Теплоэнергетика, 2021, № 3, стр. 45-58
Газификация угля: на перепутье. Технологические факторы
С. П. Филиппов a, *, А. В. Кейко a
a Институт энергетических исследований РАН
117186 Москва, ул. Нагорная, д. 31, корп. 2, Россия
* E-mail: fil_sp@mail.ru
Поступила в редакцию 16.06.2020
После доработки 13.07.2020
Принята к публикации 26.08.2020
Аннотация
Представлены результаты анализа достигнутого в мире технического состояния разработанных технологий газификации угля и спроса на них. Показано, что такие технологии к настоящему времени оказались на перепутье своего развития. Их судьба будет определяться перспективами развития угольной энергетики в целом. Уголь до сих пор играет важнейшую роль в мировой энергетике. В последние годы внешний фон для развития мировой угольной энергетики стал резко негативным. Поскольку среди топлив уголь при сжигании дает наибольшие удельные выбросы CO2, то он может стать первой жертвой разворачивающейся политики декарбонизации энергетики. В этих условиях требуется диверсификация сфер использования угля, прежде всего, за счет производства широкой гаммы химических продуктов с высокой добавленной стоимостью. Это требует разработки соответствующих технологий, в первую очередь технологий газификации, применение которых позволяет производить на основе угля практически весь набор продуктов, получаемых из нефти и природного газа. Определено, что технологии газификации уже достигли высокого уровня технической зрелости, предложено большое число конструкций газогенераторов. Установлено, что в настоящее время большинство работающих установок газификации угля используются для производства разнообразных химических продуктов, прежде всего заменителя природного газа, который затем направляется в газовые сети, а также метанола и аммиака. Отмечено малое количество реализованных и планируемых к реализации проектов парогазовых установок с внутрицикловой газификацией угля, что свидетельствует о низком интересе бизнеса к данной технологии. Между тем, такие установки имеют достаточно высокий потенциал для применения в низкоуглеродной энергетике, конечно, при решении проблемы утилизации уловленного CO2. Показано, что в мире имеется большое число производителей газогенераторного оборудования. Однако газогенераторы выпускаются в единичных экземплярах или небольшими сериями, что неизбежно ведет к их высокой стоимости. Для дальнейшего инновационного развития технологии газификации требуется объединение усилий государства и бизнеса.
В настоящее время доля угля в суммарном потреблении первичной энергии в мире превышает 27%. По этому показателю уголь уступает только нефти (32%) и опережает природный газ (22%) [1]. И за последние полвека доля угля в суммарном потреблении первичной энергии в мире не уменьшилась. В начале 70-х годов XX в. она равнялась примерно 24%. При этом добыча угля во всем мире до последнего времени неуклонно росла. За последние 50 лет она увеличилась в 2.5 раза и в настоящее время превышает 7.5 млрд т в год, из которых более 46% (почти 3.6 млрд т) приходится на Китай. В структуре добываемых углей примерно 14% занимают коксующиеся, 75% – каменные и 11% – бурые угли. Значительная часть добываемого угля (более 17%) отправляется на мировой угольный рынок, годовой объем которого перевалил за 1.3 млрд т. Наблюдается тенденция сокращения потребления угля в промышленно развитых странах и его роста в развивающихся странах [2]. Это дает основание считать уголь “топливом для бедных”, к которым, между прочим, относятся две трети населения планеты.
Крупнейшими потребителями угля в мире в настоящее время являются электростанции. На них приходится 68.9% добываемого угля, или примерно 5.2 млрд т в год. Доля угля в мировом производстве электроэнергии составляет около 38% и остается стабильной в течение последних 50 лет. Еще около 1.43 млрд т угля в год (18.9% его добычи) направляется в качестве топлива в сектор конечного потребления. Примерно 0.9 млрд т угля (11.9%) ежегодно используется на цели коксования и только 70 млн т (0.3%) подвергается другим видам термохимической переработки, в основном газификации.
Следует отметить, что на протяжении почти двух столетий уголь был доминирующим видом топлива в большинстве промышленно развитых стран. В XIX в. его доля в структуре потребляемых органических топлив в мире превышала 90% [3]. С открытием крупных месторождений углеводородов и быстро растущим спросом на нефтепродукты для двигателей внутреннего сгорания уголь к середине XX в. был существенно потеснен нефтью, а затем и природным газом. Однако полностью вытеснить его из мирового топливно-энергетического баланса углеводородам так и не удалось.
Популярность угля обусловлена следующими важнейшими факторами:
изобилием ресурсов;
широкой распространенностью по планете;
дешевизной;
хорошей траспортабельностью и удобством хранения;
довольно высокой теплотой сгорания.
Доля угля в структуре имеющихся на планете ресурсов ископаемых органических топлив (включая потенциальные для открытия месторождения, но без спекулятивных ресурсов газовых гидратов) составляет около 62%, запасы угля превышают 260 млрд ТДж [4]. Таким образом, человечество обеспечено углем на многие столетия вперед. На энергетических рынках уголь примерно в 2 раза дешевле своего основного конкурента – природного газа. В 2018 г. при среднегодовой цене на нефть в мире 12 дол/ГДж (68 дол/bbl) среднегодовая цена на энергетический уголь составляла в США 1.8, в ЕС – 3.7 и в Японии – 4.4 дол/ГДж [2]. При этом среднегодовая стоимость природного газа в этих странах в 2018 г. равнялась соответственно 3.0, 7.2 и 9.6 дол/ГДж. Теплота сгорания (низшая) каменного угля составляет около 25 ГДж/т, что примерно в 1.8 раза ниже теплоты сгорания нефти и природного газа. Однако в отличие от нефти и природного газа для перевозки и хранения угля не нужна специальная и довольно дорогостоящая инфраструктура. Возможно длительное хранение каменного угля на открытом воздухе без существенной потери его качества.
Вместе с тем уголь уступает природному газу и жидким углеводородам по потребительским свойствам. Энергетические установки на угле дороже газовых (примерно в 1.5 раза) и имеют более низкий КПД (в 1.2–1.4 раза в котельных и в 1.3–1.5 раза на электростанциях). Особенно эта разница существенна в установках небольшой мощности. Кроме того, уголь обладает отрицательными качествами, обусловленными его компонентным составом (наличием серы, азота, металлов переходного ряда и др.), что привело к серьезным экологическим проблемам в местах добычи и потребления угля. В полной мере негативные качества угля проявились при крупномасштабном его использовании. Во-первых, это загрязнение окружающей среды вредными веществами, образующимися при сжигании угля, в больших объемах и широком их ассортименте. Во-вторых, отчуждение больших территорий под шлакоотвалы и угольные карьеры. Хотя эти проблемы и можно решить технологически, но это существенно увеличит стоимость энергии, производимой на основе угля, и, следовательно, снизит его конкурентоспособность.
В последние годы внешние факторы для развития мировой угольной энергетики стали резко негативными [2]. В мире разворачивается агрессивная борьба за сохранение климата и звучат требования сократить выбросы в атмосферу парниковых газов, в частности CO2, которые, по сути, равносильны требованиям снизить потребление ископаемых органических топлив. Поскольку среди топлив наибольшие удельные выбросы при сжигании дает уголь (примерно 96 кг CO2/ГДж против 73 кг CO2/ГДж для нефти и 56 кг CO2/ГДж для природного газа [5]), то угольной энергетике уготована участь стать первой жертвой этой политики. Следует обратить внимание на то, что борьба за сохранение климата накладывается на продолжающуюся политику по сохранению окружающей среды и устойчивому развитию мировой экономики, которая и так оказывала жесткое давление на угольную энергетику.
Нужно признать, что адаптировать угольную энергетику к проводимой “климатической политике” чрезвычайно сложно из-за дороговизны технологий улавливания и последующего захоронения CO2. В этих условиях выживаемость угольной промышленности, видимо, будет во многом зависеть от того, насколько быстро удастся изменить роль угля в экономике путем расширения сфер его применения. Уголь должен быть не только источником энергии, но и сырьем для производства широкой гаммы химических продуктов с высокой добавленной стоимостью. Конечно, уголь мог бы стать основой для развития водородной энергетики, если, во-первых, было бы понятно, чем для потребителей водород как энергоноситель лучше по сравнению с электроэнергией, во-вторых, были бы найдены крупные потребители CO2 или резервуары большой вместимости для его надежного и дешевого захоронения на сверхдлительный период времени (на столетия). Все это потребует разработки соответствующих технологий глубокой переработки угля. Здесь уместным окажется предыдущий опыт создания таких технологий.
СПРОС НА ТЕХНОЛОГИИ ГАЗИФИКАЦИИ УГЛЯ
Мировой нефтяной кризис 1973 г., приведший к четырехкратному скачку цены на нефть, и начавшаяся в то время борьба за сохранение чистоты окружающей природной среды привели к тому, что проблема ускоренного создания эффективных технологий переработки угля в искусственные жидкие и газообразные топлива стала довольно острой [3]. Практически во всех ведущих странах мира были приняты соответствующие программы, обеспеченные государственным и корпоративным финансированием. Исследования развивались во всех базовых направлениях термохимической конверсии угля, включая:
пиролиз – термодеструкцию угля без доступа воздуха, обычно осуществляемую при атмосферном давлении и температуре 500–900°С;
гидрогенизацию – термохимическую деструкцию угля в среде водорода при высоком давлении (5–15 МПа) и умеренной температуре (350–450°С);
газификацию – термохимическую деструкцию угля при высокой температуре (800–1200°С и выше) и невысоком давлении (до 4 МПа) при подводе относительно небольшого количества кислорода (чистого или в составе воздуха), часто с добавлением водяного пара (иногда углекислого газа). Водяной пар нужен для увеличения выхода водорода, а кислород – для обеспечения энергией эндотермических реакций.
Основными продуктами пиролиза являются кокс (полукокс при переработке бурых углей), смола и смесь газов. Получаемая в относительно небольших количествах смола может быть переработана в жидкое топливо и разнообразные химические соединения. Газ имеет достаточно высокую теплоту сгорания и может использоваться в качестве топлива. Следует отметить, что в свое время замещение дорогого древесного угля дешевым каменноугольным коксом привело к революции в металлургии. Переработка каменноугольной смолы в разнообразные химические продукты стала основой для развития углехимии.
Процесс гидрогенизации позволяет почти полностью перевести органическую массу угля в смесь жидких углеводородов, главным образом тяжелых фракций, которые нуждаются в дополнительной переработке в жидкие моторные топлива. Проблемами этой технологии являются необходимость поддерживать очень высокое давление и большая потребность в водороде. Для производства водорода активно развивается технология парокислородной газификации угля, в результате которой получают генераторный газ с высоким содержанием СО и водорода, так называемый синтез-газ. После очистки такого газа и последующей паровой конверсии СО образуется достаточно чистый водород. Сам синтез-газ также может служить сырьем для производства синтетических жидких топлив. Соответствующий процесс в начале 20-х годов прошлого века был предложен Ф. Фишером и Г. Тропшем и назван их именами. Освоение технологий гидрогенизации, газификации угля и процесса синтеза Фишера–Тропша позволили Германии перед Второй мировой войной создать индустрию производства моторных топлив из угля. В 50–80-х годах искусственное жидкое топливо из угля в промышленных масштабах производилось в ЮАР, на поставки нефти в которую по решению ООН было наложено эмбарго за проведение политики апартеида.
Технологии пиролиза и гидрогенизации угля имеют принципиальный недостаток – низкую селективность процесса. Получаемые при их реализации жидкие продукты представляют собой смесь большого числа веществ, в основном ароматических и гетероциклических. Управлять их составом чрезвычайно сложно и возможно только в довольно узком его диапазоне. По сути, нужные продукты выделяются из того, “что получилось”. Газификация угля в совокупности с синтезом Фишера– Тропша – очень гибкая и высокоселективная технология. Она позволяет путем подбора соответствующих катализаторов производить широкий спектр химических продуктов, причем прежде всего тех, “которые нужны”.
В результате ренессанса углехимических исследований в 70–90-х годах XX в. было предложено большое число новых технологий конверсии угля, основанных на процессах его пиролиза, гидрогенизации и газификации. Многие из них были протестированы на пилотных установках и подготовлены к промышленному внедрению. Однако открытие крупных нефтяных и газовых месторождений в совокупности с проведением энергосберегающей политики и развитием ядерной энергетики, а позже с расширением использования возобновляемых источников энергии сняли проблему дефицита качественных жидких и газообразных топлив. Существенно стабилизировались мировые цены на углеводороды. Результатом стала потеря бизнесом, а затем и правительствами интереса к разработке технологий глубокой переработки угля. В настоящее время эти технологии остаются востребованными только в странах, обладающих большими запасами угля и небольшими запасами нефти и газа, в частности в Китае. Главной областью применения таких технологий стало производство неэнергетической продукции, например азотных удобрений и метанола. Задачей газификации является обеспечение этих производств водородом, получаемым при переработке угля.
В начале 70-х годов прошлого века началось массовое внедрение в энергетику газотурбинных установок (ГТУ) и высокоэффективных парогазовых установок (ПГУ) на их основе. Топливом для них служили жидкие углеводороды и природный газ. Появился соблазн внедрить ПГУ и в угольную энергетику. Для этого уголь нужно было предварительно газифицировать. Продукты газификации после очистки направляли в камеру сгорания ГТУ. Использование низкотемпературной газоочистки требовало предварительного охлаждения высокотемпературного генераторного газа, что порождало генерацию больших объемов тепловой энергии. В то же время для подачи в газогенератор требовался водяной пар. Поэтому логичными стали предложения интегрировать процессы газификации угля в цикл ПГУ. Было разработано большое число разнообразных схем ПГУ с внутрицикловой газификацией угля [ПГУ с ВЦГ; в зарубежной классификации IGCC (Integrated Gasification Combined Cycle)] [6, 7].
Россия входит в число стран–лидеров по запасам угля. По данным Мирового энергетического совета (WEC) ресурсы угля в России оцениваются в 4108 млрд т (17.8% мировых запасов) [8]. Обеспеченность страны ими при планируемых в Энергетической стратегии России объемах добычи угля к 2035 г. от 485 до 668 млн т в год [9] составляет несколько тысяч лет. Особенностью угольных ресурсов России является большая доля в них бурых углей (33.6%), характеризующихся высокой обводненностью, низкой теплотой сгорания, плохой транспортабельностью и хранимостью. Такие угли целесообразно использовать на месте добычи. Поэтому для России развитие угольных технологий, в том числе газификации, представляет особый интерес.
В России накоплен большой опыт разработки газогенераторов. В 50-х годах XX в. в Советском Союзе находилось в эксплуатации свыше 350 газогенераторных станций, на которых было установлено около 2.5 тыс. газогенераторов различных конструкций [3]. В основном это были небольшие работавшие на воздушном дутье при атмосферном давлении газогенераторы со стационарным слоем угля. Годовая выработка ими газа в 1958 г. достигала 37 млрд м3. После открытия в стране в начале 60-х годов крупных месторождений дешевого природного газа производство газа из угля оказалось экономически невыгодным и стало быстро сокращаться. В 1978 г. из угля было произведено всего 1.5 млрд м3. В основном это был газ, полученный методом подземной газификации угля.
В постсоветское время исследования в области газификации угля в России стали постепенно угасать. Со все меньшей интенсивностью они продолжались на опытных установках ВТИ (Москва) [газификация кускового угля в слое – так называемый “горновой метод”], ЦКТИ (Санкт-Петербург) [газификация пылевидного угля в потоке окислителя], “Компомаш” (Москва) [прямоточно-вихревая газификация водоугольной суспензии]. Исследования проводились также на небольших экспериментальных установках в некоторых других организациях, в частности в Институте теплофизики СО РАН (г. Новосибирск) [плазменная газификация], Уральском федеральном университете (г. Екатеринбург) [газификация пылевидного угля в потоке окислителя].
К настоящему времени в России разработки технологий термохимической деструкции угля, в том числе газификации, ведутся в основном силами энтузиастов, без значимой поддержки государства и бизнеса. Многие научные коллективы распались, лабораторная база была ликвидирована или перепрофилирована на решение новых задач. Многие технологии оказались, видимо, безвозвратно утерянными. В нынешних условиях сохранение и развитие в стране научных и технологических компетенций в области углепереработки и углехимии возможно только при государственной поддержке. В противном случае их можно очень быстро потерять. Возродить же их затем при необходимости в обозримые сроки и с приемлемыми затратами будет чрезвычайно сложно.
Тем более нельзя исключить, что нынешняя кампания по защите климата с ее жесткими требованиями к сокращению выбросов СО2 не окажется продолжительной. Дело в том, что до сих пор нет однозначного научного объяснения наблюдаемому феномену повышения температуры атмосферы планеты. Среди специалистов нет консенсуса в возложении ответственности за ее рост на антропогенную деятельность. Поэтому при стабилизации температуры земной атмосферы или развороте тенденции по ее изменению на обратную угольная энергетика будет реабилитирована.
Таким образом, к настоящему времени развитие технологий использования угля, в том числе технологий газификации, оказалось на перепутье. Их судьба будет определяться перспективами развития угольной энергетики в целом. Актуальность вопроса, поставленного десять лет назад в [10]: “Газификация угля – куда идешь?” (“Coal gasification – quo vadis?”) – только нарастает. Поэтому важной остается задача ее технического совершенствования в целях повышения энергетической и экономической эффективности.
РАЗВИТИЕ ТЕХНОЛОГИИ ГАЗИФИКАЦИИ
Предложенные в разных странах технологии газификации угля характеризуются большим разнообразием. Наиболее активно разрабатываются следующие технологии газификации:
в плотном слое угля с прямоточным или противоточным (обращенные) подводом дутья;
в кипящем слое инертного наполнителя с его циркуляцией или без нее;
в потоке мелкодисперсного угля с сухим или жидким шлакоудалением.
Ведутся разработки еще ряда технологий, например в потоке плазмы или в расплаве шлака или металла. Характеристики получаемого генераторного газа (его компонентный состав и теплота сгорания) в решающей степени определяются организацией процесса, видом исходного топлива, составом газифицирующего агента (дутья), температурой и давлением в газогенераторе. Газификации могут быть подвергнуты любые виды твердого или жидкого топлива: уголь, биомасса, горючие сланцы, мазут, а также горючие отходы (промышленные и бытовые). В качестве дутья обычно используются воздух, кислород и водяной пар (существенно реже – диоксид углерода) в определенных сочетаниях.
Выбор типа дутья и процесса газификации зависит от назначения получаемого газа. Парокислородное дутье применяется для производства газа с высоким содержанием водорода и монооксида углерода. Получаемый синтез-газ широко используется для дальнейшей переработки: служит сырьем для синтеза различных химических продуктов. Применение паровоздушного (воздушного) дутья позволяет отказаться от дорогой установки разделения воздуха и получать более дешевый, хотя и менее калорийный газ. Такой газ может использоваться в промышленности и энергетике.
География разработки и применения угольных газогенераторов весьма обширна. Поэтому, к сожалению, даже такая авторитетная база данных, как World Gasification Database [11] и известные обстоятельные обзоры, например [12], не отражают в полной мере современных масштабов применения в мире технологий газификации твердых топлив. По данным авторов, речь может идти примерно о 900 установках газификации в составе реализованных, планируемых и несостоявшихся проектов за последнюю четверть века. В их число не включены многочисленные газогенераторы малой мощности, распространенные в некоторых азиатских странах. Часть сооруженных установок к настоящему времени уже демонтирована.
На рис. 1 показано распределение установок газификации твердого топлива по типу исходного топлива. Можно заметить, что большинство твердотопливных газогенераторов в мире работают на угле. Их доля составляет около 63% в общем количестве имеющихся газогенераторных установок, а вырабатываемая ими энергия – 79% суммарной энергии газифицируемого топлива. Категория “отходы” представлена преимущественно газификацией в кипящем слое топливных гранул, изготовленных из отходов, т.е. RDF (Refuse Derived Fuel). В данную категорию не включены установки ступенчатого сжигания твердых коммунальных отходов, в которых также используются процессы пиролиза и газификации в качестве первой стадии переработки и обзор которых представлен в [13]. Категория “нефтяные” включает в себя нефтяной кокс, асфальт и нефтеносные пески. Биомасса занимает значительную долю в числе реализованных проектов (около 24%). Однако в силу существенно меньшей единичной мощности установок на биомассе ее роль в единицах энергии выглядит заметно скромнее (лишь 2%).
Рис. 1.
Распределение установок газификации по видам твердого топлива в реализованных проектах (а) и по установленной мощности (б) (в расчете на энергию газифицируемого топлива)
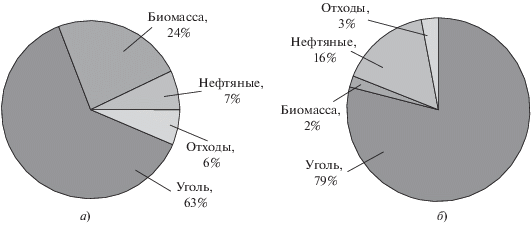
Об областях применения установок по газификации угля можно судить по данным, приведенным на рис. 2. На нем представлены имеющиеся в настоящее время в мире установки газификации (действующие и недействующие) и планируемые к реализации, общее количество которых составляет 432 шт. При анализе информации о назначении угольных газогенераторов следует обратить внимание на соотношение числа планируемых (включая уже строящиеся), реализованных и прекращенных проектов. Последние включают в себя несостоявшиеся (отмененные), перепрофилированные и досрочно прекратившие свое функционирование проекты. Довольно высокая доля планируемых проектов свидетельствует об имевшемся до недавних пор интересе бизнеса к данной сфере.
В настоящее время большинство работающих установок газификации угля (более 200) используются для производства заменителя природного газа (ЗПГ), который затем направляется в газовые сети, причем более 80% таких установок находятся в Китае. Прогресс в направлении метанирования11 синтез-газа (реакция Сабатье) обеспечил существенный прирост суммарной установленной мощности угольных газогенераторов в мире [14]. Газификация угля в целях производства ЗПГ стала одной из ведущих тенденций последнего десятилетия в рассматриваемой области. Следует отметить, что на рис. 2 не учтены китайские предприятия по коксованию угля. Между тем в Китае в последние годы массово освоена технология метанирования и более 100 предприятий коксования уже поставляют ЗПГ в сети газоснабжения.
Традиционным способом применения синтез-газа из угля остается получение жидких химических продуктов, включая этанол, уксусную кислоту, диметиловый эфир и др. Возрастает интерес к синтезу Фишера–Тропша и получению олефинов из угля. По состоянию на февраль 2020 г. на разных стадиях планирования и строительства находятся девять подобных проектов с газогенераторами единичной мощностью по углю от 1500 до 3000 т/сут и общей мощностью предприятий от 10 до 25 тыс. т/сут. При этом наблюдается и выраженная миниатюризация установок Фишера–Тропша. Их единичная мощность в недавно объявленных проектах снизилась до 1–3 т/сут по жидкому топливу. Получение химических продуктов и синтез Фишера–Тропша объединены на рис. 2 в категорию “жидкие продукты”. Комбинирование технологий газификации и синтеза позволяет производить на основе угля практически весь набор продуктов, получаемых из нефти и природного газа с использованием нефте- и газохимических технологий.
Крупнотоннажными продуктами из синтез-газа, получаемого из угля, являются метанол и аммиак, рынки которых огромны. Метанол имеет весьма широкий спектр промышленных применений. Наиболее заметная его часть служит сырьем для производства метил-трет-бутилового эфира – присадки в составе высокооктановых бензинов. Значительная часть метанола используется для получения олефинов с последующим преобразованием их в широкий ассортимент востребованных химических продуктов, что может существенно повысить экономическую эффективность углехимических предприятий. Аммиак перерабатывается в основном в азотные удобрения, спрос на которые традиционно высок и постоянно растет.
На рис. 2 можно видеть, что применение ПГУ с ВЦГ весьма невыгодно выделяется на фоне успехов в других направлениях газификации угля. На протяжении двух последних десятилетий число реализованных проектов по ПГУ с ВЦГ (за пределами Китая) равнялось всего десяти. К 2019 г. из них в эксплуатации осталось только семь. Число планируемых к реализации угольных ПГУ с ВЦГ в мире составляет также семь. Необходимо отметить, что прекращенные проекты сосредоточены в США, Канаде и Великобритании, тогда как планируемые – в странах Азиатско-Тихоокеанского региона. Малое количество планируемых к реализации проектов ПГУ с ВЦГ свидетельствует о низком интересе бизнеса к данной технологии.
Немногочисленная категория “Прочие” на рис. 2 включает в себя несколько единичных проектов, направленных на получение тепловой энергии, технологического пара и водорода. На последнее обстоятельство следует обратить особое внимание. Оно говорит о том, что до последнего времени уголь не рассматривался бизнесом в качестве крупного источника водорода, предназначенного для формирования водородной энергетики.
На рис. 3 представлено распределение эксплуатируемых в мире газогенераторов по типу процесса и виду конструкции, которые ассоциируются с компаниями-разработчиками. В подавляющем большинстве (86%) угольных газогенераторов реализуется газификация в потоке. При этом в большей части поточных газогенераторов используется кислородная конверсия водоугольной суспензии и в меньшей их части – парокислородная конверсия пылевидного угля.
Рис. 3.
Распределение количества угольных газогенераторов по типу процесса (а) и виду конструкции (б)
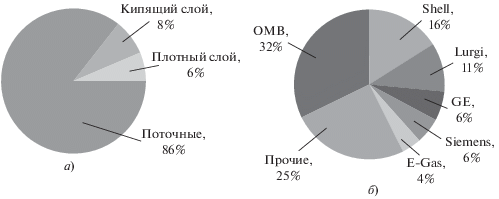
Выбор технологии газификации (способа газификации и конструкции газификатора) определяется, во-первых, свойствами используемого топлива, прежде всего его минеральной части, и, во-вторых, назначением производимого газа.
Для газификации в плотном слое требуются кусковой уголь (обычно фракции не менее 10 мм) или угольные брикеты. Получаемый газ обогащен метаном, что делает его менее пригодным для целей синтеза метанола или других жидких продуктов. Но это повышает его теплоту сгорания, что благоприятствует использованию в ПГУ. Газ содержит угольную смолу, которая усложняет и удорожает очистку. Особенности конструкции газогенератора с плотным слоем обеспечивают его высокую энергоэффективность благодаря утилизации тепла внутри реактора и сокращают потребности технологии в кислороде, что улучшает ее экономические показатели. Однако длительное пребывание топлива в таких реакторах негативно сказывается на их производительности и, следовательно, на экономических показателях. Газогенераторы с плотным слоем применяются для газификации высокозольных и низкокачественных углей, а также разнообразных твердых отходов [15].
В газогенераторах с кипящим слоем используется мелкозернистый уголь, обычно фракции не менее 1 мм и не более 10 мм. Мелкая пыль выносится из реактора, а крупные куски осаждаются на дне, забивая газораспределительную решетку. При газификации в кипящем слое при температуре 800–950°С активно идут процессы шлакования, поэтому для такой газификации больше пригодны высокореакционные угли, в частности бурые и молодые каменные. Реакторы данного типа не получили широкого коммерческого применения из-за сложности управления процессом газификации, относительно низкой степени конверсии угля, низкой калорийности получаемого газа, нередко забалластированного ожижающим агентом, и невысокой производительности реакторов вследствие ограничений на скорость дутья и площадь газораспределительной решетки.
Для газификации в потоке применяется пылевидный уголь, как правило, с фракциями не более 0.25 мм. Для измельчения угля до частиц таких размеров нужно довольно много энергии. Газификация в потоке обычно проводится при высокой температуре и требует большого расхода дорогого кислорода. Часто процесс ведут при повышенном давлении. Высокая температура процесса в сочетании с использованием пылевидного угля предопределяют важнейшие достоинства поточных газогенераторов. Прежде всего, это их высокая производительность, являющаяся следствием большой реагирующей поверхности мелких угольных частиц и высокой скорости протекания химических реакций. Время пребывания угольных частиц в газогенераторе составляет несколько секунд. Получаемый газ не содержит смолистых веществ, что упрощает и удешевляет его очистку. Высокое содержание в газе водорода и СО делает его привлекательным для использования в целях синтеза разнообразных химических веществ. Для упрощения подачи угля в реактор, работающий под высоким давлением, применяют водоугольную суспензию. Это также способствует обогащению газа водородом. Поточные газогенераторы характеризуются высокой степенью конверсии угля. В них довольно легко организовать жидкое шлакоудаление. Однако из-за повышенных потерь энергии с жидким шлаком нежелательной является переработка в таких реакторах высокозольных углей. Также возникают ограничения на использование углей с тугоплавкой золой.
Десять лет назад среди производителей и разработчиков газогенераторов наблюдались четыре лидера:
Shell (с 2019 г. – Air Products) [высокотемпературная парокислородная газификация пылевидного угля в потоке с жидким шлакоудалением];
Texaco (с 2004 г. – GE) [кислородная газификация водоугольной суспензии в движущемся потоке];
Lurgi (включая родственные BGL, SASOL, ZVU и их реплики и модификации) [газификация в слое с воздушным или парокислородным дутьем];
ConocoPhillips (ныне E-Gas) [двухстадийная газификация водоугольной суспензии кислородным дутьем с жидким шлакоудалением].
В настоящее время тройку лидеров возглавляют газогенераторы китайской конструкции OMB (ECUST – Восточно-китайский университет науки и технологий) с долей 32% (см. рис. 3). За ними с большим отрывом следуют газогенераторы фирм Shell (16%) и Lurgi (11%). Газогенераторы OMB только выходят на мировой рынок, поэтому за пределами Китая свои позиции пока сохраняют установки GE, Siemens и E-Gas, хотя их рыночная ниша сместилась из США и стран Европы в Китай, Индию, Южную Корею. Некоторыми компаниями предлагаются коммерческие газогенераторы, в существенной степени копирующие технологию Siemens. Среди них можно отметить газогенераторы Choren Coal Gasification немецкой компании Choren, HT-L китайской фирмы Hangtian и Shenhua Gasifier китайской компании Shenhua Ningxia Coal Group [15]. Завидную стойкость на рынке демонстрируют слоевые газогенераторы типа Lurgi.
Следует отметить, что среди проектов по газификации, реализуемых компаниями Shell и GE, уголь играет все меньшую роль, уступая позиции тяжелым продуктам нефтепереработки. При этом растет потребность нефтеперерабатывающих предприятий в водороде, который получают путем термоконверсии нефтяных остатков.
Разработки современных газогенераторов на воздушном дутье малочисленны. Здесь можно отметить газогенератор японской фирмы Mitsubishi Heavy Industries. Областью его применения являются ПГУ с ВЦГ. Реализовано три проекта. Достигнутый КПД электростанции составляет 42%. Исключение воздухоразделительной установки из технологической схемы отделения газификации позволяет снизить на 25% капитальные затраты на установку.
По данным [10], десять лет назад суммарная мощность установок газификации угля в мире по синтез-газу составляла 17.7 ГВт, из которых 15.3 ГВт (более 86%) располагались в Китае. С тех пор основной прирост мощности газогенераторных установок шел за счет Азиатского региона. В Китае газификацию угля считают локомотивом развития угольной отрасли. Правительство Китая планирует довести объемы газификации угля до 1 млрд т в год (30% его добычи) [16]. Технологической базой для реализации этих планов должны стать газогенераторы большой мощности, имеющие лучшие технико-экономические показатели. Известна статистика применения в Китае крупных угольных газогенераторов разных типов [17]. Среди слоевых газогенераторов наиболее распространенным остается Lurgi, число действующих экземпляров которого достигает 200 [18]. Среди поточных газогенераторов в Китае доминируют установки ECUST в модификации OMB. Существует несколько альтернативных конструкций, в которых также используется водоугольная суспензия, например Jinhua [19]. Газогенераторы OMB и Jinhua по конструкции имеют много общего с газогенератором GSP, разработка основ которого велась в Германии еще в 30-х годах прошлого века.
Общее число крупных установок газификации угля единичной мощностью свыше 700 т/сут в Китае достигает 670 шт., а их суммарная установленная мощность превышает 350 млн т/год. Из них на долю газогенераторов GE приходится примерно 23%, слоевых Lurgi – 19%, GSP – 7%, Shell – 4%. Остальные примерно 47% – это газогенераторы китайских конструкций, в составе которых 34% приходится на установки газификации водоугольной суспензии, а безусловным лидером (15%) является конструкция OMB.
В подавляющем большинстве случаев газификация угля в Китае используется для производства химических продуктов и искусственного топлива. В частности, китайская компания Shenhua Ningxia Coal Group эксплуатирует 5 газогенераторов Siemens производительностью 2 тыс. т угля в сутки каждый для переработки угля в полипропилен и еще 24 аналогичных газогенератора для переработки угля в синтетическое жидкое топливо [15]. Несколько новых газогенераторных установок большой производительности находятся на стадии проектирования и строительства. Получение электроэнергии является основным назначением только пяти крупных газогенераторов в Китае, т.е. менее 1% имеющегося в стране парка газогенераторных установок.
Из всего сказанного можно сделать вывод, что технологии газификации уже достигли высокого уровня зрелости. Предложено большое количество конструкций газогенераторов, с помощью которых можно обеспечить эффективную термохимическую конверсию углей с различными свойствами для производства газа для разных целей. Технологии газификации уже широко внедрены в промышленное производство. Основной областью их применения стала глубокая переработка угля в разнообразные химические продукты и заменитель природного газа – синтетический метан, пригодный для подачи в традиционную газовую сеть.
РАЗРАБОТКА ПГУ С ВНУТРИЦИКЛОВОЙ ГАЗИФИКАЦИЕЙ УГЛЯ
За последние 40 лет ПГУ с ВЦГ прошли все этапы инновационного цикла: 1980–1990 гг. – стадия разработки, призванная доказать техническую эффективность технологии; 1990–2000 гг. – стадия демонстрации, подтверждающая возможность коммерческого применения; 2000–2010 гг. – стадия развертывания, связанная с наработкой опыта и снижением удельной стоимости. Наконец, в 2010–2020 гг. технология должна была шагнуть в фазу широкого практического внедрения, однако этого не произошло. Из пятнадцати проектов угольных ПГУ с ВЦГ, пуск которых планировался в 2010-х годах, были реализованы только пять. Один из них работает в убыток, сроки ввода трех других перенесены, а еще шесть проектов были свернуты или перепрофилированы на природный газ еще до начала эксплуатации, а то и строительства. При этом введенные в строй установки локализуются в Японии, Корее, Китае и Индии, а прекращенные проекты – в Великобритании, США и Канаде. Еще восемь проектов были закрыты до начала строительства во время экономического кризиса 2008–2009 гг., из них семь в США и один в Великобритании. Технически реализованные проекты угольных ПГУ с ВЦГ были вполне удовлетворительными. Однако экономическая эффективность этих установок не позволила им конкурировать с традиционными электростанциями на угле и газе.
Основными мотивами к разработке ПГУ с ВЦГ в свое время были, во-первых, повышение энергетической эффективности использования угля и, во-вторых, обеспечение нормативных значений экологических характеристик угольных электростанций с меньшими затратами. Ожидалось, что КПД разрабатываемых ПГУ с ВЦГ составит 45–46%. В то время КПД угольных паротурбинных установок (ПТУ) не превышал 37–38% [3]. Ведущие мировые производители газотурбинного оборудования разработали турбины, оптимизированные для сжигания синтез-газа и водорода [20, 21].
Однако технический прогресс в электрогенерации и доступность природного газа резко изменили условия применения ПГУ с ВЦГ. Благодаря повышению параметров и оптимизации конструкции элементов основного оборудования КПД ПГУ увеличился до 60% и более, а угольных ПТУ – до 43%, в отдельных случаях до 46%. Промышленно освоены методы очистки дымовых газов угольных электростанций с приемлемыми энергетическими и экономическими показателями. В то же время ныне достигнутый уровень КПД для ПГУ с ВЦГ не превышает 43%. Освоение ультравысоких параметров пара (давление свыше 30 МПа и температура 650–700°C и более) позволяет сделать заключение, что КПД угольных электростанций может превысить 50%. Для ПГУ с ВЦГ достижение КПД более 45% является труднореализуемой задачей.
Особенностью ПГУ с ВЦГ является существенное усложнение технологической схемы по сравнению с угольной ПТУ и парогазовой установкой. При этом значительная ее часть работает под давлением (2–4 МПа). Это влечет за собой рост материалоемкости и удельной стоимости установки, увеличение расходов электроэнергии на собственные нужды, снижение надежности работы оборудования и ухудшение его маневренных качеств. Парогазовые установки с ВЦГ могут эффективно работать только в базовой части графика электрической нагрузки.
В технологической схеме ПГУ с ВЦГ можно выделить так называемые “острова”:
“технологический”, включающий в себя топливоподготовку, газогенератор, системы охлаждения и очистки генераторного газа, очистки жидких стоков и регенерации очищающих агентов;
“энергетический”, основными элементами которого являются газотурбинная и паротурбинная установки и котел-утилизатор.
При реализации предъявляемых к ПГУ с ВЦГ требований по улавливанию CO2 необходимостью становится использование кислородного или парокислородного дутья. Это позволяет исключить из состава генераторного газа балластный азот, увеличивающий объем очищаемых газов и удорожающий очистку. В этом случае в технологическую схему ПГУ с ВЦГ добавляются воздухоразделительная установка, реактор “сдвига” и система извлечения CO2 из генераторного газа (рис. 4). Для производства кислорода обычно используются дорогие криогенные установки большой производительности.
Реактор “сдвига” обеспечивает каталитическую трансформацию содержащегося в генераторном газе монооксида углерода в СО2 и дополнительный водород, используемый в качестве топлива в ГТУ. Это открывает возможности для почти полного извлечения СО2 из газообразных отходов ПГУ с ВЦГ, не достижимого при приемлемых затратах для угольной ПТУ.
Для осуществления реакции сдвига CO + H2O = = CO2 + H2 к генераторному газу дополнительно подводят водяной пар. Для извлечения СО2 из состава генераторного газа предложено несколько промышленно освоенных способов, основанных, главным образом, на химической абсорбции в мокром скруббере. Применение мокрого скруббера снижает тепловой КПД электростанции и порождает потребность в новых способах выделения и связывания СО2. Уровень очистки газа от СО2 в проектах ПГУ с ВЦГ составляет, с учетом экономических соображений, обычно 90–95%. В рамках концепции декарбонизации экономики требуется его повышение, что будет связано со значительным ростом потребления энергии и стоимости очистки.
При введении жестких ограничений на выбросы CO2 именно такая схема ПГУ с ВЦГ, обеспечивающая улавливание CO2, может оказаться востребованной, естественно, при условии решения вопроса об утилизации уловленного CO2. Извлечение CO2 из генераторного газа оказывается существенно выгоднее, чем из дымовых газов угольной ПТУ. Это объясняется меньшим объемом генераторного газа и большей концентрацией в нем CO2.
Ключевым элементом “технологического острова”, определяющим КПД всей ПГУ с ВЦГ, является газогенератор. Эффективность его работы может характеризоваться различными параметрами, в том числе степенью конверсии углерода, количеством выхода синтез-газа на 1 кг газифицируемого топлива, соотношением Н2/СО в синтез-газе. В качестве интегрального показателя может выступать коэффициент эффективности термохимической конверсии угля (КПД газификации), равный отношению суммарной химической энергии газообразных продуктов, образующихся при газификации 1 кг угля, к его теплоте сгорания. Для газогенераторов наиболее распространенных конструкций этот коэффициент варьируется от 70 до 85%. Меньшее значение типично для поточных газогенераторов, большее – для слоевых. Обычно чем выше температура газификации и чем меньше степень регенерации тепла генераторного газа, тем ниже эффективность термохимической конверсии топлива.
Необходимость тщательной очистки генераторного газа перед подачей в камеру сгорания ГТУ обусловлена тремя основными факторами:
• высокой коррозионной активностью примесей кислых газов;
• разрушительным абразивным влиянием взвешенных частиц на элементы газовой турбины;
• отравляющим действием микродисперсного углерода в составе генераторного газа на катализаторы реакции сдвига.
Промышленно освоенные процессы очистки протекают при температурах около 400°С, что вынуждает охлаждать синтез-газ, и это негативно сказывается на КПД энергоустановки. В этой связи актуальны разработки новых технологий горячей газоочистки.
Как показал накопленный опыт эксплуатации ПГУ с ВЦГ, негативным последствием усложнения технологической схемы является снижение надежности работы установки. У ПГУ с ВЦГ показатель готовности колеблется от 62 до 90% [22, 23]. Высокие его значения (80–90%) достигаются при работе установки на нефтяном коксе. При использовании угля этот показатель обычно составляет 77–82%. Для сравнения, готовность современных паротурбинных электростанций на угле составляет 90–92%, а на природном газе – 94–96%. Лучший показатель готовности ПГУ с ВЦГ на угле, равный 85%, достигнут в Корее на электростанции Taean, запущенной в 2016 г.
Около 70% случаев отказов в работе ПГУ с ВЦГ обусловлено неполадками воздухоразделительной установки, причиной которых обычно являются повреждения основного компрессора. На долю газогенератора приходится около 14% отказов в работе ПГУ с ВЦГ, причем половину таких отказов составляет плановый останов реактора газификации для замены топливных питателей. Другими причинами остановов являются шлакование оборудования газогенератора, сбои в системе транспортирования топлива и неустойчивость процессов газификации и розжига. При этом в Китае, где готовность установок газификации заметно ниже, чем в США, проблему решают путем использования резервного реактора, а иногда и двух. При средней готовности установки 77% наличие одного резервного газогенератора повышает готовность комплекса до 94.7%, а наличие двух – до 98.6%.
Обойтись без воздухоразделения, очистки генераторного газа и реактора “сдвига”, сократив на этом затраты, возможно, если перевести ГТУ на замкнутый цикл. Но в этом случае в системе появятся громоздкие теплообменники, а улавливание СО2 придется осуществлять только после сжигания топлива. Это приведет к удорожанию операции улавливания примерно в 2.5 раза. Электрический КПД такой схемы не будет высоким из-за низких параметров цикла ГТУ. Суммарный экономический эффект реализации данной схемы окажется отрицательным. Поэтому замкнутый цикл признан тупиковой ветвью эволюции ПГУ с ВЦГ.
В качестве радикального решения, позволяющего улавливать почти 100% образовавшегося СО2, можно рассматривать так называемый цикл Аллама [24]. Применение парокислородной газификации угля и последующего кислородного сжигания очищенного синтез-газа в камере сгорания ГТУ приводит к тому, что газ после ГТУ состоит из СО2 и водяного пара с незначительными примесями других газов, главным образом азота. После конденсации влаги такой газ представляет собой практически чистый СО2. Рециркуляция СО2 через газогенератор дает возможность снизить температуру в газогенераторе и повысить его энергетическую эффективность. Рециркуляция СО2 может применяться и для камеры сгорания ГТУ при необходимости снижения в ней температуры. В настоящее время цикл Аллама апробирован на пилотной установке тепловой мощностью 50 МВт в Техасе, в которой в качестве топлива используется природный газ. В перспективе применение данного цикла позволит достичь КПД 59% при работе на природном газе и 51% на угле.
Для реализации цикла Аллама нужен чистый кислород, тогда как в настоящее время кислородные газогенераторы работают на воздухе, обогащенном кислородом до 95%. Это делает актуальной разработку новых способов разделения воздуха, в частности, на основе молекулярных мембран. Благодаря исключению криогенных воздухоразделительных установок может быть повышена надежность и улучшены экономические показатели электростанции. На разделение воздуха в реализованных проектах ПГУ с ВЦГ расходуется около 16% выработанной электроэнергии. Это самая большая статья расходов на собственные нужды, которые в ПГУ с ВЦГ в сумме достигают 23%.
Близкая циклу Аллама бескомпрессорная схема ПГУ с кислородным сжиганием природного газа и полным улавливанием СО2 представлена в [25]. Она также может быть преобразована в схему ПГУ с кислородным сжиганием угля и улавливанием СО2. В подобных схемах целесообразно применять двухстадийные процессы газификации. На первой стадии из угля удаляются летучие вещества. Оставшийся коксовый остаток на второй стадии подвергается кислородной газификации. Сжатие жидкого кислорода насосом позволяет исключить компрессор из схемы ГТУ с соответствующей экономией на работе сжатия. Достоинством такой схемы является сокращение затрат на улавливание СО2. Как известно, оснащение традиционных ПГУ с ВЦГ системами улавливания СО2 отнимает до 7% от КПД электростанции и добавляет 6–10% к ее стоимости.
В целях снижения расхода энергии на собственные нужды в работах по технологическому совершенствованию ПГУ с ВЦГ повышенное внимание стало уделяться периферийным системам [26]. Лидирующими при этом стали отмечавшиеся ранее в данной статье разработки новых методов высокотемпературной очистки газов и способов воздухоразделения [27, 28], а также оптимизация технологических схем ПГУ с ВЦГ, обеспечивающая лучшую интеграцию функциональных блоков в их состав [29, 30].
Разработки новых ПГУ с ВЦГ ориентированы преимущественно на использование нефтяного кокса и угля. Создание ПГУ с ВЦГ на биомассе или переработанных твердых бытовых отходах представляется малоэффективным в силу объективного противоречия между экономически оправданными радиусом сбора низкосортного топлива и единичной мощностью газогенераторной установки [31 ] . По экономическим соображениям минимальный уровень электрической мощности ПГУ с ВЦГ в [31 ] находится в диапазоне 200–300 МВт.
Эффективным может оказаться интегрирование электрогенерирующих установок в технологические схемы производства химических продуктов из угля, например метанола, в основе которых лежат технологии газификации и синтеза. Это позволяет использовать горючие отходы основного производства и излишки тепловой энергии для генерации электроэнергии.
ВЫВОДЫ
1. Уголь до сих пор играет важнейшую роль в мировой энергетике. Крупнейшими потребителями угля остаются тепловые электростанции, на которые направляется около 69% добываемого в мире угля. Доля угля в мировом производстве электроэнергии составляет около 38% и держится на этом уровне уже около полувека, несмотря на большие масштабы развития газовой и ядерной энергетики.
2. К настоящему времени развитие технологий газификации оказалось на перепутье. Их судьба будет определяться перспективами развития угольной энергетики в целом. Поскольку среди органических топлив уголь дает при сжигании наибольшие удельные выбросы CO2, то он может стать первой жертвой политики декарбонизации энергетики.
3. Адаптировать угольную энергетику к проводимой “климатической политике” чрезвычайно сложно из-за дороговизны технологий улавливания и последующего захоронения CO2. В этих условиях обеспечить ее выживаемость можно путем расширения сфер применения угля, прежде всего, в целях производства широкой гаммы химических продуктов с высокой добавленной стоимостью, конкурентоспособных с продуктами, получаемыми из нефти и природного газа.
4. Технологии газификации угля уже достигли высокого уровня технической зрелости, предложено большое количество конструкций газогенераторов. Основной областью их применения стало производство разнообразных химических продуктов, в частности заменителя природного газа, метанола и аммиака. Однако газогенераторы выпускаются в единичных экземплярах или небольшими сериями, что ведет к их высокой стоимости. Примерно в 86% эксплуатируемых угольных газогенераторов реализуется процесс газификации в потоке. В основном это кислородная конверсия водоугольной суспензии, а также парокислородная конверсия пылевидного угля.
5. Малое количество реализованных и планируемых к реализации в мире проектов ПГУ с ВЦГ свидетельствует о низком интересе бизнеса к данной технологии, хотя такие установки имеют достаточно высокий потенциал для применения в низкоуглеродной энергетике, конечно, при решении проблемы утилизации уловленного CO2.
6. В России в постсоветское время исследования в области газификации угля стали постепенно угасать. Поскольку Россия обладает огромными запасами угля, то целесообразно поддерживать и развивать в стране соответствующие научные и технологические компетенции, нельзя допустить их потери. Это должно стать совместной заботой государства и бизнеса.
Список литературы
Key World Energy Statistics. Vienna: International Energy Agency, 2019.
World Energy Outlook. 2019. Vienna: International Energy Agency, 2019.
Каганович Б.М., Филиппов С.П., Анциферов Е.Г. Эффективность энергетических технологий: термодинамика, экономика, прогнозы. Новосибирск: Наука, 1989.
World energy and transition to sustainable development / L.S. Belyaev, O.V. Marchenko, S.P. Filippov, S.V. Solomin, T.B. Stepanova, A.L. Kokorin. Kluver Academic Publishers, 2002.
Руководящие принципы национальных инвентаризаций парниковых газов. Т. 2: Энергетика. МГЭИК, 2006. https://www.ipcc-nggip.iges.or.jp/public/2006gl/ russian/vol2.html
Ольховский Г.Г. Газификация твердых топлив в мировой энергетике (обзор) // Теплоэнергетика. 2015. № 7. С. 3–11. https://doi.org/10.1134/S0040363615070073
Ольховский Г.Г. Новые проекты ПГУ с газификацией угля (обзор) // Теплоэнергетика. 2016. № 10. С. 3–13. https://doi.org/10.1134/S0040363616100076
World Energy Resources: 2016. World Energy Council, 2016.
Энергетическая стратегия Российской Федерации на период до 2035 года. Утв. Распоряжением Правительства РФ от 09.06.2020. № 1523-р.
Gräbner M., Meyer B. Coal Gasification – Quo Vadis? // World Min.: Surf. Underground. 2010. V. 62. Is. 6. P. 355–362.
www.globalsyngas.org/resources/map-of-gasification-facilities/ [Электрон. ресурс.] (Дата обращения 05.10.2020.)
Газогенераторные технологии в энергетике / А.В. Зайцев, А.Ф. Рыжков, В.Е. Силин, Р.Ш. Загрутдинов, А.В. Попов, Т.Ф. Богатова; под ред. Рыжкова А.Ф. Екатеринбург: УралОРГРЭС, 2010.
Тугов А.Н. Современные технологии термической переработки ТКО и перспективы их реализации в России (обзор) // Теплоэнергетика. 2021. № 1. С. 5–22. https://doi.org/10.1134/S0040363621010185
Gorre J., Ortloff F., van Leeuwen C. Production costs for synthetic methane in 2030 and 2050 of an optimized Power-to-Gas plant with intermediate hydrogen storage // Appl. Energy. 2019. V. 253. P. 113594. https://doi.org/10.1016/j.apenergy.2019.113594
Оценка технико-экономического потенциала глубокой переработки каменного угля УОР “Караканский-Западный” / Фрайбергская горная академия, Институт технологий энергопроизводства и химической технологии, Фрайберг, Германия, 2017. Available online: http://www.karakan-invest.ru/investor/perspective/Otchet-FGA.pdf; accessed on 21.03.2020.
Summary of the current application status of coal gasification technology and gasifiers / Y. Yueting, Y. Qiuhua, L. Weibin, Y. Gen, P. Dengfeng // Chem. Eng. Des. Commun. 2019. V. 45. Is. 1. P. 15–44.
Ma Y., Fang Q. Application status and development trend of large-scale coal gasification technology in China // Nitrogen Fertilizers and Syngas. 2019. V. 47. Is. 3. P. 1–3.
Li Z. Application of BGL pulveriszed coal slag gasification technology in domestic industrialization // Shandong Chemical Industry. 2017. V. 46. Is. 8. P. 123–125.
Li Z., Li X., Li C. Brief introduction to coal-water slurry gasification technology of Jinhua gasifier // Fertilizer Industry. 2019. V. 46. Is. 1. P. 50–52.
Barnes I. Recent operating experience and improvement of commercial IGCC. Rep. of IEA Clean Coal Centre, 2013.
Gülen S.C. Gas turbine combined cycle power plants. CRC Press, 2019.
IGCC Puertollano. A clean coal gasification power plant. Rep. of Elcogas S.A. by THERMIE Programme, 2001.
Филиппов С.П., Кейко А.В. Обзор прорывных технологий в газовой и угольной энергетике и рекомендации по внедрению их в России: Аналит. записка. М.: ИНЭИ РАН, 2011.
Demonstration of the Allam cycle: an update on the development status of a high efficiency supercritical carbon dioxide power process employing full carbon capture / R. Allam, S. Martin, B. Forrest, J. Fetvedt, X. Lua, D. Freed, G.W. Brown, Jr., T. Sasakia, M. Itoh, J. Manning // Energy Procedia. 2017. V. 114. P. 5948–5966. https://doi.org/10.1016/j.egypro.2017.03.1731
Концептуальная схема парогазовой установки с полным улавливанием диоксида углерода из продуктов сгорания / А.С. Косой, Ю.А. Зейгарник, О.С. Попель, М.В. Синкевич, С.П. Филиппов, В.Я. Штеренберг // Теплоэнергетика. 2018. № 9. С. 23–32. https://doi.org/10.1134/S0040363618090047]
Анализ технологических решений для ПГУ с внутрицикловой газификацией угля / под ред. Рыжкова А.Ф. Екатеринбург: Изд-во Урал. гос. ун-та, 2016.
Techno-economic analysis of oxy-fuel IGCC power plants using integrated intermittent chemical looping air separation / S. Bin, X. Wen, W. Wei, K. Po-Chih // Energy Convers. Manage. 2019. V. 195. P. 290–301. https://doi.org/10.1016/j.enconman.2019.05.006
The oxygen production pre-combustion (OPPC) IGC-C plant for efficient power production with CO2 capture / C.L. Pozo, S. Cloete, J.H. Cloete Á.J. Álvaro, Sh. Amini // Energy Convers. Manage. 2019. V. 201. P. 112109. https://doi.org/10.1016/j.enconman.2019.112109
Ahmed U., Zahid U., Lee Y. Process simulation and integration of IGCC systems for H2/syngas/electricity generation with control on CO2 emissions // Int. J. Hydrogen Energy. 2019. V. 44. Is. 14. P. 7137–7148. https://doi.org/10.1016/j.ijhydene.2019.01.276
Techno-economic analysis of the effects of heat integration and different carbon capture technologies on the performance of coal-based IGCC power plants / N.M.A. Al Lagtah, S.A. Onaizi, A.B. Albadarin, F.A. Ghaith, M.I. Noura // J. Environ. Chem. Eng. 2019. V. 7. Is. 6. P. 103471. https://doi.org/10.1016/j.jece.2019.103471
Кейко А.В., Свищев Д.Н., Козлов А.Н. Газификация низкосортного твердого топлива: уровень и направления развития технологии. Иркутск: ИСЭМ СО РАН, 2007.
Дополнительные материалы отсутствуют.
Инструменты
Теплоэнергетика