Теплоэнергетика, 2023, № 4, стр. 78-91
Проблемы гидродинамики и теплообмена в связанных между собой реакторах с кипящим слоем для улавливания СО2 и получения водорода
Г. А. Рябов a, *, О. М. Фоломеев a
a Всероссийский теплотехнический институт
115280 Москва, Автозаводская ул., д. 14, Россия
* E-mail: Georgy.ryabov@gmail.com
Поступила в редакцию 13.09.2022
После доработки 12.10.2022
Принята к публикации 26.10.2022
Аннотация
Технология сжигания и газификации в химических циклах со связанными между собой реакторами с кипящим (КС) и циркулирующим кипящим слоем (ЦКС) интенсивно развивается в связи с декарбонизацией энергетики и возможностью получения полезных продуктов из органических топлив. Эта технология пока еще находится в стадии фундаментальных и прикладных исследований на лабораторных и пилотных установках мощностью до 3 МВт. Однако некоторые последние исследования убедительно доказывают, что она может обеспечить относительно низкие затраты на улавливание СО2 (на уровне 30 евро/т). Новые направления в исследованиях связаны с использованием трех реакторов с оксидами металлов (главным образом природных оксидов и оксидов железа) для получения водорода и метанола. Рассмотрены основные проблемы гидродинамики и теплообмена в системах с химическими циклами. Для выравнивания температур между связанными между собой реакторами, в одном из которых происходят реакции с поглощением тепла, а в другом – с его выделением, требуется очень большой расход циркулирующего материала. Показано, что решение задачи выноса достаточного количества частиц, влияния на него их размеров, скорости, массы слоя является крайне важным. Другая проблема – обеспечение очень высокой степени улавливания в циклонах (на уровне 99.9%), которая определяется скоростным режимом и размерами частиц. Наконец, необходимо надежно транспортировать уловленные частицы между реакторами. Показано, что при больших концентрациях частиц возрастает доля кондуктивно-конвективной составляющей теплообмена. Эта задача, как и задача теплообмена в среде пара и кислорода или кислорода и СО2, также является актуальной. Представлены некоторые результаты экспериментальных исследований, проведенных в ОАО ВТИ на крупной аэродинамической установке.
Во всем мире растет признание того, что выбросы парниковых газов необходимо сократить до нуля примерно к 2050 г., чтобы ограничить повышение глобальной температуры в этом столетии целевым показателем 1.5°C и смягчить с-ерьезные последствия изменения климата. Более 130 стран обязались прийти к нулевым, чистым выбросам к 2050 г. Китай стремится достичь углеродной нейтральности к 2060 г., а Индия ставит перед собой цель решить эту проблему к 2070 г. Современные требования декарбонизации глобальной экономики диктуют необходимость увеличения использования возобновляемых источников энергии (ВИЭ). Однако для многих стран такой подход не всегда оправдан и требует высоких затрат, тогда как надежность поставки электроэнергии жизненно важна для стабильной и растущей экономики. Для достижения необходимого сокращения выбросов СО2 потребуется ряд мер, в том числе улучшение технологических характеристик энергетических предприятий, использование возобновляемых источников энергии, альтернативных топлив и технологий улавливания, захоронения и полезного использования СО2 (CCUS).
С экономической точки зрения модернизация с CCUS, как правило, наиболее целесообразна для электростанций и промышленных объектов, которые являются молодыми, эффективными и расположены вблизи мест с возможностью использования или хранения CO2. Другими техническими характеристиками, которые необходимо учитывать при оценке того, будет ли модернизация иметь коммерческий или экономический смысл, являются мощность, наличие места на площадке для оборудования улавливания СО2, коэффициент загрузки, тип установки, близость к транспортной инфраструктуре CO2 и уверенность в долгосрочной доступности емкости для хранения CO2. В странах с развитой экономикой, где промышленные мощности, как правило, старше, существует больше возможностей для досрочного вывода установок из эксплуатации, поскольку связанные с этим экономические потери обычно ниже. В странах с развивающейся экономикой и более молодыми установками упор, скорее всего, будет сделан на модернизацию тепловых электрических станций (ТЭС) с использованием более эффективных технологий и технологий CCUS. Около 190 ГВт угольных мощностей, в основном в Китае, и 160 ГВт газовых мощностей должны быть модернизированы с помощью CCUS.
Технология CCUS будет обеспечивать более 90% совокупного сокращения выбросов CO2 при преобразовании топлива [1, 2]. Около 30% сокращений будет связано с производством водорода и аммиака из ископаемого топлива и диоксида углерода, улавливаемого предприятиями по производству биотоплива, что будет также способствовать сокращению выбросов СО2 в транспортном секторе. Оборудование для улавливания СО2 используется в коммерческих целях для очистки природного газа и других газов с 1930-х годов. Диоксид углерода был впервые введен под землю в промышленных масштабах в 1972 г., и его ежедневно транспортируют по трубопроводам и, в меньшей степени, грузовиками, поездами и кораблями во многих частях мира. Технологию CCUS можно применять на ТЭС, работающих на ископаемом топливе (как на угле, так и на природном газе), чтобы обеспечить их эксплуатацию при низком уровне выбросов СО2 в дополнение к ВИЭ.
Существуют четыре основных типа процессов улавливания СО2:
улавливание после сжигания топлива. Большинство таких технологий, используемых сегодня в проектах, представляют собой абсорбционные системы на основе аминов;
кислородное сжигание – топливо сжигается в среде кислорода и рециркулируемого CO2. Благодаря исключению азота отделение CO2 становится относительно простым процессом конденсации воды из дымовых газов. Однако для производства кислорода требуется воздухоразделительная установка, что увеличивает стоимость системы и эксплуатационные затраты;
улавливание СО2 перед сжиганием – на электростанции с комбинированным циклом с интегрированной (внутрицикловой) газификацией, при которой топливо газифицируется (преобразуется в смесь CO/H2/CO2), обычно включающей стадию реакции конверсии водяного газа для увеличения концентрации водорода путем взаимодействия монооксида углерода с водяным паром;
применение кальциевых или высокотемпературных химических циклов с оксидами металлов – носителями кислорода. Используются по меньшей мере два связанных между собой реактора с кипящим и циркулирующим кипящим слоем.
Уровень технологической готовности (TRL) компонента или системы качественно оценивает зрелость технологии на различных этапах исследований и разработок. Некоторые из технологий CCUS, находящихся на разных стадиях разработки, легко приобретают коммерческие масштабы (TRL9), большинство же из них находится на стадии пилотной установки (TRL6) или выше [3]. Препятствия для широкомасштабного развертывания CCUS не являются техническими, и существует потенциал для будущего снижения затрат за счет применения технологий следующего поколения.
Химические циклы улавливания СО2 основаны на технологии связанных между собой реакторов. В кальциевых циклах СО2 удаляется из уходящих газов. Технологии кальциевых циклов в настоящее время находятся на стадии TRL 5–6. Они были испытаны, главным образом, на пилотных установках с псевдоожиженным слоем, работающих на угле, и для производства цемента. Химические циклы с оксидами металлов – носителями кислорода также основаны на связанных между собой реакторах с циркулирующим кипящим слоем. В настоящее время ведутся разработки и реализуются уже около 35 пилотных проектов (TRL 4–6) мощностью до 3 МВт для сжигания угля, газа, нефти и биомассы [4].
В последние десятилетия водород приобретает все большее значение как источник энергии для транспорта, энергетики и строительства [1, 2]. Это во многом связано c повышением использования ВИЭ и необходимостью сохранения энергии, а также отсутствием выбросов СО2 при сжигании водорода. В некоторых странах (Великобритании, Нидерландах, Германии, Италии, США, Японии, Австралии) приняты программы исследований и коммерциализации в области получения водорода и его использования на транспорте и в энергетике. Чистый водород можно получить из ископаемого топлива или с помощью электролиза. Водород также выделяется в смеси с другими газами в качестве побочного продукта в различных процессах.
Производство водорода с использованием технологии химического цикла вызывает все больший интерес в последние годы, потому что производительность процесса его получения довольно велика и при этом происходит улавливание диоксида углерода. В таких системах используются три связанных между собой реактора [5]. Подобные схемы можно также применять и для производства метанола [6].
ТЕХНОЛОГИИ СЖИГАНИЯ И ГАЗИФИКАЦИИ В ХИМИЧЕСКИХ ЦИКЛАХ ДЛЯ УЛАВЛИВАНИЯ СО2 И ПОЛУЧЕНИЯ ПОЛЕЗНЫХ ПРОДУКТОВ
В [7] выполнен анализ современного состояния исследований и разработок по улавливанию CO2 в химических циклах сжигания и газификации топлив (CLC). В настоящее время эта технология находится в стадии исследований на лабораторных и пилотных установках мощностью до 3 МВт. Суть этой технологии сводится к такой организации процесса горения, когда переносчиком кислорода к топливу является не воздух, а оксид металла. Последний при взаимодействии с топливом в топливном реакторе восстанавливается до металла (или более низкого оксида) с образованием СО2 и водяного пара. После этого металл окисляется в воздушном реакторе и получившийся оксид вновь направляется в цикл. Выходящие из топливного реактора газы после конденсации водяного пара представляют собой практически чистый СО2, который может быть направлен на захоронение или утилизацию.
Схема процесса при сжигании газообразного топлива, включая продукты газификации твердых топлив, показана на рис. 1. В воздушном реакторе 1 с циркулирующим кипящим слоем происходят реакции окисления металлов М, а газовый поток, состоящий в основном из азота с небольшим количеством кислорода и паров воды, направляется в котел-утилизатор или газовую турбину (при работе системы под высоким давлением). Частицы оксидов металлов (ОМ) выносятся потоком в верхнюю часть воздушного реактора, откуда попадают в циклон 2, после которого они поступают в топливный реактор 3 с пузырьковым кипящим слоем, ожижающим агентом которого является газообразное топливо. В этом реакторе частицы оксидов металлов восстанавливаются до металлов и поступают через пневматический затвор 4 в воздушный реактор. Смесь газов, выходящих из топливного реактора, состоит из СО2 и водяного пара. Этот поток газов поступает в свой котел-утилизатор и далее в конденсатор водяных паров, а осушенный СО2 направляется на захоронение. В общем случае реакция восстановления выглядит следующим образом:
(1)
$\begin{gathered} \left( {2n + m} \right)OМ + C{{H}_{4}} \to \\ \to \,\,\left( {2n + m} \right)M + m{{H}_{2}}O + nC{{O}_{2}}. \\ \end{gathered} $Рис. 1.
Схема процесса сжигания газообразного топлива в химическом цикле. 1, 3 – окислительный (воздушный) и восстановительный (топливный) реактор; 2 – циклон; 4 – пневмозатвор
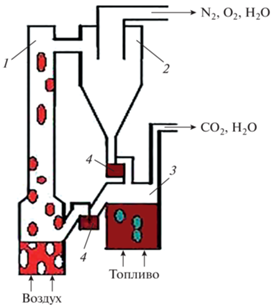
После восстановления металлы поступают в реактор 1 (см. рис. 1), где происходит их окисление с помощью воздуха или смеси кислорода и азота с пониженным содержанием кислорода (около 5%):
Реакции осуществляются при температурах 800–1100°С при суммарном тепловом эффекте, равном тепловому эффекту при обычном сжигании топлива в воздухе. В качестве оксидов – переносчиков кислорода используют оксиды различных металлов, главным образом железа и никеля. В последнее время все чаще стали применять природные минералы, например ильменит, а также отходы металлургии. В настоящее время, по данным [8], насчитывается уже более 600 работ, посвященных различным аспектам использования химических циклов. В ходе экспериментов было установлено, что возможно почти полное сжигание топлива при практически 100%-ном улавливании СО2. Пока только на нескольких установках использовали твердое топливо [9]. Продолжительность эксплуатационного опыта в мире по сжиганию топлива в химических циклах, включающих носители кислорода на основе оксидов никеля, железа, марганца, меди и кобальта, составляет более 9000 ч [10]. В последнее время значительный интерес проявляется к использованию естественных дешевых минералов – ильменита и железомарганцевых минералов. Это, прежде всего, относится к сжиганию твердых топлив [11]. Для природного газа наиболее эффективными считаются композиты на основе оксидов никеля, железа и алюминия.
Авторы [11] считают, что технология высокотемпературных химических циклов уже прошла стадию лабораторных исследований, и в ближайшее время намечено сооружение пилотных установок. Такие реакторы применяют в полигенерирующих системах с пиролизом (газификацией) и получением полезных продуктов (генераторного газа с высокой теплотой сгорания и оптимальным соотношением концентраций H2 и СО для реакции Фишера ‒ Тропша с выделением компонентов моторных топлив) [12]. Уже работают промышленные установки, например демонстрационная установка в Гюссинге (Австрия) тепловой мощностью 8 МВт и электрической мощностью 2 МВт (рис. 2). В качестве топлива используется биомасса, но установка может также работать при совместной газификации биомассы с углем. Газы после охлаждения очищаются в рукавном фильтре и мокром скруббере и поступают в газопоршневую машину. Многолетний опыт работы установки показал ее надежность и экономичность.
Рис. 2.
Схема полигенерирующей установки в Гюссинге, Австрия [12]. 1 – связанные реакторы, газификатор и дожигатель кокса; 2 – охладитель синтез-газа; 3, 11 – фильтр; 4 – скруббер; 5 – газовая турбина; 6 – катализатор; 7 – охладитель дымовых газов; 8 – котел районного теплоснабжения; 9 – мазутная горелка; 10 – дымовая труба; 12 – охладитель дымовых газов
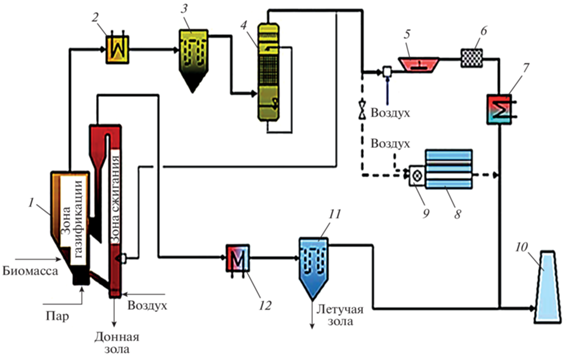
Схемы с тремя связанными реакторами являются перспективными для производства водорода с улавливанием СО2 [13]. В [14] приведена схема получения водорода при газификации углей с реализацией технологии химических циклов (рис. 3). Подобная схема (без газификатора) может быть использована для извлечения водорода из природного газа с улавливанием СО2. Система состоит из кислородной станции, газификатора, системы очистки синтез-газа, восстановительного и окислительного реакторов и тракта сжигания.
Рис. 3.
Схема получения водорода при газификации угля с использованием химических циклов [14]. 1 – газификатор; 2 – керамический фильтр; 3 – очиститель газов; 4, 5 – восстановительный и окислительный реактор; 6 – генератор; 7 – паровая турбина; 8 – компрессор; 9 – кислородная станция
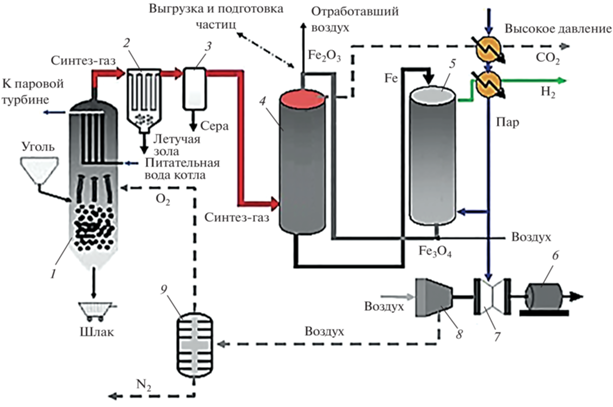
Очищенный синтез-газ поступает в восстановительный реактор с кипящим слоем из частиц оксидов железа, где образуется смесь водяных паров и СО2. Восстановленные оксиды железа направляются в окислительный реактор, в котором образуется водород. Пар генерируется при охлаждении синтез-газа и в тракте сжигания, в котором происходит регенерация Fe3O4 до Fe2O3 с помощью сжатого воздуха (транспортный реактор) и выделяется значительное количество тепла. Восстановительный и окислительный реакторы могут быть установлены один над другим с гравитационным перетоком (или с затворами). В результате имеется своеобразная система с циркулирующим кипящим слоем (транспортный реактор с подъемным движением, уловитель частиц и два опускных реактора). Считается, что в описанной системе может быть обеспечено производство водорода и электроэнергии с высоким КПД.
Сумма тепловых эффектов реакций может быть слегка эндотермической или экзотермической в зависимости от состава газа и температуры. Смесь пара и СО2 под высоким давлением поступает в конденсатор и далее СО2 может быть отправлен на захоронение. В этой системе при высоких давлении и температуре возможно использовать тепло реакций для выработки электроэнергии в комбинированном цикле, что повышает эффективность производства водорода.
Система с тремя реакторами изучена также в [15], где показано, что она имеет заметные преимущества перед другими системами производства водорода из природного газа благодаря достаточно полному улавливанию СО2. Однако при реализации этой технологии возникают проблемы, связанные с необходимостью обеспечивать очень высокую кратность циркуляции оксидов металлов между реакторами и требуемый срок службы этих оксидов без потери ими реакционной способности и уноса их из системы.
Технико-экономический анализ использования химических циклов с тремя реакторами при производстве водорода из природного газа выполнен в [16]. Термодинамическое моделирование на базе программного комплекса Aspen Plus включает в себя производство водорода в химическом цикле риформинга, паросиловой цикл и систему сжатия полученных газов (CO2 и H2). Параметрические исследования выполнялись применительно к условиям Объединенных Арабских Эмиратов, в модели варьируются ключевые рабочие параметры (массовые расходы топлива, пара, воздуха и оксидов металлов). Результаты исследований показали, что электрический КПД снижается при увеличении расхода топлива, массового расхода пара и воздуха и повышается при увеличении количества оксидов металлов. Эффективность производства водорода существенно зависит от температуры в реакторах и уменьшается с увеличением расхода пара, воздуха и оксидов металлов. Она также повышается при увеличении расхода топлива. Общая эффективность производства электроэнергии и водорода снижается с ростом расхода воздуха и пара и увеличивается с ростом массы (дополнительной подачи) оксидов металлов. Стоимость производства водорода с улавливанием CO2 составляет 1.679 дол/кг, что значительно ниже стоимости водорода, получаемого по широко распространенной в мире технологии парового риформинга метана с улавливанием CO2 (около 2.39 дол/кг).
ОСНОВНЫЕ ПРОБЛЕМЫ ГИДРОДИНАМИКИ И ТЕПЛООБМЕНА В СИСТЕМАХ ХИМИЧЕСКИХ ЦИКЛОВ СЖИГАНИЯ И ГАЗИФИКАЦИИ ТОПЛИВ
Химические циклы со связанными между собой реакторами отличаются от процессов в одиночных аппаратах с КС и ЦКС наличием сложной системы перетоков между реакторами со своими пневматическими затворами. Еще одно отличие заключается в использовании оксидов металлов – носителей кислорода, которые имеют иные физические характеристики по сравнению с традиционным материалом слоя – песком. Другие особенности, как, например, наличие большой массы и расхода циркулирующих частиц, влияние на суммарный теплообмен концентрации частиц в потоке, зависящей от гидродинамических характеристик реакторов (прежде всего скорости газов и размеров частиц), остаются такими же, как и для одиночных реакторов. Особенно важными становятся вопросы улавливания частиц для обеспечения их максимальной циркуляции между реакторами. Это требование связано с необходимостью выравнивания температур в реакторах, так как в одном из них происходит эндотермическая реакция, а в другом – экзотермическая.
Гидродинамика реакторов
Кратность циркуляции частиц по отношению к расходу воздуха или метана уменьшается при увеличении емкости оксидов по кислороду. В то же время, расход частиц не является параметром, зависящим от химических процессов, а определяется скоростью газа, его физическими свойствами, а также размером и плотностью частиц. В [17] показано, что для смеси оксидов на основе никеля (60% NiO и 40% Al2O3), необходимой для механической стабильности частиц, требуется расход циркуляции от 1 до 4 кг/(МВт · с). Для оксидов железа этот расход еще больше. При расчете мощности с использованием расхода и теплоты сгорания метана кратность циркуляции по отношению к метану должна составлять 300–1200. Грубые оценки дают значение удельного расхода на сечение окислительного реактора примерно 20 кг/(м2 · с).
В [7] приведен список наиболее значимых публикаций с результатами экспериментальных исследований гидродинамических процессов реакторов, связанных между собой. В целом можно отметить, что собственно гидродинамика каждого из реакторов вполне может быть рассчитана по многочисленным зависимостям. Например, методика расчета для аппаратов с ЦКС, разработанная в ОАО ВТИ [18], заключается в определении аксиального профиля концентраций по ее высоте и удельного расхода материала с учетом внутренней циркуляции за счет сепарации части материала в зоне потолка топки. Расчет аксиального профиля концентраций по высоте реактора с ЦКС дает зависимости этого профиля от массы слоя в реакторе, скорости газа и физических параметров газа и частиц с учетом температуры и давления. По рекомендациям [18] определяется влияние указанных параметров на удельный расход материала в реакторе.
При выведении зависимостей используются традиционные критерии Архимеда, Рейнольдса, Фруда, что дает возможность применять их и для различных газовых сред. Однако поскольку они содержат эмпирические коэффициенты, то для точного определения профиля концентраций и расхода частиц следует провести эксперимент на относительно крупных установках при реальных температурах и средах с повышенным содержанием водяных паров (паровая газификация) и СО2 (кислородное дутье с рециркуляцией СО2).
В последнее время специалисты ОАО ВТИ выполнили исследования гидродинамики бинарных систем, которая ранее не была достаточно изучена [19, 20]. При моделировании условий движения бинарных смесей, состоящих из тяжелых оксидов металлов и относительно легких частиц золы, учтены результаты работы установок по сжиганию твердых топлив в CLC. Исследования проводили на холодной модели системы связанных между собой реакторов, описанной ранее. Были определены поля массовых потоков частиц в верхней части реактора с ЦКС с помощью S-образного пробоотборного зонда. По результатам отборов исследовали подъемные, опускные и суммарные массовые потоки частиц. Далее анализировали фракционный состав подъемных потоков в центре установки и опускных потоков у стен. Доли оксидов алюминия и песка в отобранных пробах определяли с помощью рентгенофазового анализа на приборе VRA-30 с предварительной тарировкой на чистом оксиде алюминия и песке.
Исследования условий начала псевдоожижения бинарных смесей оксидов металлов и песка показали снижение скорости минимального псевдоожижения при небольшой первоначальной добавке песка. Зависимость относительного градиента давлений от объемной доли тяжелых частиц носит линейный характер. Согласно результатам исследований профилей массовых потоков в зоне выхода из реактора с ЦКС, в пределах массовых долей песка 3.5–12.0% добавка его не оказывает существенного влияния на профиль суммарных массовых потоков. Средний по поверхности размер частиц оксидов алюминия составил в этих опытах 0.236 мм, истинная плотность – 3940 кг/м3, насыпная плотность – 1970 кг/м3. На рис. 4 показана зависимость удельного расхода частиц от скорости ожижения при различных долях песка. В исследованном диапазоне этих добавок влияние на удельный расход частиц не наблюдается. По данным авторов, полученным при использовании песка (зона 5), удельный расход несколько больше, что объясняется меньшей плотностью частиц.
Рис. 4.
Зависимость удельного расхода частиц $\bar {G}$ от скорости ожижения U. 1 – чистый Al2O3; доля песка в смеси, %: 2 – 3–4; 3 ‒ 6–7; 4 – 10–12; 5 – частицы песка размером 0.18–0.20 мм, масса материала до 60 кг
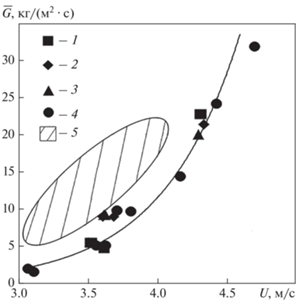
Таким образом, можно сделать вывод, что для исследованной области долей легкой фракции расчет гидродинамики реактора с ЦКС можно проводить, как для фракции оксидов металлов, с использованием разработанных ранее зависимостей. Фракционные составы всех проб из подъемного потока в центре реактора с ЦКС и опускного потока у стен легли на одну линию, что характерно для режима с ЦКС с одинаковыми плотностями частиц. Средний размер отобранных частиц лишь немного меньше среднего размера частиц Al2O3. В подъемном потоке в центре реактора доля песка несколько выше, чем в опускном потоке, и больше средних значений по массовой засыпке в реактор. При этом с увеличением скорости разница в значениях концентраций немного снижается.
Для достижения требуемого удельного расхода частиц необходима скорость воздуха более 4.5 м/с. При этом средний размер частиц должен составлять 0.15–0.20 мм, а высота слоя – не менее 0.5 м. Задачей будущих исследований является проверка данных, полученных на холодных моделях в условиях реальных температур и сред с повышенным содержанием СО2. Другой важной задачей становится уточнение разработанных рекомендаций в условиях повышенного давления газа (2–3 МПа), характерного для установок извлечения водорода.
Сепарация частиц
Для сепарации частиц после реакторов (котлов с ЦКС) обычно используют вертикальные циклоны. Именно КПД улавливания в циклоне напрямую определяет кратность циркуляции и расход циркулирующих частиц и их характерный размер. При высоком КПД уловителей (99.5%) повышение его всего на 0.1% приводит к увеличению циркуляции в 1.2 раза. При высоком фракционном КПД происходят существенное уменьшение размера циркулирующих мелких частиц, увеличение их расхода и концентрации в реакторе, а также кондуктивной составляющей теплообмена в котлах с ЦКС.
Данные многочисленных исследований, выполненных в последнее время в Китае, были учтены при создании собственной конструкции высокоэффективных сепараторов и котлов с ЦКС. Специальная форма входного патрубка и оптимальный диаметр выхлопного патрубка (4.4 м) обеспечивают повышенную эффективность улавливания частиц диаметром всего 0.023 мм. В топках с ЦКС средний размер частиц, поступающих в циклон, составляет 0.1–0.3 мм, а запыленность потока достигает 10 кг/м3. Для реакторов химических циклов запыленность еще выше. При этом полидисперсность невелика, так как она во многом определяется собственно возможностями уловителя.
При низких массовых расходах частиц образуются отдельные тонкие потоки, движущиеся вдоль стенок циклона по спирали вниз. При высоких концентрациях вся поверхность циклона покрывается сливающимися струями [21]. Модель механизма сепарации [22] составляется из двух частей. Вначале происходит классическая сепарация на входе в циклон до достижения определенной массовой загрузки потока сливающихся струй. При больших загрузках работает механизм струйного потока. При этом неуловленные частицы направляются в выхлопной патрубок. Оба механизма описываются полуэмпирическими зависимостями.
В экспериментальных данных [23] при фиксированном времени пребывания частиц наблюдается некоторое влияние критерия Рейнольдса Re в области небольших запыленностей. Предельные массовые концентрации частиц, полученные в разных исследованиях, существенно различаются – от 0.005 до 0.050 кг/кг. В [24] для этого показателя даны сложные зависимости. Согласно результатам расчетов, представленным в [25], увеличение среднего размера частиц приводит к росту концентрации. С увеличением размера циклона и повышением температуры возрастает предельная загрузка твердых частиц.
Экспериментальные данные авторов, полученные на установке со связанными между собой реакторами с циклоном повышенной эффективности диаметром 0.3 м [26], также четко показали влияние массовой концентрации частиц на эффективность улавливания. Эффективность улавливания в циклоне оказалась очень высокой (более 99.99%), что обусловлено довольно большими размерами частиц и их высокой концентрацией. Поэтому анализировать влияние факторов на полный КПД циклона η лучше с помощью уноса. На рис. 5 показана зависимость относительного уноса частиц (1 – η) от их массовой концентрации μ. Такой подход, по мнению авторов, лучше подхода с использованием массовой загрузки как отношения расхода частиц к расходу газа. Он характерен для двухфазных потоков пар – вода: при μ = 0 поток состоит из газа, при μ = 1 – из твердой фазы (см. рис. 5).
Существует множество моделей для расчета общего КПД циклона и фракционной эффективности улавливания. Одна из них – трехзонная модель, в которой рассматриваются зоны входа, опускного и подъемного потоков [26]. Турбулентное смешение определяется по профилю радиальных концентраций в каждой зоне с учетом обмена частиц. В анализ включаются реальное строение циклона, учитывается обмен частицами между зонами опускного и подъемного потоков и распределение времени релаксации. В зонах входа и опускного потока газ и частицы движутся вниз, а в зоне подъемного потока вектор скорости газа направлен преимущественно вверх. Система уравнений для каждой зоны при соответствующих допущениях и преобразованиях, выполненных авторами, приводит к комплексу формул для расчета фракционного КПД и эмпирической его зависимости от диаметра частиц [27].
Расчетные значения по представленным формулам неплохо соответствуют экспериментальным данным. Следует отметить, что зависимость фракционного КПД от диаметра частиц выведена благодаря обработке многих отечественных и зарубежных данных, полученных в том числе при исследованиях процессов в циклонах с высокой концентрацией частиц и циклонах большого диаметра. По-видимому, она в какой-то мере учитывает и запыленность потока.
При традиционном методе определения общей эффективности улавливания используется вероятностная модель. Общая эффективность улавливания очень велика и зависит как от времени релаксации, так и от диапазона концентрации относительно крупных частиц. Сравнение расчетных и экспериментальных данных по общей эффективности улавливания показало, что расчетные значения показателей всегда ниже опытных. Эта разница становится заметной при концентрации частиц более 0.5 кг/кг, составляя при этом всего 0.004–0.005%. Таким образом, можно сделать вывод, что для циклонов с очень высокой эффективностью массовая концентрация на входе в них находится в пределах возможных ошибок как расчетов, так и экспериментов.
Известно, что сопротивление циклона уменьшается с ростом массовой концентрации потока на входе в него. Это связано со снижением крутки потока и перераспределением кинетических энергий газа и твердой фазы [28]. Данные авторов по поправке на запыленность потока показали, что ее значение находится в диапазоне 0.4–0.6 и увеличивается с ростом массовой концетрации до 0.8. Влияние доли легкой фракции (песка) не обнаружено.
Для расчета поправки на запыленность существуют несколько зависимостей. Наиболее представительная из них предложена в [29], она дает значение поправки, равное 1 при чистом потоке газа. При этом достигается минимум поправки при массовых концентрациях около 0.3 кг/кг и дальнейший рост ее значения с увеличением концентрации. В [30] анализируются некоторые зависимости для расчета поправки на запыленность. Экспериментальные данные [30] показали отсутствие влияния на нее скорости газов и размеров частиц. На рис. 6 приведены данные авторов настоящей статьи и [30]. Они обобщаются единой зависимостью [31]
где $\psi $ – поправка на запыленность; μ – массовая концентрация твердых частиц.Рис. 6.
Зависмость поправки на запыленность потока от массовой концентрации частиц. U, м/с: 1 – 3.06–3.10; 2 – 3.55–3.80; 3 – 4.29–4.42; 4 ‒ 4.7; 5 – данные [30] (диаметр частиц 0.080–0.111 мм); 6 – данные [30] (диаметр частиц 0.111–0.50 мм); 7 – результаты расчета по формуле (3)
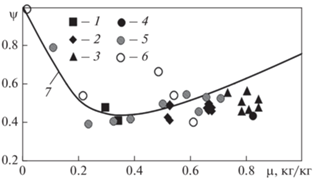
Перетоки между реакторами и баланс давлений в системе
В системах со связанными между собой реакторами большое значение имеет организация перетоков между ними. В этом плане важен опыт исследований движения частиц в опускных стояках и пневмозатворах [32–36]. Для расчета и конструирования новых систем со связанными между собой реакторами с ЦКС и КС крайне важным является расчет контура циркуляции частиц: реактор с ЦКС – циклон – переток в реактор с кипящим слоем – реактор с кипящим слоем – возврат материала в реактор с ЦКС. Расчет заключается в определении расхода материала в системе, перепадов давлений в реакторах и системе возврата уловленных частиц, сопротивления циклонов и уровня слоя в стояках под циклонами в зависимости от скоростей газов в реакторах и подаче газа в пневматические клапаны. При этом необходимо учитывать материальный баланс в элементах системы при примерно постоянной массе материала в контуре циркуляции, особенности гидродинамики элементов системы (подъемное движение в турбулентном слое и разбавленной фазе в реакторе с ЦКС, опускное движение в плотном и переходном к ожиженному режимах движения в стояках и перетоках и движение в режиме пузырькового слоя в реакторе с КС) и режимы работы пневматических затворов.
Пневматические клапаны работают по принципу пссевдоожиженных затворов, причем запирающую функцию затворов выполняет подъемный участок с наклонной течкой возврата в топку (петлевой затвор или J-клапан) либо горизонтальный участок, соединяющий сток с топкой (L-клапан). Опускное движение в стояке может происходить в режиме движущегося вниз плотного слоя или в переходном режиме. При большом проскоке ожижающего агента (газ, пар, воздух) в стояк возможен и режим с пузырьковым ожижением, который может приводить к проскоку воздуха в циклон. Границы режимов зависят от скорости скольжения Us (здесь s – от sliding) – суммы скоростей материала и газа с разными знаками направления движения. Если скорость скольжения положительна (положительное направление – вниз), то движение происходит в плотном слое, если отрицательна – то в переходном режиме, а при большом значении этой скорости – в режиме пузырькового слоя. Определить скорость скольжения довольно трудно, если не знать долю воздуха, поступающего в стояк (стояк L-клапана в том числе), от общего расхода воздуха, поданного в нижнюю часть стояка. Известно, что значительная часть воздуха уходит с потоком материала в подъемную часть затвора или в горизонтальную часть L-клапана [32, 34]. Согласно этим данным, 94–100% газа направляется в систему рециркуляции.
Долю воздуха, поступающего в стояк, можно определить методом газовых меток [34, 35], а также по перепаду давлений в опускном стояке и подъемной части затвора с учетом газа, попадающего вместе с потоком частиц. Далее рассчитывается относительная скорость скольжения Us/Um.f (здесь Um.f – скорость минимального псевдоожижения, m.f – от minimum fluidization). На рис. 7 показана зависимость относительной скорости скольжения от относительной скорости воздуха U/Um.f (здесь U – скорость воздуха), поступающего в стояк (частицы со средним диаметром 0.8 мм, истинной плотностью 1420 кг/м3 при Um.f = 0.175 м/с) по данным [36].
Рис. 7.
Зависимость относительной скорости скольжения от относительной скорости воздуха, поступающего в стояк [36]
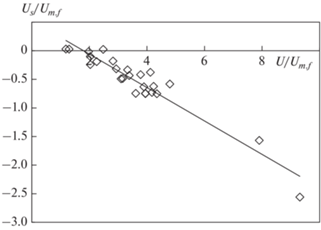
Эти данные свидетельствуют о границе между течением в плотном слое и переходным режимом при скоростях псевдоожижения в стояке в диапазоне двух – пяти скоростей минимального псевдоожижения. Результаты хорошо согласуются с данными по зависимости относительной высоты слоя в стояке от скорости ожижения. Обнаружено значительное влияние уровня слоя в стояке на долю воздуха, поступающего в стояк петлевого затвора. При низком уровне слоя довольно большая часть приточного воздуха поднимается в стояк. Число псевдоожижения, равное 4, имеет решающее значение для работы клапанов. При этом происходит смена режимов течения: при малых скоростях – нисходящий режим, а при больших скоростях пузырьки воздуха движутся вверх противотоком псевдоожиженным частицам.
В ОАО ВТИ были выполнены экспериментальные исследования гидродинамики связанных между собой реакторов и разработаны методы расчета таких систем [18, 37]. Для расчета контура циркуляции частиц существенным является установление связи между расходом циркулирующего материала, полученным при расчете реактора с ЦКС по характеристикам материала и газа при определенном перепаде давлений в реакторе (массе слоя в реакторе с ЦКС), и аэрацией в затворе и уровнем слоя в стояке затвора. При этом соблюдается материальный баланс, изменение уровня слоя в стояке приводит к изменению массы слоя в реакторе с ЦКС, а сумма масс материала в реакторе и системе возврата (главным образом в стояке) остается постоянной.
Экспериментальная установка подробно описана в работах ОАО ВТИ. Связь между циклоном реактора с ЦКС и реактором с КС осуществляется с использованием L-клапана, а возврат частиц из реактора с КС в реактор с ЦКС – через петлевой затвор. Наибольшие давления в системе относятся к точке ввода воздуха в L-клапан и точке подвода воздуха в него. С ростом массы слоя в реакторе с ЦКС давление в L-клапане снижается, а в петлевом затворе увеличивается. Оказалось, что сумма давлений в этих точках (около 23 кПа) практически не меняется во всех режимах и, по-видимому, характеризует работу всего контура со связанными между собой реакторами при постоянных массе и физических показателях материала и газа.
Многие вопросы работы перетоков между реакторами пока еще недостаточно изучены. Важным является исследование предельных режимов, ограничивающих расход частиц, а также исследование влияния характеристик газовой среды (например, при повышенном давлении) на скорость скольжения и границы переходов от движения в плотном слое к псевдоожиженному движению в опускных стояках и затворах.
Теплообмен
Как для котлов с ЦКС, так и для систем со связанными между собой реакторами теплообмен к настенным экранам и погруженным в слой поверхностям нагрева зависит от плотности (концентрации материала) потока. При этом теплообмен к поверхностям нагрева в слое является, в основном, конвективно-кондуктивным, т.е. зависит от плотности слоя, скорости псевдоожижения, размеров частиц, теплофизических характеристик газа, расположения и конструкции поверхности нагрева [38]. В этой зоне настенные экраны (ограждение реакторов) могут быть футерованы и их вклад в тепловой баланс топки незначителен. В переходной зоне и особенно в надслоевом пространстве теплообмен происходит главным образом излучением.
Технология ЦКС, характеризующаяся постоянством температуры по высоте топки при номинальной и частичной нагрузках, предусматривает возможность регулирования отвода тепла в топке благодаря изменению конвективно-кондуктивной составляющей теплообмена. С учетом того что котлы с ЦКС работают в узком диапазоне скоростей газов (4.0–5.5 м/с) и температур в топке (800–900°С), очень важным фактором являются размеры частиц в слое. В [39] предложены новые подходы к проектированию котлов с ЦКС, основанные на умеренной массе материала в слое с преобладающим количеством относительно мелких частиц размером около 0.2 мм. Предполагается, что при максимальном количестве частиц размером 0.1–0.4 мм возможен переход от турбулентного режима в режим быстрого слоя. Это достигается благодаря соответствующему составу подаваемого материала (топливо и известняк) и повышению эффективности улавливания мелких частиц. Такие подходы уже реализованы на многих котлах и позволили заметно сократить затраты электроэнергии на собственные нужды, улучшить связывание серы, снизить выбросы оксидов азота и уменьшить износ поверхностей нагрева [40].
Наибольший интерес представляют исследования конвективно-кондуктивной составляющей теплообмена. По результатам большинства исследований, проведенных в том числе и на крупных промышленных объектах, предлагаются простые эмпирические зависимости от средней плотности потока в реакторе [37, 41]. Такие зависимости пригодны для узких диапазонов температур, размеров частиц и скорости газов, характерных для котлов с ЦКС. При этом главным фактором является средняя концентрация частиц.
Для переноса данных с различных установок требуется обобщающий подход с использованием теоретических моделей. Одной из них может стать пакетная модель, в которой также применяются эмпирические коэффициенты [42]. В [43, 44] предложен критериальный подход к расчету кондуктивно-конвективной составляющей теплообмена. В качестве одной из наиболее представительных теоретических моделей целесообразно рассмотреть газокинетическую модель, предложенную Мартином [45] и доработанную впоследствии Шлундером [45]. Эта модель основана на аналогии с кинетической теорией газов для описания механизма переноса энергии движущимися частицами. Теплообмен зависит от физических свойств газа (теплопроводности) и частиц (теплоемкости). Используется аналитическое выражение для максимального коэффициента теплоотдачи между прямой стенкой и жесткой сферической частицей, находящейся в точке контакта в течение короткого промежутка времени.
В ОАО ВТИ на базе теоретической модели Мартина были разработаны расчетные зависимости для определения кондуктивной составляющей теплообмена [46]. Особенностями предложенных зависимостей являются учет профиля концентраций по ширине топки и использование расчетной пристенной концентрации в качестве определяющей для кондуктивной составляющей теплообмена. Экспериментально было подтверждено положение о зависимости кондуктивно-конвективной составляющей теплообмена от объемной концентрации в пристенной зоне, что позволяет обобщить данные, полученные на различных установках с использованием частиц, различающихся по диаметру и плотности. Однако и этот комплекс зависимостей не учитывает того, что при использовании твердых топлив в реакторе с ЦКС присутствуют как оксиды металлов, так и частицы золы. Такие исследования представляют значительный научный и практический интерес.
Теплообмен излучением рассчитывается по хорошо известной зависимости Стефана – Больцмана. Трудность расчета заключается в оценке приведенной степени излучательной способности, которую считают равной 0.7–0.8. При сравнении теплофизических свойств газов (азота, СО2 и паров воды) установлено, что, несмотря на близкие значения их теплопроводности и изобарной массовой теплоемкости, вследствие больших различий в плотности азота и паров воды значения их температуропроводности в присутствии CO2 существенно ниже. При повышенном содержании СО2 в потоке газов увеличивается теплоемкость по сравнению с условиями сжигания топлив в среде кислорода и азота, изменяются также и оптические свойства газов. Это может приводить к заметной интенсификации лучистого теплообмена на всем протяжении газового тракта вследствие увеличения концентрации трехатомных газов. Качественно эти результаты вполне объяснимы. Однако их количественное выражение с использованием традиционных зависимостей может оказаться не совсем корректным. Поэтому исследование лучистой составляющей теплообмена в отличной от традиционной при сжигании топлив газовой среде представляет значительный интерес.
ВЫВОДЫ
1. Технология сжигания и газификации топлив в химических циклах активно развивается в последнее время, так как позволяет с относительно низкими затратами улавливать СО2. Подобная технология со связанными между собой реакторами с кипящим и циркулирующим кипящим слоем пригодна для систем с производством электроэнергии, тепла и полезных продуктов. Она может быть также экономически эффективной для производства водорода.
2. Особенности технологии химических циклов – необходимость повышенного расхода циркулирующего материала и, соответственно, высокой степени их улавливания, а также надежного перетока частиц между реакторами, использование частиц оксидов металлов с высокой плотностью, изменение состава газов по сравнению с традиционным сжиганием органических топлив в котлах с ЦКС.
3. Вопросы гидродинамики реакторов с повышенным расходом частиц и сепарации частиц хорошо изучены на холодных моделях, апробированы полуэмпирические расчетные модели. Задача будущих исследований – проверка этих данных в условиях реальных температур и сред с повышенным содержанием СО2. Другой важной задачей является уточнение разработанных рекомендаций в условиях повышенного давления газа, характерного для установок получения водорода (2–3 МПа).
4. Несмотря на значительный прогресс в области исследований перетоков (опускные стояки, пневмозатворы различных конструкций), многие вопросы, касающиеся перетоков между реакторами, пока еще недостаточно изучены. Важным является изучение предельных режимов, ограничивающих расход частиц, а также влияния характеристик газовой среды (например, при повышенном давлении) на скорость скольжения и границы переходов от движения в плотном слое к псевдоожиженному движению в опускных стояках и затворах.
5. Имеющиеся теоретические и полуэмпирические зависимости для расчета кондуктивной составляющей теплообмена требуют экспериментального подтверждения. Необходимо дополнить их теоретическими представлениями и опытными данными для учета присутствия в потоке частиц как оксидов металлов, так и золы с существенно различающимися свойствами. Изменение свойств газовой среды, особенно с повышенным содержанием СО2, может приводить к заметной интенсификации лучистого теплообмена на всем протяжении газового тракта вследствие увеличения концентрации трехатомных газов. Количественное выражение с использованием традиционных зависимостей может оказаться не совсем корректным. Поэтому исследование лучистой составляющей теплообмена в отличной от традиционной при сжигании топлив газовой среде представляет значительный интерес.
Список литературы
Energy technology perspectives 2020: Special report on carbon capture utilisation and storage. CCUS in clean energy transitions. Paris: International Energy Agency, 2020. https://webstore.iea.org/ccus-in-clean-energy-transitions
Technology roadmap 2021. Washington, CSLF, 2021. www.cslforum.org
A chemical engineering perspective on the challenges and opportunities of delivering carbon capture and storage at commercial scale. Rugby: IChemE, 2018. https://www.icheme.org/media/1401/CCUS-report-2018
Further assessment of emerging CO2 capture technologies for the power sector and their potential to reduce costs. Cheltenham: IEAGHG, 2019. https://ieaghg.org/ ccs-resources/blog/new-ieaghg-technical-report-2019-09-further-assessment-of-emerging-co2-capture-technologies-for-the-power-sector-andtheir-Potential-to-reduce-costs
Review of hydrogen production using chemical-looping technology / M. Luo, Y. Yia, S. Wang, Z. Wang, M. Du, J. Pan, Q. Wang // Renewable Sustainable Energy Rev. 2018. V. 81. P. 3186–3214. https://doi.org/10.1016/j.rser.2017.07.007
Feasibility of an integrated biomass-based CLC combustion and a renewable-energy-based methanol production systems / E. Mancusi, P. Bareschinoa, P. Brachi, A. Coppola, G. Ruoppolo, M. Urciuolo, F. Pepe // Renewable Energy. 2021. V. 179. P. 29–36.
Рябов Г.А. Химические циклы сжигания и газификации топлив. Обзор исследований и новых технологических решений // Теплоэнергетика. 2022. № 1. С. 32–50. https://doi.org/10.1134/S0040363621100064
Lyngfelt A., Johansson M., Mattisson T. Chemical looping combustion – Status of development // Proc. of the 9th Inern. Conf. on CFB. Germany, Hamburg, 13–16 May 2008. P. 39–53.
Markström P., Lyngfelt A., Linderholm C. Chemical looping combustion in a 100 KW unit for solid fuels // Proc. of the 21st Intern. Conf. on CFB. Italy, Naples, 4–6 June 2012. P. 285–292.
Рябов Г.А., Санкин Д.А., Фоломеев О.М. Сжигание и газификация толив в химических циклах – новое применение технологии циркулирующего кипящего слоя для улавливания СО2 // Изв. РАН. Энергетика. 2014. № 5. С. 27–36.
Adánez J. Chemical-looping combustion of coal: Recent developments and technology challenges // Proc. of 21st Intern. Conf. on CFB. Italy, Naples, 4–6 June 2012. P. 12–27.
Pfeifer C., Aiger I., Hofbauer H. Co-gasification of biomass and coal in a 8 MW dual fluidized bed steam gasifier // Proc. of the 10th Intern. Conf. on CFB and Fluidization Technology. Synriver, Oregon, USA, 1–5 May 2011. P. 1–9.
Рябов Г.А. Использование технологии химических циклов для производства водорода // Альтернативная энергетика и экология. 2021. № 4–6. С. 83–92.
Chemical looping gasification / L.-S. Fan, F. Li, L.G. Valazquer-Vargas, S. Ramkumar // Proc. of the 9th Intern. Conf. on CFB. Germany, Hamburg, 13–16 May 2008. P. 801–806.
Chiesaa P., Giovanni L., Alberto M. Three-reactors chemical looping process for hydrogen production // Int. J. Hydrogen Energy. 2008. V. 33. No. 9. P. 2233–2245.https://doi.org/10.1016/j.ijhydene.2008.02.032
Khan M.N., Shamim T. Techno-economic assessment of a plant based on a three reactor chemical looping reforming system // Int. J. Hydrogen Energy. 2016. V. 41. Is. 48. P. 22677–22688. https://doi.org/10.1016/j.ijhydene.2016.09.016
Ryu H.J., Jin G.T. Conceptual design of 50 kW thermal chemical-looping combustor and analysis of variables // Energy Eng. J. 2003. V. 12. No. 4. P. 289–301.
Результаты расчетных и экспериментальных исследований гидродинамики циркуляционных контуров в аппаратах с циркулирующим кипящим слоем и системах со связанными реакторами / Г.А. Рябов, О.М. Фоломеев, Д.А. Санкин, Д.А. Мельников // Теплоэнергетика. 2015. № 2. С. 33–40. https://doi.org/10.1134/S0040363615020083
Ryabov G., Folomeev O., Dolgushin I. The investigation of movement conditions of particles binary mixtures in chemical looping combustion of solid fuel // J. Phys.: Conf. Ser. 2017. № 891. P. 012101. https://doi.org/10.1088/1742-6596/891/1/012101
Рябов Г.А., Фоломеев О.М., Долгушин И.А. Исследование условий движения бинарных смесей частиц применительно к сжиганию топлив в химических циклах с улавливанием диоксида углерода // Теплоэнергетика. 2018. № 7. С. 26‒33. https://doi.org/10.1134/S0040363618070081
Hugi E., Reh L. Focus on solids strand formation improves separation performance of highly loaded circulating fluidized bed recycle cyclones // Chem. Eng. Process. 2000. No. 39. P. 263–273.
Muschelknautz E., Trefz M. Secondary flow and short circuit flow at the dust discharge end of cyclone separators // European Symposium: Separation of Particles from Gases. Nürnberg, 1989. P. 345–407.
Effect of operating variables on shape of “fish-hook” curves in cyclones / A. Majumder, H. Shah, P. Shukla, J. Barnwal // Miner. Eng. 2007. No. 20. P. 204–206.
Fassani F., Goldstein L. A study of the effect of high inlet solids loading on a cyclone separator pressure drop and collection efficiency // Powder Technol. 2000. No. 107. P. 60–65.
Redemann K., Hartge E.-U., Werther J. A particle population balancing model for a circulating fluidized bed combustion system // Powder Technol. 2009. No. 191. P. 78–90.
Leith D., Licht W. The collection efficiency of cyclone type particles collectors – a new theoretical approach // AIChe J. 1972. V. 68. No. 126. P. 196–206.
Рябов Г.А., Фоломеев О.М., Шапошник Д.А. Исследование систем улавливания и возврата на установках с циркулирующим кипящим слоем // Теплоэнергетика. 2002. № 8. С. 18–24.
Knowlton T. Cyclone systems in circulating fluidized beds // Proc. of the Intern. Conf. on CFB-12. Poland, Krakow, 24‒26 May 2017. P. 47‒64.
Долгов В.Н. Аэродинамика и теплообмен циклона – утилизатора теплоты запыленных газов: дис. … канд. техн. наук. Свердловск: УПИ, 1988.
Measurement of solid entrainment by pressure drop in the cyclone / A. Martínez, P. Lisbona, Y. Lara, L.M. Romeo, A. Gil // Proc. of the 21st Intern. Conf. on CFB. Italy, Naples, 3–6 June 2012. P. 666‒672.
Ryabov G.A., Folomeev O.M. The influence of particles flow rate on separation and pressure drop in cyclones and down flow behavior in recirculating systems // Int. J. Environ. Sci. 2021. V. 6. P. 477–485.
Knowlton T.M. Non-mechanical solid feed and recycle devices circulating fluidized beds // Proc. of the 3rd Intern. Conf. on CFB Technology. N.Y.: Pergamon Press, 1988. P. 120–132.
Subbarao D. Flow rate of solids in L-valves // Proc. of the 10th Intern. Conf. on CFB and Fluidization Technology. USA, Oregon, Synriver, 1–5 May 2011.
Gas tracer study in a non-mechanical L-valve / M. Yazdanpanah, A. Hoteit, A. Forret, T. Gauthier, A. Delebarre // Proc. of the 10th Inern. Conf. on CFB and Fluidization Technology. USA, Oregon, Synriver, 1–5 May 2011.
Investigation on the hydrodynamic properties in the external loop of circulating fluidized bed with loop seal / X. Yao, T. Wang, H. Yang, H. Zhang, Q. Liu // Proc. of the 10th Intern. Conf. on CFB and Fluidization Technology. USA, Oregon, Synriver, 1–5 May 2011.
Ryabov G.A., Folomeev O.M. Features of particle flows hydrodynamics in recirculating systems and pneumatic valves of CFB boilers // J. Phys.: Conf. Ser. 2020. V. 1683. No. 2. P. 2063. https://doi.org/10.1088/1742-6596/1683/2/022035
Pressure balance model for dual CFB–FB reactors systems / G.A. Ryabov, O.M. Folomeev, D.A. Sankin, D.A. Melnikov // Proc. of the 22nd Intern. Conf. on CFB. Finland, Turku, 12–14 June 2015. P. 843–852.
Breitholz C., Leckner B. Translation of heat transfer measurements from laboratory CFBs to the conditions of CFB boilers // Heat Mass Transfer. 2000. V. 6. P. 12–23.
Guangxi Y. The formation of the CFB design theory and its practice in China // Proc. of the 22nd Inern. Conf. on CFB. Finland, Turku, 14–17 June 2015. P. 12–22.
Breitholtz C. Wall average heat transfer in CFB boilers // Proc. of the 3rd European Conf. on Fluidization. France, Toulouse, 29–31 May 2000.
Subbarao D., Basu P. Heat transfer in circulating fluidized bed. Circulating fluidized beds technology. L.: Pergamon Press, 1986.
Теплицкий Ю.С. Кондуктивно-конвективный теплообмен в дисперсных системах со взвешенными частицами // Тепломассообмен. 2000. Т. 6. С. 125–130.
Bucak O., Dogan O.M., Uysal B.Z. Heat transfer in circulating fluidized bed combustor // Proc. of 15th Intern. Conf. on Fluidized Bed Combustion. USA, Savannah, 16–19 May 1999.
Teplitskiy Y.S., Ryabov G.A. Scaling in a circulating fluidized bed: particle concentration and heat transfer coefficient in a transport zone // Int. J. Heat Mass Transfer. 1999. V. 42. P. 4065–4075.
Schlunder U.E. Heat transfer to packed and stirred beds from surface of immersed bodies // Chem. Eng. Proc. 1984. V. 18. P. 31–35.
Фоломеев О.М., Трухачев С.Н., Рябов Г.А. Исследование гидродинамики и тепломассообмена применительно к условиям работы надслоевого пространства котлов с циркулирующим кипящим слоем // Теплоэнергетика. 2000. № 10. С. 27–32.
Дополнительные материалы отсутствуют.
Инструменты
Теплоэнергетика