Химическая физика, 2021, T. 40, № 9, стр. 27-34
Энергоэффективность газификации плотного слоя твердых топлив в режиме фильтрационного горения
В. М. Кислов 1, *, М. В. Цветков 1, А. Ю. Зайченко 1, Д. Н. Подлесный 1, Е. А. Салганский 1
1 Институт проблем химической физики Российской академии наук
Черноголовка, Россия
* E-mail: vmkislov@icp.ac.ru
Поступила в редакцию 25.02.2021
После доработки 18.03.2021
Принята к публикации 22.03.2021
Аннотация
Выполнена оценка энергоэффективности газификации различных твердых топлив в режиме фильтрационного горения. Рассмотрены режимы газификации углеродных и органических топлив с влажностью до 70% и зольностью до 90%. Эффективность воздушной газификации углеродных топлив с малой влажностью не превышает 70%, а органических топлив – 85%. Эффективность воздушной газификации высоковлажных топлив может достигать 85–90%. Добавление пара в состав газообразного окислителя приводит к увеличению эффективности процесса. Эффективность паровоздушной газификации маловлажных низкозольных углеродных топлив достигает 85%. В случае органических топлив максимальная эффективность паровоздушной газификации наблюдается для топлив с зольностью 20–40%. Для высокореакционных топлив максимальная эффективность наблюдается для беззольных топлив. Если реакционная способность топлива низкая, максимальная эффективность газификации будет у высокозольных топлив.
ВВЕДЕНИЕ
Фильтрационное горение – один из перспективных методов переработки твердых топлив. Исследования фильтрационного горения различных видов углей, торфа, древесины и некоторых видов твердых горючих отходов показали, что данный режим имеет больший диапазон приемлемых для переработки зольности и влажности топлив, чем другие известные методы [1–3]. Это достигается в результате теплообмена между потоками твердых и газообразных веществ, движущихся навстречу друг другу относительно фронта химической реакции [4, 5].
В зависимости от теплофизических характеристик потоков твердой и газовой фаз могут реализоваться различные тепловые режимы горения [6, 7]. Наиболее эффективный теплообмен происходит при равенстве теплоемкостей потоков фаз, поэтому наличие в топливе заметного количества минеральных компонентов не всегда является его недостатком [8, 9]. При фильтрационном горении за счет противотока реагентов окислитель, поступающий через один из торцов реактора, нагревается при фильтрации через слой горячего зольного остатка, выходящего из зоны горения, а горячие газообразные продукты горения отдают свое тепло исходному топливу, поступающему через противоположный торец реактора [10, 11]. Таким образом, бóльшая часть тепла, выделяющегося в химических реакциях, не выносится из реактора, а концентрируется в зоне горения. За счет интенсивной рекуперации тепла от продуктов горения к исходным реагентам температура горения может быть существенно выше расчетной адиабатической [12, 13].
Экспериментально установлено, что эффективность переработки ряда трудногорючих материалов с малой зольностью, например углеводородных вязких жидкостей, может быть существенно увеличена путем смешения исходного топлива с твердым негорючим материалом [14, 15]. Полученные в этом случае энергетические параметры газификации имеют более высокие значения, чем при сжигании топлива с добавкой древесины или торфа [16, 17]. Вместе с тем определенные в результате экспериментов состав продуктов, температура и скорость горения не дают исчерпывающую информацию о характере процесса [18, 19]. Для корректного сопоставления фильтрационного горения с другими методами необходимо также учитывать энергоэффективность процесса [20, 21]. Параметром для такой оценки является коэффициент полезного действия (КПД) процесса [22]. Однако сопоставление значений КПД, приведенных в различных работах, затруднено тем, что при его расчете границы рассматриваемой энергосистемы задаются в значительной степени произвольно [23, 24], и авторы сами решают, какие потоки энергии на входе и выходе из системы следует учитывать.
Так, например, при оценке КПД газификатора важно решить, следует ли считать полезным физическое тепло продуктов газификации, поступающих в горелку? В качестве примера приведем расчет КПД газификации по обратному тепловому балансу процесса, когда из исходного КПД, равного 100%, вычитаются (выраженные в процентах) значения потерь тепла от различных источников [25]:
Как правило, величины химической и механической неполноты сгорания, а также физического тепла, выносимого из реактора золой, в сумме равны примерно 5% [26]. Потери тепла через стенку реактора у крупногабаритных реакторов составляют примерно 3–5% [27]. Потери тепла с выходящими газами для типичного режима газификации твердых топлив составляют примерно 10–15%, однако если горячий газ из реактора поступает непосредственно в горелку, то в этом случае содержащуюся в них энергию можно не считать потерянной [28, 29]. В зависимости от принятого варианта расчета значение КПД будет составлять либо 75–80%, либо примерно 90% [30]. Выводы, сделанные на основании таких расчетов, также будут разными: в первом случае оценка энергоэффективности применяемой технологии всего лишь удовлетворительная, во втором – данная технология оценена как высокоэффективная.
Расчет по обратному тепловому балансу процесса обычно используют для определения КПД котлов, но такой метод расчета неудобен, поскольку для различных режимов очень сложно точно определить все значения теплопотерь [31]. В промышленной энергетике принято рассчитывать КПД газификации, КПД газификатора и КПД энергетического комплекса [32, 33].
1. Коэффициентом полезного действия газификации называется отношение потенциального тепла газа к потенциальному теплу топлива, израсходованного на производство газа. Он не учитывает теплоту сгорания смол и физическое тепло поступающих реагентов.
2. Коэффициентом полезного действия газификатора, или термическим КПД газификатора, называется отношение потенциального тепла газа к сумме потенциального тепла топлива, израсходованного на производство газа, и теплосодержания окислителя. Данный параметр не учитывает теплоту сгорания смол. Ранее, когда в промышленности преимущественно газифицировали кокс и каменные угли, этой величиной можно было пренебречь; теперь, когда материалом для газификации в основном являются бурые угли, торф и древесина, теплоту сгорания смол не учитывать нельзя.
3. Коэффициент полезного действия энергетического комплекса определяется как отношение теплоты сгорания образующихся продуктов газификации (газа и смолы) к суммарным затратам энергии на газификацию, включающим теплоту сгорания топлива, теплосодержание дутья и расход энергии на вспомогательные устройства энергетического комплекса.
В настоящее время во многих работах энергоэффективность газификации определяют с помощью энергетического КПД, равного отношению энергии, получаемой при сгорании продуктов газификации, к суммарной энергии, введенной в систему [34]. При газификации в реактор поступают топливо и воздух при комнатной температуре и водяной пар при температуре 100 °С. Продуктами газификации являются горючие газообразные продукты (далее – горючие газы), пары воды, а при газификации пиролизующихся топлив – также смолы их термического разложения. Далее возможны два варианта использования образующихся горючих газов: 1) их можно подавать без предварительной подготовки в стандартное энергоустройство (например, в паровой котел или турбину) для получения тепловой или электрической энергии; 2) выделение из них жидких углеводородов (пиролизных смол) и раздельная подача газообразных и жидких горючих продуктов на оптимизированные энергоустановки. Первый вариант наиболее прост и уже реализован на многих предприятиях. Второй вариант более сложный, и для его промышленного внедрения необходимо решить ряд научных и технических проблем.
Главным критерием учета того или иного входящего потока в расчете КПД был его вклад в общий энергетический баланс. В этом случае КПД газификации определяется как отношение количества тепла, выделяющегося при сгорании газообразных и жидких продуктов газификации (Qg), к сумме теплоты сгорания газифицируемого топлива (Qf) и физического тепла входящих в газификатор реагентов (Qh):
Поскольку температура продуктов газификации на выходе из реактора, как правило, выше 100 °С, то для расчета КПД газификации можно использовать значения низшей теплоты сгорания [35]. Считалось, что влага, находящаяся в продуктах газификации, содержится в смолах.
Преимущество такого способа расчета, на наш взгляд, заключается, во-первых, в более четкой формулировке определения КПД газификации, а во-вторых, в том, что его расчет осуществляется на основе параметров, значения которых могут быть точно измерены в процессе работы газификатора. Это позволяет избежать необоснованного завышения значений КПД и более точно оценить полученный результат.
Цель настоящей работы – определение оптимальных режимов газификации различных твердых топлив в режиме фильтрационного горения. Основными управляющими параметрами были влажность и зольность топлива, а также реакционная способность коксового остатка.
РЕЗУЛЬТАТЫ И ИХ ОБСУЖДЕНИЕ
В настоящей работе при расчете КПД использовали результаты теоретических и экспериментальных работ по фильтрационному горению реакторного графита марки ГР-280, древесного угля марки А (ГОСТ 7657-84), березового активированного угля (БАУ-А, ГОСТ 6217-74) и березовой древесины. Описание экспериментальной установки, методики проведения экспериментов и результатов приведены в работах [36–38]. В работе [36] приведены результаты газификации воздушно-сухого древесного угля, газификация влажного древесного угля и гидролизного лигнина описана в работе [37], а древесины – в работе [38]. Описание теоретических моделей, исходных данных расчетов и результатов приведено в работах [39–42]. Модели воздушной и паровоздушной газификации углерода в стационарной постановке приведены в работах [39, 40], стационарная модель газификации органического топлива описана в работе [41]. Модель паровоздушной газификации углерода с учетом кинетики химических реакций в нестационарной постановке приведена в работе [42].
Результаты расчета паровоздушной газификации углерода представлены на рис. 1 в виде линий равных значений КПД паровоздушной газификации в следующих координатах: содержание углерода в смеси с инертным материалом – объемная концентрация пара в газообразном окислителе, выраженная в виде отношения мольных долей содержащихся в паровоздушной смеси паров воды и кислорода ([Н2О]/[О2]). С увеличением содержания углерода при фиксированном значении концентрации пара КПД газификации сначала резко возрастает, достигая максимального значения, после чего монотонно снижается. Максимальное значение КПД, равное 88%, достигается при содержании углерода 30% и концентрации пара в окислителе [Н2О]/[О2] = 1. Равенство теплоемкостей потоков твердой и газовой фаз является критерием энергоэффективности горения твердых топлив в фильтрационном режиме с противотоком [43].
Рис. 1.
Линии равных значений КПД паровоздушной газификации углерода в зависимости от содержания (а) горючего и мольного отношения пара к кислороду ([Н2О]/[О2]): 1 – 40%, 2 – 50%, 3 – 60%, 4 – 70%, 5 – 80%, 6 – 88%.
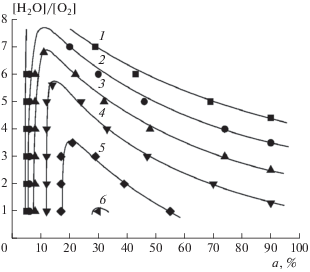
Экспериментальные исследования проводили с различными видами углеродных материалов. На рис. 2 приведены результаты экспериментов по газификации графита и древесного угля. Содержание пара в окислителе было постоянным ([Н2О]/[О2] = 6.2), средний размер частиц графита составлял 0.8 мм, древесного угля – 5 мм.
Рис. 2.
Экспериментальная зависимость КПД (Е) паровоздушной газификации ([H2O]/[O2] = 6.2) графита (кривая 1) и древесного угля (кривая 2) при постоянном составе окислителя от содержания (а) горючего; 3 – доля (f) сгоревшего графита, %.
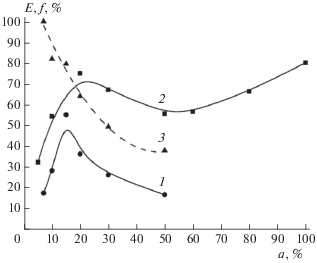
Графит является наиболее химически чистой формой углерода, однако низкая реакционная способность графита сильно затрудняет его сжигание. Изменение температурного режима может сильно изменить стехиометрию процесса [44, 45]. Если в ходе эксперимента поддерживать относительно невысокие температуры горения (1000–1300 °С), то за фронтом горения остается большое количество несгоревшего графита. При высоких температурах (1500–2000 °С) графит сгорает более полно, однако большинство конструкционных материалов не выдерживают таких температур. Проводить эксперименты с более реакционно-способными древесным и активированным углями технически проще, так как они хорошо горят даже при относительно невысоких температурах. Но они не являются химически чистой формой углерода, что может сказаться на характеристиках их горения.
С увеличением содержания графита в смеси до 15%, КПД газификации увеличивается примерно до 50%. Дальнейшее увеличение содержания графита приводит к резкому падению температуры горения, увеличению доли несгоревшего графита и снижению КПД газификации (рис. 2). Таким образом, при газификации графита наблюдается качественное соответствие данных расчета и эксперимента.
В экспериментах древесный уголь практически всегда сгорает полностью. Приведенные на рис. 2 данные показывают, что при тех же параметрах КПД газификации древесного угля заметно выше, чем КПД газификации графита. При газификации смесей с содержанием древесного угля до 50%, как и для случая с графитом, наблюдается локальный максимум (~75%) при содержании угля в смеси 20% и последующее падение КПД до ~55% при 50%-ном его содержании, однако затем величина КПД растет и достигает максимального значения (~80%) при газификации древесного угля без инертного материала. Наличие первого максимума связано с максимумом температуры горения, обусловленным равенством теплоемкостей потоков твердой и газовой фаз при этих условиях. Второй максимум появляется за счет увеличения выхода СО и Н2, образующихся в зоне восстановления волны горения при взаимодействии углерода с диоксидом углерода и парами воды. Так как в этом случае тепло горячих газообразных продуктов, выходящих из зоны горения, не теряется с газами, выходящими из газификатора, а в значительной степени идет на осуществление восстановительных реакций, то КПД газификации увеличивается.
Экспериментальная зависимость КПД паровоздушной газификации БАУ-А от содержания угля в смеси с инертным материалом и концентрации пара в газообразном окислителе представлена на рис. 3. Приведенные на рис. 3–5 точки получены методом интерполяции экспериментальных данных: зависимостей КПД газификации от доли топлива в смеси (при постоянном составе окислителя) и зависимостей КПД газификации от состава окислителя (при постоянной доле топлива в смеси).
Рис. 3.
Линии равных значений КПД паровоздушной газификации воздушно-сухого угля марки БАУ-А в зависимости от содержания угля в смеси (а) с инертным материалом и мольного отношения пара к кислороду ([Н2О]/[О2]): 1 – 65%, 2 – 70%, 3 – 75%, 4 – 80%, 5 – 85%.
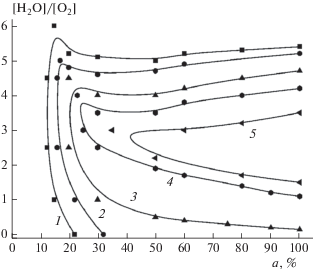
Рис. 4.
Линии равных значений КПД паровоздушной газификации гидролизного лигнина в зависимости от содержания (а) горючего и мольного отношения пара к кислороду ([Н2О]/[О2]): 1 – 70%, 2 – 75%, 3 – 80%, 4 – 83%.
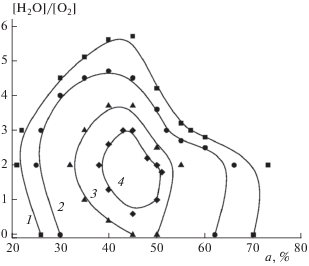
Рис. 5.
Линии равных значений КПД паровоздушной газификации древесины при различном содержании древесины в смеси (а) и мольного отношения пара к кислороду ([Н2О]/[О2]): 1 – 70%, 2 – 75%, 3 – 80%, 4 – 85%.
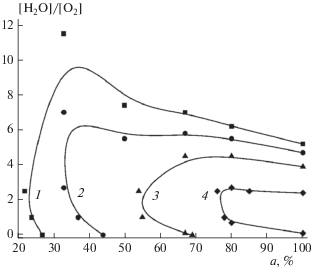
При постоянном содержании угля в смеси с увеличением содержания пара в окислителе также наблюдается локальный максимум величины КПД при содержании угля ~20%. Максимальное значение КПД (80%) также достигается при газификации древесного угля без инертного материала при объемном отношении [H2O]/[O2] = 2.5.
Таким образом, несмотря на то, что активированный уголь по химической чистоте ближе к углероду, чем древесный уголь, при его газификации максимальное значение КПД также достигается при газификации без инертного материала. Это объясняется значительно более высокой реакционной способностью древесного и активированного углей по сравнению с графитом, поэтому они могут активно взаимодействовать с окислителем и участвовать в восстановительных реакциях даже при относительно невысоких температурах.
При фильтрационном горении органических твердых топлив имеет место стадия пиролиза, которая оказывает существенное влияние на процесс горения. В зависимости от условий, установившихся в зоне пиролиза, количество и качество образующихся смолы, воды, газов и коксового остатка могут существенно различаться [46].
Общий вид приведенных на рис. 4 зависимостей изолиний КПД паровоздушной газификации гидролизного лигнина Сыктывкарского ЛПК [37, 47] качественно сходен с расчетными значениями КПД газификации углерода и результатами экспериментов с графитом, приведенными на рис. 1 и 2. С ростом содержания лигнина в смеси с 30 до 50% последний сгорал полностью, температура горения росла и увеличивался КПД газификации. При увеличении содержания лигнина с 50 до 100% температура горения и КПД газификации снижались, а доля недогоревшего кокса в твердых продуктах росла до ~25%. Смещение области максимальных значений КПД в сторону увеличения доли топлива в газифицируемой смеси по сравнению с расчетным значением (рис. 1) обусловлено пиролизом лигнина, выход кокса из которого составляет ~50%.
При газификации древесины на стадии пиролиза образуется ~15% кокса, 25–27% воды и до 60% летучих веществ, состоящих из газообразных веществ и смолы, состав и выход которых зависит от режимных факторов процесса. На рис. 5 показаны линии равных значений КПД паровоздушной газификации сухой древесины. Равенство теплоемкостей потоков твердой и газовой фаз достигается при газификации составов с содержанием древесины ~60%. При газификации составов с содержанием древесины >60% значительное влияние на состав продуктов оказывает стадия пиролиза. Максимальное значение КПД газификации древесины (88%), так же как и при газификации древесного и активированного угля марки БАУ-А достигается при газификации топлива без инертного материала.
Такие различия определяются реакционной способностью образующегося коксового остатка, поступающего в зону окисления. При пиролизе лигнина графитизация его коксового остатка начинается уже при температуре 600 °C [48], поэтому образующийся коксовый остаток, как правило, имеет низкую реакционную способность. Вследствие этого для лигнина (как и для графита) имеет место четко выраженная зависимость состава продуктов и КПД газификации от температуры горения. При газификации древесины ее коксовый остаток (древесный уголь) имеет высокую реакционную способность, поэтому состав образующихся продуктов и КПД газификации древесины не так сильно зависят от температуры горения, как при газификации графита и лигнина.
Наличие сверхадиабатических разогревов при фильтрационном горении твердого топлива позволяет эффективно газифицировать высоковлажные топлива. В работах [37, 49] на примере древесины и угля марки БАУ-А показана возможность воздушной газификации твердого топлива с инертным материалом с влажностью топлива до 70%. При этом такое высокое содержание влаги в топливе практически не оказывало влияния на характеристики горения. На рис. 6 показаны линии равных значений КПД воздушной газификации влажного угля в координатах содержание угля – влажность угля. Влажность рассчитывали по массовому содержанию воды в угле. Содержание угля в смеси с инертным материалом определяли в пересчете на сухую массу угля.
Рис. 6.
Линии равных значений КПД воздушной газификации влажного угля в координатах содержание угля (а) – влажность угля (Wt): 1 – 30%, 2 – 40%, 3 – 50%, 4 – 60%, 5 – 70%, 6 – 75%, 7 – 85%.
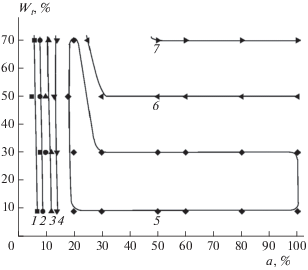
При содержании топлива в газифицируемой смеси до 20% увеличение влажности практически не влияет на КПД газификации, незначительное снижение заметно только при газификации составов с содержанием угля менее 10% и влажности выше 50% (рис. 6). При постоянной влажности угля увеличение его содержания в смеси приводит к резкому росту КПД газификации с максимальным значением в интервале содержаний угля 20–30%. При содержании угля в смеси более 30% КПД газификации не изменяется. Для углей с влажностью до 30% при газификации смесей с содержанием угля больше 20% процесс проходит с близким к максимально возможному значением КПД воздушной газификации (72%). Увеличение влажности угля с 30 до 70% приводит к росту значения КПД с 70 до 85%. Это связано с тем, что при горении составов с содержанием угля выше 20% теплоемкость потока газообразных продуктов становится больше, чем теплоемкость потока твердой фазы. В результате этого твердые продукты сгорания покидают зону горения при низких, а газообразные компоненты – при высоких температурах, создавая перед зоной горения широкую зону прогрева исходного топлива. При газификации таких смесей инертного материала с углем, имеющим низкую влажность, газообразные продукты покидают газификатор при относительно высоких температурах, и содержащееся в них физическое тепло не расходуется полезно. При газификации влажных углей тепло выходящего продукт-газа расходуется внутри реактора на испарение влаги топлива, при этом температура продукт-газа на выходе из реактора снижается. Таким образом, при газификации влажного угля достигается двойной энергетический эффект: собственного тепловыделения процесса оказывается достаточно и для сушки угля, и для его газификации с практически теми же характеристиками, что и у сухого угля.
На рис. 7 показаны значения КПД воздушной газификации смесей влажной древесины с инертным материалом при содержании сухой древесины в смеси 30 и 63%. В случае одинаковой влажности топлива при газификации влажной древесины затраты тепла, выделяющегося при сгорании древесного угля, на нагрев и испарение влаги в расчете на единицу массы топлива будут гораздо выше, чем при газификации влажного угля. Поэтому увеличение влажности древесины сверх некоторого предела начинает оказывать влияние на ход процесса.
Рис. 7.
Значения КПД (E) воздушной газификации смесей древесины различной влажности (Wt) с инертным материалом: 1–3 – содержание древесины в смеси составляет 30%, кривые 4–6 – 63%; 1, 4 – КПД, рассчитанный по теплоте сгорания газообразных продуктов; 2, 5 – КПД, рассчитанный по теплоте сгорания смолы; 3, 6 – суммарный КПД.
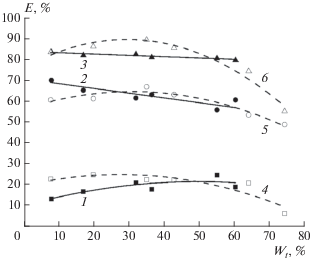
С увеличением влажности древесины примерно до 40% эффективность газификации практически не изменяется. При большей влажности скорость горения и выход смол заметно снижаются, а объем газообразных продуктов увеличивается, но их теплота сгорания заметно уменьшается, что приводит к снижению эффективности газификации [37].
Как правило, влажность топлива редко превышает 50%. Коэффициент полезного действия газификации биомассы с такой влажностью мало отличается от КПД газификации сухой биомассы, а для углей КПД газификации влажного угля даже выше, чем у сухого угля. Однако при выборе способа переработки высоковлажного топлива также следует учитывать, что при газификации содержащаяся в топливе влага в виде пара выходит вместе с образующимися газообразными продуктами. Для топлив с влажностью выше 40% объем образующихся паров воды может в 2–3 раза превышать объем газообразных продуктов. Сжигание такого влажного продукт-газа без предварительного отделения влаги может быть сильно затруднено.
ВЫВОДЫ
1. Проведенный выше анализ энергоэффективности переработки твердых топлив показывает, что зависимость энергетического КПД газификации углеродных топлив от содержания их горючей части и влажности в значительной мере определяется реакционной способностью образующегося коксового остатка.
2. Для топлив с низкореакционным типом коксового остатка определяющими факторами являются кинетика процесса и, как следствие, сильная зависимость характеристик горения от температуры. Наибольшая энергетическая эффективность газификации таких трудногорючих топлив в режиме фильтрационного горения достигается при равенстве теплоемкостей потоков твердой и газовой фаз, при котором температура горения максимальна. Для малозольных топлив наиболее действенным способом варьирования соотношения теплоемкостей потоков фаз является добавление к газифицируемому топливу частиц твердого инертного материала. При газификации трудногорючих топлив добавка инертного материала позволяет существенно повысить температуру горения и увеличить КПД газификации. Коэффициент полезного действия газификации таких топлив без инертной добавки существенно ниже, так как происходит снижение теплоты сгорания газообразных продуктов и степени сгорания топлива.
3. Для топлив с высокореакционным коксовым остатком подобных кинетических ограничений нет, поэтому энергетически более выгодными становятся режимы переработки топлив с малой зольностью.
4. Газификация в фильтрационном режиме позволяет перерабатывать топлива с влажностью 40–50% практически без снижения энергетических характеристик газификации. Сушка влажных топлив происходит внутри реактора за счет тепла выходящих из зоны горения газообразных продуктов газификации.
Исследование выполнено в рамках госзадания (регистрационный номер ЦИТИС № АААА-А19-119022690098-3).
Список литературы
Guerrero F., Espinoza L., Ripoll N. et al. // Front. Chem. 2020. V. 8. P. 145; https://doi.org/10.3389/fchem.2020.00145
Dorofeenko S.O., Polianczyk E.V. // Intern. J. Hydrog. Energy. 2019. V. 44. № 57. P. 30039; https://doi.org/10.1016/j.ijhydene.2019.09.208
Lutsenko N.A., Fetsov S.S. // Renew. Energy. 2020. V. 162. P. 466; https://doi.org/10.1016/j.renene.2020.08.029
Сеплярский Б.С., Кочетков Р.А., Лисина Т.Г., Абзалов Н.И. // Хим. физика. 2020. Т. 39. № 1. С. 31; https://doi.org/10.31857/S0207401X20010136
Кришеник П.М., Костин С.В., Озерковская Н.И., Шкадинский К.Г. // Хим. физика. 2019. Т. 38. № 2. С. 45; https://doi.org/10.1134/S0207401X19020092
Глазов С.В. // Теорет. основы хим. технологии. 2019. Т. 53. № 3. С. 290; https://doi.org/10.1134/S0040357119020052
Сеплярский Б.С., Кочетков Р.А., Лисина Т.Г. // Хим. физика. 2019. Т. 38. № 3. С. 24; https://doi.org/10.1134/S0207401X19030063
Dorofeenko S.O., Polianczyk E.V. // Fuel. 2021. V. 291. P. 120255; https://doi.org/10.1016/j.fuel.2021.120255
Сеплярский Б.С., Кочетков Р.А., Ковалев И.Д., Лисина Т.Г. // Хим. физика. 2018. Т. 37. № 6. С. 55; https://doi.org/10.7868/S0207401X18060079
Bubnovich V., Hernandez H., Toledo M., Flores C. // Fuel. 2021. V. 291. P. 120117; https://doi.org/10.1016/j.fuel.2020.120117
Кочетов Н.А., Сеплярский Б.С. // Хим. физика. 2020. Т. 39. № 9. С. 39; https://doi.org/10.31857/S0207401X20090058
Глазов С.В. // Теорет. основы хим. технологии. 2019. Т. 53. № 1. С. 54; https://doi.org/10.1134/S0040357119010032
Salgansky E.A., Zaichenko A.Y., Podlesniy D.N. et al. // Intern. J. Hydrog. Energy. 2020. V. 45. № 35. P. 17270; https://doi.org/10.1016/j.ijhydene.2020.04.177
Зайченко А.Ю., Глазов С.В., Салганский Е.А. и др. // Теорет. основы хим. технологии. 2017. Т. 51. № 5. С. 525; https://doi.org/10.7868/S0040357117050153
Glushkov D.O., Kuznetsov G.V., Nigay A.G., Yanovsky V.A. // Acta Astronaut. 2020. V. 177. P. 66; https://doi.org/10.1016/j.actaastro.2020.07.018
Santiago Y.C., González A.M., Venturini O.J., Maya D.M.Y. // Energy. 2021. V. 215. ID 119210; https://doi.org/10.1016/j.energy.2020.119210
Guerrero F., Arriagada A., Muñoz F. et al. // Fuel. 2021. V. 289. ID 119756; https://doi.org/10.1016/j.fuel.2020.119756
Vershinina K., Strizhak P., Dorokhov V., Romanov D. // Fuel. 2021. V. 285. ID 119098; https://doi.org/10.1016/j.fuel.2020.119098
Тереза А.М., Агафонов Г.Л., Андержанов Э.К. и др. // Хим. физика. 2020. Т. 39. № 8. С. 58; https://doi.org/10.31857/S0207401X20080129
Рыжков А.Ф., Абаимов Н.А., Донской И.Г., Свищёв Д.А. // Физика горения и взрыва. 2018. Т. 54. №. 3. С. 96; https://doi.org/10.15372/FGV20180310
Федяева О.Н., Востриков А.А. // Сверхкритические флюиды: теория и практика. 2018. Т. 13. № 3. С. 8.
Svishchev D.A., Kozlov A.N., Donskoy I.G., Ryzhkov A.F. // Fuel. 2016. V. 168. P. 91; https://doi.org/10.1016/j.fuel.2015.11.066
Ozonoh M., Oboirien B.O., Higginson A., Daramola M.O. // Renew. Energy. 2020. V. 145. P. 2253; https://doi.org/10.1016/j.renene.2019.07.136
Cerone N., Zimbardi F., Contuzzi L. et al. // Energy Convers. Manag. 2020. V. 221. ID 113116; https://doi.org/10.1016/j.enconman.2020.113116
Qin N., Li R.J. // Appl. Therm. Eng. 2020. V. 171. ID 115021; https://doi.org/10.1016/j.applthermaleng.2020.115021
Глушков Д.О., Кузнецов Г.В., Стрижак П.А. // Хим. физика. 2015. Т. 34. № 3. С. 48; https://doi.org/10.7868/S0207401X1503005X
González A.M., Jaén R.L., Lora E.E.S. // Renew. Energy. 2020. V. 147. P. 1151; https://doi.org/10.1016/j.renene.2019.09.045
Liu J., Luo X., Yao S., Li Q., Wang W. // Waste Manag. 2020. V. 105. P. 450; https://doi.org/10.1016/j.wasman.2020.02.040
Шмелев В.М. // Хим. физика. 2020. Т. 39. № 12. С. 43; https://doi.org/10.31857/S0207401X20120122
Донской И.Г. // Журн. прикл. химии. 2020. Т. 93. № 4. С. 506; https://doi.org/10.31857/S0044461820040052
Terhan M., Comakli K. // Appl. Therm. Eng. 2017. V. 121. P. 380; https://doi.org/10.1016/j.applthermaleng.2017.04.091
Ju Y., Lee C.H. // Energy Convers. Manag. 2017. V. 143. P. 123; https://doi.org/10.1016/j.enconman.2017.03.082
Fan X., Yang L., Jiang J. // Renew. Energy. 2020. V. 158. P. 32; https://doi.org/10.1016/j.renene.2020.05.145
Shayan E., Zare V., Mirzaee I.J.E.C. // Energy Convers. Manag. 2018. V. 159. P. 30; https://doi.org/10.1016/j.enconman.2017.12.096
Ramos A., Rouboa A. // Renew. Energy. 2020. V. 155. P. 1211; https://doi.org/10.1016/j.renene.2020.03.158
Амелин И.И., Салганский Е.А., Волкова Н.Н. и др. // Изв. РАН. Сер. хим. 2011. № 6. С. 1125.
Кислов В.М., Глазов С.В., Червонная Н.А. и др. // ХТТ. 2008. № 3. С. 9.
Салганский Е.А., Кислов В.М., Глазов С.В., Жолудев А.Ф., Манелис Г.Б. // Физика горения и взрыва. 2010. Т. 46. № 5. С. 42.
Салганский Е.А., Фурсов В.П., Глазов С.В., Салганская М.В., Манелис Г.Б. // Физика горения и взрыва. 2003. Т. 39. № 1. С. 44.
Салганский Е.А., Фурсов В.П., Глазов С.В., Салганская М.В., Манелис Г.Б. // Физика горения и взрыва. 2006. Т. 42. № 1. С. 65.
Салганский Е.А., Полианчик Е.В., Манелис Г.Б. // Физика горения и взрыва. 2013. Т. 49. № 1. С. 45.
Салганский Е.А., Кислов В.М., Глазов С.В., Жолудев А.Ф., Манелис Г.Б. // Физика горения и взрыва. 2008. Т. 44. № 3. С. 30.
Polianczyk E.V., Dorofeenko S.O. // Intern. J. Hydrog. Energy. 2019. V. 44. № 8. P. 4079; https://doi.org/10.1016/j.ijhydene.2018.12.117
Тереза А.М., Андержанов Э.К. // Хим. физика. 2019. Т. 38. № 8. С. 58; https://doi.org/10.1134/S0207401X19080120
Tereza A.M., Medvedev S.P., Smirnov V.N. // Acta Astronaut. 2020. V. 176. P. 653; https://doi.org/10.1016/j.actaastro.2020.03.045
Salgansky E.A., Kislov V.M., Glazov S.V., Salganskaya M.V. // J. Combustion. 2016. Article ID 9637082; https://doi.org/10.1155/2016/9637082
Дудкина Н.А. Дис. … канд. хим. наук. Черноголовка: ИХФ АН СССР, 1991.
Николенко Ю.М., Опра Д.П., Цветников А.К. и др. // Изв. вузов. Химия и хим. технология. 2016. Т. 59. № 9. С. 92.
Салганская М.В., Глазов С.В., Салганский Е.А. и др. // Хим. физика. 2008. Т. 27. № 1. С. 27.
Дополнительные материалы отсутствуют.
Инструменты
Химическая физика