Теплоэнергетика, 2022, № 1, стр. 32-50
Химические циклы сжигания и газификации топлив. Обзор исследований и новых технологических решений
Г. А. Рябов *
Всероссийский теплотехнический институт
115280 Москва, Автозаводская ул., д. 14, Россия
* E-mail: GARyabov@vti.ru
Поступила в редакцию 27.01.2021
После доработки 11.02.2021
Принята к публикации 17.02.2021
- EDN: TTTTRP
- DOI: 10.1134/S0040363621100064
Аннотация
Выполнен анализ современного состояния исследований и разработок по улавливанию CO2 в химических циклах сжигания и газификации топлив. Обобщены основные зарубежные публикации по данному вопросу. В настоящее время эта технология находится в стадии исследований на лабораторных и пилотных установках мощностью до 1 МВт. Показано, что технология сжигания и газификации в высокотемпературных химических циклах с оксидами металлов – носителями кислорода может быть эффективной по капитальным и эксплуатационным затратам. Суть этой технологии сводится к такой организации процесса горения, когда переносчиком кислорода к топливу является не воздух, а оксид металла. Последний при взаимодействии с топливом в топливном реакторе восстанавливается до металла (или более низкого оксида) с образованием СО2 и водяного пара. После этого металл окисляется в специальном реакторе и получившийся оксид вновь направляется в цикл. Выходящие из топливного реактора газы после конденсации водяного пара представляют собой практически чистый СО2, который может быть направлен на захоронение или утилизацию. Выполнены обзор и анализ данных по использованию различных оксидов металлов, особое внимание уделено исследованиям применения природных руд в качестве носителей кислорода. Показано, что для этой цели ильменит наиболее приемлем по свойствам (кислородная емкость, истираемость) и стоимости. Рассмотрены особенности конструкций и условий работы различных экспериментальных установок. Представлены основные подходы к расчету установок с химическими циклами. Показано, что важным для эффективной конверсии топлив помимо собственно свойств оксидов являются достаточное время пребывания частиц в реакторах и их удельная масса, которые во многом определяются гидродинамикой связанных между собой реакторов с кипящим и циркулирующим кипящим слоем. При этом необходимо обеспечить высокую кратность циркуляции частиц между реакторами, их эффективное улавливание в циклонах и надежное движение в опускных системах и пневматических затворах. Приведены результаты исследований гидродинамики связанных между собой реакторов и бинарных смесей частиц различной плотности.
Сжигание и газификация топлив в химических циклах – перспективная технология с минимальными выбросами вредных веществ и улавливанием СО2, которая является модификацией хорошо отработанной технологии циркулирующего кипящего слоя (ЦКС). Она предусматривает использование двух или нескольких связанных между собой реакторов с кипящим слоем (КС) и циркулирующим кипящим слоем. Такие реакторы применяются также в полигенерирующих системах с пиролизом (газификацией) и получением полезных продуктов (генераторный газ с высокой теплотой сгорания и оптимальным соотношением концентраций водорода и СО для реакции Фишера–Тропша с выделением компонентов моторных топлив). Суть технологии сжигания топлив в химических циклах с оксидами металлов – носителями кислорода (сhemical looping combustion – CLC) заключается в такой организации процесса горения, когда переносчиком кислорода к топливу является не воздух, а оксид металла (высокотемпературные химические циклы). Последний при взаимодействии с топливом в топливном реакторе восстанавливается до металла (или более низкого оксида) с образованием СО2 и водяного пара. После этого металл окисляется в воздушном реакторе и получившийся оксид вновь направляется в цикл. Выходящие из топливного реактора газы после конденсации водяного пара представляют собой практически чистый диоксид углерода, который может быть направлен на захоронение или утилизацию. В результате для сепарации СО2 от N2 энергия не требуется, именно поэтому потери на собственные нужды такой системы невелики и состоят в основном из затрат на сжатие СО2.
Схема процесса при сжигании газообразного топлива, включая продукты газификации твердых топлив, показана на рис. 1. В воздушном реакторе 1 с ЦКС происходят реакции окисления металлов М, а газовый поток, состоящий главным образом из азота с небольшим количеством кислорода и паров воды, направляется в котел-утилизатор или газовую турбину (при работе системы под высоким давлением). Частицы оксидов металлов ОМ выносятся потоком в верхнюю часть воздушного реактора, откуда попадают вначале в циклон 2 и далее в топливный реактор 3 с пузырьковым кипящим слоем, ожижающим агентом которого является газообразное топливо. В реакторе частицы оксидов металлов восстанавливаются до металлов и поступают через пневматический затвор 4 в воздушный реактор. Смесь газов, выходящая из топливного реактора, состоит из СО2 и водяного пара. Этот поток газов поступает в котел-утилизатор и далее направляется в конденсатор водяных паров, а осушенный СО2 подается на захоронение. В общем случае реакция восстановления выглядит следующим образом:
(1)
$\begin{gathered} \left( {{\text{2}}n + {\text{ }}m} \right){\text{ОM}} + {\text{C}}{{{\text{H}}}_{{\text{4}}}} \to \\ \to \,\,\left( {{\text{2}}n + m} \right){\text{M}} + m{{{\text{H}}}_{{\text{2}}}}{\text{O}} + n{\text{C}}{{{\text{O}}}_{{\text{2}}}}. \\ \end{gathered} $После восстановления металлы поступают в реактор 1 (см. рис. 1), где происходит их окисление с помощью воздуха или смеси кислорода с азотом с пониженным содержанием кислорода (около 5%):
Реакции происходят при температурах 800–1100°С с суммарным тепловым эффектом, равным тепловому эффекту при обычном сжигании топлива в воздухе. В качестве оксидов – переносчиков кислорода используют оксиды различных металлов, главным образом железа и никеля. В последнее время все чаще стали применять природные минералы, например ильменит, а также отходы металлургии.
В настоящее время, по данным [1], насчитывается уже более 600 работ, посвященных различным аспектам использования химических циклов. В ходе экспериментов было установлено, что возможно почти полное сжигание топлива при практически полном улавливании СО2. Многие работы направлены на исследование сжигания газа. Пока еще только на нескольких установках использовали твердое топливо [2]. Продолжительность эксплуатационного опыта в мире по сжиганию топлива в химических циклах, включающих носители кислорода с основой на оксидах никеля, железа, марганца, меди и кобальта, составляет более 9000 ч [3].
В последнее время значительный интерес проявляется к использованию при сжигании твердых топлив естественных дешевых минералов – ильменита и железомарганцевых минералов [4]. Для природного газа наиболее эффективными считаются композиты на основе оксидов никеля, железа и алюминия. Технология высокотемпературных химических циклов уже прошла стадию лабораторных исследований, и в ближайшее время намечено сооружение пилотных установок [4].
Активные исследования ведутся в области газификации с использованием химических циклов и разработки систем с получением водорода [5]. В связи с более широким, чем сжигание газообразного топлива, применением химических циклов в дальнейшем при описании процессов химического преобразования употребляется общий термин “конверсия”. Это определяется также фактически двумя разными процессами, протекающими в топливном и воздушном реакторах, которые нельзя объединить термином “сжигание”.
Существует множество модификаций химических циклов, включая паровой риформинг, карбонатные циклы очистки дымовых газов от СО2 и др. В обзоре рассмотрены вопросы выбора металлов – носителей кислорода для использования в химических циклах сжигания топлив с сепарацией CO2. Наибольший интерес представляют зарубежные данные по лабораторным установкам, стендам, а также требования к энергетическим установкам. Технология сепарации CO2 с использованием химических циклов основана на принципах псевдоожиженного слоя. Очевидно, что решение задач гидродинамики соединенных между собой аппаратов с кипящим слоем крайне необходимо для организации процесса сжигания топлив с сепарацией CO2 в химических циклах. Среди них основными являются правильный выбор режимов ожижения при заданных характеристиках частиц, определение расхода циркулирующих частиц и времени их пребывания в реакционных зонах, характеристик движения частиц в стояках и затворах, а также потерь давления.
Очевидно, что для условий России для снижения выбросов парниковых газов наиболее важно повышать эффективность сжигания органических топлив и использовать биомассу, нейтральную по выбросам СО2. Вместе с тем, изучение передового опыта в области улавливания СО2 и проведение собственных исследований актуальны прежде всего в научном плане. С учетом того что Россия подписала 22 апреля 2016 г. Парижское соглашение по климату, тематика обзора становится особенно актуальной. Важной является разработка принципиальных технологических решений при сжигании топлив в химическом цикле при умеренных капитальных и эксплуатационных затратах. Создание подобных установок в России позволит выйти на передовые рубежи исследований новых технологий, направленных на снижение выбросов парниковых газов и предотвращение глобальных изменений климата.
ОКСИДЫ МЕТАЛЛОВ – НОСИТЕЛИ КИСЛОРОДА
Одним из ключевых вопросов при организации химических циклов сжигания топлив является выбор состава смесей оксидов металлов – носителей кислорода. Эти смеси должны иметь высокую реакционную способность при восстановлении металлов на горючих газах (природном газе, продуктах газификации и т.п.). В качестве переносчиков кислорода используются оксиды различных металлов, главным образом железа, никеля и кобальта. Для повышения реакционной способности оксидов составляют композиты с оксидами алюминия, титана или магния, частицы которых имеют размеры от 100 до 250 мкм. Частицы не должны быть склонны к истиранию и агломерации при высоких температурах.
Некоторые результаты исследований свойств оксидов металлов приведены в [6]. В [7] представлены результаты реализации проекта INNOCUOUS по исследованию свойств оксидов металлов – носителей кислорода главным образом для использования в CLC-технологии с газовыми топливами, богатыми метаном. При этом важно было найти композиты оксидов с минимальной долей никеля. Испытания оксидов на основе кальция на лабораторных установках мощностью 10 и 120 кВт показали хорошие результаты. Полная конверсия метана достигалась при удельной массе оксидов 300–400 кг/МВт. Были также рассмотрены вопросы производства композитов на основе кальция и марганца.
Работа [8] посвящена исследованиям использования оксидов на лабораторном реакторе с КС при температурах 900–970°С в восстановительной и окислительной атмосферах при применении метана в качестве топлива. Кроме того, проведено сравнение скорости реакций газификации коксов для мексиканского нефтяного кокса и кокса древесины при использовании различных марганцевых руд и ильменита при температуре 970°С в среде, содержащей пары воды и азот в равных количествах. В этих условиях все марганцевые руды показали полную конверсию метана. Отмечена более высокая скорость газификации полукокса для марганцевых руд по сравнению с ильменитом.
Целью работы [9] было изучение эффективности процесса конверсии твердых топлив по технологии CLC, который называют Chemical-looping with oxygen uncoupling (CLOU). Процесс протекает в три этапа: газификация твердого топлива с образованием СО и H2 из летучих, производство кокса с определенной долей пор, выделение из оксидов кислорода, который реагирует с СО и Н2. Эксперименты проводили на лабораторной установке мощностью 1.5 кВт. Носителем кислорода служили частицы, содержавшие CuO концентрацией 60% (по массе), полученные распылительной сушкой. В качестве топлива использовали антрацит, битуминозный уголь с низким и средним содержанием летучих и лигнит. Температура в топливном реакторе изменялась от 900 до 950°C. Во всех экспериментах происходила полная конверсия угля до CO2 и H2O. Эффективность улавливания СО2 сильно зависит от сорта угля и температуры в топливном реакторе. Для лигнита была получена высокая эффективность улавливания СО2 – 99.3% при 950°C. При температуре 925°C удельная масса частиц – носителей кислорода, необходимая для достижения эффективности улавливания CO2 95%, составила, кг/(МВт · ч): 45 для лигнита, 85 для битуминозного угля со средним выходом летучих и 140 с низким выходом летучих, 490 для антрацита.
На 12-й Международной конференции по технологии кипящего слоя были представлены несколько докладов по новым исследованиям с использованием некоторых оксидов – носителей кислорода. В [10] рассмотрены возможности использования оксидов нового типа на базе меди – SrCuO2. Было выполнено сравнение этого оксида с соединением CuO/TiO2. Исследования проводили с помощью термогравиметрического анализа в условиях пяти циклов восстановления-окисления при температурах 600–800°С. При температуре 600°С кислородная емкость (доля отданного кислорода от массы оксида металла) составляла 8.02% и слегка увеличивалась с ростом температуры. Оказалось, что соединение SrCuO2 способно отдавать кислород и при температурах ниже 600°С. Преимуществом этого материала являлась его повышенная способность взаимодействовать с водородом в составе синтетического газа, получаемого при газификации биомассы. Высокая температура плавления SrCuO2 (1590°С) позволяет не опасаться возможной агломерации. Сравнение этого материала с соединением CuO/TiO2 показало, что последний обладает значительно меньшей циклической стабильностью.
В [11] представлены результаты исследования оксидов металлов на базе железа с поддержкой Al2O3, ZrO2, CeO2 при температуре 850°С и взаимодействии с СО. В топливный реактор подавали пар. Худшие результаты показал материал Fe2O3/Al2O3, который наиболее часто используют в качестве носителя кислорода при сжигании в химических циклах. Наилучшие реакционная способность и выход водорода наблюдались при использовании Fe2O3/ZrO2.
В [12] отмечается, что применение натуральных руд в CLC-процессах вызывает все больший интерес. Особенно это относится к сжиганию твердых топлив. Представлен обзор по использованию в различных установках железных, марганцевых, медных и кальциевых руд, а также их смесей. Отмечается, что при улучшении свойств оксидов металлов (повышение реакционной способности, стойкости к истиранию и способности длительно работать в системе) возрастает их стоимость, что сказывается на суммарных затратах на улавливание СО2 в химических циклах [13].
Руды являются естественным источником кислорода для производства оксидов. Если их использовать напрямую, то подготовка будет заключаться только в дроблении, рассеве с получением необходимых фракций и кальцинации. Некоторые руды содержат элементы, которые могут служить катализаторами в процессах газификации и шифт-реакции с водяным паром. Натуральные руды должны обладать достаточно высокой способностью к конверсии, прочностью и иметь высокое содержание кислорода (мощность выхода кислорода). Выход кислорода ${{R}_{{{{{\text{O}}}_{{\text{2}}}}}}}$ является одним из главных факторов и определяется следующим образом [14]:
где Wох – массовая доля кислорода в оксиде;(4)
${{R}_{{\text{О}}}} = {\text{ }}{{\left( {{{т}_{{ох}}} - {{т}_{{red}}}} \right)} \mathord{\left/ {\vphantom {{\left( {{{т}_{{ох}}} - {{т}_{{red}}}} \right)} {{{т}_{{ох}}}}}} \right. \kern-0em} {{{т}_{{ох}}}}}$– способность передачи кислорода (кислородная емкость); тох – масса полностью окислившейся частицы; тred – масса полностью восстановленной частицы.
Выход кислорода для натуральных руд несколько ниже, чем для оксидов и их композитов, но стоимость руд намного меньше. В табл. 1 приведен состав активных компонентов в рудах по данным [15]. Их доля может существенно различаться в зависимости от мест добычи.
Таблица 1.
Состав активных компонентов природных руд [15]
Носитель кислорода | Активный компонент | Состав, % | |||||
---|---|---|---|---|---|---|---|
CuO | Fe2O3 | Al2O3 | SiO2 | TiO2 | CaSO4 | ||
Хризоколла | CuO | 64.41 | 1.34 | 7.73 | 24.59 | 0.93 | – |
Куприт | Cu2O | 15.70 | 2.66 | 18.18 | 61.04 | 2.09 | – |
Малахит | CaO/Fe2O3 | 15.08 | 12.12 | 12.82 | 52.64 | 7.08 | – |
Гематит | Fe2O3 | 0.76 | 94.23 | 2.55 | 1.39 | 1.01 | – |
Ильменит | Fe2O3/TiO2 | 0.76 | 46.01 | 6.26 | 10.84 | 36.00 | – |
Лимонит | Fe2O3 | 2.18 | 66.97 | 8.78 | 18.11 | 3.79 | – |
Магнетит | Fe3O4 | 0.88 | 88.23 | 2.90 | 6.27 | 1.64 | – |
Таконит | Fe2O3 | 2.51 | 79.46 | 8.55 | 4.50 | 4.83 | – |
Ангидрит | CaSO4 | – | – | – | – | – | 94.32 |
Ильменит хорошо изучен как носитель кислорода в CLC-процессах, его цена относительно невелика (165 дол/т). Он не токсичен, хорошо дробится [16], его добывают в Австралии, Южной Африке, Китае, Канаде и России. Перед применением в качестве носителя кислорода его обрабатывают в воздушной среде при температуре 900–1200°С. Ильменит имеет высокую степень конверсии относительно водорода и оксида углерода, удовлетворительную степень истираемости (определяется экспериментально в режимах кипящего слоя по изменению массы во времени). Гематит и другие оксиды железа менее реакционны, особенно в отношении метана, кроме того, они истираются больше, но их стоимость ниже.
Марганцевые руды имеют больший выход кислорода, содержат 30–60% Mn2O3 в зависимости от места добычи, используются в металлургии, стоимость их относительно невысока (4.61 дол/т) [17]. Они могут служить носителями кислорода в системах с разделением кислорода CLOU, в которых сжигание топлива происходит в результате выделения газообразного кислорода из оксидов. Отмечается высокая истираемость таких руд и, соответственно, убыль материала с мелкими частицами. Однако низкая стоимость марганцевых руд позволяет считать их перспективным материалом для использования в химических циклах.
Носители кислорода на основе меди обладают высокими скоростями реакций восстановления и окисления и способностью переносить кислород без термодинамических ограничений. Эти оксиды легко выделяют кислород, что приводит к росту конверсии твердого топлива. Цена на эту руду самая высокая из рассмотренных естественных оксидов, она сильно зависит от колебаний стоимости металлической меди и по данным [18] составляет около 1600 дол/т.
Натуральный гипс является недорогим носителем кислорода для систем CLC. В окисленном состоянии он экологически безвреден и имеет высокий выход кислорода [19]. Оксиды на основе кальция могут агломерировать и не являются достаточно стабильными.
Большинство исследованных смесей руд – носителей кислорода содержали ильменит и дополнительные минералы. В [20] исследовали применение смеси ильменита с марганцевой рудой, что позволило увеличить степень конверсии газа с 84.2 до 91.5% и улучшить конверсию твердых топлив.
В [12] приведена сравнительная матрица (табл. 2), составленная по результатам сравнения руд и оксидов – переносчиков кислорода.
Таблица 2.
Сравнительные показатели руд и чистых оксидов
Фактор сравнения | Руда | Оксид на основе | |||||||
---|---|---|---|---|---|---|---|---|---|
железа | марганца | меди | кальция | железа | марганца | меди | кальция | ||
ильменит | Fe2O3 | Mn3O4 | CuO | CaSO4 | |||||
Конверсия топлива: | |||||||||
синтетический газ | +/– | + | + | +/– | +/– | + | + | + | + |
CH4 | +/– | +/– | +/– | +/– | +/– | +/– | – | + | +/– |
уголь | + | +/– | + | +/– | + | + | +/– | + | +/– |
Физические свойства: | |||||||||
агломерация | + | +/– | – | +/– | + | +/– | + | +/– | +/– |
спекание | + | + | +/– | +/– | + | + | +/– | – | +/– |
истирание | +/– | – | +/– | + | + | + | +/– | +/– | + |
Другие факторы: | |||||||||
выход O2 | +/– | +/– | + | + | +/– | +/– | + | + | + |
стабильность | + | +/– | + | – | + | + | +/– | + | – |
цена | + | + | +/– | + | + | +/– | – | – | + |
легкость подготовки | + | + | + | + | + | – | – | – | +/– |
Таким образом, по данным [12–20] можно заключить, что руды, обладая меньшими реакционной способностью и выходом кислорода, но низкой стоимостью, являются перспективными материалами для использования в системах сжигания твердых топлив и продуктов газификации. При этом ильменит представляется наилучшим природным минералом во многом благодаря своей механической прочности и стабильности (способности длительно работать в циклах восстановление-окисление). Смешанные руды и руды с незначительными модификациями состава показали повышенную эффективность в улавливании СО2 и являются устойчивыми носителями кислорода.
При сжигании природного газа наиболее эффективны композиты на основе соединений Ni и Fe, но они дороги и могут негативно влиять на экологию и здоровье людей. Для использования в химических циклах наиболее подходящими являются композиты оксидов металлов, размер частиц которых составляет 0.10–0.15 мм.
ЭКСПЕРИМЕНТАЛЬНЫЕ И ПИЛОТНЫЕ УСТАНОВКИ
Для исследования свойств оксидов металлов, их сравнительной реакционной способности и эффективности улавливания СО2 часто применяют лабораторные кварцевые термобалансные реакторы периодического действия с продувкой горючим газом, азотом и воздухом [21–23]. Типичная мощность лабораторных установок со связанными между собой реакторами составляет примерно 10 кВт [24–26]. Крупные установки тепловой мощностью около 100 кВт работают в Швеции [27, 28], Австрии [29], Испании и Китае. Уже несколько лет ведутся исследования на пилотной установке мощностью 1 МВт в Германии [30], газификация биомассы в химических циклах с использованием ильменита выполнена на крупной установке мощностью 2–4 МВт в университете Чалмерса (Гётеборг, Швеция) [31], проведены эксперименты по сжиганию топлива под давлением [32]. Наибольший интерес представляют конструкции относительно крупных пилотных установок и результаты работ, выполненных на них.
Важные данные были получены в Венском техническом университете на установке мощностью 120 кВт, схема которой показана на рис. 2 [29]. Установка состоит из восстановителя 1 (топливного реактора), окислителя 2 (воздушного реактора), верхнего и нижнего петлевых затворов, внутреннего петлевого затвора 4 и циклонов 3. В установке организованы главный и локальный контуры циркуляции. Главный контур включает в себя восстановитель и окислитель, циклон, верхний и нижний петлевые затворы. Локальный контур циркуляции состоит из восстановителя, циклона и внутреннего петлевого затвора. Окислитель работает в транспортном режиме ожижения, восстановитель − в режиме турбулентного ожижения. Циклон и внутренний петлевой затвор расположены рядом с восстановителем, что позволяет организовать циркуляцию частиц независимо от главного контура циркуляции. Материал в реакторе-окислителе ожижается воздухом, в реакторе-восстановителе – топливом (газом) с подводом ожижающих агентов под слой. В окислителе организована подача вторичного воздуха (половина общего количества воздуха). При фиксированном расходе воздуха повышение доли первичного воздуха приводит к увеличению кратности циркуляции и наоборот. Для ожижения петлевых затворов используется водяной пар. Несмотря на то что эта установка похожа на установки в университетах Чалмерса (Швеция) и Сарагосы (Испания), режимы ожижения (турбулентный или пузырьковый), в которых работает восстановитель, различаются.
Рис. 2.
Схема экспериментальной установки со связанными реакторами мощностью 120 кВт (г. Вена, Австрия) [29]
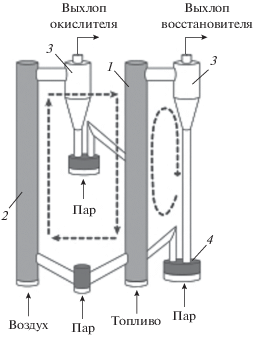
Опыты при мощности 140 кВт и избытке воздуха 1.1 показали, что повышение температуры в восстановителе приводит к увеличению конверсии и выхода СО2. При температуре в восстановителе 977°С конверсия метана составила 98%, выход СО2 – 94%. В другой серии опытов исследовали влияние расхода топлива на конверсию метана и выход СО2 при мощности 55–144 кВт. При повышении мощности увеличивается скорость газов и улучшается взаимодействие между газом и частицами в восстановителе. При мощности стенда 140 кВт масса загрузки оксидов составила около 240 кг/МВт, что соответствует удельному расходу материала (на площадь реактора) 1.4 кг/(с · МВт) или 41 000 т/ч для установки мощностью 1000 МВт. Во время экспериментов максимальный удельный расход частиц в окислителе составлял 90 кг/(м2 · с).
Важные исследования проводились на установке мощностью 100 кВт (т.) в университете Чалмерса (Швеция) [28]. Установка состоит из двух связанных реакторов – топливного и воздушного, а также декарбонизатора, предотвращающего проскок углерода в воздушный реактор. В качестве переносчика кислорода использовали оксид железа, в качестве топлива – древесный и каменный угли (пыль и крупные частицы). Ранее в качестве переносчика кислорода применяли ильменит, при котором степень конверсии была ниже, чем при оксиде железа. Максимальная степень конверсии (87%) была получена при работе на каменном угле. Однако размер частиц оксида железа меньше, чем размер частиц ильменита, и поэтому происходил их постоянный унос. Примерно 1 раз в час производили дополнительную подачу оксида железа в установку для стабилизации массы загруженного материала и, как следствие, циркуляции. Результаты проведенных экспериментов показали, что основное влияние на конверсию оказывают температура в реакторе, перепад давления в нем и расход циркулирующих частиц.
В университете г. Дармштадт (Германия) находится установка для сжигания топлива в химическом цикле мощностью 1 МВт (т.) (рис. 3) [30]. Воздушный и топливный реакторы являются связанными между собой реакторами с циркулирующим кипящим слоем. Оба реактора имеют обмуровку для снижения тепловых потерь и возможность работать в автотермическом режиме, т.е. без подвода дополнительного тепла от электронагревателей, как это делается на установках меньшей мощности. Воздушный реактор спроектирован на температуру 1050°С и ожижается воздухом, который подогревается электронагревателем до 350°С. Частицы оксида металла подаются в топливный реактор с помощью L-клапана или транспортера, подключенного к петлевому затвору. Топливный реактор спроектирован на температуру 970°С, и ожижение может осуществляться смесью газов (водяной пар, воздух, СО2), предварительно подогретой до 450°С. Расход твердого топлива составляет 150 кг/ч, что соответствует тепловой мощности 1 МВт. Топливо подается в опускной стояк топливного реактора. Уходящие газы после топливного реактора проходят камеру дожигания, в которую поступают кислород для организации горения СН4, а также оксид углерода и водород. Газы после реакторов охлаждаются в теплообменниках, очищаются в рукавных фильтрах и затем выбрасываются в атмосферу через дымовую трубу. Отделение частиц кокса от частиц оксида металла происходит в два этапа. В циклоне пониженной эффективности не улавливаются легкие частицы кокса крупных фракций. Этот кокс уносится потоком продуктов сгорания в циклон повышенной эффективности, где частицы сепарируются и подаются обратно в топливный реактор. Мелкие частицы кокса, уловленные в циклоне пониженной эффективности, подаются в специальный разделитель, который ожижается паром. Более легкие частицы кокса подхватываются потоком газа и уносятся в топливный реактор, в то время как более тяжелые частицы оксида металла подаются в воздушный реактор для последующего окисления.
Рис. 3.
Схема экспериментальной установки мощностью 1 МВт (т.) университета г. Дармштадт (Германия). 1 – вентилятор; 2 – фильтр; 3 – теплообменник; 4 – циклон; 5, 6 – воздушный и топливный реакторы; 7 – L-клапан, транспортер; 8 – отделитель углерода
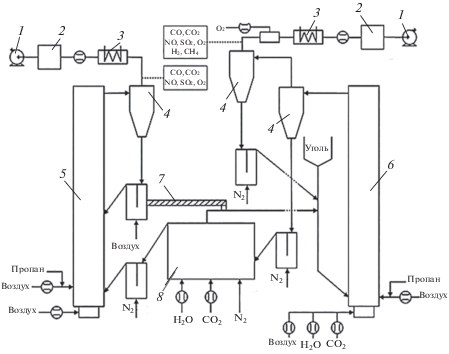
Опыты проводили с угольной пылью (фракция не более 125 мкм) и кусковым углем (размер частиц до 8 мм). На выходе из топливного реактора концентрация, %, составляла:
СН4 (в пересчете на сухие газы) .............2.1–2.9 |
Н2 ............................................................4.0–6.0 |
СО ............................................................3.7−5.1 |
СО2 (при ожижении смесью Н2О + N2) ...20–27 |
При ожижении слоя в топливном реакторе диоксидом углерода его концентрация на выходе из реактора равнялась 35–40%. Концентрация кислорода, необходимая для полного сгорания летучих, составляла 16–29% в зависимости от режима работы.
На рис. 4 показана зависимость массовых расходов G пропана, подаваемого в воздушный реактор, СО2 для ожижения слоя в топливном реакторе и угля, а также температуры t в топливном и воздушном реакторах от времени эксперимента τ. Относительно высокая концентрация метана на выходе из топливного реактора 2.1–2.9% объясняется малым временем взаимодействия летучих с переносчиком кислорода, так как уголь в реактор подается на отметке 0.69 м над уровнем решетки реактора. Содержания водорода (4.0–5.2%) и оксида углерода (4–5%) в первые 3 ч работы установки были практически неизменными. При переходе с ожижения смесью газов, состоящей из СО2, N2 и пара, к ожижению смесью из N2 и пара концентрация водорода увеличилась, но снизилась концентрация оксида углерода. Концентрация СО2 при ожижении дополнительным СО2 составляла 35−40%, при ожижении только паром и азотом − 20–27%.
Рис. 4.
Зависимость расхода СО2 (1), СН4 (2), угля (3) и температуры в топливном (4) и воздушном (5) реакторах от времени работы установки университета г. Дармштадт (Германия)
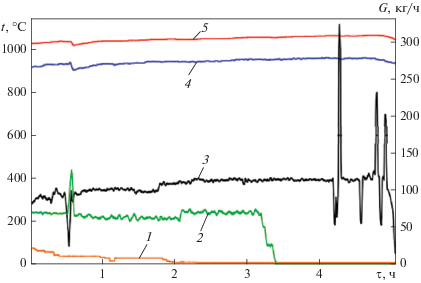
Гидравлическое сопротивление в реакторах Δр при проведении опытов было примерно постоянным: в топливном реакторе 6.0, в воздушном реакторе 9.0 кПа. Масса загруженного материала в топливном реакторе составляла 75 кг, в воздушном реакторе – 260 кг. Удельная масса загруженного материала изменялась в диапазоне 80–120 кг/МВт (т.) в зависимости от расхода угля.
Потребность кислорода, т.е. доля кислорода, недостающая для полного сгорания газов, которые образовались при пиролизе и газификации, для полной конверсии газов составила 16–20% при ожижении дополнительным СО2 и 28–30% при ожижении паром, эффективность улавливания СО2 была равна примерно 45%.
На установке мощностью 100 кВт (т.) в университете Чалмерса (Швеция) потребность в кислороде составляла 15−24% (каменный уголь/ильменит). Для сравнения, загрузка реактора в установке мощностью 1 МВт (т.) была значительно ниже – около 100 кг/МВт (т.) при Δр = 7.0 кПа против 380 кг/МВт (т.) при Δр = 20.0 кПа в установке мощностью 100 кВт (т.). Такая малая загрузка вместе с пониженной температурой (920–950°С) может обусловливать более высокую потребность в кислороде в топливном реакторе. Увеличение удельной загрузки, вероятнее всего, приведет к дальнейшему снижению потребности в кислороде. Низкую эффективность улавливания СО2 можно объяснить отсутствием сепарации углерода и внутренней рециркуляцией в топливном реакторе.
ГИДРОДИНАМИКА ПОТОКОВ ЧАСТИЦ В СВЯЗАННЫХ МЕЖДУ СОБОЙ РЕАКТОРАХ
Как показывает опыт сжигания различных топлив по CLC-технологии, помимо массы и свойств частиц – носителей кислорода важнейшим является обеспечение надежной и полной циркуляции частиц между реакторами. Поэтому исследованиям гидродинамики связанных один с другим реакторов уделяется большое внимание. Кратность циркуляции частиц по отношению к расходу воздуха (или расходу метана) уменьшается при увеличении емкости оксидов по кислороду, так как Cox пропорционально RО (здесь Cox – концентрация окислившихся частиц). В то же время расход частиц не является параметром, зависящим от химических процессов, а определяется скоростью газа, его физическими свойствами, размером и плотностью частиц. Кроме того, необходимо учесть и эффективность улавливания частиц в сепараторе.
Авторы [33] считают, что для оксидов на основе никеля (60% NiO и 40% поддержки, необходимой для механической стабильности частиц) требуется расход циркуляции от 1 до 4 кг/(с · МВт), для оксидов железа – еще больше. При расчете мощности с учетом расхода и теплоты сгорания метана следует применять кратность циркуляции по отношению к метану, равную 300–1200. В [33] указывается на необходимость проведения предварительных экспериментов по гидродинамике реакторов и рассматриваются вопросы моделирования на аэродинамических установках. В аэродинамической модели [33], имеющей размер 19 × × 19 мм (19 × 27 мм в нижней части) и высоту около 1600 мм, применяли частицы катализаторов крекинга плотностью 2500 кг/м3 (насыпная масса 1500 кг/м3) и средним размером 0.07 мм. С ростом скорости в воздушной части перетока и ожижения в нем расход циркуляции увеличивался. На рис. 5 показано распределение давления р в разных зонах по высоте установки h. В верхней части опускного стояка (уровень слоя в стояке) давление мало, затем оно возрастает и достигает максимума ниже зоны перетока. В нижней части воздушного реактора находится зона турбулентного слоя. Такие закономерности являются типичными для переточных установок такого рода.
Интерес представляют также исследования влияния различных факторов на движение частиц в связанных между собой реакторах, выполненные на лабораторных установках [34, 35] и относительно крупных моделях [36, 37]. Интересные исследования проведены в Техническом университете Вены [38–40], и предложено оригинальное решение для реактора с ЦКС с установкой турбулизаторов потока. В работах университета в Неаполе представлены результаты исследования гидродинамики систем с пиролизом [41] и описано влияние режимных факторов на условия движения частиц [42]. Гидродинамика системы со связанными реакторами с КС и ЦКС рассмотрена в работе исследователей из Кореи [43] и работах Пекинского университета Синьхуа [44].
В системах со связанными между собой реакторами большое значение имеет организация перетоков между ними. В этом плане важен опыт исследований движения частиц в опускных стояках и пневмозатворах, результаты которых представлены в работах [45–47]. При конструировании новых систем крайне важным является расчет контура циркуляции частиц топка − циклон – система возврата материала в топку, для систем со связанными реакторами с контуром реактор с ЦКС – циклон – переток в реактор с кипящим слоем – реактор с кипящим слоем важен расчет возврата материала в реактор с ЦКС. Этот расчет заключается в определении расхода материала в системе, перепадов давлений в реакторах и системе возврата уловленных частиц, сопротивления циклонов и уровня слоя в стояках под циклонами в зависимости от скоростей газов в реакторах и подачи газа в пневматические клапаны. При этом необходимо учитывать материальный баланс в элементах системы при примерно постоянной массе материала в контуре циркуляции, особенности гидродинамики в элементах системы (подъемное движение в турбулентном слое и разбавленной фазе в реакторе с ЦКС, опускное движение в плотном и переходном к ожиженному режимах движения в стояках и перетоках и движение в режиме пузырькового слоя в реакторе с КС) и режимы работы пневматических затворов.
Сотрудники Всероссийского теплотехнического института выполнили экспериментальные исследования гидродинамики потока частиц в связанных между собой реакторах и разработали методы расчета таких систем [48–52]. Для расчета контура циркуляции частиц существенным является установление связи между расходом циркулирующего материала, полученным в результате расчета реактора с ЦКС по характеристикам материала и газа при определенном перепаде давлений в реакторе (массе слоя в реакторе с ЦКС), аэрацией в затворе и уровнем слоя в стояке затвора. При этом соблюдается материальный баланс, изменение уровня слоя в стояке приводит к изменению массы слоя в реакторе с ЦКС, а сумма масс материала в реакторе и системе возврата (в основном в стояке) остается постоянной.
Методика расчета гидродинамики аппаратов с ЦКС заключается в определении аксиального профиля концентрации по высоте реактора и удельного расхода материала с учетом внутренней циркуляции из-за сепарации части материала в зоне потолка топки. Результаты расчета дают зависимость этого профиля от массы слоя в реакторе, скорости газа и физических параметров газа и частиц. По этой же методике проводится определение удельного расхода материала в реакторе. Расход материала по внешнему контуру в первом приближении вычисляется по заданной массе слоя, скорости газа в реакторе при плотности потока в верхней части реактора (в формулы из работ [49, 50] подставляется полная высота реактора) и КПД потолка реактора 50%. Сопротивление циклона принимается равным 1–2 кПа. Для того чтобы замкнуть контур циркуляции, необходимо составить уравнения связи между расходом материала, уровнем слоя в стояке и подачей газа в затвор, используя подходы, изложенные в [46, 47].
Как показывают данные вариантных расчетов, принятые подходы к оценке эффективности улавливания частиц в зоне выхода из топки дают максимальную относительную погрешность не более 7%, что вполне приемлемо в сравнении с опытными данными. Сравнивая расходы газа, которые требуются для начала движения в L-клапане и петлевом затворе, легко установить, что расход газа в петлевой затвор заметно выше, так как необходимая скорость газа всегда превышает скорость минимального псевдоожижения, тогда как в L-клапане она может быть ниже скорости минимального псевдоожижения.
Связь между циклоном реактора с ЦКС и реактором с КС в экспериментальной установке осуществляется с помощью L-клапана, а возврат частиц из реактора с КС в реактор с ЦКС – через петлевой затвор. Наибольшие давления в системе относятся к точке ввода воздуха в L-клапан р15 и точке подвода воздуха в петлевой затвор р21. Данные по изменению этих давлений в зависимости от суммы перепада давлений в топке и сопротивления циклона Δрсум приведены на рис. 6. С ростом Δрсум (с увеличением массы слоя в реакторе с ЦКС) давление р15 снижается, а р21 увеличивается. Несмотря на значительный разброс опытных точек, зависимости давлений близки к линейным.
Рис. 6.
Зависимости давлений в точках подвода воздуха в L-клапан р15 (1) и затвора реактора с КС р21 (2) от суммы перепада давлений в реакторе с ЦКС и сопротивления циклона
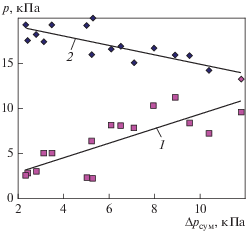
Сумма давлений р15 и р21 (около 23 кПа) практически не меняется во всех режимах и характеризует работу всего контура со связанными между собой реакторами при постоянных массе и физических характеристиках материала и газа. Этот факт, новый метод расчета, удовлетворительно описывающий изменение давления в системе, а также зависимости в начале движения в опускных системах с L-клапаном, разработанные в ВТИ, являются одними из первых в мире.
В последнее время специалисты ВТИ выполнили исследования гидродинамики бинарных систем, которая ранее не была хорошо изучена [53–56]. При моделировании условий движения бинарных смесей, состоящих из тяжелых оксидов металлов и относительно легких частиц золы, были учтены результаты исследований по CLC-технологии на холодной модели системы связанных между собой реакторов. Были определены поля массовых потоков частиц в верхней части реактора с ЦКС с помощью S-образного пробоотборного зонда. По результатам отборов были исследованы подъемные, опускные и суммарные массовые потоки частиц, затем выполнен анализ фракционного состава подъемных потоков в центре установки и опускных потоков у стен. Доли оксидов алюминия и песка в отобранных пробах определены с помощью рентгенофазового анализа на приборе VRA-30 с предварительной тарировкой на чистом оксиде алюминия и песке.
Средний размер частиц оксидов алюминия в этих опытах составил 0.236 мм, истинная плотность – 3940 кг/м3, насыпная плотность – 1970 кг/м3. В процессе опытов поддерживали постоянной массу материала в реакторе с ЦКС (40–45 кг). Первоначально опыт проводили на чистом оксиде алюминия, затем в установку добавляли около 1.5 кг песка (средний размер частиц 0.22 мм, истинная плотность 2600 кг/м3, насыпная плотность 1560 кг/м3). Исследования были проведены при скоростях воздуха в реакторе с ЦКС 3.6 и 4.3 м/с, доля песка от общей массы материала составляла 3.5–11.0%.
Результаты исследования показали снижение скорости минимального псевдоожижения при небольшой первоначальной добавке песка. Зависимость относительного градиента давлений от объемной доли тяжелых частиц носит линейный характер. При массовой доле песка 3.5–12.0% добавка его не оказывает существенного влияния на профиль суммарных массовых потоков в зоне выхода из реактора с ЦКС. Полученные данные свидетельствуют о том, что для исследованной области долей легкой фракции расчет гидродинамики реактора с ЦКС можно проводить, как для фракции оксидов металлов, с использованием разработанных ранее зависимостей. Фракционный состав всех проб из подъемного потока в центре реактора с ЦКС и опускного потока у стен располагался на единой кривой, что характерно для режима ЦКС с одинаковыми плотностями частиц. Средний размер отобранных частиц лишь немного меньше среднего размера частиц Al2O3. В подъемном потоке в центре реактора доля песка несколько выше, чем в опускном потоке, и выше средних значений по массовой засыпке в реактор. При этом с увеличением скорости разница концентраций немного снижается.
В процессе исследований также было изучено влияние массовой концентрации частиц на входе в циклон на эффективность их улавливания и сопротивление циклона. С ростом массовой концентрации сопротивление циклона снижается, что обусловлено уменьшением крутки потока и перераспределением кинетических энергий газа и твердой фазы. По данным автора, значение поправки на запыленность потока составляет 0.4–0.6 и увеличивается с повышением массовой концетрации до 0.8. Влияние доли легкой фракции (песка) не обнаружено.
Для расчета поправки на запыленность предложены несколько зависимостей. Наиболее представительная форма зависимости дает значение поправки, равное 1.0 при чистом потоке газа, при этом достигается минимум поправки при массовых концентрациях около 0.3 и дальнейший рост ее значения с повышением концентрации [57]. В работе [58] анализируются зависимости для расчета поправки на запыленность. Данные автора и [58] обобщаются единой зависимостью
(5)
$\psi = \frac{{\text{1}}}{{{\text{3}}{\text{.1}}{{\mu }^{{{\text{0}}{\text{.7}}}}} + {\text{1}}}} + {\text{0}}{\text{.67}}\mu {\text{,}}$Эффективность улавливания частиц в циклоне оказалась очень высокой (более 99.99%), что связано с их большими размерами и высокой концентрацией. Поэтому анализировать влияние факторов на КПД циклона лучше через унос. На рис. 7 показана зависимость относительного уноса частиц 1–η (здесь η – КПД) от их массовой концетрации μ. Унос заметно снижается при повышении концентрации, так как образуется сплошной поток струй и мелкие частицы увлекаются более крупными к стенке циклона [59].
Таким образом, можно заключить, что исследования гидродинамики связанных между собой реакторов являются весьма актуальными, особенно с учетом появления новых схем с различным расположением реакторов, увеличением числа реакторов до трех при получении водорода.
РАСЧЕТ И ПРОЕКТИРОВАНИЕ ЭНЕРГЕТИЧЕСКИХ УСТАНОВОК И ИХ ТЕХНИКО-ЭКОНОМИЧЕСКИЕ ПОКАЗАТЕЛИ
При проектировании установок с химическими циклами важно рассчитать некоторые параметры, которые необходимы для вычисления массы материала и кратности циркуляции [22]. Первый параметр − это кислородная емкость частиц. Другой параметр, характеризующий степень окисления переносчика кислорода в химическом цикле, − это степень конверсии оксида металла Х. Она определяется как отношение массы кислорода, перенесенного конкретной частицей, к массе кислорода, переданного полностью окислившейся частице, по формуле
где m – масса частицы оксида металла после реакции окисления.Степень окисления частицы металла может характеризоваться массовой конверсией ω:
(7)
$\omega = {m \mathord{\left/ {\vphantom {m {{{m}_{{ox}}}}}} \right. \kern-0em} {{{m}_{{ox}}}}} = {\text{1}} + {{R}_{{\text{О}}}}{\text{(}}X--{\text{1)}}.$Массовая конверсия частиц металла может быть выражена через производную dω/dt. Все вышеупомянутые параметры, измеренные в лабораторных условиях, позволяют оценить необходимую массу слоя материала для каждого реактора mсл и кратность циркуляции частиц mц в установке по следующим формулам:
(8)
${{m}_{{{\text{сл}}}}} = \frac{{\omega {{m}_{{\text{О}}}}}}{{{\text{d}}\omega {\text{/d}}t}}{\text{;}}$Большее значение Δω соответствует более полному использованию кислородной емкости частиц металла в окислительно-восстановительных реакциях. Стоит отметить, что масса слоя обратно пропорциональна степени массовой конверсии, а кратность циркуляции обратна пропорциональна степени массовой конверсии Δω.
Представленные данные показывают, что масса загрузки и кратность циркуляции являются очень важными показателями. Для химического цикла с ЦКС мощностью 1000 МВт (т.) общая масса загрузки составляет 400−2500 т, соответствующая кратность циркуляции равна 3600–30 000 т/ч. Наличие очень большого количества сыпучих материалов обусловливает главную проблему коммерческого химического цикла с ЦКС – обеспечение надежной циркуляции. В [60] указывается, что при требуемой массе загрузки 100–200 кг/МВт (т.) оценочная стоимость частиц металла составит 5.2 дол/кг (4 евро/кг). В [61] приводится также кратность циркуляции, необходимая для организации адиабатного режима работы, которая составляет 4 кг/[с · МВт (т.)], если принять разницу массовой конверсии равной 0.2.
По одной из европейских программ в настоящее время разработана концепция проекта ТЭС с ЦКС по сравнению с другими чистыми угольными технологиями. На рис. 8 показана технологическая схема ТЭС Greenfield мощностью 455 МВт со сжиганием топлива в химических циклах. Затраты на сооружение ТЭС и стоимость выработанной электроэнергии подтвердили экономическую жизнеспособность данной технологии на ТЭС Greenfield.
Рис. 8.
Технологическая схема ТЭС с сжиганием топлива в химическом цикле. 1 – дымовая труба; 2 – фильтр; 3 – конвективная шахта; 4, 5 – воздушный и топливный реакторы; 6 – циклон; 7 – скруббер; 8 – охладитель газов; 9 – дополнительный очиститель потока СО2
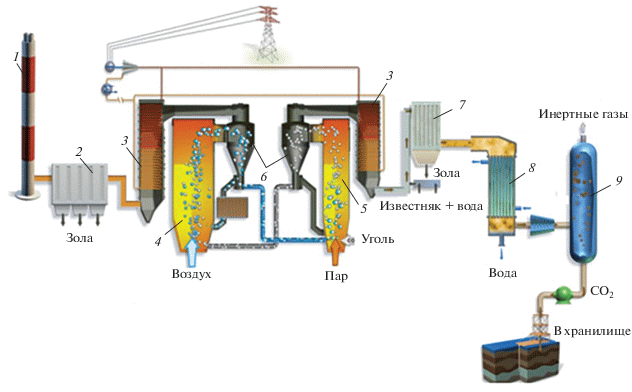
Сжигание в химическом цикле имеет некоторое сходство с обычным сжиганием топлива в циркулирующем кипящем слое. На рис. 9 показаны компоновки котла с ЦКС и котла с химическим циклом. В [62] рассмотрены основные сходства и различия двух технологий сжигания применительно к котлам мощностью 1000 МВт (т.):
Рис. 9.
Компоновки котлов с ЦКС (а) и химическим циклом сжигания топлива (б). 1 – топка, вид сверху; 2 – топка, вид по ширине; 3 – топка, вид по глубине; 4, 5 – воздушный и топливный реакторы, вид сверху; 6, 7 – воздушный и топливный реакторы, вид по ширине и глубине
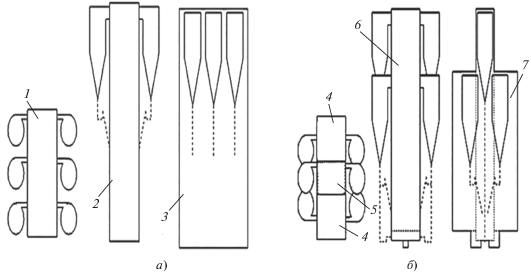
одинаковая площадь поперечного сечения реакторов, так как используются близкие скорости ожижения;
топочная камера установки с химическим циклом разделена на три части с топливным реактором в центре между двумя воздушными реакторами;
одинаковое количество циклонов, отвод материала из всех циклонов осуществляется в топливный реактор. Материал после четырех циклонов воздушного реактора вводится выше уровня слоя, тогда как материал от двух циклонов топливного реактора вводится под слой;
циркулирующий материал по каналу под реакторами подается от топливного реактора к воздушным реакторам;
топливный реактор и топка с ЦКС имеют почти одинаковую высоту (для обеспечения максимального выгорания коксовых частиц);
воздушный реактор имеет меньшую высоту, так как начиная с определенной высоты гомогенные реакции в газовой фазе не происходят. Меньшая высота реактора позволяет получить большую кратность циркуляции;
затраты на топливный реактор выше, так как требуется тепловая изоляция стен, которые участвуют в генерации пара. В то же время в воздушном реакторе коэффициент теплопередачи почти вдвое выше из-за более высокой температуры, что позволяет уменьшить площадь поверхности теплообмена;
на рис. 9 не показаны камеры дожигания после топливного реактора. Кислород можно подавать в выходные части циклонов и в переходные патрубки циклонов, которые могут работать как камеры дожигания;
топливный реактор будет иметь большую высоту слоя для обеспечения более полной конверсии и достаточного времени для газификации кокса. В воздушном реакторе требуется несколько меньшая высота слоя. Под воздушного реактора расположен выше пода топливного реактора, чтобы избежать нежелательного скачка давления в воздушном реакторе.
Основные затраты на установку с химическим циклом не зависят от стоимости котла. Наибольшие затраты связаны с компрессией полученного СО2, что традиционно для всех технологий улавливания СО2. На втором месте – затраты на приготовление кислорода в воздухоразделительных установках. При степени конверсии 85−95% потребность в кислороде составляет 5−15% количества кислорода, необходимого при чисто кислородном сжигании. Другие затраты связаны с обмуровкой топливного реактора и ожижением слоя материала паром, а также с размолом топлива. Общие затраты на улавливание СО2 могут составлять 16 – 26 евро/т СО2 в зависимости от степени конверсии в топливном реакторе и жизненного цикла оксида металла.
В табл. 3 представлена оценка дополнительных затрат на связывание СО2.
Таблица 3.
Оценка дополнительных затрат на установку с химическим циклом
Статья затрат | Удельные затраты на связывание СО2, евро/т СО2 | Диапазон удельных затрат, евро/т СО2 | Снижение КПД, % |
---|---|---|---|
Компрессия СО2 | 10.0 | 10.0 | 3.0 |
Подготовка кислорода | 6.5 | 4.0−9.0 | 0.5 |
Сооружение котла | 1.0 | 0.2−2.2 | − |
Носитель кислорода | 2.0 | 1.3−4.0 | − |
Ожижение топливного реактора | 0.8 | 0.8 | 0.8 |
Размол угля | 0.2 | 0.2 | 0.1 |
В [62] указывается на существенные различия между традиционным сжиганием топлива в ЦКС и сжиганием в химическом цикле. Размер частиц топлива не должен быть большим, чтобы обеспечить их газификацию до того, как они попадут в воздушный реактор. Ввод топлива необходимо осуществлять в нижнюю часть слоя топливного реактора для того, чтобы летучие смогли прореагировать с носителем кислорода. Меньший размер частиц также обусловливает и быстрый выход летучих (в течение примерно 1 с) при вводе топлива в слой.
В [63] рассматриваются вопросы проектирования установок на основе оксидов металлов, в частности оксида меди. Эта разработка была выполнена применительно к созданию пилотной установки мощностью 10 МВт для сжигания газов в химических циклах. По результатам работы было отмечено, что при проектировании систем с химическими циклами важным является поддержание определенного количества материала в топливном и воздушном реакторах, а также высокого расхода материала между ними. Количество требуемого материала зависит не только от реакционной способности носителей кислорода, но и от гидродинамических характеристик реакторов. Количество материала в воздушном реакторе в большинстве случаев должно быть больше, чем в топливном реакторе. Требуемое количество материала в системе должно быть выше расчетного в соответствии с реакционной способностью. Грубые оценки дают увеличение массы материала в системе в 1.5–4.0 раза по сравнению с расчетными значениями. Авторы [63] утверждают, что для носителей кислорода на основе оксидов меди с размерами частиц около 0.3 мм оптимальное соотношение между массами носителей кислорода и топлива составляет 1.7–4.0. При использовании реактора с КС в качестве топливного реактора для полной конверсии метана при температуре 800°С удельная масса оксидов должна быть не менее 130 кг/МВт, при использовании топливного реактора с ЦКС – 140 кг/МВт в топливном реакторе и 350 кг/МВт в воздушном реакторе при среднем размере частиц 0.15 мм. Затраты на сооружение оборудования и стоимость выработанной электроэнергии подтвердили экономическую жизнеспособность данной технологии сжигания при сопоставлении ее с другими чистыми угольными технологиями.
В работе [64] выполнено исследование возможности создания CLC-технологии, интегрированной в цикл электростанции с нулевым выбросом CO2 на основе 4-E анализа (энергетического, эксергетического, экологического и экономического). Проведено сравнение энергетической эффективности ТЭС без улавливания CO2 при параметрах пара докритических (17 МПа, 517°С), суперкритических (24 МПа, 537°С) и ультрасуперкритических (29.6 МПа, 700°С) и передовых ТЭС с CLC-технологией при использовании железной руды в качестве оксида металла – носителя кислорода. Рассматривался высокозольный уголь (зольность 48.87%). В системе CLC принимались давление 1 МПа и температура 900°С, причем газ из воздушного реактора поступал в газовую турбину, затем в общий поток газов, подаваемых из двух реакторов в котел. Расчеты выполнялись с использованием программного комплекса ASPEN+.
Анализ показал, что для докритического, закритического и суперкритического давлений абсолютная потеря энергетической эффективности составляет 0.92, 1.49 и 3.86% соответственно. Эти потери малы по сравнению с известными значениями 7–10% для других технологий улавливания CO2. Чистая потеря эффективности эксергии равна 0.84, 1.37 и 3.55% для докритического, закритического и суперкритического давления соответственно. При этом наибольшие потери эксергии относятся к котельной установке. Использование CLC-технологии снижает годовой выброс CO2 практически до нуля. Приведенная стоимость электроэнергии для установок с CLC-технологией для суперкритических и ультрасуперкритических параметров меньше, чем для обычных ТЭС с такими же параметрами пара. На основании данных 4-E анализа в [64] сделан вывод, что CLC-технология может стать эффективной и весьма перспективной для развивающихся стран, где уголь является главным источником энергии.
ВЫВОДЫ
1. Технология сжигания и газификации топлив в химических циклах с использованием оксидов металлов – носителей кислорода может быть эффективной как по капитальным, так и по эксплуатационным затратам.
2. Одним из ключевых вопросов при организации химических циклов сжигания топлива является выбор состава смесей оксидов металлов – носителей кислорода. При этом важно определить стоимость исходных материалов и производства композитов, так как для промышленных установок потребуется значительная масса загрузки – до 500 кг/МВт (т.). Поэтому последние исследования направлены на использование дешевых природных минералов и отходов металлургических производств.
3. Основными требованиями к характеристикам частиц загрузки являются достаточная реакционная способность, прочность при раздавливании, отсутствие тенденций к агломерации при температурах 850–1200°С, заданный фракционный состав.
4. При организации процесса сжигания топлив с сепарацией CO2 в химических циклах основные задачи – это правильный выбор режимов ожижения для заданных характеристик частиц, определение расхода циркулирующих частиц и времени их пребывания в реакционных зонах, определение потерь давления и характеристик движения частиц в стояках и затворах.
5. Сопротивление циклона при движении потока газа с высокой запыленностью сущестенно снижается по сравнению с незапыленным потоком. Влияние доли легкой фракции (песка) отсутствует. Эффективность улавливания в циклоне составляет более 99.99%. Это обусловлено высокой концентрацией относительно крупных частиц. Унос заметно снижается при росте концентрации, так как мелкие частицы увлекаются более крупными к стенке циклона.
6. Наибольшие затраты на установку с химическим циклом связаны с сжатием полученного СО2, что традиционно для всех технологий улавливания СО2. Общие затраты на улавливание СО2 могут составлять 16–26 евро/т СО2 в зависимости от степени конверсии в топливном реакторе и жизненного цикла оксида металла.
Список литературы
Lyngfelt A., Johansson M., Mattisson T. Chemical looping combustion – Status of development // Proc. of the 9th Inern. Conf. on CFB. Germany, Hamburg, 13−16 May 2008. P. 39−53.
Markström P., Lyngfelt A., Linderholm C. Chemical looping combustion in a 100 KW unit for solid fuels // Proc. of Intern. Conf. on CFB 21. Italy, Naples, 4−6 June 2012. P. 285−292.
Рябов Г.А., Санкин Д.А., Фоломеев О.М. Сжигание и газификация топлив в химических циклах – новое применение технологии циркулирующего кипящего слоя для улавливания СО2 // Изв. РАН. Энергетика. 2014. № 5. С. 27–36.
Adánez J. Chemical-looping combustion of coal: Recent developments and technology challenges // Proc. of Intern. Conf. on CFB 21. Italy, Naples, 4−6 June 2012. P. 12−27.
Chemical looping gasification / L.-S. Fan, F. Li, L.G. Valazquer-Vargas, S. Ramkumar // Proc. of the 9th Intern. Conf. on CFB. Germany, Hamburg, 13−16 May 2008. P. 801−806.
Сепарация СО2 с использованием химических циклов сжигания и газификации топлив / Г.А. Рябов, О.М. Фоломеев, Д.С. Литун, Д.А. Санкин // Теплоэнергетика. 2009. № 6. С. 39–49.
Innovative oxygen carriers uplifting chemical-looping combustion / T. Mattisson, J. Adánez, K. Mayer, F. Snijkers, G. Williams, E. Wesker, O. Bertsch, A. Lyngfelt // Energy Procedia. 2014. V. 63. P. 113–130. https://doi.org/10.1016/j.egypro.2014.11.012
Investigation of different manganese ores as oxygen carriers in chemical looping combustion (CLC) for solid fuels / M. Arjmand, H. Leion, T. Mattisson, A. Lyngfelt // Appl. Energy. 2014. V. 113. P. 1883–1894. https://doi.org/10.1016/j.apenergy.2013.06.015
Performance of CLOU process in the combustion of different types of coal with CO2 capture / I. Adanez-Rubio, A. Abad, P. Gayan, L.F. de Diego, F. Garcia-Labiano, J. Adanez // Int. J. Greenhouse Gas Control. 2013. V. 12. P. 430–440. https://doi.org/10.1016/j.ijggc.2012.11.025
Ksepko E. SrCuO2 the potential oxygen carrier material for chemical looping combustion applications // Proc. of Intern. Conf on CFB. Krakow, Poland, 23–30 May 2017. P. 1039–1044.
Ma S., Xiang W., Chen S. Evaluation of Fe-based oxygen carriers supported with Al2O3, ZrO2 and CeO2 in chemical looping hydrogen generation // Proc. of Intern. Conf. on CFB. Krakow, Poland, 23–30 May 2017. P. 981–988.
Innovative oxygen carriers uplifting chemical-looping combustion / T. Mattisson, J. Adánez, K. Mayer, F. Snijkers, G. Williams, E. Wesker, O. Bertsch, A. Lyngfelt // Energy Procedia. 2014. V. 63. P. 113–130. https://doi.org/10.1016/j.egypro.2014.11.012
Porrazzo R., White G., Ocone R. Techno-economic investigation of a chemical looping combustion based power plant // Faraday Discuss. 2016. V. 192. P. 437–457. https://doi.org/10.1039/C6FD00033A
Progress in chemical-looping combustion and reforming technologies /J. Adanez, A. Abad, F. Garcia-Labiano, P. Gayan, L.F. de Diego // Prog. Energy Combust. Sci. 2012. V. 38. Is. 2. P. 215–282. https://doi.org/10.1016/j.pecs.2011.09.001
Capturing and using CO2 as feedstock with chemical looping and hydrothermal technologies / Y. Demirel, M. Matzen, C. Winters, X. Gao // Int. J. Energy Res. 2015. V. 39. P. 1011–1047. https://doi.org/10.1002/er.3277
Moldenhauer P., Ryden M., Lyngfelt A. Testing of minerals and industrial byproducts as oxygen carriers for chemical-looping combustion in a circulating fluidized-bed 300 W laboratory reactor // Fuel. 2012. V. 93. P. 351–363. https://doi.org/10.1016/j.fuel.2011.11.009
Corathers L.A. Manganese. U.S.: Geological Survey, 2016.
Performance of cement decorated copper ore as oxygen carrier in chemical-looping with oxygen uncoupling / X. Tian, H. Zhao, K. Wang, J. Ma, C. Zheng // Int. J. Greenhouse Gas Control. 2015. V. 41. P. 210–218. https://doi.org/10.1016/j.ijggc.2015.07.015
Effect of temperature on reduction of CaSO4 oxygen carrier in chemical-looping combustion of simulated coal gas in a fluidized bed reactor / Q. Song, R. Xiao, Z. Deng, L. Shen, J. Xiao, M. Zhang // Ind. Eng. Chem. Res. 2008. V. 47. P. 8148–8159. https://doi.org/10.1021/ie8007264
Chemical-looping combustion in a 100 kW unit using a mixture of ilmenite and manganese ore as oxygen carrier / C. Linderholm, M. Schmitz, P. Knutsson, A. Lyngfelt // Fuel. 2016. V. 166. P. 533–542. https://doi.org/10.1016/j.fuel.2015.11.015
Mattisson T., Lyngfelt A., Cho P. The use of iron oxides as an oxygen carrier in chemical-looping combustion of methane with inherent separation of CO2 // Fuel. 2001. V. 80. Is. 13. P. 1953−1962. https://doi.org/10.1016/S0016-2361(01)00051-5
Cho P., Mattisson T., Lyngfelt A. Reactivity of iron oxide with methan in a laboratory fluidized bed – application of chemical-looping combustion // Proc. of the 7th Intern. Conf. on CFB. Canada, Niagara Falls, Ontario, 5−8 May 2002. P. 599−606.
Son S.R., Kim S.D. Chemical-looping combustion with NiO and Fe2O3 in a thermobalance and a circulating fluidized bed reactor with double loops // Ind. Eng. Chem. Res. 2005. V. 45. Is. 8. P. 2689–2696. https://doi.org/10.1021/ie050919x
Lyngfelt A., Thunman H. Construction and 100 h of operational experience of a 10 KW chemical-looping combustor. Chapter 36: The CO2 capture and storage project (CCP) for carbon dioxide storage in deep geological formations for climate change mitigation. V. 1: Capture and separation of carbon dioxide from combustion sources. L.: Elsevier Science, 2005.
Reactivity deterioration of NiO/Al2O3 oxygen carrier for chemical-looping combustion of coal in a 10 kWh Reactor / L. Shen, J. Wu, Z. Gao, J. Xiao // Combust. Flame. 2009. V. 156. Is. 7. P. 1377–1385. https://doi.org/10.1016/j.combustflame.2009.02.005
Berguerand N., Lyngfelt A. Design and operation of a 10 kWh chemical-looping combustor for solid fuels – Testing with South African coal // Fuel. 2008. V. 87. Is. 12. P. 2713–2726. https://doi.org/10.1016/j.fuel.2008.03.008
Performance of a NiO-based oxygen carrier for chemical looping combustion and reforming in a 120 kW unit / J. Bolhàr-Nordenkampf, P. Kolbitsc, T. Pröll, H. Hofbauer // Proc. of the 9th Intern. Conf. on Greenhouse Gas Control Technologies. Washington, 16–20 Nov. 2008.
Use of iron ore as oxygen carrier in a 100 kW chemical-looping combustor for solid fuels / C. Linderholm, M. Schmitz, M. Källén, A. Lyngfelt // Proc. of the 22nd Intern. Conf. on CFB. Finland, Turku, 12−14 June 2015.
Design of a chemical looping combustor using a dual circulating fluidized bed (DCFB) reactor system / P. Kolbitsch, J. Bolhàr-Nordenkampf, T. Pröl, H. Hofbauer // Proc. of the 9th Intern. Conf. on CFB. Hamburg, Germany, 13–16 May 2008.
Operation of a 1 MWt chemical-looping plant / P. Ohlemüller, J.-P. Busch, J. Ströhle, B. Epple // Proc. of the 22nd Intern. Conf on CFB. Finland, Turku, 12−14 June 2015.
Chemical looping gasification in a 2–4 MWt dual fluidized bed gasifier / S. Pissot, T.B. Vilches, J. Maric, M. Seemann // Proc. of 23rd Intern. Conf. on CFB-23. Seoul, Korea, May 2018. P. 956–966.
Zhang S., Xiao R., Zheng W. Investigation of chemical-looping combustion of coal with iron ore as oxygen carrier under pressurized condition // Proc. of 11th Intern. Conf. on CFB and Fluidization Technology. China, Beijing, 14–17 May 2014.
Ryu H.J., Jin G.T. Conceptual design of 50 kW thermal chemical-looping combustor and analysis of variables // J. Energy Eng. 2003. V. 12. Is. 4. P. 289−301.
A two-compartment fluidized bed reactor for CO2 capture by chemical-looping combustion / B. Kronberger, E. Johansson, G. Loffler, T. Mattison, A. Lyngfelt, H. Hofbauer // Chem. Eng. Technol. 2004. V. 27. № 12. P. 1318–1326.
Hydrodynamics of a dual fluidized bed for hydrogen generation by chemical-looping process / D. Zeng, R. Xiao, Z. Huang, S. Zhang // Proc. of 11th Intern. Conf. on CFB and Fluidization Technology. China, Beijing, 14–17 May 2014.
Thon A. A coupled fluidizes bed system for chemical-looping combustion: cold model investigation of the operation behavior / A. Thon, M. Kramp, E.U. Hartge, S. Heinrich, J. Werther // Proc. of 21st Intern. Conf. on CFB. Italy, Naples, 3–6 June 2012.
Riser hydrodynamics study for chemical-looping combustion with grope powders – impact of particle shape / S.S. Rodrigues, A. Forret, F. Montjovet, M. Lance, Th. Gauthier // Proc. of 11th Intern. Conf. on CFB and Fluidization Technology. China, Beijing, 14–17 May 2014.
Cold flow model study on a dual circulating fluidized bed (DCFB) system for chemical looping processes / T. Pröll, K. Rupanovits, P. Kolbitsch, J. Bolhar-Nordenkampf, H. Hofbauer // Proc. of the 9th Intern. Conf. on CFB. Germany, Hamburg, 13–16 May 2008.
Cold flow model investigation on a modified riser with enhanced gas-solid contact locating the regions of operation in a fluidization regime map / J.C. Schmid, T. Pröll, C. Pfeifer, R. Rauch, H. Hofbaue // Proc. of 21st Intern. Conf. on CFB. Italy, Naples, 3–6 June 2012.
Guio-Perez D.C., Pröll T., Hofbauer H. Influencing solids distribution in a dual circulating fluidized bed (DCFB) system by using ring-type internals: extensive parameter variations for corresponding solids inventories in a cold flow model // Proc. of 21st Intern. Conf. on CFB. Italy, Naples, 3–6 June 2012.
Operability analysis of a circulating fluidized-bed coupled dual-loop system for auto-thermal pyrolysis/gasification of coal / R. Solimene, P. Bareschino, R. Chirone, H. Salanito // Proc. of the 9th Intern. Conf. on CFB. Germany, Hamburg, 13–16 May 2008.
Hydrodynamics of a loop-seal operated in a circulating fluidized bed: influence of the operating conditions on gas and solid flow patterns / R. Solimene, R. Chirone, P. Salatino, P. Bareschin // Proc. of the 10th Intern. Conf. on CFB and Fluidization Technology. USA, Oregon, Synriver, 1–5 May 2011.
Hydrodynamics of dual fluidized bed systems with internal mixing channels between circulating and bubbling fluidized bed reactors / U. Lee, I. Choi, J. Song, Y. Kim, W. Yan, Y. Choi // Proc. of the 10th Intern. Conf. on CFB and Fluidization Technology. USA, Oregon, Synriver, 1–5 May 2011.
Investigation on the hydrodynamic properties in the external loop of circulating fluidized bed with loop seal / X. Yao, T. Wang, H. Yang, H. Zhang, Q. Liu // Proc. of the 10th Intern. Conf. on CFB and Fluidization Technology. USA, Oregon, Synriver, 1–5 May 2011.
Knowlton T.M. Non-mechanical solid feed and recycle devices circulating fluidized beds // 3rd Intern. Conf. on CFB Technology. N.Y.: Pergamon Press, 1988.
Subbarao D. Flow rate of solids in L-valves // Proc. of the 10th Intern. Conf. on CFB-10. USA, Oregon, Synriver, 1–5 May 2011.
Gas tracer study in a non-mechanical L-valve / M. Yazdanpanah, A. Hoteit, A. Forret, T. Gauthier, A. Delebarre // Proc. of the 10th Inernt. Conf. on CFB-10. USA, Oregon, Synriver, 1–5 May 2011.
Cold model study on interconnected fluidized bed reactors for multi-generation systems and chemical-looping processes / G.A. Ryabov, O.M. Folomeev, D.A. Sankin, K.V. Chaneev // Proc. of the 10th Intern. Conf. on CFB-10. USA, Oregon, Synriver, 1–5 May 2011. P. 169–176.
Результаты расчетных и экспериментальных исследований гидродинамики циркуляционных контуров в аппаратах с циркулирующим кипящим слоем и системах со связанными реакторами / Г.А. Рябов, О.М. Фоломеев, Д.А. Санкин, Д.А. Мельников // Теплоэнергетика. 2015. № 2. С. 33–40. https://doi.org/10.1134/S0040363615020083
Investigation on hydrodynamics of interconnected reactors and loop seal behavior for multi-generation systems / G.A. Ryabov, O.M. Folomeev, D.A. Sankin, D.A. Melnikov // Proc. of 11th Intern. Conf. on CFB and Fluidization Technology. China, Beijing, 14–17 May 2014.
Pressure balance model for dual CFB – FB reactors systems / G.A. Ryabov, O.M. Folomeev, D.A. Sankin, D.A. Melnikov // Proc. of the 22nd Intern. Conf on CFB. Finland, Turky, 12–14 June 2015.
Hydrodynamics of interconnected reactors for polygeneration systems and chemical looping combustion and gasification / G.A. Ryabov, O.M. Folomeev, D.A. Sankin, D.A. Melnikov // J. Heat Mass Transfer. 2015. V. 13. Is. 1. P. 1–22. https://doi.org/10.17654/hm013010001
Ryabov G., Folomeev O., Dolgushin I. The investigation of movement conditions of particles binary mixtures in chemical looping combustion of solid fuel // J. Physics Conf. 2017. Series 891. P. 012101. https://doi.org/10.1088/1742-6596/891/1/012101
The investigation of fluidization of solids mixture with different particles density/ G. Ryabov, D. Sankin, O. Folomeev, I. Dolgushin // Proc. of Intern. Conf. on CFB-12. Krakow, Poland, 24–26 May 2017. P. 179–186.
Ryabov G., Folomeev O., Dolgushin I. The investigation of mass flux profile and separation of binary mixture of ash and metal oxide for chemical looping combustion of solid fuels // Proс. of 23rd Intern. Conf. on CFB. Seoul, Korea, 13–17 May 2018. P. 468–476.
Рябов Г.А., Фоломеев О.М., Долгушин И.А. Исследование условий движения бинарных смесей частиц применительно к сжиганию топлив в химических циклах с улавливанием диоксида углерода // Теплоэнергетика. 2018. № 7. С. 26–33. https://doi.org/10.1134/S0040363618070081
Baskakov A.P., Dolgov V.N., Goldovin, Y.M. Aerodynamics and heat transfer in cyclones with particle-laden gas flow // Exp. Therm. Fluid. Sci. 1990. V. 3. Is. 6. P. 597–602. https://doi.org/10.1016/0894-1777(90)90076-J
Measurement of solid entrainment by pressure drop in the cyclone / A. Martínez, P. Lisbona, Y. Lara, L.M. Romeo, A. Gil // Proc. of 21st Intern. Conf. on CFB. Naples, Italy, 3–6 June 2012. P. 666–672.
Knowlton T. Cyclone systems in circulating fluidized beds // Proc. of Intern. Conf. on CFB-12. Krakow, Poland, 24–26 May 2017. P. 47–64.
Lyngfelt A. Solid fuels in chemical-looping combustion – feeding of fuel and distribution of volatiles // Proc. of 22nd Intern. Conf. on CFB. Finland, Turku, 14–17 June 2015.
Selection of oxygen carriers for chemical-looping combustion / J. Adanez, L.G. de Diego, F. Garcia-Labiano, P. Gayan, A. Abad, J.M. Palacios // Energy Fuels. 2004. V. 18. Is. 2. P. 371–377. https://doi.org/10.1021/ef0301452
Ni based mixed oxide materials for CH4 oxidation under redox cycle conditions / P. Forzatti, C. Cristiani, G. Groppi, L. Lietti // J. Molecular Catalysis. A: Chemical. 2003. № 204−205. P. 637−646.
Relevance of plant design on CLC process performance using a Co-based oxygen carriers / A. Abad, P. Gayan, F. Garcia-Labiano, de Diego, J. Adanez // Proc. of Intern. Conf. on CFB. Krakow, Poland, 23–36 May 2017. P. 989–994.
4-E analyses of chemical looping combustion based subcritical, supercritical and ultra-, coal-fird power plants / G.D. Surywanshi, B.B.K. Pillai, V.S. Patnaikuni, R. Vooradi, S.B. Anne // Energy Convers. Manage. 2019. V. 200. P. 112050. https://doi.org/10.1016/j.enconman.2019.112050
Дополнительные материалы отсутствуют.
Инструменты
Теплоэнергетика