Теплоэнергетика, 2023, № 4, стр. 55-64
Исследование свойств золы лузги подсолнечника после ее обработки различными методами торрефикации
А. В. Небываев a, *, О. Ю. Милованов a, Д. В. Климов a, С. Н. Кузьмин a, А. В. Рыженков a, В. А. Дубина b, Р. В. Завиженец b
a Национальный исследовательский университет “Московский энергетический институт”
111250 Москва, Красноказарменная ул., д. 14, Россия
b ОАО “Головное специализированное конструкторское бюро по комплекту оборудования для микроклимата”
224014 г. Брест, ул. Писателя Смирнова, д. 66, Республика Беларусь
* E-mail: ar.nebivaev2017@yandex.ru
Поступила в редакцию 28.07.2022
После доработки 12.10.2022
Принята к публикации 25.11.2022
Аннотация
Отходы растениеводства (солома, лузга подсолнечника, риса, проса и других зерновых культур) обладают низкой влажностью, малой зольностью, а их теплота сгорания близка к теплоте сгорания многих энергетических углей или превосходит ее. Энергетическая утилизация таких отходов могла бы решить экологические проблемы, связанные с сокращением выбросов парниковых газов. В то же время химический состав золы этих отходов обусловливает низкую температуру ее плавления, что приводит к шлакованию топки и быстрому росту отложений золы на конвективных поверхностях нагрева котла. Известные методы предварительной обработки отходов перед сжиганием (водная промывка, гидротермальная карбонизация) энергозатратны и малопроизводительны. Поэтому предложено оценить влияние такого метода переработки, как торрефикация, на плавкостные свойства золы. Использованы два метода торрефикации биомассы: в среде газообразных продуктов торрефикации в тарельчатом реакторе с механически перемешиваемым слоем биомассы и в кипящем слое в среде перегретого водяного пара. Исследован химический состав золы биоуглей, полученных обоими методами. На основании известных данных рассчитаны прогностические критерии, позволяющие оценить возможность расплавления золы биоуглей, образования шлаковых агломератов, отложения золы на конвективных поверхностях нагрева котлов, а также формирования агломератов при сжигании лузги подсолнечника в кипящем слое. Поскольку использование прогностических критериев во многих случаях приводит к противоречивым результатам, для оценки плавкостных свойств золы биоуглей и сходной с ними биомассы применена трехмерная диаграмма, на оси которой нанесены концентрации различных оксидов, содержащихся в золе. Диаграмма позволяет сопоставлять плавкостные свойства полученных биоуглей с плавкостными свойствами других видов биомассы. Это дает возможность сделать вывод, что биоуголь, произведенный в результате торрефикации в среде перегретого водяного пара, близок по своим топливным характеристикам к древесным отходам, т.е. может сжигаться отдельно без добавок или смесей с другими видами топлива, обладающими тугоплавкой золой.
Подсолнечник (Helianthus annuus) – травянистая культура семейства сложноцветных, широко культивируемая из-за относительно короткого цикла роста, высокой устойчивости к засухе и адаптированности к разным почвенным условиям. На рис. 1 показано распределение производства подсолнечника в мире [1].
Лузга составляет 45–60% массы семян подсолнечника в зависимости от его сорта [1]. Ее отделяют от ядра для улучшения прессования семян и увеличения выхода подсолнечного масла. Лузга – побочный продукт производства подсолнечного масла. Ее широко применяют при изготовлении кормов для животных, но для выработки энергии использование лузги ограничено [2], несмотря на то что она имеет относительно высокую теплоту сгорания.
Большое содержание энергии в этом побочном продукте делает его привлекательным в качестве топлива для получения тепловой и электрической энергии. Однако относительно высокое содержание в лузге щелочных элементов является причиной образования при ее сжигании агломератов золы и топлива, отложений золы на конвективных поверхностях нагрева котлов и их коррозии [3]. Эти процессы обусловлены неорганическим составом биотоплива, а также конструкцией котла и условиями его эксплуатации (изменением температуры газов по мере их движения по котлу) [3]. В большей мере на процесс загрязнения котла [3] влияют прежде всего щелочные (калий, натрий) и щелочно-земельные металлы (кальций, магний), а также кремний, сера, алюминий, фосфор и хлор, присутствующие в значительных количествах в биомассе.
Предварительная промывка биомассы горячей водой считается перспективным методом улучшения ее топливных характеристик, не требующим использования химических добавок [4, 5]. Этот процесс осуществляется при температуре воды, нагретой до 240°С при давлении около 3 МПа, а его продолжительность достигает 1 ч [5]. При такой обработке образцов древесины тополя, стеблей мискантуса и кукурузы, лузги проса удалось увеличить теплоту сгорания биотоплива не более чем на 12% [5]. В работе [6] отмечается, что в результате водной промывки биомассы в течение 1 ч при 80°С в золе значительно снижается содержание химических элементов, вызывающих проблемы при сжигании биотоплива: калия на 93%, натрия на 96%, фосфора на 85% и хлора на 97%. Недостаток промывки – необходимость использовать реакторы, работающие под высоким давлением, а также проводить последующую сушку биомассы. При этом теплота сгорания биотоплива повышается только на 2–12%.
Торрефикация биомассы после водной промывки представляется перспективной технологией по устранению таких проблемных элементов, как хлориды щелочных металлов и сернистые соединения. После такой комбинированной обработки уменьшилось количество шлака при сжигании соломы озимой пшеницы, который образуется после газификации этой биомассы при температуре 950°С [7]. Однако предварительная обработка биомассы усложняет и удорожает процесс получения качественного топлива, сопоставимого по своим характеристикам с ископаемым топливом.
В качестве газовой среды, в которой осуществляется торрефикация, может применяться перегретый водяной пар [8‒10]. В таком варианте предварительной обработки биомассы, вероятно, можно было бы объединить водную промывку и торрефикацию, что значительно упростило бы процесс. К тому же торрефикация протекает при давлении пара близком к атмосферному, что удешевляет конструкцию реактора для предварительной термической обработки биомассы.
Цель настоящей работы – исследование свойств золы лузги подсолнечника, подвергнутой торрефикации в кипящем слое в среде перегретого водяного пара. Проведено сравнение результатов такой обработки с результатами исследования свойств золы лузги подсолнечника, прошедшей торрефикацию в среде ее газообразных продуктов.
МАТЕРИАЛЫ, ЭКСПЕРИМЕНТАЛЬНЫЕ УСТАНОВКИ И МЕТОДИКА ЭКСПЕРИМЕНТА
Для анализа состава золы использовались следующие оборудование и приборы: низкотемпературная лабораторная печь SNOL 67/350, электропечь сопротивления камерная лабораторная SNOL 10/11–В, анализатор углерода, водорода, азота и серы TruSpec, калориметр бомбовый АКБ-1.
Содержание влаги, золы, углерода, водорода, азота, серы, теплоту сгорания лузги и полученного из нее биоугля, химический состав золы и содержание в ней микроэлементов определяли по ГОСТ [11–18]. Количество микроэлементов в золе устанавливали атомно-абсорбционным способом.
Содержание кислорода вычисляли как разницу между 100% и процентным содержанием в биомассе золы, влаги, серы, углерода, водорода и азота. Выход прокаленной массы лузги (при температуре 1000°С) составил 20%, причем выход карбонатов – 8.7%.
Схема реактора для торрефикации биомассы в среде газообразных продуктов торрефикации представлена на рис. 2. Реактор работает следующим образом. Высокотемпературный теплоноситель (термомасло ТЛВ-330), нагретый в специальном котле до 300°С, подается в рубашку реактора. После достижения температуры внутри реактора выше 220°С в него загружается порция исходной биомассы. Благодаря работе мешалки, установленной на валу, биомасса перемещается по лоткам 4 и 5. При этом происходит торрефикация биомассы в среде газообразных продуктов торрефикации, генерирующихся из биомассы при ее нагреве высокотемпературным теплоносителем. Торрефицированная биомасса выгружается из реактора через узел 3. В среде газообразных продуктов торрефикации процесс осуществляется при температуре до 250°С. Его продолжительность составляет 45 мин.
Рис. 2.
Схема реактора для торрефикации лузги подсолнечника в среде газообразных продуктов торрефикации. 1 – корпус реактора для торрефикации; 2 – узел загрузки исходной биомассы; 3 – узел выгрузки торрефицированной биомассы; 4, 5 – лотки для торрефикации; 6 – лоток для охлаждения торрефицированной биомассы; 7 – форсунка для подачи охлаждающей воды; 8 – мешалка; 9 – вал мешалки с электроприводом; 10 – трубопровод для удаления газообразных продуктов торрефикации
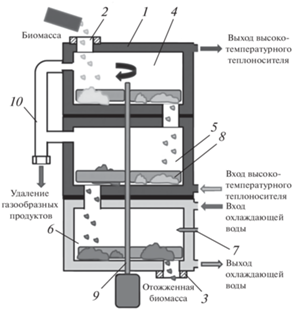
Установка для торрефикации лузги подсолнечника в кипящем слое в среде перегретого водяного пара (рис. 3) состоит из реактора для торрефикации в кипящем слое, бункеров для исходной биомассы и биоугля, циклона для отделения парогазового потока от частиц биоугля, выносимых из реактора и конденсатора парогазовой смеси (котел для генерации пара и пароперегреватель на рисунке не показаны).
Рис. 3.
Схема установки для торрефикации лузги подсолнечника в кипящем слое в среде перегретого водяного пара. 1 – реактор для торрефикации в кипящем слое; 2 – бункер для исходной биомассы; 3 – бункер для биоугля; 4 – циклон; 5 – конденсатор парогазовой смеси; 6 – термопара; 7 – датчик давления
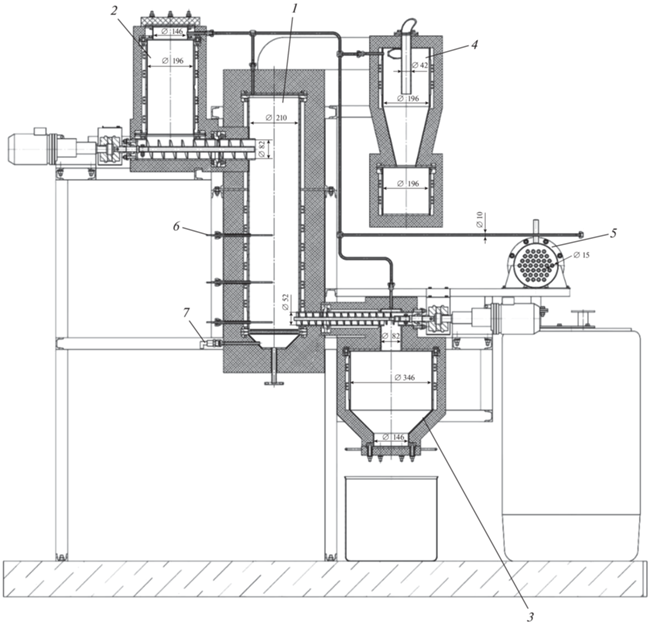
Перед началом эксперимента в реактор поместили примерно 6 дм3 биоугля из лузги подсолнечника, полученного в предыдущем эксперименте. Затем в бункер для исходной биомассы засыпали 2 кг сырья, подлежащего торрефикации, и включили подачу насыщенного водяного пара, который, проходя через пароперегреватель, направлялся под решетку. С началом загрузки исходной лузги подсолнечника с помощью газоанализатора Vario Plus Industrial Syngaz за конденсатором непрерывно осуществлялся отбор неконденсирующихся газов (диоксида и монооксида углерода, водорода и метана). После того как концентрация указанных веществ уменьшалась до первоначальных значений (до подачи биомассы в реактор), эксперимент прекращался и биоуголь выгружался в бункер. Затем вся установка продувалась холодным азотом и охлажденный биоуголь извлекался из бункера для анализа.
РЕЗУЛЬТАТЫ И ИХ ОБСУЖДЕНИЕ
В табл. 1 представлены результаты анализа исходной лузги и биоугля, полученного при торрефикации лузги подсолнечника в кипящем слое в среде перегретого водяного пара, а также биоугля, произведенного при торрефикации в среде ее газообразных продуктов.
Из данных, приведенных в табл. 1, следует, что оба примененных при исследовании метода торрефикации позволяют снизить влажность биоугля в 2.0–2.5 раза по сравнению с исходной биомассой, однако при этом его зольность увеличивается в 3.6–6.3 раза. Содержание серы, водорода и азота в биоугле остается близким к содержанию этих компонентов в исходной биомассе. Содержание углерода в биоугле возрастает в 1.13–1.24 раза относительно исходной биомассы, а кислорода – сокращается в 2 раза при торрефикации в среде перегретого водяного пара и только в 1.1 раза при торрефикации в среде ее газообразных продуктов. При резком сокращении содержания кислорода в биоугле, произведенном в процессе торрефикации в среде перегретого водяного пара, выход летучих оказывается в 1.76 раза ниже, чем в исходной лузге, а теплота сгорания биоугля возрастает на 23%. Биоуголь, полученный при торрефикации в среде ее газообразных продуктов, содержит примерно такое же количество летучих веществ, что и исходная лузга. Теплота сгорания такого биоугля только на 13% превышает теплоту сгорания исходной лузги.
Таблица 1.
Характеристики исходной лузги подсолнечника и биоуглей, полученных при торрефикации на перегретом паре и в тарельчатом реакторе
Показатель | Лузга | Биоуголь, полученный | |
---|---|---|---|
на перегретом паре | в тарельчатом реакторе | ||
Влажность, % | 8.24 | 4.06 | 3.26 |
Зольность, % | 2.06 | 12.97 | 3.59 |
Содержание, %: | |||
серы общей | 0.02 | Менее 0.01 | 0.01 |
углерода | 48.20 | 59.90 | 54.50 |
водорода | 5.71 | 4.39 | 5.91 |
азота | 0.70 | 1.32 | 0.71 |
кислорода | 35.07 | 17.35 | 32.02 |
Выход летучих веществ, % | 70.48 | 40.07 | 68.13 |
Низшая теплота сгорания, МДж/кг | 17.88 | 22.06 | 20.52 |
Таким образом, процесс торрефикации в среде перегретого водяного пара идет интенсивнее, чем в среде газообразных продуктов торрефикации, как из-за более высокой температуры процесса, так и из-за наличия водяного пара [19].
Химический состав исходной золы и полученных из нее биоуглей представлен в табл. 2. Данные таблицы свидетельствуют о том, что в результате обработки лузги двумя методами торрефикации в золе увеличивается содержание кислых соединений: SiO2, Al2O3, Fe2O3 и TiO2 – вследствие того, что из биомассы удаляется влага и относительная доля этих соединений возрастает. При разложении биомассы в перегретом водяном паре, как и в водной среде, происходит образование кислот, снижающих рН среды, в которой обрабатывается биомасса, что и приводит к уменьшению содержания в золе биомассы таких компонентов, как MgO, K2O, Na2O [20].
Таблица 2.
Содержание химических веществ, %, в золе исходной лузги и биоуглей, полученных при торрефикации на перегретом паре и в тарельчатом реакторе
Вещество | Зола | ||
---|---|---|---|
лузги | биоугля, полученного | ||
на перегретом паре | в тарельчатом реакторе | ||
SiO2 | 1.24 | 8.60 | 2.91 |
TiO2 | 0.02 | 0.07 | 0.17 |
Al2O3 | 0.36 | 0.84 | 0.69 |
Fe2O3 | 0.43 | 1.04 | 7.16 |
СаО | 6.39 | 19.93 | 6.36 |
MgO | 12.05 | 7.62 | 10.79 |
K2O | 38.99 | 18.14 | 34.05 |
Na2O | 0.93 | 0.75 | 0.63 |
P2O5 | 11.72 | 13.93 | 9.24 |
SO3 | 6.10 | 3.75 | 6.25 |
Cl | 1.77 | 0.93 | 1.75 |
Газовая среда, образующаяся в тарельчатом реакторе, также имеет пары воды, что подтверждается снижением влажности получаемого биоугля в сравнении с исходной лузгой. Но их содержание при этом намного ниже, чем при обработке лузги в среде перегретого водяного пара. Поэтому в золе биоугля, произведенного при торрефикации в тарельчатом реакторе, содержится незначительное количество MgO и К2О по сравнению с золой исходной лузги.
По этой же причине торрефикация в среде перегретого водяного пара приводит к почти двукратному сокращению содержания хлора в золе, тогда как после торрефикации в среде ее газообразных продуктов изменение содержания хлора практически не происходит.
Очевидно, что наличие паров воды в газовой фазе и образование кислой среды приводят к снижению концентрации некоторых микроэлементов в золе биоуглей в сравнении с золой исходной лузги (меди, никеля, хрома, свинца). Концентрация же других микроэлементов, которые не подвергаются воздействию кислот, увеличивается (табл. 3).
Таблица 3.
Содержание микроэлементов, мг/кг, в золе исходной лузги и биоуглей
Микроэлемент | Зола | ||
---|---|---|---|
лузги | биоугля, полученного | ||
на перегретом паре | в тарельчатом реакторе | ||
Ванадий | Менее 10 | 13 | Менее 10 |
Марганец | 333 | 635 | 751 |
Медь | 425 | 327 | 502 |
Никель | 102 | 42 | 112 |
Стронций | 180 | 425 | 196 |
Хром | 567 | 59 | 377 |
Цинк | 149 | 573 | 485 |
Свинец | 43 | 21 | 52 |
Мышьяк | Менее 10 | Менее 10 | Менее 10 |
При сжигании биоугля, полученного из лузги подсолнечника в результате торрефикации в среде перегретого водяного пара, можно ожидать меньших, в сравнении со сжиганием исходной лузги, выбросов соединений никеля, меди, хрома и свинца, но бо́льших выбросов соединений марганца, стронция, цинка. При сжигании биоугля, произведенного при торрефикации лузги подсолнечника в тарельчатом реакторе в среде газообразных продуктов торрефикации, выбросы хрома, в сравнении с исходной лузгой, будут предположительно меньше, а выбросы соединений марганца, меди, цинка и свинца, скорее всего, увеличатся.
Далее следует обсудить возможность возникновения проблем при сжигании торрефицированной лузги подсолнечника, связанных со шлакованием топки и образованием отложений на конвективных поверхностях нагрева или агломератов при сжигании этих биоуглей в топках с кипящим слоем.
Появление шлаковых агломератов зависит от многих факторов (в том числе, как упоминалось ранее, от химического состава золы биотоплива). Например, при сжигании биотоплива в кипящем слое на процесс образования агломератов влияют химический состав инертного материала, температура слоя, фракционный состав биотоплива, соотношение между воздухом, подаваемым в кипящий слой, и общим расходом воздуха, требуемого для поддержания процесса горения, и т.п. [21].
Для оценки склонности топлива к шлакованию поверхностей нагрева было разработано несколько критериев [6, 22], в том числе соотношение основных и кислотных соединений (B/A) [22]:
(1)
$\frac{B}{A} = \frac{{F{{e}_{2}}{{O}_{3}} + CaO + MgO + N{{a}_{2}}O + {{K}_{2}}O}}{{Si{{O}_{2}} + A{{l}_{2}}{{O}_{3}} + T{{i}_{2}}O}},$Было показано, что кислотные соединения повышают общую температуру плавления, в то время как основные соединения дают противоположный эффект. Считается, что зола имеет малую склонность к шлакованию при B/A < 0.5, среднюю при 0.5 < B/A < 1.0, высокую при 1.00 < B/A < < 1.75 и очень высокую при B/A > 1.75 [23].
Критерий агломерации BAI при сжигании биомассы в кипящем слое рассчитывался, как в работе [6]:
Согласно [6], в кипящем слое наблюдается агломерация, если BAI принимает значения меньше 0.15.
Критерий загрязнения Fu был предложен в [24] для оценки опасности загрязнения конвективных поверхностей нагрева котлов при сжигании биотоплива. Он рассчитывается по формуле
Низкая склонность к росту отложений золы ожидается при Fu < 0.6, высокая ‒ при 0.6 < Fu < < 40.0 и очень высокая – при Fu > 40.
При расчете по формуле (1) установлено: для исходной лузги B/A = 36.29, для биоугля, полученного при торрефикации в тарельчатом реакторе в среде газообразных продуктов торрефикации, B/A = 15.65, для биоугля, произведенного в среде перегретого водяного пара в кипящем слое, B/A = 4.99. То есть торрефикация лузги подсолнечника, согласно проведенным расчетам, не исключает возможности шлакования при сжигании этого биотоплива, но, предположительно, уменьшает вероятность возникновения этого процесса в 2.31–7.27 раза.
При выполнении расчетов по формулам (2) и (3) были определены значения BAI и Fu (табл. 4).
Таблица 4.
Индексы (критерии) агломерации и загрязнения для биотолива трех видов
Биотопливо | BAI | Fu |
---|---|---|
Исходная лузга | 0.01 (происходит агломерация) | 1448.7 |
Биоуголь, полученный при торрефикации: | ||
в тарельчатом реакторе в среде ее газообразных продуктов | 0.206 (агломерация не наблюдается) | 542.65 |
в среде перегретого водяного пара в кипящем слое | 0.055 (происходит агломерация) | 94.31 |
Для всех трех образцов биотоплива характерна очень высокая вероятность появления отложений золы на конвективных поверхностях нагрева котла.
В работе [23] отмечается, что индексы, рассчитанные по формулам (1)–(3), иногда дают противоречивые предсказания. Например, по прогнозу, основанному на соотношении B/A для щепы хвойных пород, загрязнение поверхностей нагрева должно быть чрезвычайно высоким, тогда как по прогнозу для того же топлива, основанному на индексе Fu, загрязнение будет низким, что больше соответствует практике применения этого биотоплива. Все критерии [см. (1)–(3)], с одной стороны, указывают на большую склонность широко используемых видов топлива, таких как древесная щепа, к шлакованию и загрязнению поверхностей нагрева, но, с другой стороны, показывают, что топлива с низкой температурой плавления золы (например, гранулы из соломы) имеют малую склонность к шлакованию.
В [23] была предложена относительно надежная альтернатива прогностическим критериям – тройная диаграмма, представленная на рис. 4. Оксиды были разделены на три группы в соответствии с рекомендациями работ [25, 26]. Хлор и некоторые оксиды, такие как SO3 и TiO2, были исключены из числа исходных данных, выбраны были только самые распространенные оксиды, чтобы сократить время анализа. Два соединения CaO и MgO были сгруппированы вместе, поскольку они часто обнаруживаются в образцах с высокой температурой плавления и хорошо коррелируют с температурой плавления золы. Оксид SiO2 был сгруппирован с двумя другими металлическими соединениями – Al2O3 и Fe2O3, которые часто встречаются в образцах золы биомассы в небольших количествах. Наконец, два щелочных соединения K2O и Na2O были сгруппированы с P2O5, поскольку было установлено, что они являются наиболее распространенными оксидами в образцах золы с низкой температурой плавления.
Рис. 4.
Тройная диаграмма, построенная на основе данных [25, 26] (предложена в работе [23] для прогнозирования поведения золы биомассы). 1 – исходная лузга подсолнечника; 2, 3 – биоуголь, полученный из лузги подсолнечника в результате ее торрефикации в среде перегретого водяного пара и в тарельчатом реакторе в среде газообразных продуктов торрефикации соответственно; 4, 5 – зола промытой и исходной древесины цитрусовых [6]; 6 – зола мискантуса [20]; 7, 8, 9 – зола мискантуса, подвергнутого гидротермальной карбонизации при температуре 160, 180 и 200°С соответственно [20]
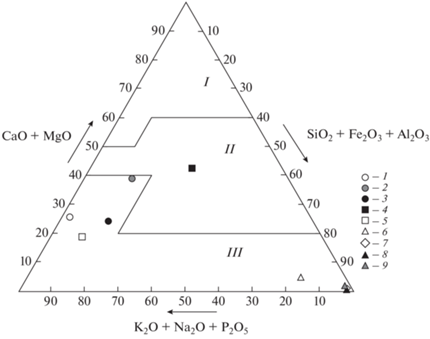
Диаграмма была разделена на три отдельные области. Образцы из области I имеют высокую температуру начала деформации золы и, следовательно, не должны вызывать проблем с загрязнением при сжигании биомассы. К этой области относится древесная биомасса (ель, сосна, тополь, ива) как в виде щепы, включая кору, так и в виде гранул. Область II – переходная между областями с высокой и низкой температурами начала деформации золы (загрязненная древесина, древесные отходы, бумага, осадок сточных вод, лузга риса и т.д.). В область III попадают сельскохозяйственные отходы (солома пшеницы, ржи, ячменя, овса, кукурузы), травы, жом сахарного тростника, шелуха и семена подсолнечника, куриный помет и навоз крупного рогатого скота. Биоотходы, относящиеся к последней области, имеют высокую склонность к зашлаковыванию и загрязнению поверхностей нагрева, и поэтому их нельзя использовать без добавок или совместного сжигания с топливом, менее склонным к образованию агломератов.
На диаграмму нанесены данные для золы исходной лузги подсолнечника и золы биоугля, полученного двумя методами торрефикации. Как можно видеть на рисунке, топливные характеристики биоугля, полученного в результате торрефикации в среде перегретого водяного пара, в отношении шлакования котла и загрязнения конвективных поверхностей нагрева приближаются к характеристикам древесных отходов.
На диаграмму нанесены также данные по золе промытой и непромытой древесины цитрусовых [6], по золе исходного мискантуса и мискантуса, подвергнутого гидротермальной карбонизации при температуре 160, 180 и 200°С [20].
Как видно на рис. 4, водная промывка, так же как и торрефикация в среде перегретого водяного пара, позволяет значительно улучшить топливные характеристики биомассы в отношении шлакования котла и загрязнения конвективных поверхностей нагрева.
Гидротермальная карбонизация не может значительно улучшить топливные характеристики биомассы и существенно снизить ее склонность к шлакованию котла и загрязнению конвективных поверхностей нагрева, несмотря на то что в результате такой обработки содержание соединений калия, например, в золе мискантуса снижается в 10 раз [20].
ВЫВОДЫ
1. Проведенные исследования показали, что торрефикация лузги подсолнечника в среде газообразных продуктов торрефикации в тарельчатом реакторе и в среде перегретого водяного пара в кипящем слое позволяет улучшить топливные характеристики этих биоотходов благодаря повышению их теплоты сгорания на 15–23%.
2. Что касается влияния торрефикации на плавкостные свойства золы, то использование прогностических критериев не позволило сделать однозначный вывод о том, что после торрефикации можно снизить скорость роста отложений на конвективных поверхностях нагрева котла или минимизировать опасность образования агломератов при сжигании лузги в кипящем слое.
3. Тройная диаграмма дает возмржность сопоставить характеристики различных биотоплив через соотношения между содержанием разных групп оксидов, наиболее часто встречающихся как в биотопливах с тугоплавкой золой, так и в биотопливах, зола которых имеет низкую температуру плавления. С помощью этой диаграммы было установлено, что после торрефикации в среде перегретого водяного пара из лузги подсолнечника может быть получено топливо, близкое по топливным характеристикам к древесным отходам.
Список литературы
Perea-Moreno M.-A., Manzano-Agugliaro F., Perea-Moreno A.-J. Sustainable energy based on sunflower seed husk boiler for residential buildings // Sustainability. 2018. V. 10. Is. 10. P. 3407. https://doi.org/10.3390/su10103407
Cubitto M.A., Gentili A.R. Bioremediation of crude oil-contaminated soil by immobilized bacteria on an agroindustrial waste – sunflower seed husks // Bioremediation J. 2015. V. 19. Is. 4. P. 277–286. https://doi.org/10.1080/10889868.2014.995376
Fouling propensity of high-phosphorus solid fuels: Predictive criteria and ash deposits characterisation of sunflower hulls with P/Ca-additives in a drop tube furnace / L. De Fusco, A. Boucquey, J. Blondeau, H. Jeanmart, F. Contino // Fuel. 2016. V. 170. P. 16–26. https://doi.org/10.1016/j.fuel.2015.12.017
Liquid hot water pretreatment of lignocellulosic biomass at lab and pilot scale / J.M. Jimenez-Gutierrez, R.A.J. Verlinden, P.C. van der Meer, L.A.M. van der Wielen, A.J.J. Straathof // Processes. 2021. V. 9. Is. 9. P. 1518. https://doi.org/10.3390/pr9091518
Runge T., Wipperfurth P., Zhang C. Improving biomass combustion quality using a liquid hot water treatment // Biofuels. 2013. V. 4. Is. 1. P. 73–83. https://doi.org/10.4155/bfs.12.70
Vamvuka D., Zografos D. Predicting the behaviour of ash from agricultural wastes during combustion // Fuel. 2004. V. 83. Is. 14–15. P. 2051–2057. https://doi.org/10.1016/j.fuel.2004.04.012
Investigations on the effect of pre-treatment of wheat straw on ash-related issues in chemical looping gasification (CLG) in comparison with woody biomass / F. Lebendig, I. Funcia, R. Pérez-Vega, M. Müller // Energies. 2022. V. 15. Is. 9. P. 3422. https://doi.org/10.3390/en15093422
Superheated steam as carrier gas and the sole heat source to enhance biomass torrefaction / D. Zhang, X. Chen, Z. Qi, H. Wang, R. Yang, W. Lin, J. Li, W. Zhou, F. Ronsse // Bioresour. Technol. 2021. V. 331. P. 124955. https://doi.org/10.1016/j.biortech.2021.124955
Production of activated carbon from biochar obtained by wet torrefaction of chicken manure as sole feedstock, and in mixture with sawdust in a fluidized bed powered with superheated steam / R.L. Isemin, A.V. Melezhyk, S.N. Kuzmin, A.V. Nebyvayev, N.S. Muratova, A.V. Mikhalev, O.Y. Milovanov, Y.S. Teplitskii, E.K. Buchilko, E.A. Pitsukha, A.J. Grebenkov, M. Brule, F. Tabet // Chem. Eng. Trans. 2021. V. 86. P. 1519–1524. https://doi.org/10.3303/CET2186254
Comparison of characteristics of poultry litter pellets obtained by the processes of dry and wet torrefaction / R. Isemin, A. Mikhalev, O. Milovanov, D. Klimov, V. Kokh-Tatarenko, M. Brulé, F. Tabet, A. Nebyvaev, S. Kuzmin, V. Konyakhin // Energies. 2022. V. 15. Is. 6. P. 2153. https://doi.org/10.3390/en15062153
ГОСТ 32975.3-2014. Биотопливо твердое. Определение содержания влаги высушиванием. Введ. в действие с 01.04.2016.
ГОСТ 32988-2014. Биотопливо твердое. Определение зольности. Введ. в действие с 01.04.2016.
ГОСТ 33256-2015. Биотопливо твёрдое. Определение содержания общих серы и хлора. Введ. в действие с 01.04.2016.
ГОСТ 32985-2014. Биотопливо твердое. Определение углерода, водорода и азота инструментальными методами. Введ. в действие с 01.04.2016.
ГОСТ 32990-2014. Биотопливо твердое. Определение выхода летучих веществ. Введ. в действие с 01.04.2016.
ГОСТ 33106-2014. Биотопливо твердое. Определение теплоты сгорания. Введ. в действие с 01.04.2016.
ГОСТ 10538-87. Топливо твердое минеральное. Методы определения химического состава золы. Введ. в действие с 01.01.1988.
ГОСТ 32977-2014. Топливо твердое минеральное. Определение микроэлементов в золе атомно-абсорбционным способом. Введ. в действие с 01.04.2016.
Torrefaction of pelletized corn residues with wet flue gas / T. Onsree, N. Tippayawong, T. Williams, K. McCullough, E. Barrow, R. Pogaku, J. Lauterbach // Bioresour. Technol. 2019. V. 285. P. 121330. https://doi.org/10.1016/j.biortech.2019.121330
Characteristics of miscanthus fuel by wet torrefaction on fuel upgrading and gas emission behavior / J.-H. Park, Y.-C. Choi, Y.-J. Lee, H.-T. Kim // Energies. 2020. V. 13. Is. 10. P. 2669. https://doi.org/10.3390/en13102669
Zhao L. Agglomeration during fluidized bed combustion and gasification of biomass. Technical University of Denmark, 2021.
Prediction of biomass ash fusion behaviour by the use of detailed characterization methods coupled with thermodynamic analysis / T. Rizvi, P. Xing, M. Pourkashanian, L.I. Darvell, J.M. Jones, W. Nimmo // Fuel. 2015. V. 141. P. 275–284. https://doi.org/10.1016/j.fuel.2014.10.021
An overview of slagging and fouling indicators and their applicability to biomass fuels / J. Lachman, M. Baláš, M. Lisý, H. Lisá, P. Milčák, P. Elbl // Fuel Process. Technol. 2021. V. 217. P. 106804. https://doi.org/10.1016/j.fuproc.2021.106804
Critical review of predictive coefficients for biomass ash deposition tendency / A. Garcia-Maraver, J. Mata-Sanchez, M. Carpio, J.A. Perez-Jimenez // J. Energy Inst. 2017. V. 90. Is. 2. P. 214–228. https://doi.org/10.1016/j.joei.2016.02.002
Vassilev S.V., Baxter D., Vassileva Ch.G. An overview of the behaviour of biomass during combustion. Part II: Ash fusion and ash formation mechanisms of biomass types // Fuel. 2014. V. 117. Part A. P. 152–183. https://doi.org/10.1016/j.fuel.2013.09.024
Vassilev S.V., Baxter D., Vassileva Ch.G. An overview of the behaviour of biomass during combustion. Part I: Phase-mineral transformations of organic and inorganic matter // Fuel. 2013. V. 112. P. 391–449. https://doi.org/10.1016/j.fuel.2013.05.043
Дополнительные материалы отсутствуют.
Инструменты
Теплоэнергетика