Теплофизика высоких температур, 2021, T. 59, № 3, стр. 362-372
Моделирование тепломассопереноса в цилиндрическом испарителе контурной тепловой трубы с прямоугольным интерфейсом
М. А. Чернышева *, Ю. Ф. Майданик **
ФГБУН Институт теплофизики Уральского отделения РАН
Екатеринбург, Россия
* E-mail: mariya@itp.uran.ru
** E-mail: maidanik@itp.uran.ru
Поступила в редакцию 10.12.2019
После доработки 17.09.2020
Принята к публикации 22.12.2020
Аннотация
Рассматривается задача стационарного тепломассопереноса в цилиндрическом испарителе контурной тепловой трубы с тепловым интерфейсом, имеющим форму прямоугольного параллелепипеда, с источником тепла, расположенным на одной из его больших поверхностей. Проведено численное моделирование тепловых процессов в рассматриваемой системе при различных плотностях теплового потока. Получены данные о распределении температуры в испарителе и тепловом интерфейсе. Выполнен анализ температурной неоднородности на поверхности нагрева интерфейса и интенсивности испарения теплоносителя в пароотводные каналы испарителя.
ВВЕДЕНИЕ
Контурные тепловые трубы (КТТ) – это герметично-замкнутые, пассивные, двухфазные устройства, предназначенные для эффективной передачи тепла от горячего источника к холодному стоку даже при незначительной разнице температур между ними. КТТ работают по испарительно-конденсационному циклу. Прокачка теплоносителя в них осуществляется за счет капиллярного давления, создаваемого менисками пористой структуры (фитиля), которая в отличие от обычных тепловых труб размещается только в зоне подвода тепла [1, 2]. Основные функциональные преимущества контурных тепловых труб по сравнению с тепловыми трубами заключаются в том, что КТТ сохраняют работоспособность и высокую теплопередающую способность при любой ориентации в пространстве благодаря использованию специальных мелкопористых фитилей, способных создавать достаточно высокое капиллярное давление. Раздельные гладкостенные трубопроводы для потоков пара и жидкости (рис. 1), имеющие небольшой диаметр порядка 2–5 мм, за счет своей гибкости могут легко конфигурироваться в стесненных условиях, которые реализуются, например, в системах охлаждения электронных компонентов, таких как CPU, GPU и LED.
Рис. 1.
Внешний вид КТТ (а) и схема цилиндрического испарителя с прямоугольным тепловым интерфейсом (б).
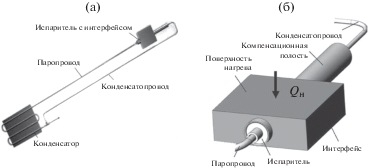
Испаритель, являясь ключевым элементом КТТ, во многом определяет работоспособность и эффективность этого устройства. Испаритель состоит из корпуса, фитиля, пароотводных каналов и компенсационной полости, в которую поступает жидкость, вытесняемая из конденсатора, при запуске и работе КТТ [3]. Размеры испарителей и их конфигурация могут быть различны. В настоящее время активно разрабатываются и исследуются испарители четырех типов: цилиндрический, прямоугольный, плоскоовальный и дискообразный [4]. Выбор того или иного типа испарителя для конкретной технической задачи определяется исходя из ряда требований, предъявляемых к КТТ. В первую очередь, они касаются тепловых характеристик КТТ, их конфигурации и габаритных параметров. Помимо этого, к числу решающих требований относится обеспечение герметичности КТТ при высоких внутренних давлениях, которые могут иметь место при использовании низкотемпературных теплоносителей, например таких как аммиак, в рабочем диапазоне температур от 50°С и выше. В работе [5] отмечено, что испарители, имеющие достаточно большие плоские поверхности (от 8 см2 и выше), весьма чувствительны к внутреннему давлению, которое может создавать теплоноситель при максимальной рабочей температуре охлаждаемых компонентов, достигающей 70–90°С. С этой точки зрения наиболее подходящими являются цилиндрические испарители, которые лучше противостоят внутреннему давлению и, кроме того, являются более простыми в изготовлении, чем плоские.
Вместе с тем, поскольку большинство тепловыделяющих объектов имеют плоскую термоконтактную поверхность, при использовании для их охлаждения контурной тепловой трубы с цилиндрическим испарителем возникает необходимость во вспомогательном элементе, обеспечивающем качественный тепловой контакт между ними. Этот дополнительный элемент сопряжения плоской поверхности горячего объекта и цилиндрической поверхности испарителя называется тепловым интерфейсом или “седлом”. При этом полное термическое сопротивление системы “тепловыделяющий объект – сток тепла” соответственным образом возрастает на величину термического сопротивления теплового интерфейса. Анализ опубликованных работ также показал, что остаются открытыми два вопроса. Первый из них касается однородности температуры на термоконтактной поверхности теплового интерфейса, поскольку от этого в конечном итоге зависит изотермичность охлаждаемого объекта. Второй вопрос: обеспечивает ли тепловой интерфейс достаточно равномерный подвода тепла к поверхности испарителя (что весьма важно для эффективной работы испарителя, а следовательно, и всей КТТ)?
В работе [6] представлена 3D-модель цилиндрического испарителя КТТ с медным седлом. Авторы рассмотрели различные геометрические конфигурации испарителя. Модель учитывает несимметричное распределение теплового потока на внешней поверхности испарителя КТТ. Результаты моделирования использовались для оптимизации конструкции формы седла с целью уменьшения его термического сопротивления, а также снижения температурных градиентов в испарителе и на поверхности нагрева седла. Авторы [7] рассмотрели задачу переноса тепла от теплового источника к цилиндрическому испарителю через медный тепловой интерфейс в форме прямоугольного параллелепипеда при одностороннем подводе тепла к его термоконтактной поверхности (рис. 1). Результаты моделирования показали, что при такой конфигурации интерфейса с односторонним нагревом имеет место неравномерный подвод тепла к поверхности испарителя, величина которого увеличивается с ростом тепловой нагрузки. В [8] представлены результаты имитационного численного моделирования течения и сопряженного тепломассопереноса в трехмерной модели испарителя контурной тепловой трубы, установленной на спутнике TacSat-4. Корпус испарителя, выполненный из алюминиевого профиля сложной конфигурации, совмещал в себе функции и теплового интерфейса, и корпуса, в котором размещался фитиль цилиндрической формы. Тепло подводилось к большой стороне корпуса, так называемого “основания”, предназначенного для размещения на нем термостатируемого объекта. Получены данные о распределении плотности теплового потока, отводимого от основания в среднем поперечном сечении испарителя. Согласно полученным результатам, максимальное значение плотности теплового потока приходится на центр основания испарителя, т.е. напротив пароотводного канала, наиболее близко расположенного к поверхности нагрева.
Данная работа посвящена исследованию тепломассопереноса в системе “тепловой интерфейс – цилиндрический испаритель” для оценки степени неоднородности поля температур на термоконтактной поверхности теплового интерфейса, а также неравномерности подвода тепла к испарителю и теплообменных процессов в его зоне испарения.
ФИЗИЧЕСКАЯ ПОСТАНОВКА ЗАДАЧИ
Рассматривается задача переноса тепла в объекте сложной геометрии, состоящем из теплового интерфейса в форме прямоугольного параллелепипеда и цилиндрического испарителя контурной тепловой трубы (рис. 1б). Тепловой интерфейс имеет центральное сквозное цилиндрическое отверстие, в которое встроен испаритель. Предполагается, что между испарителем и интерфейсом имеет место идеальный тепловой контакт, а длина зоны нагрева испарителя Lq равна длине интерфейса Lинт. Испаритель состоит из корпуса, пароотводных каналов, центрального канала и фитиля (рис. 2). Корпус представляет собой тонкостенную металлическую трубку, в которой размещен фитиль. В то время как интерфейс и корпус являются твердотельными сплошными элементами, фитиль, изготавливаемый из мелкого спеченного порошка, по своей структуре является пористым телом, проницаемым для жидкой фазы теплоносителя и не проницаемым для пара. Центральный канал полностью заполнен холодной жидкостью, что позволяет обеспечить равномерное по всей его поверхности впитывание жидкости в пористый материал, которая затем под действием капиллярных сил движется через фитиль в радиальном направлении к горячему корпусу испарителя. Здесь находится зона испарения, которая организована системой пароотводных каналов.
Согласно физической модели, охлаждаемый объект с постоянной мощностью тепловыделения Qн располагается на одной из больших сторон теплового интерфейса, тогда как другие его стороны за счет естественной конвекции обмениваются теплом с окружающей средой, температура которой постоянна Токр. Поток тепла от нагреваемой поверхности проникает через интерфейс к поверхности испарителя, а затем в фитиль, на внешней поверхности которого располагаются продольные каналы, предназначенные для отвода пара из испарителя. Вершины выступов фитиля, расположенные между пароотводными каналами, обеспечивают тепловой контакт пористого материала с внутренней поверхностью корпуса испарителя. Боковые стороны и дно пароотводных каналов формируют развитую поверхность испарения, а испаряющие мениски обращены в пароотводные каналы. Фазовый переход жидкость–пар индуцируется перегревом жидкости на поверхности испарения относительно температуры насыщенного пара в пароотводных каналах Ts.. Значения температуры пара Ts и температуры жидкости, поступающей в центральный канал Tохл, являются входными параметрам задачи. Массовый расход теплоносителя в КТТ определяется тепловым потоком, затраченным на испарение жидкости в пароотводные каналы:
При стационарном режиме работы КТТ массовый расход пара, покидающего испаритель, равен массовому расходу жидкости, которая возвращается из конденсатора по конденсатопроводу в центральный канал, а из него, впитываясь в фитиль, движется по порам к испаряющей поверхности.
МАТЕМАТИЧЕСКАЯ МОДЕЛЬ
Математическая постановка рассматриваемой задачи с учетом принятых допущений представлена ниже. Перенос тепла в тепловом интерфейсе описывается уравнением теплопроводности в декартовой системе координат:
Для описания процессов тепломассопереноса в испарителе используется цилиндрическая система координат. Уравнение теплопроводности для цилиндрической стенки корпуса имеет вид
Предположение о преимущественно радиальном течении жидкости через фитиль позволяет записать уравнение энергии для этого элемента испарителя в виде
Уравнение движения жидкой фазы теплоносителя в пористом материале записывается на основе закона Дарси:
Уравнение неразрывности для потока жидкости в фитиле с учетом допущения, что vφ = 0, имеет вид
Радиальная составляющая скорости описывается уравнением
Ниже представлено уравнение баланса энергии для рассматриваемого объекта
Qн = Qисп + Ql + Qцк+ Qокр,
где Qн – равномерный поток тепла на нагреваемой поверхности интерфейса, большая часть которого расходуется на испарение жидкости в пароотводные каналы Qисп. Второе и третье слагаемые в правой части уравнения учитывают соответственно тепловой поток, затраченный на нагрев жидкости во время ее фильтрации через фитиль, Ql и тепловой поток Qцк, проникающий в центральный канал и повышающий температуру холодной жидкости, которая возвращается сюда из конденсатора. Теплообмен внешней поверхности интерфейса с окружающей средой представлен в уравнении баланса энергии величиной Qокр.
Граничные условия записываются следующим образом. На термоконтактной поверхности теплового интерфейса:
Для плотности теплового потока qн при равномерном подводе тепла к термоконтактной поверхности теплового интерфейса имеем
Поток тепла на других поверхностях теплового интерфейса:
Для зоны испарения (поверхность фитиля, обращенная в пароотводные каналы):
На внутренних границах задаются условия сопряжения по тепловым потокам и температурам. В местах контакта фитиля и корпуса испарителя:
На границе между корпусом и тепловым интерфейсом:
${{{v}}_{r}} = 0.$
Впитывающая поверхность фитиля:
Sцк = 2πrцкLq.
Массовый расход теплоносителя, поступающего из центрального канала в фитиль, равен массовому расходу жидкости, испаряющейся в пароотводные каналы:
Характеристики фитиля, такие как эффективная теплопроводность и проницаемость, определяются с учетом его пористости. Формула для проницаемости Kф имеет вид
Значение коэффициента Bф, полученное эмпирическим путем для спеченных металлических мелкопористых фитилей, равно 0.05 [1]. Согласно экспериментальным данным [11], эффективная теплопроводность насыщенного жидкостью фитиля keff пористостью 60%, спеченного из никелевого порошка, составляет от 4 до 5 Вт/(м К).
ЧИСЛЕННАЯ РЕАЛИЗАЦИЯ МОДЕЛИ И ПОСТРОЕНИЕ РАСЧЕТНОЙ СЕТКИ
Решение рассматриваемой краевой задачи получено с использованием метода декомпозиции расчетной области без наложения подобластей [12]. На схеме, представленной на рис. 3, показано разбиение исходной области Ω на две неперекрывающиеся подобласти. Первая “охватывает” весь испаритель Ω1 и является внутренней по отношению ко второй, которая включает в себя тепловой интерфейс Ω2. Для каждой подобласти сформулированы соответствующие подзадачи и граничные условия. Поиск независимого численного решения этих подзадач осуществлялся при условии сопряжения полученных решений на их общей границе Γ.
При построении дискретного аналога системы дифференциальных уравнений и граничных условий использовался метод контрольного объема, обеспечивающий консервативность конечно-разностной схемы [13]. Для расчетов создана сетка, покрывающая всю расчетную область Ω, которая фактически является комбинацией двух сеточных фрагментов различной конфигурации, принадлежащих двум подобластям задачи. Рис. 3 демонстрирует принцип построения расчетной сетки. Видно, что каждый из ее двух фрагментов соответствующим образом адаптирован к особенностям геометрии подобластей Ω1 и Ω2. Так, для элементарных ячеек, принадлежащих тепловому интерфейсу и испарителю, использовались шаблоны прямоугольной и цилиндрической сеток соответственно. Для стыковки соседних элементарных ячеек, принадлежащих различным подобластям, а также для выполнения условия локальной ортогональности теплового потока через их общее ребро вокруг испарителя сформирована зона сопряжения в виде тонкого слоя, пространственно принадлежащая подобласти Ω2. В зоне сопряжения сетка имела нерегулярную структуру с различной конфигурацией элементарных ячеек. Отметим, что используемая в расчетах сетка является согласованной, поскольку все граничные точки находятся в ее узлах, а каждое ребро элементарных ячеек содержит только два узла. Такое построение сетки упрощает аппроксимацию граничных условий на всех границах исследуемого объекта сложной геометрической формы.
При построении расчетной сетки в подобласти Ω1 приняты во внимание результаты численного моделирования процессов тепломассопереноса в испарителе КТТ с организованным удалением пара через пароотводные каналы, представленные в работах [9, 14]. Результаты показали, что зона испарения, расположенная в пристеночном слое фитиля, характеризуется значительными градиентами параметров решения задачи, таких как температура, давление и скорость жидкости в фитиле. Поэтому для лучшего разрешения той части испарителя, где расположены пароотводные каналы, сделано измельчение сетки, тогда как более грубая сетка покрывала запорный слой фитиля. Общее количество ячеек расчетной сетки в радиальном направлении для подобласти Ω1 равно 97, при этом 50 узлов приходились на зону испарения и 10 на корпус испарителя.
Что касается подобласти интерфейса Ω2, то здесь также принимался во внимание принцип экономичного построения расчетной сетки со сгущением ее узлов на участках, где наблюдаются высокие градиенты температуры. Измельчение сетки сделано в тонком слое интерфейса, который располагается непосредственно под его греющей поверхностью. Численное решение задачи получено на расчетной сетке для интерфейса, состоящей из 1938 ячеек.
Ядром программы расчета является итерационный цикл, в который включены два последовательно выполняемых расчетных блока. В первом блоке определяются искомые параметры для теплового интерфейса, а в другом выполняется поиск решения для испарителя. “Сшивание” значений температур и тепловых потоков на их общей границе осуществлялось посредством процедуры обмена соответствующими данными между этими расчетными блоками на каждом итерационном шаге.
Система линейных уравнений, полученная дискретизацией исходных дифференциальных уравнений и граничных условий, решается методом Зейделя. Условие завершения итерационного процесса имеет вид
где N – номер итерации, i – номер узловой точки, ε – допустимая погрешность вычислительной процедуры. В расчетах этот параметр принят равным 10–3.При определении теплофизических параметров теплоносителя используются табличные данные, представленные в [15]. Кубическая сплайн-интерполяция применяется для преобразования табличных данных в температурные зависимости Ψ = f(T), где Ψ – теплофизический параметр теплоносителя. Расчет температуры в i-м узле расчетной сетки на каждом итерационном шаге с номером N осуществляется при значениях теплофизических параметров Ψ теплоносителя, которые определяются согласно этим функциональным зависимостям при температуре, полученной на предыдущем итерационном шаге (N – 1). Алгоритм для идентификации текущего значения параметра Ψ описывается следующим образом:
РЕЗУЛЬТАТЫ ЧИСЛЕННОГО МОДЕЛИРОВАНИЯ И ИХ АНАЛИЗ
Параметры модели и исходные данные. На основе изложенной математической модели проведены численные расчеты полей температур в исследуемом объекте, а также полей давления в фитиле при различных плотностях теплового потока на нагреваемой стороне теплового интерфейса. Основные геометрические размеры и значения теплофизических параметров интерфейса и испарителя приведены в таблице.
Основные параметры задачи
Длина, ширина и толщина интерфейса, мм | 40 × 40 × 12 |
Площадь поверхности нагрева, мм2 | 40 × 40 |
Теплопроводность интерфейса (Сu, Al), Вт/(м К) | 380, 210 |
Диаметр испарителя, мм | 10 |
Толщина корпуса испарителя, мм | 0.3 |
Диаметр центрального канала, мм | 2 |
Глубина и ширина пароотводных каналов, мм | 1, 1 |
Количество пароотводных каналов | 12 |
Теплопроводность корпуса, Вт/(м К) | 17 |
Эффективная теплопроводность фитиля, Вт/(м К) | 4 |
Пористость фитиля, % | 60 |
Радиус пор, мкм | 4 |
Теплоноситель | Фреон 152а |
Температура пара, °С | 40 |
Температура жидкости на входе в испаритель, °С | 20 |
Коэффициент теплоотдачи при испрении, Вт/(м2 К) | 10 000 |
Коэффициент теплоотдачи в центральный канал, Вт/(м2 К) | 100 |
Распределение температуры в тепловом интерфейсе. Плотность теплового потока, подводимого к интерфейсу, в расчетах менялась от 1.25 до 12.5 Вт/см2. Расчет проведен для медного и алюминиевого интерфейсов. Все остальные параметры модели оставались неизменными.
В качестве примера на рис. 4 показано температурное поле медного интерфейса в сечении, перпендикулярном продольной координате при плотности теплового потока 6.25 Вт/см2 (Qн = 100 Вт). Центральная область, занимаемая испарителем, исключена из рассмотрения, поскольку детальный анализ результатов будет представлен ниже. Видно, что периферийные части интерфейса имеют более высокую температуру по сравнению с центральной частью, которая расположена вблизи испарителя, представляющего собой сток тепла. При этом самая холодная зона интерфейса находится под испарителем.
На рис. 5 представлено изменение температуры на термоконтактной поверхности интерфейса по оси X для медного и алюминиевого интерфейсов при плотности теплового потока 6.25 Вт/cм2. Видно, что температура термоконтактной поверхности медного интерфейса ниже, чем алюминиевого, и более однородна. Вместе с тем поведение температурных кривых в целом можно охарактеризовать, как подобное. Так, наиболее горячие участки расположены по краям термоконтактных поверхностей, тогда как их центральные части, находящиеся в непосредственной близости к испарителю, имеют более низкую температуру. Это обстоятельство следует учитывать, например, при термостатировании охлаждаемого объекта, и осуществлять контроль прежде всего температуры удаленных от центра областей, как наиболее теплонапряженных. Следует также отметить, что обе температурные зависимости, представленные на графике, являются нелинейными функциями от x-координаты. Так, при удалении от холодной центральной части поверхности к ее горячим периферийным участкам температура растет сначала быстро, а затем темп ее изменения замедляется. Поведение температуры на наиболее отдаленных участках можно охарактеризовать как квазистабилизированное, причем оно выражено более четко у медного интерфейса.
Рис. 5.
Температура на термоконтактной поверхности медного (1) и алюминиевого (2) интерфейсов при qн = 6.25 Вт/см2.
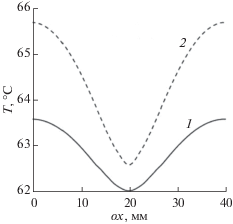
На рис. 6 представлены значения максимального перепада температур ΔTmax на термоконтактной поверхности интерфейса, определяемые как разница температур в самой горячей и самой холодной точках при различных плотностях теплового потока:
Рис. 6.
Максимальные перепады температуры на термоконтактной поверхности медного (1) и алюминиевого (2) интерфейсов при изменении плотности теплового потока.
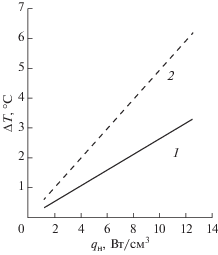
ΔTmax = Tmax – Tmin,
где Tmin – температура в центре поверхности, Tmax – температура в ее крайней точке (из-за симметрии задачи Tmax = T |х= 0 = T |х=b). Видно, что с увеличением плотности теплового потока имеет место линейный рост ΔTmax как для медного, так и для алюминиевого интерфейса, причем у последнего ΔTmax почти в два раза больше, чем у медного. При плотности теплового потока 12.5 Вт/см2, что соответствует подводимой тепловой нагрузке 200 Вт, неоднородность температуры на термоконтактной поверхности ΔTmax становится весьма существенной, достигая 3.3 и 6.2°С для медного и алюминиевого интерфейсов соответственно.
Плотность теплового потока на границе интерфейс–испаритель. Неоднородность температурного поля в центральной части интерфейса приводит к тому, что внешняя поверхность испарителя подвергается различным тепловым воздействиям. На рис. 7 показана величина приведенной компоненты плотности теплового потока на границе между интерфейсом и испарителем в зависимости от угловой координаты:
где qn – нормальная компонента плотности теплового потока на внешней поверхности испарителя, размещенного в интерфейсе; φ – угловая координата, отсчитываемая от полярной оси, которая направлена перпендикулярно к термоконтактной поверхности интерфейса; qравн – нормальная компонента плотности теплового потока при равномерном подводе тепла той же мощности к испарителю (qn(φ) = const). С точки зрения эффективности работы испарителя равномерный подвод тепла следует рассматривать как оптимальный вариант. Отклонение расчетных кривых для медного и алюминиевого интерфейсов от линии $q_{{{\text{равн}}}}^{*}(\varphi )$ = 1 показывает степень неравномерности нагрева испарителя. Так, для алюминиевого интерфейса отклонение плотности теплового потока в верхней горячей и нижней холодной точках испарителя от значения $q_{{{\text{равн}}}}^{*}$ при равномерном нагреве составляет 6.4 и 11.6% соответственно. Для медного интерфейса величина этого отклонения снижена. Это говорит о том, что имеет место более равномерный подвод тепла к поверхности испарителя. Отклонение плотности теплового потока в верхней горячей и нижней холодной точках испарителя с медным интерфейсом составляет 3.9% и 7.0% соответственно.Рис. 7.
Приведенная плотность теплового потока на поверхности испарителя с медным (1) и алюминиевым (2) интерфейсами; 3 – qравн.
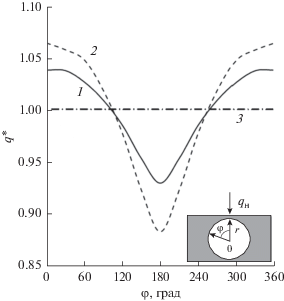
Распределение температуры в испарителе. На рис. 8a в качестве примера представлено температурное поле испарителя, размещенного в алюминиевом интерфейсе, в сечении, перпендикулярном продольной координате, при плотности теплового потока, подводимого к интерфейсу, qн = = 3.125 Вт/см2. В испарителе имеется горячая зона в виде узкого дугообразного сегмента, которая охватывает верхнюю часть корпуса и примыкающий к нему тонкий пристеночный слой фитиля. Высокие температуры в этой части испарителя обусловлены близким расположением к ней горячей термоконтактной поверхности интерфейса.
Рис. 8.
Температурное поле испарителя с Al тепловым интерфейсом (a) и распределение температуры на поверхности испарителя с медным (1) и алюминиевым (2) интерфейсами (б) при qн = 3.125 Вт/см2 и Ts = 40°C, теплоноситель – фреон 152а.
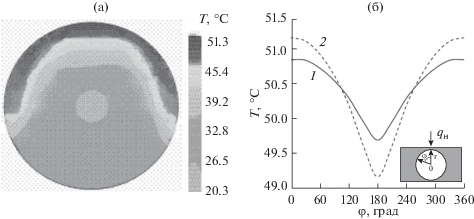
На рис. 8б показано изменение температуры на внешней поверхности корпуса испарителя, размещенного в медном и алюминиевом интерфейсах, при qн = 3.125 Вт/см2. Распределение температуры на внешней поверхности испарителя сильно зависит от теплопроводности материала интерфейса. Медный интерфейс обеспечивает более равномерный нагрев испарителя, и его температурная кривая имеет более сглаженный вид по сравнению с кривой для испарителя, размещенного в алюминиевом интерфейсе. Вместе с тем, несмотря на то что значения температур в верхней и нижней точках испарителя с различными интерфейсами отличаются значительно, боковые части испарителя имеют приблизительно одинаковую температуру.
Интенсивность испарения жидкости с поверхности фитиля в пароотводные каналы зависит от перепада температур между этой поверхностью и насыщенным паром над ней Ts. Таким образом, в верхней горячей части испарителя процесс парообразования должен идти более активно, чем в нижней холодной его части. Рассчитав полное количество теплоты Qi, затраченное на испарение в каждом из 12 пароотводных каналов, можно оценить вклад каждого канала в работу испарителя, используя для этого формулу
Рис. 9.
Интенсивность испарения в пароотводные каналы (№ = 1–12) испарителя с медным (1) и алюминиевым (2) интерфейсами.
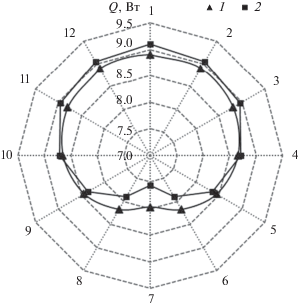
На рис. 10 показано падение давления в фитиле в зависимости от угловой координаты φ для трех значений плотности теплового потока qн, подводимого к алюминиевому интерфейсу. На рисунке также представлены зависимости капиллярного давления от φ, полученные при температурах на внешней поверхности фитиля при соответствующих qн. На каждом из трех графиков можно наблюдать противоположную тенденцию поведения кривых. С ростом qн капиллярное давление падает из-за повышения температуры, а фильтрационные потери давления растут. Отметим также, что на горячем участке зоны испарения, характеризуемой высокой интенсивностью парообразования, капиллярное давление имеет наименьшее значение по сравнению с тем давлением, которое создают мениски, находящиеся в более холодных частях фитиля, где имеют место низкие расходы жидкости в фитиле и, соответственно, низкие потери давления. Рис. 10а демонстрирует режим нормальной работы КТТ, при котором для всей поверхности фитиля с большим запасом выполняется основное условие работоспособности теплопередающих устройств с капиллярной прокачкой теплоносителя, таких как, например, контурные тепловые трубы, а именно
Рис. 10.
Капиллярное давление (1) и падение давления в фитиле (2) при изменении плотности теплового потока: (a) – qн = 12.5 Вт/см2, нормальный режим; (б) – 18.3 Вт/см2, предкризисный режим; (в) – 18.8 Вт/см2, кризис; теплоноситель – фреон 152а.
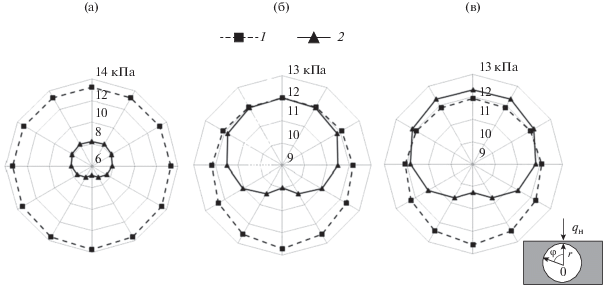
При увеличении теплового потока, подводимого к интерфейсу, кривые ΔPф = f(φ) и ΔPс = f(φ) сближаются, поскольку потери давления в фитиле с ростом qн увеличиваются, тогда как капиллярное давление падает из-за повышения температуры испарителя. На рис. 10б показана ситуация, при которой КТТ работает в предкризисном режиме. В верхней наиболее горячей части испарителя потери давления в фитиле становятся соизмеримы с величиной капиллярного давления:
Дальнейшее незначительное повышение qн до величины 18.8 Вт/см2 приводит к кризису теплообменных процессов в горячей части фитиля (рис. 10в). Видно, что в секторе –60° ≤ φ ≤ +60° кривая ΔPф = f(φ) располагается выше кривой ΔPс = f(φ). Это означает, что капиллярного давления здесь недостаточно для прокачки теплоносителя и подпитки фитиля жидкостью. Такая ситуация является неблагоприятной для работы КТТ, поскольку приводит к осушению фитиля, кризису теплообмена в зоне испарения и прекращению циркуляции теплоносителя в КТТ. Соответственно, в данном случае значение qн = 18.8 Вт/см2 определяет верхнюю границу теплопередающей способности КТТ из-за капиллярных ограничений.
Верификация расчетной модели. Верификация расчетной модели проводилась на основе сравнения полученных результатов расчета с данными работы [7], в которой представлен анализ расчетных данных распределения температуры в медном тепловом интерфейсе КТТ, имеющем такие же геометрические параметры. Результаты численного моделирования при одностороннем подводе тепла к интерфейсу получены с использованием коммерческого пакета SolidWorks Simulation. В этой компьютерной модели испаритель не рассматривался, а поверхность контакта между испарителем и интерфейсом моделировалась как поверхностный сток тепла с заданным коэффициентом теплообмена. Согласно выполненным расчетам [7], при тепловых нагрузках 100 Вт (6.25 Вт/см2) и 300 Вт (18.75 Вт/см2) неоднородность температуры на поверхности контакта интерфейс–испаритель составляет 1.8 и 5°С соответственно. Значения неоднородности температуры на этой поверхности, полученные по предложенной расчетной модели, при этих же значениях тепловой нагрузки равны 1.66 и 4.95°С соответственно. Расхождение значений неоднородности температуры двух компьютерных расчетов составляет около 8%. Более низкие значения неоднородности температуры, полученные в данной работе, по-видимому, связаны с тем, что в ее расчетной модели учитываются процессы теплопереноса в самом испарителе.
Кроме того, изучена зависимости численного решения от разрешения исследуемого объекта с целью поиска минимально необходимой расчетной сетки для получения качественного расчета. На участках с повышенными градиентами температуры проведены исследования чувствительности численного решения к размеру элемента расчетной сетки на этих участках. В работах [9, 13] показано, что таким особым участком является зона испарения. Результаты оценочных расчетов, полученные в данной работе на грубой сетке, также показали, что значения градиентов температуры здесь значительно выше, чем на других частях испарителя. Для исследования сходимости решения задачи по расчетной сетке было использовано шесть вариантов локального измельчения сетки. Количество ячеек, покрывающих зону испарения, менялось в радиальном направлении от 6 до 50. На рис. 11 показаны значения температуры в самой горячей точке испарителя, которая расположена на его оси симметрии, в непосредственной близости от нагреваемой поверхности интерфейса, при последовательном измельчении расчетной сетки в зоне испарения. Эта температура выбрана в качестве параметра для контроля сходимости численного решения задачи по размеру шага расчетной сетки, так как в экспериментальных исследованиях значения этой температуры используются в качестве основной рабочей характеристики контурной тепловой трубы. Расчеты проведены при плотности теплового потока qн = 3.125 Вт/cм2 (50 Вт), подводимой к медному интерфейсу. Температура пара в пароотводных каналах равна 40°С. Анализ результатов на рис. 11 говорит о том, что имеет место выход полученной расчетной кривой на асимптоту, при которой дальнейшее измельчение сетки не приводит к существенному изменению температуры. Видно, что чувствительность численного решения задачи к локальному сгущению расчетной сетки в зоне испарения становится крайне низкой уже при количестве ячеек N = 30. При N = 40 и выше температура практически не меняется. Значение N = 50 принято как достаточное для удовлетворительной дискретизации зоны испарения. Результаты численного моделирования тепломассопереноса в системе “прямоугольный интерфейс – цилиндрический испаритель”, представленные в работе, получены для N = 50.
ЗАКЛЮЧЕНИЕ
Разработана модель тепломассопереноса в цилиндрическом испарителе контурной тепловой трубы, размещенном в центре теплового интерфейса, в виде прямоугольного параллелепипеда при подводе тепла к одной из его сторон. Описан алгоритм численного решения задачи. Получены данные о распределении температуры и интенсивности испарения в испарителе с медным и алюминиевым интерфейсами.
Анализ результатов показал, что теплопроводность интерфейса существенным образом влияет на формирование поля температур как самого интерфейса, так и испарителя. Наиболее холодной зоной на нагреваемой поверхности интерфейса является его центральная часть. Увеличение плотности теплового потока на теплоподводящей поверхности интерфейса приводит к повышению неравномерности распределения температуры на этой поверхности. При изменении плотности теплового потока от 1.25 до 12.5 Вт/см2 неоднородность температуры для алюминиевого интерфейса увеличивается с 0.62 до 6.22°С, тогда как у медного интерфейса она повышается с 0.33 до 3.32°С.
Получены данные о неравномерности плотности теплового потока на границе интерфейс–испаритель. Выявлен теплонапряженный участок испарителя с высокой интенсивностью теплообменных процессов в зоне испарения, который располагается вблизи нагреваемой поверхности интерфейса. Результаты показали, что использование более теплопроводных материалов для интерфейса снижает степень неравномерности теплообмена в испарителе, повышая эффективность его работы.
Обозначения. b – ширина, hисп – теплота парообразования, S – площадь, r – радиус, rc – радиус капилляра, v – скорость, x – координата, сp – изобарная теплоемкость, κ – коэффициент теплопроводности, μ – вязкость, ρ – плотность, Ω – поверхность, σ – поверхностное натяжение.
Индексы: исп – испарение, инт – интерфейс, корп – корпус, н – нагрев, ох – охлаждающий, пк – пароотводной канал, равн – равномерный, ф – фитиль, цк – центральный канал, окр – окружающий, eff – эффективный, q – зона нагрева, l – жидкость, n – нормаль.
Список литературы
Майданик Ю.Ф., Ферштатер Ю.Г., Пастухов В.Г. Контурные тепловые трубы: разработка, исследования, элементы инженерного расчета. Препринт. Свердловск: Изд. УрО АН СССР, 1989. 52 с.
Ku J. Operating Characteristics of Loop Heat Pipes // Int. Conf. on Environmental Systems, Denver (SAE). July 1999. Paper 1999-01-2007.
Maydanik Yu.F. Review: Loop Heat Pipes // Appl. Therm. Eng. 2005. V. 25. P. 623.
Maydanik Yu.F., Chernysheva M.A., Pastukhov V.G. Review: Loop Heat Pipes with Flat Evaporators // Appl. Therm. Eng. 2014. V. 67. P. 294.
Maydanik Yu.F., Vershinin S.V., Chernysheva M.A. Experimental Study of an Ammonia Loop Heat Pipe with a Flat Disk-shaped Evaporator Using a Bimetal Wall // Appl. Therm. Eng. 2017. V. 126. P. 643.
Hodot R., Sartre V., Lefevre F., Sarno C. 3D Modeling and Optimization of a Loop Heat Pipe Evaporator // 17th Int. Heat Pipe Conf. (17th IHPC). Kanpur, India, 2013. № 13.
Maydanik Y.F., Vershinin S.V., Chernysheva M.A. The Results of Comparative Analysis and Tests of Ammonia Loop Heat Pipes with Cylindrical and Flat Evaporators // Appl. Therm. Eng. 2018. V. 144. P. 479.
Пожилов А.А., Зайцев Д.К., Смирнов Е.М., Смирновский А.А. Численное моделирование теплопереноса в трехмерной модели контурной тепловой трубы // Науч.-тех. ведомости СПбГПУ. Физ.-мат. науки. 2017. Т. 10(3).
Ферштатер Ю.Г. Теплообмен в тепловых трубах с раздельными каналами. Дис. … канд. физ.-мат. наук. Свердловск, 1988. 194 с.
Белоногов А.Г. Влияние динамических факторов на тепломассоперенос в тепловых трубах. Дис. … канд. физ.- мат. наук. Свердловск, 1989. 159 с.
Беляев А.А. Тепло- и массоперенос в мелкопористых капиллярных структурах тепловых труб. Дис. … канд. физ.-мат. наук. Свердловск, 1990. 168 с.
Самарский А.А., Бабищевич П.Н. Вычислительная теплопередача. М.: Едиториал УРСС, 2003. 782 с.
Anderson D.A., Tannehill J.C., Fletcher R.H. Computational Fluid Mechanics and Heat Transfer. N.Y.: Hemisphere Publ. Corp., 1990.
Chernysheva M.A., Maydanik Y.F. Simulation of Heat and Mass Transfer in a Cylindrical Evaporator of a Loop Heat Pipe // Int. J. Heat Mass Transfer. 2019. V. 131. P. 442.
http:// webbook.nist.gov
Дополнительные материалы отсутствуют.
Инструменты
Теплофизика высоких температур