Проблемы машиностроения и надежности машин, 2023, № 2, стр. 94-102
Конечноэлементное моделирование гибридной аддитивной технологии с использованием лазерно-ударно-волновой обработки
Г. Ж. Сахвадзе *
Институт машиноведения им. А.А. Благонравова РАН
Москва, Россия
* E-mail: sakhvadze@mail.ru
Поступила в редакцию 07.07.2022
После доработки 18.11.2022
Принята к публикации 20.12.2022
- EDN: CPDMRD
- DOI: 10.31857/S0235711923020074
Аннотация
Металлические изделия, изготовленные с помощью аддитивных технологий, обычно имеют неблагоприятные механические характеристики. Лазерно-ударно-волновая обработка – это механическая обработка поверхностей с высокой скоростью деформирования, которая упрочняет приповерхностный слой изделия и обеспечивает создание благоприятных механических свойств. В настоящей статье путем объединения технологий лазерно-ударно-волновой обработки и аддитивных технологий разрабатывается гибридная аддитивная технология, и исследуется роль лазерно-ударно-волновой обработки в гибридной аддитивной технологии с использованием метода конечных элементов. Полученные результаты показывают, что частота упрочненного слоя является критическим технологическим параметром, влияющим на перераспределение остаточных напряжений, который сильно зависит от количества тепла, выделяемого в процессе 3D-печати. Благодаря полученным результатам, разработанная технология гибридная аддитивная технология получает свое место в разновидностях аддитивных технологий и имеет потенциал для внедрения на практике в качестве нового способа производства высококачественных металлических изделий.
Свойства металлических изделий, созданных с помощью аддитивных технологий (АТ), остаются важным и актуальным направлением исследований во всем мире [1]. Неудовлетворительные механические свойства полученных изделий и низкая производительность являются основными техническими препятствиями для более широкого внедрения на практике технологии аддитивного производства (АП). В частности, большие растягивающие остаточные напряжения (РОН), и, как следствие, растрескивания, остаются серьезной проблемой для эксплуатационных характеристик полученных 3D-изделий. Сегодня для снятия РОН обычно используют термическую обработку. Хотя термообработка действительно уменьшает РОН, предотвращая большие деформации и растрескивание, она имеет свои очевидные недостатки [2].
Гибридные аддитивные технологии (ГАТ) возникли как совместное использование классических АТ с одним или несколькими вторичными технологиями, которые дополняют друг друга и в итоге возникает синергетический эффект, что благоприятно отражается на качестве получаемых изделий и их функциональных характеристиках [2]. Гибридная аддитивная технология, использующая механическую обработку поверхности, такую как лазерно-ударно-волновую обработку (ЛУВО), представляет большой интерес, например, при производстве подшипников, различных инструментов и штампов, из-за способности ЛУВО к упрочнению и созданию благоприятных сжимающих остаточных напряжений (СОН) на глубинах, превышающих обычную глубину проникновения СОН, доступных при классической поверхностной обработке.
ЛУВО при распространении ударной волны в материале вызывает сильную пластическую деформацию с высокой скоростью деформирования, что создает в приповерхностной области мощных полей СОН. Следовательно, повышается усталостная долговечность и износостойкость материалов за счет замедления зарождения и распространения трещин. В настоящей статье предлагается сочетание аддитивного производства с послойным лазерно-ударно-волновым упрочнением в качестве нового подхода к управлению объемными механическими свойствами ГАТ-изделий, которое продлевает их срок службы.
Схематизация гибридной аддитивной технологий (ГАТ). В гибридной аддитивной технологии первичной технологией должна быть одна из традиционных аддитивных технологии – либо технология прямого осаждения материала (Directed energy deposition DED, в дальнейшем – ПОМ), либо технология сплавления в порошковом слое (powder bed fusion PBF), либо технология изготовления объектов с использованием ламинирования (laminated object manufacturing LOM). В настоящей статье технология ПОМ выступает в качестве первичной технологии, объединясь с технологией ЛУВО, которая выступает в качестве вторичной технологии. Схема ГАТ, с использованием технологий ПОМ и ЛУВО, показана на рис. 1.
Рис. 1.
Схема гибридной аддитивной технологии (ГАТ) с использованием совмещения технологий ПОМ (в качестве первичной технологии) и ЛУВО (в качестве вторичной технологии): 1 – ПОМ; 2 – ЛУВО; 3 – один из слоев ГАТ-изделия.
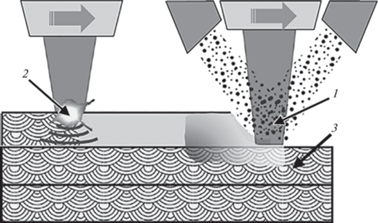
Конечно-элементное моделирование ГАТ. При ПОМ по мере добавления слоев возникают остаточные напряжения, которые с каждым шагом меняются, что влияет на механические свойства и последующие эксплуатационные характеристики готового изделия. Основными элементами, необходимыми для успешного моделирования технологии ПОМ, являются: движущийся источник тепла (в нашем случае – лазер), способ добавления новых слоев, граничные условия и модель материала, характеристики которого зависят от температуры.
Для моделирования технологии ГАТ разработана двумерная модель (рис. 2).
Рис. 2.
Схема для моделирования технологии ГАТ с тепловыми и механическими граничными условиями: 1 – печатаемое 3D-изделие; 2 – подложка; 3 – узел № 751 в конечноэлементной модели.
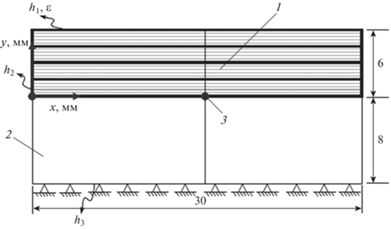
На подложку наносится 20 слоев, каждый шириной 30 мм и толщиной 0.3 мм. Подложка под слоями имеет размеры 30 мм на 8 мм. Для моделирования ГАТ разрабатываются сразу две модели с идентичной геометрией: одна – для теплового анализа (ПОМ), другая – для механического анализа (ЛУВО). В тепловой модели используются конечные элементы типа DC2D4, которые представляют собой 4-узловые диффузионные теплопроводящие элементы, используемые для измерения температур, возникающих при применении движущегося источника тепла. В механической модели используются конечные элементы типа CPE4, которые представляют собой 4-узловые билинейные плоские деформационные элементы, которые способны определять напряжения, возникающие как от источника тепла, так и от ЛУВО. Размеры конечных элементов в слоях составляют 20 × 20 мкм, а в подложке они гораздо больше 80 × 80 мкм, чтобы минимизировать время вычислений. Добавление материала во время ГАТ моделируется посредством последовательной активации нового набора элементов в начале каждого шага (используется так называемый метод неактивных элементов).
Для моделирования динамики температур, возникающих во время ПОМ в каждом слое, используется методика движущегося теплового потока [3]. Тепловой поток представлен как неравномерно распределенное тепло, величина которого зависит от местоположения и времени. Принято, что тепловой поток соответствует гауссову распределению, моделируется с использованием конечноэлементного пакета ABAQUS, в частности, подпрограммой DFLUX, и равен [4]
(1)
$q = \frac{{CP}}{{{{\pi }}{{r}^{2}}}}{{e}^{{\frac{{ - 2{{{\left( {x - {v}t} \right)}}^{2}}}}{{{{r}^{2}}}}}}},$Таблица 1.
Параметры теплового потока при АТ
Мощность лазера, Вт | Размер лазерного пятна, мм | Скорость сканирования, мм/с | Длина сканирования, мм |
---|---|---|---|
400 | 1.36 | 10 | 30 |
Таким образом, к модели ставятся тепловые граничные условия по теплопроводности, конвекции и излучению. Передача тепла между слоями учитывается через коэффициент теплопроводности k, коэффициент конвективной теплопередачи h и коэффициент излучения ε. Тепло, отводимое подложке, определяется через свободную конвекцию в нижней части подложки h3 = 1000 Вт/(м2 K). Граничные условия для принудительной конвекции и излучения задаются на верхней поверхности каждого слоя во время нанесения материала h1 = 100 Вт/(м2 K), ε = 0.62. Тем самым учитывается как тепло, передаваемое через инертный газ, вдуваемого в ванну с расплавом, так и тепло, излученное в окружающую среду. Свободная конвекция в окружающую среду задается в качестве граничных условий на краях слоев и подложки h2 = 25 Вт/(м2 K).
Моделирование добавления слоя. Чтобы смоделировать добавление нового слоя во время ПОМ, большинство исследователей используют один из двух методов: метод тихих элементов и метод неактивных элементов [5]. В методе тихих элементов в самом начале анализа в модели уже присутствуют печатаемые элементы, но им присваиваются пониженные свойства материала. Эти свойства получаются путем умножения начальных свойств на соответствующие коэффициенты масштабирования [6]. Элементы с пониженными свойствами сначала никак не влияют на процесс (их как будто бы нет). По мере продвижения процесса и готовности этих тихих элементов к печати, им присваиваются реальные свойства материала, тем самым обозначается их появление в модели.
Метод неактивных элементов – это еще один подход, аналогичный методу тихого элемента. Разница между ними заключается в том, что осажденные элементы деактивированы с самого начала анализа. Элементы активируются на каждом этапе по отдельности (или в виде слоя), когда источник тепла воздействует на этот слой. В настоящей статье используется именно этот метод.
Исследуемый материал. В статье исследуется подшипниковая сталь ШХ15 (зарубежный аналог – AISI 52100), которая широко применяется в машиностроительной и авиационно-космической отраслях, причем не только для производства подшипников, но и других деталей, где требуется высокая твердость, износостойкость и контактная прочность.
При анализе теплопередачи для определения температурных полей используются механические и теплофизические свойства, зависящие от температуры. В табл. 2 приведены упругие свойства (зависимость модуля Юнга и коэффициента Пуассона от температуры).
Таблица 2.
Зависимость упругих характеристик подшипниковой стали ШХ15 от температуры
Температура, К | Модуль Юнга, ГПа | Коэффициент Пуассона |
---|---|---|
295 | 201.33 | 0.277 |
473 | 178.58 | 0.269 |
673 | 162.72 | 0.255 |
873 | 103.42 | 0.342 |
1073 | 86.57 | 0.396 |
1273 | 66.58 | 0.490 |
Зависимости пластических и физических свойств (предела текучести, пластической деформации, параметров определяющего соотношения Джонсона–Кука, плотности, коэффициента теплового расширения, коэффициента теплопроводности) от температуры приведены в [7].
Общая схема конечноэлементного моделирования ГАТ. Для моделирования технологии ГАТ был использован конечноэлементный пакет ABAQUS, в частности – его модули ABAQUS/Standard (для определения температур и термонапряжений) и ABAQUS/Explicit (для определения остаточных напряжений при ЛУВО). Блок-схема процедуры моделирования показана на рис. 3. Для моделирования ГАТ разрабатываются сразу две модели с идентичной геометрией: одна модель для анализа процесса теплопередачи с элементами DC2D4, а другая – для анализа напряжений с элементами CPE4.
При моделировании ГАТ (рис. 3) сначала анализируется процесс теплопередачи и определяются распределения температур по слоям, далее полученные температуры экспортируются для вычисления термонапряжений, возникающих от воздействия вычисленных температур. Затем анализируется процедура ЛУВО, где в качестве начальных данных импортируются термонапряжения, возникающие от добавления слоев, и определяются остаточные напряжения, чем и завершается первый цикл упрочнения. В следующем цикле добавляется еще один набор слоев и опять происходит анализ теплопередачи. В этом анализе напряжения от рассчитанных заново температур вычисляются с учетом напряжений, возникающих от предыдущей ЛУВО, которые в этом анализе выступают в качестве начальных данных.
Этот же цикл повторялся до тех пор, пока не напечатаются все слои. Разные аспекты такого моделирования приведены в работах [8–15]. Особенности моделирования только ЛУВО приведены в [16, 17].
Полученные результаты и их анализ. В настоящей статье проводится моделирование 5-ти характерных для ГАТ режимов: 1) вместо ГАТ исследуется чистая АТ (т.е., режим без ЛУВО); 2) технология ЛУВО применяется только на окончательной поверхности (режим поверхностной ЛУВО); 3) ГАТ при использовании ЛУВО через каждые 10 слоев (Г10-режим); 4) использование ЛУВО через каждые 5 слоев (Г5-режим); 5) использование ЛУВО на каждом слое (Г1-режим). Результаты этих пяти случаев сопоставляются и анализируются, определяя тем самым влияние частоты упроченного слоя на характер распределения остаточных напряжений в самых слоях. Заметим, что все случаи моделируются для исследуемого материала ШХ15.
Распределения остаточных напряжений в изделии при разных режимах ГАТ. Окончательные распределения остаточных напряжений по глубине (рис. 2, по направлению y) для всех 5-ти исследуемых режимов показаны на рис. 4. Режим “Без ЛУВО” представляет собой модель традиционной АТ без ЛУВО. Из графика (рис. 4, кривая 1) видно, что остаточные напряжения в этом режиме во всех слоях растягивающие из-за непрерывного приложения теплового потока к слоям (в изделии всюду имеем РОН). Этот непрерывный тепловой поток расширят материал и вызывают в них РОН, величина которых в слоях колеблется 600–1325 МПа. Для сопоставления результатов в разных гибридных режимах был смоделирован и режим однократного лазерного упрочнения, нанесенного на поверхность после напечатания двадцатого слоя (“режим поверхностной ЛУВО”). В этом случае нельзя сказать, что имеет место чистая ГАТ, т.к. здесь ЛУВО не полностью сопрягается с технологией ПОМ.
Рис. 4.
Профили остаточных напряжений ($\sigma _{{{\text{RES}}}}^{{{\text{11}}}}$) для изучаемых 5-ти режимов ГАТ: 1 – режим без ЛУВО; 2 – режим поверхностной ЛУВО; 3 – Г10-режим; 4 – Г5-режим; 5 – Г1-режим. Слева от вертикальной пунктирной линии расположены слои 1–20 печатаемого изделия, справа – подложка.
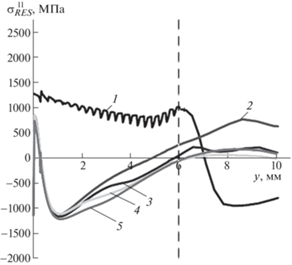
Скорее всего, здесь имеет место традиционная технология лазерно-ударно-волновой обработки поверхности. Как видим (рис. 4, линия 2), РОН от ЛУВО превращаются в СОН и достигают своего максимума в величину 1120 МПа. СОН в этом случае сохраняются до глубины 4.9 мм, далее они переходят в РОН. Также были исследованы три гибридных режима при различных частотах упрочненного слоя (рис. 4, линии 3–5). Глубина СОН увеличивается по мере увеличения частоты упрочненного слоя от 5.8 мм для Г10-режима до 6.5 мм для Г5-режима. Здесь достигается своеобразная точка насыщения, т.к. при дальнейшем увеличении частоты упрочненного слоя до единицы (Г1-режим) глубина СОН уменьшается до 6.3 мм. Хотя, несмотря на достижение точки насыщения, видим, что повышение частоты упрочненного слоя увеличивает ширину области со СОН. Заметим, что величина пиковых значений СОН для всех случаев варьируются от –1120 до –1220 МПа.
Анализ изменения температуры. Динамика термического состояния во время ГАТ имеет решающее значение для изучения эволюции остаточных напряжений в изделии. Температуры, возникающие от теплового потока во время добавления слоя, стимулируют возникновение так называемого эффекта “термического подавления” СОН и других эффектов, возникающих в результате ЛУВО [18]. При моделировании технологии ПОМ тепловой поток направляется на каждый слой и определяется распределение температур, возникающих во время 3D-печати. Температуры, образующейся в ранее добавленных слоях, также изменяются по мере нанесения новых слоев. Для наблюдения за динамикой температур для удобства был выбран узел номер 751 (рис. 2) в середине верхней части подложки. В этом узле рассчитаются температуры от добавления всех 20 слоев. Изменения температуры во времени по мере добавления слоев показаны на рис. 5. При добавлении первого слоя (линия 1) пиковая температура на верхней части подложки достигает 2700 К. При добавлении второго слоя температура составляет уже 1544 К. По мере добавления следующих слоев пиковая температура в узле уменьшается экспоненциально. Как известно [19, 20], температуры выше критической температуры (приблизительно 820 К), влияют на микроструктуру слоев. Температура в исследуемом узле выше критической температуры до добавления седьмого слоя. Когда добавляется восьмой слой, температура падает ниже температуры перехода (она равна 778 К). Это указывает на то, что тепловой поток при добавлении нового слоя влияет на микроструктуру семи слоев под ним. Хотя в этой статье изменение микроструктуры не рассматривается, очень важно знать об этом хотя бы на качественном уровне.
Рис. 5.
Изменения температуры во времени по мере добавления всех слоев изделия (1–20) в узле № 751 (рис. 2); T1 – температура плавления; T2 – критическая температура.
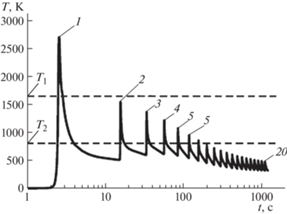
Выводы. Разработана конечно-элементная 2D-модель гибридной аддитивной технологии (ГАТ), состоящая от последовательно применяемых технологий прямого осаждения материала (ПОМ) и лазерно-ударно-волновой обработки (ЛУВО). Показано, что благодаря послойному упрочнению слоев по технологии ЛУВО, во время ГАТ в печатаемых изделиях образовываются сжимающие остаточные напряжения (СОН), которые хоть и испытывают тепловое и/или механическое перераспределение, полностью не исчезают и остаются в изделии.
Показано, что уменьшение частоты упрочненного слоя с 20 до 5 увеличивает глубину упрочненного слоя (т.е., слоя со стабильными СОН). Также показано, что глубина упрочненного слоя максимальна при упрочнении каждого 5-го слоя (в Г5-режиме), т.е., показано, что, упрочнение чаще, чем через каждые пять слоев, не увеличивает глубину СОН, что имеет важное практическое значение.
Список литературы
Huang Y., Leu M.C., Mazumder J. et al. Additive manufacturing: current state, future potential, gaps and needs, and recommendations // J. Manuf. Sci. Eng. 2015. V. 137. P. 1.
Sealy M.P., Madireddy G., Willims R. et al. Hybrid processes in additive manufacturing // J. Manuf. Sci. Eng. 2018. V. 140. P. 1.
Manvatkar V.D., Gokhale A.A., Jagan R. et al. Estimation of melt pool dimensions, thermal cycle, and hardness distribution in the laser-engineered net shaping process of austenitic stainless steel // Metall. Mater. Trans. 2011. V. 42. P. 1.
Heigel J.C., Michaleris P., Reutzel E.W. Thermo-mechanical model development and validation of directed energy deposition additive manufacturing of Ti-6A1-4V // Addit. Manuf. 2015. V. 5. P. 9.
Wang L., Felicelli S.D., Pratt P. Residual stresses in LENS-deposited AISI410 stainless steel plates // Mater. Sci. Eng. A. 2008. V. 496. P. 234.
Chiumenti M., Lin X., Cervera M. et al. Numerical simulation and experimental calibration of additive manufacturing by blown powder technology. Part I: thermal analysis // Rapid Prototyp. J. 2017. V. 23. P. 448.
Anca A., Fachinotti V.D., Escobar-Palafox G. et al. Computational modelling of shaped metal deposition // Int. J. Numer. Methods Eng. 2011. V. 85. P. 84.
Chiumenti M., Cervera M., Salmi A. et al. Finite element modeling of multi-pass welding and shaped metal deposition processes // Comput. Methods Appl. Mech. Eng. 2010. V. 199. P. 2343.
Peyre P., Aubry P., Fabbro R. et al. Analytical and numerical modeling of direct metal deposition laser process // J. Phys. Appl. 2008. V. 41. P. 1.
Denlinger E.R., Heigel J.C., Michaleris P. Residual stress and distortion modeling of electron beam direct manufacturing Ti-6AI-4V // Proceedings of the IMechE. 2015. V. 229. P. 1803.
Marimuthu S., Clark D., Allen J. et al. Finite element modelling of substrate thermal distortion in direct laser additive manufacture of an aero-engine component // Proc. IMechE. 2013. V. 227. P. 1987.
Voothaluru R., Richard L.C., Cheng G.J. Finite element analysis of the variation in residual stress distribution in laser shock peening of steels // J. Manuf. Sci. Eng. 2012. V. 134. P. 061010.
Sealy M.P., Madireddy G., Li C. et al. Finite element modeling of hybrid additive manufacturing by laser shock peening // Proc. Annual Int. Solid Freeform Fabrication Symposium. 2016. P. 306.
Anurag S., Guo Y.B., Horstemeyer M.F. The effect of materials testing modes on finite element simulation of hard machining via the use of internal state variable plasticity model coupled with experimental study // Comput. Struct. 2009. V. 87. P. 303.
Shah S.M., Nelias D., Zain-ul-abdein M. et al. Numerical simulation of grinding induced phase transformation and residual stresses in AISI-52100 steel // Finite Elem. Anal. Des. 2012. V. 61. P. 1.
Sakhvadze G.Zh., Sakhvadze G.G., Kavtaradze R.Z. Increasing the Crack Resistance of Materials by Means of Laser Shock Processing // Russian Engineering Research. 2021. V. 41. № 1. P. 27.
Sakhvadze G.Zh. Simulation of the Technology of Laser-Shock-Wave Processing of Titanium Alloys with Shape Memory Using Dimensional Analysis // J. of Machinery Manufacture and Reliability. 2021. V. 50. № 4. P. 332.
Adu-Gyamfi S., Ren X.D., Larson E.A. et al. The effects of laser shock peening scanning patterns on residual stress distribution and fatigue life of AA2024 aluminium alloy // Opt. Laser Technol. 2018. V. 108. P. 177.
Huang S., Sheng J., Wang Z. et al. Finite element and experimental analysis of elevated-temperature fatigue behavior of IN718 alloy subjected to laser peening // Int. J. Fatigue. 2020. V. 131. P. 105337.
Xu S., Huang S., Meng X. et al. Thermal evolution of residual stress in IN718 alloy subjected to laser peening // Opt. Lasers Eng. 2017. V. 94. P. 70.
Дополнительные материалы отсутствуют.
Инструменты
Проблемы машиностроения и надежности машин