Прикладная биохимия и микробиология, 2019, T. 55, № 1, стр. 64-68
Анализ качества отходов в двухстадийной биогидрометаллургической технологии переработки медно-цинкового концентрата
Н. В. Фомченко 1, *, М. И. Муравьёв 1
1 Институт микробиологии им. С.Н. Виноградского, Федеральный исследовательский центр
“Фундаментальные основы биотехнологии” Российской академии наук
119071 Москва, Россия
* E-mail: natalya.fomchenko@gmail.com
Поступила в редакцию 20.04.2018
После доработки 16.07.2018
Принята к публикации 25.07.2018
Аннотация
Показано, что в двухстадийном биогидрометаллургическом процессе переработки медно-цинкового концентрата ионы железа и цветных металлов накапливались в жидкой фазе. Изучено удаление осадков железа из раствора, полученного после химического выщелачивания концентрата и биорегенерации раствора выщелачивания. Показано, что при увеличении рН до 2.4 добавлением извести железо практически полностью (98.3%) удалялось из жидкой фазы в виде ярозита, а около 95% цветных металлов оставалось в растворе в виде сульфатов, из которых медь и цинк могут быть выделены в товарные продукты. Сравнительный анализ полученных осадков (в том числе отходов двухстадийного процесса) показал, что потери цветных металлов были значительно ниже, чем в отходах обогащения медно-цинковых руд и медеплавильного производства.
Ранее было показано, что перспективным способом переработки медно-цинковых концентратов может быть биогидрометаллургический процесс, позволяющий селективно извлекать в раствор цинк и значительное количество железа, а основное количество меди оставлять в твердом осадке [1–5]. Предложенный способ является продолжением разработок двухстадийного биогидрометаллургического процесса выщелачивания цветных металлов из сульфидного сырья [6–12].
В состав исследуемого медно-цинкового концентрата входят три сульфидных минерала: халькопирит (CuFeS2), сфалерит (ZnS) и пирротин (FeS), которые могут окисляться сульфатом трехвалентного железа по следующим реакциям:
(1)
$\begin{gathered} {\text{CuFe}}{{{\text{S}}}_{2}} + 2{\text{F}}{{{\text{e}}}_{{\text{2}}}}{{\left( {{\text{S}}{{{\text{O}}}_{{\text{4}}}}} \right)}_{3}} = \\ = \,\,5{\text{FeS}}{{{\text{O}}}_{{\text{4}}}} + {\text{CuS}}{{{\text{О }}}_{4}} + 2{{{\text{S}}}^{0}}, \\ \end{gathered} $(2)
${\text{ZnS}} + {\text{F}}{{{\text{e}}}_{2}}{{\left( {{\text{S}}{{{\text{O}}}_{4}}} \right)}_{3}} = {\text{ZnS}}{{{\text{O}}}_{{\text{4}}}} + 2{\text{FeS}}{{{\text{O}}}_{4}} + {{{\text{S}}}^{0}},$(3)
${\text{FeS}} + 2{\text{F}}{{{\text{e}}}_{{\text{2}}}}{{\left( {{\text{S}}{{{\text{O}}}_{{\text{4}}}}} \right)}_{3}} = 3{\text{FeS}}{{{\text{O}}}_{4}} + {{{\text{S}}}^{0}}.$При выщелачивании сульфидных минералов в жидкую фазу постоянно переходят медь, цинк и железо, содержание которого значительно превышает содержание цветных металлов. Так, было показано, что после химического выщелачивания медно-цинкового концентрата биораствором при исходной концентрации ионов Fe3+ около 20 г/л, в жидкой фазе накапливалось 27.8 г/л ионов железа [3].
На стадии химического выщелачивания медно-цинкового концентрата (первой стадии) образуются следующие продукты: выщелоченный осадок – медный концентрат и сернокислый раствор, содержащий двух- и трехвалентное железо, цинк и медь. Для создания технологии с рециркуляцией технологических потоков (двухстадийной технологии) необходима биорегенерация растворов, полученных после выщелачивания (вторая стадия). При этом в процессе биорегенерации двухвалентное железо в жидкой фазе должно быть полностью окислено до трехвалентного. Для повторного использования биорегенерированного раствора на стадии химического выщелачивания избыток железа должен быть удален. Одним из способов удаления железа из сернокислых растворов может являться так называемый ярозитный процесс, включающий осаждение железа в виде сульфатгидроксокомплекса при повышенной температуре [13, 14]. При этом в жидкой фазе должны оставаться сульфаты цветных металлов, из которых медь и цинк могут быть выделены в товарной форме.
Цель работы – проведение процесса химического выщелачивания медно-цинкового концентрата, биорегенерация раствора после химического выщелачивания, а также получение и исследование качества осадков (отходов) и жидкой фазы после отделения осадков.
МЕТОДИКА
Объектом исследования был сульфидный концентрат руды Тарньерского месторождения (Свердловская область, Россия). Рудные минералы в концентрате представлены халькопиритом (CuFeS2), сфалеритом (ZnS), пирротином (FeS) и пиритом (FeS2). Содержание элементов в концентрате (%): медь (10.1), цинк (7.36), железо (36.1), общая сера (34.5), сера растворимых сульфатов (1.78), кремний (0.83) и кальций (<0.1).
Химическое выщелачивание проводили в химическом реакторе с механическим перемешиванием (500 об./мин). Температуру устанавливали с помощью термостата, соединенного с реактором. В реактор вносили 1 л биораствора с концентрацией ионов Fe3+ 16.5 г/л и 100 г медно-цинкового концентрата. Температуру процесса устанавливали на уровне 80°С. Об окончании процесса выщелачивания свидетельствовало прекращение снижения значения Eh и стабилизация концентраций ионов железа. Было проведено 4 цикла выщелачивания, в конце каждого из которых твердую фазу отделяли от жидкой и возвращали в реактор. После выщелачивания твердую фазу отделяли от жидкой.
Биорегенерацию биорастворов проводили в биореакторе с рабочим объемом 1 л при перемешивании верхнеприводной турбинной мешалкой с частотой 500 об./мин, барботажем воздуха с расходом 4 л/мин и термостатированием U-образным теплообменником, соединенным с водяным циркуляционным термостатом. Количество посевного материала в биореакторе составляло 20%. Необходимые значения pH (не более 1.6) устанавливали и поддерживали добавлением 5 М раствора серной кислоты. Биорегенерацию проводили до полного окисления ионов Fe2+ до Fe3+. Было проведено 4 цикла биорегенерации и наработано 4 л раствора для исследования качества осадков и жидкой фазы, полученных при удалении ионов трехвалентного железа из этих растворов.
Для биорегенерации использовали умеренно термофильную культуру, растущую при 40°С, Leptospirillum spp., Sulfobacillus spp., а также археи Ferroplasma acidiphilum и Acidiplasma spp. Штаммы микроорганизмов, входящие в состав культур, были выделены из медно-цинковых пиритных отходов (ОАО “Святогор”, ПАО “Гайский ГОК”, Россия) и сульфидных концентратов золотосодержащих руд месторождений Олимпиадинское (Россия), а также Кокпатас и Даугызтау (Республика Узбекистан).
Осаждение железа из растворов после биорегенерации проводили добавлением 25%-ной суспензии гидроксида кальция при 70°С. Осадок отделяли фильтрованием, высушивали до постоянного веса и взвешивали.
Значения рН и Eh измеряли с помощью рН‑метра рН-150МИ (“Измерительная техника”, Россия). Концентрацию Fe3+ и Fe2+ в жидкой фазе определяли колориметрическим методом при 475 нм по реакции с роданидом калия [15], используя фотометр КФК-3 (“ЗОМЗ”, Россия). Концентрацию ионов меди и цинка устанавливали с помощью атомно-абсорбционного спектрометра с пламенной атомизацией 3100 (“Perkin Elmer”, США). На основании материального баланса определяли распределение металлов между осадками и жидкой фазой.
РЕЗУЛЬТАТЫ И ИХ ОБСУЖДЕНИЕ
В процессе биорегенерации микроорганизмы окисляли ионы двухвалентного железа до трехвалентного, которые при повышении рН выпадали в виде осадков гидроксосульфатов (ярозитов):
(4)
$\begin{gathered} 3{\text{F}}{{{\text{e}}}_{{\text{2}}}}{{\left( {{\text{S}}{{{\text{O}}}_{{\text{4}}}}} \right)}_{3}} + 12{{{\text{H}}}_{{\text{2}}}}{\text{O}} + {{{\text{M}}}_{{\text{2}}}}{\text{S}}{{{\text{O}}}_{4}} = \\ = \,\,2{\text{MF}}{{{\text{e}}}_{3}}{{\left( {{\text{S}}{{{\text{O}}}_{{\text{4}}}}} \right)}_{2}}{{\left( {{\text{OH}}} \right)}_{6}}{\kern 1pt} \downarrow + \,\,6{{{\text{H}}}_{{\text{2}}}}{\text{S}}{{{\text{O}}}_{4}}, \\ \end{gathered} $Известно, что эта реакция протекает более интенсивно при повышенной температуре [16]. При протекании реакций осаждения ионов железа цветные металлы должны оставаться в жидкой фазе в виде сульфатов, так как полное осаждение железа происходит при рН от 2.2 до 3.0, а медь и цинк при этом не образуют трудно растворимых соединений.
На рис. 1 представлена зависимость динамики изменения концентрации металлов в жидкой фазе от значения рН. Из результатов следовало, что в исходном растворе после биорегенерации рН раствора составлял 1.60, а концентрация ионов металлов была следующей (г/л): Fe3+ − 16.1, Zn2+ − 1.70 и Cu2+ − 0.67. В процессе увеличения рН концентрация ионов железа в жидкой фазе начинала резко снижаться (за счет образования осадка железа), особенно при повышении рН до 1.9–2.4, а концентрация цветных металлов изменялась незначительно. Это свидетельствовало о селективности удаления трехвалентного железа из жидкой фазы по отношению к цветным металлам, незначительное снижение концентрации которых, очевидно, могло быть связано с механическим захватом ионов образующимся осадком.
Рис. 1.
Зависимость концентрации ионов Fe3+ (1), Zn2+ (2) и Cu2+ (3) в жидкой фазе от рН при нейтрализации биораствора гидроксидом кальция.
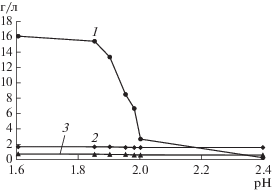
На рис. 2 представлена зависимость от рН количества осажденного железа и получаемого осадка, а также содержания железа в осадке. При этом объем нейтрализуемого раствора в каждой точке рН составлял 0.5 л. Из представленных данных следовало, что резкое увеличение количества осадка наблюдалось в диапазоне рН 1.9–2.0, что совпадало с резким снижением концентрации ионов железа в растворе (рис. 1). При этом минимальное количество осадка при рН 1.85 составило 2.5 г, а максимальное при рН 2.4 – 46.2 г. Расчет содержания железа в осадке в зависимости от рН показал, что оно снижалось с 23.6 до 17.1%.
Рис. 2.
Зависимость количества получаемого осадка (1) осажденного железа (2), а также содержания железа в осадке (3) от рН при нейтрализации биораствора гидроксидом кальция.
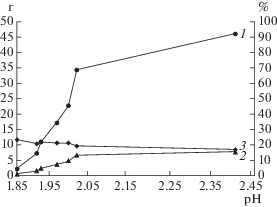
Полученные результаты можно объяснить тем, что при увеличении рН увеличивался расход гидроксида кальция при выпадении в осадок нерастворимого сульфата (гипса, бассанита):
(5)
${\text{С а }}{{\left( {{\text{О Н }}} \right)}_{2}} + {{{\text{H}}}_{{\text{2}}}}{\text{S}}{{{\text{O}}}_{4}} = {\text{С а S}}{{{\text{O}}}_{4}}{\kern 1pt} \downarrow + \,\,2{{{\text{H}}}_{{\text{2}}}}{\text{O}}.$Образующийся сульфат кальция увеличивал количество осадка и снижал содержание в нем железа. Однако образование сульфата кальция способствовало удалению из раствора после биорегенерации избытка сульфатов, что можно отнести к положительному моменту, поскольку в жидкой фазе при этом оставались только сульфаты цинка и меди.
В табл. 1 представлены результаты расчета содержания и извлечения железа, меди и цинка в осадок, полученный в процессе нейтрализации биораствора. Из представленных данных следовало, что в зависимости от увеличения расхода извести количество осадка возрастало, а содержание железа снижалось, при этом содержание цветных металлов практически не изменялось, а извлечение металлов в осадок увеличивалось. Максимальное извлечение железа составило 98.3%, а цинка и меди – только 5.2 и 4.5% соответственно. Полученные данные свидетельствовали о высокой селективности отделения железа от цветных металлов, так как в жидкой фазе оставалось около 95% меди и цинка и только 1.7% железа. В растворе после отделения осадка при рН 2.4 концентрация железа составляла 0.26 г/л, меди – 0.64 г/л, а цинка – 1.61 г/л. Полученные растворы сульфатов цветных металлов оказались пригодными для выделения металлов в товарной форме с помощью жидкостной экстракции.
Таблица 1.
Содержание металлов в осадках, полученных при нейтрализации раствора после биорегенерации (объем раствора 0.5 л)
Масса осадка, г | Расход извести (в пересчете на СаО), г | Содержание в осадке, % | Извлечение в осадок, % | ||||
---|---|---|---|---|---|---|---|
Fe | Zn | Cu | Fe | Zn | Cu | ||
17.2 | 5.4 | 21.5 | 0.20 | 0.029 | 46.5 | 2.06 | 0.74 |
34.4 | 9.0 | 19.5 | 0.23 | 0.09 | 83.3 | 4.65 | 4.62 |
46.2 | 9.9 | 17.1 | 0.19 | 0.074 | 98.3 | 5.20 | 4.50 |
Сравнительные данные состава получаемого отхода и различных отходов переработки медно-цинковых руд (хвосты обогащения, металлургические шлаки и отходы их переработки) представлены в табл. 2.
Таблица 2.
Содержание меди, цинка и железа в различных типах отходов переработки медно-цинковых руд
Отходы | Содержание, % | ||
---|---|---|---|
Cu | Zn | Fe | |
Осадок после нейтрализации биораствора при рН 2.4 (отход биогидрометаллургической переработки медно-цинкового концентрата) | 0.074 | 0.19 | 17.1 |
Пиритные хвосты (отходы) обогащения медно-цинковых руд УГМК [17–19] | ~0.3 | ~0.5 | до 30.0 |
Шлаки медеплавильного производства [20–22] | 0.5–3.7 (~1–2) | ~3.6 | 25–50 (~40) |
Отходы переработки медеплавильных шлаков [20–22] | <1.0 | ~3.6 | 25–50 (~40) |
Из данных табл. 2 следовало, что получаемый по предлагаемой биогидрометаллургической технологии переработки медно-цинкового концентрата отход содержал значительно меньше цветных металлов, чем отходы других отраслей промышленности, связанных с переработкой подобного сырья.
Таким образом, установлено, что полученный в процессе удаления избытка железа из биораствора осадок ярозитов содержал небольшое количество цветных металлов. Получаемый отход являлся инертным, так как в отличие от отходов обогащения руд, не мог окисляться природным биоценозом ацидофильных микроорганизмов с образованием токсичных кислых вод, содержащих тяжелые металлы. Поэтому даже складирование этого отхода не может ухудшить экологическую обстановку в промышленных регионах. Получаемые отходы могут рассматриваться как компоненты строительных материалов [23].
Работа выполнена при финансовой поддержке президиума РАН по программе фундаментальных исследований № I.48.
Список литературы
Фомченко Н.В., Муравьев М.И. // Прикл. биохимия и микробиология. 2017. Т. 53. № 1. С. 82–87.
Фомченко Н.В., Муравьев М.И. // Прикл. биохимия и микробиология. 2017. Т. 53. № 4. С. 395–399.
Фомченко Н.В., Муравьев М.И. // Прикл. биохимия и микробиология. 2017. Т. 53. № 6. С. 630–634.
Fomchenko N.V., Muravyov M.I. // Hydrometallurgy. 2017. V. 174. P. 116–122.
Фомченко Н.В., Муравьев М.И., Меламуд В.С. // Прикл. биохимия и микробиология. 2018. Т. 54. № 4. С. 416–420.
Муравьев М.И., Фомченко Н.В., Кондратьева Т.Ф. // Прикл. биохимия и микробиология. 2011. Т. 47. № 6. С. 663–671.
Muravyov M.I., Fomchenko N.V., Kondrat’eva T.F. // Adv. Mater. Res. 2015. V. 1130. P. 359–362.
Муравьев М.И., Фомченко Н.В. // Прикл. биохимия и микробиология. 2013. Т. 49. № 6. С. 561–569.
Muravyov M.I., Bulaev A.G., Kondrat’eva T.F. // Miner. Eng. 2014. V. 64. P. 63–66.
Фомченко Н.В., Бирюков В.В., Муравьев М.И. // Биотехнология. 2007. № 6. С. 65–71.
Fomchenko N.V., Kondrat’eva T.F., Muravyov M.I. // Hydrometallurgy. 2016. V. 164. P. 78–82.
Fomchenko N.V., Muravyov M.I. // Int. J. Miner. Process. 2014. V. 133. P. 112–118.
Dutrizac J.E., Jambor J.L. // Rev. Mineral. Geochem. 2000. V. 40. № 1. P. 405–452.
Pappu A., Saxena M., Asolekar S.R. // Sci. Tot. Environ. 2006. V. 359. № 1–3. P. 232–243.
Woods J.T., Mellon M.G. // Ind. Eng. Chem. Anal. Ed. 1941. V. 13. № 8. P. 551–554.
Bigham J.M., Jones F.S., Özkaya B., Sahinkaya E., P-uhakka J.A., Tuovinen O.H. // Int. J. Miner. Process. 2010. V. 94. № 3–4. P. 121–128.
Kondrat'eva T.F., Pivovarova T.A., Bulaev A.G., Melamud V.S., Muravyov M.I., Usoltsev A.V., Vasil’ev E.A. // Hydrometallurgy. 2012. V. 111–112. P. 82–86.
Шадрунова И.В., Хабиров Е.Т., Трубкин И.С. // Горный информационно-аналитический бюллетень (научно-технический журн.). 2005. № 11. С. 259–263.
Muravyov M.I., Fomchenko N.V. // Miner. Eng. 2018. V. 122. P. 267–276.
Sarfo P., Das A., Wyss G., Young C. // Waste Manage. 2017. V. 70. P. 272–281.
Piatak N.M., Parsons M.B., Seal R.R. II // Appl. Geochem. 2015. V. 57. P. 236–266.
Bellemans I., DeWilde E., Moelans N., Verbeken K. // Adv. Colloid Interface Sci. 2017. http://dx.doi.org/10.1016/ j.cis.2017.08.001.
Fonti V., Dell’Anno A., Beolchini F. // Sci. Tot. Environ. 2016. V. 563–564. P. 302–319.
Дополнительные материалы отсутствуют.
Инструменты
Прикладная биохимия и микробиология