Теплофизика высоких температур, 2021, T. 59, № 3, стр. 467-480
Пиролитические методы термической переработки твердых коммунальных отходов
В. В. Хасхачих 1, *, О. М. Ларина 1, Г. А. Сычев 1, Г. Я. Герасимов 2, В. М. Зайченко 1
1 Объединенный институт высоких температур РАН
Москва, Россия
2 Институт механики МГУ им. М.В. Ломоносова
Москва, Россия
* E-mail: v.khaskhachikh@gmail.com
Поступила в редакцию 25.04.2020
После доработки 10.08.2020
Принята к публикации 20.10.2020
Аннотация
Представлены результаты исследований применения пиролитических методов переработки твердых коммунальных отходов в жидкое и газообразное топливо. Рассмотрены особенности и типы пиролитического процесса, детально проанализированы основные продукты пиролиза, полученные при различных температурах и скоростях нагрева исходной массы твердых коммунальных отходов. Поскольку жидкие продукты, полученные при обычном пиролизе, содержат большое количество кислородсодержащих соединений и воды, для получения высококачественного котельного или транспортного топлива используются каталитические методы. Рассмотрены основные типы катализаторов, их свойства и степень влияния на процесс. Проанализированы преимущества двухстадийного процесса, в котором продукты пиролиза на второй стадии процесса подвергаются высокотемпературному каталитическому крекингу с образованием синтез-газа.
ОГЛАВЛЕНИЕ
Введение
Закономерности процесса пиролиза
Характеристика продуктов пиролиза
Каталитический пиролиз
Двухстадийная пиролитическая конверсия ТКО
Типы реакторов пиролиза
Экологические аспекты пиролитических методов
Заключение
Список литературы
ВВЕДЕНИЕ
Одной из наиболее социально значимых экологических проблем в современном мире является проблема обращения с твердыми коммунальными отходами (ТКО), объем которых непрерывно увеличивается. Так, в 2016 г. в Российской Федерации было произведено 260 млн м3 ТКО, из которых менее 10% было направлено на мусороперерабатывающие или мусоросжигательные заводы [1]. Основная масса ТКО вывозится на полигоны, деятельность которых приводит к загрязнению атмосферы, почвы и грунтовых вод, негативно влияет на растительный и животный мир, ухудшает качество жизни населения близлежащих территорий [2]. С другой стороны, размещение на полигонах отходов, не прошедших предварительную сортировку, приводит к безвозвратной потере ценных видов сырья и материалов (бумага, стекло, металл, пластик и др.), пригодных к повторной переработке, а также к необходимости вывода значительного количества земель из хозяйственного оборота [3].
Практика обращения с ТКО в развитых странах показывает, что основное направление в решении проблемы утилизации отходов связано с их вовлечением в повторное использование. Для этих целей в сфере обращения с отходами разработан принцип 3R (Reduce – снижение образования, Reuse – повторное использование, Recycle – переработка во вторичное сырье), направленный на минимизацию количества отходов, подлежащих захоронению [4]. В европейских странах, которые являются лидерами в отрасли утилизации и обезвреживания отходов, доля ТКО, вовлеченных в повторное использование, достигает 80–87%, что значительно превышает аналогичный показатель для нашей страны [3, 5].
Наиболее рациональным способом утилизации ТКО является их повторное использование в качестве альтернативного источника энергии (waste-to-energy) [6]. Сжигание ТКО широко распространено в мировой практике и позволяет не только получать энергию от сжигания необработанных или несортированных отходов, но также уменьшать их объем почти на 90%, что обеспечивает отказ от использования полигонов [7]. С другой стороны, в результате сжигания отходов получается твердый остаток (зола) и газообразные вещества, зачастую представляющие еще большую опасность с экологической точки зрения. Для снижения вредных выбросов на современных мусоросжигательных заводах применяются многоступенчатые системы газоочистки, стоимость которых, как правило, превышает стоимость основного оборудования [8].
Технологии, основанные на термическом разложении (пиролизе) ТКО, можно рассматривать в качестве альтернативы их прямому сжиганию [9]. Пиролитические методы термической переработки твердых отходов позволяют уменьшить количество вредных выбросов, в частности, крайне токсичных полихлорированных дибензо-пара-диоксинов и дибензофуранов (PCDD/Fs) [10], а также не требуют дорогостоящей подготовки топлива и приспособлены для переработки отходов различного состава [11]. Следует отметить, что жидкие продукты пиролиза (пиролитическое масло) содержат большое количество кислородсодержащих соединений и поэтому не приспособлены для прямого сжигания в энергетических установках. По этой причине в последнее время интенсивно разрабатываются двухстадийные методы термической переработки ТКО, в которых выделяемые в процессе пиролиза летучие соединения подвергаются последующему каталитическому крекингу с получением синтез-газа. Данный газ может использоваться как топливо для электрогенерирующих энергоустановок или в качестве сырья для производства компонентов жидких моторных топлив [12].
В данной статье представлен краткий обзор экспериментальных и теоретических работ по исследованию различных методов пиролитической переработки ТКО в топливо, пригодное к использованию в различных энергетических установках.
ЗАКОНОМЕРНОСТИ ПРОЦЕССА ПИРОЛИЗА
Под пиролизом понимается процесс, который связан с термическим разложением органических составляющих ТКО в атмосфере инертных газов. По сравнению со сжиганием пиролиз имеет более низкую температуру процесса и, соответственно, меньшие выбросы вредных веществ в атмосферу [13]. Пиролизные установки более приспособлены к различным типам твердых отходов, чем установки для их сжигания, что позволяет перерабатывать составляющие отходов, трудно поддающиеся утилизации (пластмасса, автопокрышки, отработанные масла и другие) [14]. Процесс пиролиза позволяет преобразовывать материалы с низкой удельной энергией в топливо с высокой удельной энергией, одновременно восстанавливая ценные химические вещества [15]. Одним из значительных преимуществ данного процесса является использование многих видов сырья, включая промышленные, коммунальные и медицинские отходы.
Процесс термического разложения углеводородного материала, входящего с состав ТКО, можно представить в виде трех отдельных стадий [16]. На первой стадии происходит сушка исходного сырья. Далее происходит пиролиз сухого материала с выделением летучих компонентов. Процесс сопровождается фрагментацией и усадкой перерабатываемого материала. И, наконец, на заключительной стадии процесса продукты пиролиза подвергаются дальнейшему преобразованию во вторичных химических реакциях. Схематично процесс термического разложения ТКО в инертной атмосфере представлен на рис. 1. Первичный пиролиз представляет собой разрыв химических связей в крупных углеводородных цепях органических составляющих ТКО при температурах от 250 до 600°C с образованием углеводородных молекул и молекул неконденсирующихся газов. Под вторичным пиролизом понимается дальнейшее преобразование продуктов первичного пиролиза, находящихся в высокотемпературной зоне реактора. Этот процесс обычно включает реакции реформинга, крекинга, дегидратации и другие.
В зависимости от условий проведения процесса пиролиз подразделяется на быстрый, среднескоростной и медленный [17]. Для быстрого пиролиза характерны высокие скорости нагрева (порядка 103°C/мин и выше) до температур порядка 500–600°C и малое время пребывания летучих продуктов пиролиза в высокотемпературной зоне (∼1 с) [18]. Это накладывает ограничения на размер частиц исходного материала. Размер и форма частиц исходного материала не столь критичны для среднескоростного пиролиза, который позволяет перерабатывать более широкий спектр ТКО [19]. Среднескоростной пиролиз характеризуется скоростями нагрева порядка 100°C/мин, а время пребывания летучих веществ в высокотемпературной зоне увеличивается до 10–30 с. Следует также отметить, что пиролитическое масло, полученное при среднескоростном пиролизе биомассы, имеет улучшенные характеристики и может непосредственно использоваться в качестве топлива для дизельных двигателей [20]. Медленный пиролиз (торрефикация и карбонизация) характеризуется низкими температурами процесса и является обычной практикой для получения твердого топлива из биомассы. Торрефикацией принято называть термическую обработку биомассы при температурах 250–280°C в инертной среде [21]. Торрефикация применяется для повышения потребительских свойств твердых топлив из биомассы. Процесс карбонизации воспроизводит в ускоренном виде процесс образования ископаемых углей [22].
Твердые бытовые отходы содержат широкий спектр разнородных материалов. Типичная смесь ТКО для стран Европы состоит в основном из пищевых и садовых отходов (32%), бумаги и картона (29%), стекла (11%) и пластика (8%) [11]. Для Москвы соответствующая смесь содержит бумагу (20%), пищевые отходы (18%), стекло (17%) и пластик (14%) [23]. По сравнению с общими для России показателями доля пищевых отходов и бумаги в Москве меньше, а доля пластика и стекла больше. В связи с большой неопределенностью в составе ТКО достаточно сложно предсказать состав продуктов их пиролиза. Поэтому продукты пиролиза ТКО, как правило, делятся на три группы: полукокс, смола (пиролитическое масло) и неконденсирующийся газ (рис. 1). Предполагается, что процесс протекает в соответствии с одностадийными или многостадийными механизмами реакций [24].
Тем не менее, большое количество работ посвящено разработке детальных механизмов пиролиза основных компонентов ТКО [25, 26]. Этот процесс протекает, как правило, в разных температурных диапазонах для разных компонентов. В частности, компоненты биомассы ТКО разлагаются при температуре 300–400°C, а разложение пластмасс происходит при более высокой температуре – 380–500°C. В схематичном виде диапазоны температур термического разложения различных компонентов ТКО показаны на рис. 2, где также приведены основные продукты их разложения [27].
Рис. 2.
Температурные интервалы термического разложения компонентов ТКО и основные продукты разложе-ния [27].
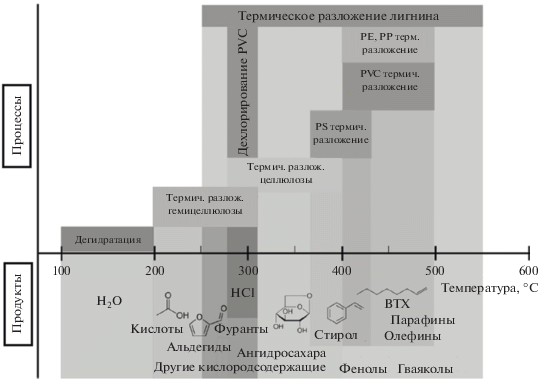
Растительная биомасса, а также материалы, полученные на ее основе (древесина, бумага, текстиль, пищевые отходы и другие), состоят в основном из целлюлозы (40–60%), гемицеллюлозы (15–30%) и лигнина (10–25%). Этот тип твердых отходов имеет достаточно сложную молекулярную структуру. Тем не менее для этого типа твердых отходов разработаны достаточно сложные механизмы пиролиза, которые позволяют описать процесс на молекулярном уровне [28]. Пластмассовая фракция ТКО содержит в основном такие полимеры, как полиэтилен (PE), полипропилен (PP), полистирол (PS), полиэтилентерефталат (PET) и поливинилхлорид (PVC). Эти полимерные материалы имеют правильную молекулярную структуру. Поэтому механизмы их термического разложения достаточно хорошо изучены [26]. Как видно из рис. 2, большинство из этих полимеров разрушаются в достаточно узком температурном интервале от 360 до 500°C.
ХАРАКТЕРИСТИКА ПРОДУКТОВ ПИРОЛИЗА
Как отмечалось выше, твердые коммунальные отходы, произведенные в разное время в разных географических регионах, имеют разный состав [23]. Поэтому достаточно сложно получить какие-либо общие закономерности распределения продуктов пиролиза. Тем не менее условия проведения процесса (скорость нагрева, температура, время пребывания летучих продуктов в высокотемпературной области и т.д.) позволяют определить взаимосвязь между основными продуктами пиролиза. Медленный пиролиз (торрефикация), который характеризуется низкими температурами процесса и длительным временем пребывания выделившихся летучих продуктов в зоне реакции, способствует образованию газа и твердого остатка [29]. Высокие температуры процесса и длительное время пребывания летучих в области высоких температур способствуют превращению сырья в газ, в то время как умеренные температуры и короткое время пребывания в высокотемпературной области являются оптимальными для получения жидких продуктов пиролиза [30]. На рис. 3 приведено сравнение распределений различных продуктов пиролиза применительно к различным условиям проведения процесса [31]. Следует отметить, что быстрый пиролиз в настоящее время представляет особый интерес, поскольку с его помощью можно получать большое количество жидких продуктов, которые можно использовать в энергетических целях [32].
Рис. 3.
Распределение продуктов при различных типах пиролиза [31]: 1 – смола, 2 – вода, 3 – полукокс, 4 – газ.
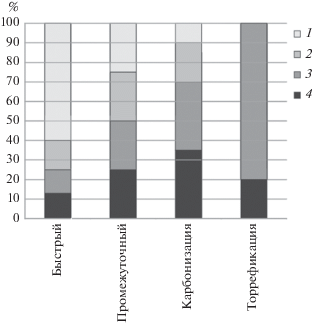
В настоящее время имеется большое количество экспериментальных работ, посвященных исследованию влияния различных параметров процесса на выход продуктов пиролиза. На рис. 4 представлена подборка имеющихся экспериментальных данных по распределению продуктов пиролиза биомассы для различных типов сырья, типов реактора и условий проведения эксперимента [16]. Эти данные сгруппированы в две последовательности экспериментальных точек, которые соответствуют высоким и низким скоростям нагрева. Разброс данных объясняется различиями в исходном типе биомассы, типе реактора и условиях пиролиза (размер частиц, высота слоя, время пребывания в реакционной зоне, скорость нагрева и другие). В частности, исследование поведения летучих продуктов пиролиза для различных видов биомассы, которое было проведено в лабораторном реакторе с кипящим слоем при температуре от 750 до 900°C, показало, что различия в выходе полукокса составляют величину порядка 10%, а различия в выходе жидких продуктов достигает 20 мас. % исходного сырья [33]. Влияние таких условий пиролиза, как размер частиц, может составить 6 мас. % сырья для данного материала и температурного режима [34].
Рис. 4.
Подборка экспериментальных данных по выходу продуктов пиролиза для различных типов сырья, типов реактора и условий проведения эксперимента [16]: (а) полукокс, (б) смола + вода, (в) газ, (г) вода; 1 – медленный, 2 – быстрый нагрев.
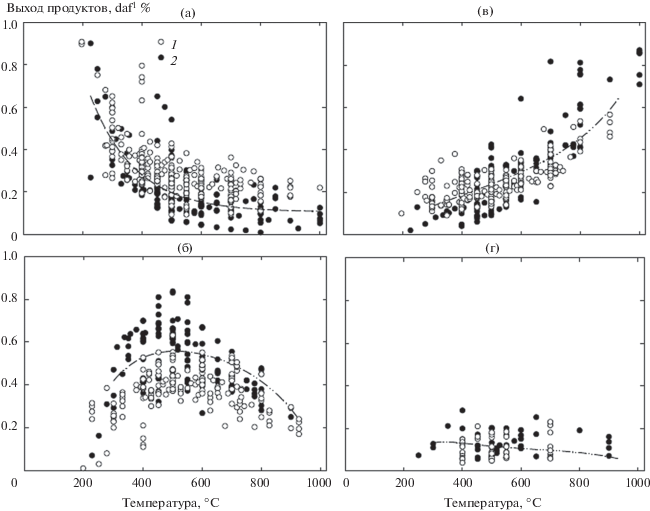
Анализ экспериментальных точек, изображенных на рис. 4, показывает, что наиболее важными параметрами процесса, определяющими количество получаемых продуктов (твердых, жидких и газообразных), являются конечная температура процесса и скорость нагрева исходного материала. В области низких температур (порядка 300°C и ниже) основным продуктом пиролиза ТКО является полукокс. Промежуточный температурный интервал (400–600°C) характеризуется максимальным выходом смолы, в то время как при высоких температурах (порядка 800°C и выше) доминирующим является выделение неконденсирующихся газов. Снижение выхода полукокса при повышении температуры от 200 до 600°C объясняется термической деструкцией органических компонентов исходного сырья. Оценки показывают, что при температурах выше 600°C полукокс содержит около 15% углерода, порядка нескольких процентов кислорода и менее процента водорода от начальной массы перерабатываемого материала [16]. Исследования по термическому разложению ТКО показывают, что полученный в результате пиролиза полукокс по своим свойствам аналогичен полукоксу от пиролиза биомассы, который можно использовать для улучшения плодородия почвы [13].
Важным параметром процесса пиролиза ТКО является выход жидких продуктов, которые могут использоваться в энергетических целях, а также для производства моторных топлив. Выход жидких продуктов пиролиза увеличивается с ростом температуры, достигает максимума, а затем начинает уменьшаться (рис. 4). Максимальный выход жидких продуктов при высоких скоростях нагрева достигает 45–75%, тогда как при медленном нагреве эта величина лежит в диапазоне от 35 до 55%. Температура максимального выхода составляет около 500°C. Снижение выхода жидких продуктов пиролиза при более высоких температурах объясняется вторичными химическими реакциями разложения пиролитического масла на более легкие компоненты и неконденсирующийся газ, которые происходят в свободном пространстве на выходе из реактора [35]. В условиях высоких скоростей нагрева и короткого времени пребывания продуктов пиролиза в высокотемпературной зоне образуется большое количество воскообразного материала, который является составной частью жидких продуктов пиролиза [36]. При медленном нагреве подобный воскообразный материал, состоящий из длинных алифатических цепочек типа полиэтилена, образуется в меньших количествах.
Данные по выходу пиролитической воды лежат в диапазоне от 5 до 20% (в расчете на сухую беззольную массу) практически во всем температурном интервале. Этот продукт термического разложения органической массы ТКО образуется на начальной стадии процесса при температуре ниже 300°C и связан с дегидратацией химической структуры исходного материала. Выход пиролитической воды имеет почти постоянное значение при дальнейшем увеличении температуры. Это указывает на то, что увеличение общего выхода жидких продуктов пиролиза при повышенных температурах достигается за счет выделения пиролитического масла.
Выход неконденсирующегося газа при низких температурах (менее 500°C), когда интенсивность вторичных реакций разложения компонентов пиролитического масла незначительна, слабо коррелирует с изменением температуры. Основное количество газа образуется за счет разложения химической структуры исходного углеводородного материала ТКО. Неконденсирующийся газ пиролиза состоит в основном из CO2, CO и небольших количеств CH4, CxHy и H2 (в расчете на массовые доли). В области высоких температур (выше 600°C) наблюдается резкое увеличение выхода газа при последующем нагреве. В этом температурном диапазоне доминирующим газовым компонентом является CO, а это указывает на то, что разложение масла во вторичных химических реакциях приводит в основном к образованию CO. Большая часть оставшегося масла разлагается на CH4, CxHy и H2, увеличивая выход газа примерно с 1 мас. % при 500°C до 10 мас. % при температуре выше 850°C [16].
КАТАЛИТИЧЕСКИЙ ПИРОЛИЗ
Обычный пиролиз ТКО представляет собой термическое разложение органической составляющей исходного материала в инертной среде с образованием полукокса (золы и фиксированного углерода), смолы (пиролитического масла), пиролитической воды и неконденсирующегося газа. Наиболее ценным продуктом пиролиза ТКО является смола, в состав которой входят сотни типов кислородсодержащих соединений, таких как кислоты, кетоны, альдегиды, фенолы и ангидросахара [18]. 11Присутствие данных соединений, а также большого количества пиролитической воды в жидких продуктах пиролиза приводит к тому, что их низшая теплотворная способность составляет порядка 40–50% от соответствующего значения для углеводородного топлива [28]. Высокое содержание кислот и воды в пиролитическом масле делает его также несовместимым с традиционной топливной инфраструктурой [37]. Все это дает основания для более глубокой переработки жидких продуктов пиролиза с целью получения качественного котельного или транспортного топлива. Эта проблема в настоящее время решается с использованием методов каталитического пиролиза.
Общую схему каталитического пиролиза можно представить следующим образом. Первичный пиролиз, связанный с разложением ТКО, обычно осуществляется при температуре порядка 500°C, но в некоторых случаях эта температура повышается до 700°C, причем выход продуктов пиролиза существенно зависит от этого параметра процесса. Вторичные химические реакции, связанные с каталитической конверсией продуктов первичного пиролиза, протекают при более высоких температурах. Основными из них являются деоксигенация, крекинг, ароматизация, кетонизация, гидроочистка и реформинг [38]. В зависимости от метода контакта катализатора с парогазовой смесью, которая образуется при пиролизе ТКО, каталитический пиролиз можно разделить на две разновидности [28]. Первая разновидность, в которой катализатор смешивается с исходным сырьем и подается в реактор пиролиза, называется каталитическим пиролизом in-situ [39], тогда как разновидность, в которой образующаяся при пиролизе парогазовая смесь проходит через слой катализатора, называется каталитическим пиролизом ex-situ [40]. Эти две разновидности каталитического пиролиза схематично изображены на рис. 5.
Реакция каталитической деоксигенации кислородсодержащих соединений, входящих в состав смолы, является эффективным путем снижения концентрации кислорода в жидких продуктах пиролиза ТКО [38]. Типичные реакции деоксигенации, такие как дегидратация, декарбоксилирование и декарбонилирование, приводят к отщеплению атомов кислорода от углеводородных молекул с образованием H2O, CO2 и CO соответственно. Наиболее важной из этих реакций является декарбонилирование кислородсодержащих соединений, поскольку эта реакция обладает наибольшей эффективностью и значительно увеличивает соотношение [C]/[H] в смоле [41].
Тяжелые фракции смолы, проходя через слой катализатора, могут превращаться в легкие углеводороды в серии реакций каталитического крекинга. Эти реакции включают в себя разрыв C−C-связей, перенос атомов водорода, изомеризацию, отщепление боковой цепи от ароматического кольца и деоксигенацию [42]. Вторичные каталитические реакции также включают поверхностные реакции осаждения углерода и смолы, реакции газификации углерода и паровой каталитический реформинг смолы с образованием H2O, CO, CO2, легких алифатических и ароматических углеводородов. Эти реакции приводят к снижению концентрации смолы в продуктах пиролиза и увеличению концентрации газа и воды.
Одним из широко используемых катализаторов для улучшения качества жидких продуктов пиролиза является коксовый остаток [38]. Он является наиболее дешевым реагентом, поскольку образуется в процессе пиролиза и, следовательно, внешнего ввода катализатора в реактор пиролиза не требуется. Кроме того, когда летучие вещества из ТКО проходят через слой коксового остатка, используется скрытая теплота испарения воды и сохраняется теплосодержание как коксового остатка, так и летучих продуктов пиролиза [43]. Это происходит по той причине, что эмиссия летучих веществ и газификация коксового остатка происходят одновременно, и, следовательно, они взаимодействуют до момента падения температуры в реакторе.
Другим широко используемым катализатором для реформинга продуктов пиролиза является CaO, который обладает довольно высокой каталитической активностью и низкой стоимостью [44]. Этот катализатор может действовать как абсорбент, реагент и катализатор в зависимости от условий процесса пиролиза. Как показывают исследования, добавление CaO в сырье способствует разложению высокомолекулярных компонентов смолы, что приводит к снижению выхода смолы и увеличению выхода газа [45]. Доломит также является дешевым и распространенным материалом. Его использование в качестве катализатора при термической переработке ТКО приводит к увеличению выхода и качества пиролитического газа, а также снижению выхода смолы за счет крекинга и реформинга высокомолекулярных углеводородных компонентов смолы [46]. В некоторых исследованиях в качестве катализатора для улучшения качества смолы, образующейся во время пиролиза ТКО, используется также цеолит [47]. Сравнение количества жидких продуктов, полученных при пиролизе полистирольных пластиковых отходов, показывает, что максимальный выход смолы при обычном пиролизе составляет 80.8% с выходом газа 13% и кокса 6.2%, тогда как при каталитическом пиролизе с использованием синтетического и природного цеолита соответствующие выходы составляют 52, 17.7 и 30.7% соответственно [48].
ДВУХСТАДИЙНАЯ ПИРОЛИТИЧЕСКАЯ КОНВЕРСИЯ ТКО
Альтернативой традиционной пиролитической переработке ТКО является двухстадийный метод, в котором парогазовая смесь, как продукт пиролиза, на второй стадии процесса подвергается высокотемпературному каталитическому крекингу с образованием синтез-газа [12, 49, 50]. Этот метод позволяет преобразовывать низкосортные жидкие продукты пиролиза ТКО в высококалорийное газообразное топливо с теплотворной способностью порядка 16 МДж/м3 [50]. Синтез-газ, образующийся при каталитическом крекинге жидких продуктов пиролиза ТКО, состоит в основном из смеси водорода и оксида углерода с отношением объемных долей в диапазоне от 1 до 2. Конечный продукт двухстадийной переработки ТКО не содержит жидкой фракции, что свидетельствует о полном термическом разложении высокомолекулярных соединений, входящих в состав летучих продуктов пиролиза. Это, с одной стороны, повышает эффективность преобразования исходного материала в высококалорийное топливо, а с другой стороны, позволяет решить экологическую проблему утилизации ТКО с минимальным уровнем выбросов вредных веществ в окружающую среду.
Принципиальная возможность двухстадийной пиролитической конверсии компонентов ТКО в синтез-газ была продемонстрирована в ряде исследований, выполненных как в России [12, 51, 52], так и за рубежом [46, 53–55]. Технологическая схема метода включает в себя несколько этапов [56]. На первом этапе происходит подготовка исходного сырья к последующей переработке с отбором ценных фракций сырья (бумага, стекло, металл, пластик и другие) на линии сортировки и измельчением оставшейся части сырья в шредере. На втором этапе подготовленное к переработке сырье поступает в реактор пиролиза, где при температуре порядка 500°C происходит процесс его термического разложения с образованием твердого остатка и летучих продуктов пиролиза, представляющих собой парогазовую смесь. На третьем этапе парогазовая смесь направляется в реактор крекинга, где при температуре порядка 1000°C осуществляется ее термокаталитическая конверсия в синтез-газ, который в основном состоит из CO и H2. В качестве катализатора в реакторе крекинга может использоваться угольный остаток, полученный путем пиролиза исходного сырья [12]. Образовавшийся синтез-газ на четвертом этапе процесса охлаждается в теплообменнике и очищается от HCl.
Рассмотренный метод термической переработки ТКО позволяет получать высококалорийный синтез-газ, который по своим характеристикам пригоден для использования как в виде топлива для энергетических установок, так и в качестве сырья для синтеза компонентов жидких моторных топлив [57]. Отсутствие в очищенном синтез-газе хлорсодержащих компонентов создает условия, препятствующие повторному образованию хлорированных диоксинов при его дальнейшем использовании [58].
Метод двухстадийной пиролитической конверсии ТКО может стать основой для создания локальных теплоутилизационных комплексов, которые обслуживают городские микрорайоны или небольшие населенные пункты. Подобный комплекс способен дать совместное решение двух проблем: обеспечение микрорайона тепловой и электрической энергией и утилизацию твердых коммунальных отходов непосредственно на месте их образования [59]. Это в свою очередь позволит получить существенный экономический эффект за счет как сокращения объемов вывоза ТКО, так и получения энергии из бросового сырья вместо привозного топлива.
Внедрение комплекса в непосредственной близости от собственного жилья существенно повысит социальную ответственность граждан при сортировке отходов и сборe фракций, представляющих интерес с точки зрения возможности их повторного использования (бумага, стекло, металл, пластик и другие).
ТИПЫ РЕАКТОРОВ ПИРОЛИЗА
Для проведения термической переработки ТКО с использованием методов пиролиза применяются различные типы реакторов [31]. В зависимости от способа подвода тепла к перерабатываемому материалу их можно подразделить на следующие типы: нагрев измельченных ТКО через стенку реактора с последующим перераспределением тепла в объеме реактора, использование газового теплоносителя для нагревания сырья [60] и теплообмен между твердым теплоносителем и перерабатываемым материалом, которые предварительно перемешиваются на входе в реактор. К первой группе реакторов относятся реакторы с фиксированным слоем [61, 62], барабанные реакторы типа вращающейся печи [63, 64], шнековые реакторы [65] и другие. Основным преимуществом реакторов данного типа является надежность и стабильность в работе, а также хорошая воспроизводимость результатов [14]. С другой стороны, данная технология нагрева характеризуется сравнительно низкой интенсивностью теплообмена и, соответственно, низкой производительностью [60].
Отличительная особенность процесса термической переработки ТКО в реакторе с фиксированным слоем заключается в сравнительно небольшой скорости нагрева исходной смеси, что является следствием низкой теплопередачи от стенок реактора к перерабатываемому материалу в условиях отсутствия перемешивающих устройств. Поэтому температура внутри реактора, имеющего относительно большие размеры, сильно снижается от его стенки к центру. Это затрудняет прогрев перерабатываемого материала и, соответственно, приводит к неравномерности его разложения. По этой причине реакторы с фиксированным слоем применяются главным образом в мелкомасштабных лабораторных установках для определения основных параметров, влияющих на выход продуктов пиролиза [66].
Барабанные реакторы типа вращающейся печи являются более эффективными по сравнению с реакторами с фиксированным слоем с точки зрения скорости и равномерности прогрева исходного материала. Этот тип реактора-пиролизера достаточно широко используется в крупномасштабных установках для проведения медленного пиролиза ТКО, так как скорость нагрева твердых отходов в подобном реакторе не превышает 100°C/мин, а время их пребывания в реакторе достигает 60 мин [67]. Этот тип реакторов нашел более широкое применение, поскольку имеет ряд преимуществ перед реакторами с фиксированным слоем [13]. В частности, за счет вращения барабана достигается хорошее перемешивание различных компонентов смеси твердых отходов, а также снижаются температурные градиенты внутри реактора. Изменение скорости вращения барабана позволяет варьировать время пребывания смеси в реакторе, а большой объем реактора обеспечивает переработку больших объемов исходного материала без их предварительной обработки [68].
Основным элементом шнекового реактора, который обеспечивает перемещение перерабатываемого материала вдоль оси реактора, является винтовой шнек, вращающийся в закрытой цилиндрической оболочке. Теплообмен в шнековых реакторах небольшого диаметра осуществляется через стенку реактора [69]. Нагрев твердых отходов в высокопроизводительных шнековых реакторах производится с помощью твердого теплоносителя, который смешивается с исходным материалом на входе в реактор [70]. В качестве твердого теплоносителя в таких реакторах обычно используются небольшие металлические сферы, керамические шарики, песок, карбид кремния и другие. Для отделения частиц твердого теплоносителя от общей смеси теплоносителя и полукокса, образующегося при пиролизе ТКО, используется просеивающая система определенного типа, которая размещается на выходе из реактора. Общая схема шнековых реакторов, на которой показаны все разновидности теплообменных процессов, приведена на рис. 6. Наиболее полный обзор реакторов шнекового типа представлен в [17], где рассматриваются основы пиролиза, дается подробное описание различных систем шнековых реакторов, а также анализируются преимущества и недостатки данной технологии.
Принцип теплообмена между газовым теплоносителем и измельченным исходным материалом ТКО лежит в основе реакторов с кипящим слоем. Для таких реакторов характерны высокие скорости нагрева частиц твердых отходов, а также хорошее перемешивание компонентов перерабатываемой смеси. Реакторы данного типа просты по конструкции, удобны в эксплуатации, а также представляют большие возможности для масштабирования [31]. Такие реакторы обычно используются для изучения влияния температуры процесса и времени пребывания частиц твердых отходов в зоне реакции на выход продуктов пиролиза [71]. Реакторы с кипящим слоем характеризуются высоким выходом жидких продуктов пиролиза. В частности, при термической переработке биомассы и отходов пластика выход смолы достигает 70 мас. % в пересчете на сухую беззольную массу [72]. Условием достижения высоких скоростей нагрева сырья является небольшой размер твердых частиц (порядка 2–3 мм). В этом случае скорость нагрева является лимитирующей стадией процесса. Реакторы с кипящим слоем широко используются в лабораторных исследованиях. Однако их использование в промышленных масштабах ограничено. Это связано с тем, что отделение материала слоя от остатка кокса, образовавшегося в процессе пиролиза, а также его рециркуляция в слой является достаточно сложной задачей [13].
Тип реакторов с кипящим слоем наряду с реакторами, использующими традиционный пузырьковый кипящий слой, включает в себя также реакторы, основанные на принципе циркулирующего кипящего слоя и конического фонтанирующего слоя. Циркулирующий кипящий слой представляет собой более сложную разновидность кипящего слоя, когда твердые частицы, уносимые из реактора, отделяются от газового потока в циклоне и возвращаются в слой [73]. Основное отличие реакторов данного типа от реакторов с традиционным кипящим слоем заключается в том, что время пребывания частиц полукокса в кипящем слое почти такое же, как и летучих продуктов пиролиза [74]. Кроме того, более высокие скорости потока газа приводят к большему истиранию частиц полукокса и, соответственно, к их большей концентрации в собранных жидких продуктах пиролиза [31]. Реакторы с коническим фонтанирующим слоем представляют собой отдельный тип реакторов с кипящим слоем, которые имеют коническую форму корпуса реактора. Эта инновационная технология успешно используется для пиролиза биомассы [75].
Третья разновидность нагрева измельченных твердых отходов основана на использовании твердого теплоносителя. Внутренний теплообмен между твердыми частицами в реакторе значительно увеличивает скорость нагрева частиц твердых отходов по сравнению с внешним теплообменом через стенки реактора [76]. Это приводит к быстрому пиролизу частиц ТКО и значительно улучшает производительность реактора. Использование условий быстрого пиролиза позволяет, с одной стороны, достичь максимального выхода жидкой фракции, а с другой стороны, повысить концентрацию легких углеводородных фракций в пиролитическом масле и тем самым улучшить качество получаемого продукта [77]. Важным преимуществом реакторов с твердым теплоносителем по сравнению с реакторами с кипящим слоем является отсутствие большого количества псевдоожижающих газов, что значительно снижает энергозатраты на быстрое охлаждение и последующую конденсацию жидких продуктов и повышает эффективность их отделения от общей массы продуктов пиролиза [78].
Твердый теплоноситель используется в высокопроизводительных шнековых реакторах [17], а также в реакторах-пиролизерах барабанного типа [79]. Применение твердого теплоносителя для термической обработки низкосортных топлив является основой технологии “Галотер”, которая в настоящее время наиболее эффективна и получила коммерческое применение [80]. Эта технология основана на быстром нагреве мелкозернистого твердого топлива твердым теплоносителем (зола, образовавшаяся при пиролизе топлива) в реакторе с вращающимся барабаном. Коммерческая реализация технологии представлена в промышленных установках УТТ-3000 с производительностью 3000 т/сутки применительно к пиролизу горючих сланцев [81]. Опыт эксплуатации этих установок, а также испытания их применения для переработки других материалов, содержащих органические вещества (автомобильные покрышки, нефтешламы, загрязненные нефтью почвы, осадки сточных вод, некоторые виды ТКО), значительно расширяют область их применения.
Несмотря на значительный прогресс в изучении пиролиза компонентов ТКО и смеси в целом, пиролитические методы термической переработки ТКО пока не нашли широкого промышленного применения. Достаточно полный обзор действующих установок по пиролизу ТКО приведен в [13, 67]. Российский опыт внедрения методов пиролиза в практику термической переработки ТКО значительно уступает мировому уровню. Тем не менее в последнее время наблюдается положительная тенденция в создании установок подобного типа. В частности, в работе [82] был предложен пилотный проект строительства завода по переработке ТКО методом высокотемпературного пиролиза пропускной способностью 100 кт/год.
ЭКОЛОГИЧЕСКИЕ АСПЕКТЫ ПИРОЛИТИЧЕСКИХ МЕТОДОВ
Современные пиролитические методы термической переработки ТКО характеризуются тем, что все продукты пиролиза собираются или перерабатываются. Процесс пиролиза уменьшает количество термических оксидов азота из-за более низких температур и восстановительной среды, реализуемых в реакторе-пиролизере [13]. Кроме того, меньший объем газа, образующегося при пиролизе, требует устройств очистки меньших размеров для удаления NOx, NH3, SO2 и HCl, что снижает капиталовложения и эксплуатационные расходы. Одним из преимуществ пиролитической переработки ТКО по сравнению с их прямым сжиганием является значительное снижение выбросов тяжелых металлов (Cd, Pb, Zn, Cu, Hg и As) в окружающую среду благодаря их удержанию в твердом остатке [83].
Термические методы переработки ТКО, включая пиролиз, приводят к образованию большого количества продуктов неполного сгорания, которые содержат токсичные и стойкие органические вещества [84]. Присутствие хлорорганических соединений в твердых отходах способствует образованию заметных количеств PCDD/Fs, которые относятся к числу наиболее токсичных веществ [58]. Следует отметить, что PCDD/Fs образуются практически во всех процессах, связанных с термической переработкой органических веществ в присутствии различных соединений хлора [85]. Основным механизмом образования PCDD/Fs в процессе пиролиза является гетерогенный процесс denovo, который связан с карбонизацией структурных элементов углеродной матрицы в органическом веществе с одновременным хлорированием образующихся структур PCDD/Fs и выходом их в газовую фазу [86]. Процесс denovo играет существенную роль при температуре ниже 450°C и содержании кислорода в газовом потоке порядка нескольких процентов [87]. Так как при пиролизе свободный кислород в системе отсутствует, количество образующихся PCDD/Fs на порядок ниже, чем при сжигании.
Наиболее привлекательным с экологической точки зрения является метод двухстадийной пиролитической конверсии ТКО [12]. Пиролиз перерабатываемой органической массы ТКО (первая стадия процесса) сопровождается выходом хлора в газовую фазу в виде HCl при температуре порядка 500°C [88]. При этом в парогазовой смеси возможно газофазное образование PCDD/Fs за счет конденсации и последующего хлорирования фенольных структур, содержащихся в смоле [89]. На следующей стадии процесса парогазовая смесь поступает в реактор термокаталитического крекинга для переработки в синтез-газ. При температуре крекинга порядка 1000°C происходит полное разложение компонентов смолы, включая фенолы и образованные на стадии пиролиза PCDD/Fs [90]. Охлажденный синтез-газ, который предполагается использовать для генерации тепловой и/или электрической энергии или для синтеза компонентов жидких моторных топлив, на следующем этапе подвергается очистке от HCl. Отсутствие в очищенном синтез-газе хлорсодержащих компонентов создает условия, препятствующие повторному образованию хлорированных диоксинов при дальнейшем его использовании.
ЗАКЛЮЧЕНИЕ
Наиболее рациональным способом утилизации ТКО является их повторное использование в качестве альтернативного источника энергии, что требует разработки новых методов реализации процесса. Эти методы в первую очередь включают пиролитическую конверсию твердых отходов в жидкое и газообразное топливо.
В зависимости от условий проведения процесса, он подразделяется на быстрый, среднескоростной и медленный пиролиз. Одним из основных продуктов быстрого и среднескоростного пиролиза является масло, состоящее на 40–50% из кислородсодержащих соединений, что затрудняет его использование в качестве топлива. Эта проблема решается путем применения методов каталитического пиролиза.
Наиболее широко используемые технологии пиролиза ТКО основаны на шнековых реакторах и реакторах с кипящим слоем. Применение твердого теплоносителя является основой технологии “Галотер”, которая в настоящее время является наиболее эффективной технологией пиролитической переработки низкосортных топлив, включая различного рода твердые отходы.
Привлекательным с экологической и практической точек зрения является метод двухстадийной пиролитической конверсии ТКО, в котором продукты пиролиза на второй стадии процесса подвергаются высокотемпературному каталитическому крекингу с образованием синтез-газа. Предлагаемый метод может стать основой для создания локальных теплоутилизационных комплексов, которые обслуживают городские микрорайоны или небольшие населенные пункты.
Исследование выполнено при финансовой поддержке РФФИ в рамках научного проекта № 20-58-00043.
Список литературы
Волкова А.В. Рынок утилизации отходов. М.: Изд-во ВШЭ, 2018. 87 с.
He P., Chen L., Shao L., Zhang H., Lü F. Municipal Solid Waste (MSW) Landfill: A Source of Microplastics? – Evidence of Microplastics in Landfill Leachate // Water Res. 2019. V. 159. P. 38.
Glushkov D., Paushkina K., Shabardin D., Strizhak P., Gutareva N. Municipal Solid Waste Recycling by Burning it as Part of Composite Fuel with Energy Generation // Journal of Environmental Management. 2019. V. 231. P. 896.
Huang B., Wang X., Kua H., Geng Y., Bleischwitz R., Ren J. Construction and Demolition Waste Management in China Through the 3R Principle // Resour. Conserv. Recycl. 2018. V. 129. P. 36.
Тугов А.Н., Родионов В.И. Термическая переработка ТКО в мире // Твердые бытовые отходы. 2016. № 8. С. 20.
Kumar A., Samadder S.R. A Review on Technological Options of Waste to Energy for Effective Management of Municipal Solid Waste // Waste Manage. 2017. V. 69. P. 407.
Mukherjee C., Denney J., Mbonimpa E.G., Slagley J., Bhowmik R. A Review on Municipal Solid Waste-to-energy Trends in the USA // Renew. Sustain. Energy Rev. 2020. V. 119. № 109512.
Wyrzykowska-Ceradini B., Gullett B.K., Tabor D., Touati A. Waste Combustion as a Source of Ambient Air Polybrominated Diphenylethers (PBDEs) // Atmos. Environ. 2011. V. 45. № 24. P. 4008.
Sipra A.T., Gao N., Sarwar H. Municipal Solid Waste (MSW) Pyrolysis for Bio-fuel Production: A Review of Effects of MSW Components and Catalysts // Fuel Process. Technol. 2018. V. 175. P. 131.
Gerasimov G.Ya. Comparative Analysis of PCDD/Fs Formation During Pyrolysis and Incineration of Medical Waste // IOP Conf. Series: Earth and Environ. Sci. 2019. V. 272. № 022116.
Czajczyńska D., Anguilano L., Ghazal H., Krzyzynska R., Reynolds A.J., Spencer N., Jouhara H. Potential of Pyrolysis Processes in the Waste Management Sector // Therm. Sci. Eng. Prog. 2017. V. 3. № 1. P. 171.
Лавренов В.А., Ларина О.М., Синельщиков В.А., Сычев Г.А. Двухстадийная пиролитическая конверсия различных видов биомассы в синтез-газ // ТВТ. 2016. Т. 54. № 6. С. 950.
Chen D., Yin L., Wang H., He P. Pyrolysis Technologies for Municipal Solid Waste: A Review // Waste Manage. 2014. V. 34. № 12. P. 2466.
Martinez J.D., Puy N., Murillo R., Garcia T., Navarro M.V., Mastral A.M. Waste Tyre Pyrolysis – A Review // Renew. Sustain. Energy Rev. 2013. V. 23. P. 179.
Lombardi L., Carnevale E., Corti A. A Review of Technologies and Performances of Thermal Treatment Systems for Energy Recovery from Waste // Waste Manage. 2015. V. 37. P. 26.
Neves D., Thunman H., Matos A., Tarelho L., Gomez-Barea A. Characterization and Prediction of Biomass Pyrolysis Products // Prog. Energy Combust. Sci. 2011. V. 37. № 5. P. 611.
Campuzano F., Brown R.C., Martinez J.D. Auger Reactors for Pyrolysis of Biomass and Wastes // Renew. Sustain. Energy Rev. 2019. V. 102. P. 372.
Mohan D., Pittman C.U., Steele P.H. Pyrolysis of Wood/Biomass for Bio-oil: A Critical Review // Energy & Fuels. 2006. V. 20. № 3. P. 848.
Singh R., Krishna B.B., Mishra G., Kumar J., Bhaskar T. Strategies for Selection of Thermo-chemical Processes for the Valorisation of Biomass // Renew. Energy. 2016. V. 98. P. 226.
Yang Y., Brammer J.G., Ouadi M., Samanya J., Hornung A., Xu H.M., Li Y. Characterization of Waste Derived Intermediate Pyrolysis Oils for Use as Diesel Engine Fuels // Fuel. 2013. V. 103. P. 247.
Антропов А.П., Батенин В.М., Зайченко В.М. Новые технологии распределенной энергетики // ТВТ. 2015. Т. 53. № 1. С. 111.
Garcia-Nunez J.A., Pelaez-Samaniego M.R., Garcia-Perez M.E., Fonts I., Abrego J., Westerhof R.J.M., Garcia-Perez M. Historical Developments of Pyrolysis Reactors: A Review // Energy & Fuels. 2017. V. 31. № 6. P. 5751.
Glushkov D., Paushkina K., Shabardin D., Strizhak P. Environmental Aspects of Converting Municipal Solid Waste into Energy as Part of Composite Fuels // Journal of Cleaner Production. 2018. V. 201. P. 1029.
Diaz Silvarrey L.S., Phan A.N. Kinetic Study of Municipal Plastic Waste // Int. J. Hydrogen Energy. 2016. V. 41. № 37. P. 16352.
Anca-Couce A. Reaction Mechanisms and Multi-scale Modelling of Lignocellulosic Biomass Pyrolysis // Prog. Energy Combust. Sci. 2016. V. 53. P. 41.
Sharuddin S.D.A., Abnisa F., Daud W.M.A.W., Aroua M.K. A Review on Pyrolysis of Plastic Wastes // Energy Convers. Manage. 2016. V. 115. P. 308.
Sophonrat N., Sandström L., Zaini I.N., Yang W. Stepwise Pyrolysis of Mixed Plastics and Paper for Separation of Oxygenated and Hydrocarbon Condensates // Appl. Energy. 2018. V. 229. P. 314.
Wang S., Dai G., Yang H., Luo Z. Lignocellulosic Biomass Pyrolysis Mechanism: A State-of-the-art Review // Prog. Energy Combust. Sci. 2017. V. 62. P. 33.
Директор Л.Б., Синельщиков В.А., Сычев Г.А. Теплофизические свойства летучих продуктов низкотемпературного пиролиза древесной массы // ТВТ. 2020. Т. 58. № 1. С. 45.
Tsai W.T., Lee M.K., Chang Y.M. Fast Pyrolysis of Rice Husks: Product Yields and Compositions // Bioresour. Technol. 2007. V. 98. № 1. P. 22.
Bridgwater A.V. Review of Fast Pyrolysis of Biomass and Product Upgrading // Biomass Bioenergy. 2012. V. 38. P. 68.
Owusu P.A., Banadda N., Zziwa A., Seay J., Kiggundu N. Reverse Engineering of Plastic Waste into Useful Fuel Products // J. Anal. Appl. Pyrolysis. 2018. V. 130. P. 285.
Gómez-Barea A., Nilsson S., Barrero F.V., Campoy M. Devolatilization of Biomass and Waste in Fluidized Bed // Fuel Process. Technol. 2010. V. 91. № 11. P. 1624.
Thunman H., Niklasson F., Johnsson F., Leckner B. Composition of Volatile Gases and Thermochemical Properties of Wood for Modeling of Fixed or Fluidized Beds // Energy & Fuels. 2001. V. 15. № 6. P. 1488.
Morf P., Hasler P., Nussbaumer T. Mechanisms and Kinetics of Homogeneous Secondary Reactions of Tar from Continuous Pyrolysis of Wood Chips // Fuel. 2002. V. 81. № 7. P. 843.
Velghe I., Carleer R., Yperman J., Schreurs S. Study of the Pyrolysis of Municipal Solid Waste for the Production of Valuable Products // J. Anal. Appl. Pyrolysis. 2011. V. 92. № 2. P. 366.
Miskolczi N., Ateş F., Borsodi N. Comparison of Real Waste (MSW and MPW) Pyrolysis in Batch Reactor over Different Catalysts. Part II: Contaminants, Char, and Pyrolysis Oil Properties // Bioresour. Technol. 2013. V. 144. P. 370.
Wang N., Chen D., Arena U., He P. Hot Char-catalytic Reforming of Volatiles from MSW Pyrolysis // Applied Energy. 2017. V. 191. P. 111.
Galadima A., Muraza O. In situ Fast Pyrolysis of Biomass with Zeolite Catalysts for Bio Aromatics/Gasoline Production: A Review // Energ. Convers. Manage. 2015. V. 105. P. 338.
Wan S., Wang Y. A Review on ex situ Catalytic Fast Pyrolysis of Biomass // Front. Chem. Sci. Eng. 2014. V. 8. № 3. P. 280.
Chen T., Zhang J., Wu J. Kinetic and Energy Production Analysis of Pyrolysis of Lignocellulosic Biomass Using a Three-parallel Gaussian Reaction Model // Bioresour. Technol. 2013. V. 211. P. 502.
Dickerson T., Soria J. Catalytic Fast Pyrolysis: A Review // Energies. 2013. V. 6. № 1. P. 514.
Wang N., Qian K., Chen D., Zhao H., Yin L. Upgrading Gas and Oil Products of the Municipal Solid Waste Pyrolysis Process by Exploiting in-situ Interactions Between the Volatile Compounds and the Char // Waste Manage. 2020. V. 102. P. 380.
Song Q., Zhao H., Xing W., Song L., Yang L., Yang D., Shu X. Effects of Various Additives on the Pyrolysis Characteristics of Municipal Solid Waste // Waste Manage. 2018. V. 78. P. 621.
Chen X., Chen Y., Yang H., Chen W., Wang X., Chen H. Fast Pyrolysis of Cotton Stalk Biomass Using Calcium Oxide // Bioresour. Technol. 2017. V. 233. P. 15.
He M., Xiao B., Liu S., Hu Z., Guo X., Luo S., Yang F. Syngas Production from Pyrolysis of Municipal Solid Waste (MSW) with Dolomite as Downstream Catalysts // J. Anal. Appl. Pyrolysis. 2010. V. 87. № 2. P. 181.
Gandidi I.M., Susila M.D., Mustofa A., Pambudi N.A. Thermal-catalytic Cracking of Real MSW into Bio-crude Oil // J. Energy Inst. 2018. V. 91. № 2. P. 304.
Rehan M., Miandad R., Barakat M., Ismail I., Almeelbi T., Gardy J., Hassanpour A., Khan M., Demirbas A., Nizami A. Effect of Zeolite Catalysts on Pyrolysis Liquid Oil // Int. Biodeterior. Biodegrad. 2017. V. 119. P. 162.
Lu P., Huang Q., Chi Y., Wang F., Yan J. Catalytic Cracking of Tar Derived from the Pyrolysis of Municipal Solid Waste Fractions over Biochar // Proc. Combust. Inst. 2019. V. 37. № 3. P. 2673.
Veses A., Sanahuja-Parejo O., Callén M.S., Murillo R., García T. A Combined Two-Stage Process of Pyrolysis and Catalytic Cracking of Municipal Solid Waste for the Production of Syngas and Solid Refuse-derived Fuels // Waste Manag. 2020. V. 101. P. 171.
Батенин В.М., Зайченко В.М., Косов В.Ф., Синельщиков В.А. Пиролитическая конверсия биомассы в газообразное топливо // Докл. РАН. 2012. Т. 446. № 2. С. 179.
Зайченко В.М., Лавренов В.А., Синельщиков В.А. Исследование характеристик газообразного топлива, получаемого методом двухстадийной пиролитической конверсии древесных отходов // Альтернативная энергетика и экология. 2016. № 23–24. С. 42.
He M., Hu Z., Xiao B., Li J., Guo X., Luo S., Yang F., Feng Y., Yang G., Liu S. Hydrogen-Rich Gas from Catalytic Steam Gasification of Municipal Solid Waste (MSW): Influence of Catalyst and Temperature on Yield and Product Composition // Int. J. Hydrogen Energy. 2009. V. 34. № 1. P. 195.
Saad J.M., Williams P.T. Catalytic Dry Reforming of Waste Plastics from Different Waste Treatment Plants for Production of Synthesis Gases // Waste Manage. 2016. V. 58. P. 214.
Lopez G., Artetxe M., Amutio M., Alvarez J., Bilbao J., Olazar M. Recent Advances in the Gasification of Waste Plastics. A Critical Overview // Renew. Sustain. Energy Rev. 2018. V. 82. № 1. P. 576.
Kachalov V.V., Lavrenov V.A., Lishchiner I.I., Malova O.V., Tarasov A.L., Zaichenko V.M. Scientific Bases of Biomass Processing into Basic Component of Aviation Fuel // J. Phys.: Conf. Series. 2016. V. 774. № 012136.
Yan Q., Yu F., Liu J., Street J., Gao J., Cai Z., Zhang J. Catalytic Conversion Wood Syngas to Synthetic Aviation Turbine Fuels over a Multifunctional Catalyst // Bioresour. Technol. 2013. V. 127. P. 281.
Altarawneh M., Dlugogorski B.Z., Kennedy E.M., Mackie J.C. Mechanisms for Formation, Chlorination, Dechlorination, and Destruction of Polychlorinated Dibenzo-p-dioxins and Dibenzofurans (PCDD/Fs) // Prog. Energy Combust. Sci. 2009. V. 35. № 3. P. 245.
Чирков В.Г. Мини-ТЭС на пиролизном топливе // Теплоэнергетика. 2007. № 8. С. 35.
Директор Л.Б., Зайченко В.М., Синельщиков В.А. Численное моделирование энерготехнологического комплекса с реакторов торрефикации // ТВТ. 2017. Т. 55. № 1. С. 133.
Chen C., Jin Y., Chi Y. Effects of Moisture Content and CaO on Municipal Solid Waste Pyrolysis in a Fixed Bed Reactor // J. Anal. Appl. Pyrolysis. 2014. V. 110. P. 108.
Isemin R., Klimov D., Larina O., Sytchev G., Zaichenko V., Milovanov O. Application of Torrefaction for Recycling Bio-waste Formed During Anaerobic Figestion // Fuel. 2019. V. 243. P. 230.
Li S., Yan J., Li R., Chi Y., Cen K. Axial Transport and Residence Time of MSW in Rotary Kilns: Part I. Experimental // Powder Technol. 2002. V. 126. № 3. P. 217.
Gikas P., Zhu B., Batistatos N.I., Zhang R. Evaluation of the Rotary Drum Reactor Process as Pretreatment Technology of Municipal Solid Waste for Thermophilic Anaerobic Digestion and Biogas Production // J. Environ. Manage. 2018. V. 216. P. 96.
Haydary J., Susa D., Dudáš J. Pyrolysis of Aseptic Packages (Tetrapak) in a Laboratory Screw Type Reactor and Secondary Thermal/Catalytic Tar Decomposition // Waste Manage. 2013. V. 33. № 5. P. 1136.
Ismail T.M., Ren X., Abd El-Salam M. Influence of Simulated MSW Sizes on the Combustion Process in a Fixed Bed: CFD and Experimental Approaches // Waste Manage. 2016. V. 49. P. 272.
Malkow T. Novel and Innovative Pyrolysis and Gasification Technologies for Energy Efficient and Environmentally Sound MSW Disposal // Waste Manage. 2004. V. 24. № 1. P. 53.
Mancini G., Viotti P., Luciano A., Raboni M., Fini D. Full Scale Treatment of ASR Wastes in a Modified Rotary Kiln // Waste Manage. 2014. V. 34. № 11. P. 2347.
Luz F.C., Cordiner S., Manni A., Mulone M., Rocco V. Biomass Fast Pyrolysis in Screw Reactors: Prediction of Spent Coffee Grounds Bio-oil Production Through a Monodimensional Model // Energy Convers. Manage. 2018. V. 168. P. 98.
Brassard P., Godbout S., Raghavan V. Pyrolysis in Auger Reactors for Biochar and Bio-oil Production: A Review // Biosyst. Eng. 2017. V. 161. P. 80.
Mastral F.J., Esperanza E., Garcia P., Juste M. Pyrolysis of High-density Polyethylene in a Fluidised Bed Reactor. Influence of the Temperature and Residence Time // J. Anal. Appl. Pyrol. 2002. V. 63. № 1. P. 1.
Xue Y., Zhou S., Brown R.C., Kelcar A., Bai X. Fast Pyrolysis of Biomass and Waste Plastic in a Fluidized Bed Reactor // Fuel. 2015. V. 156. P. 40.
Treedet W., Suntivarakorn R. Design and Operation of a Low Cost Bio-oil Fast Pyrolysis from Sugarcane Bagasse on Circulating Fluidized Bed Reactor in a Pilot Plant // Fuel Process. Technol. 2018. V. 179. P. 17.
Lappas A.A., Samolada M.C., Iatridis D.K., Voutetakis S.S., Vasalos I.A. Biomass Pyrolysis in a Circulating Fluid Bed Reactor for the Production of Fuels and Chemicals // Fuel. 2002. V. 81. № 16. P. 2087.
Alvarez J., Amutio M., Lopez G., Barbarias I., Bilbao J., Olazar M. Sewage Sludge Valorization by Flash Pyrolysis in a Conical Spouted Bed Reactor // Chem. Eng. J. 2015. V. 273. P. 173.
Gerasimov G., Khaskhachikh V., Potapov O., Dvoskin G., Kornileva V., Dudkina L. Pyrolysis of Sewage Sludge by Solid Heat Carrier// Waste Manage. 2019. V. 87. P. 218.
Chen L., Zhang X.-D., Sun L.-Z., Xu H.-J., Si H., Mei N. Study on the Fast Pyrolysis of Oil Sludge and Its Product Distribution by PY-GC/MS // Energy & Fuels. 2015. V. 30. № 12. P. 10 222.
Fu P., Bai X., Yi W., Li Z., Li Y. Fast Pyrolysis of Wheat Straw in a Dual Concentric Rotary Cylinder Reactor with Ceramic Balls as Recirculated Heat Carrier // Energy Convers. Manage. 2018. V. 171. P. 855.
Ma Z., Gao N., Xie L., Li A. Study of the Fast Pyrolysis of Oilfield Sludge with Solid Heat Carrier in a Rotary Kiln for Pyrolytic Oil Production // J. Anal. Appl. Pyrolysis. 2014. V. 105. P. 183.
Gerasimov G., Volkov E. Modeling Study of Oil Shale Pyrolysis in Rotary Drum Reactor by Solid Heat Carrier // Fuel Process. Technol. 2015. V. 139. P. 108.
Volkov E. High-efficiency Technology for Oil Shale Processing // Oil Shale. 2013. V. 30. № 2. P. 95.
Rumyantseva A., Berezyuk M., Savchenko N., Rumyantseva E. Modern Technologies of Processing Municipal Solid Waste: Investing in the Future // IOP Conf. Series: Earth and Environmental Science. 2017. V. 72(1). 012015.
Bernardo M., Lapa N., Gonçalves M., Barbosa R., Mendes B., Pinto F. Toxicity of Char Residues Produced in the Co-pyrolysis of Different Wastes // Waste Manage. 2010. V. 30. № 4. P. 628.
Zhou H., Wu C., Onwudili J.A., Meng A., Zhang Y., Williams P.T. Polycyclic Aromatic Hydrocarbons (PAH) Formation from the Pyrolysis of Different Municipal Solid Waste Fractions // Waste Manage. 2015. V. 36. P. 136.
Kulkarni P.S., Crespo J.G., Afonso C.A.M. Dioxins Sources and Current Remediation Technologies – A Review // Environ. Int. 2008. V. 34. № 1. P. 139.
Gao Q., Edo M., Larsson S.H., Collina E., Rudolfsson M., Gallina M. et al. Formation of PCDDs and PCDFs in the Torrefaction of Biomass with Different Chemical Composition // J. Analyt. Appl. Pyrolysis. 2017. V. 123. P. 126.
Герасимов Г.Я. Образование диоксинов при сжигании хлорсодержащих топлив // ФГВ. 2001. Т. 37. № 2. С. 29.
Lu P., Huang Q., Bourtsalas A.C.T., Themelis N.J., Chi Y., Yan J. Review on Fate of Chlorine During Thermal Processing of Solid Wastes // J. Environ. Sci. 2018. V. 78. P. 13.
Gerasimov G. Modeling Study of Polychlorinated Dibenzo-p-dioxins and Dibenzofurans Behavior in Flue Gases under Electron Beam Irradiation // Chemosphere. 2016. V. 158. P. 100.
Hu B., Huang Q., Chi Y., Yan J. Polychlorinated Dibenzo-p-dioxins and Dibenzofurans in Three-stage Municipal Solid Waste Gasifier // J. Clean. Prod. 2019. V. 218. P. 920.
Дополнительные материалы отсутствуют.
Инструменты
Теплофизика высоких температур