Теплоэнергетика, 2022, № 8, стр. 72-81
Переработка золошлаковых отходов сжигания угольных топлив на ТЭЦ Арктической зоны России с получением пористых геополимерных материалов
Е. А. Яценко a, *, Б. М. Гольцман a, **, С. В. Трофимов a, Г. И. Лазоренко b
a Южно-Российский государственный политехнический университет (НПИ) им. М.И. Платова
346428 Ростовская обл., Новочеркасск, ул. Просвещения, д. 132, Россия
b Ростовский государственный университет путей сообщения
344038 Ростов-на-Дону, пл. Ростовского Стрелкового Полка Народного Ополчения, д. 2, Россия
* E-mail: e_yatsenko@mail.ru
** E-mail: boriuspost@gmail.com
Поступила в редакцию 01.12.2021
После доработки 19.01.2022
Принята к публикации 26.01.2022
- EDN: VSDYWE
- DOI: 10.56304/S0040363622070104
Аннотация
В современных условиях наиболее остро стоит вопрос улучшения экологической обстановки во всем мире. Одним из путей его решения в России может стать утилизация золошлаковых отходов, так как для их складирования на золоотвалах требуются колоссальные территории, которые таким образом выпадают из хозяйственного оборота страны. Одно из перспективных направлений утилизации золошлаковых отходов – дорожное строительство, поскольку освоение и благополучие регионов в большой степени зависит от наличия и качества развитой транспортной инфраструктуры. Основные трудности, возникающие при строительстве и эксплуатации дорог в Арктической зоне в условиях повышенной влажности и многолетней мерзлоты, связаны с неравномерным увеличением объема грунта из-за замерзания содержащейся в нем влаги. Для решения этой проблемы применяют теплоизоляционные материалы, а именно пористые геополимеры, полученные путем щелочной активации алюмосиликатного сырья, например золошлаковых отходов. В данной работе использовались золошлаковые отходы Апатитской ТЭЦ и Северодвинской ТЭЦ-1. Для их исследования применялись методы рентгеноспектрального флуоресцентного (XRF) и порошкового рентгенофазового анализа (XRD). По результатам XRF-анализа было выявлено, что исследуемые золошлаковые отходы относятся к разряду кислых. Согласно XRD-анализу, золошлаковые отходы имеют низкое содержание кристаллических фаз, представленных диоксидом кремния (SiO2) и гематитом (Fe2O3). Также присутствует аморфная структура в виде щелочной и щелочно-земельной ферроалюмосиликатной стеклофазы. Для исследования свойств геополимеров были разработаны составы с применением двух порообразующих добавок: алюминиевой пудры и 30%-ного раствора пероксида водорода. После синтеза геополимеров их средние плотности составляли: у золошлаковых отходов Апатитской ТЭЦ 430 и 381 кг/м3 соответственно, у отходов Северодвинской ТЭЦ-1 – 454 и 402 кг/м3 соответственно. Для всех образцов геополимеров характерно интенсивное порообразование с неравномерным распределением пор. Рентгенограммы полученных геополимеров показали малую интенсивность порообразования и низкое содержанием кристаллических фаз во всех исследованных составах.
Ежегодно на объектах угольной энергетики России – твердотопливных ТЭЦ – образуется более 20 млн т золошлаковых отходов – минерального несгораемого остатка угольного топлива, состоящего в основном из различных алюмосиликатных компонентов (55–90%), несгоревшего угля (5–25%) и магнитных минералов (5–20%) [1, 2]. Общий объем накопленных золошлаковых отходов, занимающих территорию более 220 км2, составляет около 1.8–2.0 млрд т [3]. Согласно Федеральному классификационному каталогу отходов, золошлаковые отходы относятся к V классу опасности, т.е. обладают низкой степенью вредного воздействия на окружающую среду. Однако размывание золошлаковых отвалов талыми водами и дождевыми потоками может привести к накоплению в поверхностных и подземных водах продуктов эрозии, к загрязнению и отчуждению почв. Возможно также пыление золы с поверхности золошлаковых отвалов, которое ведет к негативному изменению приземного слоя атмосферы [4]. В настоящее время в России из-за малого объема переработки золошлаковых отходов (не более 15%) [5] целесообразен поиск новых ресурсосберегающих технологий, позволяющих применять золошлаковые отходы в различных отраслях экономики, например в автодорожном строительстве и производстве строительных материалов [6–8].
Кроме того, в связи с тем что золошлаковые отходы обладают высокой дисперсностью и содержат в своем составе значительные доли стекловидных алюмосиликатных фаз, представляет интерес их переработка в перспективные геополимерные материалы [9]. Производство геополимерных вяжущих материалов заключается в щелочной обработке техногенного (золошлаки, зола-унос) или природного (магматические горные породы) сырья [10]. Данный процесс не требует высокотемпературного обжига и не сопровождается значительным выделением углекислого газа [11], что является огромным преимуществом по сравнению с технологией производства портландцемента, получаемого при температурах 1500–1600°C. Результаты проведенных исследований геополимеров свидетельствуют об их долговечности, экологичности и высокой морозостойкости [12, 13]. Например, установлено, что геополимерный бетон на основе золошлаковых отходов обладает морозостойкостью 150 циклов [14].
Геополимеры применяют и в традиционном строительстве. Так, в Австралии из геополимерного бетона изготовляют плиты перекрытий, а в Венеции используют для реставрации архитектурных сооружений [15]. На основе геополимеров можно получать высокоэффективные пористые теплоизоляционные материалы для укладки дорожных слоев, а также асфальтового покрытия [16, 17]. Это особенно актуально для экстремальных климатических условий Арктической зоны, где при строительстве дорог нередко возникает проблема “морозного пучения”, т.е. деформации дорожного полотна, вызванного замерзанием и увеличением объема капиллярной влаги, неравномерно распределенной в верхнем слое грунта. Применение пористых геополимеров при дорожном строительстве в Арктической зоне в условиях многолетней мерзлоты позволит обеспечить дренаж влаги в глубь грунта и повысить его стабильность (когда верхний слой грунта минимально подвержен изменениям объема вследствие замерзания/оттаивания влаги).
Таким образом, разработка составов и изучение особенностей формирования пористых геополимеров на основе золошлаковых отходов ТЭЦ Арктической зоны России для их дальнейшего применения в дорожном строительстве является актуальной и перспективной задачей.
МЕТОДИКА ПРОВЕДЕНИЯ ИССЛЕДОВАНИЙ
В качестве основного сырья для синтеза пористых геополимерных материалов были использованы золошлаковые отходы Апатитской ТЭЦ и Северодвинской ТЭЦ-1. Определение оксидного и элементного состава золошлаковых отходов проводилось методом рентгеноспектрального флуоресцентного анализа на последовательном вакуумном спектрометре модели PW2400 производства Philips Analytical (Нидерланды). Анализ микроструктуры пористых геополимерных материалов осуществлялся с помощью электронного микроскопа BresserDuolux.
Фазовый состав исходных золошлаковых отходов и синтезированных образцов определяли с помощью порошкового рентгенофазового анализа. Образцы измельчали и исследовали с помощью рентгеновского порошкового дифрактометра ARL (Thermo Fisher Scientific), входящего в состав ЦКП “Нанотехнологии” Южно-Российского государственного политехнического университета (НПИ) им. М.И. Платова. Полученные в ходе исследования данные обрабатывали с использованием программного комплекса Crystallographica Search-Match Version 3 базы данных ICDD PDF 2 (Международный центр дифракционных данных).
Таблица 1.
Химический оксидный состав золошлаковых отходов
Золошлаковые отходы | Содержание оксидов, % (по массе) | |||||||||||||
---|---|---|---|---|---|---|---|---|---|---|---|---|---|---|
SiO2 | Al2O3 | Fe2O3 | MgO | Na2O | K2O | CaO | TiO2 | MnO | P2O5 | SO3 | ппп* | Прочие | Всего | |
Апатитской ТЭЦ | 52.39 | 22.15 | 7.73 | 2.63 | 0.78 | 1.94 | 3.59 | 1.05 | 0.07 | 0.36 | 0.37 | 6.46 | 0.48 | 100.00 |
Северодвинской ТЭЦ-1 | 60.78 | 17.69 | 5.93 | 2.71 | 3.56 | 2.29 | 2.08 | 0.82 | 0.07 | 0.21 | 0.32 | 2.29 | 1.25 | 100.00 |
Синтез геополимеров проводили по следующей технологии: золошлаковые отходы сушили при температуре 100°С до постоянной массы и измельчали до размера частиц менее 250 мкм [18, 19]. Для щелочной активации алюмосиликатных компонентов в качестве активирующего вещества использовали смесь жидкого стекла и раствора NaOH. К заданному количеству порошка NaOH марки ХЧ (химически чистый) добавляли воду для получения 12 М (моль/л) раствора. Далее его смешивали с навеской жидкого стекла [гидросиликат натрия, силикатный модуль 2, содержание воды 55% (по массе)], после чего полученную суспензию вливали в навеску золошлакового отхода. Перемешивание геополимерной суспензии вели в течение 10 мин в барабанной мельнице (соотношение “геополимерная смесь : мелющие тела” составляло 1.0 : 1.5) [19, 20]. После приготовления смеси в нее добавляли порообразователь (порошок алюминия или 30%-ный раствор пероксида водорода), после чего перемешивали еще 10 мин при тех же условиях [21].
Полученные составы (сырьевую смесь) разливали в цилиндрические формы диаметром 37 мм и высотой 40 мм и высушивали. Сушка проводилась в помещении без прямого попадания солнечных лучей при комнатной температуре 25 ± 2°С в течение 14 сут [22, 23] при относительной влажности воздуха 58 ± 5%. Линейные размеры образцов после сушки определяли штангенциркулем, после чего по их значениям рассчитывали объем (см3):
где h, D – высота и диаметр образца, см.Массу образцов m измеряли с точностью до 0.01 г, а их среднюю плотность, кг/м3, определяли по формуле
Каждое записанное тестовое значение плотности представляло собой среднее из трех значений плотности синтезированных образцов геополимеров каждого состава.
Размер и распределение пор в образцах определяли по программе NanoMeasurer 1.2, позволяющей по результатам микрофотографирования в автоматическом режиме собирать и анализировать данные о количестве и размере пор.
ЭКСПЕРИМЕНТАЛЬНАЯ ЧАСТЬ
При исследовании золошлаковых отходов Апатитской ТЭЦ и Северодвинской ТЭЦ-1 были определены их оксидный и элементный составы, представленные в табл. 1, 2 .
Таблица 2.
Элементный состав прочих оксидов, содержащихся в золошлаковых отходах и не вошедших в табл. 1
Золошлаковые отходы | Содержание элементов, ×10–4% (по массе) | ||||||||||||||||
---|---|---|---|---|---|---|---|---|---|---|---|---|---|---|---|---|---|
Cr | V | Ni | Cu | Zn | Rb | Sr | Zr | Ba | U | Th | Y | Nb | Pb | As | Cl | Mo | |
Апатитской ТЭЦ | 205 | 223 | 180 | 137 | 179 | 80 | 1216 | 298 | 2060 | 14 | 19 | 91 | 20 | 71 | 32 | 12 | 5 |
Северодвинской ТЭЦ-1 | 103 | 116 | 56 | 39 | 81 | 81 | 338 | 277 | 1103 | 5 | 11 | 37 | 16 | 33 | 11 | 10 227 | 5 |
Согласно анализу данных, приведенных в табл. 1 , основные компоненты золошлаковых отходов Апатитской ТЭЦ и Северодвинской ТЭЦ-1 – оксиды кремния и алюминия. Исследованные золошлаковые отходы по содержанию компонентов относятся к низкокальциевым, так как содержание соединений CaO + MgO не превышает 12%, что соответствует кислым отходам. Кислые золошлаковые отходы не обладают вяжущими свойствами, но могут приобрести их при добавлении интенсификаторов твердения. Также при повышенном содержании SiO2 отходы в меньшей степени подвержены кристаллизации и образуют аморфную структуру. Кроме того, оба исследованных вида золошлаковых отходов содержат 2–6% соединений из категории “потери при прокаливании” (убыль массы вещества, нагреваемого до определенной температуры), представленных в основном несгоревшим углеродом (так называемый недожог). Это может оказать негативное влияние на качество геополимеров при их длительной эксплуатации в условиях Арктической зоны России.
Для определения фазового состава золошлаковых отходов Апатитской ТЭЦ и Северодвинской ТЭЦ-1 был проведен порошковый рентгенофазовый анализ (рис. 1), результаты которого позволяют сделать вывод, что оба исследованных материала характеризуются низкой интенсивностью пиков ввиду невысокого содержания кристаллических фаз, представленных диоксидом кремния (SiO2) в форме высокотемпературного α-кварца (номер карточки из базы данных ICDD: 010-89-8936). На рентгенограммах отходов также присутствует гало в углах сьемки 2θ от 14° до 30°, что свидетельствует о наличии аморфной структуры в виде щелочной и щелочно-земельной ферроалюмосиликатной стеклофазы.
Рис. 1.
Рентгенограмма золошлаковых отходов на Апатитской ТЭЦ (а) и Северодвинской ТЭЦ-1 (б). 1 – α-кварц
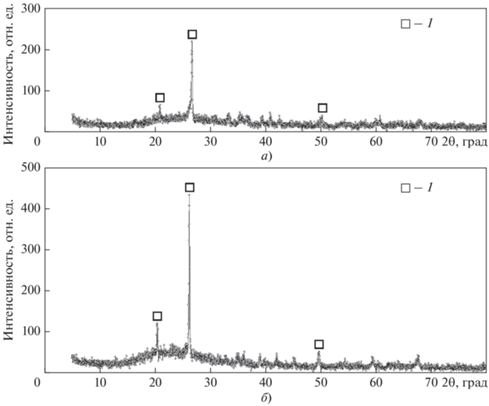
На основе золошлаковых отходов Северодвинской ТЭЦ-1 и Апатитской ТЭЦ были синтезированы пористые геополимеры двух составов с добавлением различных порообразующих добавок: в составе 1 использовалась алюминиевая пудра, а в составе 2 – 30%-ный раствор пероксида водорода (H2O2). В табл. 3 приведены шихтовый состав сырьевых смесей и такие характеристики синтезированных геополимеров, как средняя плотность и прочность при сжатии. Составы на основе золошлаковых отходов Северодвинской ТЭЦ-1 обозначены как 1с и 2с, Апатитской ТЭЦ – 1а и 2а. Для каждого состава было синтезировано по три образца.
Таблица 3.
Шихтовый состав сырьевых смесей и характеристики синтезированных геополимеров
Cостав | Содержание компонента, % (по массе)* | Средняя плотность, кг/м3 | Прочность при сжатии, МПа | |||||
---|---|---|---|---|---|---|---|---|
золошлак | NaOH (сухой) | вода | жидкое стекло | пероксид водорода, сверх 100 | алюминиевая пудра, сверх 100% | |||
1с | 75 | 2.5 | 4.5 | 18 | – | 2 | 430 | 2.76 |
2с | 75 | 2.5 | 4.5 | 18 | 2 | – | 381 | 2.26 |
1а | 75 | 2.5 | 4.5 | 18 | – | 2 | 454 | 2.81 |
2а | 75 | 2.5 | 4.5 | 18 | 2 | – | 402 | 2.52 |
Представленные в табл. 3 данные свидетельствуют о том, что наименьшей плотностью и, соответственно, большей пористостью обладают образцы на основе золошлаковых отходов Северодвинской ТЭЦ-1. Лучший результат в качестве порообразующей добавки для тех и других золошлаков показал 30%-ный раствор пероксида водорода: разница плотностей образцов с порообразующими добавками составляла в среднем 50 кг/м3: 430–450 кг/м3 для алюминиевой пудры и 380–400 кг/м3 для пероксида водорода. При уменьшении плотности образцов, как и ожидалось, снизился предел прочности на сжатие с 2.8 до 2.3–2.5 МПа.
Микроструктуры синтезированных геополимеров на основе золошлаковых отходов Апатитской ТЭЦ и Северодвинской ТЭЦ-1 с введением порообразующих добавок показаны на рис. 2, 3. Образцы на основе золошлаковых отходов обеих ТЭЦ с добавлением алюминиевой пудры характеризуются интенсивным порообразованием. Для отходов Апатитской ТЭЦ наблюдается неравномерное распределение макропор (см. рис. 2, а), размеры которых составляют от 0.8 до 6.0 мм, а для отходов Северодвинской ТЭЦ-1 это распределение практически равномерное (см. рис. 3, а). Образцы (см. рис. 2, б) на основе золошлаковых отходов обеих ТЭЦ с добавлением 30%-ного раствора пероксида водорода также характеризуются интенсивным порообразованием и неравномерным распределением макропор, максимальные размеры которых для золошлаков Апатитской ТЭЦ составляют 12.0 мм, а Северодвинской ТЭЦ-1 – 7.2 мм. Распределение размеров пор в геополимерах на основе золошлаковых отходов обеих ТЭЦ представлено на рис. 4.
Рис. 2.
Микроструктура синтезированных геополимеров на основе золошлаковых отходов Апатитской ТЭЦ с применением в качестве порообразующей добавки алюминиевой пудры (а) и 30%-ного раствора пероксида водорода (б)
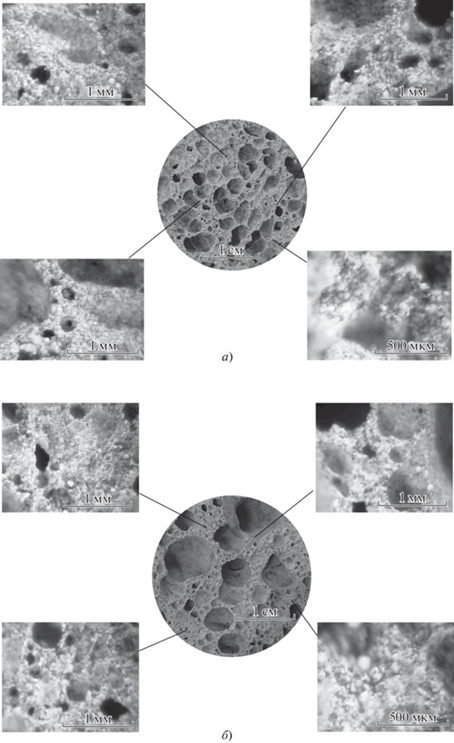
Рис. 3.
Микроструктура синтезированных геополимеров на основе золошлаковых отходов Северодвинской ТЭЦ-1 с применением в качестве порообразующей добавки алюминиевой пудры (а) и пероксида водорода (б)
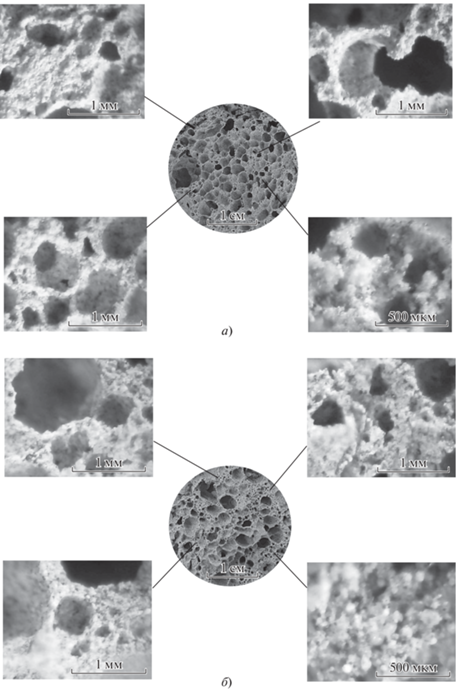
Рис. 4.
Распределение размеров пор в геополимерах на основе золошлаковых отходов Апатитской ТЭЦ (а) и Северодвинской ТЭЦ-1 (б). Порообразующая добавка: 1 – алюминиевая пудра; 2 – 30%-ный раствор пероксида водорода
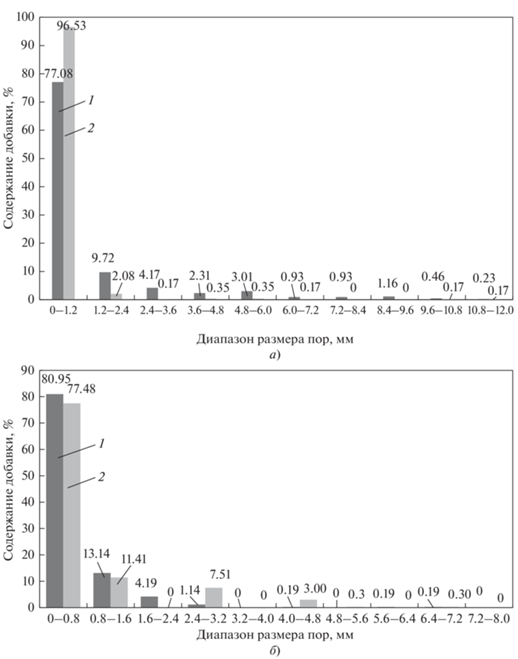
Проанализировав структуры образцов геополимеров на основе золошлаковых отходов Апатитской ТЭЦ и Северодвинской ТЭЦ-1, можно сделать следующий вывод: при применении различных добавок порообразование происходит интенсивно, при этом наиболее распространенными оказываются закрытые макропоры размером до 1.6 мм. Полученные геополимеры составов 2с и 2а с введением в качестве порообразующей добавки пероксида водорода характеризуются наличием крупных пор, что может негативно сказаться на стабильности свойств получаемых образцов – прочности и теплопроводности.
Для определения фазового состава синтезированных на основе золошлаковых отходов Апатитской ТЭЦ (рис. 5) и Северодвинской ТЭЦ-1 (рис. 6) геополимеров был проведен порошковый рентгенофазовый анализ, результаты которого показывают, что во всех четырех представленных составах присутствует интенсивное гало в углах сьемки 2θ от 14° до 34°, что свидетельствует о наличии рентгеноаморфной стеклофазы. Все исследованные материалы характеризуются низкой интенсивностью пиков и, следовательно, невысоким содержанием кристаллических фаз, которые в синтезированных образцах с порообразующей добавкой алюминиевой пудры представлены диоксидом кремния SiO2 в форме α-кварца и альбитом NaAlSi3O8, а с порообразующей добавкой 30%-ного раствора пероксида водорода – только диоксидом кремния SiO2. Образование небольшого количества альбита в составах с алюминиевым порообразователем обусловлено, вероятно, действием атомов алюминия, которые в процессе окисления ведут к формированию кристаллов альбита [10].
Рис. 5.
Рентгенограмма синтезированных геополимеров на основе золошлаковых отходов Апатитской ТЭЦ с применением в качестве порообразующей добавки алюминиевой пудры (а) и 30%-ного раствора пероксида водорода (б). 1 – α-кварц; 2 – альбит (NaAlSi3O8)
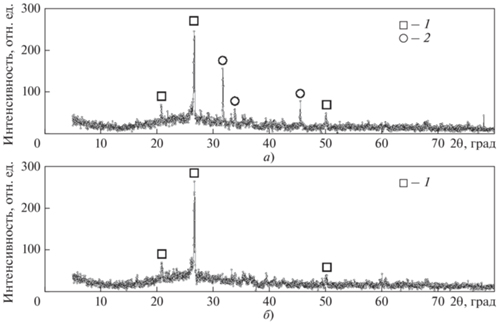
Рис. 6.
Рентгенограмма синтезированных геополимеров на основе золошлаковых отходов Северодвинской ТЭЦ-1 с применением в качестве порообразующей добавки алюминиевой пудры (а) и 30%-ного раствора пероксида водорода (б). Обозначения см. рис. 5
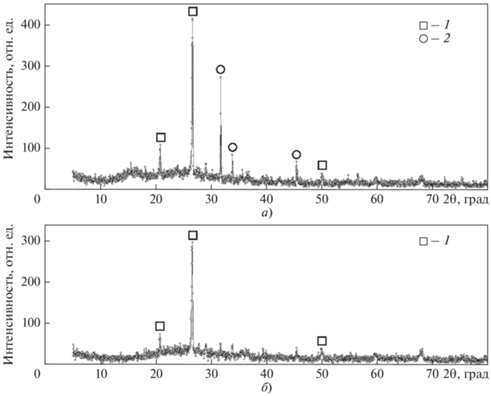
Низкая интенсивность пиков кристаллических фаз и наличие стеклофазы в геополимерных материалах приводит к избыточной внутренней энергии и, как следствие, высокой реакционной способности получаемых материалов. Это можно объяснить тем, что глинистые компоненты, присутствующие в углях, длительное время находятся в зоне высоких температур, вследствие чего спекаются и образуют остеклованные частицы.
Таким образом, в процессе экспериментов была доказана возможность использования золошлаковых отходов ТЭЦ Арктической зоны России в качестве основного сырья для синтеза пористых геополимерных материалов. Такие материалы могут найти широкое применение в различных отраслях экономики, в частности в дорожном строительстве.
ВЫВОДЫ
1. Золошлаковые отходы, образующиеся на Апатитской ТЭЦ и Северодвинской ТЭЦ-1, пригодны для использования в качестве сырья при производстве пористых геополимеров. Наилучшей порообразующей добавкой является 30%-ный раствор пероксида водорода: разница в плотности ее и другой порообразующей добавки – алюминиевой пудры составляет в среднем 12%. Более равномерным распределением и меньшими размерами пор отличаются образцы с алюминиевой пудрой, в образцах с 30%-ным раствором пероксида водорода присутствуют макропоры размером более 2.5 мм в большем количестве, исключение составляют образцы на основе золошлаковых отходов Апатитской ТЭЦ. Значительное количество макропор может отрицательно сказаться на прочности и теплопроводности получаемых материалов.
2. На рентгенограммах синтезированных геополимеров наблюдаются низкая интенсивность пиков кристаллических фаз и наличие стеклофазы, что обусловливает избыточную внутреннюю энергию и, как следствие, высокую реакционную способность производимых материалов.
3. Золошлаковые отходы Апатитской ТЭЦ и Северодвинской ТЭЦ-1, находящихся в Арктической зоне, можно рекомендовать в качестве основного сырья для синтеза геополимерных материалов.
Список литературы
Законодательное регулирование использования золошлаковых отходов угольных ТЭЦ: “Круглый стол” / М-во энергетики РФ, 2019. https://minenergo.gov.ru/node/14014
Методы обогащения золошлаковых отходов угольных ТЭЦ и пути их вовлечения в хозяйственный оборот (обзор) / Ю.В. Рябов, Л.М. Делицын, Н.Н. Ежова, С.В. Сударева // Теплоэнергетика. 2019. № 3. С. 3–24. https://doi.org/10.1134/S0040363619030056
Исследование возможностей комплексной переработки отходов предприятий энергетики Приморского края / Е.И. Шамрай, А.В. Таскин, С.И. Иванников, А.А. Юдаков // Современные наукоемкие технологии. 2017. № 3. С. 68–75. https://doi.org/10.17513/snt.36618
Черенцова А.А., Олесик С.М. Оценка золошлаковых отходов как источник загрязнения окружающей среды и как источник вторичного сырья // Горный информ.-аналит. бюл. 2013. № 3. С. 230–243.
Goltsman B.M., Yatsenko L.A., Goltsman N.S. Production of foam glass materials from silicate raw materials by hydrate mechanism // Solid State Phenomena. 2020. V. 299. P. 293–298. https://doi.org/10.4028/www.scientific.net/SSP.299.293
Применение зол и золошлаковых отходов в строительстве / Н.И. Ватин, Д.В. Петросов, А.И. Калачев, П. Лахтинен // Magazine Civil Eng. 2011. Т. 22. № 4. С. 16–21. https://doi.org/10.5862/MCE.22.2
Waste slag from heating plants as a partial replacement for cement in mortar and concrete production. Part I. Physical–chemical and physical–mechanical characterization of slag / A. Nedeljković, M. Stojmenović, J. Gulicovski, N. Ristić, S. Milićević, J. Krstić, M. Kra-gović // Minerals. 2020. V. 10. Is. 11. P. 992. https://doi.org/10.3390/min10110992
Yatsenko E.A., Goltsman B.M. Study of synthesis processes of heat-insulating silicate materials for external protection of steel oil pipelines // CIS Iron Steel Rev. 2020. V. 20. P. 33–36. https://doi.org/10.17580/cisisr.2020.02.08
Ahmed M.F., Nuruddin M.F., Shafiq N. Compressive strength and workability characteristics of low-calcium fly ash-based self-compacting geopolymer concrete // Int. J. Civil Environ. Eng. 2011. V. 5. Is. 2. P. 72–78. https://doi.org/10.5281/zenodo.1330481
Davidovits J. Geopolymer chemistry and applications. 5rd ed. France, Saint-Quentin: Institut Géopolymère, 2020.
Dombrowski K., Buchwald A., Weil M. The influence of calcium content on the structure and thermal performance of fly ash based geopolymers // J. Mater. Sci. 2007. V. 42. Is. 9. P. 3033–3043. https://doi.org/10.1007/s10853-006-0532-7
Steinerova M. Mechanical properties of geopolymer mortarsin relation to their porous structure // Ceram. – Silik. 2011. V. 55. Is. 4. 362–372.
Provis J.L., van Deventer J.S.J. Geopolymers: structure, processing, properties and industrial applications. Woodhead Publishing, 2009.
Škvára F., Jílek T., Kopecký L. Geopolymer materials based on fly ash // Ceram. – Silik. 2005. V. 49. Is. 3. P. 195–204.
Дудников А.Г., Дудникова М.С., Реджани А. Геополимерный бетон и его применение // Строительные материалы, оборудование, технологии XXI века. 2018. № 1–2. С. 38–45.
Development of porous fly ash-based geopolymer with low thermal conductivity / J. Feng, R. Zhang, L. Gong, Y. Li, W. Cao, X. Cheng // Mater. Des. 2015. V. 65. P. 529–533. https://doi.org/10.1016/j.matdes.2014.09.024
Utilisation of waste-based geopolymer in asphalt pavement modification and construction – A review / A. Milad, A.S.B. Ali, A.M. Babalghaith, Z.A. Memon, N.S. Mashaan, S. Arafa, N.I.Md. Yusoff // Sustainability. 2021. V. 13. Is. 6. https://doi.org/10.3390/su13063330
Wu J. Preparation and characterization of ultra-lightweight foamed geopolymer (UFG) based on fly ash-metakaolin blends // Constr. Build. Mater. 2018. V. 168. P. 771–779. https://doi.org/10.1016/j.conbuildmat.2018.02.097
Waste-based geopolymeric mortars with very high moisture buffering capacity / A. De Rossi, J. Carvalheiras, R.M. Novais, M.J. Ribeiro, J.A. Labrincha, D. Hotza, R.F.P.M. Moreira // Constr. Build. Mater. 2018. V. 191. P. 39–46. https://doi.org/10.1016/j.conbuildmat.2018.09.201
Development of eco-friendly geopolymers with ground mixed recycled aggregates and slag / J. Tan, J. Cai, X. Li, J. Pan, J. Li. // J. Cleaner Prod. 2020. V. 256. P. 120369. https://doi.org/10.1016/j.jclepro.2020.120369
Peculiarities of foam glass synthesis from natural silica-containing raw materials / E.A. Yatsenko, B.M. Goltsman, L.V. Klimova, L.A. Yatsenko // J. Therm. Anal. Calorim. 2020. V. 142. P. 119–127. https://doi.org/10.1007/s10973-020-10015-3
Natural fibers as reinforcement additives for geopolymers – A review of potential eco-friendly applications to the construction industry / G. Silva, S. Kim, R. Aguilar, J. Nakamatsu // Sustainable Mater. Technol. 2020. V. 23. P. e00132. https://doi.org/10.1016/j.susmat.2019.e00132
Optimization and mechanical-physical characterization of geopolymers with Construction and Demolition Waste (CDW) aggregates for construction products / M. Panizza, M. Natalia, E. Garbin, V. Ducman, S. Tam-burini // Constr. Build. Mater. 2020. V. 264. P. 120158. https://doi.org/10.1016/j.conbuildmat.2020.120158
Дополнительные материалы отсутствуют.
Инструменты
Теплоэнергетика