Теплоэнергетика, 2022, № 7, стр. 23-37
Численное исследование эффективности внутреннего оребрения “активного” объема проточных металлогидридных реакторов очистки водорода от примесей
М. Д. Нащёкин a, К. Б. Минко a, *
a Национальный исследовательский университет “Московский энергетический институт”
111250 Москва, Красноказарменная ул., д. 14, Россия
* E-mail: minkokb@gmail.com
Поступила в редакцию 24.10.2021
После доработки 16.11.2021
Принята к публикации 24.11.2021
- EDN: XTCYOL
- DOI: 10.1134/S0040363622070050
Аннотация
Одним из путей развития альтернативной энергетики является использование водорода в качестве энергоносителя. В настоящее время в мире производство относительно чистого водорода путем электролиза воды не превышает 5%, другие способы получения водорода сопровождаются загрязнением его примесями. В то же время для использования в топливных элементах, системах охлаждения турбин и двигателях требуется водород высокой чистоты. Один из перспективных и безопасных методов очистки водорода основан на избирательном его поглощении при фильтрации смеси водород ‒ примесь через слой металлогидрида. В данной статье представлены результаты численного исследования процессов тепломассопереноса в проточном металлогидридном реакторе очистки водорода с внутренним оребрением “активного” объема (объема сорбирующей засыпки). Для интенсификации теплопередачи от засыпки к охлаждаемым/нагреваемым стенкам реактора в конструкции были использованы радиальные ребра из различных металлов. Выполнен анализ различных вариантов внутреннего оребрения, влияния условий внешнего охлаждения на процессы тепло- и массообмена в реакторе. Проверена чувствительность результатов расчета к точности определения параметров математической модели. Показано, что при внутреннем оребрении и правильном подборе условий внешнего охлаждения характеристики металлогидридной системы хранения и очистки водорода могут быть значительно улучшены. Сделан вывод о том, что плотность оребрения (количество ребер) и теплопроводность материала, из которого изготовлены ребра, оказывают заметное влияние на эффективность проточного реактора только при достижении на его внешней стенке определенных значений коэффициента теплоотдачи к охлаждающей жидкости.
Высокая селективность обратимого взаимодействия водорода с гидридообразующими материалами – интерметаллическими сплавами (ИМС) ‒ позволяет разрабатывать простые и эффективные системы извлечения водорода из газовых смесей, которые обеспечивают его тонкую очистку [1]. Выделяют два принципиально различных метода очистки водорода: метод короткоцикловой абсорбции [2] и очистку методом фильтрации смеси через засыпку из частиц ИМС [3]. При короткоцикловой абсорбции в объем реактора поступает смесь водород ‒ примесь, водород начинает избирательно сорбироваться сплавом. При этом в свободном объеме реактора происходит накопление загрязняющих водород газовых примесей, что приводит к постепенному снижению скорости зарядки реактора водородом. Для восстановления динамики зарядки выполняют продувку свободного объема и удаляют накопившиеся примеси, после чего на вход подают смесь исходного состава. Процесс циклически повторяется до полного насыщения водородом гидридообразующего сплава.
При втором методе предусматривается фильтрация водорода и загрязняющих его примесей через объем засыпки из частиц ИМС. При этом до момента так называемого “прорыва” водорода на выходе из реактора его покидает практически не содержащая водород смесь исходных загрязняющих примесей. После насыщения водородом сплав может храниться сколь угодно долго и при необходимости водород может извлекаться из него, при этом чистота десорбируемого водорода составляет не менее 99.999%.
Наиболее значимой характеристикой систем очистки является коэффициент извлечения водорода ω – отношение количества водорода, запасенного в металлогидриде, к общему объему водорода, поступившему на вход в процессе очистки. Следует отметить, что эти технологии ограничены очисткой водорода от так называемых пассивных газов (азот, диоксид углерода и др.), не отравляющих сорбирующий ИМС.
В настоящее время выполнено значительное количество исследований прототипов устройств подобного класса и оценок возможности их применения в различных технологических процессах. В работе [4] исследовалось извлечение водорода (140 м3/день)22 из продувочного газа, образующегося при синтезе аммиака. При эксплуатации в течение 6 мес авторы продемонстрировали работоспособность пилотной установки в широком диапазоне рабочих параметров [давление на входе от 1 до 4 МПа, плотность массового потока смеси через металлогидридную засыпку от 300 до 1000 дм3/(м2 ∙ с)]. Среднее значение коэффициента извлечения водорода изменялось от 90 до 93% при чистоте водорода выше 99%.
Похожий технологический процесс был экспериментально исследован в [5] для получения водорода и его последующего применения при производстве термополированного стекла. В [6, 7] предложена металлогидридная технология для повышения степени чистоты водорода, используемого в системах охлаждения мощных турбогенераторов электростанций. В [8] металлогидридная система была использована для извлечения водорода из смеси H2/CO2 и рекомендована к применению как вторая ступень системы очистки биоводорода с предварительным удалением отравляющих металлогидрид компонентов в мембранном модуле.
В работах [9, 10] авторы разработали энергоустановку, работающую на биоводороде, и провели испытания проточного металлогидридного реактора по очистке водорода от примеси СО2, при этом коэффициент извлечения водорода составил более 80%. Экспериментальные результаты по разделению смеси водорода (объемная доля водорода 10%) с метаном в проточном металлогидридном реакторе представлены в [11]. Продемонстрирована возможность применения металлогидридных систем очистки для извлечения водорода из смесей водород‒природный газ, образующихся при доставке водорода потребителям с использованием имеющейся инфраструктуры для транспортировки природного газа.
В работе [12] использовалась модель с сосредоточенными параметрами для изучения металлогидридной системы извлечения водорода из смеси водород ‒ диоксид углерода. Рассматривалась зарядка металлогидридного реактора смесью с массовой долей диоксида углерода 2.15%, после короткой продувки происходила десорбция чистого водорода. Как считают авторы [12], ключевым фактором является правильный подбор параметров процесса (внешнего давления и времени продувки), в противном случае в системе может сохраниться значительная доля диоксида углерода. Коэффициент теплоотдачи α от засыпки к охлаждающей воде для экспериментально исследованного режима был равен 250 Вт/(м2 ∙ К), но, как показали параметрические исследования, для устранения влияния условий охлаждения на эффективность очистки требовалось увеличение коэффициента теплоотдачи до α = 350‒450 Вт/(м2 ∙ К).
В настоящее время активно исследуются различные способы повышения эффективности металлогидридных систем очистки водорода, в числе которых разработка сплавов, пригодных для использования в системах подобного класса [13], и оптимизация тепловых схем, направленных на повышение эффективности отвода значительного тепла реакции сорбции через слой из частиц металлогидрида, обладающий крайне низкой теплопроводностью (теплопроводность засыпки, насыщенной газовой смесью, может быть в 2‒3 раза ниже, чем при насыщении чистым водородом).
Используемые методы интенсификации процессов теплоотдачи в металлогидридных реакторах систематизированы в [14]. Один из наиболее часто применяемых способов интенсификации ‒ размещение каналов с охлаждающей жидкостью внутри металлогидридной засыпки с оребрением межтрубного пространства. В работах [15‒19] анализируется эффективность подобных конструкций для снижения времени зарядки системы хранения водорода. Результаты этих работ показывают, что оптимальный шаг установки элементов, отводящих тепло, составляет от 5 до 10 мм, что хорошо согласуется с исследованиями, выполненными ранее другими авторами [20]. В некоторых работах, например [21], предлагается использовать тепловую трубу, которая обеспечивает эффективный “пассивный” отвод тепла из центральной перегретой части засыпки.
Работы [15‒20] посвящены изучению и оптимизации процессов тепло- и массообмена в реакторах с внутренним оребрением, в которых используется исключительно чистый водород. Полученные результаты трудно перенести на системы очистки водорода методом продувки газовой смеси, так как для них коэффициент извлечения водорода в значительной степени связан со степенью равномерности скорости сорбции водорода по всему сечению реактора, нормальному к направлению движения смеси. Существенная неоднородность может приводить к резкому падению коэффициента извлечения водорода в тот момент, когда слой ИМС вблизи хорошо охлаждаемой стенки реактора “насытится” водородом и начнет “пропускать” его к выходу из системы. При этом отвод тепла должен происходить из области активной сорбции водорода, засыпка которой имеет крайне низкие значения эффективной теплопроводности, что связано с уменьшением объемной доли водорода в смеси.
Насколько известно авторам, особенности процессов тепло- и массопереноса в металлогидридных системах для очистки водорода методом продувки при наличии внутреннего оребрения детально не изучались. Существующие работы посвящены либо анализу общей производительности систем подобного типа, либо исследованию возможности использования пеноматериалов [22] или высокотеплопроводных добавок [23] для повышения их эффективности. Целью данной работы является изучение с помощью численного моделирования влияния внутреннего оребрения на эффективность функционирования металлогидридной системы очистки водорода методом продувки.
ФИЗИЧЕСКАЯ ПОСТАНОВКА ЗАДАЧИ
В настоящей работе рассматривались цилиндрические металлогидридные реакторы двух исходных конструкций для очистки водорода: реактор с внутренним оребрением и без него (рис. 1). Основные характеристики реактора без оребрения были взяты из [24]. В реакторе использовалось 1.6 кг сплава LaFe0.1Mn0.3Ni4.8, максимальная емкость по водороду равнялась 245 дм3. Радиус металлогидридной засыпки ${{R}_{1}} = 26.5\,\,{\text{мм,}}$ толщина стенки реактора ${{\delta }_{w}}$ = 2 мм. Высота металлогидридной засыпки в реакторе без внутреннего оребрения составляла 210 мм, при наличии оребрения она увеличилась до 256 мм. Ребра длиной 20 мм имели трапециевидную форму, толщина ребра у основания ${{\delta }_{t}}$ = 4 мм. В исходной конструкции стенки и ребра были выполнены из стали.
Рис. 1.
Варианты конструкции металлогидридного реактора. а ‒ общий вид реактора; б ‒ реактор без оребрения; в ‒ реактор с оребрением

В качестве основного был выбран один из режимов, описанный в работе [24]. На вход в реактор подавалась газовая смесь постоянного состава (мольная доля H2 – 73%, N2 – 27%) при фиксированном давлении (0.5 МПа). На выходе из реактора с помощью дросселя поддерживался фиксированный расход смеси. При этом в эксперименте [24] можно выделить два характерных интервала времени: период в течение 8 мин до выхода на квазистационарный режим с расходом смеси на выходе 0.60 дм3/мин и последующий режим квазистационарной очистки водорода с расходом смеси на выходе 1.06 дм3/мин. Вся система была погружена в термостат, заполненный смесью воды и льда и обеспечивающий постоянную температуру ${{T}_{0}}$ = 0°С. Оценки коэффициента теплоотдачи по соотношениям для свободной конвекции, выполненные в [25], дали значение около 100 Вт/(м2 ∙ К), и именно это значение было принято в качестве базового в настоящей работе.
МАТЕМАТИЧЕСКАЯ МОДЕЛЬ
Для описания процессов тепло- и массопереноса в металлогидридном реакторе использовалась система уравнений сохранения для твердой (засыпка, стенка реактора, ребра) и газовой фаз [26, 27]. Если при моделировании процессов в металлогидридных системах, работающих с чистым водородом, вполне приемлемым является принятие существенных упрощений, то для систем очистки водорода принципиально важен учет эффектов, связанных с фильтрацией газовой фазы через слой металлогидридной засыпки [28]. Для области, занятой металлогидридной засыпкой, уравнения сохранения массы имеют вид:
для твердой фазы
(1)
$\left( {1 - \varepsilon } \right){{\rho }_{{0,s}}}{{X}_{s}}\frac{{{\text{d}}X}}{{{\text{d}}t}} = \frac{{{{M}_{{{\text{Me}}}}}}}{{{{M}_{{\text{H}}}}}}\dot {m};$для газовой фазы
(2)
$\begin{gathered} \frac{{\partial \left( {\varepsilon {{\rho }_{{0,g}}}{{x}_{j}}} \right)}}{{\partial t}} + \nabla \cdot \left( {\varepsilon {{\rho }_{{0,g}}}{{{\vec {w}}}_{g}}{{x}_{j}} - \varepsilon {{\rho }_{{0,g}}}D{\text{*}}\nabla {{x}_{j}}} \right) = - {{{\dot {m}}}_{j}}, \\ j = 1, \ldots ,N; \\ {{{\dot {m}}}_{1}} = \dot {m}\,\,({\text{водород}}),\,\,\,\,{{{\dot {m}}}_{{j > 1}}} = 0\,\,({\text{примесные}}\,\,{\text{газы}}). \\ \end{gathered} $Здесь $\varepsilon $ – пористость; ${{\rho }_{0}}$ – истинная плотность фазы, кг/м3; ${{X}_{s}}$ – количество атомов водорода на один атом металла; $X$ – доля сплава, насыщенного водородом; t – время, с; ${{M}_{{{\text{Me}}}}}$ – молекулярная масса металла, кг/моль; ${{M}_{{\text{H}}}}$ – молекулярная масса атомарного водорода, кг/моль; $\dot {m}$ – объемная мощность источника массы водорода, кг/(м3 ∙ с); ${{x}_{j}}$ – массовая концентрация j-го компонента смеси; ${{\vec {w}}_{g}}$ – вектор осредненной скорости газа в порах, м/с; $D{\text{*}}$ – “эффективный” коэффициент диффузии, м2/с; индексы “g” и “s” относятся к газовой и твердой фазе соответственно.
Уравнения сохранения энергии:
для твердой фазы
(3)
$\begin{gathered} \left( {1 - \varepsilon } \right){{\rho }_{{0,s}}}{{c}_{{p,s}}}\frac{{\partial {{T}_{s}}}}{{\partial t}} = \nabla \cdot \left[ {\left( {1 - \varepsilon } \right)\lambda _{s}^{*}\nabla {{T}_{s}}} \right] + \\ + \,\,{{\alpha }_{{sg}}}{{A}_{{sg}}}\left( {{{T}_{g}} - {{T}_{s}}} \right) + \dot {m}\left[ {\Delta {{h}_{{sg}}} + c_{{p,{\text{H}}}}^{{(s)}}\left( {T{\text{*}} - {{T}_{s}}} \right)} \right]; \\ \end{gathered} $для газовой фазы
(4)
$\begin{gathered} \varepsilon {{\rho }_{{0,g}}}{{c}_{{p,g}}}\frac{{\partial {{T}_{g}}}}{{\partial t}} + \left( {\varepsilon {{\rho }_{{0,g}}}{{{\vec {w}}}_{g}}{{c}_{{p,g}}} - \varepsilon {{\rho }_{{0,g}}}\sum\limits_{j = 1}^N {{{c}_{{p,j}}}D{\text{*}}\nabla {{x}_{j}}} } \right)\nabla {{T}_{g}} = \\ = \nabla \cdot \left[ {\varepsilon \lambda _{g}^{*}\nabla {{T}_{g}}} \right] + {{\alpha }_{{sg}}}{{A}_{{sg}}}\left( {{{T}_{s}} - {{T}_{g}}} \right) - \dot {m}c_{{p,{\text{H}}}}^{{(g)}}\left( {T{\text{*}} - {{T}_{g}}} \right). \\ \end{gathered} $Здесь ${{c}_{p}}$ – удельная изобарная теплоемкость фазы, Дж/(кг ∙ К); T – температура фазы, К; $\lambda {\text{*}}$ – эффективная теплопроводность фазы, Вт/(м ∙ К); ${{\alpha }_{{sg}}}$ – коэффициент межфазной теплоотдачи, Вт/(м2 ∙ К); ${{A}_{{sg}}}$ – удельная межфазная поверхность, м2/м3; $\Delta {{h}_{{sg}}} = - \Delta h$ – теплота фазового перехода водорода из газообразного состояния в твердое, Дж/кг; $c_{{p,{\text{H}}}}^{{(s)}},$ $c_{{p,{\text{H}}}}^{{(g)}}$ – теплоемкость водорода в газовом и твердофазном состояниях, Дж/(кг ∙ К); $T{\text{*}}$ – температура фазового равновесия при равновесном давлении, К.
Закон сохранения импульса для газовой фазы:
(5)
$\begin{gathered} \frac{{\partial \left( {\varepsilon {{\rho }_{{0,g}}}{{w}_{{g,i}}}} \right)}}{{\partial t}} + \nabla \cdot \left( {\varepsilon {{\rho }_{{0,g}}}{{{\vec {w}}}_{g}}{{w}_{{g,i}}} - \varepsilon \mu _{g}^{*}\nabla {{w}_{{g,i}}}} \right) = \\ = - \varepsilon {{\left( {\nabla p} \right)}_{i}} - \varepsilon \frac{{\mu _{g}^{*}}}{{k'}}{{w}_{{g,i}}},\;\,\,\,i = x,y,z. \\ \end{gathered} $Здесь $\mu _{g}^{*}$ – эффективная динамическая вязкость, Па · с; $k{\kern 1pt} '$ – проницаемость, м2; p – давление, Па.
Плотность смеси рассчитывали по уравнению идеального газа, молекулярную вязкость – по модели Уилки [29], коэффициенты теплопроводности – по модели Масона ‒ Саксена [30]. Эффективную вязкость принимали равной молекулярной вязкости смеси. Объемные и мольные доли компонентов считались равными, а их связь с массовой долей определяли по стандартным соотношениям для идеальной газовой смеси.
Для расчета объемного источника в уравнениях (1)–(4) использовалось соотношение из работы [31]
Пористость сплава LaNi4.8Mn0.3Fe0.1 составляла 0.564, а характерный размер частиц принимался равным 10 мкм [24]. Плотность сплава ‒ 8020 кг/м3, теплоемкость ‒ 420 Дж/(кг ∙ К). Равновесное давление определялось путем аппроксимации экспериментальных данных [32]. Тепловой эффект реакции составлял 34.89 кДж/моль.
Проницаемость системы $k{\kern 1pt} '$ принималась равной 0.254 мкм2. Такое значение проницаемости было получено в работе [33] для перепада давления по высоте реактора 0.4 МПа, что соответствует режиму, принятому в качестве базового в настоящей работе. Проницаемость $k{\kern 1pt} ',$ используемая в уравнении (5), отличается от проницаемости k, приведенной в работе [33] и равной 0.45 мкм2, так как $k{\kern 1pt} ' = k\varepsilon .$ Это связано с различием скоростей (средней в порах и фильтрационной), относительно которых записывается закон фильтрации Дарси.
Эффективная теплопроводность газовой фазы $\lambda _{g}^{*}$ принималась равной теплопроводности смеси ${{\lambda }_{{mix}}},$ а $\lambda _{s}^{*}$ рассчитывалась из условия выполнения локального однотемпературного приближения [27]:
Учет кнудсеновских эффектов при выбранном рабочем давлении приводит к снижению эффективной теплопроводности примерно на 3%, поэтому данные эффекты не учитывались. Таким образом,
Межфазный теплообмен характеризовался постоянным значением числа Нуссельта [35], что практически не сказывалось на результатах расчета. При моделировании разность температур фаз не превышала 0.1 К.
Коэффициент диффузии вычислялся по соотношению из [36]:
При определении эффективного коэффициента диффузии принималась во внимание извилистость τ пористой среды (уменьшение проходного сечения учитывалось в уравнениях сохранения):
(6)
$D* = \tau D = {{\varepsilon }^{{{1 \mathord{\left/ {\vphantom {1 3}} \right. \kern-0em} 3}}}}D.$Для оценки извилистости τ использовались рекомендации [37].
Для области, занятой стенкой и ребрами, использовались уравнения для твердой фазы, которые получались из ранее представленной системы путем приравнивания пористости нулю и зануления массовых источников, при этом эффективные свойства заменялись на свойства металлов, из которых были изготовлены стенка и ребра (табл. 1).
Таблица 1.
Свойства материалов, из которых изготовлены стенки и ребра реактора [38]
Свойство материала | Сталь | Латунь | Медь |
---|---|---|---|
Плотность, кг/м3 | 8055 | 8530 | 8933 |
Теплоемкость, Дж/(кг ∙ К) | 480.0 | 380.0 | 385.0 |
Теплопроводность, Вт/(м · К) | 15.1 | 110.0 | 401.0 |
В качестве граничных условий на входе в систему принимались постоянные давление и состав смеси, на выходе – ее постоянный расход, различный на двух временных участках. С внешней стороны охлаждаемой стенки задавался коэффициент теплоотдачи, а также температура охлаждающей жидкости. Для твердой фазы при z = H (см. рис. 1) задавались адиабатные граничные условия, что соответствовало низким коэффициентам теплопроводности в немоделируемом свободном объеме над металлогидридной засыпкой. Считалось, что газовая фаза поступает в расчетную область с температурой равной температуре охлаждающей жидкости. Начальная температура во всей расчетной области была равна температуре охлаждающей жидкости.
При моделировании варианта реактора очистки без оребрения (см. рис. 1, б) использовалась двумерная постановка задачи ввиду осевой симметрии процессов в исследуемой конструкции. При моделировании варианта с оребрением (см. рис. 1, в) рассматривался вырезанный по радиусам сектор с половиной ребра по толщине, на боковых границах которого задавались условия симметрии. Моделирование проводилось с использованием структурной сетки в цилиндрических координатах. Все расчеты были выполнены с помощью CFD-кода ANES [39].
ВЫБОР РАСЧЕТНОЙ СЕТКИ И ВЕРИФИКАЦИЯ МАТЕМАТИЧЕСКОЙ МОДЕЛИ
На рис. 2 представлены зависимости объемной доли водорода на выходе из реактора от времени, полученные при использовании трех различных сеток (табл. 2). Часть параметров [число контрольных объемов (КО) по радиусу засыпки и число КО по высоте] была выбрана при проведении аналогичных расчетов в двумерной осесимметричной постановке. На рис. 2 приведены данные для промежутка времени от 60 до 70 мин, в течение которого при использовании разных сеток различия в результатах расчета объемной доли водорода (потери водорода) на выходе из реактора ${{r}_{{{{{\text{H}}}_{2}}}}}$ достигают максимальных значений. Расчеты проводились для варианта с восемью стальными ребрами.
Рис. 2.
Зависимости объемной доли водорода на выходе из реактора от времени. Номера кривых соответствуют номерам сеток
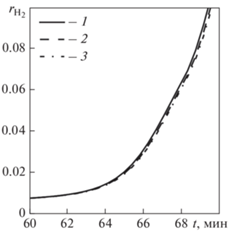
Таблица 2.
Параметры расчетных сеток
Сетка | Число контрольных объемов | ||||
---|---|---|---|---|---|
по радиусу для стенки | по радиусу для засыпки | по углу для засыпки | по углу для ребра | по высоте | |
№ 1 | 2 | 10 | 3 | 2 | 50 |
№ 2 | 3 | 10 | 5 | 3 | 50 |
№ 3 | 4 | 10 | 7 | 4 | 50 |
На рис. 2 видно, что независимость результатов от сетки достигается уже при использовании сетки № 2, поэтому она и была выбрана для проведения всех дальнейших расчетов.
Для верификации модели привлекались экспериментальные данные, приведенные в работе [24]. При этом было важно определить влияние параметров, значения которых невозможно получить из описания экспериментального исследования. Для этого было выполнено несколько вариационных расчетов. Определить точно условия охлаждения было затруднительно ввиду наличия льда в охлаждающей жидкости. Оценки показали, что верхняя и нижняя границы коэффициентов теплоотдачи составляют 100 и 300 Вт/(м2 ∙ К) соответственно. В базовом расчете коэффициент теплоотдачи принимался равным 100 Вт/(м2 ∙ К).
Еще одним важным параметром является расход смеси на входе в систему. Расходы неабсорбируемой примеси, рассчитанные по данным о ее составе и показаниям расходомеров, установленных на входе в установку и на выходе из нее [24], различались до 10%. В базовом варианте расчетов использовалось среднее значение расхода смеси на выходе по данным расходомеров, размещенных на входе в реактор и выходе из него. Для оценки влияния расхода на результаты расчета были проведены два дополнительных расчета, в которых расход смеси на входе в систему задавался с использованием оценок, основанных на экспериментальных данных о расходах и составе смеси на входе в реактор или на выходе из него. Были проведены также расчеты с проницаемостью, увеличенной и уменьшенной на 50% относительно выбранного значения (0.254 мкм2).
Важным параметром, в значительной степени влияющим на эффективный коэффициент диффузии, является извилистость. Были проведены расчеты с извилистостью 0.1, 0.5 и 1.0. Основные расчеты выполнялись с коэффициентом диффузии, рассчитанным по формуле (6).
В табл. 3 представлены данные о чувствительности результатов расчета к варьированию различных входных параметров, требуемых для замыкания математической модели. Параметром для сравнения служило время, при котором объемная доля водорода на выходе из реактора начинает резко возрастать и достигает 3% (начало “прорыва” водорода).
Таблица 3.
Значения времени, при котором объемная доля водорода на выходе из реактора начинает резко возрастать и достигает 3% (результаты вариационных расчетов)
Параметр | Время, с | Отклонение от базового значения, % |
---|---|---|
Эксперимент [24] | 2817 | 0 |
Базовый вариант | 2908 | +3.2 |
Варьирование коэффициента теплоотдачи [базовое значение 100 Вт/(м2 ∙ К)] | ||
α = 200 Вт/(м2 ∙ К) | 3203 | +13.7 |
α = 300 Вт/(м2 ∙ К) | 3300 | +17.2 |
Варьирование расхода смеси (базовое значение – среднее между оценками по показаниям расходомеров на входе в реактор и выходе из него) | ||
Расход смеси, определяемый по показаниям расходомеров и составу смеси, дм3/мин: | ||
на входе | 2963 | +5.2 |
на выходе | 2857 | +1.4 |
Варьирование проницаемости (базовое значение 0.254 мкм2) | ||
k = 0.353 мкм2 | 3001 | +6.5 |
k = 0.127 мкм2 | 2482 | ‒11.9 |
Варьирование извилистости (базовое значение τ = ε1/3) | ||
$\tau $ = 0.1 | 2489 | ‒11.6 |
$\tau $ = 0.5 | 2850 | +1.2 |
$\tau $ = 1.0 | 2915 | +3.5 |
Исходя из полученных результатов, выбранные параметры для базового расчета можно считать вполне корректными (отклонение 3.2%). Из-за неопределенностей в экспериментальных данных подобрать более точные параметры не представляется возможным. На рис. 3 приводятся результаты верификационных расчетов для варианта конструкции реактора без внутреннего оребрения.
Рис. 3.
Зависимость объемной доли водорода на выходе из реактора без оребрения от времени. 1 – расчет; 2 – эксперимент [24]
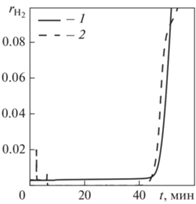
В целом полученные данные дают основания утверждать, что предлагаемая модель позволяет предсказывать характеристики проточного реактора очистки водорода с хорошей точностью.
РЕЗУЛЬТАТЫ МОДЕЛИРОВАНИЯ
Выполнено моделирование процессов в конструкции реактора с восемью стальными ребрами (см. рис. 1, в). На рис. 4 для реактора с оребрением и без него представлены временные зависимости среднеобъемной доли прореагировавшего сплава Xmean и коэффициента извлечения водорода, а также зависимости объемной доли водорода в потоке на выходе из реактора от доли прореагировавшего сплава и объема сорбированного водорода.
Рис. 4.
Зависимости доли прореагировавшего сплава (а) и коэффициента извлечения водорода (б) от времени, потери на выходе из реактора от доли прореагировавшего сплава (в) и от объема поглощенного водорода (г). 1 – реактор без оребрения; 2 – реактор с восемью стальными ребрами

Использование ребер в металлогидридном реакторе приводит к увеличению времени, при котором потери водорода на выходе из реактора начинают резко расти, а коэффициент извлечения ω – падать. При этом количество поглощаемого водорода до начала его значительных потерь на выходе для реактора с внутренним оребрением по сравнению с неоребренной конструкцией увеличивается на 40% – c 125 до 175 дм3. Доли прореагировавшего сплава в обоих вариантах реактора до момента времени примерно 50 мин (соответствует началу потерь в реакторе без ребер) совпадают, так как их рост полностью определяется расходом и составом смеси на входе в систему.
На рис. 5 представлены поля температуры в центральных по высоте засыпки горизонтальных сечениях реактора для конструкции без ребер и конструкции с восемью ребрами. Моменты времени соответствуют максимальному разогреву реактора в данном сечении. Распределение температуры в ребрах близко к одномерному. Даже стальные ребра позволяют организовать эффективный отвод тепла из засыпки и сделать распределение температур более равномерным.
Рис. 5.
Поля температуры в центральных сечениях по высоте засыпки в момент наибольшего разогрева. а ‒ реактор без оребрения; б – реактор с восемью стальными ребрами
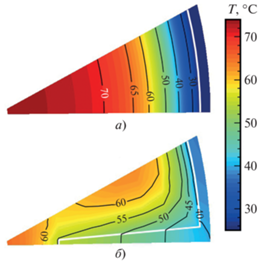
На рис. 6 приведены одномерные распределения температуры и доли прореагировавшего сплава по высоте реактора, осредненные по сечению для реакторов двух конструкций для момента времени 50 мин. Рисунок 6, а показывает, что при наличии ребер область значительного разогрева по высоте имеет меньшую протяженность. Благодаря лучшему отводу тепла в оребренном реакторе сплав реагирует более эффективно и протяженность области, в которой происходит активная сорбция водорода, снижается (см. рис. 6, б). Следует отметить, что “узкий” и “горизонтально” формирующийся фронт реакции является весьма важным обстоятельством. Подобный фронт исключает “прорыв” водорода у холодных стенок реактора в то время, когда в центральной части засыпки сорбирующий сплав далек от насыщения водородом.
Рис. 6.
Одномерные распределения осредненных по сечению температуры (а) и доли прореагировавшего сплава (б) по высоте реактора в момент времени t = 50 мин. 1 – реактор без оребрения; 2 – реактор с восемью стальными ребрами
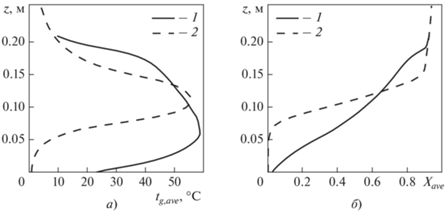
Проведен анализ влияния числа ребер на эффективность системы. Расчеты выполнены для трех вариантов с 4, 8 и 16 ребрами, при этом объем, занятый ребрами, оставался постоянным. Для трех указанных вариантов ребра различались только толщиной у основания, которая равнялась 8, 4 и 2 мм соответственно.
На рис. 7 представлена зависимость потерь водорода на выходе из реактора от объема поглощенного водорода для реакторов с 4, 8 и 16 стальными ребрами. Видно, что при уменьшении расстояния между ребрами в исследованных пределах эффективность очистки водорода повышается незначительно. Повышение эффективности связано с падением термического сопротивления между засыпкой и поверхностью ребер из-за сокращения расстояния между ними. При использовании 16 ребер количество поглощенного водорода (до момента резкого роста потерь) увеличивается на 5% по сравнению с вариантом с четырьмя ребрами и на 1% по сравнению с вариантом с восемью ребрами.
Рис. 7.
Зависимость потерь на выходе из реактора от объема поглощенного водорода. Количество ребер в реакторе: 1 – 0; 2 –4; 3 –8; 4 ‒ 16
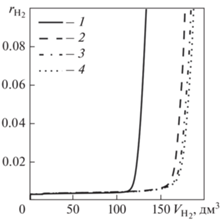
Для анализа влияния материала ребер на эффективность работы металлогидридной системы были исследованы различные материалы: сталь, латунь и медь. Цилиндрическая стенка реактора при этом считалась выполненной из стали, ее термическое сопротивление равнялось 1.28 × 10–4 м2 ∙ К/Вт, что существенно меньше, чем термическое сопротивление при теплоотдаче от стенки к охлаждающей жидкости. Свойства материалов, из которых изготовлялись ребра, представлены в табл. 1. Далее приводятся результаты моделирования только для конструкции с восемью ребрами, так как ранее было показано, что изменение количества ребер при сохранении занимаемого ими объема не приводит к существенному изменению характеристик системы очистки.
Для каждого варианта выполнялась дополнительная серия расчетов с целью оценить влияние параметров внешнего охлаждения на процесс очистки водорода. Это связано с тем, что при уменьшении внутреннего термического сопротивления из-за наличия внутреннего оребрения влияние условий внешнего охлаждения существенно возрастает. Эта особенность иллюстрируется рис. 8, на котором представлено распределение по высоте реактора безразмерной температуры θ, рассчитанной по формуле
где ${{T}_{{w,ave}}}$ – средняя температура твердой непроницаемой фазы в данном сечении (стенка или стенка и ребра).Рис. 8.
Изменение безразмерной температуры θ по высоте реактора при коэффициенте теплоотдачи на внешней поверхности стенки реактора 100 Вт/(м2 ∙ К). 1 – реактор без оребрения; 2 – реактор с восемью стальными ребрами

В расчетах, результаты которых приведены на рис. 8, значение коэффициента теплоотдачи на внешней поверхности стенки реактора принято равным 100 Вт/(м2 ∙ К).
На рисунке видно, что безразмерная температура непроницаемой твердой фазы приближается к единице, т.е. основное термическое сопротивление обусловлено теплопередачей от стенки к охлаждающей жидкости. При этом для варианта без ребер термические сопротивления от засыпки к стенке и от стенки к охлаждающей жидкости примерно равны.
Для наглядной иллюстрации влияния на работу металлогидридного реактора материала ребер и условий внешнего охлаждения было выполнено моделирование процесса сорбции водорода в реакторе с внутренним оребрением, в котором температура внутри ребер и стенки задавалась равной температуре охлаждающей среды. По сути данный вариант соответствовал идеализированному реактору, в котором ребра выполнены из материала с бесконечно большой теплопроводностью, а охлаждение внешней стенки реактора обусловлено бесконечно большим коэффициентом теплоотдачи.
На рис. 9 представлено отношение количества сорбированного водорода до начала значительных потерь водорода на выходе из реактора к количеству водорода, поглощенному в идеализированном реакторе. Видно, что основное увеличение коэффициента теплоотдачи со 100 до 500 Вт/(м2 ∙ К) приводит к существенному росту количества водорода, сорбируемого до начала потерь, тогда как увеличение значения коэффициента выше 1000 Вт/(м2 ∙ К) нецелесообразно.
Рис. 9.
Отношение количества сорбированного водорода до начала потерь в реакторе с восемью ребрами к количеству водорода, поглощенному в идеализированном реакторе с таким же числом ребер. Материал ребер: 1 – сталь; 2 – латунь; 3 – медь
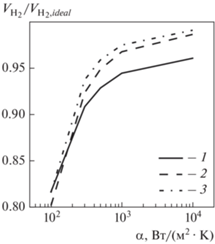
Результаты, полученные для латунных и медных ребер, практически не различаются, при этом указанные материалы обеспечивают значительный выигрыш по сравнению со стальными ребрами. Это преимущество увеличивается с ростом коэффициента теплоотдачи. Следует отметить, что при низком коэффициенте теплоотдачи на внешней стенке, равном 100 Вт/(м2 ∙ К), стальные ребра, как это ни странно, оказываются несколько эффективней. Причина заключается в том, что благодаря высокой осевой теплопроводности латунных и медных ребер происходит небольшой разогрев всего объема засыпки (на 5‒7°С), что приводит к повышению равновесного давления и, как следствие, повышению значения давления, до которого может опуститься парциальное давление водорода. Если считать за момент “прорыва” водорода момент времени, при котором объемная доля водорода на выходе достигнет 10%, то более эффективными окажутся медные и латунные ребра.
Анализ результатов показал, что распределение водорода по высоте реактора для всех рассмотренных режимов описывается следующей зависимостью:
(7)
${{r}_{{{{{\text{H}}}_{2}},ave}}} = {{r}_{{{{{\text{H}}}_{2}},in}}} - \frac{{{{r}_{{{{{\text{H}}}_{2}},in}}}}}{{1 + \exp \left[ {{{4\left( {z - {{z}_{0}}} \right)} \mathord{\left/ {\vphantom {{4\left( {z - {{z}_{0}}} \right)} {\Delta l}}} \right. \kern-0em} {\Delta l}}} \right]}},$На рис. 10 представлен пример распределения двух характерных зависимостей осредненной по сечению реактора объемной доли водорода ${{r}_{{{{{\text{H}}}_{2}},ave}}}$ по высоте реактора ${z \mathord{\left/ {\vphantom {z H}} \right. \kern-0em} H}$ для варианта без ребер и варианта со стальными ребрами и коэффициентом теплоотдачи на внешней стенке, равным 100 Вт/(м2 ∙ К). Видно, что кривые аппроксимации профилей довольно хорошо описывают резкий профиль при наличии внутреннего оребрения. Совпадение результатов расчета с аппроксимирующей кривой для реактора без внутреннего оребрения хуже, чем для реактора с оребрением, но также удовлетворительно воспроизводит распределение водорода по высоте реактора. Характерный линейный масштаб фронта реакции $\Delta l$ при наличии оребрения существенно снижается.
Рис. 10.
Профили осредненной по сечению реактора объемной доли водорода на выходе из реактора без ребер (а) и реактора со стальными ребрами (б); коэффициент теплоотдачи равен 100 Вт/(м2 ∙ К). 1 – результаты расчета; 2 – аппроксимация
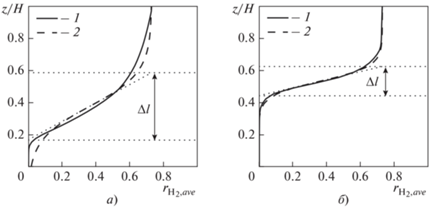
На рис. 11 данная динамика представлена более наглядно в виде зависимости $L(t) = H - {{z}_{0}}(t)$ (L – расстояние от входа в засыпку), при этом ширина закрашенной области соответствует $\Delta l(t).$ По мере продвижения фронта вдоль засыпки ширина фронта растет из-за снижения давления вследствие необходимости фильтрации практически всего расхода смеси к фронту через всё больший слой засыпки.
Рис. 11.
Зависимость отношения расстояния фронта от входа в засыпку к длине реактора от времени. Ширина закрашенной области соответствует $\Delta l(t).$ Реактор: 1 – без ребер; 2 – со стальными ребрами; 3 – идеализированный
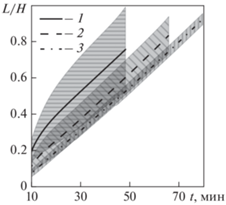
Для стальных и медных ребер была определена ширина фронта перед началом потерь водорода для различных значений коэффициента теплоотдачи. На рис. 12 представлена зависимость отношения полученных значений ширины фронта к ширине фронта для варианта конструкции без ребер (0.10 м) от коэффициента теплоотдачи. На рис. 12 это отношение обозначено как $l{\kern 1pt} '.$
Рис. 12.
Зависимость отношения $l{\kern 1pt} '$ от коэффициента теплоотдачи на внешней стенке реактора. Материал ребер: 1 – сталь; 2 – медь
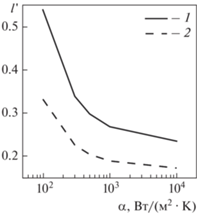
На рисунке видно, что даже для значения коэффициента теплоотдачи равного 100 Вт/(м2 ∙ К) ширина фронта снижается в 2‒3 раза при использовании внутреннего оребрения. Увеличение коэффициента теплоотдачи более 1000 Вт/(м2 ∙ К) практически не сказывается на ширине фронта. Как было отмечено ранее, при уменьшении характерной ширины фронта в несколько раз количество сорбируемого водорода при снижении внутреннего термического сопротивления растет не так значительно (см. рис. 9), так как время начала потерь определяется величиной $L + {{\Delta l} \mathord{\left/ {\vphantom {{\Delta l} 2}} \right. \kern-0em} 2}.$ Изменение термического сопротивления существенно сказывается только на втором слагаемом, в то время как первое слагаемое зависит лишь от общего расхода водорода в смеси, подаваемой в систему.
Для определения возможности увеличения скорости зарядки реактора благодаря повышению расхода водорода на входе была выполнена серия расчетов. В качестве конструкции для моделирования был выбран реактор с восемью стальными ребрами и коэффициентом теплоотдачи равным 500 Вт/(м2 ∙ К). Расход смеси ${{G}_{{in}}}$ увеличивался на 10, 20, 50% по сравнению с базовым значением ${{G}_{{in,base}}},$ а состав смеси оставался прежним.
На рис. 13 показано изменение отношения количества сорбированного водорода до начала значительных потерь ${{V}_{{{{{\text{H}}}_{2}}}}}$ к количеству водорода, поглощенному в исходном варианте реактора ${{V}_{{{{{\text{H}}}_{2}},base}}}$ [реактор без оребрения, коэффициент теплоотдачи равен 100 Вт/(м2 ∙ К)]. Видно, что незначительное повышение расхода смеси, а значит, и водорода допустимо и не приводит к резкому падению эффективности системы. Однако важно понимать, что существенное увеличение расхода смеси приведет к большим перепадам давления по высоте реактора (рис. 14) и сокращению количества сорбируемого водорода до начала потерь.
Рис. 13.
Зависимость отношения количества сорбированного водорода до начала потерь к количеству водорода, поглощенному в реакторе с базовым расходом, от расхода смеси на входе в реактор
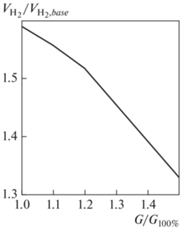
Рис. 14.
Зависимость перепада давления по высоте реактора от времени при изменении расхода газовой смеси по сравнению с базовым значением. ${{{{G}_{{in}}}} \mathord{\left/ {\vphantom {{{{G}_{{in}}}} {{{G}_{{in,base}}}}}} \right. \kern-0em} {{{G}_{{in,base}}}}}{\kern 1pt} {\text{:}}$ 1 – 1.0; 2 – 1.1; 3 – 1.2; 4 – 1.5
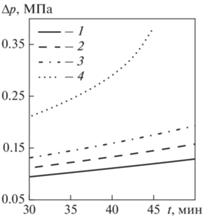
Выбор оптимального расхода смеси зависит от целей, которые стоят перед проектировщиками металлогидридных систем очистки водорода. В одном случае важным является сокращение количества циклов зарядки/разрядки реактора при сохранении прежней средней производительности системы (расхода водорода на входе). Например, в [40] даются похожие рекомендации по уменьшению количества циклов зарядки/разрядки для систем компримирования водорода. Для рассматриваемой в работе конструкции реактора благодаря установке восьми стальных ребер и повышению коэффициента теплоотдачи к охлаждающей воде до 500 Вт/(м2 ∙ К) количество сорбируемого водорода увеличилось за один цикл почти на 60%. В другом случае необходимо повысить среднюю производительность системы (увеличить расход водорода). Такая же конструкция реактора позволяет повысить расход смеси, а значит, и водорода на 50%, при этом количество сорбируемого за цикл водорода возрастет на 30%.
В заключение следует отметить, что часто используемое в литературе [18, 41] нереалистичное значение проницаемости засыпки, равное 10‒8 м2, не позволяет предсказать столь сильную зависимость характеристик системы от расхода смеси на входе в реактор.
ВЫВОДЫ
1. Разработанная и верифицированная математическая модель может быть рекомендована для использования при оптимизации металлогидридных систем очистки водорода различного назначения.
2. Процесс сорбции имеет вид фронта, распространяющегося от входа в реактор к выходу из него, при этом скорость движения фронта практически не зависит от условий охлаждения и определяется входным расходом смеси. Протяженность области, в которой объемная доля водорода падает от значения на входе до нулевого, и положение фронта относительно горизонтали в значительной степени определяются условиями охлаждения.
3. Для рассмотренной в настоящей работе конструкции реактора без внутреннего оребрения протяженность фронта сопоставима с высотой засыпки.
4. Установка ребер внутри металлогидридной засыпки обеспечивает значительное повышение эффективности проточного металлогидридного реактора очистки водорода. Для рассмотренной в работе конструкции при установке восьми латунных ребер и повышении коэффициента теплоотдачи к охлаждающей жидкости до 500 Вт/(м2 ∙ К) до начала потерь обеспечивается сорбция на 60% большего количества водорода, чем в реакторе без оребрения. При оребрении из латуни удается сорбировать на 4‒5% большее количество водорода, чем при оребрении из стали. В идеализированном реакторе с ребрами из материала с бесконечной теплопроводностью и бесконечно большим коэффициентом теплоотдачи к охлаждающей среде сорбируется водорода всего на 5% больше, чем в реакторе с восемью латунными ребрами.
5. Перепад давления между входом в реактор и выходом из него является важной характеристикой, существенно влияющей на эффективность системы очистки. Установка ребер и надлежаще выбранные условия внешнего охлаждения в значительной степени компенсируют негативное влияние роста перепада давления при увеличении расхода смеси на входе. Для рассматриваемой в данной работе конструкции реактора установка восьми стальных ребер и повышение коэффициента теплоотдачи к охлаждающей воде до 500 Вт/(м2 ∙ К) позволяют увеличить расход смеси, а значит, и водорода на 50%, при этом количество сорбируемого за цикл водорода увеличится на 30% по сравнению с первоначальной конструкцией реактора.
6. При моделировании крупномасштабных систем хранения водорода следует опираться на экспериментальные данные о проницаемости металлогидридной засыпки. Часто используемые в литературе нереалистичные значения проницаемости засыпки (примерно 10‒8 м2) не позволяют предсказывать существенную зависимость характеристик системы очистки от расхода водорода на входе в реактор.
Список литературы
Hydrogen direct adsorptive separation: Development status and trends / P. Hao, S. Li, S. Li, Y. Shi, N. Cai // Energy Fuels. 2020. V. 34. Is. 12. P. 15126–15140. https://doi.org/10.1021/acs.energyfuels.0c02317
Saitou T., Sugiyama K. Hydrogen purification with metal hydride sintered pellets using pressure swing adsorption method // J. Alloys Compd. 1995. V. 231. Is. 1–2. P. 865–870. https://doi.org/10.1016/0925-8388(95)01774-7
Rudman P.S., Sandrock G.D., Goodell P.D. Hydrogen separation from gas mixtures using LaNi5 pellets // J. Less-Common Met. 1983. V. 89. Is. 2. P. 437–446. https://doi.org/10.1016/0022-5088(83)90354-5
Hydrogen separation from mixed gas streams using reversible metal hydrides / J.J. Sheridan, F.G. Eisenberg, E.J. Greskovich, G.D. Sandrock, E.L. Huston // J. Less-Common Met. 1983. V. 89. Is. 2. P. 447–455. https://doi.org/10.1016/0022-5088(83)90355-7
The recovery, purification, storage and transport of hydrogen separated from industrial purge gas by means of mobile hydride containers / M. Au, C. Chen, Z. Ye, T. Fang, J. Wu, O. Wang // Int. J. Hydrogen Energy. 1996. V. 21. Is. 1. P. 33–37. https://doi.org/10.1016/0360-3199(95)00044-E
Металлогидридная технология очистки водорода для водородоохлаждаемых турбогенераторов / В.И. Борзенко, Д.О. Дуников, С.П. Малышенко, Л.И. Чубараева // Изв. РАН. Энергетика. 2012. № 3. С. 151‒166.
Takeda H. The development of the application systems using hydrogen absorbing alloys // J. Adv. Sci. 1998. V. 10. Is 4. P. 227–231. https://doi.org/10.2978/jsas.10.4_227
Biohydrogen purification using metal hydride technologies / D. Dunikov, V. Borzenko, D. Blinov, A. Kazakov, C.-Y. Lin, S.-Y. Wu, C.-Y. Chu // Int. J. Hydrogen Energy. 2016. V. 41. Is. 46. P. 21787–21794. https://doi.org/10.1016/j.ijhydene.2016.08.190
Blinov D.V., Borzenko V.I., Kazakov A.N. Metal hydride flow-through hydrogen purification method for renewable energy production and storage // Proc. of the Intern. Multi-Conference on Industrial Engineering and Modern Technologies (FarEastCon-2018). IEEE. Russia, Vladivostok, 2‒4 Oct. 2018.
Перспективные металлогидридные технологии хранения и очистки водорода / Д.В. Блинов, В.И. Борзенко, А.В. Бездудный, Н.В. Кулешов // Изв. вузов. Проблемы энергетики. 2021. Т. 23. № 2. С. 149‒160. https://doi.org/10.30724/1998-9903-2021-23-2-149-160
Dunikov D., Blinov D. Extraction of hydrogen from a lean mixture with methane by metal hydride // Int. J. Hydrogen Energy. 2020. V. 45. Is. 16. P. 9914–9926. https://doi.org/10.1016/j.ijhydene.2020.01.201
High purity hydrogen production by metal hydride system: A parametric study based on the lumped parameter model / K.A.J. Koua, L. Tong, T. Yang, J. Xiao // J. Wuhan Univ. Technol. Sci. Ed. 2021. V. 36. Is. 1. P. 127–135. https://doi.org/10.1007/s11595-021-2385-y
Poisoning-tolerant metal hydride materials and their application for hydrogen separation from CO2/CO containing gas mixtures / K.D. Modibane, M. Williams, M. Lototskyy, M.W. Davids, Y. Klochko, B.G. Pollet // Int. J. Hydrogen Energy. 2013. V. 38. Is. 23. P. 9800–9810. https://doi.org/10.1016/j.ijhydene.2013.05.102
Nguyen H.Q., Shabani B. Review of metal hydride hydrogen storage thermal management for use in the fuel cell systems // Int. J. Hydrogen Energy. 2021. V. 46. Is. 62. P. 31699–31726. https://doi.org/10.1016/j.ijhydene.2021.07.057
Keshari V., Maiya P.M. Numerical study of solid state hydrogen storage system with finned tube heat exchanger // Heat Transfer. Eng. 2020. V. 41. Is. 6–7. P. 484–496. https://doi.org/10.1080/01457632.2018.1546661
Gkanas E.I., Statheros T., Khzouz M. Heat management on rectangular metal hydride tanks for green building applications // Int. J. Hydrogen Energy. 2019. V. 44. Is. 35. P. 19267–19274. https://doi.org/10.1016/j.ijhydene.2018.06.030
Gkanas E.I., Khzouz M. Study on the hydrogenation of an Mm-based AB5-intermetallic for sustainable building applications // Int. J. Energy Res. 2019. V. 43. Is. 14. P. 8033‒8048. https://doi.org/10.1002/er.4794
Hydrogen absorption performance of a novel cylindrical MH reactor with combined loop-type finned tube and cooling jacket heat exchanger / X.-S. Bai, W.-W. Yang, W.-Y. Zhang, F.-S. Yang, X.-Y. Tang // Int. J. Hydrogen Energy. 2020. V. 45. No. 52. P. 28100–28115. https://doi.org/10.1016/j.ijhydene.2020.04.209
Modeling and numerical simulation of a 5 kg LaNi5-based hydrogen storage reactor with internal conical fins / S. Chandra, P. Sharma, P. Muthukumar, S.S.V. Tatiparti // Int. J. Hydrogen Energy. 2020. V. 45. Is. 15. P. 8794–8809. https://doi.org/10.1016/j.ijhydene.2020.01.115
Эффективность оребрения активного объема металлогидридного реактора / О.В. Боровских, Д.О. Лазарев, Г.Г. Яньков, В.И. Артемов // Теплоэнергетика. 2009. № 3. С. 53‒56.
Elhamshri F.A.M., Kayfeci M. Enhancement of hydrogen charging in metal hydride-based storage systems using heat pipe // Int. J. Hydrogen Energy. 2019. V. 44. Is. 34. P. 18927–18938. https://doi.org/10.1016/j.ijhydene.2018.10.040
Artemov V.I., Minko K.B., Yan’kov G.G. Numerical study of heat and mass transfer processes in a metal hydride reactor for hydrogen purification // Int. J. Hydrogen Energy. 2016. V. 41. Is. 23. P. 9762–9768. https://doi.org/10.1016/j.ijhydene.2016.01.124
Enhancement of heat- and mass-transfer processes in a metal-hydride flow-through hydrogen-purification reactor / M.D. Nashchekin, M.V. Minko, S.B. Morgunova, K.B. Minko // Int. J. Hydrogen Energy. 2020. V. 45. Is. 46. P. 25013–25029. https://doi.org/10.1016/j.ijhydene.2020.06.233
Очистка водорода методом продувки через металлогидрид / Д.В. Блинов, В.И. Борзенко, Д.О. Дуников, С.П. Малышенко // Вестник МЭИ. 2012. № 2. С. 44‒49.
Блинов Д.В. Исследование тепловых процессов в системах твердофазного аккумулирования и очистки водорода: дис. … канд. техн. наук. М.: НИУ МЭИ, 2016.
Nashchekin M.D., Minko K.B., Artemov V.I. Numerical analysis of constructive and regime parameter effects on the efficiency of metal hydride systems for hydrogen purification // Case Stud. Therm. Eng. 2019. V. 14. P. 100485. https://doi.org/10.1016/j.csite.2019.100485
Minko K.B., Artemov V.I., Yan’kov G.G. Numerical simulation of sorption/desorption processes in metal-hydride systems for hydrogen storage and purification. Part I: Development of a mathematical model // Int. J. Heat Mass Transfer. 2014. V. 68. P. 683–692. https://doi.org/10.1016/j.ijheatmasstransfer.2013.09.056
Numerical and experimental study of heat-and-mass transfer processes in two-stage metal hydride hydrogen compressor / K.B. Minko, M.S. Bocharnikov, Y.B. Yanenko, M.V. Lototskyy, A. Kolesnikov, B.P. Tarasov // Int. J. Hydrogen Energy. 2018. V. 43. Is. 48. P. 21874–21885. https://doi.org/10.1016/j.ijhydene.2018.09.211
Wilke C.R. A viscosity equation for gas mixtures // J. Chem. Phys. 1950. V. 18. Is. 4. P. 517–519. https://doi.org/10.1063/1.1747673
Mason E.A., Saxena S.C. Approximate formula for the thermal conductivity of gas mixtures // Phys. Fluids. 1958. V. 1. Is. 5. P. 361–369. https://doi.org/10.1063/1.1724352
Mayer U., Groll M., Supper W. Heat and mass transfer in metal hydride reaction beds: Experimental and theoretical results // J. Less-Common Met. 1987. V. 131. Is. 1–2. P. 235–244. https://doi.org/10.1016/0022-5088(87)90523-6
Малышенко С.П., Романов И.А. Особенности процессов сорбции-десорбции водорода в металлогидридных системах различного масштаба // Матер. XVIII Школы-семинара молодых ученых и специалистов под руководством акад. РАН А.И. Леонть-ева. Москва, 23‒27 мая 2011 г.
Блинов Д. В., Дуников Д.О., Казаков А.Н. Экспериментальное определение проницаемости металлогидридной засыпки сплава семейства LaNi5 // ТВТ. 2016. Т. 54. Вып. 1. С. 150‒153. https://doi.org/10.7868/S0040364415060058
Влияние неабсорбируемых газовых примесей на процессы тепломассообмена в металлогидридных устройствах для аккумулирования и очистки водорода / В.И. Артемов, Д.О. Лазарев, Г.Г. Яньков, В.И. Борзенко, Д.О. Дуников, С.П. Малышенко // ТВТ. 2004. Т. 42. Вып. 6. С. 972‒979.
Минко К.Б. Моделирование процессов сорбции/десорбции водорода в твердофазных системах хранения и очистки водорода: дис. … канд. техн. наук. М.: НИУ МЭИ, 2016.
Варгафтик Н.Б. Справочник по теплофизическим свойствам газов и жидкостей. 3-е изд., стер. и испр. М.: Старс, 2006. [Перепечатка со 2-го изд., 1972 г.]
Ho C.K., Webb S.W. Gas transport in porous media. Springer, 2006.
Fundamentals of heat and mass transfer / T.L. Bergman, A.S. Lavine, F.P. Incropera, D.P. DeWitt. John Wiley & Sons, 2011.
Код ANES. [Электрон. ресурс.] URL: http://anes.ch12655.tmweb.ru/ (дата обращения: 21.10.2021).
Metal hydride hydrogen compressors for energy storage systems: layout features and results of long-term tests / B.P. Tarasov, M.S. Bocharnikov, Y.B. Yanenko, P.V. Fursikov, K.B. Minko, M.V. Lototskyy // J. Phys. Energy. 2020. V. 2. No. 2. P. 024005. https://doi.org/10.1088/2515-7655/ab6465
Heat and mass transfer during the storage of hydrogen in LaNi5-based metal hydride: 2D simulation results for a large scale, multi-pipes fixed-bed reactor / A. Chibani, S. Merouani, C. Bourgiou, L. Hamadi // Int. J. Heat Mass Transfer. 2020. V. 147. P. 118939. https://doi.org/10.1016/j.ijheatmasstransfer.2019.118939
Дополнительные материалы отсутствуют.
Инструменты
Теплоэнергетика