Теплоэнергетика, 2022, № 2, стр. 56-64
Результаты стендовых испытаний и численного моделирования колебаний ротора с задеваниями в подшипниках с водяной смазкой
В. Ф. Шатохин a, *, Г. В. Голобоков a, О. В. Орлов a
a ПАО “Калужский турбинный завод”
248010 г. Калуга, Московская ул., д. 241, Россия
* E-mail: shatokhin_vf@paoktz.ru
Поступила в редакцию 12.02.2021
После доработки 05.03.2021
Принята к публикации 17.03.2021
- EDN: YMYYJC
- DOI: 10.1134/S0040363622010039
Аннотация
Приведены описания конструкции опорных подшипников скольжения с водяной смазкой и результаты стендовых испытаний ротора турбогенератора, закончившихся повреждением подшипников. Разработан программный модуль для математического моделирования колебаний ротора с задеваниями о подшипник. Выполнено моделирование этого процесса при различных значениях податливости и демпфирования в опорах, коэффициентах трения скольжения в местах задеваний. Существенное внимание уделено возможной опасности перерастания аварии в катастрофическую фазу, определяемую развитием асинхронного обката ротором статорных элементов (статора). Опасность задеваний ротором статора заключается в возникновении сил его контактного взаимодействия со статором, вызывающих самовозбуждающие колебания системы ротор – опоры. Природа этих сил связана с появлением трения скольжения при контакте вращающегося ротора со статором. Силы контактного взаимодействия при задеваниях являются определяющими по сравнению с другими возбуждающими колебания силами. Короткий промежуток времени развития асинхронного обката определяет его взрывной характер. Показано, что увеличение податливости и демпфирования в опорах не способствует развитию опасной для целостности конструкции формы контактного взаимодействия ротора с подшипником – асинхронного обката. При податливых опорах и потерях энергии в демпферных устройствах в процессе колебаний с задеваниями развивается синхронный обкат с силами давления на подшипники, не представляющими опасность для конструкции, пока идет процесс срабатывания системы безопасности установки по превышению допускаемых амплитуд вибрации. В качестве демпферов в опорах выбраны амортизаторы АДП-2400, динамические ударные характеристики которых определены на ударном стенде. При более жестких опорах и отсутствии демпфирования при задеваниях развивается асинхронный обкат ротором подшипника с силами давления на подшипники, опасными для их целостности.
Совершенствование конструкций подшипников и проверка их работоспособности в условиях нагружения, приближенных к реальным, не всегда обеспечивают их нормальную работу в конкретной установке, особенно в случае возможных задеваний ротора о подшипник. На рис. 1 показана схема ротора турбогенератора, установленного в подшипниках на водяной смазке, в [1] приведено теоретическое обоснование такой конструкции. В настоящей работе представлены результаты стендовых испытаний, проведенных для выяснения причин повреждений подшипников.
КОНСТРУКЦИЯ ПОДШИПНИКОВ НА ВОДЯНОЙ СМАЗКЕ
Для испытаний были выбраны подшипники трех вариантов исполнения.
В подшипнике варианта 1 роторная втулка состояла из цилиндрических стержней, связанных металлическим корпусом (рис. 2), вкладыш был выполнен цилиндрическим (рис. 3), пара трения изготовлена из силицированного графита.
В подшипнике варианта 2 на роторе располагалась гладкая цилиндрическая втулка, статор был выполнен из цилиндрических стержней, вставленных в металлический корпус, пара трения была изготовлена из твердого сплава. Конструкция вкладыша показана на рис. 4.
Для увеличения толщины несущего слоя смазки в подшипнике варианта 3 был использован принцип гидростатического взвешивания. “Живучесть” подшипника при понижении давления смазки обеспечивалась конструктивными особенностями, сохраняющими в нем высокие гидродинамические свойства.
Для повышения надежности при работе оборудования применяют специальные комбинированные подшипники, в которых объединены гидростатический и гидродинамический принципы работы. В них, так же как и в гидростатических подшипниках, смазка подается через дроссели в специальные каналы на поверхности скольжения. Между каналами имеются развитые поверхности для создания гидродинамической подъемной силы, которая в сочетании с антифрикционными свойствами трущихся материалов обеспечивает “живучесть” подшипника при снижении давления смазки. Вкладыш выполнен в виде отдельных самоустанавливающихся сегментов. Конструкция подшипника показана на рис. 5. В паре трения роторная втулка выполнена из закаленной нержавеющей стали, на рабочую поверхность сегментов нанесено антифрикционное покрытие толщиной 1 мм.
РЕЗУЛЬТАТЫ СТЕНДОВЫХ ИСПЫТАНИЙ
Ресурсные испытания подшипника варианта 1 были выполнены на стенде при удельной нагрузке 0.95 МПа, скорости скольжения 67.5 м/с в течение 1000 ч. При испытаниях износ поверхностей трения не превысил погрешности измерения.
Из-за наличия в спектре вибрации подшипника дискретных составляющих на частотах, кратных частоте вращения ротора, была проведена проверка подшипника варианта 2. Критическая частота вращения ротора составила около 4000 мин–1 (рис. 6). При испытаниях подшипника в составе изделия на частоте вращения 1895 мин–1 было зафиксировано повышение температуры воды на выходе из подшипника на 8°С в течение 90 с, при этом вибрация увеличилась до 5 мм/с (рис. 7). При ревизии были обнаружены повреждения пары трения и цвета побежалости (рис. 8).
Рис. 6.
Зависимость амплитуды вибрации А подшипников варианта 2 от частоты вращения ротора n. 1, 2 – вертикальное направление подшипников № 1 и 2; 3, 4 – поперечное направление подшипников № 1 и 2
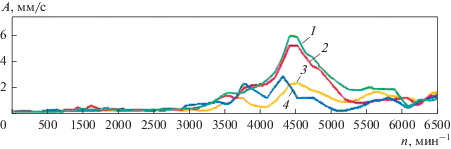
Рис. 7.
Развитие оборотов и вибрации подшипника при инциденте. 1 – частота вращения ротора; 2, 3 – вибрация в вертикальном и поперечном направлении
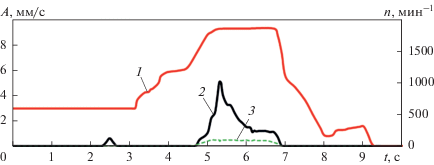
Рис. 8.
Вид рабочей поверхности вкладыша подшипника варианта 2 после инцидента. 1, 3 – ограничительные полукольца; 2 – стержень из твердого сплава; 4 – вкладыш
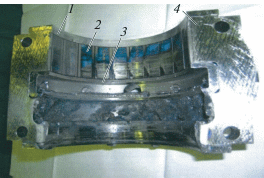
При испытаниях другого изделия с подшипниками варианта 2 на стенде при частоте вращения 1000 мин–1 вибрация составила 0.5 мм/с. При частоте 3300 мин–1 вибрация повысилась до 3–4 мм/с, затем началось самопроизвольное снижение частоты вращения до 2880 мин–1, несмотря на стремление системы регулирования увеличить частоту вращения. Продолжительность короткого выбега ротора составила примерно 17 с. Произошло заклинивание ротора и повреждение втулок и вкладышей обоих подшипников.
Стендовые испытания подшипников варианта 2 закончились их повреждением вследствие контактного взаимодействия вращающегося ротора с подшипником с выделением тепловой энергии трения при задеваниях. Большие амплитуды колебаний и задевания были инициированы неуравновешенным диском муфты, использовавшимся в системе контроля частоты вращения ротора. Обкат с проскальзыванием цапфы ротора о вкладыш подшипника сопровождался выделением тепловой энергии, что привело к нарушению целостности вкладыша и рубашки цапфы ротора.
Результаты стендовых испытаний подшипника варианта 3 замечаний не вызывали. Ротор с диском муфты был отбалансирован до начала испытаний, что исключило причину вибрации с амплитудами колебаний, превышающими допускаемые в системе ротор – опоры. Для сопоставления на рис. 9 приведены зависимости вибрации на корпусе подшипников вариантов 1, 3 в составе изделия от частоты вращения.
МОДЕЛИРОВАНИЕ КОЛЕБАНИЙ РОТОРА С ПОДШИПНИКАМИ ВАРИАНТА 2
Ротор турбины был установлен на двух одинаковых подшипниках скольжения с водяной смазкой. Зазор в подшипнике составлял 0.3 × 10–3 м. Частота вращения ротора, на которой произошло повреждение подшипников, была равна 3300 мин–1 при резонансной (критической) частоте nр = = 4000 мин–1. Резонансный пик на амплитудно-частотной характеристике указывает на существенное демпфирование в системе ротор – опоры. Задевание ротора в подшипниках не сопровождалось контактом ротора с корпусом в проточной части (между опорами), так как зазор между ними заранее был увеличен.
Численное моделирование колебаний ротора с задеваниями о подшипники выполнено в целях исследования процесса контактного взаимодействия ротора со статором, определения вероятности более опасного развития аварии, когда силы контактного взаимодействия в месте задеваний вызывают самовозбуждающиеся колебания ротора и асинхронный обкат ротором статора, который может привести к катастрофическим последствиям для установки в целом. Асинхронный обкат представляет собой самовозбуждающийся процесс движения ротора (прецессию ротора) в направлении, обратном собственному вращению, при появлении трения скольжения в месте задеваний [2]. Если контакт разрывается, сила трения исчезает, возбуждающие обкат силы перестают действовать на ротор, их действие возобновляется при следующем контакте. Таких контактов и разрывов может быть несколько, после чего ротор успокаивается при достаточном демпфировании в системе и незначительной разбалансировке или переходит в безотрывное движение (обкат) по статору [2, 3].
В случае превышения разбалансировки ротора ε допустимого значения εдоп, которое зависит от многих факторов (отстройки от резонанса, демпфирования в системе, жесткости корпуса или опор, трения в месте контакта и т.п.), развивается асинхронный обкат ротором статорных элементов. При ε < εдоп сила трения, как и сила прижатия ротора к статору, оказывается недостаточной и развивается процесс с синхронной прецессией, когда вращающийся ротор проскальзывает, двигаясь в направлении собственного вращения. Такую прецессию поддерживают силы неуравновешенности ротора, инерционная составляющая его внезапной разбалансировки, неконсервативные силы жесткости и демпфирования в пленке скольжения подшипников, неконсервативные составляющие аэродинамических и электродинамических сил в системе ротор – опоры.
В первом приближении повреждение подшипников можно объяснить именно задеваниями, проскальзыванием ротора при синхронном обкате, выделением тепловой энергии в месте контакта. При превышении неуравновешенности ротора (ε > εдоп) и задевании в подшипнике трение скольжения приводит к появлению сил контактного взаимодействия и самовозбуждающимся колебаниям с развитием более опасного явления – асинхронного обката ротором статора, заканчивающегося самоликвидацией установки.
Задевания ротором статора опасны именно развитием асинхронного обката и разрушительными последствиями. Конструкции с вращающимися элементами при колебаниях с задеваниями несут в себе опасность самоликвидации установки в целом за счет энергии собственного вращения ротора вследствие перехода системы в резонансное состояние под действием возбуждающих сил контактного взаимодействия ротора со статором при задеваниях. При развитии обката угловая скорость прецессии ротора возрастает и “подтягивается” до ближайшего резонанса системы ротор – опоры. При этом резонансная частота определяется всеми имеющимися в системе связями, в том числе и возникающей при задеваниях дополнительной связью, налагаемой на систему динамическими свойствами статора в месте контакта. Разрушительные последствия аварии объясняются именно резонансом системы ротор – опоры, к которому приводят силы контактного взаимодействия. Неконсервативные силы контактного взаимодействия ротора со статором по своему характеру аналогичны силам в пленке подшипников скольжения и силам аэродинамического потока в проточной части и уплотнениях турбин, способствующим появлению низкочастотной вибрации роторов и пороговой мощности турбоагрегатов [4]. Различаются они направлением действия: силы контактного взаимодействия вызывают и поддерживают обратную прецессию ротора. Сам процесс развития асинхронного обката занимает короткое время и носит взрывной характер [2, 3]. Самовозбуждающиеся колебания ротора от сил контактного взаимодействия в процессе задеваний несут в себе опасность значительных разрушений катастрофического характера [5]. К примеру, в 1967 г. произошла авария на Новочеркасской ГРЭС, через несколько лет – на Ермаковской электростанции (Казахстан). Аварии в Японии, Англии на турбоагрегатах мощностью 90, 330, 500, 600 МВт подтвердили, что развитие процесса аварии имеет общий характер, подчиняется общим законам, их последствия похожи и подробно описаны в [2]. В работах [6–9] приведены некоторые дополнительные аспекты колебаний с задеваниями.
Моделирование развития контактного взаимодействия исследуемого ротора со статором при задеваниях было выполнено с помощью разработанного программного модуля расчета колебаний роторов с задеваниями о статорные элементы. Алгоритм численного моделирования процесса развития обката ротором подшипника приведен в работах [2, 3, 5, 10], схема контактного взаимодействия ротора со статором показана на рис. 10.
Рис. 10.
Схема контакта ротора с подшипником. 1 – ротор; 2 – подшипник; 3 – элемент, характеризующий жесткость и демпфирование в подшипнике; 4 – статор; О – центр расточки подшипника; О1 – центр сечения ротора; О2 – положение центра масс ротора; ω – угловая скорость вращения ротора; N – реакция опоры; Т – сила трения скольжения; Р – точка контакта ротора с опорой; r – радиус ротора; u – перемещение центра сечения ротора в радиальном направлении; α – угол поворота ротора в момент разбалансировки; ${{\theta }}$ – угол прецессии; F1, F2 – силы со стороны опор ротора; ${{u}_{{10}}} = {{u}_{1}} + {{\varepsilon }}\cos {{\omega }}t;$ ${{u}_{{20}}} = {{u}_{2}} + {{\varepsilon }}\sin {{\omega }}t$
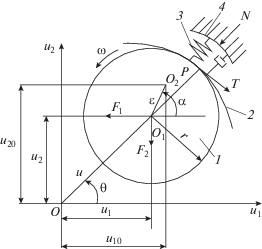
Исходные уравнения движения ротора в пределах зазора с учетом сил, действующих на ротор, могут быть представлены в следующем виде:
при отсутствии задеваний о статорные элементы
(1)
$\left[ M \right]{{\ddot {\bar {u}}}_{{10}}} + \left[ B \right]\dot {\bar {u}} + \left[ K \right]\bar {u} = 0;$при контакте ротора со статором
(2)
$\left[ M \right]{{\ddot {\bar {u}}}_{{10}}} + \left[ B \right]\dot {\bar {u}} + \left[ K \right]\bar {u} + \left[ A \right]\bar {z} = 0,$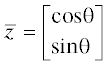
В окончательные уравнения для численного интегрирования входит матрица коэффициентов контактной жесткости [2, 3]
При отсутствии контакта ротора со статором или после разрыва контакта (т.е. когда u < δ) aij = 0.
Попеременное решение уравнений (1), (2) с контролем перемещений ротора и сравнением их с зазором в подшипнике позволяет моделировать процесс колебаний ротора с периодическими задеваниями о подшипник, разрывом контакта и последующим новым контактом. Основное обстоятельство, которое необходимо учитывать при моделировании и интегрировании уравнений (1), (2), – изменение начальных условий в момент времени входа в контакт и выхода из него. Интегрирование выполняется методами Рунге – Кутты. В качестве возбуждающего фактора, вызывающего колебания ротора с последующими задеваниями, была принята внезапная разбалансировка ротора (отрыв массы 0.03068 кг на радиусе 1 м в момент времени t = 0, что составляет 0.0024% массы ротора). Переходные колебания после внезапной разбалансировки начинаются из равновесного положения цапфы ротора в расточке подшипника. При этом, как показали исследования [2, 3, 5, 10], после контакта дальнейшее развитие обката определяется динамическими свойствами колебательной системы ротор – опоры, характером возбуждающих сил и мало зависит от первоначальной причины, вызвавшей задевания. Развитие обката подчиняется законам самовозбуждающихся колебаний системы.
Система ротор – опоры характеризуется следующими показателями: масса ротора составляет 1.301 т, rв = 0.065 м, χ = 0.1–0.5, относительный зазор в подшипнике равен 0.0046. Нелинейная характеристика жесткости опоры вместе с вкладышем подшипника представляется зависимостью сила – деформация с учетом зазора в подшипнике. Неуравновешенность ротора 0.03068 кг на радиусе 1 м обусловлена неуравновешенным диском муфты и смещением на 1 мм его массы по отношению к оси вращения.
Отстройка частоты вращения ротора от резонанса системы ротор – опоры соответствует рекомендациям [4]. Однако и в этих условиях (как показали моделирование и эксперимент) развитие обката возможно в его опасной форме, что определяется жесткостью опор, демпфированием в системе, разбалансировкой ротора. Естественно, условия возникновения опасной формы обката усугубляются при приближении угловой скорости вращения ротора к значению, характерному для резонанса системы. На рис. 11–14 показаны результаты численного моделирования развития колебаний при задеваниях цапфой ротора втулки подшипника и наличии опор разных типов. Штриховой линией показана окружность, представляющая зазор в подшипнике, в пределах которого движение цапфы ротора происходит без задеваний.
Рис. 11.
Траектории движения цапфы в подшипнике при задеваниях в случае податливых опор с потерями в демпферных устройствах при χ = 0.1. t, с: а – 0.30–0.37; б – 0.360–0.388; в – 1.4–1.8
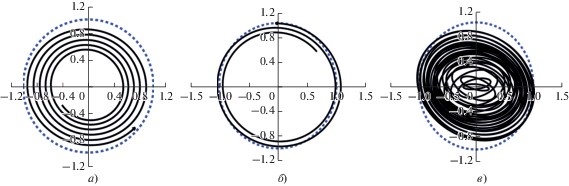
Рис. 12.
Изменение во времени основных характеристик движения ротора при колебаниях с задеваниями его о статор при неуравновешенности 0.03086 кг/м, δ = 0.3 мм, rв = 0.065 м. а – траектория движения ротора при t = 0.360–0.388 с; б – угловая скорость прецессионного движения ротора; в – относительная сила нормального давления на статор (по отношению к массе ротора); г – относительное перемещение ротора (по отношению к зазору); д – скорость ротора относительно статора в точке контакта; е – коэффициент контактной жесткости в месте задеваний; ж – угловая скорость вращения ротора
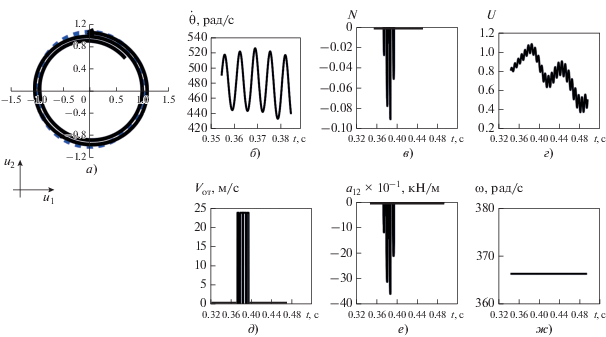
Рис. 13.
Зависимость относительной силы давления на статор от времени в жестких опорах при kст = 0.1 × × 109 кН/м
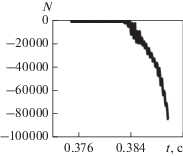
Рис. 14.
Траектории движения цапфы в подшипнике с задеваниями в жестких опорах при kст = 0.1 × 109 кН/м. χ: а – в – 0.5; г – е – 0.1; t, с: а – 0.25–0.36; б, д – 0.370–0.388; в, е – 0.3700–0.3892; г – 0.30–0.38
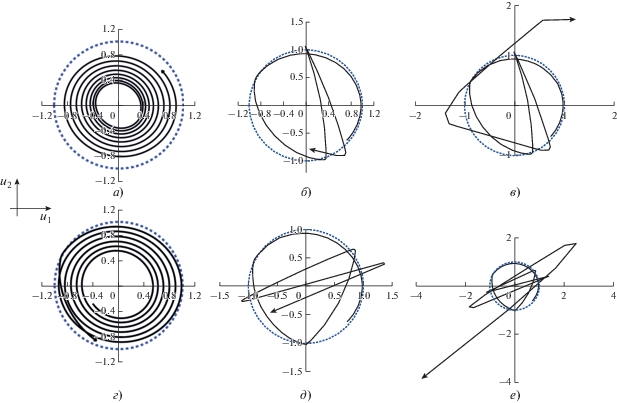
В податливых опорах значение динамической жесткости статора зависит от деформации демпферных устройств с гистерезисной петлей потерь энергии и составляет 0.7 × 105–0.28 × 107 кН/м при δ > 0.3 × 10–3 м. Предполагается, что в опорах по кругу располагаются амортизаторы АДП-2400 (в обойме). В каждый момент времени при задеваниях параметры опоры (жесткость и демпфирование) определяются гистерезисной петлей деформирования амортизатора в точке контакта с ротором. Жесткость опор одинакова в горизонтальном (1) и вертикальном (2) направлениях колебаний. Противоударный амортизатор АДП-2400 разработан при участии авторов, имеет экспериментальные ударные характеристики при разных начальных скоростях нагружения, может применяться для погашения энергии колебаний.
На рис. 11, 12 показаны результаты численного моделирования развития колебаний при задеваниях. Движение ротора сопровождается увеличением амплитуд колебаний с последующим контактом и отскоками (см. рис. 11, а и 12, в) и затуханием колебаний (см. рис. 11, в и 12, г). Относительная скорость ротора в месте контакта практически мало изменяется за время контактов (см. рис. 12, д). Угловая скорость прецессии при задеваниях изменяется в пределах 80 рад/с (см. рис. 12, б). При этом относительная сила нормального давления при задеваниях не превышает одной десятой массы ротора (см. рис. 12, в). В таких условиях тепловая энергия от трения при задеваниях незначительна за время срабатывания системы безопасности. Увеличение разбалансировки в случае податливого статора при наличии гистерезисной петли потерь энергии не приводит к обратной прецессии (асинхронному обкату). Автомат безопасности отключит установку при превышении амплитуд вибрации без существенных нарушений ее целостности.
В относительно жестких опорах (kст = 0.1 × × 109 кН/м) жесткость одинакова в горизонтальном (1) и вертикальном (2) направлениях колебаний при перемещениях ротора с δ > 0.3 × 10–3 м, демпфирование в опорах отсутствует. В более жестких опорах деформация мала, а следовательно, и потери отсутствуют. Относительная сила давления в месте контакта практически мгновенно возрастает до опасных значений с сопутствующими факторами (см. рис. 13). По-видимому, повреждения подшипников рассматриваемого ротора можно объяснить отсутствием потерь при деформировании жестких опор. Характер развития процесса контактного взаимодействия ротора со статором показан на рис. 14, а, б в зависимости от состояния рабочих поверхностей пары трения. Движение ротора сопровождается ударами и отскоками с переходом при t = 0.370–0.388 c к асинхронному обкату ротором подшипника. Сила нормального давления в подшипниках существенно превышает значения, приведенные на рис. 12, в, и опасна для их целостности.
Следует отметить, что слабое звено в виде слоя баббита или другого антифрикционного покрытия в конструкции подшипника (вариант 2) отсутствовало. В случае больших амплитуд вибрации, сравнимых с зазором, контакт вращающегося ротора с опорами происходил непосредственно с жестким телом вкладыша и опоры в целом. Жесткие опоры не способствовали сохранению целостности конструкции при задеваниях. Повреждение подшипников произошло даже при рекомендуемом запасе частоты вращения ротора относительно резонансной вследствие неуравновешенности массы фланца муфты, которая привела к возрастанию амплитуд вынужденных колебаний с увеличением частоты вращения ротора и последующим задеваниям его о втулку подшипника с началом развития синхронного обката.
ВЫВОДЫ
1. Жесткие опоры подшипников скольжения способствуют развитию обката ротором статора с проскальзыванием и выделением тепловой энергии при задеваниях.
2. Увеличение податливости опор и сопротивления скорости смещения (демпфирования в опорах) ротора при задеваниях уменьшает опасность повреждения подшипников при срабатывании автомата безопасности и выходе из резонансной зоны.
3. Неуравновешенность массы фланца муфты ротора приводит к увеличению амплитуд вынужденных колебаний и задеваниям ротора о втулку подшипника с началом развития синхронного обката.
Список литературы
Орлов О.В. Исследование опорных сегментных подшипников на водяной смазке для турбомашин: дис. … канд. техн. наук. Калуга, 2003.
Шатохин В.Ф. Колебания роторов с обкатом ротором статора (методы математического моделирования и программные средства). Dusseldorf: Lambert Academic Publishing, 2016.
Шатохин В.Ф. Возбуждающие обкат силы при колебаниях ротора с задеваниями о статор // Теплоэнергетика. 2017. № 7. С. 17–22. https://doi.org/10.1134/S004036361707007
Костюк А.Г. Динамика и прочность турбомашин. М.: Изд-во МЭИ, 2000.
Костюк А.Г., Шатохин В.Ф., Волоховская О.А. Движение неуравновешенного ротора при задеваниях о статор // Теплоэнергетика. 2012. № 2. С. 3–11.
Gasch R. Vibration of large turbo-rotors in fluid-film bearings on an elastic foundation // J. Sound Vib. 1976. V. 47. Is. 1. P. 53–73. https://doi.org/10.1016/0022-460X(76)90407-7
Williams R.J. Parametric study of reverse whirl instability using an analytical equilibrium model: BRITE_EURAM project ROSTADYN Technical Report 4.17. August 1996.
Банах Л.Я. Колебания ротора при постоянном контакте с неподвижными и легкими подвижными элементами роторной системы // Сборник Vibroengineering Procedia 22, Dynamics of Strongly Nonlinear Systems. Сер. “22nd Intern. Conf. on Vibroengineering”, 2016. Р. 90–96.
Шатохин В.Ф. Погашающая способность демпферных устройств при обкате ротором статора // Теплоэнергетика. 2019. № 2. С. 32–40. https://doi.org/10.1134/S0040363619020061
Шатохин В.Ф. Развитие обката неуравновешенного ротора по статору // Электрические станции. 2013. № 11. С. 17–28.
Дополнительные материалы отсутствуют.
Инструменты
Теплоэнергетика