Журнал неорганической химии, 2022, T. 67, № 10, стр. 1485-1491
Влияние концентрации золя на основные характеристики аэрогелей оксида алюминия
Е. А. Страумал a, *, И. О. Гожикова a, С. Ю. Котцов b, С. А. Лермонтов a
a Институт физиологически активных веществ РАН
142432 Черноголовка, Северный пр-д, 1, Россия
b Институт общей и неорганической химии им. Н.С. Курнакова РАН
119991 Москва, Ленинский пр-т, 31, Россия
* E-mail: lenochka.chg@gmail.com
Поступила в редакцию 16.02.2022
После доработки 06.04.2022
Принята к публикации 11.04.2022
- EDN: ASVYGV
- DOI: 10.31857/S0044457X22100208
Аннотация
Аэрогели оксида алюминия получены из хлорида алюминия гексагидрата с использованием оксида пропилена в качестве гелирующего агента с последующей сверхкритической сушкой в CO2. Для получения лиогелей использованы золи различной концентрации: от 0.063 до 0.567 моль/л. С уменьшением концентрации золя продолжительность гелирования увеличивалась и составляла от 2 до 25 мин, а удельная поверхность аэрогелей практически не менялась и составляла от 335 до 406 м2/г. При этом образцы, полученные из золей с более высокой концентрацией, имели большее количество макропор. Микроструктура образцов исследована методом сканирующей электронной микроскопии, она практически не изменялась в зависимости от концентрации золя. Все образцы демонстрировали аморфную структуру при исследовании методом рентгенофазового анализа. Концентрационный предел гелирования составил 0.251 моль/л.
ВВЕДЕНИЕ
Наноразмерный оксид алюминия имеет целый ряд полезных свойств: контролируемую пористость, большую удельную поверхность, высокую химическую и термическую стабильность, коррозионную устойчивость, а также биосовместимость [1–3]. Благодаря комплексу этих свойств материалы на основе оксида алюминия в настоящее время находят широкое применение в различных областях. Они используются как фильтрующие элементы для коррозионно-активных газов при высокой температуре, для расплавленных металлов, в качестве костных имплантов, биореакторов, катализаторов и их носителей [4–6]. Оксогидроксиды алюминия также находят широкое применение. Так, материалы на основе бемита с модифицированной поверхностью могут быть использованы для сорбции тяжелых металлов, например, Ni(II) [7, 8].
Одними из наиболее перспективных наноразмерных материалов на основе оксида и оксогидроксида алюминия являются аэрогели. Аэрогели – это твердые мезопористые материалы, обладающие комплексом уникальных свойств: высокими удельной поверхностью и пористостью, низкой плотностью, а также низкой тепло- и звукопроводностью. Благодаря сочетанию таких свойств аэрогели широко применяются в различных областях, например, в качестве теплоизоляторов, ловушек для космической пыли, сорбентов для сверхкритической флюидной хроматографии [9–11].
Обычно аэрогели получают методом низкотемпературного золь-гель синтеза с последующей сверхкритической сушкой. Ранее показано, что, изменяя параметры золь-гель синтеза (химическую природу растворителя и гелирующего агента, состав прекурсора), можно в широких пределах менять структуру получаемого аэрогеля, а именно: размер и форму частиц, составляющих каркас геля, его удельную площадь поверхности и т.д. [12–18]. Кроме того, модифицируя поверхность полученного аэрогеля, можно придавать ему дополнительные каталитические свойства. Например, аэрогель Al2O3, допированный металлическими Pt или Pd, может быть использован в качестве катализатора в реакции окисления метана [19] и в процессе восстановления нитробензола до анилина [20]. Ранее показано [17], что нанесение сульфатных групп на поверхность аэрогеля придает последнему суперкислотные свойства.
Очевидно, что концентрация прекурсора и гелирующего агента в исходном золе должна напрямую влиять на свойства получаемого геля. Тем не менее не удалось найти работы, посвященные детальному изучению концентрации исходного золя на основные характеристики получаемых аэрогелей Al2O3.
Цель работы – исследование влияния концентрации исходного золя на основные характеристики получаемых аэрогелей, а также установление минимальной концентрации золя, необходимой для формирования геля.
ЭКСПЕРИМЕНТАЛЬНАЯ ЧАСТЬ
Метанол (99.8%, Acros), пропиленоксид (99.5%, Acros), гексагидрат хлорида алюминия (AlCl3 ⋅ 6H2O, 99%, Acros), трет-бутилметиловый эфир (МТБЭ, 99%, Acros) использовали без дополнительной очистки.
Получение лиогелей Al2O3. За основу для синтеза лиогелей оксида алюминия принята стандартная методика, описанная в работе [21], согласно которой для приготовления геля оксида алюминия необходимо 1 г гексагидрата хлорида алюминия растворить в 6.6 мл выбранного растворителя (например, метанола), а затем добавить 3.12 мл оксида пропилена в качестве гелирующего агента.
Готовили гели оксида алюминия с различной концентрацией исходного золя. Количество соли (AlCl3 · 6H2O) и оксида пропилена брали с коэффициентом от 0.9 до 0.1 по сравнению со стандартной методикой. При этом соотношение Al/пропиленоксид сохраняли постоянным, как в исходной методике. Количество реагентов для приготовления золя в зависимости от концентрации представлено в табл. 1. Относительную концентрацию (Crel) рассчитывали как отношение концентрации использованного золя к концентрации золя по стандартной методике.
Таблица 1.
Количество реагентов для приготовления золей различной концентрации, Vsolv = 6.6 мл
Образец | Crel | m(AlCl3 ⋅ 6H2O), г | Vоп, мл |
---|---|---|---|
S-0.9 | 0.9 | 0.9 | 2.808 |
S-0.8 | 0.8 | 0.8 | 2.496 |
S-0.7 | 0.7 | 0.7 | 2.184 |
S-0.6 | 0.6 | 0.6 | 1.872 |
S-0.5 | 0.5 | 0.5 | 1.56 |
S-0.4 | 0.4 | 0.4 | 1.248 |
S-0.3 | 0.3 | 0.3 | 0.936 |
S-0.2 | 0.2 | 0.2 | 0.624 |
S-0.1 | 0.1 | 0.1 | 0.312 |
Полученные золи помещали в герметичные полипропиленовые контейнеры. После образования геля образцы оставляли при комнатной температуре на 1 сут для старения. Затем полученные гели промывали МТБЭ 5 раз, заменяя растворитель каждые сутки для удаления непрореагировавших веществ и побочных продуктов реакции, и затем сушили в CO2 в сверхкритических условиях.
Сверхкритическая сушка. Сверхкритическую сушку в CO2 проводили в установке, состоящей из насоса высокого давления для CO2 Supercritical 24 (SSI, США), стального реактора емкостью 50 мл и регулятора обратного давления BPR (Waters, США). Образцы гелей промывали жидким CO2 в течение 2 ч при температуре 20°C и давлении 15 МПа, затем повышали температуру в реакторе до 50°C и промывали образец сверхкритическим CO2 в течение 2–2.5 ч. После этого давление в нагретом автоклаве постепенно снижали до атмосферного, автоклав охлаждали до комнатной температуры и вскрывали.
Методы анализа. Удельную площадь поверхности аэрогелей определяли методом низкотемпературной адсорбции азота (анализатор АТХ 06 Катакон, Россия) с применением модели Брюнауэра–Эммета–Теллера (БЭТ) по 5 точкам. Измерения полных изотерм адсорбции–десорбции проводили для образцов с использованием того же прибора по 28 точкам в диапазоне парциальных давлений азота p/p0 = 0.05–0.98. Перед измерениями осуществляли дегазацию образцов в токе сухого азота (1 атм) при 120°C в течение 60 мин.
Плотность и усадку образцов оценивали геометрически по отношению массы к объему и объема образца после усадки к исходному объему геля соответственно.
Рентгенофазовый анализ (РФА) твердофазных образцов проводили на дифрактометре Bruker D8 Advance (CuKα-излучение) при скорости вращения гониометра 5 град./мин.
Величину pH золей измеряли с помощью стеклянного электрода на анализаторе жидкостей Эксперт-001.
Для визуализации микроструктуры образца использовали метод сканирующей электронной микроскопии (Carl Zeiss N Vision 40). Микрофотографии были получены при ускоряющем напряжении 3 кВ с использованием детектора вторичных электронов (SE2). Рабочее расстояние составляло 3.5 мм.
РЕЗУЛЬТАТЫ И ОБСУЖДЕНИЕ
Процесс получения лиогеля по золь-гель методу можно условно разделить на три стадии: гидролиз исходной соли, образование первичных олигомеров (считается, что все гели на основе оксида алюминия состоят из олигомеров Al13 [22]) и формирование сетки геля за счет “сшивки” олигомеров между собой. Предположили, что чем меньше концентрация таких олигомеров в исходном золе, тем более разреженный гель можно получить. Ожидалось, что, разбавляя исходный золь, можно уменьшить плотность, а также увеличить удельную площадь поверхности получаемого геля (и аэрогеля).
Известно, что катионы металлов в водных растворах могут существовать в виде аква-, гидроксо- и оксоформ. Существование той или иной формы катиона металла в растворе определяется величиной pH. Реакция конденсации, приводящая к образованию сетки геля, требует присутствия в растворе гидроксоформ катионов металлов. Известно, что для водных растворов солей алюминия при pH < 3 существует акваформа – [Al(H2O)6]3+, а при повышении pH образуются частицы состава [Al(OH)x(H2O)6 ‒x](3 ‒x)+ [23]. Измерены значения pH исходных золей в зависимости от их концентрации. Величина pH увеличивалась с уменьшением концентрации золя и составляла 0.6 и 0.9 для образцов S-0.9 и S-0.3 соответственно.
Известно, что оксиды алкенов, например пропиленоксид, способны вступать в реакции раскрытия эпоксидного цикла, необратимо поглощая протон. Схема реакции раскрытия цикла приведена на рис. 1. Таким образом при добавлении пропиленоксида к раствору pH раствора повышается, что приводит к образованию гидроксоформ катионов алюминия и образованию геля.
Обнаружено, что продолжительность гелирования увеличивается при переходе от высоких концентраций к более низким. Образцы S-0.2 и S-0.1 за время наблюдения (две недели) гелей не образовывали, продолжительность гелирования образца S-0.3 составляла 2 ч. Однако через сутки образец снова стал жидким. Продолжительность гелирования в зависимости от концентрации золя приведена на рис. 2.
Следующим необходимым этапом золь-гель синтеза является старение. Во время старения происходит уплотнение и упрочнение сетки геля за счет продолжающихся процессов конденсации [24]. За счет этих же процессов часто наблюдается синерезис – усадка геля, сопровождаемая выталкиванием жидкости из пор. Данные по величине усадки геля в процессе старения в зависимости от концентрации исходных веществ приведены в табл. 2. Усадку считали геометрически как изменение объема геля, отнесенное к исходному объему.
Таблица 2.
Плотность аэрогеля и величины усадки геля в процессе старения и после сушки в зависимости от концентрации золя
Параметр | S-0.9 | S-0.8 | S-0.7 | S-0.6 | S-0.5 | S-0.4 |
---|---|---|---|---|---|---|
Усадка (старение), % | 32 | 27 | 20 | 0 | 0 | 0 |
Усадка (сушка), % | 65 | 62 | – | 62 | 66 | – |
Плотность, г/см3 | 0.08 | 0.09 | – | 0.08 | 0.08 | – |
Из представленных данных видно, что гели, полученные из более разбавленных золей, дают меньшую величину усадки во время старения. Более того, образцы S-0.6…S-0.4 вообще не дают усадки при старении. Вероятно, это связано с тем, что чем более разбавленный лиогель получаем, тем дальше находятся частицы друг от друга и, соответственно, из-за стерического эффекта образуют меньше связей друг с другом во время старения. Эта гипотеза хорошо подтверждается тем, что образцы, не уменьшившиеся в объеме вследствие усадки, после старения являются гораздо менее прочными (хуже держат форму).
Для получения аэрогелей из лиогелей использовали стандартную методику – низкотемпературную сверхкритическую сушку в CO2. Такая методика сушки применяется для синтеза аэрогелей, так как она позволяет избежать действия капиллярных сил на стенки пор геля и, следовательно, предотвращает разрушение структуры мокрого геля [25]. Тем не менее полученные результаты показывают, что в процессе сушки лиогель уменьшается в объеме.
При сверхкритической сушке в CO2 происходят последовательно следующие процессы: замена растворителя в порах геля на жидкий CO2, доведение CO2 до суперкритического состояния и удаление сверхкритического флюида.
При замене одного растворителя в порах геля на другой, в том числе на жидкий CO2, на границе раздела жидкостей возникает мениск при условии, что поверхностные натяжения жидкостей не равны.
Величины поверхностного натяжения для жидкого CO2 и МТБЭ составляют соответственно 1.19 × 10–3 и 18.56 × 10–3 Н/м при 20°С [26, 27]. В связи с этим в процессе замены МТБЭ в порах геля на жидкий CO2 возникает капиллярное давление, которое может быть рассчитано по формуле Лапласа:
где p – капиллярное давление, γ1 и γ2 – поверхностное натяжение жидкостей в порах (жидкость, которая изначально заполняла поры геля, и жидкость, на которую ее заменяют; в конкретном случае – это поверхностные натяжения МТБЭ и жидкого CO2), r – радиус поры, θ – контактный угол смачивания.Возникающее капиллярное давление может приводить как к растрескиванию, так и к усадке геля [25]. С другой стороны, сверхкритическая сушка приводит к разрушению сольватных оболочек частиц геля, которые частично препятствовали конденсации соседних гидроксильных групп и, следовательно, усадке геля. Плотность полученных аэрогелей практически не изменяется в зависимости от концентрации исходного золя (табл. 2).
Измерить усадку некоторых образцов после сушки не удалось, так как образцы в процессе сушки превратились в порошок. Усадка образцов в процессе сушки практически не зависит от концентрации золя. Тем не менее, можно отметить, что образец S-0.5 сильнее уменьшился в объеме вследствие усадки, чем образец S-0.8. Возможно, усадка образцов в процессе сушки может происходить по двум причинам: стресс вследствие замены растворителя и разрушение сольватных оболочек частиц геля.
Одним из основных параметров, характеризующих пористые материалы, в том числе аэрогели, является величина их удельной площади поверхности, которую определяли методом низкотемпературной адсорбции азота (табл. 3). Видно, что удельная площадь поверхности практически не изменяется в зависимости от концентрации исходного золя. Среднее ее значение составляет 362 ± 27 м2/г. Величина среднеквадратичного отклонения равна 7.5%, что не превышает типичную погрешность метода БЭТ [28].
Таблица 3.
Удельная поверхность аэрогелей в зависимости от концентрации исходного золя
Параметр | S-0.9 | S-0.8 | S-0.7 | S-0.6 | S-0.5 | S-0.4 |
---|---|---|---|---|---|---|
Sуд, м2/г | 380 | 406 | 334 | 335 | 341 | 378 |
Для более детальной характеризации пористой структуры образцов аэрогелей были получены полные изотермы адсорбции–десорбции азота для образцов S-0.4 и S-0.9 (рис. 3).
Видно, что обе изотермы адсорбции–десорбции азота относятся к типу IV (по классификации ИЮПАК), характерному для образцов с мезопорами, внутри которых происходит капиллярная конденсация, приводящая к формированию петли гистерезиса. Тип гистерезиса может быть отнесен к H3-типу (ИЮПАК), характерному для макропористых структур, которые не полностью заполняются адсорбатом [28].
Объем сорбции азота (q) в образце S-0.9 несколько больше для всех значений парциального давления азота. При максимальном измеренном парциальном давлении (p/p0 = 0.97) происходит резкое увеличение объема сорбции для образца S-0.9 (qа. д. с. = 2573 мл/г СТД для S-0.9 и 824 мл/г СТД для S-0.4), что, очевидно, вызвано наличием большого количества макропор в этом образце.
Распределение пор по размерам, рассчитанные по модели Баррета–Джойнера–Халенды, приведены на рис. 4. В образцах присутствует множество мезопор (2–50 нм) преимущественно размером до 25 нм, причем их количество близко в обоих образцах. Характерной особенностью образцов является наличие значительного количества макропор (d > 50 нм). Для образца S-0.9 их количество очень велико и составляет основную часть объема пор, благодаря чему он обладает кратно большими кумулятивным объемом пор (4.0 по сравнению с 1.3 мл/г для S-0.4) и средним размером пор (41 по сравнению с 12 нм для S-0.4) по десорбционной ветви кривой.
Рис. 4.
Распределение пор по размерам в образцах S-0.9 и S-0.4, рассчитанное по модели Баррета–Джойнера–Халенды, по десорбционной (а) и адсорбционной (б) ветвям кривой.
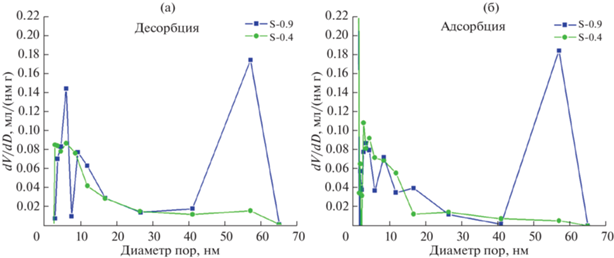
Сделан вывод, что несмотря на близкие значения удельной поверхности для всех образцов, их пористая структура сильно различается в зависимости от концентрации исходного золя. Использование золя с большей концентрацией (образец S-0.9) приводит к образованию большего количества макропор.
Микроструктуру полученных образцов исследовали методом сканирующей электронной микроскопии. Микрофотографии образцов S-0.9, S-0.7 и S-0.4 представлены на рис. 5. Видно, что микроструктура образцов практически не меняется с изменением концентрации исходного золя. Это соответствует остальным полученным экспериментальным данным.
Исследование методом РФА показало, что образцы аэрогелей S-0.9, S-0.7 и S-0.4 являются аморфными (рис. 6).
ЗАКЛЮЧЕНИЕ
Получены аэрогели Al2O3, различающиеся концентрацией исходного золя (от 0.1 до 0.9 по сравнению со стандартной методикой, что эквивалентно концентрации гексагидрата хлорида алюминия от 0.063 до 0.567 моль/л). Концентрационный предел гелирования составил 0.251 моль/л (0.4 от стандартной методики). Показано, что микроструктура геля, а также его удельная поверхность и фазовый состав практически не зависят от концентрации исходного золя. Это связано с тем, что гели с различной исходной концентрацией в разной степени подвержены усадке как при старении, так и при сверхкритической сушке. Величина усадки при этом практически полностью нивелирует эффект, ожидаемый от разбавления золя. Показано, что образцы, приготовленные из золей с большей концентрацией, демонстрируют большее количество макропор. Кроме того, при использовании золей разной концентрации можно изменять продолжительность гелирования в широком диапазоне (от 2 до 25 мин), что может быть актуальным при получении композитов на основе гелей и аэрогелей, а также при необходимости пропитывать золем другие материалы.
Список литературы
Alzukaimi J., Jabrah R. // Int. J. Appl. Ceram. Technol. 2019. V. 16. № 2. P. 820. https://doi.org/10.1111/ijac.13126
Chen Z., Xu G., Cui H. et al. // Int. J. Appl. Ceram. Technol. 2018. V. 15. № 6. P. 1550. https://doi.org/10.1111/ijac.13043
Kita K., Kondo N. // Int. J. Appl. Ceram. Technol. 2020. V. 17. № 1. P. 311. https://doi.org/10.1111/ijac.13362
Colombo P. // Philos. Trans. R. Soc. Ser. A. 2006. V. 364. № 1838. P. 109. https://doi.org/10.1098/rsta.2005.1683
Yu J.Y., Sun X.D., Li Q. et al. // Adv. Mater. Res. 2008. V. 41. P. 265. https://doi.org/10.4028/www.scientific.net/AMR.41-42.265
Lermontov S.A., Yurkova L.L., Straumal E.A. et al. // Russ. J. Inorg. Chem. 2016. V. 61. № 1. P. 7. https://doi.org/10.1134/S0036023616010137
Kropacheva T.N., Gazizyanova A.R., Gil’mutdinov F.Z. // Russ. J. Inorg. Chem. 2020. V. 65. № 8. P. 1150. https://doi.org/10.1134/S0036023620080070
Kozerozhets I.V., Panasyuk G.P., Semenov E.A. et al. // Russ. J. Inorg. Chem. 2020. V. 65. № 4. P. 587. https://doi.org/10.1134/S0036023620040099
Smirnova I., Gurikov P. // J. Supercrit. Fluids. 2018. V. 134. P. 228. https://doi.org/10.1016/j.supflu.2017.12.037
Smirnova I., Gurikov P. // Annu. Rev. Chem. Biomol. 2017. V. 8. P. 307. https://doi.org/10.1146/annurev-chembioeng-060816-101458
Kostenko M.O., Ustinovich K.B., Pokrovskii O.I. // Russ. J. Inorg. Chem. 2020. V. 65. № 10. P. 1577. https://doi.org/10.1134/S0036023620100125
Gash A.E., Tillotson T.M., Satcher Jr J.H. et al. // J. Non-Cryst. Solids. 2001. V. 285. № 1–3. P. 22. https://doi.org/10.1016/S0022-3093(01)00427-6
Gash A.E., Satcher J.H., Simpson R.L. // Chem. Mater. 2003. V. 15. № 17. P. 3268. https://doi.org/10.1021/cm034211p
Gash A.E., Satcher J.H., Simpson R.L. // J. Non-Cryst. Solids. 2004. V. 350. P. 145. https://doi.org/10.1016/j.jnoncrysol.2004.06.030
Gao Y.P., Sisk C.N., Hope-Weeks L.J. // Chem. Mater. 2007. V. 19. № 24. P. 6007. https://doi.org/10.1021/cm0718419
Lermontov S.A., Straumal E.A., Mazilkin A.A. et al. // J. Phys. Chem. C. 2016. V. 120. № 6. P. 3319. https://doi.org/10.1021/acs.jpcc.5b10461
Lermontov S.A., Straumal E.A., Mazilkin A.A. et al. // Mater. Lett. 2018. V. 215. P. 19. https://doi.org/10.1016/j.matlet.2017.12.031
Lermontov S.A., Sipyagina N.A., Malkova A.N. et al. // Russ. J. Inorg. Chem. 2014. V. 59. № 12. P. 1392. https://doi.org/10.1134/S0036023614120134
Aegerter M.A., Leventis N., Koebel M.M. Aerogels Handbook. N.Y.: Springer, 2011. 932 p. https://doi.org/10.1007/978-1-4419-7589-8
Armor J.N., Carlson E.J., Zambri P.M. // Appl. Catal. 1985. V. 19. № 2. P. 339. https://doi.org/10.1016/S0166-9834(00)81756-X
Baumann T.F., Gash A.E., Chinn S.C. et al. // Chem. Mater. 2005. V. 17. № 2. P. 395. https://doi.org/10.1021/cm048800m
Henry M., Jolivet J. P., Livage J. Aqueous chemistry of metal cations: hydrolysis, condensation and complexation // Chemistry, Spectroscopy and Applications of Sol-Gel Glasses. Berlin: Springer, 1992. 206 p. https://doi.org/10.1007/BFb0036968
Levy D., Zayat M. The Sol-Gel Handbook. Wiley, 2015. 1557 p. https://doi.org/10.1002/9783527670819
Brinker C.J., Scherer G.W. The physics and chemistry of sol-gel processing. San Diego: Academic Press, 1990. 908 p. https://doi.org/10.1080/10426919308934843
Pierre A.C., Pajonk G.M. // Chem. Rev. 2002. V. 102. № 11. P. 4243. https://doi.org/10.1021/cr0101306
Wang X., Pan J., Wu J. et al. // J. Chem. Eng. Data. 2006. V. 51. № 4. P. 1394. https://doi.org/10.1021/je060097q
Jianxin P., Yigang L. // Phys. Chem. Liq. 2009. V. 47. № 3. P. 267. https://doi.org/10.1080/00319100701824389
Thommes M., Kaneko K., Neimark A.V. et al. // Pure Appl. Chem. 2015. V. 87. № 9–10. P. 1051. https://doi.org/10.1515/pac-2014-1117
Дополнительные материалы отсутствуют.
Инструменты
Журнал неорганической химии