Химия высоких энергий, 2022, T. 56, № 3, стр. 227-234
Получение ультрадисперсного порошка железа совмещением электролиза и высоковольтного разряда
С. В. Ким a, b, *, М. И. Байкенов a, А. А. Айнабаев a, К. С. Ибишев b, М. Г. Мейрамов c, В. П. Григорьева d, Ф. Ма e
a Карагандинский университет им. Е.А. Букетова
100028 Караганда, Республика Казахстан
b Химико-металлургический институт им. Ж. Абишева
100009 Караганда, Республика Казахстан
c Институт органического синтеза и углехимии Республики Казахстан
100009 Караганда, Республика Казахстан
d АО Институт топлива, катализа и электрохимии им. Д.В. Сокольского
050010 Алматы, Казахстан
e Синьцзянский университет
830000 СУАР Урумчи, Китайская Народная Республика
* E-mail: vanquishV8@mail.ru
Поступила в редакцию 21.09.2021
После доработки 10.01.2022
Принята к публикации 14.01.2022
- EDN: VXUVTH
- DOI: 10.31857/S0023119322030068
Аннотация
Определены оптимальные условия получения ультрадисперсного порошка железа при совмещении процессов электролиза и высоковольтного разряда. Установлено, что максимальный выход по току q = 97.88% достигается при плотности тока D = 10 000 А/м2; концентрации сульфата железа C (FeSO4 · 7H2О) = 50 г/л; продолжительности процесса τ = 60 мин; концентрации сульфата аммония C ((NH4)2SO4) = 40 г/л и величины высоковольтного напряжения U = 8000 В. Методами электронной микроскопии установлено, что полученный порошок железа содержит наноразмерные частицы, величина удельной поверхности которых, определенная с помощью низкотемпературной адсорбции азота по методу БЭТ, составила 31.5 ± 0.3 м2/г. Анализ Мёссбауэровской спектроскопии показал наличие магнитоупорядоченных фаз: α-Fe и γ-Fe2O3; фазы, близкой к гидроксиду α-FeOOH (гетит) и возможное наличие смеси β-FeOOH (акоганит) и γ-FeOOH (лепидокрокит). Установлено, что конверсия фенантрена при гидрогенизации в течение 60 мин в присутствии полученного порошка железа выше, чем в присутствии промышленного железо-хромового катализатора СТК-1 и достигает 32.99%.
ВВЕДЕНИЕ
Научно-технический потенциал процесса протекания высоковольтного разряда в жидкости привлекает внимание исследователей уже много лет и перспективы его применения для получения наноразмерных материалов основаны на простоте, низких энергозатратах и возможности получения наноразмерных порошков не только индивидуальных веществ, но и различных соединений [1]. Возможность регулирования основных характеристик (размера и химического состава) получаемых продуктов достигается изменением параметров разряда (коронный, искровой, тлеющий и т.д.), полярности тока (прямой и обратной полярности), параметров тока (прямой и переменный), материалов электродов и состава электролита [1–3].
Обработка заготовок электрическими разрядами может вызвать протекание процессов закалки и легирования в поверхностных слоях заготовки, что приводит к упрочнению поверхности и увеличение ее коррозионной стойкости [4]. Также воздействие электрического разряда на жидкость через воздушный слой может инициировать свободнорадикальные реакции с участием радикалов H∙, OH∙, O∙, что может приводить к образованию перекиси водорода [5–7]. Накопление перекиси водорода в растворе может быть использовано для обеззараживания воды, при этом выход перекиси водорода зависит от материалов электродов и подаваемого на них напряжения, а также от проводимости воды и формы разряда [8].
Совмещение гидравлического эффекта Юткина с процессом электролиза представляет научно-практический интерес, поскольку импульсный электрический разряд в жидкости сопровождается рядом явлений, таких как образование плазмы, ультразвук, ионизирующее и электромагнитное излучения, ударно-волновое воздействие и т.д. [9, 10]. Комплексное воздействие импульсного электрического разряда в жидкости может способствовать интенсификации электрохимических процессов, поскольку возникающие ультразвуковые колебания, могут вызвать депассивацию анода [11].
В настоящей работе приводятся результаты исследований по изучению влияния высоковольтного разряда на процесс электрохимического получения ультрадисперсного порошка железа. Также установлены каталитические свойства полученного порошка железа при гидрогенизации фенантрена.
ЭКСПЕРИМЕНТАЛЬНАЯ ЧАСТЬ
Для электрохимического синтеза ультрадисперсного порошка железа использовали водный электролит, содержащий сульфат железа FeSO4·7H2О, сульфат аммония (NH4)2SO4. В качестве катода был выбран титановый электрод, а в качестве растворимого анода было использовано железо марки АРМКО (содержание железа 99.8–99.9%).
Реактор для синтеза был сконструирован, таким образом, чтобы при электрохимическом растворении железного анода прикатодная область подвергалась электроимпульсному воздействию искрового разряда высокого напряжения. Для осуществления данной схемы, в верхней части реактора были установлены катод из титана для синтеза порошка железа и два вольфрамовых анода. Вольфрамовые аноды в виде острия были направлены перпендикулярно к плоскости катода по одному с каждой стороны и предназначены для высоковольтного воздействия электрического разряда. Зазор между катодом и вольфрамовыми анодами был выставлен на уровне 3 мм. Для обеспечения протекания электроискрового разряда во время процесса электролиза катод был подключен к обоим источникам: постоянного напряжения и высоковольтного напряжения. Ранее данным методом был получен наноразмерный порошок никеля, схема установки и результаты полученных исследований представлены в работе [12].
Поскольку в данной работе для синтеза ультрадисперсных порошков железа использовались многокомпонентные электролиты, а процесс электролиз проводился при различных плотностях тока и сопровождался импульсным воздействием разрядов высокого напряжения различной величины, то для установления зависимостей выхода по току от различных факторов был использован вероятностно-детерминированный метод [13]. Данный метод позволяет определять факторы, оказывающие на влияние различные физико-химические процессы, в его основе лежит уравнение М.М. Протодьяконова для описания статистических многофакторных зависимостей:
где yi – частная функция, i – номер частной функции, n – количество частных функций.В качестве факторов были взяты: плотность тока (D, А/м2); концентрация сульфата железа (C (FeSO4 · 7H2О), г/л); продолжительность процесса (τ, мин); концентрация сульфата аммония (C ((NH4)2SO4), г/л) и величина высоковольтного напряжения (U, кВ).
Факторы и их уровни (диапазон изменения значений), представлены в табл. 1.
Таблица 1.
Факторы и их уровни
Факторы | Уровни факторов | ||||
---|---|---|---|---|---|
Плотность тока DК, А/м2 | 5000 | 7500 | 10 000 | 12 500 | 15 000 |
Концентрация FeSO4·7H2О, г/л | 40 | 50 | 60 | 70 | 80 |
Продолжительность процесса τ, мин | 20 | 30 | 40 | 50 | 60 |
Концентрация (NH4)2SO4, г/л | 25 | 30 | 35 | 40 | 45 |
Величина высоковольтного напряжения, U, В | 8000 | 10 000 | 12 000 | 14 000 | 16 000 |
Диапазоны уровней каждого фактора были установлены экспериментально. Концентрацию сульфата железа варьировали в интервале от 40–80 г/л, что является достаточным для поддержания концентрации ионов железа в электролите. Время синтеза в интервале 20–60 мин достаточно для образования необходимого количества порошка железа, концентрация сульфата аммония в диапазоне 25–45 г/л обеспечивает стабильность значений pH электролита. Минимальное значение высоковольтного разряда 8 кВ обусловлено тем, что меньше этой величины не происходит импульсного электроискрового пробоя, поскольку электролит содержит повышающую электропроводность, добавку сульфата аммония. Максимальное значение высоковольтного разряда обусловлено физическими возможностями источника. Морфология поверхности полученного порошка железа установлена с помощью сканирующего электронного микроскопа MIRA 3 TESCAN.
Рентгенофазовый анализ проведен с помощью дифрактометра ДРОН 4–07 с применением рентгеновского излучения с длиной волны λ = = 0.179085 нм (CoKα-излучение), режим съемки: скорость развeртки 4 град/мин, рабочие параметры трубки: 30 кВ, 20 мА.
Идентификация полученных веществ проведена с помощью рентгенометрической картотеки ASTM.
Мёссбауэровская спектроскопия проведена с применением источника возбужденных ядер 57Co в матрице хрома, активностью 100 мКи. Спектры обрабатывались на ПК методом наименьших квадратов. Величины изомерных сдвигов (IS) приведены относительно α-Fe. Температура снятия спектров – 293 К. Режим съемки “на просвет”.
Величина удельной поверхности полученного порошка железа определена на установке Sorbi MS с помощью низкотемпературной адсорбции азота по методу БЭТ, изотермы адсорбции азота получены при 77 К.
Для оценки влияния каталитических свойств различных наноматериалов на механизм гидрогенизации тяжелого сырья в качестве модельных объектов широко применяют антрацен и фенантрен, которые входят в состав сырой нефти, креозота и каменноугольной смолы [14].
Для установления каталитической активности синтезированный ультрадисперсный порошок железа использован в качестве катализатора при гидрогенизаци фенантрена в автоклаве при давлении 5 МПа, температуре 400ºC и времени проведения процесса 60 мин.
Химический состав исходного фенантрена, а также продуктов гидрогенизации, установлен с помощью газового хроматографа Agilent 7890 А с масс-селективным детектором Agilent 5975 C. Анализ проводили при следующих условиях: тип колонки – Rxi-5ms; длина колонки – 30 м; диаметр колонки – 0.25 мм; толщина адсорбента колонки – 0.25 µм; температура испарителя – 250°С; температура колонки – 60–300°С; скорость нагрева колонки – 8°С/мин; температура источника ионов – 230°С; температура квадрупольного конденсатора – 150°С; газ-носитель – гелий; давление газа в колонке – 2 psi; объем пробы – 0.2 мкл; режим ввода – с разделением потока (split); режим регистрации масс-спектров – сканирование (scan); библиотека – NIST 08; метод расчета состава фракций – относительно площади пиков (полуколичественный метод). Обработка результатов производилась автоматически при помощи программы GS-MSD Data Analysis.
РЕЗУЛЬТАТЫ И ОБСУЖДЕНИЕ
Значения выходов по току (qэ, %) порошка железа, полученные при различных значениях плотности тока (D, А/м2); концентрации сульфата железа (C (FeSO4 · 7H2О), г/л); продолжительности процесса (τ, мин); концентрации сульфата аммония (C ((NH4)2SO4), г/л) и величины высоковольтного напряжения (U, кВ) приведены в табл. 2.
После группировки опытных данных по уровням факторов, получим частные зависимости выхода по току от каждого фактора:
Обобщенное уравнение, согласно выбранной методике [13], будет иметь следующий вид:
Существенный функциональный характер полученной математической модели подтверждается значением коэффициента корреляции R = 0.8.
Таблица 2.
Значения выходов по току (qэ, %) порошка железа, полученные при различных значениях выбранных факторов
№ опыта | D, А/м2 | $C\,({\text{FeS}}{{{\text{O}}}_{4}}),$ г/л | τ , мин | C ((NH4)2SO4), г/л | U, кВ | qэ, % |
---|---|---|---|---|---|---|
1 | 5000 | 40 | 20 | 25 | 8000 | 66.72 |
2 | 5000 | 60 | 40 | 35 | 12 000 | 57.88 |
3 | 5000 | 50 | 30 | 30 | 10 000 | 71.01 |
4 | 5000 | 80 | 60 | 45 | 16 000 | 81.01 |
5 | 5000 | 70 | 50 | 40 | 14 000 | 66.11 |
6 | 10000 | 40 | 40 | 30 | 16 000 | 79.48 |
7 | 10000 | 60 | 30 | 45 | 14 000 | 78.85 |
8 | 10000 | 50 | 60 | 40 | 8000 | 97.88 |
9 | 10000 | 80 | 50 | 25 | 12 000 | 75.33 |
10 | 10000 | 70 | 20 | 35 | 10 000 | 66.18 |
11 | 7500 | 40 | 30 | 40 | 12 000 | 73.84 |
12 | 7500 | 60 | 60 | 25 | 10 000 | 76.07 |
13 | 7500 | 50 | 50 | 35 | 16 000 | 67.51 |
14 | 7500 | 80 | 20 | 30 | 14 000 | 43.78 |
15 | 7500 | 70 | 40 | 45 | 8000 | 91.98 |
16 | 15 000 | 40 | 60 | 35 | 14 000 | 97.72 |
17 | 15 000 | 60 | 50 | 30 | 8000 | 77.43 |
18 | 15 000 | 50 | 20 | 45 | 12 000 | 92.31 |
19 | 15 000 | 80 | 40 | 40 | 10 000 | 85.7 |
20 | 15 000 | 70 | 30 | 25 | 16 000 | 54.68 |
21 | 12 500 | 40 | 50 | 45 | 10 000 | 93.38 |
22 | 12 500 | 60 | 20 | 40 | 16 000 | 75.84 |
23 | 12 500 | 50 | 40 | 25 | 14 000 | 52.01 |
24 | 12 500 | 80 | 30 | 35 | 8000 | 78.78 |
25 | 12 500 | 70 | 60 | 30 | 12 000 | 61.65 |
В результате проведенных экспериментов было установлено, что наибольший выход по току q = = 97.88% достигается при плотности тока D = = 10 000 А/м2; концентрации сульфата железа C (FeSO4 · 7H2О) = 50 г/л; продолжительности процесса τ = 60 мин; концентрации сульфата аммония C ((NH4)2SO4) = 40 г/л величины высоковольтного напряжения U = 8000 В.
На снимке сканирующей электронной микроскопии, представленном на рис. 1, видно, что полученный порошок железа представляет собой агрегаты, состоящие из частиц нанометрового уровня.
Из дифрактограммы на рис. 2 видно, что полученный порошок железа представляет смесь α-Fe (рефлексы: 2.02; 1.43; 1.17 Å) и FeO(OH) (4.98; 4.19; 3.40; 2.69; 2.58; 2.45; 2.26; 2.18; 1.92; 1.80; 1.72; 1.60; 1.56; 1.51; 1.47; 1.45; 1.36; 1.31 Å).
По результатам Мёссбауэровской спектроскопии, представленной на рис. 3, было установлено, что в полученном порошке железа содержатся магнитоупорядоченные фазы: α-Fe; γ-Fe2O3; фаза, близкая к гидроксиду α-FeOOH (гетит), возможно, замещенный.
Парамагнитные фазы: возможно, смесь гидроксидов железа β-FeOOH (акоганит) и γ-FeOOH (лепидокрокит) и (или) мелкодисперсных (менее 8 нм) частиц вышеперечисленных магнитоупорядоченных фаз, которые при таком размере частиц не показывают зеемановского сверхтонкого расщепления.
Удельная поверхность полученного порошка железа, определенная с помощью низкотемпературной адсорбции азота по методу БЭТ, составила 31.5 ± 0.3 м2/г.
Анализ, проведенный с помощью газового хроматографа, показал, что в составе исходного фенантрена содержались: флуорен – 3.67% и дибензотиофен – 2.08%.
Состав продуктов, полученных в результате каталитической гидрогенизации фенантрена в присутствии полученного порошка железа при давлении 5 МПа, температуре 400°C и времени проведения процесса 60 мин приведены в табл. 3, хроматограмма представлена на рис. 4.
Таблица 3.
Состав продуктов гидрогенизации фенантрена в присутствии полученного порошка железа и промышленного железо-хромового катализатора СТК-1
Порядковый номер | Соединение | Порошок Fe | СТК-1 |
---|---|---|---|
Выход, % | |||
1 | Фенол | 0.36 | – |
2 | Нафталин | 0.13 | 0.09 |
3 | 1-метилнафталин | 0.18 | – |
4 | 2-этинилнафталин | 0.45 | – |
5 | 1-этилнафталин | 1.38 | – |
6 | 2-этилнафталин | – | 0.69 |
7 | 2-этилдифенил | 0.16 | – |
8 | 4-этилдифенил | – | 0.07 |
9 | 2-метилдифенилметан | 0.56 | – |
10 | Флуорен | 3.2 | 2.84 |
11 | 9-метилфлуорен | 1.02 | 0.78 |
12 | Бензол, 1,1'-этилиденбис | 0.84 | – |
13 | 9,10-дигидроантрацен | 4.39 | 0.25 |
14 | 9,10-дигидрофенантрен | 16.83 | 18.61 |
15 | 1,2,3,4-тетрагидроантрацен | 3.27 | – |
16 | 1,2,3,4-тетрагидрофенантрен | 5.97 | 4.81 |
17 | Фенантрен | 61.26 | 71.86 |
На рис. 4 нумерация пиков приведена в соответствии с порядковым номером соединения в Табл. 3.
Для сравнения каталитической активности полученного ультрадисперсного порошка железа с известным промышленным катализатором была проведена гидрогенизация фенантрена в присутствии промышленного железо-хромового катализатора СТК-1 (Fe2O3 – 83.0%, Cr2O3 – 7.5%, CuO – 2.0%) при тех же условиях.
Состав продуктов, полученных в результате гидрогенизации фенантрена в присутствии промышленного железо-хромового катализатора СТК-1 представлен в табл. 3, хроматограмма приведена на рис. 5. На рис. 5 нумерация пиков приведена в соответствии с порядковым номером соединения в табл. 3.
Рис. 5.
Хроматограмма продуктов гидрогенизации фенантрена в присутствии промышленного железо-хромового катализатора СТК-1.
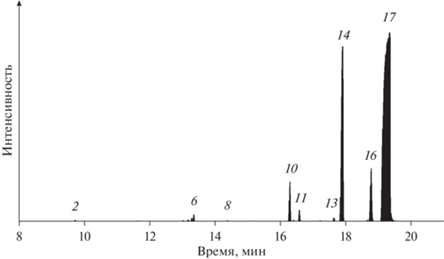
Из результатов, представленных в табл. 3 видно, что каталитические свойства полученного ультрадисперсного порошка железа выше промышленного железо-хромового катализатора. Конверсия фенантрена при каталитической гидрогенизации в течение 60 мин в присутствии полученного порошка железа составила 32.99%, при этом на долю гидропроизводных приходится 30.46%. Для промышленного железо-хромового катализатора СТК-1 конверсия фенантрена при тех же условиях составила 22.39%.
ЗАКЛЮЧЕНИЕ
В результате проведенных исследований установлено, что совмещение высоковольтного разряда и электролиза на постоянном токе является эффективным методом получения ультрадисперсных порошков железа, обладающих высокой каталитической активностью. Эффективность метода подтверждается не только высокими значениями выходов по току, но и относительной простотой конструкции установки, позволяющей во время электрохимического восстановления порошка железа воздействовать на катод импульсными электрическими разрядами высокого напряжения. При этом данный процесс проводится при обычных условиях и для образования ультрадисперсного порошка железа достаточно напряжения импульсных электрических разрядов в 8 кВ. Высокая каталитическая активность полученного порошка железа характеризуется тем, что в составе продуктов гидрогенизации фенантрена при использовании синтезированного порошка железа в качестве катализатора содержание гидропроизводных выше примерно на 10%, чем при использовании промышленного железо-хромового катализатора СТК-1.
Список литературы
Бураков В.С., Савастенко Н.А., Тарасенко Н.В., Невар Е.А. // Журн. прикладной спектроскопии. 2008. Т. 75. № 1. С. 111.
Saito G., Akiyama T. // J. Nanomaterials. 2015. V. 2015. Article ID 123696.
Horikoshi S., Serpone N. // RSC Advances. 2017. Iss. 75. P. 47196.
Krastev D., Yordanov B. // Micro and Nanosystems. 2014. V. 6. Iss. 1. P. 21.
Аристова Н.А., Пискарев И.М., Ивановский А.В., Селемир В.Д., Спиров Г.М., Шлепкин С.И. // Журн. физической химии. 2004. Т. 78. № 7. С. 1326.
Шутов Д.А., Батова Н.А., Рыбкин В.В. // Химия высоких энергий. 2020. Т. 54. № 1. С. 68.
Пискарев И.М. // Химия высоких энергий. 2020. Т. 54. № 3. С. 223.
Сон Э.Е., Суворов И.Ф., Какуров С.В., Гайсин Ал.Ф., Самитова Г.Т., Соловьева Т.Л., Юдин А.С., Рахлецова Т.В. // Теплофизика высоких температур. 2014. Т. 52. № 4. С. 512.
Юткин Л.А. Электрогидравлический эффект и его применение в промышленности. Л.: Машиностроение, 1986. 253 с.
Пробой жидкостей при импульсном напряжении / Под ред. проф., д. т. н. В.Я. Ушакова. Томск: НТЛ, 2005. 488 с.
Аксельруд Г.А., Молчанов А.Д. Растворение твердых веществ. М.: Химия, 1977. 272 с.
Ибишев К.С., Малышев В.П., Ким С.В., Сарсембаев Б.Ш., Егоров Н.Б. // Химия высоких энергий. 2017. Т. 51. № 3. С. 234.
Малышев В.П. Вероятностно-детерминированное отображение. Караганда: Гылым, 1994. 376 с.
Wang K., Guan J., He D., Zhang Q. // Advanced Materials Research 2012. V. 512–515. P. 2200.L
Дополнительные материалы отсутствуют.
Инструменты
Химия высоких энергий