Журнал неорганической химии, 2022, T. 67, № 8, стр. 1194-1198
Синтез, структура и фазовый состав высокоэнтропийной керамики (HfTiCN)-TiB2
Н. С. Евсеев a, *, А. Е. Матвеев a, П. Ю. Никитин a
a Национальный исследовательский Томский государственный университет
634050 Томск, пр-т Ленина, 36, Россия
* E-mail: evseevns@gmail.com
Поступила в редакцию 15.12.2021
После доработки 05.03.2022
Принята к публикации 10.03.2022
- EDN: KFJCNA
- DOI: 10.31857/S0044457X22080098
Аннотация
Исследован фазовый состав и структура композиционного керамического материала (HfTiCN)-TiB2, полученного на основе высокоэнтропийной системы Hf–Ti–C–N–B в режиме сопряженного самораспространяющегося высокотемпературного синтеза (СВС, горения). Количественная оценка с помощью метода Ритвельда показала, что содержание фазы HfTiCN в продуктах горения составляет 40 мас. %, а содержание фазы TiB2 – 60 мас. %. Установлено, что структура СВС-материалов состоит из частиц и агломератов HfTiCN, распределенных в матрице TiB2. Средний размер частиц TiB2 и HfTiCN составляет 6.1 и 3.3 мкм соответственно. Предложен вероятный механизм образования композиционного материала (HfTiCN)-TiB2 в режиме сопряженного самораспространяющегося высокотемпературного синтеза системы Hf–Ti–C–N–B. Представленные результаты свидетельствуют о принципиальной возможности получения методом СВС композиционного керамического материала (HfTiCN)-TiB2.
ВВЕДЕНИЕ
Развитие современных технологий невозможно без создания новых материалов с повышенными физико-механическими характеристиками (рабочая температура, стойкость к окислению, твердость, прочность и др.). В последнее время внимание ученых сконцентрировано на высокоэнтропийных сплавах (ВЭC) и керамических материалах на их основе [1–3]. Уникальность таких материалов объясняется высоким значением энтропии смешения, которая растет с увеличением числа компонентов, входящих в систему. Согласно классической термодинамике, повышение энтропии приводит к снижению свободной энергии (потенциал Гиббса) [4]. Снижение свободной энергии существенно повышает возможность образования фаз, состоящих из атомов различных элементов, что приводит к существенному искажению кристаллической решетки. Вследствие этих особенностей высокоэнтропийные материалы обладают рядом улучшенных физико-механических свойств по сравнению с традиционными (двух- или трехкомпонентными) материалами. Высокоэнтропийные сплавы получают, как правило, методом плавления исходных металлических компонентов. В работе [5] авторы продемонстрировали успешное применение метода дугового плавления смеси металлов Co–Cr–Cu–Fe–Ni–Ti в атмосфере аргона для получения высокоэнтропийного сплава CoCrCuFeNiTi. Полученный сплав обладает уникальным сочетанием прочности при растяжении (до 1650 МПа) и большой пластичности (22%).
В работе [6] исследована термодинамическая стабильность высокоэнтропийной керамики Ca3Fe3.5 –xTi2xV1.5 –xO12, полученной в режиме высокотемпературного твердофазного синтеза на основе системы (1.5 – x)CaVO9–(3.5 – x)Fe3O4–(2x)CaTiO3–(3.5 – x)O2 в интервале температур 1100–1483 K. Установлено, что в процессе синтеза формируются твердые растворы замещения, в которых ионы железа и ванадия замещаются ионами титана. При этом показано, что увеличение концентрации титансодержащего компонента приводит к повышению энтропии системы (–61.0 Дж/(моль K) и снижению свободной энергии Гиббса (–30 K Дж/моль). Способ получения высокоэнтропийной боридной керамики (Hf0.2Zr0.2Ti0.2Mo0.2Ta0.2)B2 продемонстрирован в работе [7]. В качестве исходных материалов были использованы порошки диборидов гафния, циркония, титана, молибдена и тантала. Результаты исследований показали, что в процессе искрового плазменного спекания формируется двумерная высокоэнтропийная фаза (Hf0.2Zr0.2Ti0.2Mo0.2Ta0.2)B2, состоящая из слоев атомов металлов, разделенных слоями атомов бора. Авторы работы показали, что полученная высокоэнтропийная боридная керамика обладает повышенной твердостью и стойкостью к окислению по сравнению с традиционными боридами, полученными в таких же условиях. Данные исследования показывают, что энтропия смешения в керамических материалах, полученных на основе многокомпонентной системы, существенно влияет на их структуру и свойства.
Одним из перспективных и высокоэффективных методов получения простых керамик является самораспространяющийся высокотемпературный синтез (СВС), который базируется на высокотемпературных экзотермических реакциях исходных компонентов смеси [8–11]. Методом СВС были получены такие классы соединений, как карбиды [12], бориды [13], нитриды [14], силициды [15], интерметаллиды [16], а также композиционные материалы различного состава [17–20]. Одним из преимуществ этого метода является контроль фазового состава и структуры продуктов реакции в процессе самораспространяющегося высокотемпературного синтеза [21–23]. Ранее авторами настоящей работы были предложены новые методы получения борида алюминия-магния AlMgB14 и композита AlMgB14-TiB2. Преимущество этих методов заключается в том, что процессы синтеза осуществляются за счет тепла донорной системы, которая находится внутри основной смеси или является внешним источником энергии (химическая печь) [24–26]. В работах [27, 28] демонстрируется успешное применение СВС для получения высокоэнтропийного сплава CoCrFeNiMnAlx. Получение ВЭС методом самораспространяющегося высокотемпературного синтеза осуществляли в режиме алюмотермической реакции из смеси порошков алюминия и оксидов NiO, Cr2O3, Co3O4, Fe2O3 с последующим отделением оксида алюминия от целевой фазы. Исследование фазового состава целевого материала, полученного из порошковой смеси оксидов с концентрацией алюминия х = 0.2, показало наличие одной фазы твердого раствора с ГЦК-решеткой.
На основании вышеизложенного мы предполагаем, что метод СВС может успешно применяться для получения высокоэнтропийных керамических материалов и композитов на их основе.
Цель настоящей работы – изучение фазового состава и структуры материалов, полученных из высокоэнтропийной системы Hf–Ti–C–N–B в режиме самораспространяющегося высокотемпературного синтеза.
ЭКСПЕРИМЕНТАЛЬНАЯ ЧАСТЬ
В качестве исходных компонентов использовали порошки гафния (дисперсность <300 мкм, чистота >99%), титана (дисперсность <280 мкм, чистота >99%), бора (дисперсность <0.6 мкм, чистота >99%) и углерода (дисперсность <0.8 мкм, чистота >99%). Горение исследуемой порошковой смеси проводили в среде азота.
Исходные компоненты смешивали в соотношении (мас. %) 35Ti + 5C + 25Hf + 5B. Титан и бор были взяты в избытке относительно стехиометрии простых соединений TiC и HfB2. Такой состав был выбран для создания донорных экзотермических реакций между титаном и бором, которые сопровождаются выделением большого количества тепла. Тепло, полученное от донорной системы, позволяет осуществить акцепторные реакции с образованием многокомпонентной высокоэнтропийной системы. Из полученной смеси путем холодного одноосного прессования готовили образцы диаметром 23 мм и высотой 30 мм. Давление прессования составляло 25 МПа. Полученные образцы помещали в реактор постоянного давления объемом 3 л. Для осуществления азотирования исходных образцов в процессе СВС емкость реактора заполняли газообразным азотом особой чистоты (ГОСТ 9293-74, 99.99%) до давления 3.5 МПа. Инициирование реакции синтеза осуществляли путем нагрева верхней поверхности образца молибденовой спиралью. Рентгенофазовый анализ полученных продуктов синтеза проводили на дифрактометре Shimadzu XRD 6000 с CuKα-излучением на основе базы данных PDF4+. Микроструктуру полученных продуктов синтеза определяли с помощью сканирующего электронного микроскопа с катодом Шоттки Tescan MIRA 3 LMU (Tescan Orsay Holding, Brno, Czech Republic), оборудованного энергодисперсионным рентгеновским спектрометром Oxford Instruments Ultim Max 40 (Oxford Instruments, High Wycombe, UK). Размер частиц определяли методом секущих с использованием РЭМ-изображений.
РЕЗУЛЬТАТЫ И ОБСУЖДЕНИЕ
Дифрактограмма полученных продуктов горения системы Hf–Ti–C–N–B приведена на рис. 1. Согласно результатам рентгенофазового анализа, в полученных продуктах горения обнаружены фазы TiB2 и HfTiCN. Количественная оценка с использованием метода Ритвельда показала, что содержание фаз HfTiCN и TiB2 составляет ~40 и ~60 мас. % соответственно.
В табл. 1 приведены структурные параметры решеток исходных эталонов, а также их уточненные параметры. Установлено, что решетки уточненных состояний, а также координаты их атомов отличаются от исходных эталонов. Решетка HfTiCN имеет пр. гр. P4/mmm, а решетка TiB2 – пр. гр. P6/mmm.
Таблица 1.
Структурные параметры решеток полученных продуктов горения
Фаза | Состояние | a, Å | c, Å | α = β, град | γ, град | Содержание, мас. % |
---|---|---|---|---|---|---|
HfTiCN | Исходное | 3.119 | 4.459 | 90.00 | 90.00 | 40 |
Уточненное | 3.073 | 4.354 | 90.00 | 90.00 | ||
TiB2 | Исходное | 3.029 | 3.228 | 90.00 | 120.00 | 60 |
Уточненное | 2.991 | 3.215 | 90.00 | 120.00 |
На рис. 2 приведено РЭМ-изображение структуры полученных продуктов горения (рис. 2а), многослойное изображение ЭДС (рис. 2б), а также картирование по элементам (рис. 2в). Установлено, что структура представлена темными и светлыми частицами. Энергодисперсионный анализ показал, что в темных областях (рис. 2а) преобладают элементы титана и бора, что соответствует фазе диборида титана TiB2, а в светлых областях (рис. 2а) обнаружены элементы Hf, Ti, C, N, что соответствует фазе HfTiCN. Таким образом, результаты элементного анализа согласуются с результатами рентгенофазового анализа.
Рис. 2.
РЭМ-изображение продуктов горения системы Hf–Ti–C–N–B (а), многослойное ЭДС-изображение (б), разделение по спектрам (в).
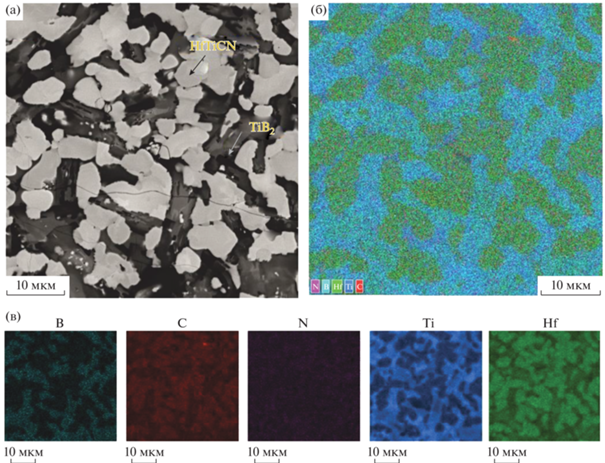
На рис. 3 представлены гистограммы распределения частиц HfTiCN и TiB2 в продуктах горения по размерам. Установлено, что размер частиц HfTiCN изменяется от 0.3 до 9.5 мкм, а их средний размер равен ~3.3 мкм. Размер частиц TiB2 изменяется от 0.9 до 16.9 мкм, а их средний размер равен ~6.1 мкм.
На основании проведенных исследований предложен вероятный механизм образования композиционного материала (HfTiCN)-TiB2 в режиме сопряженного самораспространяющегося высокотемпературного синтеза системы Hf–Ti–C–N–B. Под воздействием нагрева спирали происходит передача тепла в верхний слой образца. Далее происходит плавление частиц титана, который насыщается частицами бора и углерода. Поскольку энтальпия образования диборида титана (–321.5 кДж/моль) [29] ниже энтальпии образования карбида титана (–133.7 кДж/моль) [30], после насыщения расплава титана бором и углеродом происходит экзотермическая реакция образования диборида титана (TiB2). В процессе экзотермической реакции выделяется большое количество тепла, которое затрачивается на плавление частиц гафния и растворение в полученном расплаве оставшихся частиц углерода при насыщении расплава газообразным азотом. На следующей стадии происходит экзотермическая реакция образования соединения HfTiCN с последующим формированием в продуктах синтеза композиционной структуры, состоящей из частиц HfTiCN, распределенных между частицами диборида титана.
ЗАКЛЮЧЕНИЕ
В результате проведенных исследований горения высокоэнтропийной системы Hf–Ti–C–N–B в режиме СВС был получен керамический композиционный материал HfTiCN–TiB2. Исследована структура и состав продуктов горения системы Hf–Ti–C–N–B. Установлено, что содержание фазы HfTiCN в полученных продуктах горения составляет ~40 мас. %, а содержание фазы TiB2 – ~60 мас. %. Установлено, что средний размер частиц TiB2 в продуктах горения равен 6.1 мкм, а средний размер частиц HfTiCN – 3.3 мкм. Предложен вероятный механизм образования композиционного материала (HfTiCN)-TiB2 в режиме сопряженного самораспространяющегося высокотемпературного синтеза системы Hf–Ti–C–N–B.
Список литературы
Cantor B., Chang I.T.H., Knight P., Vincent A.J.B. // Mater. Sci. Eng. A. 2004. V. 375. P. 213. https://doi.org/10.1016/j.msea.2003.10.257
Yeh J.W., Chen S.-K., Lin S.-J. et al. // Adv. Eng. Mater. 2004. V. 6. № 5. P. 299. https://doi.org/10.1002/adem.200300567
Yang X., Zhang Y., Liaw P.K. // Proc. Eng. 2012. V. 36. P. 292. https://doi.org/10.1016/j.proeng.2012.03.043
Ахметов Н.С. Общая и неорганическая химия. М.: Высш. школа, 1981. 679 с.
Wang X.F., Zhang Y., Qiao Y., Chen G.L. // Intermetallics. 2007. V. 15. № 3. P. 357. https://doi.org/10.1016/j.intermet.2006.08.005
Денисов Г.В. // Журн. неорган. химии. 2013. Т. 58. № 2. С. 168. [Denisov G.V. // Russ. J. Inorg. Chem. 2013. V. 58. № 2. P. 134. https://doi.org/10.1134/S0036023613020034]
Gild J., Zhang Y., Harrington T. et al. // Scientific Reports. 2016. V. 6. № 1. P. 1. https://doi.org/10.1038/srep37946
Matveev A., Zhukov I., Ziatdinov M. et al. // Materials. 2020. V. 13. № 5. P. 1050. https://doi.org/10.3390/ma13051050
Matveev A., Nikitin P., Zhukov I. et al. // Ceram. Int. 2021. V. 47. № 15. P. 21140. https://doi.org/10.1016/j.ceramint.2021.04.117
Evseev N., Nikitin P., Ziatdinov M. et al. // Materials. 2021. V. 14. P. 5482. https://doi.org/10.3390/ma14195482
Evseev N., Ziatdinov M., Romandin V. et al. // Processes. 2020. V. 8. № 9. P. 1056. https://doi.org/10.3390/pr8091056
Zaytsev A.A., Borovinskaya I.P., Vershinnikovet V.I. et al. // Int. J. Refract. Met. Hard Mater. 2015. V. 50. P. 146. https://doi.org/10.1016/j.ijrmhm.2014.12.008
Golla B.R., Mukhopadhyay A., Basu B. et al. // Prog. Mater Sci. 2020. V. 111. P. 100651. https://doi.org/10.1016/j.pmatsci.2020.100651
Амосов А.П., Титова Ю.В., Майдан Д.А. и др. // Журн. неорган. химии. 2016. Т. 61. № 10. С. 1282. [Amosov A.P., Titova Y.V., Maidan D.A. et al. // Russ. J. Inorg. Chem. 2016. V. 61. № 10. P. 1225. https://doi.org/10.1134/S0036023616100028]
Faraji M., Adeli M., Soltanieh M. // Ceram. Int. 2021. V. 47. № 2. P. 2822. https://doi.org/10.1016/j.ceramint.2020.09.136
Romero A., Rodríguez G.P., Marjaliza E. // J. Alloys Compd. 2022. V. 891. P. 161876. https://doi.org/10.1016/j.jallcom.2021.161876
Simonenko E.P., Simonenko N.P., Sevastyanov D.V. et al. // Russ. J. Inorg. Chem. 2016. V. 61. № 13. P. 1649. https://doi.org/10.1134/S0036023616130039
Matveev A., Promakhov V., Schultz N. et al. // Materials. 2021. V. 14. № 20. P. 5914. https://doi.org/10.3390/ma14205914
Чижиков А.П., Константинов А.С., Бажин П.М. // Журн. неорган. химии. 2021. Т. 66. № 8. С. 1002. [Chizhikov A.P., Konstantinov A.S., Bazhin P.M. // Russ. J. Inorg. Chem. 2021. V. 66. № 8. P. 1115. https://doi.org/10.1134/S0036023621080039]
Pazniak A., Bazhin P., Shchetinin I. et al. // Ceram. Int. 2019. V. 45. № 2. P. 2020. https://doi.org/10.1016/j.ceramint.2018.10.101
Zhukov I.A, Promakhov V.V., Matveev A.E. et al. // Russ. Phys. J. 2018. V. 60. P. 2025. https://doi.org/10.1007/s11182-018-1319-4
Matveev A., Zhukov I., Ziatdinov M. et al. // Materials. 2020. V. 13. № 5. P. 1050. https://doi.org/10.3390/ma13051050
Ковалев Д.Ю., Лугинина М.А., Вадченко С.Г. // Журн. неорган. химии. 2017. Т. 62. № 12. С. 1635. [Kovalev D.Y., Luginina M.A., Vadchenko S.G. // Russ. J. Inorg. Chem. 2017. V. 62. № 12. P. 1638. https://doi.org/10.1134/S0036023617120117]
Nikitin P.Yu., Zhukov I.A., Matveev A.E. et al. // Ceram. Int. 2020. V. 46. № 14. P. 22733. https://doi.org/10.1016/j.ceramint.2020.06.039
Nikitin P.Y., Matveev A.E., Zhukov I.A. // Ceram. Int. 2021. V. 47. № 15. P. 21698. https://doi.org/10.1016/j.ceramint.2021.04.183
Никитин П.Ю., Жуков И.А., Болдин М.С. и др. // Журн. неорган. химии. 2021. Т. 66. № 8. С. 1150. [Nikitin P.Y., Zhukov I.A., Boldin M.S. et al. // Russ. J. Inorg. Chem. 2021. V. 66. P. 1252. https://doi.org/10.1134/S0036023621080167]
Kashaev N., Ventzke V., Stepanov N. et al. // Intermetallics. 2018. V. 96. P. 63. https://doi.org/10.1016/j.intermet.2018.02.014
Санин В.Н., Юхвид В.И., Икорников Д.М. и др. // Докл. АН. 2016. Т. 470. № 4. С. 421. [Sanin V.N., Yukhvid V.I., Ikornikov D.M. et al. // Dokl. Phys. Chem. 2016. V. 470. № 2. P. 145. https://doi.org/10.1134/S001250161610002X]
Akhachinskij V.V., Chirin N.A. // Symposium on the thermodynamics of nuclear materials. Vienna, 1975. V. 2. P. 467.
Vrel D.L., Lihrmann J.M., Petitet J.P. // J. Chem. Eng. Data. 1995. V. 40. № 1. P. 280. https://doi.org/10.1021/je00017a062
Дополнительные материалы отсутствуют.
Инструменты
Журнал неорганической химии