Теплоэнергетика, 2022, № 10, стр. 94-104
Моделирование объемной конденсации при расширении парогазовой смеси в проточной части ступени турбодетандерного агрегата
А. А. Сидоров a, *, А. К. Ястребов a
a Национальный исследовательский университет “Московский энергетический институт”
111250 Москва, Красноказарменная ул., д. 14, Россия
* E-mail: AlexSid-MPEI@yandex.ru
Поступила в редакцию 29.12.2021
После доработки 19.02.2022
Принята к публикации 23.03.2022
- EDN: UMPNZR
- DOI: 10.56304/S0040363622090065
Аннотация
В реальных условиях рабочая среда, поступающая в турбодетандер, может содержать некоторое количество примесей, влияющих на характеристики потока, результирующее значение температуры на выходе из ступени турбодетандерного агрегата (ТДА) и срок службы его проточной части. Наличие примесей зачастую становится причиной эрозионного разрушения лопаток рабочего колеса ТДА вследствие их бомбардировки каплями образующегося конденсата. Современные типовые методы расчета эффектов кавитации и объемной конденсации либо не позволяют учитывать наличие данных эффектов и степень их влияния на характеристики потока и проточную часть ТДА на этапе их проектирования, либо имеют довольно малую точность и являются лишь инструментом вероятностного предсказания эффектов кавитации и объемной конденсации, ввиду чего современная холодильная техника, а также турбомашиностроительная отрасль в целом нуждаются в таком инструменте, который был бы лишен указанных недостатков. Впервые для решения задачи объемной конденсации при расширении парогазовой смеси в проточной части конкретной ступени ТДА применяется модель конденсации, в основе которой лежит кинетическое уравнение для функции распределения капель по размерам в нестационарной трехмерной постановке. Модель реализована в виде специального модуля, интегрируемого в CFD-пакет. На базе трехмерных нестационарных расчетов проводится сравнительный анализ влияния конденсации на термогазодинамику процесса расширения неконденсирующегося газа-носителя и конденсирующейся примеси в проточной части ступени конкретной модели ТДА. Локализованы возможные области возникновения объемной конденсации, на основе расположения которых анализируются вероятные последствия (окажет ли это какое-либо влияние на термогазодинамику и появятся ли области, подверженные эрозионному износу). В настоящей работе предлагается методика расчета расширения многокомпонентных смесей в проточной части ступени ТДА как без учета конденсации, так и с ее учетом.
Представленное исследование – продолжение статьи [1], посвященной моделированию термогазодинамики процесса расширения чистого газа без примесей в проточной части ступени турбодетандерного агрегата, а также верификации расчетной модели на основе ее сравнения с результатами реальных испытаний. Главная цель настоящей работы – исследование объемной конденсации при расширении газа с примесями (т.е. рабочее тело представляет собой парогазовую смесь) в проточной части той же ступени ТДА.
При подготовке материала данной статьи было рассмотрено большое число источников, характеризующих современное состояние исследований объемной конденсации, а также области применения CFD-пакетов в расчетах термогазодинамики проточных частей турбодетандерных агрегатов. Можно выделить две научные школы – отечественную, направленную в основном на теоретические изыскания (среди которых стоит особенно выделить работы профессора М.Е. Дейча, Д.И. Плачендовского и Н.М. Корценштейна [2–7]) и зарубежную, в большей степени ориентированную на экспериментальные исследования [8–10]. Изучение объемной конденсации было и остается актуальным направлением исследований фазовых переходов ввиду его довольно широкого распространения в технике. CFD-моделирование активно применяется для исследования термогазодинамики, а также для оптимизации проточных частей ступеней ТДА как в качестве самостоятельного инструмента для их проектирования, так и для проведения поверочных расчетов. Из-за сложности проведения экспериментальных исследований, а также отсутствия в открытом доступе информации по проточным частям и режимным картам, работы, посвященные CFD-исследованиям, не опираются на экспериментальные исследования и по большей части либо не проверяются, либо верифицируются по результатам аналитических расчетов.
Объемная конденсация – достаточно часто встречающееся в технике явление, однако не всегда полезное. В реальных условиях рабочая среда, поступающая в турбодетандер, содержит некоторое количество примесей, влияющих на характеристики потока, результирующее значение температуры на выходе из ТДА и срок службы проточной части агрегата. Наличие примесей зачастую становится причиной эрозионного разрушения лопаток рабочего колеса ТДА вследствие бомбардировки их каплями образующегося конденсата.
Следует обратить внимание на проблему поиска подходящих экспериментальных данных для верификации получаемого решения. Так, чтобы сопоставить расчетные и экспериментальные данные, необходимо иметь, во-первых, чертежи или трехмерную модель проточной части ТДА, а в идеальном случае – поверхность сканирования реально испытанного образца, что, как правило, является интеллектуальной собственностью и коммерческой тайной и не распространяется в открытых источниках; во-вторых, режимную карту, программу и методику испытаний и, в-третьих, непосредственно результаты испытаний, получение которых для систем с объемной конденсацией в потоке затруднено ввиду высокой стоимости измерительных комплексов и сложности самого процесса сбора данных.
Таким образом, прямое сравнение результатов расчета для объемной конденсации в ТДА с экспериментальными данными других авторов не представляется возможным. Однако авторы настоящей работы считают, что суперпозиция двух верифицированных подходов к описанию рассматриваемой проблемы даст корректный результат. В предыдущих работах были верифицированы модуль решения кинетического уравнения для функции распределения капель по размерам [11], отвечающий за учет конденсации в потоке, и методика решения задачи о расширении газовых потоков в проточной части турбодетандерного агрегата [1], которые дают основания утверждать, что объединение данных подходов применимо к решению задачи об объемной конденсации при расширении парогазовой смеси в турбодетандере.
ПОСТАНОВКА ЗАДАЧИ
В работе разбираются два варианта постановки задачи об учете объемной конденсации. В первом варианте рассматривается расширение парогазовой смеси, состоящей из гелия и азота, в ступени ТДА без учета фазовых переходов, а во втором – с учетом объемной конденсации в потоке, при этом гелий выступает в качестве неконденсирующегося газа-носителя, а азот – в виде конденсирующегося пара. Задача в обеих постановках решается в однотемпературном приближении, т.е. при равенстве температур газа и капель, что оправдано в случае, если примесь составляет не более 5% смеси [7]. В предлагаемой постановке количество пара поддерживается именно на таком уровне. Выбор компонентов обусловлен отсутствием экспериментальных данных для сравнения с результатами расчета и последующей верификации. Так, условно принимается, что газообразный гелий смешивается с основным компонентом воздуха – парами азота. В реальных условиях такое смешение возможно при наличии негерметичных участков в подающем тракте, однако фактически является нештатным режимом работы.
Математическое описание
Математическое описание рассматриваемой задачи включает в себя систему уравнений, состоящую из уравнений Навье – Стокса для сжимаемого газа, усредненных по Рейнольдсу и Фавру [12], уравнений состояния, а также уравнений турбулентности для замыкания системы. Ударные волны не моделируются, поэтому объемная вязкость не учитывается в уравнениях движения [13].
В силу того что в настоящей постановке задачи имеются три компонента (пар, неконденсирующийся газ и жидкость), необходимо использовать три уравнения сохранения массы: одно для смеси в целом – уравнение неразрывности и два для компонентов. Однако, поскольку массовая доля жидкости определяется при решении системы моментных уравнений, допускается использование уравнения неразрывности и одного уравнения сохранения массы компонента (для пара). При этом закон сохранения массы компонента смеси выглядит следующим образом [14]:
(1)
$\frac{{\partial {{\rho }_{q}}}}{{\partial t}} + \frac{{\partial \left( {{{\rho }_{q}}{{u}_{k}}} \right)}}{{\partial {{x}_{k}}}} + \frac{{\partial {{j}_{{qk}}}}}{{\partial {{x}_{k}}}} = 0,$Диффузионные потоки массы определяются по закону Фика и в общем виде представлены как
(2)
${{j}_{q}} = - {{\rho }_{q}}D\nabla {{m}_{q}} = - {{\rho }_{q}}D\frac{{\partial {{m}_{q}}}}{{\partial {{x}_{k}}}}{{i}_{k}},$В настоящей работе, как и в [1], используется обновленная k‒ω SST-модель турбулентности, так как она показала наилучшую устойчивость для сжимаемых течений [15].
Уравнения состояния
Следующий важный шаг в решении поставленной задачи – описание взаимосвязи между термодинамическими характеристиками рабочего тела: плотностью, давлением и температурой. Учитывая, что рассматриваемая смесь состоит из двух реальных газов, необходимо задействовать два уравнения состояния. Так, свойства гелия описываются с помощью уравнения состояния реальных газов Редлиха – Квонга, основания для применения которого приведены в предыдущей работе авторов [1].
Однако использование этого же уравнения для азота невозможно, так как для него в рабочем диапазоне давлений и температур не выполняется условие применимости. В настоящей работе для паров азота предлагается интерполяционное уравнение вида [16]
где p – давление, МПа; pкр – критическое давление, МПа; $w = {{{{\rho }}(p,T)} \mathord{\left/ {\vphantom {{{{\rho }}(p,T)} {{{\rho }_{{кр}}}}}} \right. \kern-0em} {{{\rho }_{{кр}}}}}$ – приведенная плотность; ${{\rho }}$ – плотность, кг/м3; ${{\rho }_{{кр}}}$ – критическая плотность, кг/м3; $\tilde {T} = {T \mathord{\left/ {\vphantom {T {{{T}_{{кр}}}}}} \right. \kern-0em} {{{T}_{{кр}}}}}$ – приведенная температура; Т – температура, К; Ткр – критическая температура, К; Z – коэффициент сжимаемости; Zкр– критический коэффициент сжимаемости.Коэффициент сжимаемости Z вычисляется также по интерполяционному соотношению
(4)
$Z = 1 + {{A}_{0}} = 1 + \sum\limits_{i = 1}^n {\sum\limits_{j = 0}^m {{{b}_{{ij}}}\frac{{{{w}^{i}}}}{{{{{\tilde {T}}}^{j}}}}} } ,$При этом критический коэффициент сжимаемости Zкр, для азота принятый равным 0.2896, находится по этому же выражению, однако w и $\tilde {T}$обращаются в единицу согласно их определению. Уравнение состояния (3) решается методом последовательных приближений с точностью ε = = 0.0001.
Учитывая вышесказанное, можно записать уравнение состояния в классическом виде через плотность смеси в зависимости от температуры и давления [17]:
(5)
${{\rho }_{{см}}}\left( {p,T} \right) = \frac{{p{{M}_{{см}}}}}{{{{Z}_{{см}}}\left( {p,T} \right)RT}},$Описание кинетики конденсации
Для описания процесса объемной конденсации применяется кинетическое уравнение для функции распределения капель по размерам в общем виде [18]:
(6)
$\frac{{\partial {{f}_{r}}}}{{\partial t}} + \vec {v}\nabla {{f}_{r}} + \frac{\partial }{{\partial r}}\left( {\dot {r}\,{{f}_{r}}} \right) = \frac{I}{{{{\rho }_{{см}}}}}\delta \,(r - {{r}_{{кр}}}),$Для того чтобы определить интегральные характеристики конденсационного аэрозоля, например числовую плотность капель в единице массы и средний размер капель, а также произвести расчет объемных источников массы и энергии, следует рассмотреть моменты функции распределения [18]:
где n = 0–3 – количество моментов функции распределения.Числовую плотность капель можно найти через нулевой момент функции распределения ${{N}_{d}} = \rho {{\Omega }_{0}},$ а средний радиус капель численно равен отношению первого момента к нулевому: $\bar {r} = {{{{\Omega }_{1}}} \mathord{\left/ {\vphantom {{{{\Omega }_{1}}} {{{\Omega }_{0}}}}} \right. \kern-0em} {{{\Omega }_{0}}}}.$
Иногда используется также функция распределения частиц по размерам, нормированная на количество капель в единице объема:
Для решения кинетического уравнения, по аналогии с кинетической теорией газов, можно применить моментный метод, позволяющий получить эквивалентную систему уравнений для первых четырех моментов (n = 0–3) функции распределения. Для этого уравнение (6) умножают на rn и интегрируют по всем значениям радиуса капель r. Если скорость роста капель от радиуса не зависит, система принимает вид
(9)
$\frac{{d{{\Omega }_{n}}}}{{dt}} = n\dot {r}{{\Omega }_{{n - 1}}} + \frac{I}{\rho }r_{{кр}}^{n} - \vec {v}\nabla {{\Omega }_{n}}.$Расчет критического радиуса проводят по формуле Томпсона [18]:
где σ – коэффициент поверхностного натяжения, Н/м; ρl – плотность конденсата, кг/м3; Rv – индивидуальная газовая постоянная для паровой фазы, Дж/(кг ∙ К); $s = {{{{p}_{v}}} \mathord{\left/ {\vphantom {{{{p}_{v}}} {{{p}_{s}}}}} \right. \kern-0em} {{{p}_{s}}}}$ – степень пересыщения; ${{p}_{v}}$ – давление пара, Па; ps – давление насыщения, Па.В данной работе для расчета скорости нуклеации используется широко известная формула Френкеля – Зельдовича [18]:
где
${{M}_{v}}$ – молярная масса пара, г/моль; NA – число Авогадро, моль–1; α – коэффициент конденсации.
Скорость роста капель определяют по формуле Герца – Кнудсена для однотемпературной постановки [19]:
(12)
$\dot {r} = \frac{{{{\alpha }}{{p}_{s}}}}{{{{{{\rho }}}_{l}}(T)}}\left( {\frac{{s - 1}}{{\sqrt {2{{\pi }}{{R}_{v}}T} }}} \right).$Рождение новой фазы, т.е. появление капель конденсата, а также теплообмен при выполнении необходимых условий учитываются через объемные источники массы Sm и энергии Se, в рассматриваемой задаче состоящие из двух слагаемых, первое из которых отвечает за вклад в термогазодинамику процесса образования капель, а второе – за вклад процесса их роста.
Формулу для объемного источника массы конденсата можно записать следующим образом:
(13)
${{S}_{m}} = \frac{4}{3}\pi r_{{кр}}^{3}{{\rho }_{l}}(T)I + 4\pi {{\rho }_{l}}(T)\rho (T)\dot {r}{{\Omega }_{2}},$Очевидно, что сток массы для паровой фазы равен Sm по модулю и противоположен по знаку.
Выражение для определения объемного источника энергии имеет вид
где L(T) – теплота парообразования, кДж/кг.Свойства компонентов смеси
Рабочее тело представляет собой парогазовую смесь, состоящую из газа-носителя гелия и паров азота. Поскольку в настоящей задаче гелий выступает в качестве неконденсирующегося компонента, описание дополнительных свойств, по сравнению с предыдущей работой [1], не требуется. Таким образом, в настоящем разделе представлены свойства второго компонента смеси – азота.
Зависимость давления от температуры на линии насыщения, или в данном случае кривая сублимации, является особенно важной для корректной работы модуля при решении кинетического уравнения для функции распределения капель по размерам. В данной работе для азота используется следующая зависимость давления насыщения от температуры [20]:
(15)
$\ln \left( {\frac{{{{p}_{s}}}}{{{{p}_{{кр}}}}}} \right) = \frac{{126.2}}{T}\left[ {A\tau + B{{\tau }^{{1.5}}} + C{{\tau }^{{2.5}}} + D{{\tau }^{5}}} \right],$Так же, как было показано в [21], при решении поставленной задачи в выражениях для кинетики конденсации и при термогазодинамических расчетах необходимо учитывать влияние температуры на свойства азота, поэтому в настоящей работе используются зависимости для плотности жидкости [22], поверхностного натяжения [23] и теплоты парообразования [24] от температуры. Энтальпия, энтропия и коэффициент сжимаемости вычисляются через интерполяционные функции, представленные в [16].
Изоэнтропийный КПД
Для определения такой важной характеристики процесса детандирования, как изоэнтропийный КПД ηs, являющийся мерой приближения реального процесса расширения к идеальному, необходимо иметь значения действительного (холодопроизводительности) и располагаемого теплоперепада для смеси, т.е. изменения энтальпии (равного работе, так как теплообмен с окружающей средой не рассматривается) в реальном и идеальном (изоэнтропийном) процессах:
(16)
${{\eta }_{s}} = \frac{{h_{{хол}}^{{см}}}}{{h_{s}^{{см}}}} = \frac{{h_{н}^{{см}} - h_{к}^{{см}}}}{{h_{s}^{{см}}}},$Энтальпия смеси реальных газов с высокой достоверностью может быть вычислена по формуле [25]
где mq – массовая доля q-го компонента смеси; hq – энтальпия компонента смеси, Дж/кг.Однако требуется, чтобы точка отсчета при определении энтальпии была одной и той же для всех компонентов смеси, в противном случае необходимо оперировать перепадом энтальпий.
При этом массовая доля q-го компонента смеси реальных газов равна [17]
Таким образом, энтальпия смеси реальных газов определяется как
(19)
$\begin{gathered} {{h}_{{см}}}\left( {p,T} \right) = \sum\limits_{j = 1}^{mn} {\frac{{{{Z}_{{см}}}{{M}_{j}}}}{{{{M}_{{см}}}{{Z}_{j}}}}{{C}_{j}}{{h}_{j}}} = \\ = \sum\limits_{j = 1}^{mn} {\left[ {{{{\left( {\sum\limits_{q = 1}^n {\frac{{{{C}_{q}}}}{{{{Z}_{q}}}}} } \right)}}^{{ - 1}}}{{{\left( {\sum\limits_{q = 1}^{mn} {\frac{{{{Z}_{{см}}}}}{{{{Z}_{q}}}}{{C}_{q}}{{M}_{q}}} } \right)}}^{{ - 1}}}\frac{{{{M}_{j}}}}{{{{Z}_{j}}}}{{C}_{j}}{{h}_{j}}} \right]} , \\ \end{gathered} $Тогда
(20)
$\begin{gathered} {{\eta }_{s}} = \frac{{\left[ {\sum\limits_{j = 1}^{mn} {\frac{{{{Z}_{{см}}}{{M}_{j}}}}{{{{M}_{{см}}}{{Z}_{j}}\left( {{{p}_{н}},{{T}_{н}}} \right)}}{{C}_{j}}{{h}_{j}}\left( {{{p}_{н}},{{T}_{н}}} \right)} } \right]_{н}^{{см}}}}{{\left[ {\sum\limits_{j = 1}^{mn} {\frac{{{{Z}_{{см}}}{{M}_{j}}}}{{{{M}_{{см}}}{{Z}_{j}}\left( {{{p}_{к}},{{T}_{s}}} \right)}}{{C}_{j}}{{h}_{j}}\left( {{{p}_{к}},{{T}_{s}}} \right)} } \right]_{s}^{{см}}}} - \\ - \,\,\frac{{\left[ {\sum\limits_{j = 1}^{mn} {\frac{{{{Z}_{{см}}}{{M}_{j}}}}{{{{M}_{{см}}}{{Z}_{j}}\left( {{{p}_{к}},{{T}_{к}}} \right)}}{{C}_{j}}{{h}_{j}}\left( {{{p}_{к}},{{T}_{к}}} \right)} } \right]_{к}^{{см}}}}{{\left[ {\sum\limits_{j = 1}^{mn} {\frac{{{{Z}_{{см}}}{{M}_{j}}}}{{{{M}_{{см}}}{{Z}_{j}}\left( {{{p}_{к}},{{T}_{s}}} \right)}}{{C}_{j}}{{h}_{j}}\left( {{{p}_{к}},{{T}_{s}}} \right)} } \right]_{s}^{{см}}}}. \\ \end{gathered} $Для упрощения восприятия в настоящей работе не приводятся описания расчетной модели, сетки и граничных условий, рассмотренные в [1]. Стоит лишь отметить, что для исключения влияния на результаты расчетов разбиения модели проточной части на элементы проводилось исследование сеточной сходимости как в целом по сгущению сетки в области высоких градиентов, так и по призматическому подслою. Так, например, при подготовке сетки с призматическим подслоем для высоты первого пристеночного элемента принималось y+ = 0.9, а в ходе исследования сеточной сходимости было отмечено, что требуется не менее 25 элементов в подслое.
Особенность данной работы заключается в дополнении расчетного CFD-пакета специальным модулем для решения кинетического уравнения для функции распределения по размерам [18]. Подробное описание работы модуля представлено в [11].
РЕЗУЛЬТАТЫ И ИХ ОБСУЖДЕНИЕ
В данном разделе приводятся зависимости температуры, давления, степени пересыщения, скорости нуклеации, числовой плотности капель, критического радиуса и других параметров, построенные вдоль вспомогательной оси (рис. 1). Ось располагается в канале на плоскости поперечного сечения направляющего аппарата между двумя его лопатками.
Рис. 1.
Расположение вспомогательной оси на плоскости сечения направляющего аппарата проточной части ступени турбодетандерного агрегата
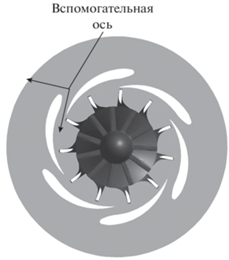
Одна из основных задач настоящей работы – локализация областей возникновения фазовых переходов, а именно объемной конденсации. На рис. 2 видно, что таких зон в проточной части ступени несколько (разделены условно):
Рис. 2.
Локализация областей активной конденсации. 1 – область образования капель; 2 – зона интенсивного прироста массы
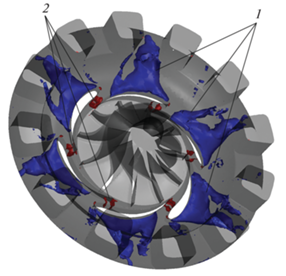
в первой зоне (на рис. 2 отмечена цифрой 1) происходит активное образование капель – их количество растет, но при этом размер остается практически неизменным, так как площадь поверхности капель мала, а скорость их роста достаточно большая;
во второй зоне (на рис. 2 отмечена цифрой 2) масса капель, образовавшихся ранее и образующихся в текущем процессе, начинает интенсивно расти, и в этом случае их суммарная площадь существенно выше, чем в первой зоне, что также дает значительный вклад в тепловыделение.
Как было показано ранее, источниковый член состоит из двух слагаемых, первое из которых отвечает за образование капель. На рис. 2 видно, что большая интенсивность процесса образования капель сосредоточена до направляющего аппарата, т.е. фактически во входном коллекторе. При этом по распределению второго слагаемого (см. рис. 2), отвечающего за рост капель, видно, что зона интенсивного прироста массы располагается в каналах направляющего аппарата.
Следует отметить, что степень пересыщения во входном коллекторе выше единицы (рис. 3, а), что является необходимым условием для возникновения фазового перехода, а скорость нуклеации имеет ярко выраженные области высокой интенсивности в указанных областях (зоны 1 и 2 на рис. 2) (рис. 3, б).
Важно также отдельно рассмотреть область каналов направляющего аппарата, где степень пересыщения (рис. 4, а), скорость нуклеации (рис. 4, б) и скорость роста капель (рис. 4, г) имеют ярко выраженные максимумы, а критический радиус капель (рис. 4, в) ‒ выраженный минимум. Пересыщения на уровне трех единиц в данном случае достаточно для образования конденсата.
Рис. 4.
Распределение степени пересыщения s (а), относительной скорости нуклеации I (б) (Imax = 2.057 × × 1022 м–3 · с–1), критического радиуса (в) и скорости роста радиуса капель (г). x – расстояние от входа в направляющий аппарат вдоль вспомогательной кривой

Еще одна имеющая большое значение характеристика процесса объемной конденсации – средний размер капель конденсата. В ходе расчетов было установлено, что при конденсации в направляющем аппарате образуются довольно крупные капли, радиус которых достигает 1.3 мкм и даже более. Их скорость на выходе из направляющего аппарата очень высока и может составлять 400–500 м/с, что качественно согласуется с данными, приведенными в [4]. Известно, что малые капли, как правило, не отклоняются от средней линии тока и не оказывают влияния на элементы проточной части, в то время как именно крупные капли, ударяющиеся на большой скорости о лопатки рабочего колеса и отскакивающие в сторону от направляющего аппарата, представляют существенную опасность для них и для всей проточной части. Важно отметить, что в настоящей работе не учитывается коалесценция капель, которая может привести к занижению размера капель.
Из представленных распределений и зависимостей можно сделать вывод об адекватности и физичности полученных распределений (т.е. они не противоречат общепринятым представлениям о физике процесса), а также о их некотором качественном согласовании с представлениями о протекании процесса объемной конденсации и его влиянии на характеристики потока.
Влияние объемной конденсации на изоэнтропийный КПД
На следующем шаге определения влияния объемной конденсации на работу ступени в целом следует оценить негативный вклад этого процесса в эффективность ступени.
Для упрощения представления материала далее приводятся обобщенные результаты расчетов термогазодинамики проточной части ступени турбодетандерного агрегата для трех случаев (табл. 1):
Таблица 1.
Давление на поверхности лопатки рабочего колеса
Параметр | Чистый газ (He) | Смесь газов (He + 5% N2) | |
---|---|---|---|
без учета конденсации | с учетом конденсации | ||
Давление, МПа: | |||
начальное pн | 1.8 | 1.8 | 1.8 |
конечное pк | 0.0764 | 0.0719 | 0.0719 |
Температура, К: | |||
начальная Tн | 99.98 | 99.98 | 99.98 |
конечная Tк | 44.89 | 45.29 | 48.73 |
в конечной точке изоэнтропийного процесса Th-s | 27.92 | 27.40 | 26.53 |
Энтальпия, кДж/кг: | |||
начальная hн | 539.64 | 539.64 | 539.64 |
конечная hк | 248.22 | 250.28 | 268.16 |
в конечной точке изоэнтропийного процесса hs | 379.73 | 382.38 | 387.21 |
H | 291.50 | 289.36 | 271.81 |
Массовый расход, кг/с: | |||
гелия | 0.2 | 0.2 | 0.2 |
азота | 0 | 0.01 | 0.01 |
Частота вращения рабочего колеса ω, тыс. мин–1 | 140 | ||
Изоэнтропийный КПД ηs, % | 76.77 | 75.68 | 70.20 |
для условий, указанных в работе [1], где в качестве рабочего тела был выбран чистый газ, а фазовые переходы отсутствовали;
для смесевого рабочего тела, также без учета фазовых переходов [26];
для исследования расширения смесевого рабочего тела с учетом объемной конденсации.
Как следует из табл. 1, наличие примеси без учета фазовых переходов незначительно влияет на итоговый изоэнтропийный КПД вследствие малого количества примесей (в настоящем расчете пары азота составляют не более 5% массы потока). Однако если учитывать возможность возникновения объемной конденсации, то это влияние оказывается весьма существенным: изоэнтропийный КПД ступени снижается примерно на 6.5%, что объясняется активным тепловыделением при росте капель (тепловыделение происходит также при образовании капель, однако оно на порядки меньше тепловыделения при росте капель).
На рис. 5 видно, что в зоне активного роста капель температура и давление увеличиваются вследствие активного тепловыделения, в итоге влияющего на качество работы ступени: глубина охлаждения потока в направляющем аппарате снижается, что приводит к поступлению в рабочее колесо более теплого потока, а значит, ступень турбодетандера менее эффективно выполняет свою основную функцию – генерацию холода.
Влияние объемной конденсации на износ проточной части
Помимо снижения эффективности процесса детандирования при расширении смесевого потока при объемной конденсации, есть как минимум еще одно ее негативное воздействие. Вследствие образования и роста капель до довольно большого размера (около 2.6 мкм в диаметре) увеличивается вероятность износа как проточной части в целом, так и лопаток рабочего колеса. Длительное воздействие газокапельного потока может приводить к эрозионному разрушению рабочего колеса и гарантированно снижает рабочий ресурс проточной части.
Для оценки влияния износа следует рассмотреть проекцию поверхности лопатки рабочего колеса (рис. 6). При поступлении рабочего тела в проточную часть поверхность лопатки принимает на себя бóльшую часть создаваемой потоком нагрузки, под действием которой вращается рабочее колесо.
На рис. 7 представлено распределение давления по проекции поверхности лопатки рабочего колеса для двух расчетных вариантов истечения чистого газа без примесей и без учета фазовых переходов и истечения смеси с учетом объемной конденсации. Распределение статического давления для расчетного варианта со смесевым рабочим телом без учета конденсации не приводится, так как это распределение мало отличается от варианта чистого газа без конденсации.
Рис. 7.
Распределение статического давления по проекции рабочей поверхности лопатки рабочего колеса. а – чистый газ без конденсации; б – смесь с учетом конденсации
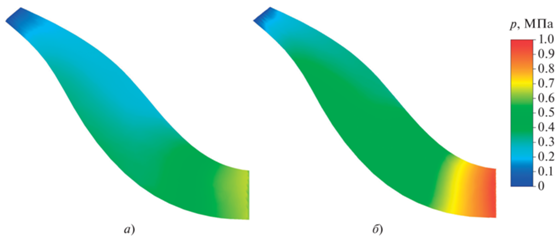
Видно, что при расчете для смеси давление на лопатку в области входной кромки существенно выше, чем при истечении чистого газа. Так, например, в области входа в межлопаточный канал (см. рис. 7, а) максимальное давление потока чистого газа составляет приблизительно 607.95 кПа, в то время как парогазовой смеси (см. рис. 7, б) – примерно 1013.25 кПа (табл. 2). Это объясняется тем, что капли конденсата, образовавшиеся в подводящем коллекторе и активно растущие в направляющем аппарате, имеют бóльшую плотность по сравнению с газом-носителем и очень высокую скорость, при которой этот смесевой поток “врезается” в лопатку. Именно такое длительное (или импульсное, высокой частоты) воздействие приводит к разрушению рабочего колеса. Косвенное подтверждение таким выводам приводится в [27].
Таблица 2.
Давление на поверхности лопатки рабочего колеса
Давление, МПа | Чистый газ (He) | Смесь газов (He + 5% N2) | |
---|---|---|---|
без учета конденсации | с учетом конденсации | ||
Среднее pср | 0.344 | 0.351 | 0.528 |
Максимальное pmax | 0.672 | 0.685 | 1.029 |
В настоящей работе на данном этапе задача формирования каких-либо рекомендаций по уменьшению негативного влияния объемной конденсации не ставилась. Основной целью было проверить адекватность и физичность результатов при применении модели объемной конденсации, реализованной в виде специального интегрируемого в расчетный пакет модуля. При этом следует обратить особое внимание на локализацию областей возможных фазовых переходов, определение интенсивности этого процесса, а также обнаружение “слабых” мест проточной части, с высокой долей вероятности подверженных деформациям или негативным изменениям вследствие процесса объемной конденсации.
ВЫВОДЫ
1. Задача объемной конденсации при расширении парогазового потока в проточной части ступени ТДА решена с помощью впервые предложенного специального модуля для решения кинетического уравнения для функции распределения капель по размерам.
2. Для парогазового потока конкретного состава и известной проточной части ступени турбодетандерного агрегата области объемной конденсации целесообразно локализовать, причем фактически их можно разделить на два типа: в одной происходит активное образование капель без существенного роста (во впускном коллекторе, до направляющего аппарата), в другой – активный рост и образование капель (в каналах направляющего аппарата).
3. Наличие примеси в потоке до 5% не оказывает влияния на эффективность ступени при условии, что фазовые переходы отсутствуют (это не является новым результатом, однако хорошо иллюстрирует применимость предлагаемого подхода).
4. Расширение парогазового потока в условиях возникновения объемной конденсации оказывает существенное влияние на эффективность работы ступени. Так, при рассмотрении конкретного режима изоэнтропийный КПД ступени снизился почти на 6.5% вследствие тепловыделения при конденсации.
5. В процессе конденсации образующиеся капли вырастают до максимальных размеров – примерно 2.6 мкм в диаметре и имеют высокую скорость на выходе из направляющего аппарата – 400–500 м/с.
6. Давление на поверхность лопатки рабочего колеса в области входной кромки в случае возникновения в потоке объемной конденсации почти в 1.5 раза выше давления в режиме без конденсации. Длительное воздействие высокого давления в этой области при большом размере и высокой скорости капель может привести к снижению эксплуатационного ресурса и последующему разрушению рабочего колеса.
7. Интеграция специального модуля в CFD-пакет практически не оказывает негативного влияния на расчетное время до достижения сходимости результатов решения и, соответственно, не требует значительного увеличения вычислительных мощностей. Специальный модуль достаточно хорошо программно оптимизирован, вследствие чего различие в среднем времени расчета до достижения соответствующего уровня сходимости результатов с модулем и без него составляет менее 5% при прочих равных условиях.
8. Дальнейшая работа подразумевает отработку методики, позволяющей оценивать степень влияния объемной конденсации на проточную часть ступени турбодетандерного агрегата и, соответственно, подготовку рекомендаций по внесению изменений в форму проточной части на этапе проектирования при профилировании направляющего аппарата и рабочего колеса.
Список литературы
Сидоров А.А., Ястребов А.К. Численное моделирование процесса детандирования в турбоагрегате расширительного типа методом конечных объемов // Теплоэнергетика. 2021. № 8. С. 17–25. https://doi.org/10.1134/S0040363621070043
Дейч М.Е., Филиппов Г.А. Газодинамика двухфазных сред. 2-е изд. М.: Энергоиздат, 1981.
Дейч М.Е., Филиппов Г.А. Двухфазные течения в элементах теплоэнергетического оборудования. М.: Энергоатомиздат, 1987.
Плачендовский Д.И. Исследование двухфазных режимов работы криогенных турбодетандеров: дис. … канд. техн. наук. М., 1981.
Корценштейн Н.М., Самуйлов Е.В., Ястребов А.К. Новый метод моделирования объемной конденсации пересыщенного пара // ТВТ. 2009. Т. 47. № 1. С. 89–100.
Корценштейн Н.М., Ястребов А.К. Объемная конденсация в запыленном парогазовом потоке с учетом распределения пылинок по размерам // Коллоид. журн. 2016. Т. 78. № 4. С. 444–449. https://doi.org/10.7868/S0023291216040108
Kortsenshteyn N.M., Yastrebov A.K. Interphase heat transfer during bulk condensation in the flow of vapor – gas mixture // Int. J. Heat Mass Transfer. 2012. V. 55. Is. 4. P. 1133–1140. https://doi.org/10.1016/j.ijheatmasstransfer.2011.09.059
Temperature and gas-phase composition measurements in supersonic flows using tunable diode laser absorption spectroscopy: The effect of condensation on the boundary-layer thickness / S. Tanimura, Y. Zvinevich, B.E. Wyslouzil, M. Zahniser, J. Shorter, D. Nelson, B. McManus // J. Chem. Phys. 2005. V. 122. Is. 19. 194304. https://doi.org/10.1063/1.1900084
Lamanna G. On nucleation and droplet growth in condensing nozzle flows. Technische Universiteit Eindhoven, 2000. https://doi.org/10.6100/IR539104
3D Numerical modeling of zeotropic mixtures and pure working fluids in an ORC turbo-expander / I. Gad-el-Hak, A.E. Hussin, A.M. Hamed, N.A. Mahmoud // Int. J. Turbomach. Propul. Power. 2017. V. 2. Is. 1. https://doi.org/10.3390/ijtpp2010002
Сидоров А.А., Ястребов А.К. Интеграция модуля численного решения кинетического уравнения в CFD-пакет для задачи объемной конденсации при истечении парогазовой смеси через сопло // Вестник Дагестан. гос. техн. ун-та. Техн. науки. 2021. Т. 48. № 1. https://doi.org/10.21822/2073-6185-2021-48-1-65-75
Ландау Л.Д., Лифшиц Е.М. Теоретическая физика. В 10 т. Т. 6: Гидродинамика. М.: Физматлит, 2015.
Fluent theory guide 14. [Электрон. ресурс.] https://www.ansys.com/Products/Fluids/ANSYS-Fluent
Лабунцов Д.А., Ягов В.В. Механика двухфазных систем: учеб. пособие для вузов. М.: Изд-во МЭИ, 2000.
Wilcox D.C. Formulation of the k-ω turbulence model revisited // AIAA J. 2008. V. 46. Is. 11. P. 2823–2838. https://doi.org/10.2514/1.36541
Термодинамические свойства азота / В.В. Сычев, А.А. Вассерман, Ф.Д. Козлов, Г.А. Спиридонов, В.А. Цымарный / Государственная служба стандартных справочных данных. М.: Изд-во стандартов, 1977.
ГОСТ Р 8.974–2019. Газовый анализ. Пересчет данных состава газовых смесей. Утв. и введ. в действие приказом Федерального агентства по техническому регулированию и метрологии от 30.10.2019 № 1062-ст.
Стернин Л.Е. Основы газодинамики двухфазных течений в соплах. М.: Машиностроение, 1974.
Шишкова И.Н., Ястребов А.К. Расчет потока массы пара при изотермической конденсации на сферических каплях в широком диапазоне чисел Кнудсена на основе решения кинетического уравнения Больцмана // Коллоид. журн. 2016. Т. 78. № 5. С. 660–667. https://doi.org/10.7868/S0023291216050177
Wagner W. A new correlation method for thermodynamic data applied to the vapour pressure curves of argon, nitrogen and water / IUPAC Thermodynamic Tables Project Centre // Cryogenics. 1978. V. 18. Is. 2. P. 122. https://doi.org/10.1016/0011-2275(78)90125-X
Сидоров А.А., Ястребов А.К. Влияние геометрических характеристик канала и свойств парогазовой смеси на объемную конденсацию при течении в сопле // Теплоэнергетика. 2018. № 1. С. 68–76. https://doi.org/10.1134/S004036361801006X
Van Itterbeek A., Verbeke O. Density of liquid nitrogen and argon as a function of pressure and temperature // Physica. 1960. V. 26. Is. 11. P. 931–938. https://doi.org/10.1016/0031-8914(60)90042-2
Stansfield D. The surface tension of liquid argon and nitrogen // Proc. Phys. Soc. 2002. V. 72. Is. 5. 854. https://doi.org/10.1088/0370-1328/72/5/321
Selected cryogenic data notebook / J.E. Jensen, W.A. Tuttle, R.B. Stewart, H. Brechna, A.G. Prodell. Brookhaven National Laboratory, 1980.
Cengel Y.A., Boles M.A. Thermodynamics: An engineering approach. 5th ed. McGraw-Hill, 2006.
Sidorov A.A., Yastrebov A.K. CFD-calculation of influence of impurities on the characteristics of a helium turboexpander // J. Phys.: Conf. Ser. 2020. V. 1683. 022052. https://doi.org/10.1088/1742-6596/1683/2/022052
Мартьянов О.А., Меркулов В.И. Обзор проблемы течения влажного воздуха в турбодетандерах // Изв. МГТУ МАМИ. 2014. Т. 8. № 4-1. С. 51–55.
Дополнительные материалы отсутствуют.
Инструменты
Теплоэнергетика