Теплофизика высоких температур, 2022, T. 60, № 4, стр. 584-588
Пиролитическая конверсия биомассы в синтез-газ с заданным соотношением [H2]/[CO]
В. А. Синельщиков 1, *, Г. А. Сычев 1, Ю. М. Фалеева 1
1 Объединенный институт высоких температур РАН
Москва, Россия
* E-mail: sinelshchikov@mail.ru
Поступила в редакцию 05.07.2021
После доработки 05.11.2021
Принята к публикации 23.11.2021
- EDN: VESIIX
- DOI: 10.31857/S0040364422040044
Аннотация
Представлены экспериментальные данные по влиянию величины массовых потерь при торрефикации на состав и объемный выход синтез-газа, полученного методом двухстадийной пиролитической конверсии древесной биомассы и торфа. Показано, что предварительная торрефикация биомассы позволяет получать синтез-газ с заданным соотношением объемных долей водорода и монооксида углерода в диапазоне от 1 до 2. Параметром, определяющим состав синтез-газа, является величина массовых потерь при торрефикации в расчете на сухое беззольное состояние.
ВВЕДЕНИЕ
Синтез-газ, представляющий собой смесь, основными компонентами которой являются водород и монооксид углерода, может быть использован как в качестве газообразного топлива в газовых котлах, двигателях внутреннего сгорания и газотурбинных агрегатах, так и в качестве сырья для ряда химических технологий, в частности для получения жидких синтетических топлив [1, 2]. Исходя из того, для каких целей предполагается использовать синтез-газ, формулируются требования к его составу и характеристикам. Состав синтез-газа определяется видом исходного сырья и методом его переработки.
Использование термических методов переработки дает возможность получать синтез-газ практически из любого вида углеводородного сырья [3]. Из ископаемых углеводородных ресурсов синтез-газ получают методами паровой и углекислотной конверсии метана, парциальным окислением метана, паровоздушной конверсией угля. Для конверсии возобновляемого углеводородного сырья (биомассы) в синтез-газ применяются воздушная, кислородная, плазменная газификация и пиролиз.
Одной из проблем, характерных для большинства методов газификации биомассы и особенно актуальной при использовании пиролитических методов переработки, является высокая концентрация конденсирующихся органических соединений в получаемой газовой смеси [4]. Наличие таких соединений существенно ограничивает возможность дальнейшего использования полученного газа без его предварительной очистки. Данные соединения конденсируются в технологических трактах, приводя к их засорению, дезактивируют катализаторы, применяемые при использовании синтез-газа в химической промышленности и, в частности, при производстве жидких моторных топлив. Для очистки синтез-газа используются механические, термические и каталитические методы [5]. Естественно, что использование термических и каталитических методов, позволяющих конвертировать конденсирующиеся органические соединения в компоненты синтез-газа, предпочтительно, поскольку фактически приводит к увеличению степени конверсии исходной биомассы в газообразное топливо.
Синтез-газ, свободный от конденсирующихся летучих соединений, можно получать как за счет применения соответствующих технологий внутри реактора газификации (первичные методы), так и за счет очистки газа на выходе из реактора (вторичные методы) [6, 7]. В обоих случаях при использовании каталитических методов применяются в основном одни и те же катализаторы. В [8] при сопоставлении активности и стабильности различных катализаторов, используемых для удаления конденсирующихся органических соединений, в их число включен биоуголь. Из представленных данных следует, что по своим свойствам биоуголь не уступает, а в ряде случаев и превосходит другие катализаторы. Механизм взаимодействия конденсирующихся органических соединений с поверхностью биоугля в присутствии воды и СО2, используемых в качестве газифицирующих агентов и образующихся при пиролизе биомассы, исследован в [9]. Авторы [8] также отмечают, что за счет взаимодействия с парами воды и СО2 (реакция Будуара) биоуголь постоянно расходуется, однако, поскольку он является одним из продуктов, образующихся при газификации, это обстоятельство не представляется важным. В то же время упомянутые реакции, с одной стороны, приводят к активации поверхности биоугля и тем самым способствуют стабилизации его свойств как катализатора, а с другой, в результате этих реакций образуются Н2 и СО, т.е. основные компоненты синтез-газа.
Использование биоугля для переработки конденсирующихся летучих соединений лежит в основе метода двухстадийной пиролитической конверсии, в котором на первой стадии проводится пиролиз исходного сырья, а на второй – высокотемпературный крекинг пиролизных газов и паров путем их фильтрации через нагретый слой биоугля [10, 11]. В результате можно получать чистый синтез-газ с низшей удельной теплотой сгорания на уровне 11 МДж/м3. Одновременно за счет гетерогенного крекинга как неконденсирующихся, так и конденсирующихся летучих продуктов пиролиза при их взаимодействии с нагретой углеродной поверхностью существенно увеличивается эффективность энергетической конверсии различных видов возобновляемого углеводородного сырья в синтез-газ [12].
Подход, связанный с пространственным разделением зон пиролиза и газификации, используется в так называемых многоступенчатых газификаторах [13]. В частности, в [14, 15] он успешно применен для уменьшения содержания смол в получаемом газе. В газификаторах, исследованных в [14, 15], первая стадия аналогична первой стадии в методе двухстадийной пиролитической конверсии. Однако на второй стадии требуемая температура в зоне крекинга достигалась за счет сжигания части летучих продуктов пиролиза. Подача в зону крекинга воздуха, необходимого для сжигания, приводила к наличию в получаемом газе большого количества азота и, соответственно, снижению его теплоты сгорания до 6.5 МДж/м3.
Как следует из данных, приведенных в [12], отношение мольных долей водорода и монооксида углерода [H2]/[CO] в составе синтез-газа, получаемого методом двухстадийной пиролитической конверсии основных видов биомассы растительного происхождения (древесина, торф, отходы сельскохозяйственного производства), изменяется в диапазоне 1–1.2. Это отношение, а также объем получаемого синтез-газа определяются элементным составом перерабатываемого сырья, а именно, содержанием в нем кислорода и водорода, и могут быть рассчитаны на основе уравнений материального баланса [12]. Таким образом, подбирая вид сырья с соответствующим содержанием водорода и кислорода или целенаправленно изменяя элементный состав перерабатываемого сырья перед его конверсией, можно получать синтез-газ с заранее заданным составом.
В [12] показано, что, применяя метод двухстадийной пиролитической конверсии для переработки осадка сточных вод, характеризующегося относительно низким по сравнению с биомассой растительного происхождения содержанием кислорода, можно получать синтез-газ с соотношением объемных долей [H2]/[CO], близким к 2. Это дает возможность в дальнейшем использовать полученный синтез-газ для производства жидких моторных топлив [16].
В процессе торрефикации, используемой для улучшения потребительских свойств твердого биотоплива [17, 18], происходит изменение элементного состава биомассы. При этом, как следует из диаграммы Ван Кревелена для древесной биомассы, с ужесточением режима торрефикации, т.е. с увеличением температуры и времени выдержки, соотношение между содержанием водорода и кислорода в торрефицированном сырье изменяется в сторону увеличения содержания водорода [19]. Цель работы состоит в экспериментальном подтверждении возможности использования данного эффекта для получения синтез-газа с заданным соотношением [H2]/[CO].
ЭКСПЕРИМЕНТАЛЬНАЯ УСТАНОВКА И МЕТОДИКА ПРОВЕДЕНИЯ ЭКСПЕРИМЕНТОВ
В качестве сырья для получения синтез-газа в данной работе использовались древесные и торфяные пеллеты цилиндрической формы диаметром 6 и длиной 10 мм. Основные характеристики пеллет приведены в таблице вместе с данными из [19]. Торрефикация пеллет проводилась при различных температурах в интервале от 230 до 350°С. Темп нагрева составлял 10°С/мин, время выдержки при заданной температуре равно 30 мин. Элементный состав исходных и торрефицированных пеллет определялся с помощью HCNS-анализатора Vario MACRO Cube.
Характеристики исходного сырья в расчете на сухое состояние
Сырье | Зольность, мас. % | Элементный состав, мас. % | Содержание летучих, мас. % | Фиксированный углерод, мас. % | ||||
---|---|---|---|---|---|---|---|---|
H | C | N | S | O | ||||
Древесные пеллеты | 0.3 | 49.9 | 6.1 | 0.1 | – | 43.6 | 82.0 | 17.7 |
Торфяные пеллеты | 5.7 | 54.7 | 5.1 | 1.1 | 0.1 | 33.3 | 64.0 | 30.3 |
Древесная стружка [19] | 0.2 | 49.5 | 6.2 | 0.2 | – | 43.9 | 85.1 | 14.7 |
Эксперименты по двухстадийной пиролитической конверсии выбранных видов биомассы в синтез-газ проводились на установке, аналогичной использованной ранее в работах [11, 12]. Принципиальная схема установки представлена на рис. 1.
Рис. 1.
Схема установки: 1 – двухсекционная печь, 2 – зона пиролиза, 3 – зона крекинга летучих продуктов пиролиза, 4 – холодильник, 5 – газосчетчик барабанный, 6 – газгольдер, 7 – газовый анализатор.
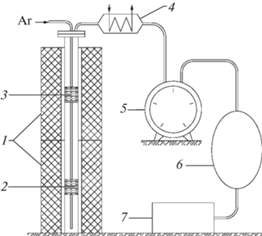
Реактор, выполненный в виде металлической трубы диаметром 37 мм и высотой 850 мм, помещался в двухсекционную печь с независимыми нагревателями. В зонах пиролиза и крекинга устанавливались тигли, плотно прилегавшие к стенкам реактора и имевшие газопроницаемое перфорированное дно. В тигель, расположенный в зоне пиролиза, помещалось перерабатываемое сырье, в качестве которого использовались исходные или предварительно торрефицированные пеллеты из древесины и торфа. В тигель, расположенный в зоне крекинга, помещался древесный уголь, полученный путем пиролиза древесины. Объем зоны крекинга, заполненной биоуглем, выбирался таким образом, чтобы при заданной скорости нагрева перерабатываемого сырья время взаимодействия летучих продуктов пиролиза с биоуглем составляло несколько секунд. Согласно [11, 20], при температуре в зоне крекинга, равной 1000°C, этого времени достаточно для полной конверсии конденсирующихся летучих продуктов в синтез-газ.
Перед началом эксперимента реактор и весь газовый тракт продувались аргоном для обеспечения инертной газовой среды. В начале эксперимента зона крекинга нагревалась до температуры 1000°C, которая в дальнейшем поддерживалась на этом уровне в процессе всего эксперимента. Затем установка еще раз продувалась аргоном и включался нагреватель зоны пиролиза, которая нагревалась до 1000°C со скоростью 7°C/мин. Выходящая из реактора газовая смесь направлялась в водоохлаждаемый холодильник, затем проходила через барабанный газосчетчик с жидкостным затвором и собиралась в газгольдере. В конце эксперимента при достижении в зоне пиролиза температуры 1000°C установка еще раз продувалась аргоном для того, чтобы оставшаяся в реакторе, газосчетчике и подводящих магистралях смесь газов поступила в газгольдер. После этого интегральный состав газовой смеси, собранной в газгольдере, измерялся с помощью анализатора газа MRU Vario Plus Industrial. Результаты измерений состава и объемного выхода газа пересчитывались таким образом, чтобы исключить объемную долю аргона.
РЕЗУЛЬТАТЫ ИССЛЕДОВАНИЙ И ОБСУЖДЕНИЕ
На основе данных по элементному составу исходных и торрефицированных пеллет построена диаграмма Ван Кревелена, представленная на рис. 2. Видно, что с увеличением массовых потерь при торрефикации отношение содержания водорода к содержанию кислорода как в древесине, так и в торфе увеличивается.
Рис. 2.
Диаграмма Ван Кревелена: 1 – древесные пеллеты, 2 – стружка древесины хвойных пород [19], 3 – торфяные пеллеты; стрелка – направление, в котором происходит ужесточение режимов торрефикации и увеличение массовых потерь.

На рис. 2 также приведены данные из [19]. В [19] интервал температур торрефикации составлял 240–340°С, нагрев осуществлялся за несколько минут, а время выдержки составляло 60 мин. Несмотря на различие в режимных параметрах процесса торрефикации, результаты, полученные в данной работе, хорошо согласуются с результатами [19]. Отмеченное совпадение косвенно подтверждает вывод, сделанный в [21], о том, что вместо двух режимных параметров, характеризующих процесс торрефикации (температура и время выдержки), для описания свойств торрефицированной биомассы и, в частности, ее элементного состава, можно использовать только величину массовых потерь в расчете на сухое беззольное состояние. Именно эта величина будет использована в дальнейшем при обсуждении состава синтез-газа, который можно получить из торрефицированной биомассы методом двухстадийной пиролитической конверсии.
Из результатов газового анализа следует, что в состав полученного синтез-газа помимо Н2 и СО входили СН4, СО2. При этом общая объемная доля СН4, СО2 не превышала 4%. На рис. 3 представлены экспериментальные данные, характеризующие отношение объемных долей Н2 и СО в синтез-газе, полученном из исходных и торрефицированных при различных условиях древесных и торфяных пеллет. На рис. 4 приведены данные по удельному объемному выходу синтез-газа. При этом в обоих случаях в качестве определяющего параметра использована величина массовых потерь при торрефикации в расчете на сухое беззольное состояние.
Рис. 3.
Отношение мольных долей [H2]/[CO] в синтез-газе из исходного и торрефицированного сырья в зависимости от величины массовых потерь при торрефикации: 1, 4 – древесные пеллеты; 2 – стружка древесины хвойных пород [19]; 3, 5 – торфяные пеллеты; 1–3 – расчет; 4, 5 – эксперимент.
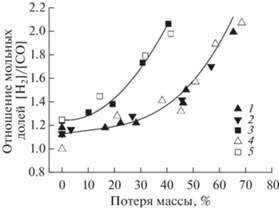
Рис. 4.
Удельный объемный выход синтез-газа из исходного и торрефицированного сырья в зависимости от величины массовых потерь при торрефикации: 1‒5 – то же, что на рис. 3.
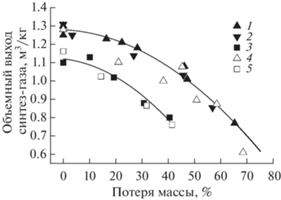
Так же на рисунках приведены результаты расчета отношения [Н2]/[СО] и объемного выхода синтез-газа, выполненные на основе уравнений материального баланса с использованием данных элементного анализа. Предположение о том, что в процессе двухстадийной пиролитической конверсии весь водород, содержащийся в перерабатываемом сырье, выделяется в виде H2, а кислород в виде CO, подтверждается как экспериментальными данными по составу синтез-газа (объемная доля H2 и CO более 96%), так и хорошим согласием между результатами эксперимента и расчета (рис. 3 и 4).
Таким образом, за счет предварительной торрефикации исходного сырья и последующей его переработки методом двухстадийной пиролитической конверсии из древесины и торфа можно получать синтез-газ с отношением мольных долей [H2]/[CO] в диапазоне 1–2. Резкое увеличение объемного содержания водорода в синтез-газе, полученном из древесных и торфяных пеллет, начинается при использовании торрефицированного сырья, массовые потери которого составляют более 30 и 20% соответственно. Одновременно существенно падает удельный объемный выход синтез-газа (см. рис. 4), поскольку с ростом массовых потерь при торрефикации в торрефицированном сырье уменьшается содержание летучих продуктов.
ЗАКЛЮЧЕНИЕ
Экспериментально показано, что сочетание двух методов термической переработки биомассы растительного происхождения, а именно торрефикации и двухстадийной пиролитической конверсии, может быть использовано для получения синтез-газа с заранее заданным соотношением объемных долей Н2 и СО. Увеличение объемной доли Н2 в получаемом синтез-газе достигается за счет изменения элементного состава биомассы, происходящего в процессе торрефикации. Возможность целенаправленно менять состав синтез-газа существенно расширяет область его дальнейшего применения в химической промышленности. В частности, синтез-газ с соотношением объемных долей водорода и монооксида углерода, равным 2, может быть использован для производства жидких моторных топлив.
Работа выполнена при финансовой поддержке Министерства науки и высшего образования РФ.
Список литературы
Hagos F.Y., Aziz A.R.A., Sulaiman S.A. Trends of Syngas as a Fuel in Internal Combustion Engines // Adv. Mech. Eng. 2014. 401587.
Wang L., Weller C.L., Jones D.D., Hanna M.A. Contemporary Issues in Thermal Gasification of Biomass and its Application to Electricity and Fuel Production // Biomass Bioenergy. 2008. V. 32. P. 573.
Hydrogen and Syngas Production and Purification Technologies / Eds. Liu K., Song C., Subramani V. USA: John Wiley & Sons, 2010. 533 p.
Milne T.A., Evans R.J., Abatzoglou N. Biomass Gasification “Tars”: Their Nature, Formation, and Conversion. National Renewable Energy Laboratory (NREL). NREL/TP-570-25357. Colorado, 1998. 121 p.
Anis S., Zainal Z.A. Tar Reduction in Biomass Producer Gas via Mechanical, Catalytic, and Thermal Methods: A Review // Renewable Sustainable Energy Rev. 2011. V. 15. P. 2355.
Devi L., Ptasinski K.J., Janssen F.J.J.G. A Review of the Primary Measures for Tar Elimination in Biomass Ga-sification Processes // Biomass Bioenergy. 2003. V. 24. P. 125.
Abu El-Rub Z., Bramer E.A., Brem G. Review of Catalysts for Tar Elimination in Biomass Gasification // Ind. Eng. Chem. Res. 2004. V. 43. P. 6911.
Abu El-Rub Z., Bramer E.A., Brem G. Experimental Comparison of Biomass Chars with Other Catalysts for Tar Reduction // Fuel. 2008. V. 87. P. 2243.
Feng D., Zhao Y., Zhang Y., Sun S. Effects of H2O and CO2 on the Homogeneous Conversion and Heterogeneous Reforming of Biomass Tar over Biochar // Int. J. Hydrogen Energy. 2017. V. 42. P. 13070.
Chembukulam S.K., Dandge A.S., Kovilur N.L., Seshagiri R.K., Vaidyeswaran R. Smokeless Fuel from Carbonized Sawdust // Ind. Eng. Chem. Prod. Res. Dev. 1981. V. 20. P. 714.
Батенин В.М., Зайченко В.М., Косов В.Ф., Синельщиков В.А. Пиролитическая конверсия биомассы в газообразное топливо // Докл. РАН. 2012. Т. 446. № 2. С. 179.
Лавренов В.А., Ларина О.М., Синельщиков В.А., Сычев Г.А. Двухстадийная пиролитическая конверсия различных видов биомассы в синтез-газ // ТВТ. 2016. Т. 54. № 6. С. 950.
Heidenreich S., Foscolo P.U. New Concepts in Biomass Gasification // Prog. Energy Combust. Sci. 2015. V. 46. P. 72.
Brandt P., Larsen E., Henriksen U. High Tar Reduction in a Two-Stage Gasifier // Energy Fuels. 2000. V. 14. P. 816.
Henriksen U., Ahrenfeldt J., Jensen T.K., Gøbel B., Bentzen J.D., Hindsgaul C., Sørensen L.H. The Design, Construction and Operation of a 75 kW Two-stage Gasifier // Energy. 2006. V. 31. P. 1542.
Larina O.M., Lishchiner I.I., Malova O.V., Zaichenko V.M. Obtaining Main Components of Liquid Motor Fuels from Sewage Sludge // Proc. 26th Biomass Conference and Exhibition. Copenhagen, 2018. P. 1051.
Bergman P.C.A., Kiel J.H.A. Torrefaction for Biomass Upgrading // Proc. 14th Europ. Biomass Conference and Exhibition. Paris, 2005. P. 206.
Kosov V.V., Sinelshchikov V.A., Sytchev G.A., Zaichenko V.M. Effect of Torrefaction on Properties of Solid Granula-ted Fuel of Different Biomass Types // High Temp. 2014. V. 52. № 6. P. 907.
Peng J.H., Bi X.T., Sokhansanj S., Lim C.J. Torrefaction and Densification of Different Species of Softwood Residues // Fuel. 2013. V. 111. P. 411.
Kosov V.V., Kosov V.F., Zaichenko V.M. Investigation of a Two-stage Process of Biomass Gasification // Chem. Eng. Trans. 2015. V. 43. P. 457.
Директор Л.Б., Синельщиков В.А., Сычев Г.А. Теплофизические свойства летучих продуктов низкотемпературного пиролиза древесной биомассы // ТВТ. 2020. Т. 58. № 1. С. 47.
Дополнительные материалы отсутствуют.
Инструменты
Теплофизика высоких температур