней пластине вскрываются контактные площадки для внешних выводов.
Этап 4. ТЭГ в сборе состоит из чипа, закрепленного между двумя алюминиевыми частями корпуса. Верхняя часть корпуса выполнена в виде цилиндра (радиатора), нижняя – в виде пластины, на которую крепится плата с внешними выводами ТЭГ (рис. 9), что обеспечивает эффективный теплообмен. Кристалл монтировался на плату через эпоксидный клей с алюминиевой пудрой в качестве наполнителя, также способствующей повышению теплопроводности. Электрические соединения между контактными площадками кристалла и соответствующими контактными площадками печатной платы выполнялись методом клиновой ультразвуковой микросварки. Для надежности контакта и уменьшения токовой нагрузки на проводник все соединения дублировались. Завершающий этап – монтаж кольца-изолятора и радиатора на печатную плату с чипом. Диэлектрическое кольцо располагается между алюминиевыми частями корпуса. Кольцо устанавливалось на эпоксидный клей без наполнителя. Радиатор монтировался на кольцо с помощью эпоксидного клея. С целью улучшения теплопередачи между кристаллом и радиатором на место их контакта наносилась термопаста Titan TTG-G30015.
4. ЭКСПЕРИМЕНТ
Согласно изложенному проведено проектирование, моделирование и изготовление ТЭГ. Для проведения измерений использована экспериментальная установка, принцип работы и устройство которой представлены в работах [8–10]. Напряжение термо-ЭДС Eтэдс, генерируемое ТЭГ, прямо пропорционально коэффициенту Зеебека α генератора и разнице температур ΔT между горячей Th и холодной Tc сторонами термоэлектрического генератора:
На внешней нагрузке RН создается напряжение U, равное термо-ЭДС за вычетом падения напряжения на внутреннем сопротивлении генератора R:
где сила тока I в цепи определяется выражением:Мощность, отдаваемая во внешнюю цепь, вычисляется по следующей формуле:
(2)
$P = UI = \frac{{{{\alpha }^{2}}\Delta {{T}^{2}}}}{{{{{\left( {R + {{R}_{{\text{Н }}}}} \right)}}^{2}}}}{{R}_{{\text{Н }}}}.$Для создания разности температур на сторонах ТЭГ к его горячей стороне необходимо подвести тепловой поток Qh, а с холодной стороны отвести тепловой поток Qc. По закону сохранения энергии разница тепловых потоков составит электрическую мощность P:
Принцип работы и устройство установки следующие: источник тепла подводит тепловой поток Qh к горячей стороне ТГМ, радиатор (в более общем случае – система охлаждения) отводит от холодной стороны ТЭГ тепловой поток Qc. Для эффективной работы необходимо обеспечить максимально допустимую разность температур между сторонами генератора. ТЭГ преобразует разность значений температур горячей и холодной сторон в ток, который поступает в сопротивление внешней нагрузки RН. Экспериментальная установка снабжена измерительными приборами: вольтметром для измерения падения напряжения на внешней нагрузке, электронными термометрами для контроля температуры на сторонах модуля. ТЭГ фиксировался между источником тепла и радиатором с прижимным усилием 1 кН, контролируемым динамометром. Для обеспечения равномерного температурного поля на поверхностях ТЭГ между модулем и источником тепла (а также модулем и радиатором) использовались промежуточные медные пластины. Кроме того, для наилучшего теплового контакта на границе “ТЭГ–медная пластина” использовалась термопаста Nano Grease.
Во время эксперимента поддерживалась постоянной температура горячей стороны Th. Значения внешней нагрузки RН варьировалось в пределах от 10 Ом до 10 кОм. В процессе эксперимента контролировалась температура на поверхностях TЭГ, а также измерялось выходное напряжение на нагрузке. Величины тока и выходная мощность рассчитывались по формулам (1) и (2) соответственно. Результаты экспериментальных измерений представлены на рис. 10 и рис. 11.
ЗАКЛЮЧЕНИЕ
В работе представлены результаты проектирования, моделирования и разработанный авторами технологический процесс создания тонкопленочных термоэлектрических генераторов для маломощных приложений. В отличие от известных работ [18, 19] для увеличения выходной удельной мощности ТЭГ предложено: изменить тип металлизации с Cr–Au, Ti–Cu–Ti на Cr–Cu–Ti, что обеспечило лучшую адгезию; изменить режим электрохимического осаждения для формирования термоэлементов с оптимальными, полученными в ходе моделирования, значениями геометрических размеров с высотой более 20 мкм. Кроме того, для повышения эксплуатационных качеств ТЭГ разработан, в отличие от работ [18, 19], корпусный вариант изделия.
Проведенные испытания показали, что разработанный термоэлектрический генератор обеспечивает выходную мощность 3–56 мкВт при перепаде температур 25–100 K. Оценка полученных результатов показывает, что выходная удельная мощность разработанного ТЭГ составляет P/S = = 0.33 мкВт/кв. мм, что в 1.4 раза больше, чем в работе [19].
При использовании данных генераторов для схем питания систем мониторинга объектов с выходной мощностью до 10 мВт практически значимый перепад температур составляет порядка 100°. Данная мощность обеспечивается сборкой ячеек подобных генераторов площадью до 25 кв. см.
В основе разработки ТЭГ – моделирование физической структуры генератора. В качестве параметров моделирования используются: коэффициент Зеебека, удельное электрическое сопротивление, удельная теплопроводность. Значения параметров зависят от технологии и имеют большой разброс. Как следствие, в модели использовались усредненные значения параметров, известных из опубликованных данных и рассчитанных методом наименьших квадратов. Тем не менее, разброс в значениях результатов моделирования и эксперимента составил значительную величину – до 2 раз. Возможная причина – большая дисперсия значений параметров (см. рис. 2, рис. 3), достигающая 20–30%. Подобный эффект может быть промоделирован методом наихудшего случая, но для этого требуется соответствующие статистические данные по результатам изготовления и измерениям.
Список литературы
Champier D. Thermoelectric generators: A review of applications // Energy Conversion and Management. 2017. V. 140. P. 167–181.
Nguyen H.T., Nguyen V.T., Takahito O. Flexible thermoelectric power generator with Y-type structure using electrochemical deposition process // Applied Energy. 15 January 2018. V. 210. P. 467–476.
Deng F., Qiu H., Chen J., Wang L., Wang B. Wearable Thermoelectric Power Generators Combined With Flexible Supercapacitor for Low-Power Human Diagnosis Devices // IEEE Transactions on Industrial Electronics. February 2017. V. 64. № 2. P. 1477–1485.
Volvenko S., Dong Ge, Zavjalov S., Gruzdev A., Rashich A., Svechnikov E. Experimental wireless ultra wideband sensor network for data collection // Progress In Electromagnetics Research Symposium – Spring (PIERS). 22–25 May 2017.
Antonova E.E., Looman D.C. Finite element for thermoelectric devices in ANSYS // Proc. ICT’05. 24th International Conference on Thermoelectronics. Clemson. USA. 2005. P. 215–218.
Hogblom O., Andersson R. Analysis of thermoelectric generator performance by use of simulations and experiments // J. Electronic Materials. 2014. V. 43. № 6. P. 2247–2254.
Li W., Paul M.C. et al. Multiphysics simulations of a thermoelectric generator // Energy Procedia. 2015. V. 75. P. 633–638.
Geppert B., Groeneveld D., Korotkov A., Loboda V., Feldhoff A. Finite-Element Simulations of a Thermoelectric Generator and Their Experimental Validation // Energy Harvesting and Systems. 2015. V. 2(1). P. 94–105.
Korotkov A.S., Loboda V.V., Makarov S.B., Feldhoff A. Modeling Thermoelectric Generators Using the ANSYS Software Platform: Methodology, Practical Applications, and Prospects // Russian Microelectronics. 2017. V. 46. № 2. P. 131–138.
Korotkov A., Loboda V., Feldhoff A., Groeneveld D. Simulation of Thermoelectric Generators and Its Results Experimental Verification // Proc. IEEE International Symposium on Signals, Circuits and Systems (ISSCS 2017). 13–14 July 2017. Iasi. Romania. 2017.
Kim I.H., Choi S., Seo W.S., Cheong D.I. Preparation and Thermoelectric Properties of Bi2T2.7Se0.3 Nanocomposites // J. Korean Phys. Soc. 2012. V. 61. P. 1376–1380.
Lee G.E., Eum A.Y., Song K.M., Kim I.H., Lim Y.S. Preparation and Thermoelectric Properties of n-Type Bi2Te2.7Se0.3 // J. Electronic Materials. 2015. V. 40. P. 1579–1584.
Kim J.I., Lee E.S., Kim J.Y., Choi S.M. Thermoelectric properties of unoxidized graphene/Bi2Te2.7Se0.3 composites synthesized by exfoliation/re-assembly method // Phys. Status Solidi RRL 8. 2014. P. 357–361.
Lee K.H., Kim H.S., Kim S.I., Lee E.S., Lee S.M. Enhancement of Thermoelectric Figure of Merit for Bi0.5Sb1.5Te3 by Metal Nanoparticle Decoration // J. Electronic Materials. 2012. V. 41. P. 1165–1169.
Blank V.D., Buga S.G., Kulbachinskii V.A., Kytin V.G., Medvedev V.V. Thermoelectric properties of Bi0.5Sb1.5Te3/C60 nanocomposites // Physical Review. B 86. 2012. 075426.
Nguyen P.K., Lee K.H., Moon J., Kim S.I., Ahn K.A. Spark erosion: a high production rate method for producing Bi0.5Sb1.5Te3 nanoparticles with enhanced thermoelectric performance // Nanotechnology. 2012. V. 23. 415604. 7 p.
Annapragada S.R., Salamon T., Kolodner P., Hodes M., Garimella S.V. Determination of Electrical Resistivity in Thermoelectric Moduls (TEMs) from Modul Level Maesurements // IEEE Transactions on Components, Packaging and Manufacturing Technology. 2012. V. 2. № 4. April 2012. P. 668–676.
Snyder G.J., Lim J.R., Huang Chen-Kuo, Fleurial J.-P. Thermoelectric microdevice fabricated by a MEMS-like electrochemical process // Nature Materials. 2003. V. 2. Aug. 2003. P. 528–531.
Kim M.J., Oh T.S. Thermoelectric Thin Film Device of Cross-Plane Configuration Processed by Electrodeposition and Flip-Chip Bonding // Materials Transactions. 2012. V. 53. № 12. P. 2160–2165.
Дополнительные материалы отсутствуют.
Инструменты
Микроэлектроника