Химическая физика, 2022, T. 41, № 8, стр. 93-98
Термодинамическая оценка режимов окислительной конверсии продуктов пиролиза древесины с получением водорода и синтез-газа
М. В. Цветков 1, 2, *, В. М. Кислов 1, Ю. Ю. Цветкова 1, А. Ю. Зайченко 1, Д. Н. Подлесный 1, И. В. Седов 1, Е. А. Салганский 1
1 Институт проблем химической физики Российской академии наук
Черноголовка, Россия
2 Сахалинский государственный университет
Южно-Сахалинск, Россия
* E-mail: tsvetkov@icp.ac.ru
Поступила в редакцию 08.11.2021
После доработки 16.12.2021
Принята к публикации 20.12.2021
- EDN: XRCQTA
- DOI: 10.31857/S0207401X22080143
Аннотация
Проведена термодинамическая оценка режимов окислительной конверсии продуктов пиролиза древесины с получением водорода и синтез-газа. Исследованы режимы воздушной, кислородной и паровоздушной конверсии продуктов пиролиза древесины. В случае воздушной конверсии с увеличением коэффициента избытка топлива (φ) концентрация водорода логарифмически растет и достигает 29 об.% при φ = 10 и Т = 1000 К, однако уже при φ = 3 в продуктах появляется конденсированный углерод. Увеличение температуры до 1300 К незначительно повышает выход водорода: до 33 об.% при φ = 10, и при этой температуре сажеобразование начинается при φ = 5. Добавление паров воды приводит к увеличению содержания водорода в продуктах, а сажеобразование в этом случае начинается при φ = 9. Кислородная конверсия позволяет увеличить концентрации водорода и монооксида углерода в продуктах до 42.1 и 45.5 об.%, соответственно, вследствие отсутствия разбавления их азотом. Образование конденсированного углерода не является недостатком процесса, недостатком процесса, поскольку он (углерод) может рассматриваться как целевой продукт; при этом снижается количество выбросов диоксида углерода.
ВВЕДЕНИЕ
Экономическое развитие современного общества невозможно без обеспечения соответствующего уровня (и объема) вырабатываемой энергии. Практикуемое использование ископаемых источников в качестве основы энергетики в настоящее время не полностью отвечает современным требованиям человечества к энергоэффективности и экологичности топливно-энергетического комплекса. Ограниченность ресурсов, снижение их качества и экологические проблемы, связанные с их добычей и переработкой, а также выбросы вредных веществ, образующихся при их сжигании, стимулируют поиск новых, экологически чистых источников энергии [1, 2].
Современной тенденцией в развитии технологической оснащенности общества является переход к низкоуглеродной энергетике и использованию углеродно-нейтральных видов топлив. Одно из таких топлив – газообразный водород, что обусловлено присущим ему рядом преимуществ, главные из которых – экологическая чистота и высокий уровень энергии в единице массы [3–5].
В отличие от природного газа запасов молекулярного водорода в природе не существует, поэтому для его получения используют различное сырье и методы. В основу одной из классификаций способов получения водорода главным критерием положена его углеродная нейтральность: чем больше оксидов углерода выделяется при производстве водорода, тем менее экологичным будет считаться такой способ получения [6]. Степень углеродной нейтральности каждого способа получения водорода обозначается цветом [7].
Наиболее экологически чистым является процесс получения “зеленого” водорода, осуществляемый с помощью электролиза воды, с использованием энергии, получаемой из возобновляемых источников, таких как ветер, солнечная или гидроэнергия. При таком способе производства водорода выбросы СО2 минимальны, однако он является самым дорогостоящим [8, 9], поэтому его масштабы в настоящее время невелики. Несколько более дешевым, но менее экологичным является процесс получения “желтого” (“оранжевого”) водорода путем электролиза воды с использованием электроэнергии, полученной на атомных электростанциях. Выбросы СО2 при осуществлении этого процесса также минимальны, но получение энергии на АЭС потенциально связано с другими типами экологических загрязнений [10–13].
На данный момент большая часть водорода производится из ископаемых источников энергии. Основная его часть (до 90%) относится к так называемому “серому” водороду, получаемому путем каталитической (в основном паровой и парокислородной) конверсии природного газа (метана), проводимой в две стадии, на первой из которых в качестве промежуточного продукта получается синтез-газ (он также используется в качестве полупродукта в некоторых нефтехимических производствах); вторая стадия заключается в проведении реакции дальнейшей паровой конверсии одного из компонентов синтез-газа – CO, что позволяет получить дополнительное количество водорода [14, 15]. Данный способ требует меньших внешних энергозатрат, чем производство “зеленого” водорода, однако в ходе химической реакции выделяется углекислый газ, причем в том же объеме, что и при сгорании природного газа (расходуется также энергия на конверсию), поэтому “серый” водород тоже не может считаться экологически чистым [16, 17]. Если при конверсии осуществляется улавливание и захоронение образующегося СО2 (технологии Carbon Capture, Utilization and Storage), то удается достичь примерно двукратного сокращения вредных углеродных выбросов. Получаемый таким образом “голубой” водород может считаться более экологически чистым, чем “серый”, но его производство является весьма дорогостоящим [8, 9, 14, 18]. Разрабатываются и другие способы получения “чистого” водорода, например такие, как термокаталитический и плазменный пиролиз метана с получением “бирюзового” водорода и твердого углерода, а также способы, основанные на реакции металлов (алюминий, магний) с водяным паром [1, 19–22].
Самым дешевым, но наименее экологичным способом получения водорода является газификация каменного (бурого) угля [23–25]. Полученный таким способом водород называют “коричневым” (“бурым”). Степень углеродной нейтральности этого способа можно повысить, если вместо угля газифицировать биомассу. Биомассу относят к возобновляемым и углеродно-нейтральным топливам, так как ежегодно происходит увеличение объема биомассы, а рост последней сопровождается поглощением CO2 из воздуха [26–28].
Общим недостатком процессов газификации возобновляемых топлив является наличие в получаемых продуктах, помимо углекислого газа, монооксида углерода, водорода, метана, этилена и других газообразных веществ, а также некоторого количества смол, образующихся при термическом разложении топлив [29]. Требования, предъявляемые к содержанию смол в используемых в современной промышленности газообразных топливах и синтез-газе, весьма высоки. Например, для выработки электроэнергии с помощью современных газовых моторов содержание смол должно быть не более 100 мг/м3, для топливных ячеек – менее 100 ppm, а для осуществления синтеза Фишера–Тропша (каталитический процесс, используемый для получения жидких углеводородов) – менее 1 ppm [30, 31].
Ни один из существующих методов газификации биомассы не позволяет гарантировать необходимых пределов содержания смол в получаемых газообразных продуктах, поэтому перед их использованием необходима дополнительная очистка от пиролизных смол. Одним из перспективных методов очистки на данный момент является термохимическая конверсия смол в синтез-газ, так как она позволяет не только очищать газ от смол, но и преобразовывать их в дополнительное количество синтез-газа. Наиболее простым вариантом термохимической конверсии является парциальное окисление пиролизных смол, которое при использовании нестехиометрических (недостаточных) количеств окислителя позволяет преобразовать пиролизные смолы в компоненты синтез-газа. Очевидное преимущество данного способа конверсии – возможность за счет тепловыделения при парциальном окислении смол провести процесс без дополнительных затрат энергии. Сочетание методов газификации биомассы с последующей окислительной конверсией продуктов пиролиза предложено и экспериментально исследовано в работе [32]. Показано, что можно получить газообразные продукты газификации древесины практически без содержания жидких продуктов пиролиза.
Цель настоящей работы – термодинамическая оценка оптимальных условий получения водорода и синтез-газа при окислительной конверсии продуктов пиролиза древесины при атмосферном давлении.
МЕТОДИКА РАСЧЕТА
Для исследования многокомпонентных химических систем используются расчеты на основе моделей термодинамического равновесия, которые подробно описаны в литературе [33, 34]. Как правило, применяются два подхода для расчета параметров термодинамического равновесия изолированных многокомпонентных систем: поиск минимума свободной энергии Гиббса [35, 36] или решение задачи установления состояния системы, характеризующегося максимальной энтропией. Оба эти подхода являются равнозначными.
Для определения оптимальных условий получения газообразных продуктов с максимальным содержанием водорода проведен термодинамический расчет характеристик процесса конверсии продуктов пиролиза древесины с помощью программного комплекса TERRA [34] при различной температуре. Рассчитывали систему, состоящую из продуктов пиролиза древесины (брутто-формула C1H1.48O0.58, взятая из [37]), азота и кислорода, варьируя содержания водяного пара ([H2O] = 0 и 10 об.%) и кислорода в смеси с азотом ([O2] = 21 и 100 об.%). Коэффициент избытка топлива (φ), равный отношению количества кислорода, необходимого для полного окисления пиролизной смолы, к подаваемому количеству кислорода, изменяли в диапазоне от 2 до 10. Богатые топливные смеси имеют коэффициент избытка топлива больше единицы, а при φ = 1 происходит полное окисление продуктов пиролиза древесины до углекислого газа и воды. В расчетах задавали давление, равное атмосферному (0.1 МПа). Для заданного состава смеси в результате расчетов получали равновесный состав продуктов при определенной температуре. Температуру снизу ограничивали значением в 1000 К, так как при низких значениях температуры скорости химических реакций снижаются и термодинамическое равновесие будет достигаться за большее время [38–40].
РЕЗУЛЬТАТЫ И ИХ ОБСУЖДЕНИЕ
Конверсия продуктов пиролиза древесины с воздухом
Рассмотрим случай окислительной конверсии продуктов пиролиза древесины с воздухом. В общем случае продукты газификации древесины содержат как газообразные вещества, так и продукты ее пиролиза. В работе [37] показано, что выход продуктов пиролиза при газификации древесины составляет до 66 мас.%, включая воду, поэтому рассчитываем характеристики процесса конверсию только продуктов пиролиза древесины.
На рис. 1а представлены зависимости мольного содержания продуктов конверсии от коэффициента избытка топлива φ при значении температуры в конверторе 1000 К. Увеличение коэффициента избытка топлива от 2 до 4 приводит к росту концентрации монооксида углерода с 15 до 28 об.%. При дальнейшем увеличении значения φ концентрация СО плавно снижается. Концентрация водорода растет с увеличением φ и достигает 29 об.% при φ = 10. Содержание паров воды и диоксида углерода снижается с ростом φ до 4 и далее выходит на постоянный уровень. При φ > 3 в продуктах появляется конденсированный углерод (С(с)). В одном кубическом метре продуктов конверсии может содержаться примерно 500 г конденсированного углерода при φ = 10. С учетом того, что древесина считается углеродно-нейтральным топливом, режимы конверсии продуктов ее пиролиза с получением конденсированного углерода можно условно считать процессами, приводящими к изъятию CO2 из общего углеродного цикла (при условии выделения и использования или захоронения углерода).
Рис. 1.
Зависимости мольного содержания продуктов конверсии (X) от коэффициента избытка топлива φ для пиролизной смолы брутто-формулы C1H1.48O0.58: а – при 1000 К, [H2O] = 0 и [O2] = 21 об.%; б – при 1300 К, [H2O] = 0 и [O2] = 21 об.%, в – при 1300 К, [H2O] = 10 об.% и [O2] = 21 об.%; г – при 1300 К, [H2O] = 0 и [O2] = 100. Кривые: 1 – CO, 2 – H2, 3 – C(c), 4 – H2O, 5 – CO2.
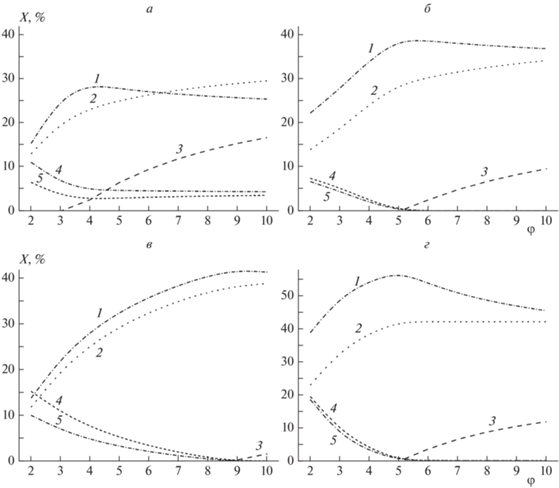
На рис. 1б представлены зависимости мольного содержания продуктов конверсии от коэффициента избытка топлива φ при значении температуры в конверторе 1300 К. Рост температуры приводит к увеличению содержаний СО и водорода и снижению содержаний диоксида углерода и паров воды в продуктах конверсии. Увеличение значения φ от 2 до 5 приводит к росту концентрации монооксида углерода с 22 до 38 об.%. При дальнейшем увеличении φ концентрация СО немного снижается. Концентрация водорода растет с увеличением φ и достигает 33 об.% при φ = 10. Содержание паров воды и диоксида углерода снижается до нуля с ростом значения φ до 5. При φ > 5 в продуктах появляется конденсированный углерод. При увеличении температуры конверсии режимы с образованием конденсированного углерода наблюдаются в области значений φ, соответствующих более богатым смесям.
Если проводить конверсию продуктов пиролиза древесины при температуре 1300 К без добавления воздуха, то максимальное содержание водорода, СО и конденсированного углерода в продуктах составит соответственно 42.1, 33.1 и 24.3 об.% (табл. 1). Таким образом, из 100 г пиролизных смол образуется 22.2 г конденсированного углерода. Однако в этом случае на проведение конверсии требуется подвод энергии извне.
Конверсия продуктов пиролиза древесины с воздухом и водяным паром
Добавление паров воды при конверсии может приводить к снижению температуры и увеличению содержания водорода в продуктах. На рис. 1в представлены зависимости мольного содержания продуктов конверсии от коэффициента избытка топлива φ при содержании паров воды 10 об.% в смеси с воздухом и значении температуры в конверторе 1300 К. При добавлении паров воды режимы с образованием конденсированного углерода реализуются только при φ > 9, т.е. для очень богатых смесей. С увеличением значения φ до 10 содержание СО и водорода растет соответственно до 41 и 38 об.%, а содержание паров воды и диоксида углерода снижается до нуля. Добавление паров воды приводит к увеличению содержания водорода в продуктах.
Аналогичный результат получен и при конверсии продуктов пиролиза древесины без добавления воздуха (табл. 1). Если проводить конверсию продуктов пиролиза древесины при температуре 1300 К и добавлении 10 об.% паров воды, то максимальное содержание водорода, СО и конденсированного углерода в продуктах составит соответственно 46.7, 38.5 и 14.3 об.% (табл. 1). В этом случае из 100 г пиролизных смол образуется 12.7 г конденсированного углерода.
Конверсия продуктов пиролиза древесины с кислородом
Использование чистого кислорода вместо воздуха при окислительной конверсии позволяет получать продукты, не разбавленные азотом. На рис. 1г представлены зависимости мольного содержания продуктов кислородной конверсии от коэффициента избытка топлива φ при значении температуры в конверторе 1300 К. Зависимости содержания продуктов конверсии от φ аналогичны случаю воздушной конверсии (см. рис. 1б). Максимальное содержание СО и водорода составляет соответственно 56 и 42 об.%. Содержание этих веществ выше, чем для случая воздушной конверсии (см. рис. 1б), за счет отсутствия разбавления продуктов азотом. Однако если в конвертор с продуктами пиролиза поступают газообразные продукты воздушной газификации древесины, то разбавление азотом тоже будет происходить, но в меньшей степени. Поэтому кислородную конверсию следует применять для продуктов пиролиза, отделенных от газообразных продуктов газификации древесины.
В табл. 2 представлено сравнение расчетных и экспериментальных данных по равновесным продуктам конверсии пиролизных смол древесины. В работе [32] проведено экспериментальное исследование воздушной конверсии продуктов газификации древесины. В реакторе фильтрационного горения происходила воздушная газификация сосновой древесины, продукты которой далее направлялись в конвертор, куда подавалось дополнительное количество воздуха для проведения окислительной конверсии продуктов пиролиза древесины. Из данных, приведенных в табл. 2, видно, что с уменьшением коэффициента избытка топлива температура в конверторе увеличивается за счет более полного окисления. Расчетный состав продуктов конверсии близок к составу продуктов конверсии, полученному в экспериментах, за исключением содержания водорода. Это можно объяснить тем, что в экспериментах не успевает установиться термодинамическое равновесие. Однако в целом, расчеты позволяют количественно оценивать характеристики окислительной конверсии продуктов пиролиза древесины.
Таблица 2.
Концентрации (в об.%) основных компонентов конверсии продуктов пиролиза древесины
φ | Температура конверсии, К | [СО2] | [N2] | [СО] | [СH4] | [H2] | |||||
---|---|---|---|---|---|---|---|---|---|---|---|
эксп. | расч. | эксп. | расч. | эксп. | расч. | эксп. | расч. | эксп. | расч. | ||
1.67 | 1200 | 15.3 | 12.4 | 65.6 | 64.2 | 14.1 | 14.0 | 0.8 | 0 | 2.8 | 8.8 |
1.43 | 1225 | 16.6 | 14.5 | 66.5 | 69.7 | 13.6 | 10.1 | 0.3 | 0 | 1.8 | 5.8 |
ЗАКЛЮЧЕНИЕ
Для определения оптимальных условий получения газообразных продуктов с максимальным содержанием водорода проведен термодинамический расчет характеристик процесса окислительной конверсии продуктов пиролиза древесины. Pасчеты позволяют количественно оценивать эти характеристики. Увеличение коэффициента избытка топлива, так же как и температуры конверсии, приводит к росту концентраций монооксида углерода и водорода. Добавление паров воды при фиксированной температуре конверсии приводит к увеличению содержания водорода в продуктах.
Если проводить конверсию продуктов пиролиза древесины при температуре 1300 К без добавления воздуха, то максимальное содержание водорода, СО и конденсированного углерода в продуктах составит соответственно 42.1, 33.1 и 24.3 об.%. Из 100 г пиролизных смол образуется 22.2 г конденсированного углерода. Однако в этом случае для проведения конверсии требуется подвод энергии извне.
Использование чистого кислорода при окислительной конверсии продуктов пиролиза позволяет получать продукты, не разбавленные азотом. Однако кислородную конверсию следует применять для продуктов пиролиза, отделенных от газообразных продуктов газификации древесины, содержащих в своем составе азот. При этом максимальное содержание СО и водорода достигает соответственно 56 и 42 об.%.
С учетом того, что древесина считается углеродно-нейтральным топливом, режимы конверсии продуктов ее пиролиза с получением конденсированного углерода (биококса) имеют отрицательный углеродный след, поскольку получаемый биококс является хорошим удобрением и депонированный в почву углерод изымается из атмосферного цикла.
Исследование выполнено в рамках госзадания (регистрационный номер АААА-А19-119022690098-3).
Список литературы
Шмелев В.М., Арутюнов В.С., Янг Х., Им Ч. // Хим. физика. 2017. Т. 36. № 5. С. 38; https://doi.org/10.7868/S0207401X17050090
Oliveira A.M., Beswick R.R., Yan Y. // Curr. Opin. Chem. Eng. 2021. V. 33. ID 100701; https://doi.org/10.1016/j.coche.2021.100701
Sunny N., Mac Dowell N., Shah N. // Energy Environ. Sci. 2020. V. 13. № 11. P. 4204; https://doi.org/10.1039/D0EE02016H
Арутюнов В.С., Стрекова Л.Н. // Нефтегазохимия. 2021. № 1–2. С. 8; https://doi.org/10.24412/2310-8266-2021-1-2-8-11
Алдошин С.М., Арутюнов В.С., Савченко В.И. и др. // Хим. физика. 2021. Т. 40. № 5. С. 46; https://doi.org/10.31857/S0207401X21050034
Megía P.J., Vizcaíno A.J., Calles J.A., Carrero A. // Energy Fuels. 2021. V. 35. № 20. P. 16403; https://doi.org/10.1021/acs.energyfuels.1c02501
Newborough M., Cooley G. // Fuel Cells Bulletin. 2020. V. 2020. № 11. P. 16; https://doi.org/10.1016/S1464-2859(20)30546-0
Kakoulaki G., Kougias I., Taylor N. et al. // Energy Convers. Manag. 2021. V. 228. ID 113649; https://doi.org/10.1016/j.enconman.2020.113649
Dawood F., Anda M., Shafiullah G.M. // Intern. J. Hydrog. Energy. 2020. V. 45. № 7. P. 3847; https://doi.org/10.1016/j.ijhydene.2019.12.059
Scamman D., Newborough M. // Ibid. 2016. V. 41. № 24. P. 10е080; https://doi.org/10.1016/j.ijhydene.2016.04.166
Karaca A.E., Dincer I., Gu J. // Ibid. 2020. V. 45. № 41. P. 22е148; https://doi.org/10.1016/j.ijhydene.2020.06.030
Якубсон К.И. // ЖПХ. 2020. Т. 93. № 12. С. 1675; https://doi.org/10.31857/S0044461820120014
Miller H.A., Bouzek K., Hnat J. et al. // Sustain. Energy Fuels. 2020. V. 4. P. 2114; https://doi.org/10.1039/c9se01240k
Zhang H., Sun Z., Hu Y. H. // Renew. Sustain. Energy Rev. 2021. V. 149. P. 111330; https://doi.org/10.1016/j.rser.2021.111330
Ripoll N., Salgansky E., Toledo M. // Intern. J. Heat Mass Transf. 2021.V. 177. ID 121472; https://doi.org/10.1016/j.ijheatmasstransfer.2021.121472
Boretti A. // Intern. J. Hydrog. Energy. 2021. V. 46. № 46. P. 23988; https://doi.org/10.1016/j.ijhydene.2021.04.182
Fierro M., Requena P., Salgansky E., Toledo M. // Chem. Eng. J. 2021. ID 130178; https://doi.org/10.1016/j.cej.2021.130178
Howarth R.W., Jacobson M.Z. // Energy Sci. Eng. 2021. V. 9. № 10. P.1676; https://doi.org/10.1002/ese3.956
Филиппов С.П., Ярославцев А.Б. // Успехи химии. 2021. Т. 90. № 6. С. 627; https://doi.org/10.1070/RCR5014
Kerscher F., Stary A., Gleis S. et al. // Intern. J. Hydrog. Energy. 2021. V. 46. № 38. P. 19897; https://doi.org/10.1016/j.ijhydene.2021.03.114
Harun K., Adhikari S., Jahromi H. // RSC Advances. 2020. V. 10. № 67. P. 40882; https://doi.org/10.1039/D0RA07440C
Rin T., Sangwichien C., Yamsaengsung R., Reungpeerakul T. // Intern. J. Hydrog. Energy. 2021. V. 46. № 56. P. 28е450. https://doi.org/10.1016/j.ijhydene.2021.06.101
Chen Q.Q., Lv M., Gu Y. et al. // Joule. 2018. V. 2. № 4. P. 607; https://doi.org/10.1016/j.joule.2018.02.015
Клишин В.И., Патраков Ю.Ф., Мандров Г.А. // Химия твердого топлива. 2013. № 5. С. 51; https://doi.org/10.7868/S0023117713050058
Midilli A., Kucuk H., Topal M. E., Akbulut U., Dincer I. // Intern. J. Hydrog. Energy. 2021. V. 46. № 50. P. 25385; https://doi.org/10.1016/j.ijhydene.2021.05.088
Lee R.P., Seidl L.G., Meyer B. // Clean Energy. 2021. V. 5. № 2. P. 180; https://doi.org/10.1093/ce/zkab002
Goede A.P.H. // EPJ Web Conf. EDP Sci. 2018. V. 189. P. 00010; https://doi.org/10.1051/epjconf/201818900010
Prabowo B., Aziz M., Umeki K. et al. // Appl. Energy. 2015. V. 158. P. 97; https://doi.org/10.1016/j.apenergy.2015.08.060
Podlesniy D.N., Zaichenko A.Yu., Tsvetkov M.V. et al. // Fuel. 2021. V. 298. ID 120862; https://doi.org/10.1016/j.fuel.2021.120862
Richardson Y., Blin J., Julbe A. // Prog. Energy Combust. Sci. 2012. V. 38. № 6. P. 765; https://doi.org/10.1016/j.pecs.2011.12.001
Shen Y., Yoshikawa K. // Renew. Sustain. Energy Rev. 2013. V. 21. P. 371; https://doi.org/10.1016/j.rser.2012.12.062
Кислов В.М., Глазов С.В., Салганская М.В., Пилипенко Е.Н., Цветкова Ю.Ю. // ЖПХ. 2021. Т. 94. № 3. С. 363; https://doi.org/10.31857/S0044461821030117
Петров В.В., Варзарев Ю.Н., Старникова А.П., Абдуллин Х.А. // Хим. физика. 2020. Т. 39. № 2. С. 37; https://doi.org/10.31857/S0207401X20020089
Трусов Б.Г. // Матер. XIV Междунар. конф. по химической термодинамике. Спб: НИИХ СПбГУ, 2002. С. 483.
Antzara A., Heracleous E., Bukur D.B., Lemonidou A.A. // Energy Procedia. 2014. V. 63. P. 6576; https://doi.org/10.1016/j.egypro.2014.11.694
Tabrizi F.F., Mousavi S.A.H.S., Atashi H. // Energy Convers. Manage. 2015. V. 103. P. 1065; https://doi.org/10.1016/j.enconman.2015.07.005
Salgansky E.A., Kislov V.M., Glazov S.V., Salgan-skaya M.V. // J. Combustion. 2016. ID 9637082; https://doi.org/10.1155/2016/9637082
Козлов С.Н., Тереза А.М., Медведев С.П. // Хим. физика. 2021. Т. 40. № 8. С. 34; https://doi.org/10.31857/S0207401X21080070
Tereza A.M., Medvedev S.P., Smirnov V.N. // Acta Astronaut. 2020. V. 176. P. 653; https://doi.org/10.1016/j.actaastro.2020.03.045
Тереза А.М., Агафонов Г.Л., Андержанов Э.К. и др. // Хим. физика. 2021. Т. 40. № 8. С. 56; https://doi.org/10.31857/S0207401X21080136
Дополнительные материалы отсутствуют.
Инструменты
Химическая физика