Теплоэнергетика, 2022, № 1, стр. 85-90
Оценка возможности обезжелезивания возвратного производственного конденсата ТЭС гранулированным карбонатным шламом
Л. А. Николаева *
Казанский государственный энергетический университет
420066 Казань, Красносельская ул., д. 51, Россия
* E-mail: larisanik16@mail.ru
Поступила в редакцию 18.03.2021
После доработки 15.04.2021
Принята к публикации 21.04.2021
- EDN: UNSURY
- DOI: 10.1134/S0040363621120080
Аннотация
Предложена технология обезжелезивания производственного конденсата ТЭС и его очистки от нефтепродуктов гранулированными сорбционными материалами, изготовленными на основе карбонатного шлама. Карбонатный шлам – отход энергетики, образующийся на стадии предварительной очистки воды при известковании и коагуляции. Гранулированный сорбционный материал для обезжелезивания получен по следующей технологии: шлам с частицами размером от 0.01 до 0.09 мм смешивается с жидким натриевым стеклом при массовом и объемном соотношении 2 : 1. Термообработка проводится при температуре 250°С в течение 60 мин. Определены технологические характеристики, а также статическая и динамическая обменные емкости гранулированного сорбционного материала по отношению к катионам железа на модельных растворах. По уравнению Шилова рассчитаны время и коэффициент защитного действия слоя разработанного материала. Показано, что рН фильтрата соответствует нейтральной среде, а сорбционный материал не привносит вторичное загрязнение в производственный конденсат и удовлетворяет нормативным показателям качества. Предусматривается регенерация отработанного сорбента разбавленным раствором серной кислоты с нарастающей концентрацией от 0.5 до 2.5%, протекающим противопоточно производственному конденсату. Представлена типовая схема очистки возвратного производственного конденсата с загрузкой сорбционного материала в механические и ионообменные фильтры для обезжелезивания. Подобрано стандартное оборудование для изготовления фильтрующего материала по месту очистки конденсата. Рассчитана себестоимость изготовления материала и очистки 1 м3 конденсата. Определены предотвращенный экологический ущерб окружающей природной среде и экономический эффект от модернизации технологической схемы очистки возвратного производственного конденсата на Казанской ТЭЦ-1.
Возвратный производственный конденсат является основной и наиболее ценной составляющей питательной воды для котлов любых давлений (высокого, сверхвысокого и сверхкритического) и производительности. Возвратный конденсат от внешних потребителей пара используется после его очистки от загрязнений, полученных в процессе производства.
Возвратный конденсат загрязнен оксидами и гидроксидами железа и меди, образующимися в результате коррозии трубопроводов, баков, конденсаторов и теплообменников. Эти соединения находятся в конденсате преимущественно в коллоидной и грубодисперсной формах. Попадая в воду котлов, реакторов и парогенераторов, продукты коррозии участвуют в образовании отложений на теплопередающих поверхностях, а переходя в пар – на лопаточном аппарате турбины. В пусковые периоды работы энергооборудования концентрация продуктов коррозии в конденсатах достигает 100–1000 мкг/дм3 и снижается в период стабильной эксплуатации до 10–30 мкг/дм3 при нормируемых значениях 2–10 мкг/дм3 [1].
На ТЭС с производственными отборами пара применяются установки для очистки конденсата, возвращаемого внешними потребителями пара. При выборе технологии и схем очистки производственного конденсата учитывают не только влияние загрязняющих примесей на состояние поверхностей нагрева теплосилового оборудования, но и воздействие продуктов термического разложения этих примесей. Конденсат, который может быть загрязнен соединениями, образующимися при термолизе: минеральными или органическими кислотами, – не должен использоваться в цикле ТЭС. Технологии и аппараты для очистки производственного конденсата должны обеспечивать водный режим в соответствии с правилами технической эксплуатации.
Производственный конденсат, загрязненный различными примесями, должен пройти прежде всего очистку от нефтепродуктов, а в дальнейшем и обезжелезивание с последующим обессоливанием.
Первоначальная очистка производственного конденсата от механических примесей, смол, масел и других загрязнений выполняется у потребителей. На водоподготовительных установках ТЭС производится доочистка конденсата от нефтепродуктов, оксидов железа и меди, солей жесткости.
Возвращаемый конденсат не должен содержать потенциально кислых или щелочных соединений, вызывающих отклонение рН котловой воды от установленных норм более чем на 0.5 ед. при неизменном режиме коррекционной обработки воды фосфатами или фосфатами с едким натром. Если возвращаемый на электростанцию конденсат не соответствует нормам качества питательной воды, то должна быть предусмотрена его очистка до достижения нормативных показателей.
Производительность установки по очистке производственного конденсата предусматривается с учетом возможного покрытия его 50%-ных потерь. Качество конденсата должно удовлетворять следующим нормативным значениям [2]:
Жесткость общая, мкг-экв/дм3 .........................50 |
Содержание, мкг/дм3: |
железа .........................................................100 |
меди ..............................................................20 |
кремния ......................................................120 |
нефтепродуктов ..........................................0.5 |
pH ..............................................................8.5–9.5 |
Окисляемость, мг О/дм3 .....................................5 |
Эффективная очистка от нефтепродуктов производственного конденсата осуществляется при их концентрации не более 20 мг/дм3. При концентрации, не превышающей 10 мг/дм3, эффективная очистка может быть достигнута с применением только адсорбционных фильтров, оснащенных, как правило, активированным углем различных марок. Если концентрация нефтепродуктов выше 10 мг/дм3, то установки оборудуют специальными отстойниками с нефтеловушками.
Целью настоящей работы является исследование возможности использования гидрофобного сорбционного материала для очистки возвратного производственного конденсата от эмульгированных и растворенных нефтепродуктов, а также гранулированного сорбционного материала для обезжелезивания. Сорбционные материалы изготовлены на основе карбонатного шлама химводоподготовки.
Типовая схема очистки производственного конденсата включает в себя отстойник и доочистку на механических, адсорбционных и ионитовых фильтрах. В настоящей работе предлагается модернизировать типовую схему очистки путем применения гидрофобного гранулированного сорбционного материала (ГСМ) и гранулированного сорбционного материала (ГРСМ), изготовленных на основе шлама химводоочистки (ХВО), являющегося отходом энергетических предприятий.
В ранних работах автора данной статьи [3] была разработана технология получения ГСМ для доочистки производственного конденсата от эмульгированных и растворенных нефтепродуктов.
Для проведения экспериментальных исследований использовали шлам осветлителей Казанской теплоэлектроцентрали (Казанской ТЭЦ-1) (влажность 3%) с частицами размером 0.009–0.050 мм, образующийся на стадии предварительной очистки воды при известковании и коагуляции. Рентгенографический качественный фазовый анализ шлама на дифрактометре D8 ADVANCE фирмы Bruker показал следующий химический состав, %:
Кальцит СаСО3 ...............................................73.0 |
Брусит Mg(OH)2 ...............................................8.0 |
Портландит Ca(OH)2 ........................................1.0 |
Кварц SiO2 ........................................................0.4 |
Прочие вещества .............................................17.6 |
Влагоемкость шлама химводоподготовки составляет 57%, что подтверждает его высокую гидрофильность и плохую смачиваемость неполярными соединениями.
Также были определены технологические характеристики и адсорбционная емкость материала по эмульгированным и растворенным продуктам нефти Шийского месторождения. Разработана технология получения гранулированного сорбционного материала: из карбонатного шлама при смешивании его со связующим жидким натриевым стеклом в соотношении 1 : 2 вручную формируют гранулы диаметром от 0.5 до 2.5 мм; эти гранулы проходят термообработку при 700°С в течение 60 мин, затем пропитываются 5%-ной водной эмульсией “Силор”, после чего высушиваются до постоянной массы при температуре 105–110°С [4].
В данной работе разработан и изучен гранулированный сорбционный материал для обезжелезивания производственного конденсата.
Обычно при очистке возвратного производственного конденсата на ТЭС от ионов железа и взвешенных примесей используются механические, адсорбционные, ионообменные фильтры с гранулированной загрузкой.
В настоящей работе предлагается следующая технология производства гранулированного сорбционного материала. Для получения гранул шлам с частицами размером от 0.01 до 0.09 мм смешивается с жидким натриевым стеклом при массовом и объемном соотношении 2 : 1. Термообработку проводят при температуре 250°С в течение 60 мин. Гранулы получают вручную окатыванием.
Гранулированный сорбционный материал имеет следующие технологические характеристики:
Суммарный объем пор, см3/г .....................0.450 |
Удельная площадь поверхности, м2/кг ...............................................................720 |
Прочность на истирание, % ............................78 |
Адсорбционная способность ГРСМ по отношению к катионам железа оценивалась на модельных растворах хлорида железа FeCl3. Эффективность очистки от ионов железа составила 92%. На рис. 1 показана изотерма адсорбции11 Fe3+ материалом ГРСМ из водных модельных растворов хлорида железа в статических условиях. При ее определении использовался метод переменных навесок и постоянной концентрации.
Выпуклая форма изотермы относится к I типу по классификации Брунауэра, Демина и Теллера и соответствует изотерме Ленгмюра L-типа по классификации Смита.
Для производственных процессов наибольшее значение имеет адсорбция ионов железа в динамических условиях, которая обладает существенными технологическими, эксплуатационными и экономическими преимуществами по сравнению с адсорбцией в статических условиях. Адсорбция в динамических условиях позволяет более полно использовать емкость сорбента. Процесс адсорбции ионов железа исследован на ГРСМ фракции 0.5–2.5 мм на лабораторной установке, представляющей собой фильтрационную стеклянную колонку диаметром 25 мм. Концентрация ионов железа в модельном растворе равнялась 1 мг/дм3 и являлась средней на входе в адсорбционный фильтр. Высота слоя загрузки составляла 20 см, масса – 56 г, скорость фильтрования – 3.5 м/ч. Проскок ионов железа фиксировался при концентрации в фильтрате Сф, равной 0.1 мг/дм3, и объеме очищенного модельного раствора 250 дм3. Получена кривая адсорбции катионов железа ГРСМ в динамических условиях (рис. 2).
В ходе эксперимента определены динамическая обменная емкость (ДОЕ) и полная обменная емкость (ПОЕ). Результаты эксперимента представлены в табл. 1.
Таблица 1.
Динамическая и полная обменные емкости ГРСМ по отношению к катионам железа
Показатель | Обменная емкость ГРСМ | |
---|---|---|
динамическая (ДОЕ) | полная (ПОЕ) | |
Емкость, мг/г | 133.9 | 276.8 |
Объем пропущенной воды, дм3 | 150 | 310 |
Время τ и коэффициент защитного действия слоя загрузки ГРСМ K рассчитаны по уравнению Шилова [5]: $\tau = KL - {{\tau }_{0}},$ где L – высота слоя загрузки ГРСМ, м; τ0 – потеря времени защитного действия слоя загрузки ГРСМ, ч. Получены следующие значения: τ = 70.5 ч, $K$ = 382.6 ч/м.
Фильтрат имеет рН = 6.8–7.5. После фильтрования через гранулы ГРСМ состав воды изменяется, поэтому проводился контроль воды по остаточной общей жесткости, рН, окисляемости и содержанию кремния. Эти показатели качества фильтрата должны изменяться в соответствии с ионным обменом между функциональными группами сорбционного материала и катионами железа. Выбор метода регенерации отработанного сорбционного материала зависит от эффективности очистки от катионов железа и технико-экономических показателей. Предусматривается регенерация материала разбавленным раствором серной кислоты Н2SO4 с нарастающей концентрацией от 0.5 до 2.5%, протекающим противопоточно производственному конденсату.
Для исключения вторичного загрязнения, привносимого материалом ГРСМ в фильтрат, определены показатели его качества при пропускании дистиллированной воды через фильтрующий слой, которые соответствуют показателям качества возвратного производственного конденсата (табл. 2).
Таблица 2.
Показатели качества фильтрата при фильтровании воды в динамических условиях через ГРСМ
Объем пропущенной воды, дм3 | Жесткость общая, мг-экв/дм3 | Щелочность общая, мг-экв/дм3 | Железо общее, мг/дм3 | Кремнесодержа-ние, мг/дм3 | Окисляемость, мг О/дм3 |
---|---|---|---|---|---|
Исходная вода | 2.21 | 1.51 | 0.16 | 0.31 | 7.0 |
0.2 | 2.1 | 5.87 | 1.72 | 1.25 | 6.8 |
0.4 | 2.1 | 4.11 | 0.92 | 0.1 | 2.0 |
0.6 | 2.1 | 1.22 | 0.28 | 0.1 | 2.0 |
1.0 | 0.05 | 1.11 | 0.12 | 0.1 | 2.0 |
10.1 | 0.05 | 1.12 | 0.1 | 0.1 | 2.0 |
Типовая схема очистки производственного конденсата предусматривает последовательное извлечение нефтепродуктов в отстойнике и обезжелезивание на механических, адсорбционных и ионообменных фильтрах (рис. 3).
Рис. 3.
Технологическая схема очистки возвратного производственного конденсата на Казанской ТЭЦ-1. 1 – отстойник; 2 – механический фильтр; 3 – адсорбционный фильтр; 4, 5 – ионообменные фильтры; 6 – бункер подачи сорбционного материала; 7 – бункер охлаждения и хранения готового сорбционного материала; 8 – муфельная печь; 9 – тарельчатый гранулятор
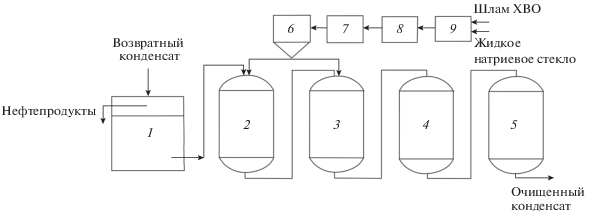
В адсорбционных фильтрах для очистки конденсата обычно применяется малозольный древесный активированный уголь марок БАУ и ДАК. Высота фильтрующего слоя составляет 1.5–2.0 м. Восстановление адсорбционной способности активированного угля в условиях эксплуатации ТЭС малоэффективно, так как связано с высокими финансовыми затратами и необходимостью расхода дорогостоящего фильтрующего материала, в качестве которого может быть использован антрацит.
Если по технологии использования пара конденсат не загрязняется нефтепродуктами, то механический фильтр заполняется сорбционным материалом, совмещая функции обезжелезивания и катионирования.
В технологии предлагается использовать ГРСМ для обезжелезивания и обессоливания производственного конденсата.
Линия производства сорбционного материала в технологической схеме включает следующие операции (см. рис. 3). Смешивание шлама с жидким натриевым стеклом и гранулирование происходят в тарельчатом грануляторе ГТ-0.6, предназначенном для получения гранул из сыпучих материалов. Гранулы имеют размер 0.5–2.5 мм, характеризуются прочностью на истирание 78% и средней гидрофильностью. Полученные гранулы выдерживаются в муфельной печи при температуре 250°С в течение 60 мин. После прокаливания гранулы поступают в бункер охлаждения и хранения, а затем в бункер подачи готового сорбента в адсорбер.
Рассчитанная себестоимость изготовленного ГРСМ составила 13.8 тыс. руб/т, себестоимость очистки возвратного производственного конденсата – 24.6 руб/м3. Экономическая оценка предотвращенного экологического ущерба от деградации почв и земель для Казанской ТЭЦ-1 производилась по временной методике Данилова-Данильяна и составила 1200 тыс. руб/год.
ВЫВОДЫ
1. Разработанная технология очистки производственного конденсата ТЭС гранулированным сорбционным материалом на основе карбонатного шлама позволяет проводить обезжелезивание конденсата и снижать концентрацию в нем железа в ионной коллоидной и грубодисперной формах до нормативных значений. Эффективность очистки превышает 92%.
2. Предложенная технология дает возможность получать гранулированный сорбционный материал на основе карбонатного шлама. Для ее реализации подобрано стандартное технологическое оборудование.
3. Проведенные экспериментальные исследования по изучению адсорбции ионов железа из модельных растворов в статических и динамических условиях гранулированным сорбционным материалом подтверждают высокую эффективность процесса. Время и коэффициент защитного действия слоя, рассчитанные по уравнению Шилова, составили τ = 70.5 ч, K = 382.6 ч/м.
Список литературы
Копылов А.С., Лавыгин В.М., Очков В.Ф. Водоподготовка в энергетике: учеб. пособие для вузов. М.: Изд-во МЭИ, 2003.
РД34. 37.515-93. Методические указания по очистке и контролю возвратного конденсата. Нормативные документы для тепловых электростанций и котельных. М.: ВТИ, 1998.
Николаева Л.А., Голубчиков М.А. Очистка производственных сточных вод от нефтепродуктов модернизированным сорбционным материалом на основе карбонатного шлама // Водоснабжение и санитарная техника. 2016. № 7. С. 51–58.
Николаева Л.А. Очистка сточных вод ТЭС от нефтепродуктов гидрофобным карбонатным шламом // Теплоэнергетика. 2020. № 10. С. 79–85. https://doi.org/10.1134/S0040363620100082
Касаткин А.Г. Основные процессы и аппараты химической технологии. М.: ТИД “Альянс”, 2006.
Дополнительные материалы отсутствуют.
Инструменты
Теплоэнергетика